플라스틱 사출 성형이란
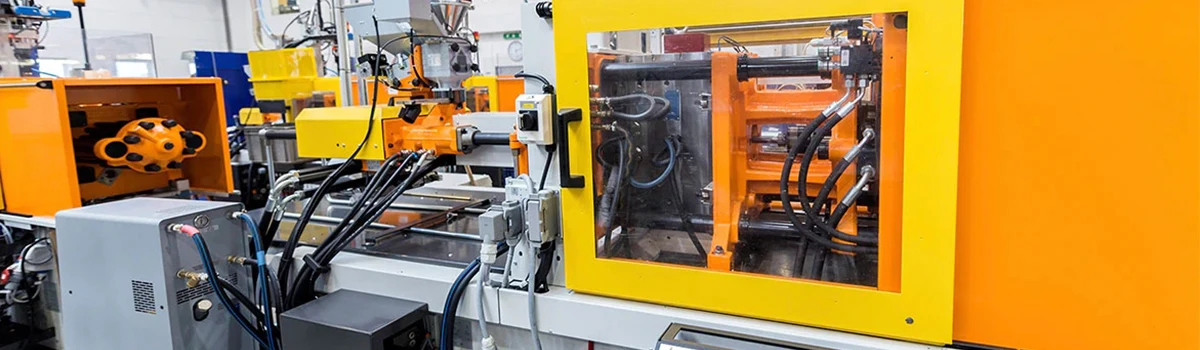
열가소성 사출 성형은 플라스틱 재료로 대량 부품을 제조하는 방법입니다. 설계 옵션의 신뢰성과 유연성으로 인해 사출 성형은 포장, 소비자 및 전자 제품, 자동차, 의료 등을 포함한 많은 산업에서 사용됩니다.
사출 성형은 세계에서 가장 널리 사용되는 제조 공정 중 하나입니다. 열가소성 수지는 가열되면 부드러워지고 흐르며 냉각되면 응고되는 폴리머입니다.
어플리케이션
사출 성형은 플라스틱 부품을 제조하는 가장 일반적인 최신 방법입니다. 동일한 개체의 대량 생산에 이상적입니다. 사출 성형은 와이어 스풀, 포장, 병 뚜껑, 자동차 부품 및 구성 요소, 게임 콘솔, 주머니 빗, 악기, 의자 및 작은 테이블, 보관 용기, 기계 부품 및 기타 여러 플라스틱 제품을 포함하여 많은 것을 만드는 데 사용됩니다.
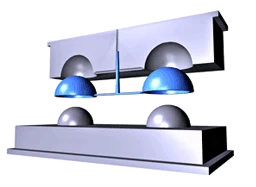
금형 설계
CAD 패키지와 같은 소프트웨어에서 제품을 설계한 후 일반적으로 강철 또는 알루미늄과 같은 금속으로 금형을 만들고 정밀 가공하여 원하는 부품의 형상을 형성합니다. 금형은 사출 금형(A 플레이트)과 이젝터 금형(B 플레이트)의 두 가지 기본 구성 요소로 구성됩니다. 플라스틱 수지는 스프루 또는 게이트를 통해 금형에 들어가고 A 및 B 플레이트의 면에 가공된 채널 또는 러너를 통해 금형 캐비티로 흐릅니다.
사출 성형 공정
열가소성 플라스틱을 성형할 때 일반적으로 펠렛화된 원료는 호퍼를 통해 왕복 나사가 있는 가열된 배럴로 공급됩니다. 스크루는 체크 밸브를 통해 원재료를 전달하며 스크루 전면에서 샷이라고 하는 볼륨으로 모입니다.
샷은 금형의 스프루, 러너 및 캐비티를 채우는 데 필요한 수지의 양입니다. 재료가 충분히 모이면 재료가 고압 및 속도로 부품 형성 캐비티로 강제 주입됩니다.
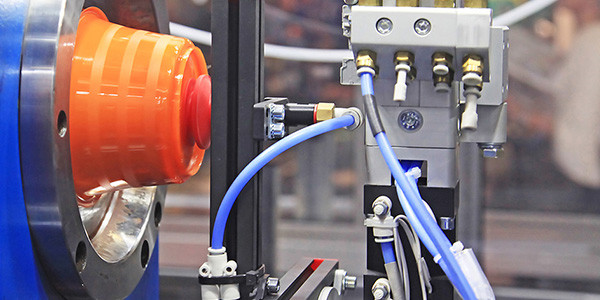
사출 성형은 어떻게 작동합니까?
플라스틱이 스프루, 러너, 게이트 등을 포함하여 금형을 채운 후에는 재료가 부품 형태로 균일하게 응고될 수 있도록 금형을 설정 온도로 유지합니다. 배럴로의 역류를 중지하고 수축 효과를 줄이기 위해 냉각하는 동안 보압이 유지됩니다. 이 시점에서 다음 주기(또는 샷)를 예상하여 더 많은 플라스틱 알갱이가 호퍼에 추가됩니다. 냉각되면 플래튼이 열리고 완성된 부품을 배출할 수 있으며 스크류가 다시 한 번 뒤로 당겨져 재료가 배럴에 들어가고 프로세스를 다시 시작할 수 있습니다.
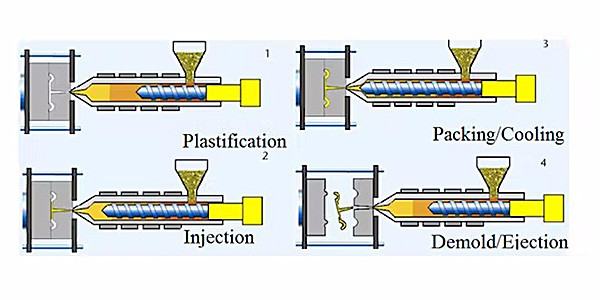
사출 성형 주기는 금형 닫기, 플라스틱 알갱이 공급/가열, 금형에 가압, 고체 부품으로 냉각, 부품 배출 및 금형 다시 닫기와 같은 연속 프로세스로 작동합니다. 이 시스템은 플라스틱 부품의 신속한 생산을 가능하게 하며 설계, 크기 및 재료에 따라 작업일에 10,000개 이상의 플라스틱 부품을 만들 수 있습니다.
사출 성형 주기
사출 성형 주기는 일반적으로 2초에서 2분 사이로 매우 짧습니다. 여러 단계가 있습니다.
1. 클램핑
재료를 금형에 주입하기 전에 금형의 두 반쪽이 클램핑 장치에 의해 단단히 닫힙니다. 유압식 클램핑 장치는 금형 반쪽을 함께 밀고 재료가 주입되는 동안 금형을 닫힌 상태로 유지하기에 충분한 힘을 가합니다.
2.주사
금형이 닫힌 상태에서 폴리머 샷이 금형 캐비티에 주입됩니다.
3. 냉각
캐비티가 채워지면 더 많은 폴리머가 캐비티에 들어갈 수 있도록 유지 압력이 가해져 플라스틱이 냉각되면서 수축하는 것을 보상합니다. 그 동안 나사가 돌아가서 다음 샷을 앞쪽 나사로 공급합니다. 이로 인해 다음 샷이 준비될 때 나사가 후퇴합니다.
4. 방출
부품이 충분히 냉각되면 금형이 열리고 부품이 배출된 후 주기가 다시 시작됩니다.
장점
1. 빠른 생산; 2. 디자인 유연성; 3. 정확도; 4.낮은 인건비; 5.낮은 낭비