사출 성형의 일반적인 성형 결함에 대한 솔루션
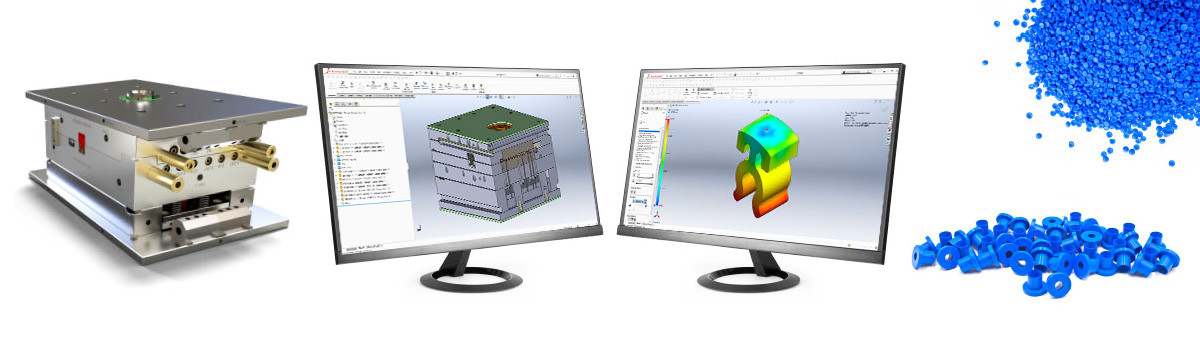
금형을 사용하여 플라스틱 사출 성형 부품을 가공할 때 결함이 흔히 발생하며 이는 가공 효율에 큰 영향을 미칩니다. 다음은 플라스틱 사출 성형 부품에 대한 일반적인 성형 결함 및 해결 방법입니다.
짧은 샷
미성형은 금형이 완전히 채워지지 않아 불완전하게 만들어진 제품을 말합니다.
이 결함은 일반적으로 게이트에서 가장 멀리 떨어진 지점이나 몰드의 좁은 영역을 통해서만 도달할 수 있는 부품에 나타납니다. 좁은 영역이 용융물의 흐름에 영향을 미칠 수 있기 때문입니다.
미성형은 마이크로 플로우 마크를 유발하거나 제품의 상당 부분이 명백히 누락될 수 있습니다.
원인:
짧은 샷의 원인은 다음과 같습니다.
금형에 주입된 원료가 충분하지 않습니다.
용융 저항이 커서 금형을 완전히 채울 수 없습니다.
금형의 통풍이 잘 되지 않아 용융물을 막는 캐비테이션이 발생하여 용융물이 금형의 일부 영역으로 흐르지 못하게 됩니다.
버
버는 금형 캐비티에서 압출된 잉여 원료가 제품에 부착되어 발생합니다.
이 결함은 제품의 가장자리 또는 금형의 각 구성 부분에 발생합니다. 원료는 금형 또는 이동 및 고정 금형의 접합 부위에서 넘칠 수 있습니다.
Burr는 금형 코어에서도 찾을 수 있는데, 이는 유압 또는 앵귤러 핀 때문입니다.
버의 정도는 다양하며 때로는 얇거나 두껍습니다.
원인:
버의 원인은 다음과 같습니다.
클램핑 금형 표면이 손상되었거나 심하게 마모되었습니다.
이동금형과 고정금형은 잠겼을 때 위치가 이탈됩니다.
금형의 원료 압력은 금형 클램핑 력보다 높습니다.
위에서 언급한 세 번째 조건은 여러 가지 이유로 인해 발생합니다. 다음 상황에서 원료의 압력이 금형 클램핑 력보다 높습니다.
사출 금형의 첫 번째 단계(금형 충전 단계)에서 너무 많은 원료가 채워져 금형 내부의 압력이 증가합니다.
금형 충전 공정 중에 용융 흐름의 큰 저항은 금형 내부의 압력도 상승시킵니다.
압력 유지 단계에서 금형 캐비티 압력이 너무 높습니다.
형체력이 충분하지 않습니다.
하락
분해는 많은 결과를 가져올 수 있습니다. 문제의 범위와 심각도도 다양합니다. 심할 경우 제품의 완전한 변색 및 기계적 물성 저하의 원인이 됩니다. 국부적 열화는 어두운 줄무늬나 반점만 유발합니다.
원인:
열화는 원료가 손상되어 발생합니다. 플라스틱을 형성하는 긴 사슬 분자는 과도한 열이나 과도한 전단 응력의 작용으로 분해됩니다. 분자가 분해되는 동안 휘발성 가스는 분해 과정을 가속화하여 원료의 탈색을 유발합니다. 다량의 분자 분해는 최종적으로 원료의 함량을 파괴하고 기계적 특성에 부정적인 영향을 미칩니다.
재료 배럴의 불균일한 온도로 인해 국부적으로 열화가 발생할 수 있습니다.
다음과 같은 상황에서 성능 저하가 발생할 수 있습니다.
원료가 원료 배럴 또는 핫 러너 시스템에서 과열되고 있습니다.
원재료가 배럴에 너무 오래 머물러 있습니다.
사출 성형 공정 중에 원료에 가해지는 전단 응력이 너무 큽니다. 노즐이 막히거나 게이트와 러너가 너무 좁으면 전단 응력이 증가합니다.
흉한 모습
정상적인 상황에서 제품의 모양은 금형의 모양과 일치해야 합니다. 변형은 제품의 변형을 말합니다.
상태가 악화되면 제품이 금형에서 배출될 때 제품이 완전히 변형됩니다. 상태가 심각하지 않은 경우 제품 모양에 작은 불규칙성이 나타납니다.
길지만 지지 가장자리가 없거나 큰 평면은 변형되기 가장 쉬운 영역입니다.
원인:
변형의 원인:
금형이 해제될 때 온도가 너무 높습니다.
두께가 두꺼운 부분과 얇은 부분의 냉각시간이 다르고 금형을 이동하고 고정할 때의 금형 온도 차이로 인해 제품 내부의 수축률이 다릅니다.
충진 시 금형 흐름이 원활하지 않거나(소위 "동결 방향") 압력 유지 단계에서 금형 캐비티 내부의 압력이 너무 높습니다.
불순물
불순물은 종종 다양한 색상, 패치 또는 줄무늬의 반점 형태로 나타납니다. 가장 흔한 것은 검은 반점입니다.
불순물은 아주 작은 반점일 수 있지만 심각할 경우 명백한 줄무늬 또는 탈색의 큰 부분일 수도 있습니다.
원인:
불순물은 다음과 같은 원료와 혼합된 잡화로 인해 발생합니다.
배럴로 수송될 때 잡화와 섞이는 원료.
원료의 분해는 기계 볼트, 건조 드럼의 내벽, 조인트/노즐과 같은 절단 메커니즘에서 떨어지고 원료에 혼합될 수 있습니다.
라미네이션
라미네이션은 제품 표면과 기타 원재료의 특성 및 질감의 차이로 인해 제품 표면에 "표피 효과"를 발생시켜 제거할 수 있는 박리 표피를 형성합니다.
라미네이션이 심한 경우 전체 단면적이 서로 다른 층으로 구성되어 함께 녹지 않습니다. 결함이 명확하지 않은 경우 제품의 외관이 요구 사항을 충족할 수 있지만 제품의 기계적 특성이 손상됩니다.
원인:
라미네이션에는 두 가지 주요 원인이 있습니다. 첫 번째는 서로 다른 두 종류의 원료가 잘못 섞였을 때입니다. 두 가지 원료는 동시에 압력을 받아 배럴로 이송됩니다. 그러나 금형이 냉각될 때 함께 녹을 수 없는 경우에는 서로 다른 층을 강제로 함께 눌러 제품을 형성하는 것과 같습니다.
두 번째: 콜드 멜트가 좁은 게이트를 강제로 통과하면 전단 응력이 생성됩니다. 전단 응력이 너무 높으면 미리 녹은 용융 층이 완전히 융합될 수 없습니다.
혼합 위험:
한 가지 주의할 점은 함께 혼합된 일부 원료는 강한 화학 반응을 일으킬 수 있다는 것입니다. 예를 들어 PVC와 Avetal은 혼합해서는 안 됩니다.
실버 리니어
슬라이버 선형은 국부적인 현상일 뿐 심할 경우 전체 표면으로 확장될 수 있습니다.
은선은 제품의 외관에 영향을 미치고 제품의 기계적 특성을 손상시킵니다.
원인:
다음 두 가지 사항으로 인해 은색 선형이 발생합니다.
원료가 젖어서 일부는 공기 중의 증기를 흡수합니다. 원료가 너무 젖어 있으면 Barrel의 고온 고압 하에서 가압 증기가 생성될 수 있습니다. 이 증기는 제품 표면을 뚫고 은색 줄무늬를 형성합니다.
용융물은 열 손상을 입어 국부적인 열화를 일으킵니다. 생성된 휘발성 가스는 금형 표면에서 차단되어 제품 표면에 줄무늬를 생성합니다.
이것은 열화만큼 나쁘지 않습니다. 용융물의 온도가 높거나 가소화 또는 금형에 주입하는 동안 전단 응력을 받는 한 이런 일이 발생할 수 있습니다.
광택/그림자
제품의 표면 마감은 금형과 동일해야 합니다. 둘의 표면 마감이 다른 경우 광택/음영 불량이 발생하였다.
결함이 발생하면 표면이 어둡고 거친 표면이 매끄럽고 광택이 있습니다.
원인:
광택/그림자의 원인은 다음과 같습니다.
용융물이 매끄럽지 않게 흐르거나 금형 표면의 온도가 낮아 재료 성형 시 금형 표면 마감을 복제할 수 없습니다.
압력을 유지하는 동안 캐비티의 압력은 냉각 과정에서 재료가 금형 표면에 달라붙어 수축 자국을 남길 만큼 충분히 높지 않습니다.
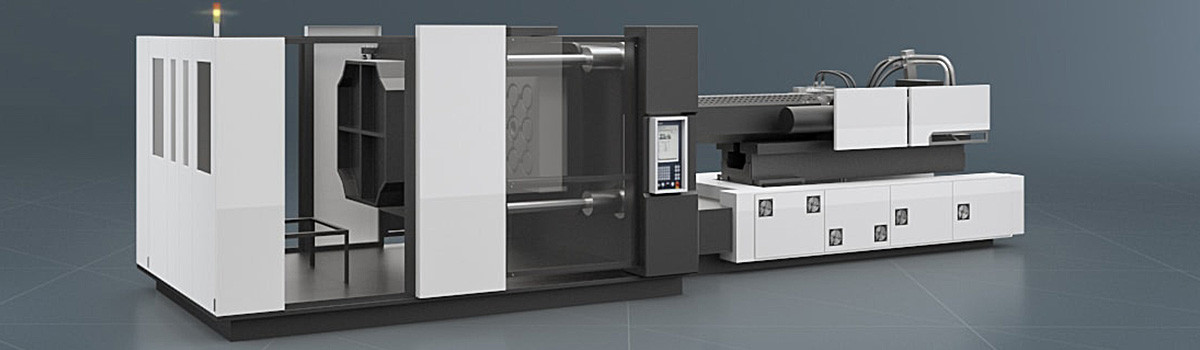
플로우 마크
플로우 마크는 다양한 형태로 제품 표면에서 찾아볼 수 있습니다. 일반적으로 그림자 영역을 형성합니다.
플로우 마크는 제품 표면에 손가락으로 느낄 수 없는 엠보싱이나 함몰이 생기지 않습니다. 이 결함은 드래그 마크, 고스트 및 그림자라고도 합니다.
흐름 자국이 분명하면 홈이 생기고 제품 표면에 자국과 같은 결함이 남습니다.
원인:
플로우 마크는 다음과 같은 경우에 찾을 수 있습니다.
용융물의 유동성이 좋지 않거나 금형의 표면 온도가 낮아 금형 충전 공정에서 플라스틱의 유동 저항이 커집니다.
금형 충진에서 금형의 고르지 않은 표면, 금형 표면에 인쇄된 마크 또는 패턴 또는 충진 공정 중 용융 흐름 방향의 변경으로 인해 발생할 수 있는 저항이 있는 용융 유동.
접합선
접합선은 금형을 채우는 동안 두 개의 용융 선단이 만날 때 생성되며 제품 표면에 선처럼 나타납니다.
이음선은 제품 표면의 균열선과 같으며 감지하기가 쉽지 않습니다.
금형을 설계할 때 눈에 보이는 접합선이 불가피합니다. 이 경우 접합선을 최대한 짧게 하여 제품의 강도 및 외관 손상을 방지합니다.
원인:
멜트 프론트 생성에는 여러 가지 이유가 있습니다. 가장 가능한 이유는 금형 코어의 가장자리를 따라 흐르는 용융 흐름일 수 있습니다. 두 용융물이 만나면 접합선이 생성됩니다. 두 용융 전면의 온도는 성공적으로 융합될 수 있을 만큼 충분히 높아야 하며 제품의 강도와 외관에 영향을 미치지 않아야 합니다.
두 용융물이 완전히 융합되지 않으면 결함이 발생합니다.
결함의 원인:
금형은 더 두꺼운 부분과 더 얇은 부분을 가지고 있으며 용융물의 흐름 속도가 다릅니다. 용융물이 금형의 얇은 부분을 통해 흐를 때 온도가 낮습니다.
러너마다 길이가 다릅니다. 외톨이 주자는 식히기 쉽습니다.
금형 캐비티 압력은 압력 유지 단계에서 용융물이 완전히 융합될 만큼 충분하지 않습니다.
남은 기포는 용융 전면이 융합할 수 없게 만들어 연소로 이어집니다.
타고있는
버닝은 쇼트 샷과 비슷하지만 가장자리가 불규칙하게 변색되고 약간의 타는 냄새가 납니다. 상태가 심각할 때 플라스틱 타는 냄새와 함께 카본 블랙 부분이 제품에 나타납니다.
결함이 제거되지 않으면 종종 금형에 검은색 침전물이 생깁니다. 연소 시 발생하는 가스나 기름 물질을 즉시 확인하지 않으면 공기 구멍이 막힐 수 있습니다. 연소는 일반적으로 경로의 끝에서 발견됩니다.
원인:
연소는 내부 연소 효과로 인해 발생합니다. 공기 중의 압력이 매우 짧은 시간에 급격히 증가하면 온도가 상승하여 화상을 입을 수 있습니다. 수집된 데이터에 따르면 사출 성형 공정의 내부 연소 효과는 최대 600도까지 고온을 생성할 수 있습니다.
화상은 다음과 같은 경우에 발생할 수 있습니다.
금형 충진 속도가 빨라 금형 캐비티에서 공기가 빠져나가지 못하고 들어오는 플라스틱의 차단으로 인해 기포가 발생하고 압축 후 내연 효과가 발생합니다.
통풍구가 막히거나 환기가 원활하지 않습니다.
금형의 공기는 공기 구멍에서 비워야 합니다. 환기가 위치, 개수, 크기 또는 기능에 의해 영향을 받으면 공기가 금형에 남아 연소됩니다. 금형 조임력이 크면 통풍이 잘 안 됩니다.
수축
수축은 제품 표면의 미세한 구멍을 말합니다.
결함이 경미한 경우 제품 표면이 고르지 않습니다. 심각한 경우 제품의 넓은 영역이 무너집니다. 아치, 손잡이, 돌출부가 있는 제품은 종종 수축 결함이 발생합니다.
원인:
수축은 냉각 중에 원료의 대면적 수축으로 인해 발생합니다.
제품의 두꺼운 영역(아치와 같은)에서 재료의 코어 온도가 낮기 때문에 수축이 표면의 수축보다 늦게 발생하여 원료 내부에 수축력이 발생하고 바깥쪽을 안쪽 함몰부로 당깁니다. 수축을 일으키기 위하여.
수축은 다음과 같은 상황에서 발생합니다.
금형 캐비티의 압력은 냉각 과정에서 원료의 수축으로 인해 발생하는 힘보다 낮습니다.
냉각 공정 중 금형 캐비티의 가압 시간이 부족하여 원료가 게이트에서 캐비티 밖으로 흘러 나옵니다.
과량의 원료가 주입되기 전에 스크류가 완전히 인출되므로 성형 및 압력 유지 단계에서 원료의 완충 능력이 충분하지 않습니다.
게이트와 러너의 단면적은 제품의 두께보다 훨씬 작습니다. 즉, 제품 압출 공정 전에 게이트가 이미 동결되었음을 의미합니다.
버블
진공 기포는 투명 제품에서 쉽게 볼 수 있는 기포 형태로 제시됩니다. 불투명한 제품의 단면에서도 볼 수 있습니다.
원인:
기포는 제품의 진공 부분으로 냉각 과정에서 원료가 수축할 때 발생합니다.
수축과 마찬가지로 원료 내부에서 수축력이 발생합니다. 차이점은 기포가 형성될 때 제품의 외관이 고화되어 붕괴가 없기 때문에 중공 기포가 발생한다는 것입니다.
기포의 원인은 다음을 포함하여 감소의 원인과 동일합니다.
비효율적인 금형 캐비티 압력
불충분한 캐비티 가압 시간
러너와 게이트의 크기가 너무 작음
스프레이 자국
스프레이 자국은 게이트 반대편의 나사산 영역을 나타냅니다. 분사 자국은 제품의 외관에 영향을 줄 뿐만 아니라 제품의 강도에도 영향을 미칩니다.
원인:
용사 자국은 금형 충전 공정 중에 제어할 수 없는 용융 흐름으로 인해 발생합니다.
녹은 플라스틱은 엄청난 압력으로 금형에 들어갑니다. 금형 충전 속도가 너무 높으면 금형 캐비티의 열린 틈에서 플라스틱이 배출되어 빠르게 튀어 나와 냉각됩니다. 이때 나사산이 형성되어 녹은 플라스틱이 게이트로 들어가는 것을 차단합니다.
스프레이 자국의 주요 원인은 게이트의 잘못된 위치 또는 게이트 디자인입니다. 다음 두 가지 상황은 결함 상황을 악화시킵니다.
높은 금형 충전 속도
금형 충전 중 용융 흐름 불량