플라스틱 사출성형 방법 및 제조공정을 단계별로 설명
플라스틱 사출성형 방법 및 제조공정을 단계별로 설명
지난 50년간 플라스틱 소재산업은 기초소재를 압도하고 심지어 철강산업을 능가할 만큼 엄청난 규모로 발전했다. 플라스틱은 모든 경제에서와 마찬가지로 가장 먼 곳과 산업화된 국가를 포함한 모든 도시에서 사회적 지위에 관계없이 모든 가정에 들어왔습니다. 이 산업의 발전은 매우 흥미롭고 우리가 살고 있는 세상의 방식을 변화시켰습니다.
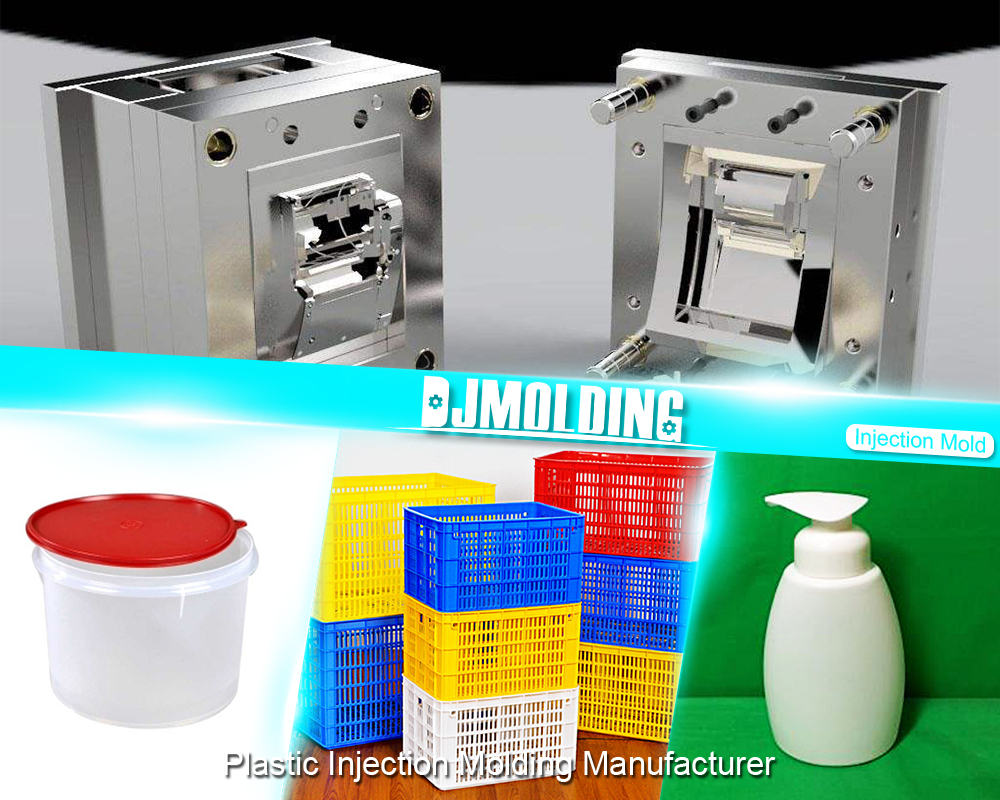
사출 성형 공정
플라스틱 화합물은 서로 크게 다르며 다양한 가공 방법에 적합합니다. 각 재료는 여러 가지 방법으로 제조할 수 있지만 여러 가지 방법 중 하나에 더 적합합니다. 대부분의 공정에서 성형 재료는 분말 또는 과립 형태이지만, 일부 공정에서는 사용 전에 예비 사전 성형 작업이 수행됩니다. 열가소성 물질에 열을 가해 녹이면 가소화된다고 합니다. 이미 용융되었거나 열적층된 재료는 압력을 가하고 재료가 응고되어 금형의 모양을 취하는 금형을 채워 유동하게 만들 수 있습니다. 이 과정은 다음과 같이 알려져 있습니다. 사출 성형. 사출 성형의 기본 원리는 다음 세 가지 기본 작업으로 구성됩니다.
- a) 압력을 가하면 플라스틱이 흐를 수 있는 지점까지 플라스틱의 온도를 높입니다. 이는 일반적으로 재료의 고체 과립을 가열하고 씹어 균일한 점도와 온도로 용융물을 형성함으로써 수행됩니다. 현재 이 작업은 배럴의 열과 함께 플라스틱을 녹이는(가소화) 기계적 작업(마찰)을 제공하는 나사를 통해 기계 배럴 내부에서 수행됩니다. 즉, 스크류는 플라스틱 재료를 운반, 혼합 및 가소화합니다. 이는 그림에 나와 있습니다.
- b) 닫힌 금형에서 재료가 응고되도록 합니다. 이 단계에서 기계 배럴에 이미 적층된 용융 재료는 노즐을 통해 전달(사출)되며, 노즐은 최종 제품의 모양을 취하는 공동에 도달할 때까지 배럴을 금형의 다양한 채널에 연결합니다.
- c) 조각 추출을 위해 금형을 엽니다. 이는 금형 내부에서 재료에 압력을 가한 후 열(가소화를 위해 가해진 열)을 제거하여 재료가 원하는 방식으로 응고되도록 한 후에 수행됩니다.
다양한 성형 절차에서 용융 또는 가소화 온도의 변화는 열가소성 재료인지 열 고정성인지에 따라 다른 역할을 합니다.
의 융합 열가소성 물질 재료는 통제된 조건 하에서 가소화 실린더에서 점진적으로 수행됩니다. 가소화 실린더에 의해 제공되는 외부 가열은 재료를 회전하고 혼합하는 스핀들의 마찰로 인해 발생하는 열을 추가합니다. 가소화 실린더의 다양한 구역의 온도 제어는 호퍼에서 노즐까지 재료 경로를 따라 다양한 지점에 삽입된 열전대를 통해 수행됩니다. 열전대는 각 구역의 온도를 미리 설정된 수준으로 유지하는 자동 제어 장치에 연결됩니다. 그러나 금형에 주입되는 용융물의 실제 온도는 실린더나 노즐의 열전대에 의해 기록된 온도와 다를 수 있습니다.
따라서 재료의 온도는 절연판 위에 노즐을 통해 소량의 재료가 나오도록 하여 바로 그 자리에서 측정하는 것이 바람직하다. 금형의 온도 변화에 따라 품질이 다양하고 치수가 다양한 부품이 생산될 수 있으며, 작동 온도가 분리될 때마다 금형 캐비티에 주입된 용융 물질이 더 빠르게 또는 더 느리게 냉각됩니다. 금형 온도가 낮아지면 성형 부품이 더 빨리 냉각되어 구조의 방향이 뚜렷해지고 내부 응력이 높아지며 기계적 특성이 낮아지고 표면 외관이 나빠질 수 있습니다.
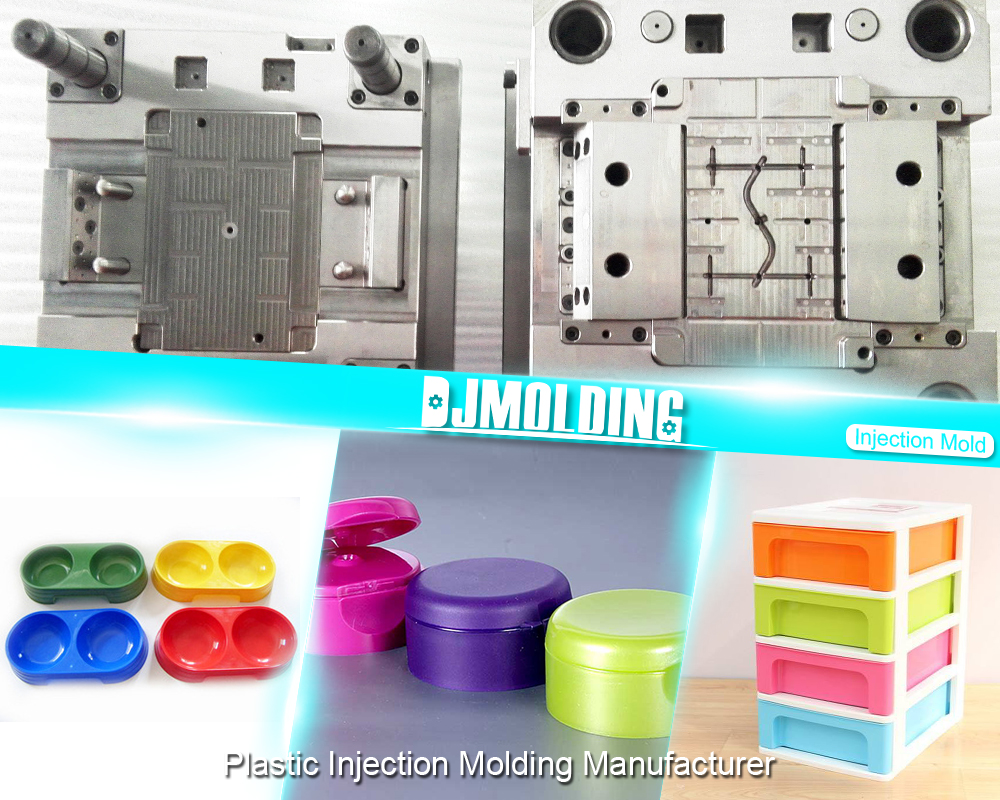
설명에 대한 자세한 내용은 플라스틱 사출 성형 방법 및 제조 공정을 단계별로 확인하려면 Djmolding을 방문하세요. https://www.djmolding.com/ 자세한 정보입니다.