少量のカスタムプラスチック射出成形: 精密部品の製造に関する包括的なガイド
少量のカスタムプラスチック射出成形: 精密部品の製造に関する包括的なガイド
内外を発見する カスタムプラスチック射出成形、精密部品を作成する多用途の製造プロセス。 このプロセスに含まれる利点、用途、重要な考慮事項について学びます。
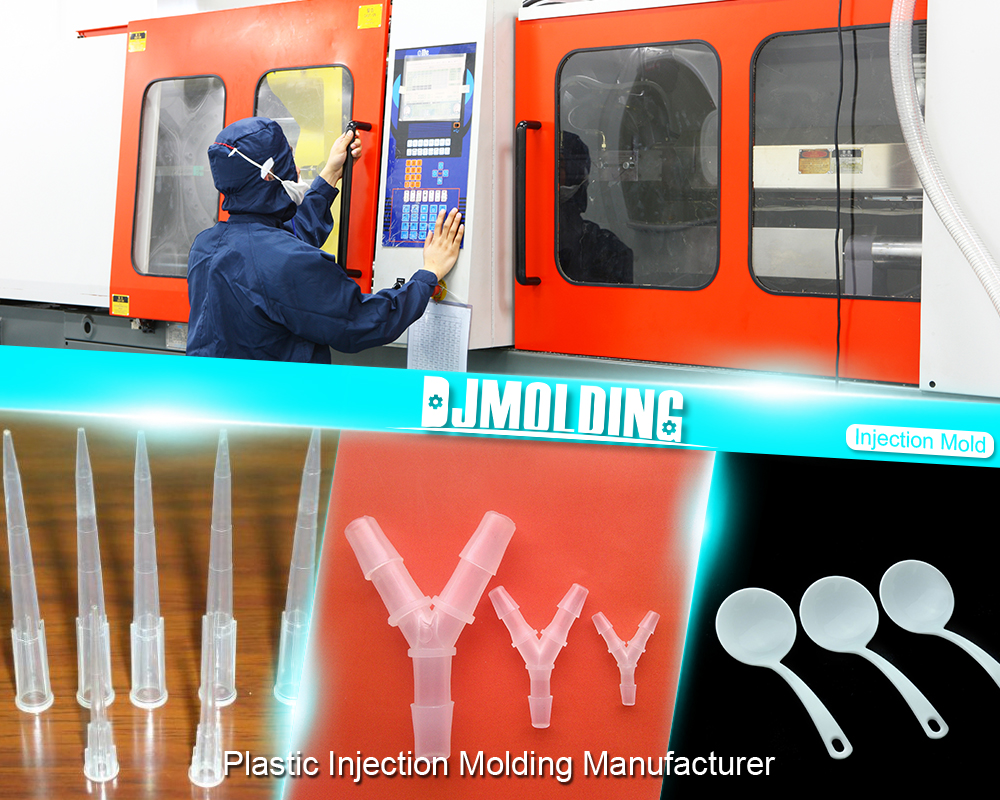
概要
カスタムプラスチック射出成形は、非常に効率的であり、多くの業界で重要な製造プロセスとして広く採用されています。 メーカーは、溶融プラスチックをカスタム設計の金型に射出することで、高品質で複雑な部品を精度と一貫性を持って製造できます。 この包括的なガイドでは、カスタム プラスチック射出成形の世界を深く掘り下げ、その定義、利点、用途、実装の成功に影響を与える要因を探ります。
カスタムプラスチック射出成形について理解する
定義とプロセスの概要
カスタムプラスチック射出成形では、溶融プラスチックを金型キャビティに射出することでプラスチック部品を製造します。 溶けたプラスチックが金型内で固化し、目的の形状が形成されます。 通常、このプロセスには、金型の設計、材料の選択、射出成形機の操作、冷却、後処理など、いくつかの重要なステップが含まれます。
カスタムプラスチック射出成形の利点
- コスト効率と高い生産率: 射出成形では、材料の無駄を最小限に抑えて部品を大量生産できるため、大規模製造においてはコスト効率の高いオプションとなります。
- 設計の柔軟性と複雑な形状: このプロセスにより、複雑なデザイン、複雑な形状、および複数のコンポーネントを XNUMX つの部品に統合することが可能になります。
- 材料のオプションと性能特性: カスタムプラスチック射出成形は、特定の用途に適した独自の特性を備えた幅広い熱可塑性プラスチック材料をサポートしています。
カスタムプラスチック射出成形の一般的な用途
カスタムプラスチック射出成形は、自動車、エレクトロニクス、医療機器、消費財などを含むさまざまな業界で幅広く使用されています。 この技術は、ハウジング、エンクロージャ、ギア、ボタン、および公差が厳しい複雑な部品などのコンポーネントの製造に使用されます。
射出成形プロセスの重要なコンポーネントとステップ
金型の設計・開発
- 金型の種類: XNUMX プレート金型、XNUMX プレート金型、ホット ランナー金型などのさまざまな金型は、部品や生産量の要件に基づいて明確な利点を提供します。
- 金型の材料と構造に関する考慮事項: 金型の寿命、コスト、耐熱性、耐久性などの要因が金型材料の選択に影響します。
材料の選択と準備
適切な熱可塑性プラスチック材料を選択することは、所望の部品特性、耐久性、性能を達成するために非常に重要です。機械的特性、耐薬品性、環境への配慮などの要素が材料の選択に影響します。 材料の準備には、乾燥、混合、および場合によっては添加剤の添加が含まれます。
射出成形機の操作
- クランプおよび射出ユニット: クランプユニットは金型を所定の位置に保持し、射出ユニットはプラスチックを溶かして金型に射出します。
- 温度と圧力の制御: 正確な温度と圧力のパラメータ制御により、最適な金型充填と部品の品質が保証されます。
冷却と排出
プラスチックを射出した後、冷却して固まり、金型の形を整えます。 欠陥を防止し、寸法精度を達成するには、適切な冷却が不可欠です。 冷却されると、エジェクター ピンまたはその他の機構を使用して部品が金型から取り出されます。
後処理と仕上げ
最終的に必要な部品仕様を達成するには、余分な材料のトリミング、表面処理、組み立てなどの後処理作業が必要になる場合があります。
カスタムプラスチック射出成形の成功に影響を与える要因
設計上の考慮事項
- パーツの複雑さと形状: 複雑な部品設計では、適切な充填と部品の排出を確保するために、金型の設計と材料の流れを慎重に検討する必要があります。
- 抜き勾配と壁の厚さ: 適切な抜き勾配と均一な肉厚は、金型を離型し、ヒケや反りなどの欠陥を防ぐために重要です。
材料の選択と特性
適切な熱可塑性プラスチック材料を選択するには、強度、剛性、柔軟性、耐薬品性、耐熱性、望ましい表面仕上げなどの要素を考慮する必要があります。 部品の特定の要件とその用途を理解することは、情報に基づいた材料の選択に役立ちます。
ツーリングと金型の設計
金型の設計と構造は、カスタムプラスチック射出成形の成功において重要な役割を果たします。 エンジニアは、金型設計時に部品の複雑さ、アンダーカット、ゲートの位置、通気、冷却チャネルなどの要素を考慮する必要があります。 一貫した生産を確保し、ダウンタイムを最小限に抑えるには、適切な工具のメンテナンスと定期的な検査が不可欠です。
品質管理と検査
高品質の部品を生産するには、堅牢な品質管理措置を導入することが不可欠です。 射出成形プロセスのさまざまな段階での検査とテストは、問題を迅速に特定して対処するのに役立ちます。 寸法チェック、目視検査、および材料テストは、カスタムプラスチック射出成形で使用される標準的な品質管理手法です。
カスタムプラスチック射出成形の利点と制限
Advantages
コスト効率と高い生産率
射出成形により、短期間で多くの部品を生産できるため、XNUMX個あたりのコストが削減されます。 プロセスの高い再現性と効率により、コスト削減に貢献します。
設計の柔軟性と複雑な形状
カスタムプラスチック射出成形 薄壁、内部機能、さまざまな厚さを含む、複雑で複雑な部品設計が可能になります。 このプロセスは、他の製造方法では困難または不可能な、アンダーカット、ねじ山、および複雑な形状を備えた部品の作成に対応します。
材料のオプションと性能特性
射出成形は、汎用プラスチック、エンジニアリングプラスチック、高性能ポリマーなどのさまざまな熱可塑性プラスチック材料をサポートします。 この多用途性により、メーカーは、意図した用途の要件を満たす特定の機械的、熱的、電気的、または化学的特性を持つ材料を選択することができます。
制限事項
初期工具費用
金型の設計と構築には多額の初期費用がかかる場合があり、複雑な部品や複数のキャビティが必要な場合には工具の費用が高くなる可能性があります。 ただし、生産量が増加するにつれて、部品あたりのコストは大幅に減少します。
設計上の制約と制限
射出成形には、抜き勾配、均一な肉厚、適切なゲートとエジェクター ピンの位置などの設計上の制限があります。 部品の設計段階で、設計者は成形を確実に成功させ、部品の品質を維持するためにこれらの制約を考慮する必要があります。
時間と生産量の考慮事項
金型の設計、工具、材料の準備など、射出成形プロセスのセットアップには時間がかかります。 カスタムプラスチック射出成形は、中規模から大量の生産量において最もコスト効率が高くなります。 3D プリントや機械加工などの代替方法は、少量生産に適している場合があります。
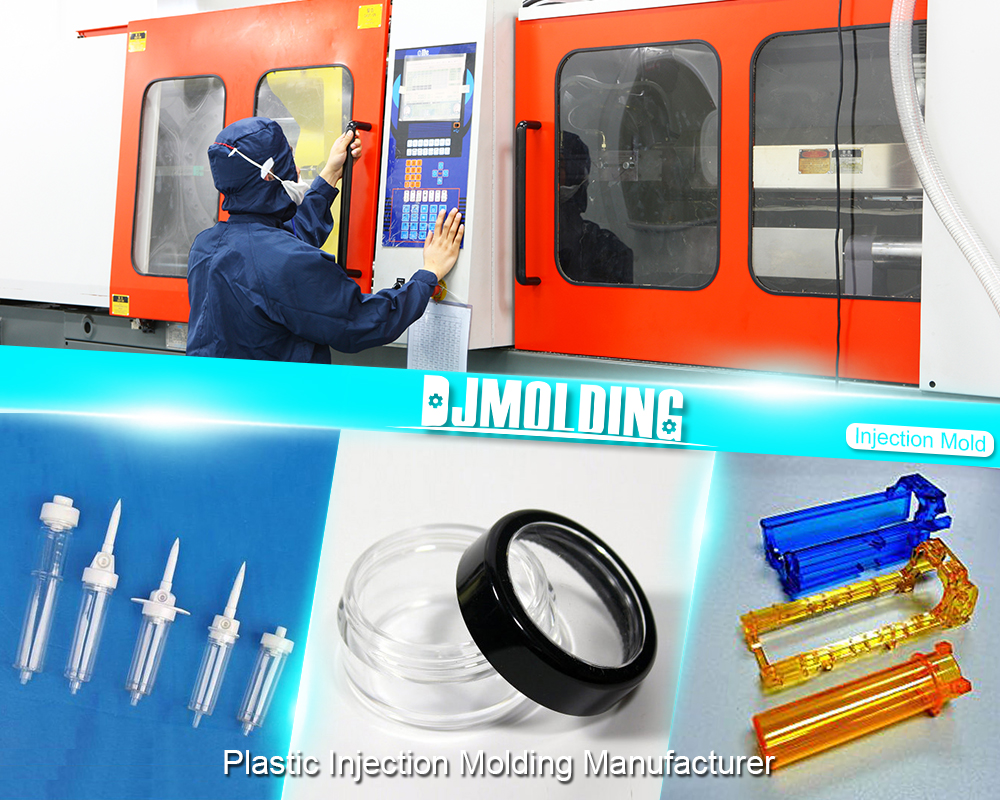
まとめ
カスタムプラスチック射出成形は、高品質で精密な部品を製造するためにさまざまな業界で使用される多用途で効率的な製造プロセスです。 この包括的なガイドでは、カスタム プラスチック射出成形の定義、利点、一般的な用途について説明しました。 また、射出成形プロセスに含まれる主要なコンポーネントと手順、実装の成功に影響を与える要因、プロセスの利点と限界についても説明しました。 カスタムプラスチック射出成形の機能と考慮事項を理解することで、メーカーは情報に基づいた意思決定を行い、特定の製造ニーズにその可能性を活用できるようになります。
詳細については 少量のカスタムプラスチック射出成形、Djmolding を訪れることができます。 https://www.djmolding.com/ 詳細はこちら