플라스틱 사출 성형 주요 고려 사항
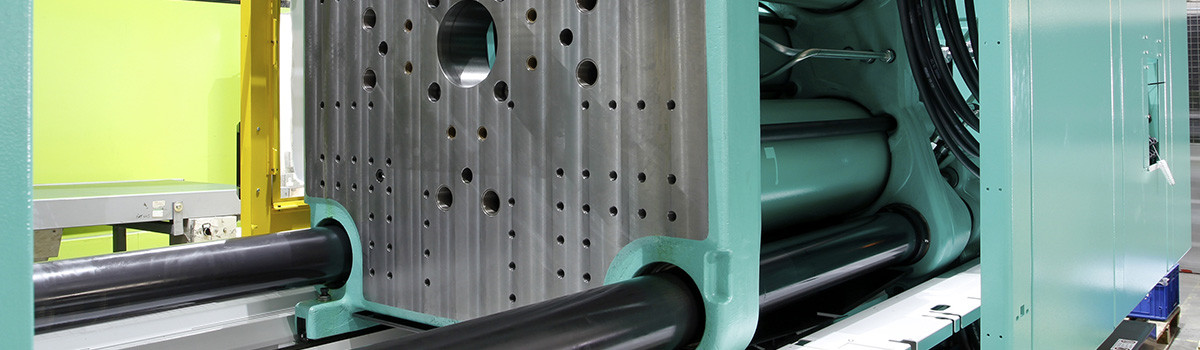
성공적인 사출 성형 프로젝트는 한 번에 여러 요소를 고려해야 합니다.
재료 선택
재료는 사출 성형에서 중요한 역할을 합니다. 숙련된 사출 성형 공급자가 예산 및 성능 요구 사항에 맞는 열가소성 수지를 선택하도록 도와줄 수 있습니다. 성형업체는 구매하는 열가소성 수지의 대량 구매에 대해 할인을 받는 경우가 많기 때문에 이러한 절감액을 여러분에게 전가할 수 있습니다.
공차 변동
사출 성형을 통해 만들어진 모든 제품은 의도한 용도에 맞는 특정 공차를 가져야 합니다. 특정 재료는 필요한 공차를 성형하거나 유지하기 어려울 수 있으며 툴링 설계도 최종 부품의 공차에 영향을 미칠 수 있습니다. 항상 특정 제품에 대한 허용 오차 범위에 대해 사출 성형기와 논의하십시오.
배럴 및 노즐 온도
성형기는 수지가 금형 전체를 흐르는 능력에 영향을 미치기 때문에 사출 성형 시 특정 배럴 및 노즐 온도를 유지해야 합니다. 배럴 및 노즐 온도는 열분해 온도와 용융 온도 사이에서 정확하게 설정되어야 합니다. 그렇지 않으면 오버플로, 플래시, 느린 흐름 또는 채워지지 않은 부품이 발생할 수 있습니다.
열가소성 유량
성형기는 가열된 플라스틱이 95% ~ 99%가 채워질 때까지 금형의 캐비티에 가능한 한 빨리 주입되도록 최적의 유속을 유지해야 합니다. 적절한 유속을 유지하면 플라스틱이 캐비티로 흐르기에 적합한 점도 수준을 유지할 수 있습니다.
사출 성형 작업에서 고려해야 할 다른 요소는 다음과 같습니다.
*게이트 위치
* 싱크 마크
* 차단 각도
*텍스처링
* 구배 및 구배 각도 방향
* 강철 안전 지역
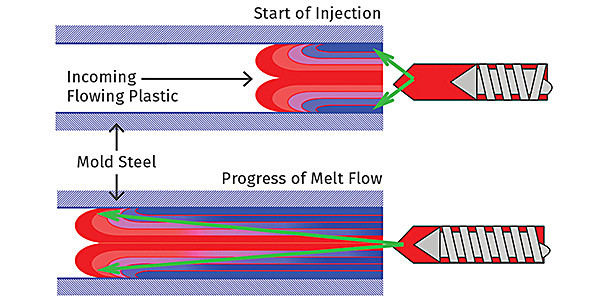
사출 성형 공정의 XNUMX가지 주요 단계
사출 성형 공정에는 XNUMX가지 주요 단계가 포함되며 제대로 수행되지 않으면 이러한 단계에서 문제가 발생할 수 있습니다.
1. 클램핑
이 과정에서 금형의 두 반쪽은 클램핑 장치를 사용하여 단단히 고정되며, 클램핑 장치는 수력을 사용하여 금형을 닫기에 충분한 힘을 가합니다. 적절한 클램핑력이 없으면 프로세스에서 벽 섹션이 고르지 않고 무게가 일관되지 않으며 크기가 다양해질 수 있습니다. 과도한 클램핑력은 미성형, 화상 및 광택 수준 변화를 초래할 수 있습니다.
2.주사
성형기는 용융된 열가소성 재료를 래밍 장치 또는 고압의 나사로 금형에 주입합니다. 그런 다음 부품이 균일한 속도로 냉각되도록 해야 합니다. 그렇지 않은 경우 최종 부품에 미관에 영향을 미치는 흐름선이나 원하지 않는 패턴이 있을 수 있습니다.
3. 주거 압력
열가소성 수지 재료가 금형에 주입되면 금형 제작자는 캐비티를 완전히 채우기 위해 더 많은 압력을 가합니다. 그들은 일반적으로 금형의 게이트가 동결될 때까지 용융된 열가소성 재료를 유지합니다. 체류 기간은 올바른 압력을 적용해야 합니다. 너무 낮으면 완제품에 싱크 마크가 남을 수 있습니다. 압력이 너무 높으면 버, 치수가 커지거나 부품이 금형에서 분리되는 문제가 발생할 수 있습니다.
4. 냉각
체류 후 금형이 채워지지만 금형에서 제거하기에는 여전히 너무 뜨거울 수 있습니다. 따라서 성형업체는 금형이 플라스틱에서 열을 흡수하는 데 일정 시간을 할당합니다. 성형기는 열가소성 수지 재료의 충분하고 균일한 냉각을 유지해야 합니다. 그렇지 않으면 최종 제품이 뒤틀릴 위험이 있습니다.
5. 금형 개봉
금형 사출기의 가동판이 열립니다. 일부 금형에는 공기 분사 제어 또는 코어 당김 기능이 있으며 성형기는 부품을 보호하면서 금형을 여는 데 사용되는 힘의 수준을 제어합니다.
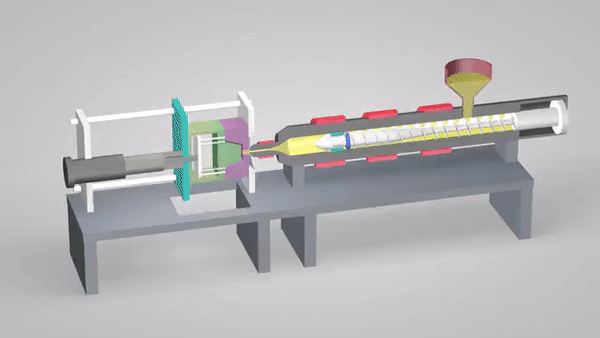
6. 부품 제거
최종 제품은 배출 시스템, 막대 또는 로봇의 펄스로 사출 금형에서 배출됩니다. 금형 표면의 나노 이형 코팅은 취출 중에 찢어지거나 찢어지는 것을 방지합니다.
공정 문제로 인한 일반적인 성형 결함
다음과 같은 사출 성형과 관련된 몇 가지 성형 결함이 있습니다.
뒤틀림: 뒤틀림은 부품이 고르지 않게 수축될 때 발생하는 변형입니다. 의도하지 않게 구부러지거나 뒤틀린 모양으로 나타납니다.
분사 : 열가소성 수지가 너무 느리게 주입되어 캐비티가 가득 차기 전에 굳기 시작하면 최종 제품이 분사될 수 있습니다. 분사는 부품 표면에 물결 모양의 제트 기류처럼 보입니다.
싱크 마크: 이는 불균일한 냉각으로 인해 발생하는 표면 움푹 들어간 곳이거나 성형기가 부품이 냉각될 충분한 시간을 허용하지 않아 재료가 안쪽으로 수축되는 경우에 발생합니다.
웰드 라인: 이들은 일반적으로 구멍이 있는 부품 주위에 형성되는 가는 선입니다. 녹은 플라스틱이 구멍 주위를 흐르면서 두 흐름이 만나지만 온도가 적절하지 않으면 흐름이 제대로 접착되지 않습니다. 그 결과 용접선이 생겨 최종 부품의 내구성과 강도가 감소합니다.
배출 마크: 부품이 너무 일찍 또는 과도한 힘으로 배출되면 이젝터 로드가 최종 제품에 자국을 남길 수 있습니다.
진공 보이드: 부품 표면 아래에 에어 포켓이 갇히면 진공 보이드가 발생합니다. 부품의 내부 섹션과 외부 섹션 사이의 고르지 않은 응고로 인해 발생합니다.
DJmolding의 사출 성형 서비스
대용량 맞춤형 사출성형 전문업체인 디제이몰딩은 13년의 사출성형 경력을 가지고 있습니다. DJmolding이 설립된 이래로 고객에게 최고 품질의 사출 성형 부품을 제공하기 위해 최선을 다해 왔습니다. 오늘날 우리의 불량률은 백만분의 일 미만입니다.