Термопластично вбризгување калапи
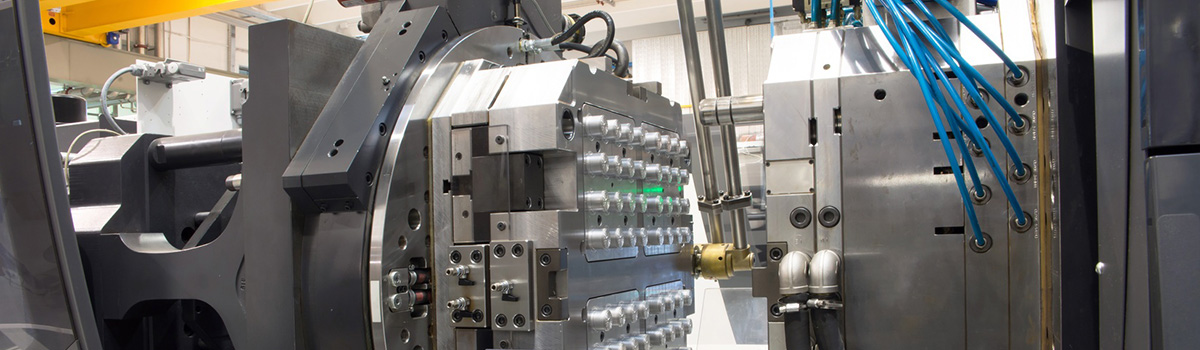
Термопластичното вбризгување е популарен производствен процес кој се користи за создавање на различни пластични делови за повеќе индустрии. Овој процес вклучува топење на пластични пелети и нивно вбризгување во калап за да се добие тродимензионална форма. Термопластичното вбризгување е високо ефикасно и исплатливо за производство на големи количини висококвалитетни пластични делови со тесни толеранции. Овој сеопфатен водич ќе ги истражи различните аспекти на обликувањето со термопластично вбризгување, вклучувајќи ги неговите предности и недостатоци, типовите на користени термопластики, процесот на обликување со вбризгување, размислувањата за дизајнирање и многу повеќе.
Историја на термопластично вбризгување калапи
Историјата на термопластичното вбризгување опфаќа повеќе од еден век технолошки напредок, материјален развој и индустриски апликации. Од своите скромни почетоци како процес на обликување на целулоид до денешна софистицирана технологија, обликувањето со инјектирање продолжува да биде витална техника за производство, поттикнувајќи ги иновациите и обликувајќи различни индустрии.
- Рани случувања:Џон Весли Хајат и неговиот брат Исаја ја развиле првата практична машина за обликување со вбризгување, следејќи го потеклото на термопластичното вбризгување до крајот на 19 век. Во 1872 година, тие патентирале уред кој користел клип за инјектирање на целулоид во шуплината на мувла, создавајќи цврсти предмети. Овој пробив ги постави темелите за модерниот процес на обликување со инјектирање.
- Напредокот во материјалите:Во почетокот на 20 век, воведувањето на нови синтетички полимери отвори нови можности за обликување со инјектирање. Бакелит, фенолна смола, стана популарен материјал за обликување поради неговите одлични електрични изолациски својства. Во текот на 1930-тите и 1940-тите, напредокот во полимерната хемија доведе до развој на други термопластики, како што се полистирен и полиетилен, кои дополнително го проширија опсегот на материјали погодни за обликување со инјектирање.
- Индустриско усвојување: Широкото усвојување на термопластично вбризгување калапи започна во 1950-тите, бидејќи производителите ја препознаа неговата исплатливост и разноврсност. Воведувањето машини под висок притисок овозможи побрзо време на циклусот и зголемен обем на производство. Како резултат на тоа, се појави разновиден избор на производи и за лична и за индустриска употреба. Тие вклучуваат компоненти за автомобил, домашни апарати и играчки.
- Технолошки иновации:Со текот на децениите, технологијата за обликување со инјектирање продолжи да се развива. Во 1960-тите, се појавија машини контролирани од компјутер, што овозможија прецизна контрола врз процесот на обликување. Воведувањето на системи за жешки тркачи во 1980-тите го намали отпадот и ја подобри ефикасноста со елиминирање на потребата од тркачи и прскалки. Во последниве години, напредокот во автоматизацијата, роботиката и 3D печатењето дополнително ја револуционизираа индустријата за обликување со инјектирање, овозможувајќи сложени дизајни и намалување на времето за производство.
- Одржливост и рециклирање:Со растечките грижи за животната средина, индустријата за лиење со вбризгување ги прифати мерките за одржливост. Производителите развија био-базирана и рециклирана термопластика, намалувајќи ја зависноста од материјалите базирани на фосилни горива. Дополнително, подобрените технологии за рециклирање овозможија повторна обработка на отпадот по потрошувачка и пост-индустриски, минимизирајќи го влијанието врз животната средина на термопластичното вбризгување.
- Идни изгледи:Иднината на термопластичното вбризгување изгледа ветувачка. Индустријата истражува иновации како што се обликување со микро вбризгување за минијатурни компоненти, техники на мулти-материјал и преливање за сложени делови и интегрирање на интелигентни технологии за следење и оптимизација на процесите. Понатаму, истражувачите очекуваат напредокот во биоразградливите материјали и производството на адитиви да го револуционизира полето, правејќи го обликувањето со инјектирање уште поодржливо и разноврсно.
Предности на термопластично вбризгување калапи
Термопластичното вбризгување нуди бројни предности за производителите. Обезбедува флексибилност на дизајнот, овозможувајќи сложени и сложени дизајни со различни карактеристики. Процесот е економичен, намалувајќи го материјалниот отпад и намалувајќи ги единечните трошоци. Термопластичното обликување со вбризгување поддржува повеќе материјали, обезбедувајќи разновидност за различни апликации.
- Флексибилност на дизајнот:Термопластичното обликување со вбризгување овозможува сложени и сложени дизајни со карактеристики како што се подрез, тенки ѕидови и различни дебелини, обезбедувајќи им на дизајнерите огромна слобода.
- Ефикасност на трошоците: Процесот е многу ефикасен, го намалува материјалниот отпад и ги намалува единечните трошоци. Симултаното обликување на повеќе делови и брзите производни циклуси придонесуваат за заштеда на трошоците.
- Разновидност на материјалот: Термопластичното обликување со вбризгување поддржува широк спектар на материјали, овозможувајќи им на производителите да ја изберат најсоодветната опција за секоја апликација, вклучувајќи крути или флексибилни, транспарентни или непроѕирни и хемиски отпорни материјали.
- Јачина и издржливост:Термопластиката со вбризгување може да покаже одлични механички својства, како што се висока јачина, цврстина и отпорност на удар. Опциите за засилување, како што се стаклени или јаглеродни влакна, дополнително ги подобруваат овие својства.
- Конзистентност и квалитет:Калапот со вбризгување обезбедува постојан квалитет од дел до дел и прецизност на димензиите, обезбедувајќи тесни толеранции и сигурни производи. Процесот, исто така, обезбедува мазна и униформа завршна обработка на површината, елиминирајќи ја потребата од дополнителни завршни операции.
- Приспособливост и масовно производство:Калапот со инјектирање може да се скалира од мали до големи волумени, што го прави погодно за масовно производство. Откако производителите ќе го создадат калапот, тие можат да произведат големи количини идентични делови со минимални варијации.
- Интеграција и собрание:Деловите калапирани со инјектирање можат да вклучат повеќе компоненти во едно парче, намалувајќи ја потребата од дополнителни процеси на склопување. Оваа интеграција ги подобрува перформансите на производот, го намалува времето на склопување и ги намалува трошоците.
- Одржливост:Индустријата за обликување со инјектирање покажува зголемен фокус на одржливоста. Достапноста на био-базирани и рециклирани материјали овозможува производство на еколошки производи. Ефикасното користење на материјалот и рециклирањето на термопластиката придонесуваат за позелен производствен процес.
Овие придобивки го направија широко прифатен метод на производство во различни индустрии, обезбедувајќи висококвалитетни, економични и еколошки решенија за сложени барања за производи.
Недостатоци на термопластичното вбризгување
Додека термопластичното вбризгување нуди бројни предности, има и неколку недостатоци. Производителите треба внимателно да ги проценат овие фактори и да ги измерат во однос на придобивките за да ја одредат соодветноста на термопластичното вбризгување за нивните специфични апликации.
- Висока почетна инвестиција: Поставувањето на операција за обликување со термопластично вбризгување бара значителна почетна инвестиција во дизајнот и изработката на калапи и купување на специјализирани машини. Трошоците поврзани со создавање калапи и алатки може да бидат значителни, особено за сложени и сложени дизајни.
- Ограничувања на дизајнот: Додека обликувањето со термопластично вбризгување нуди флексибилност на дизајнот, постојат одредени ограничувања. На пример, постигнувањето униформа дебелина на ѕидот низ целиот дел може да биде предизвик, што доведува до варијации во дистрибуцијата на материјалите и потенцијални структурни слабости. Дополнително, присуството на поткопчиња или сложени геометрии може да бара употреба на дополнителни карактеристики на мувла или секундарни операции, зголемувајќи ги трошоците и времето на производство.
- Долг воден тајмс:Процесот на дизајнирање и изработка на калапи за обликување со инјектирање може да одземе многу време, што ќе доведе до подолго време за развој на производот. Процесот на повторување на дизајнот, производството на мувла и тестирањето може да додадат значително време на целокупната временска рамка за производство, што можеби не е погодно за проекти со тесни рокови.
- Ограничувања за избор на материјал:Иако обликувањето со термопластично вбризгување поддржува широк спектар на материјали, постојат одредени ограничувања и ограничувања. Некои материјали може да имаат специфични барања за обработка или ограничена достапност, што влијае на изборот на дизајнот и изборот на материјали за одредена апликација.
- Ограничувања на големината на делот:Машините за обликување со вбризгување имаат ограничувања во големината, како во однос на физичката големина на уредот, така и во однос на големината на калапите што можат да ги сместат. Производството на огромни делови може да бара специјализирана опрема или алтернативни методи на производство.
- Влијание врз животната средина:Додека индустријата работи на одржливост, процесот на обликување со термопластично вбризгување сè уште генерира отпаден материјал, вклучително и отпадоци и прскалки. Неопходно е правилно отстранување и рециклирање на овие материјали за да се минимизира влијанието врз животната средина.
- Комплексноста на оптимизацијата на процесите:Постигнувањето на оптимални процесни параметри за обликување со термопластично вбризгување може да биде сложено и одзема многу време. Производителите мора внимателно да ги контролираат и оптимизираат температурата, притисокот, стапките на ладење и времетраењето на циклусот за да обезбедат постојан квалитет на деловите и да ги минимизираат дефектите.
Видови термопластика што се користат во обликување со инјектирање
Ова се само неколку примери на термопластика што вообичаено се користи во обликувањето со инјектирање. Секој материјал има уникатни својства, што го прави погоден за специфични апликации засновани на сила, флексибилност, хемиска отпорност, транспарентност и цена. Производителите треба да ги земат предвид овие својства и барања при изборот на соодветна термопластика за нивните проекти за лиење со инјектирање.
- Полипропилен (PP):Полипропиленот е разноврсна термопластика која најчесто се користи во обликувањето со инјектирање. Тој нуди одлична хемиска отпорност, мала густина и добра сила на удар. PP (полипропилен) има широк опсег на апликации во пакување, автомобилски компоненти, апарати за домаќинство и медицински помагала.
- Полиетилен (PE):Полиетилен е уште еден широко користен термопластик во обликувањето со инјектирање. Достапен е во различни форми, како што се полиетилен со висока густина (HDPE) и полиетилен со мала густина (LDPE). PE нуди добра хемиска отпорност, цврстина и флексибилност, што го прави погоден за шишиња, контејнери и цевки.
- Полистирен (PS):Полистиренот е разноврсна термопластика позната по својата јасност, цврстина и достапност. Наоѓа вообичаена употреба во пакувањето, стоките за широка потрошувачка и производите за еднократна употреба. PS (полистирен) овозможува брза обработка и обезбедува добра димензионална стабилност, но може да биде кршлив и подложен на пукање од еколошки стрес.
- Акрилонитрил бутадиен стирен (ABS): ABS е популарна термопластика позната по одличната отпорност на удар и издржливост. Ги комбинира својствата на акрилонитрил, бутадиен и стирен за да создаде разновиден материјал погоден за автомобилски делови, електронски куќишта и играчки.
- Поливинил хлорид (ПВЦ): ПВЦ е широко употребувана термопластика позната по својата одлична хемиска отпорност, издржливост и ниска цена. Може да биде крут или флексибилен во зависност од формулацијата и употребените адитиви. ПВЦ (поливинил хлорид) наоѓа вообичаена употреба во градежништвото, електричната изолација, здравствените производи и пакувањето.
- Поликарбонат (компјутер): Поликарбонатот е проѕирна термопластика со извонреден удар и висока отпорност на топлина. Наоѓа вообичаена употреба во апликации кои бараат оптичка јасност, како што се автомобилски компоненти, безбедносни шлемови и електронски дисплеи.
- Најлон (полиамид):Најлон е силна и издржлива термопластика позната по своите одлични механички својства и хемиска отпорност. Наоѓа вообичаена употреба во апликации кои бараат висока јачина, како што се автомобилски делови, индустриски компоненти и производи за широка потрошувачка.
- Полиетилен терефталат (ПЕТ):ПЕТ е популарна термопластика за производство на шишиња, контејнери и материјали за пакување. Тој нуди добра јасност, хемиска отпорност и бариерни својства, што го прави погоден за апликации за храна и пијалоци.
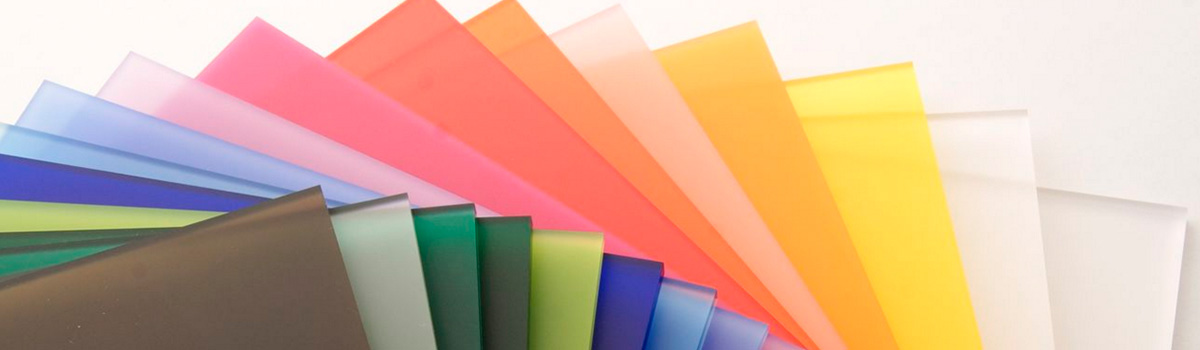
Својства на термопластиката што се користи во обликувањето со инјектирање
Овие својства на термопластиката играат клучна улога во одредувањето на нивната соодветност за специфични апликации за обликување со инјектирање. Производителите мора внимателно да ги разгледаат овие својства и да изберат соодветна термопластика врз основа на саканите перформанси, условите на животната средина и барањата за трошоци.
- Механички својства:Термопластиката што се користи во обликувањето со инјектирање може да покаже различни механички својства, вклучително и цврстина на истегнување, отпорност на удар и цврстина на виткање. Овие својства ја одредуваат способноста на материјалот да ги издржи применетите сили и неговата севкупна издржливост во различни примени.
- Хемиска отпорност:Многу термопластики што се користат во обликувањето со инјектирање имаат извонредна отпорност на хемикалии, растворувачи и масла. Ова својство е клучно за апликации кои вклучуваат изложеност на сурови средини или корозивни материи.
- Термичка стабилност:Термичката стабилност на термопластиката се однесува на нивната способност да издржат покачени температури без значително деградирање. Некои термопластики покажуваат одлична отпорност на топлина, што им овозможува да ги задржат своите механички својства дури и при високи температури.
- Електрични својства:Термопластиката што се користи во обликувањето со инјектирање може да има специфични електрични својства, вклучително и електрична изолација, спроводливост или диелектрична сила. Овие својства се од суштинско значење за апликации во електричната и електронската индустрија, каде што материјалите мора да обезбедат сигурни електрични перформанси.
- Транспарентност и јасност:Одредени термопластики, како што се поликарбонат и PET, нудат одлична транспарентност и јасност, што ги прави погодни за апликации кои бараат оптички својства. Производителите најчесто ги користат овие материјали во производи како што се проѕирни прозорци, леќи и дисплеи.
- Флексибилност и цврстина: Флексибилноста и цврстината се основните својства на термопластиката што се користи во апликации кои бараат отпорност на удар и издржливост. Некои термопластики, како што се ABS и најлон, нудат одлична цврстина, овозможувајќи им да издржат повторени удари без да се скршат.
- Димензионална стабилност:Стабилноста на димензиите се однесува на способноста на термопластиката да ја одржува својата форма и големина под различни услови, вклучително и температурни промени. Материјалите со добра димензионална стабилност обезбедуваат конзистентни димензии на делот, минимизирајќи го ризикот од искривување или изобличување.
- Хемиска компатибилност:Хемиската компатибилност на термопластиката се однесува на нивната способност да се спротивстават на деградација или интеракција со различни хемикалии, вклучувајќи киселини, бази и растворувачи. За да се обезбедат оптимални перформанси, од суштинско значење е изборот на термопластика што може да ја издржи специфичната хемиска средина со која ќе се сретне при планираната апликација.
- Густина: Термопластиката имаат различни дебелини, што може да влијае на нивната тежина и севкупните својства на делот. Материјалите со мала густина, како што е полиетиленот, нудат лесни решенија, додека материјалите со висока густина, како што е полипропиленот, обезбедуваат дополнителна цврстина и цврстина.
Процес на вбризгување: чекор-по-чекор
Процесот на обликување со вбризгување ги следи овие чекори, овозможувајќи ефикасно и прецизно производство на висококвалитетни термопластични делови. Секој чекор бара внимателна контрола и мониторинг за да се обезбедат конзистентни димензии на делови, својства на материјалот и севкупен квалитет.
- Дизајн и изработка на мувла: Првиот чекор во процесот на обликување со инјектирање е дизајнот и изработката на калапот. Производителите мора да создадат прецизен и детален дизајн на мувла за да ги постигнат посакуваните спецификации на делот. Производителите потоа го произведуваат калапот користејќи различни техники, како што се CNC или обработка со електрично празнење (EDM).
- Подготовка на материјалот: Следниот чекор е подготовка откако калапот е подготвен. Термопластични пелети или гранули се избираат врз основа на саканите својства на материјалот и се топат во бункер. Операторите потоа го внесуваат материјалот во бурето на машината за вбризгување, каде што се топи и хомогенизира.
- Инјекција:За време на фазата на инјектирање, операторите ја инјектираат стопената термопластика во шуплината на мувлата под висок притисок. Единицата за вбризгување на машината го турка стопениот материјал низ млазницата и во калапот. Материјалот ја исполнува шуплината на мувлата, земајќи го обликот на саканиот дел.
- Ладење и зацврстување:По полнењето на калапот, операторите дозволуваат стопената пластика да се олади и зацврсти. Ладењето е клучно за постигнување димензионална стабилност и правилно формирање на делови. Операторите можат да го контролираат процесот на ладење со циркулирање на течноста за ладење низ каналите во калапот или со користење на плочи за ладење.
- Отворање и исфрлање на мувла:Операторите го отвораат калапот и го исфрлаат делот од шуплината на мувлата откако пластиката ќе се зацврсти. Системот за исфрлање во машината користи иглички, плочи за исфрлање или воздушни експлозии за да го отстрани регионот од калапот. Калапот потоа е подготвен за следниот циклус на инјектирање.
- Постобработка: По исфрлањето, делот може да претрпи операции по обработката, како што се отсекување, бришење или завршна површина. Овие чекори помагаат да се отстрани вишокот материјал, да се изедначат грубите рабови и да се подобри конечниот изглед на делот.
- Инспекција за квалитет: Последниот чекор вклучува проверка на инјектираните делови за квалитет и обезбедување дека ги исполнуваат наведените барања. Различни техники за контрола на квалитетот, вклучувајќи мерење на димензии, визуелна инспекција и функционално тестирање, може да се применат за да се потврди квалитетот и интегритетот на делот.
- Рециклирање и повторна употреба на материјали:Секој вишок или отпаден материјал создаден за време на обликувањето со инјектирање може да се рециклира и повторно да се користи. Намалувањето на употребата на нов термопластичен материјал помага да се минимизира отпадот и да се подобри одржливоста.
Опрема што се користи во обликување со вбризгување
Овие компоненти на опремата го олеснуваат процесот на вбризгување, од топење и вбризгување на термопластичниот материјал до обликување, ладење и исфрлање на завршниот дел. Правилната работа и одржувањето на овие компоненти на опремата се клучни за постигнување на ефикасно, висококвалитетно производство на калапи со вбризгување.
- Машина за вбризгување:Примарната опрема во обликувањето со инјектирање е одговорна за топење на термопластичниот материјал, негово вбризгување во калапот и контролирање на процесот.
- Мувла: Калапот, прилагодено дизајниран да ја создаде саканата форма и карактеристики на пластичниот дел, се состои од две половини, шуплината и јадрото. Операторите го монтираат на единицата за стегање на машината за вбризгување.
- Бункер:Контејнер што го чува термопластичниот материјал во форма на пелети или зрнеста форма и го внесува во бурето на машината за вбризгување за топење и вбризгување.
- Буре и завртка: Бурето, цилиндрична комора, го топи и хомогенизира термопластичниот материјал додека завртката се ротира во него за да се стопи, измеша и стандардизира материјалот.
- Системи за греење и ладење:Машините за обликување со вбризгување имаат грејни елементи, како што се електрични грејачи или грејачи кои користат врело масло, за да ја подигнат температурата на бурето, и системи за ладење, како што се циркулација на вода или масло, за ладење на мувлата и зацврстување на пластичниот дел.
- Систем за исфрлање:Го отстранува обликуваниот дел од шуплината на мувлата по зацврстувањето, вообичаено користејќи иглички, плочи или воздушни експлозии за време на отворањето на мувлата.
- Систем за контрола:Набљудува и контролира различни параметри на процесот на вбризгување, овозможувајќи им на операторите да поставуваат и приспособат параметри како што се брзината на вбризгување, температурата, притисокот и времето на ладење.
Машини за вбризгување: Видови и карактеристики
Секој тип на машина за вбризгување има свои карактеристики и предности, што им овозможува на производителите да го изберат најсоодветен уред за нивните специфични производствени барања.
- Машини за хидраулично вбризгување: Овие машини користат хидраулични системи за генерирање на потребниот притисок за инјектирање стопена пластика во калапот. Тие се познати по нивната висока сила на стегање, прецизна контрола и разноврсност при ракување со различни термопластики. Хидрауличните машини се погодни за производство во големи размери и можат да сместат сложени калапи.
- Електрични машини за калапи со вбризгување:Електричните машини користат електрични серво мотори за работа на машината, вклучувајќи ги и системите за вбризгување, стегање и исфрлање. Тие нудат прецизна контрола, енергетска ефикасност и побрзо време на одговор од хидрауличните машини. Електричните машини се идеални за апликации за прецизно обликување кои бараат голема повторливост и точност.
- Хибридни машини за вбризгување:Хибридните машини ги комбинираат придобивките и од хидрауличните и од електричните уреди. Тие користат комбинација од хидраулични и електрични серво системи за да постигнат висока прецизност, енергетска ефикасност и исплатливост. Хибридните машини се погодни за широк опсег на апликации, обезбедувајќи рамнотежа помеѓу перформансите и оперативните трошоци.
- Машини за вбризгување со две плочи: Машините со две плочи имаат уникатен дизајн со две посебни плочи за стегање на калапот. Овој дизајн обезбедува зголемена стабилност, подобрена синхронизација на мувлата и овозможува поголеми димензии на калапи и поголеми сили на стегање. Машините со две плочи се погодни за големи и сложени делови кои бараат прецизно обликување.
- Повеќекомпонентни машини за вбризгување:Производителите ги дизајнираат овие машини за да произведуваат делови со повеќе материјали или бои во еден циклус на обликување. Имаат различни единици и калапи за инјектирање, што овозможува истовремено вбризгување на различни материјали. Повеќекомпонентните машини нудат флексибилност и ефикасност во производството на сложени делови со различни карактеристики.
- Машини за обликување со микро-инјектирање:Специфично дизајнирани за производство на мали и прецизни делови, машините за обликување со микро вбризгување нудат неверојатно висока прецизност и точност. Тие можат да произведат сложени детали со тесни толеранции и минимален материјален отпад. Електрониката, медицинските уреди и микрооптиката најчесто користат машини за обликување со микро-инјектирање.
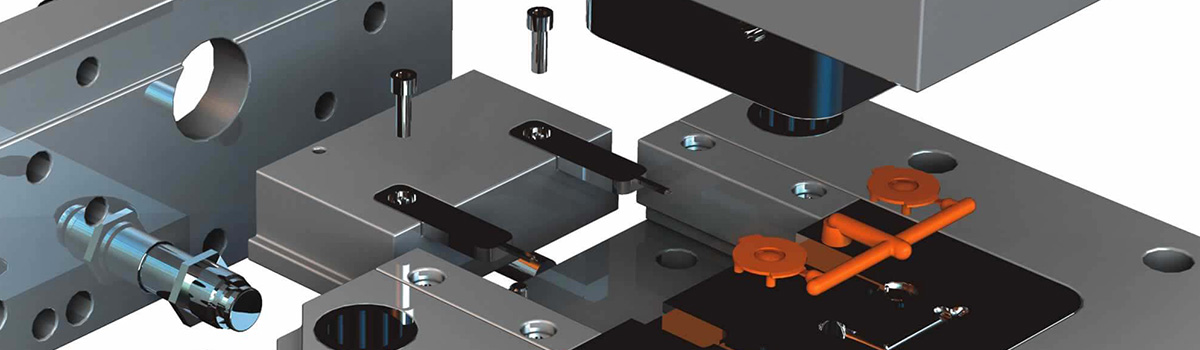
Размислувања за дизајн на мувла за вбризгување
Внимателните размислувања за дизајнот на мувлата се од суштинско значење за успешно производство на калапи со инјектирање.
- Дизајн на делови:Дизајнот на калапот треба да одговара на специфичните барања на делот, вклучувајќи ја неговата форма, димензии и функционални карактеристики. Производителите треба правилно да ги земат предвид аглите на влечење, дебелината на ѕидот, поткопчињата и сите неопходни елементи за да обезбедат лесно исфрлање и квалитет на делот.
- Материјал за мувла: Изборот на материјалот за мувла е клучен за постигнување издржливост, димензионална стабилност и отпорност на топлина. Вообичаените материјали за мувла вклучуваат челични легури, алуминиумски легури и челици за алат. Изборот на материјал зависи од фактори како што се обемот на производството, сложеноста на делот и очекуваниот век на алатот.
- Систем за ладење:Ефикасното ладење е од суштинско значење за правилно зацврстување на делот и минимизирање на времето на циклусот. Дизајнот на калапот треба да вклучува канали за ладење или стратешки позиционирани влошки за да се обезбеди рамномерно ладење на мувлата. Правилното ладење го намалува ризикот од искривување, собирање и дефекти на делови.
- Вентилација:Потребно е соодветно проветрување за да се овозможи истекување на воздух и гасови за време на процесот на вбризгување. Недоволното проветрување може да доведе до замки за гас, траги од изгореници или нецелосно полнење на делови. Производителите можат да постигнат вентилација со вградување на жлебови за вентилација, иглички или други механизми во дизајнот на калапот.
- Систем за исфрлање:Дизајнот на мувлата треба да вклучува ефективен систем за исфрлање за безбедно и ефикасно отстранување на обликуваниот дел од шуплината на мувлата. Системот за исфрлање може да се состои од иглички за исфрлање, чаури или други механизми, стратешки поставени за да се избегне мешање во функцијата или критичните карактеристики.
- Дизајн на портата:Портата е местото каде што стопената пластика влегува во шуплината на мувлата. Дизајнот на портата треба да обезбеди правилно полнење на делови, да ги минимизира линиите на проток и да спречи предвремено замрзнување на материјалот. Стандардните дизајни на портите вклучуваат рабни порти, тунелски порти и системи за топла тркала, во зависност од барањата на делот и својствата на материјалот.
- Линија за разделба:Дизајнот на калапот треба да дефинира соодветна линија за разделба, која е линијата каде што се спојуваат двете половини од калапот. Правилното поставување на линијата за разделба обезбедува минимално несовпаѓање на блицот и линијата за разделба и го олеснува ефикасното склопување на калапот.
- Одржување и сервисирање на мувла: Производителите треба да размислат за леснотијата на одржување, поправка и сервисирање на мувла. Компонентите на мувлата треба да бидат лесно достапни за чистење, проверка и замена. Вградувањето на функции како влошки за брзо менување или модуларни дизајни на калапи може да ја подобри услужливоста на мувлата.
Материјали за мувла што се користат во обликување со инјектирање
Соработката со специјалисти за калапи материјали и разгледување на специфичните потреби на апликацијата за обликување може да помогне да се одреди најсоодветниот материјал за постигнување оптимални перформанси на мувла и квалитет на делови.
- Челични легури: Челичните легури, како што се челиците за алати (на пример, P20, H13) и нерѓосувачките челици, најчесто се користат за калапи за вбризгување поради нивната одлична издржливост, отпорност на топлина и отпорност на абење. Овие материјали можат да ги издржат високите температури и притисоци во процесот на обликување со вбризгување и нудат добра димензионална стабилност за производство на висококвалитетни делови.
- Алуминиумски легури:Алуминиумските легури, како што се 7075 и 6061, се лесни и нудат добра топлинска спроводливост, што ги прави погодни за калапи кои бараат ефикасно ладење. Производителите често користат алуминиумски калапи за прототипирање, производство со мал обем или апликации каде што намалувањето на тежината е критично. Сепак, алуминиумските калапи може да имаат помала издржливост во споредба со легурите на челик.
- Бакарни легури:Бакарните легури, како што е бакарот од берилиум, покажуваат висока топлинска спроводливост и добра обработливост. Тие се користат во калапи кои бараат одличен пренос на топлина за ефективно ладење. Бакарните легури можат да помогнат да се намалат времињата на циклусот со брзо отстранување на топлината од обликуваниот дел, што резултира со побрзо зацврстување.
- Челици за алат:Челиците за алати, вклучувајќи ги H13, S7 и D2, се дизајнирани за апликации со алатки со високи перформанси. Овие челици нудат комбинација од висока јачина, цврстина и отпорност на абење. Челиците за алати одговараат на калапи со голем обем на производство, абразивни материјали или тешки услови за обликување.
- Легури на никел:Легурите на никел, како што се Inconel и Hastelloy, се познати по нивната исклучителна отпорност на корозија, цврстина на висока температура и термичка стабилност. Производителите ги користат овие легури во калапи кои се справуваат со корозивни материјали или бараат отпорност на екстремни температури и агресивни средини за обликување.
- Композитни материјали:Композитните материјали, како што се армирана пластика или композити со метални влошки, повремено се користат за специфични апликации за обликување. Овие материјали нудат баланс на својства, како што се висока јачина, термичка стабилност и намалена тежина. Композитните калапи можат да бидат исплатливи алтернативи за специфични производствени барања.
Видови калапи за инјектирање
Калапот со инјектирање е разновиден и широко користен производствен процес за пластични делови.
- Калап со две плочи:Калапот со две плочи е најчестиот тип на мувла за инјектирање. Се состои од две плочи, шуплината плоча и основната плоча, кои се одвојуваат за да овозможат исфрлање на обликуваниот дел. Плочата на шуплината ја содржи шуплинската страна на калапот, додека јадрото ја сместува јадрото. Производителите користат калапи со две плочи за производство на широк спектар на делови поради нивниот релативно едноставен дизајн.
- Калап со три плочи:Калапот со три плочи е напредна верзија на калапот со две плочи. Вклучува дополнителна плоча, тркач или плоча со спру. Плочата за тркала создава посебен канал за шприцот, тркачите и портите, што овозможува полесно отстранување на обликуваниот дел. Производителите вообичаено користат калапи со три плочи за детали со сложени системи за затворање или кога е пожелно да се избегне остаток од портата на парчето.
- Мувла за топла тркач:Системот за тркач и портата се загрева во топли калапи за тркала, со што се елиминира потребата за зацврстување и повторно топење на материјалот во текот на секој циклус. Системот за топла тркала се состои од загреани колектори и млазници кои ја одржуваат стопената состојба на пластиката. Калапи за топла тркала нудат предности како што се намалено време на циклус, помал отпад од материјалот и подобрен квалитет на делови со минимизирање на остатоците од портата.
- Калап за ладен тркач: Калапи за ладни тркала имаат традиционален систем за тркала и порти каде што стопената пластика тече низ ладни тркачи кои се зацврстуваат со секој циклус. Операторите последователно ги отстрануваат зацврстените тркачи, што резултира со материјален отпад. Производителите обично користат сложени калапи за тркалачки калапи за производство со помал волумен или кога трошоците за материјали се помалку критични поради нивниот поедноставен дизајн.
- Вметнете мувла:Калапи за вметнување вметнуваат метални или пластични влошки во шуплината на калапот за време на калапот со инјектирање. Влошките може претходно да се стават во калапот или да се вметнат со автоматизирани процеси. Овој калап овозможува интегрирање на дополнителни компоненти или зајакнувачки елементи во обликуваниот дел, зголемувајќи ја неговата функционалност или сила.
- Overmold: Прекутирањето вклучува обликување на еден материјал преку друг, обично поврзување на цврста пластична подлога со помек еластомер или термопластика. Овој процес овозможува создавање делови со повеќе материјали или текстури во еден калап, обезбедувајќи подобрено држење, амортизирање или естетски карактеристики.
Фактори кои влијаат на трошоците за вбризгување
Разгледувањето на овие фактори може да им помогне на производителите да ги проценат и оптимизираат трошоците за обликување со вбризгување, обезбедувајќи рамнотежа помеѓу квалитетот, ефикасноста и економичноста за нивните специфични барања за производство.
- Комплексност на дел:Комплексноста на дизајнот на делот игра значајна улога во одредувањето на цената на калапи со инјектирање. Сложените геометрии, отсеците, тенки ѕидови или сложени карактеристики може да бараат дополнителни алатки, специјализирани калапи или подолги циклуси, зголемувајќи ги севкупните трошоци за производство.
- Избор на материјал:Изборот на термопластичен материјал влијае на цената на калапи со инјектирање. Различните материјали имаат различни цени по килограм, а факторите како што се достапноста на материјалот, својствата и барањата за обработка можат да влијаат на вкупните трошоци за материјалот.
- Алатка и дизајн на калапи: Почетните трошоци за алати и дизајн на мувла се значајни во трошоците за лиење со инјектирање. Факторите како што се сложеноста на мувлата, бројот на шуплини, големината на мувлата и материјалот од мувла придонесуваат за трошоците за алати и производство на мувла. Покомплексните калапи или калапи кои бараат напредни функции може да ја зголемат почетната инвестиција.
- Обем на производство: Обемот на производство директно влијае на цената по дел во обликувањето со инјектирање. Повисоките книги често резултираат со економии на обем, намалувајќи ги трошоците по дел. Спротивно на тоа, производствените серии со низок волумен може да предизвикаат повисоки трошоци поради поставувањето, алатките и материјалниот отпад.
- Време на циклус: Времето на циклусот, кое ги вклучува фазите на ладење и исфрлање, влијае на производниот капацитет и вкупните трошоци. Подолго време на циклус резултира со намалено производство и потенцијално повисоки цени. Оптимизирањето на дизајнот на мувлата, системот за ладење и параметрите на процесот може да го минимизира времето на циклусот и да ја подобри ефикасноста.
- Барања за квалитет:Строгите барања за квалитет или специфичните сертификати може да влијаат на цената на обликувањето со вбризгување. За да се исполнат точните толеранции, барањата за завршна обработка на површината или дополнителното тестирање може да бидат потребни други ресурси, процеси или инспекции, што ќе придонесе за вкупните трошоци.
- Секундарни операции:Ако обликуваните делови бараат пост-обработка, како што се склопување, бојадисување или дополнителни чекори за завршна обработка, овие операции може да го надополнат вкупниот трошок за обликување со вбризгување.
- Добавувач и локација:Изборот на добавувач на калапи за инјектирање и нивната локација може да влијае на трошоците. Трошоците за работна сила, режиските трошоци, логистиката и транспортните трошоци варираат врз основа на локацијата на добавувачот, што влијае на вкупните трошоци за производство.
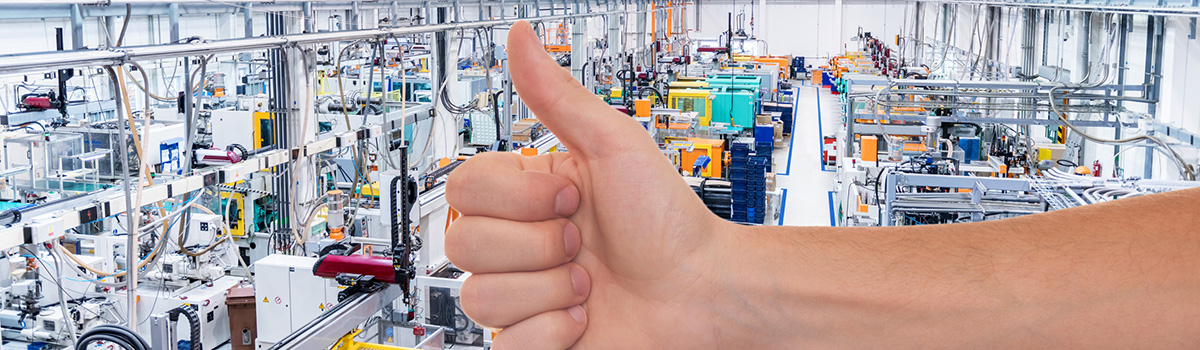
Контрола на квалитет во лиење со вбризгување
Спроведувањето робусни мерки за контрола на квалитетот во текот на процесот на вбризгување помага да се идентификуваат и да се решат потенцијалните дефекти, отстапувања или недоследности, обезбедувајќи производство на висококвалитетни делови што ги задоволуваат спецификациите и барањата на клиентите.
- Следење на процесот: Континуираното следење на клучните параметри на процесот, како што се температурата на топење, притисокот на вбризгување, времето на ладење и времето на циклусот, обезбедува конзистентност и повторливост во производството на делови. Мониторингот во реално време и автоматизираните системи можат да детектираат варијации или отстапувања од поставените параметри, овозможувајќи навремено прилагодување и одржување на стабилноста на процесот.
- Инспекција и мерење:Редовниот преглед и мерење на обликуваните делови се од суштинско значење за да се потврди точноста на димензиите, квалитетот на деловите и придржувањето кон спецификациите. Нашите услуги покриваат низа методи за контрола на квалитетот, како што се мерење димензии, анализа на квалитетот на површината, спроведување визуелни инспекции и изведување функционални тестови. Различни техники на инспекција, како што се машините за мерење на координати (CMM) и оптички и визуелни системи за инспекција, се користат за точна проценка.
- Статистичка контрола на процесите (СПЦ): SPC вклучува собирање и анализа на податоци за процесот за следење и контрола на квалитетот на обликувањето со вбризгување. Статистичките методи, како што се контролните графикони и анализата на способностите на процесот, помагаат да се идентификуваат трендовите, да се детектираат варијациите на процесот и да се осигура дека процесот останува во дефинираните контролни граници. SPC овозможува проактивна идентификација на проблемите и ја олеснува оптимизацијата на процесот.
- Тестирање на материјал: Тестирањето на суровините, како што се термопластика, адитиви и бои, обезбедува нивниот квалитет и соодветност за обликување со инјектирање. Тестирањето на материјалот може да вклучува анализа на индексот на проток на топење (MFI), механички својства, термички карактеристики и состав на материјалот. Потврдувањето на квалитетот на материјалот помага да се спречат дефекти и недоследности во обликуваните делови.
- Одржување и инспекција на алат:Правилното одржување и редовната проверка на калапите за вбризгување се од клучно значење за обезбедување квалитет во обликувањето со инјектирање. Редовното чистење, подмачкување и проценка на компонентите на мувла помагаат да се спречи абење, оштетување или деградација што може да влијае на квалитетот на деловите. Навремената поправка или замена на истрошените или оштетените компоненти на мувлата е од суштинско значење за одржување на постојани перформанси на калапот.
- Документација и следливост:Одржувањето сеопфатна документација и евиденција за следливост е од суштинско значење за контрола на квалитетот во обликувањето со инјектирање. Од витално значење е да се евидентираат параметрите на процесот, резултатите од инспекцијата, информациите за материјалот и сите промени или прилагодувања направени за време на производството. Соодветната документација овозможува следливост на деловите, ја олеснува анализата на основната причина и обезбедува конзистентност во квалитетот.
- Обука и развој на вештини: Обезбедувањето соодветна обука и програми за развој на вештини за операторите, техничарите и персоналот за контрола на квалитетот го подобрува нивното разбирање за процесите на обликување со вбризгување, барањата за квалитет и техниките на инспекција. Добро обучениот персонал може да открие дефекти, да решава проблеми и ефикасно да спроведе корективни мерки, обезбедувајќи висококвалитетно производство.
Вообичаени дефекти во калапи со вбризгување и како да ги избегнете
Редовната инспекција, следење и анализа на процесите на обликување со вбризгување и правилното одржување и прилагодување на опремата и калапи може да помогнат да се идентификуваат и да се решат овие вообичаени дефекти.
- Ознаки од мијалник:Трагите од мијалникот се вдлабнатини или вдлабнатини на површината на обликуваниот дел предизвикани од нерамномерно ладење или собирање. Треба да се земе предвид соодветна локација и дизајн на портата, оптимален дизајн на системот за ладење и рамномерна распределба на дебелината на ѕидот за да се избегнат траги од мијалникот. Зголемувањето на притисокот на вбризгување или прилагодувањето на времето на ладење, исто така, може да помогне да се минимизираат трагите од мијалникот.
- Warpage:Варењето се однесува на деформација или свиткување на обликуваниот дел по исфрлањето поради нерамномерно ладење или преостанати напрегања. Одржувањето на еднаква дебелина на ѕидот, користењето на соодветни канали за ладење и обезбедувањето балансирано полнење и пакување на калапот се клучни за да се спречи искривување. Оптимизирањето на температурата на мувлата, користењето соодветни агли на влечење и контролирањето на температурата на материјалот и брзината на вбризгување може да помогне да се минимизира искривувањето.
- Блесок:Блесок се јавува кога вишокот материјал се влева во линијата за разделување на калапот, што резултира со тенки, несакани проекции или дополнителен материјал на завршниот дел. Може ефикасно да се спречи блицот со обезбедување на правилен дизајн на калапот, вклучувајќи примена на соодветна сила на стегање, прецизно усогласување и користење на соодветни техники за вентилација. Оптимизирањето на параметрите на процесот како што се притисокот на вбризгување, температурата и времето на циклус го намалува блицот.
- Кратка снимка:Брзо истрелување се случува кога инјектираниот материјал не ја пополнува шуплината на мувлата, што резултира со нецелосен дел. Правилниот избор на материјалот, обезбедувањето соодветна температура и вискозност на топењето и одржувањето на соодветен притисок и време на вбризгување се неопходни за да се избегнат кратки фотографии. Дополнително, потврдувањето на дизајнот на калапот за доволна големина на тркачот и портата и правилното проветрување може да помогне да се спречат брзи снимки.
- Линии за заварување:Линиите за заварување се јавуваат кога два или повеќе фронтови за проток на растопениот материјал се среќаваат и се зацврстуваат, што резултира со видлива линија или ознака на површината на делот. Добриот дизајн на портата и тркачот, оптималната температура на топење, брзината на вбризгување и прилагодувањето на протокот на материјалот и геометријата на делови може да ги минимизираат линиите на заварување. Анализата на протокот на мувла и оптимизацијата на поставеноста на портата, исто така, може да помогне да се спречат или ублажат линиите за заварување.
- Траги од изгореници:Трагите од изгореници се обезбојувања или црни дамки на површината на обликуваниот дел предизвикани од прекумерна топлина или прегревање на материјалот. Избегнувањето на екстремната температура на топење, користењето соодветни канали за ладење и оптимизирањето на времето на циклусот може да помогне да се спречат траги од изгореници. Соодветното проветрување, правилниот дизајн на вратата и контролирањето на температурата на мувлата, исто така, придонесуваат за минимизирање на трагите од изгореници.
Операции по лиење: завршна обработка и склопување
По обликувањето со вбризгување, за многу обликувани делови може да бидат потребни дополнителни операции за завршна обработка и склопување за да се постигне саканиот финален производ. Овие операции по лиење може да вклучуваат:
- Сечење:Отстранете го вишокот материјал или трепкајте околу обликуваниот дел со помош на алатки за кастрење или сечење.
- Површински третман:Подобрување на изгледот или функционалноста на површината на делот користејќи различни техники како што се бојадисување, обложување или текстура.
- Собрание:Спојување на повеќе обликувани делови или додавање компоненти како што се прицврстувачи, влошки или етикети за да се заврши финалниот производ.
- Тестирање:Проверка на квалитетот и функционалноста на деловите преку различни методи на тестирање како што се димензионална анализа, тестирање на својствата на материјалот или тестирање на перформансите.
- Пакување и испорака:Правилно пакување и етикетирање на готовиот производ за испорака до клиенти или крајни корисници.
Изборот на операции по лиење зависи од специфичната примена и посакуваните карактеристики на финалниот производ. Блиската соработка помеѓу експерти за обликување со инјектирање, специјалисти за завршна обработка и монтажа и клиентот е од клучно значење за постигнување на посакуваниот апсолутен квалитет и функционалност на производот. Правилното планирање и интегрирањето на операциите по лиење во производниот процес може да помогне да се обезбеди ефикасно производство и навремена испорака на производи со висок квалитет.
Калапи со вбризгување наспроти други процеси на производство на пластика
Секој процес на производство на пластика има предности и ограничувања, што ги прави погодни за различни апликации.
- Калапи со инјектирање: Калапот со инјектирање е многу разновиден и широко користен производствен процес за производство на пластични делови. Тој нуди предности како што се висока производствена ефикасност, прецизна репликација на делови и способност за создавање сложени геометрии. Калапот со вбризгување е погодно за производствени серии со голем обем и овозможува користење на широк опсег на термопластични материјали. Тој нуди одлична прецизност на димензиите и завршна обработка на површината, што го прави идеален за различни индустрии како што се автомобилската индустрија, стоките за широка потрошувачка и медицинските уреди.
- Калапи со дување: Калапот со дување е процес кој се користи првенствено за производство на шупливи пластични делови, како што се шишиња, контејнери и автомобилски компоненти. Тоа вклучува топење на пластика и надувување во шуплина на мувла, создавајќи ја саканата форма. Обликувањето со дување е погодно за производство со голем обем и може да произведе големи, лесни делови со еднаква дебелина на ѕидот. Сепак, тој е ограничен во однос на сложеноста на делот и изборот на материјал во споредба со обликувањето со инјектирање.
- Термоформирање:Термоформирањето е процес кој се користи за производство на пластични делови со загревање на термопластичен лим и негово обликување со помош на калапи или вакуумско формирање. Наоѓа вообичаена употреба во пакувањето, производите за еднократна употреба и производите од големи размери, како што се послужавниците и капаците. Термоформирањето нуди рентабилно производство за големи делови и овозможува брзо прототипирање. Сепак, има ограничувања во однос на сложеноста на делот, изборот на материјал и прецизноста на димензиите во споредба со обликувањето со инјектирање.
- Истиснување:Екструзијата е континуиран процес за производство на пластични профили, листови, цевки и филмови. Тоа вклучува топење на пластична смола и нејзино протерување низ матрицата за да се создаде посакуваната форма. Екструзијата е погодна за производство на долги, континуирани должини на пластични производи со конзистентен пресек. Додека истиснувањето нуди високи стапки на производство и економичност, тоа е ограничено во однос на сложените геометрии на делови и прецизната димензионална контрола во споредба со обликувањето со инјектирање.
- Калапи со компресија:Калапот со компресија вклучува поставување на претходно измерена количина на термореактивниот материјал во загреана шуплина на мувла и негово компресирање под висок притисок додека не се стврдне. Наоѓа вообичаена употреба во производството на делови со висока јачина и димензионална стабилност, како што се автомобилски компоненти и електрична изолација. Калапот со компресија нуди добра конзистентност на делот, висока производна ефикасност и можност за користење на широк спектар на материјали. Сепак, тој е ограничен во однос на сложеноста на делот и времето на циклус во споредба со обликувањето со инјектирање.
Примени на термопластично вбризгување калапи
Различни индустрии широко користат термопластично калапи со инјектирање поради неговата разновидност, ефикасност и исплатливост. Некои од апликациите на калапи со термопластично вбризгување вклучуваат:
- Автомобилска индустрија: Автомобилската индустрија нашироко користи термопластично вбризгување за производство на различни компоненти, вклучувајќи внатрешни и надворешни облоги, контролни табли, панели на вратите, браници и електрични конектори. Процесот овозможува прецизна репликација на делови, сложени геометрии и лесни материјали, подобрувајќи ја ефикасноста на горивото и флексибилноста на дизајнот.
- Стоки за широка потрошувачка:Калапот со инјектирање наоѓа широка примена во производството на стоки за широка потрошувачка, како што се апарати за домаќинство, електронски уреди, контејнери за пакување и играчки. Процесот овозможува масовно производство на издржливи, висококвалитетни производи со конзистентни димензии и завршна површина. Овозможува и опции за прилагодување и брзи повторувања на производот.
- Медицински уреди:Калапот со инјектирање игра клучна улога во медицинската индустрија за производство на широк асортиман на уреди, вклучувајќи шприцеви, хируршки инструменти, имплантирани компоненти и системи за испорака на лекови. Процесот обезбедува производство на стерилни, прецизни и биокомпатибилни делови кои ги исполнуваат строгите регулаторни барања на здравствениот сектор.
- Електроника и електрична индустрија:Електронската индустрија користи обликување со вбризгување за производство на електрични конектори, куќишта, прекинувачи и други компоненти. Процесот нуди висока димензионална прецизност, одлична завршница на површината и можност за инкорпорирање на карактеристики како што се обликување со вметнување и преливање, што овозможува ефикасно производство на сложени електронски склопови.
- Индустрија за пакување:Различни индустрии, вклучувајќи храна и пијалоци, фармацевтски производи и лична нега, вообичаено користат калапи за инјектирање за производство на контејнери за пластични пакувања, капачиња, затворачи и шишиња. Процесот овозможува создавање на лесни, издржливи и естетски привлечни решенија за пакување со ефикасни циклуси на производство.
- Воздухопловна индустрија:Воздухопловниот сектор користи обликување со вбризгување за производство на лесни и со високи перформанси компоненти како што се воздушни канали, загради, внатрешни панели и структурни делови. Процесот овозможува користење на напредни материјали и сложени геометрии на делови, што придонесува за намалување на тежината и подобрена ефикасност на горивото.
Влијание врз животната средина на термопластично вбризгување калапи
Термопластичното вбризгување е популарен процес на производство поради неговите многубројни придобивки, но исто така е од суштинско значење да се земе предвид неговото влијание врз животната средина. Еве неколку точки што треба да се земат предвид:
- Ефикасност на материјалот:Термопластичното обликување со вбризгување ја промовира ефикасноста на материјалот со минимизирање на отпадот. Процесот користи прецизна контрола врз количината на материјал вбризгуван во калапот, намалувајќи ја потребата за вишок материјал. Производителите исто така можат да користат техники за повторно мелење и рециклирање за повторна употреба на отпадоци или отфрлени делови, со што дополнително се намалува отпадот од материјалот.
- Потрошувачка на енергија:Производителите дизајнираат машини за обликување со инјектирање за да бидат енергетски ефикасни, со модерни модели кои вклучуваат напредни технологии како што се серво мотори и погони со променлива брзина. Овие карактеристики ја оптимизираат употребата на енергија со намалување на потрошувачката на енергија за време на обликувањето, што резултира со помали потреби за енергија и намалено влијание врз животната средина.
- Управување со отпад:Додека го минимизираат материјалниот отпад, производителите треба да имплементираат соодветни практики за управување со отпад за да се справат со преостанатите материјали, прскалки или тркалца. Производителите можат да воспостават програми за рециклирање за собирање и повторна употреба на пластичниот отпад создаден за време на обликувањето со инјектирање, со што се намалува отпадот што се испраќа на депониите.
- Намалување на емисијата: Термопластичното обликување со вбризгување генерално генерира помали емисии од другите производни процеси. Производителите можат да ги намалат емисиите со користење на еколошки материјали, имплементирање на енергетски ефикасна опрема и примена на напредни издувни системи и системи за филтрирање за да се фатат емисиите што се ослободуваат.
- Избори за одржливи материјали:Изборот на термопластични материјали може значително да влијае на еколошката одржливост на обликувањето со инјектирање. Изборот за биоразградлива или био-базирана пластика, како и рециклирани или рециклирани материјали, може да помогне да се намали севкупниот еколошки отпечаток на процесот.
Размислувања за животниот циклус: Да се земе предвид целиот животен циклус на обликуваниот производ е од суштинско значење за проценка на неговото влијание врз животната средина. За време на фазите на дизајнирање и избор на материјали, производителите треба да ги земат предвид факторите како што се издржливоста на делот, неговата можност за рециклирање и потенцијалот за исфрлање или повторна употреба на крајот на работниот век.
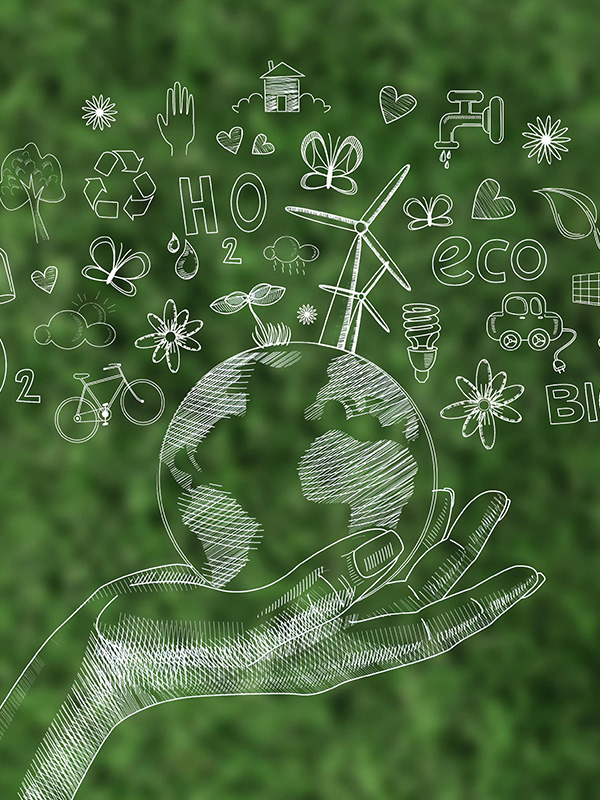
Иднината на термопластично вбризгување калапи
Иднината на обликувањето со термопластично вбризгување изгледа ветувачка, со континуиран напредок во технологијата и зголемена побарувачка за висококвалитетни, прецизни делови во различни индустрии. Некои од клучните случувања што се очекуваат во наредните години вклучуваат:
- Зголемена употреба на автоматизација и роботика за подобрување на ефикасноста и намалување на трошоците.
- Напорите се фокусирани на развој на нови материјали и процеси за подобрување на перформансите на деловите и овозможување нови апликации.
- Тоа е растечко усвојување на одржливи практики, како што се користење на рециклирани материјали и оптимизирање на потрошувачката на енергија, за да се намали влијанието врз животната средина од обликувањето со инјектирање.
- Поголема интеграција на дигиталните технологии, како што е софтверот за 3D печатење и симулација, за подобрување на процесите на дизајн и производство.
Глобалниот пазар на обликување со вбризгување се шири, особено во економиите во развој, поттикнат од зголемената побарувачка за пластични производи во различни индустрии.
Избор на вистинскиот партнер за вбризгување
Изборот на вистинскиот партнер за вбризгување е од клучно значење за успехот на вашиот проект. Одвојте време да оцените повеќе опции, да извршите посети на локацијата и да се вклучите во темелни дискусии за да обезбедите компатибилно и долгорочно партнерство.
- Експертиза и искуство:Побарајте партнер за вбризгување со големо знаење и искуство во индустријата. Тие треба да имаат докажано искуство за испорака на висококвалитетни производи и решенија до клиентите во различни сектори. Размислете за нивното разбирање за различни материјали, дизајни на калапи и производни процеси.
- Производствени способности: Проценете ги производните способности на партнерот за вбризгување. Осигурајте се дека имаат добро опремен објект со современи машини и технологии за да се справат со вашите барања за проектот. Размислете за нивниот производствен капацитет, способноста да се справи со различни големини и сложености на делови, како и способноста да се задоволат вашите посакувани обеми на производство и временски рокови.
- Обезбедување на квалитет:Квалитетот е најважен во обликувањето со инјектирање. Оценете ги системите за контрола на квалитетот и сертификатите на потенцијалниот партнер. Побарајте партнери кои следат строги стандарди за квалитет, имаат силни процеси на инспекција и вршат сеопфатно тестирање за да се обезбеди квалитет и конзистентност на делови.
- Дизајн и инженерска поддршка:Доверлив партнер за обликување со вбризгување треба да понуди дизајн и инженерска поддршка за да го оптимизирате дизајнот на вашиот дел за производственост. Тие треба да имаат квалификувани инженери кои можат да обезбедат вреден придонес за изборот на материјали, дизајнот на мувла и оптимизацијата на процесите за да го подобрат квалитетот и ефикасноста на деловите.
- Конкурентност на трошоците:Иако цената не треба да биде единствениот одлучувачки фактор, од суштинско значење е да се проценат цените и конкурентноста на трошоците на партнерот за вбризгување. Побарајте детални понуди и разгледајте ги трошоците за алати, трошоците за материјали, трошоците за работна сила и сите дополнителни услуги што ги обезбедуваат.
- Комуникација и соработка:Ефективната комуникација и соработка се од суштинско значење за успешно партнерство. Осигурете се дека партнерот за вбризгување има добри комуникациски канали, одговара на вашите прашања и може да обезбедува редовни ажурирања на проектот. Колаборативниот пристап ќе помогне да се осигуриме дека ги исполнуваме вашите барања и навремено да се справиме со сите предизвици.
- Референци и прегледи на клиентите:Побарајте референци од клиенти или читајте рецензии/сведоштва за да добиете увид во искуствата на другите клиенти со партнерот за вбризгување. Добивањето на овие информации може да помогне да се одреди нивната сигурност, брзина и целокупното ниво на задоволство на клиентите.
Заклучок
Термопластичното вбризгување е разноврсна и исплатлива метода за производство на пластични делови во големи количини. Неговата способност да произведува сложени форми со висока прецизност и конзистентност стана популарен избор за различни индустрии, вклучувајќи автомобилска, медицинска, електроника и стоки за широка потрошувачка. Со разбирање на различните аспекти на обликувањето со термопластично вбризгување, вклучувајќи ги неговите предности, недостатоци и размислувања за дизајнот, можете да донесувате информирани одлуки за изборот на вистинскиот партнер за вбризгување за вашите деловни потреби.