플라스틱 사출 성형의 기초
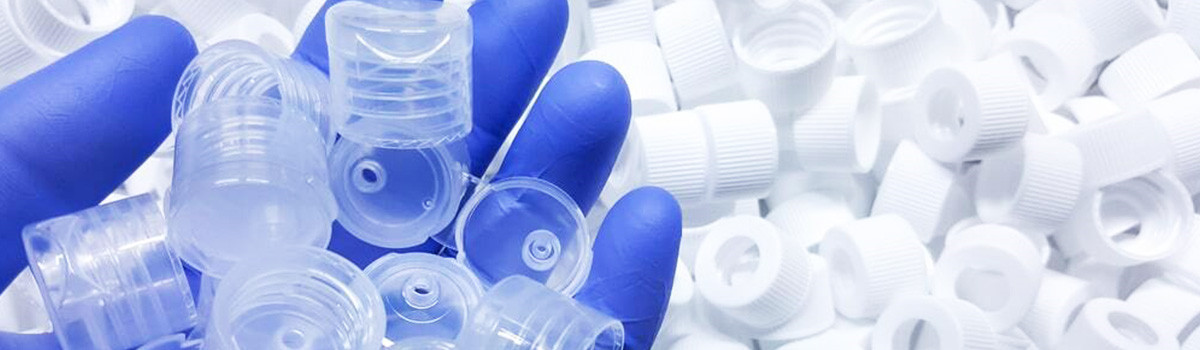
사출 성형 공정과 작동 방식을 살펴보십시오.
플라스틱 사출 성형은 열가소성 펠릿을 대량의 복잡한 부품으로 변환하는 널리 사용되는 제조 기술입니다. 사출 성형 공정은 다양한 플라스틱 재료에 적합하며 휴대폰 케이스, 전자 하우징, 장난감, 심지어 자동차 부품까지 현대 생활의 필수 요소입니다. 이 기사에서는 사출 성형의 기본 사항을 분석하고 사출 성형 작동 방식을 설명하며 3D 인쇄와 어떻게 다른지 설명합니다.
플라스틱 사출 성형의 기본은 무엇입니까?
플라스틱 사출 성형 공정의 기본에는 제품 디자인 생성, 제품 디자인에 맞는 금형 제작, 플라스틱 수지 펠릿 용융 및 압력을 사용하여 용융된 펠릿을 금형에 주입하는 것이 포함됩니다.
아래 각 단계의 분석을 참조하십시오.
1. 제품 디자인 만들기
설계자(엔지니어, 금형 제작자 등)는 사출 성형 프로세스에 특정한 기본 설계 지침에 따라 부품(CAD 파일 또는 기타 전송 가능한 형식)을 생성합니다. 설계자는 설계에 다음 기능을 포함하여 플라스틱 사출 금형의 성공률을 높여야 합니다.
*나사 인서트/패스너용 보스
* 일정하거나 거의 일정한 벽 두께
* 가변 벽 두께 사이의 부드러운 전환
*두꺼운 섹션의 중공 캐비티
*둥근 모서리
* 수직 벽의 기울기 각도
*지지용 갈비뼈
*Friction fit, 스냅핏 조인트 및 기타 비 패스너 결합 기능
*살아있는 경첩
또한 설계자는 설계 결함을 줄이기 위해 다음 기능을 최소화해야 합니다.
*균일하지 않은 벽 두께 또는 특히 얇은/두꺼운 벽
*구배 각도가 없는 수직 벽
*급격한 기하학적 변화(모서리, 구멍 등)
*잘못 설계된 늑골
*언더컷/오버행
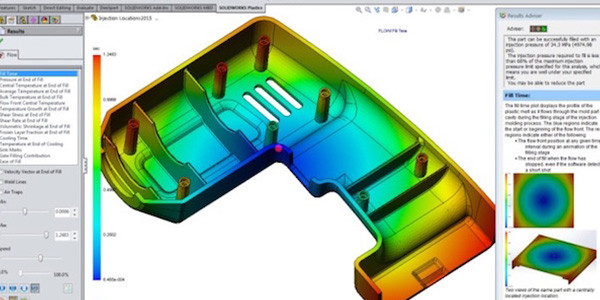
2. 제품 디자인에 맞는 툴링 몰드 만들기
고도로 숙련된 기계공과 공구 제작자가 제품 설계를 사용하여 사출 성형기용 금형을 제작합니다. 툴링 몰드(단순히 툴이라고도 함)는 사출 성형기의 심장이자 영혼입니다. 제품 설계를 위한 네거티브 캐비티와 스프루, 러너, 게이트, 통풍구, 이젝터 시스템, 냉각 채널 및 이동 부품과 같은 추가 기능을 포함하도록 세심하게 설계되었습니다. 툴링 금형은 6063 알루미늄, P20 강철, H13 강철 및 420 스테인리스강과 같이 수만(때로는 수십만)의 가열 및 냉각 주기를 견딜 수 있는 특정 등급의 강철 및 알루미늄으로 만들어집니다. 금형 제작 공정은 제작 및 승인을 포함하여 완료하는 데 20주 이상이 걸리므로 이 단계는 사출 성형의 가장 확장된 측면입니다. 사출성형에서 가장 고가 부품이기도 하며, 일단 툴링 금형을 제작하면 추가 비용을 들이지 않고는 대폭 변경이 불가능하다.
3. 플라스틱 수지 펠렛 녹이기
작업자가 완성된 금형을 얻은 후 사출 성형기에 삽입하고 금형이 닫히면 사출 성형 주기가 시작됩니다.
플라스틱 과립은 호퍼와 배럴에 공급됩니다. 왕복 나사가 뒤로 당겨져 재료가 나사와 배럴 사이의 공간으로 미끄러질 수 있습니다. 그런 다음 스크류가 앞으로 튀어 나와 재료를 배럴 안으로 밀어 넣고 용융 플라스틱으로 녹는 히터 밴드에 더 가깝게 만듭니다. 용융 온도는 재료 사양에 따라 일정하게 유지되므로 배럴이나 금형 자체에서 품질 저하가 발생하지 않습니다.
4. 압력을 사용하여 녹은 펠릿을 금형에 주입
왕복 나사는 금형 스프루 부싱으로 알려진 금형의 오목한 부분에 안착된 노즐을 통해 이 녹은 플라스틱을 밀어냅니다. 움직이는 압반 압력은 금형과 노즐을 단단히 결합하여 플라스틱이 빠져나가지 않도록 합니다. 용융된 플라스틱은 이 공정에 의해 가압되어 금형 캐비티의 모든 부분으로 들어가고 금형 통풍구를 통해 캐비티 공기를 배출합니다.
사출 성형기 구성 요소
사출 성형기의 구성 요소에는 호퍼, 배럴, 왕복 나사, 히터, 가동 플래튼, 노즐, 금형 및 금형 캐비티가 포함됩니다.
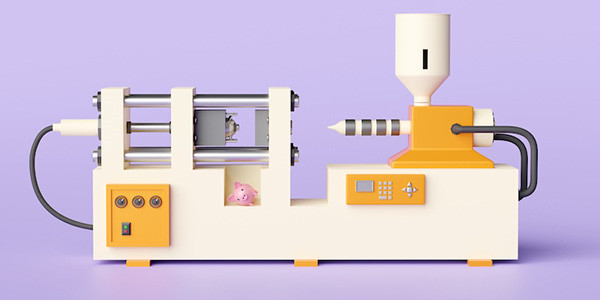
아래 목록의 각 사출 성형 구성 요소에 대한 추가 정보:
*홉 따는 기계: 플라스틱 알갱이가 기계에 공급되는 개구부.
*통: 왕복 나사와 플라스틱 과립을 포함하는 사출 성형기의 외부 하우징. 배럴은 여러 개의 히터 밴드로 둘러싸여 있으며 가열된 노즐로 기울어져 있습니다.
* 왕복 나사: 배럴을 통해 녹을 때 플라스틱 재료를 운반하고 가압하는 코르크 스크류 구성 요소.
*히터: 가열 밴드라고도 하는 이 구성 요소는 플라스틱 알갱이에 열 에너지를 제공하여 고체 형태에서 액체로 바꿉니다. 형태.
*움직일 수 있는 플래튼: 몰드 코어에 연결된 움직이는 구성 요소로 압력을 가하여 두 몰드 절반을 밀폐 상태로 유지하고 완성된 부품이 드러날 때 몰드 코어를 해제합니다.
*대통 주둥이: 온도와 압력을 가능한 한 안정적으로 유지하면서 금형 캐비티에 녹은 플라스틱을 위한 표준 배출구를 제공하는 가열된 부품.
*곰팡이: 금형 캐비티와 이젝터 핀, 러너 채널, 냉각 채널, 통풍구 등과 같은 추가 지원 기능을 포함하는 구성 요소 또는 구성 요소. 최소한 금형은 고정면(배럴에 더 가까운)과 금형의 두 부분으로 분리됩니다. 코어(움직이는 플래튼 위).
*금형 캐비티: 녹은 플라스틱으로 채울 때 원하는 최종 부품과 지지대, 게이트, 러너, 스프루 등으로 성형되는 네거티브 공간입니다.
사출 성형은 어떻게 작동합니까?
플라스틱이 스프루, 러너, 게이트 등을 포함하여 금형을 채운 후에는 재료가 부품 형태로 균일하게 응고될 수 있도록 금형을 설정 온도로 유지합니다. 배럴로의 역류를 중지하고 수축 효과를 줄이기 위해 냉각하는 동안 보압이 유지됩니다. 이 시점에서 다음 주기(또는 샷)를 예상하여 더 많은 플라스틱 알갱이가 호퍼에 추가됩니다. 냉각되면 플래튼이 열리고 완성된 부품을 배출할 수 있으며 스크류가 다시 한 번 뒤로 당겨져 재료가 배럴에 들어가고 프로세스를 다시 시작할 수 있습니다.
사출 성형 주기는 금형 닫기, 플라스틱 알갱이 공급/가열, 금형에 가압, 고체 부품으로 냉각, 부품 배출 및 금형 다시 닫기와 같은 연속 프로세스로 작동합니다. 이 시스템은 플라스틱 부품의 신속한 생산을 가능하게 하며 설계, 크기 및 재료에 따라 작업일에 10,000개 이상의 플라스틱 부품을 만들 수 있습니다.
Djmolding은 중국의 소량 사출 성형 회사입니다. 우리의 플라스틱 사출 성형 공정은 리드 타임이 1일, 연간 최대 10000개의 부품을 공급하는 맞춤형 프로토타입 및 최종 사용 생산 부품을 생산합니다.