プラスチック射出成形について知っておくべきことすべて
プラスチック射出成形について知っておくべきことすべて
プラスチック射出成形 は、複雑なプラスチック部品を製造するために広く使用されている製造プロセスです。 このブログ投稿では、プラスチック射出成形の基本、その機能、用途、利点、欠点について説明します。
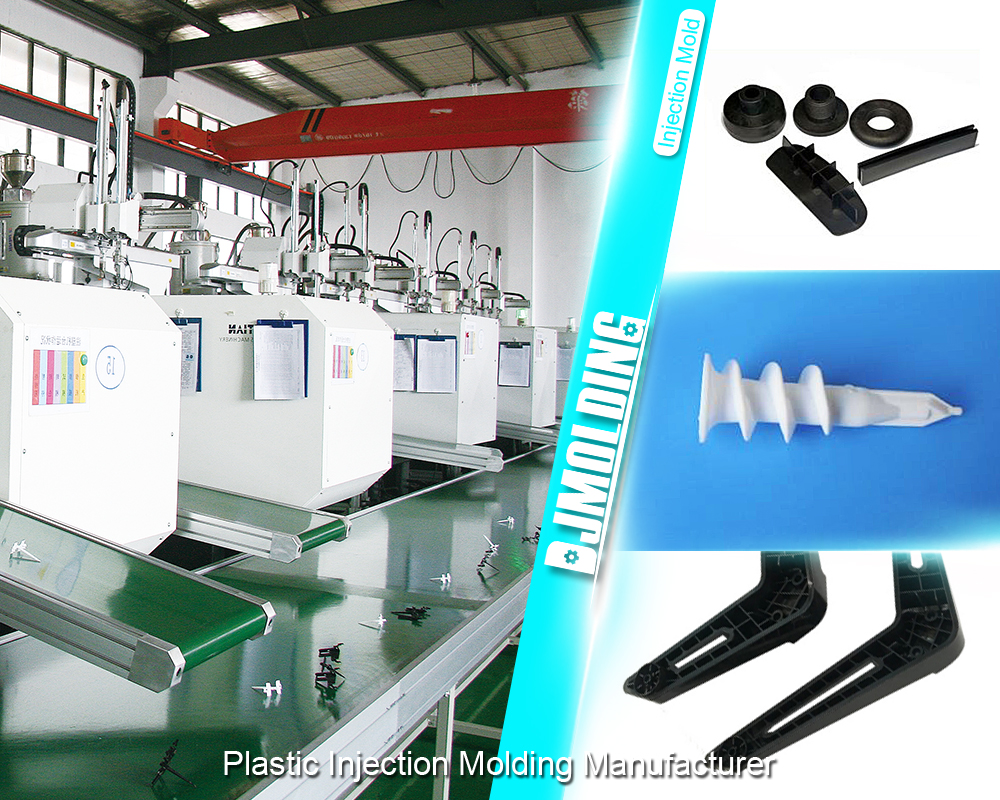
プラスチック射出成形:
プラスチック射出成形は、高品質のプラスチック製品を大量に生産するための最も一般的な製造方法の XNUMX つです。 自動車、医療、包装、消費財などのさまざまな業界では、製品の製造に射出成形が使用されています。 このプロセスには、プラスチック ペレットを溶かし、高圧下で金型に注入することが含まれます。 その後、プラスチックが冷えて固化し、金型キャビティが形成されます。 このブログ投稿では、プラスチック射出成形プロセスの詳細を詳しく説明します。
プラスチック射出成形プロセス
プラスチック射出成形は、複数のステップを含む複雑なプロセスです。 プラスチック射出成形プロセスに含まれる基本的な手順は次のとおりです。
金型設計
プロセスの最初のステップは金型の設計です。 プロセスの最初のステップは、コンポーネントの 3D モデルの作成に役立つコンピューター支援設計 (CAD) ソフトウェアを使用して金型を開発することです。 この設計に基づいて、鋼またはアルミニウムを使用して金型が作成されます。
材料の選択
次のステップは、コンポーネントの材料を選択することです。 熱可塑性プラスチックは、何度でも溶かして再形成できるため、プラスチック射出成形に最も一般的に使用される材料です。 選択される材料は、意図された用途に適している必要があります。
加熱と溶解
設計チームが金型を作成し、適切な材料を選択すると、射出成形機がプラスチック ペレットを加熱して溶かします。 射出成形プロセスでは、材料が均一に溶けるように温度が注意深く制御されます。
注射
次に、溶融したプラスチックを高圧下で金型キャビティに注入します。 圧力により、材料が隙間全体を確実に満たし、金型の形状になります。
冷却と排出
その後、プラスチックを冷却して固化させ、金型キャビティの形状をとります。 プラスチックが冷えると、射出成形機が金型を開き、コンポーネントを取り出します。
プラスチック射出成形の用途
プラスチック射出成形は、さまざまな業界でさまざまなコンポーネントを製造するために使用されています。 プラスチック射出成形の最も一般的な用途のいくつかを以下に示します。
- 自動車産業: さまざまな業界がプラスチック射出成形を使用して、自動車のダッシュボード、バンパー、内装トリムなどのさまざまなコンポーネントを製造しています。
- 医療部門: プラスチック射出成形では、注射器、吸入器、手術器具などの医療機器が製造されます。
- 包装業界: プラスチック射出成形では、ボトルのキャップ、容器、蓋などの包装部品が製造されます。
- 消費財業界: プラスチック射出成形では、玩具、電子機器、家電製品などのさまざまな消費者製品が製造されます。
プラスチック射出成形の利点
プラスチック射出成形 は広く使用されている製造プロセスであり、他の製造方法に比べていくつかの利点があります。 このプロセスでは、溶融プラスチックを金型キャビティに射出し、冷却して固化して高品質の部品を形成します。 プラスチック射出成形の利点をいくつか紹介します。
高効率
プラスチック射出成形は、大量の部品を迅速に生産できる効率の高いプロセスです。 これは、数百、場合によっては数千の機能を迅速に備えた自動プロセスであり、大規模な生産実行に最適です。 さらに、プロセスを最適化してサイクル時間を最小限に抑え、効率をさらに向上させることができます。
一貫性と精度
プラスチック射出成形により、高精度で一貫したサイズと形状の部品が製造されます。 金型キャビティにより、機械が希望の寸法で要素を作成し、プロセスの再現性が高くなります。 プラスチック射出成形によって製造される一貫した品質は、正確な測定が重要な用途に不可欠であり、製造されるコンポーネントの品質が一貫していることが保証されます。
多才
プラスチック射出成形では、さまざまなサイズや形状のコンポーネントを製造できます。 設計者は、他の方法では製造が困難または不可能な薄肉部品など、複雑な形状のフィーチャを備えた金型を作成できます。 さらに、このプロセスでは、エンジニアリンググレードの樹脂を含むさまざまなプラスチック材料を使用でき、コンポーネントの望ましい特性に基づいて選択できます。
高い費用対効果
プラスチック射出成形は、部品を大量に生産するためのコスト効率の高いプロセスです。 金型の設計と製造の初期コストは高くなる可能性がありますが、生産量が増加するにつれてコンポーネントあたりのコストは減少します。 さらに、プロセスを自動化できるため、人件費が削減され、効率が向上します。 余分な材料はリサイクルして将来の生産に使用できるため、材料の無駄が最小限に抑えられ、コストの削減にも役立ちます。
最小限の材料廃棄物
プラスチック射出成形では、余分な材料をリサイクルして将来の生産に使用できるため、材料の無駄が最小限に抑えられます。 プラスチック射出成形は、必要な量の材料のみを溶かして金型キャビティに注入するため、他の製造方法より効率的であり、無駄が削減されます。 通常、余分な材料は収集されて再利用されるため、廃棄物が削減され、持続可能性が向上します。
最も重大な欠点
メーカーはプラスチック射出成形の利点を活かして広く使用していますが、いくつかの重大な欠点を考慮する必要があります。 このセクションでは、プラスチック射出成形の最も重要な欠点について説明します。
高い初期投資
プラスチック射出成形の主な欠点の XNUMX つは、金型の作成に必要な初期投資が高額であることです。 金型の設計と作成プロセスは、特に複雑な設計や大型の金型の場合、コストがかかる場合があります。 金型のコストは中小企業や新興企業にとって参入障壁となる可能性があり、高額な投資を行う余裕のある大企業と競争することが困難になります。
設計の柔軟性が限られている
金型によってコンポーネントの設計が制限されるため、手順の変更が困難になり、費用がかかる可能性があります。 金型を頻繁に変更することは、変更のたびに追加の時間と費用が必要となるため、重大な欠点となる可能性があります。 設計の柔軟性におけるこの制限は、頻繁な更新やカスタマイズが必要な製品にとって特に困難になる可能性があります。
生産時間
プラスチック射出成形のもう XNUMX つの欠点は、設計から製造までに数週間かかることです。 金型の設計と作成、材料の準備、生産に時間がかかるため、納期を短縮することが困難になる場合があります。 金型の変更は、迅速な生産時間を必要とする企業や短い製品ライフサイクルに直面している企業にとって、重大なデメリットとなる可能性があります。
環境影響
プラスチック射出成形プロセスは環境に悪影響を与える可能性があります。 このプロセスでは、プラスチックを加熱して溶かすために化石燃料を使用する必要があり、温室効果ガスの排出につながります。 さらに、このプロセスでは過剰なプラスチックやエネルギーの使用による廃棄物が発生し、環境に悪影響を与える可能性があります。
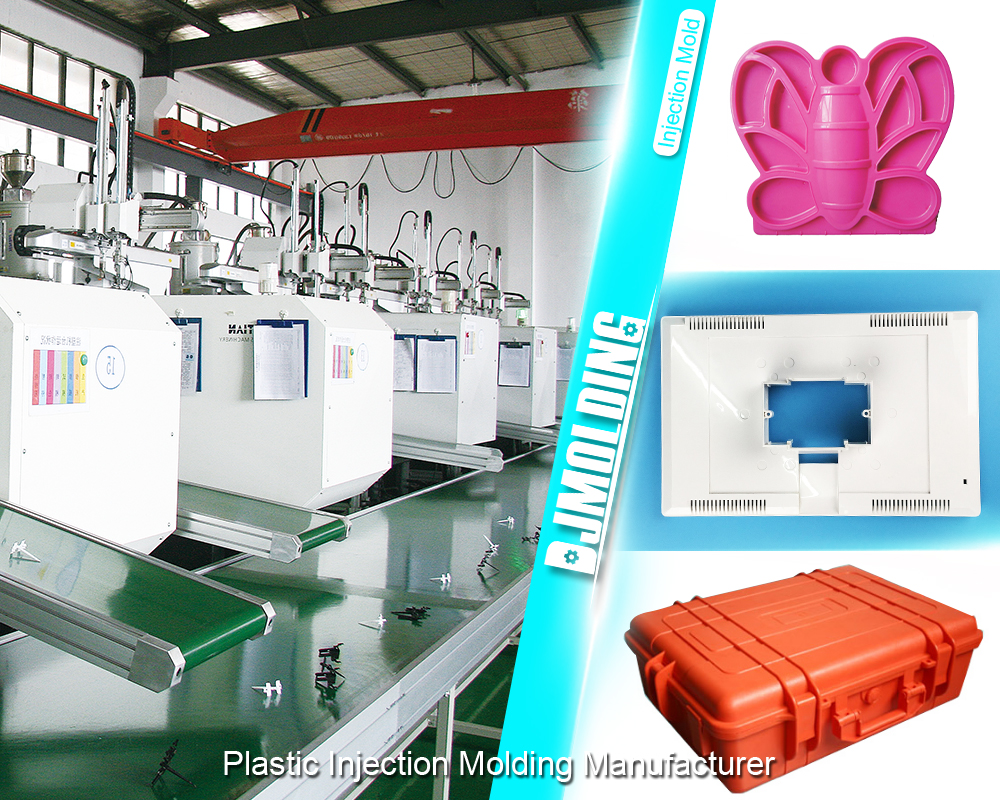
結論
結論として、プラスチック射出成形は、高品質のプラスチック製品を生産するための信頼性が高く効率的な製造プロセスです。 一貫性、精度、費用対効果などの利点により、さまざまな業界で人気があります。 ただし、初期投資が高くつくことや設計の柔軟性が制限されることなどのデメリットも考慮する必要があります。 プラスチック射出成形は、製造業界に革命をもたらした貴重な技術です。 技術の進歩に伴い、プラスチック射出成形は進化と改良を続け、より効率的でコスト効率が高く、環境に優しいものになると考えられます。
詳細については プラスチック射出成形、Djmolding を訪れることができます。 https://www.djmolding.com/ 詳細はこちら