Што е калапи со инјектирање на пластика
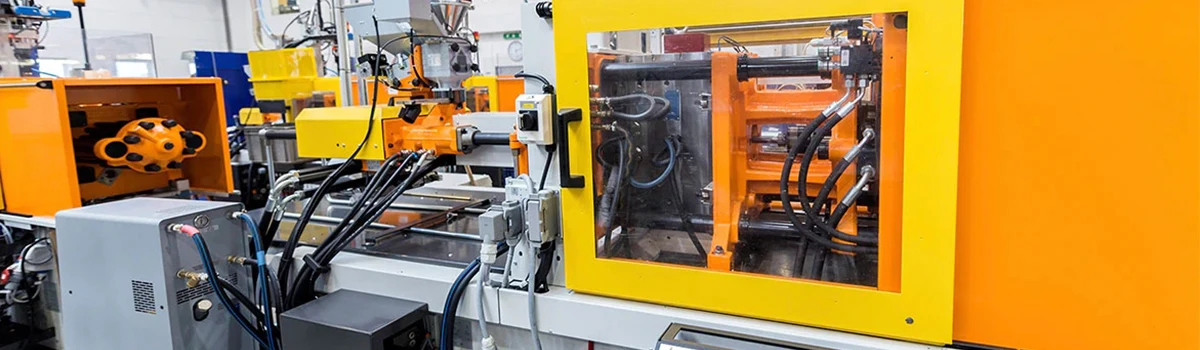
Термопластичното вбризгување е метод за производство на делови со голем волумен со пластични материјали. Поради својата сигурност и флексибилност во дизајнерските опции, обликувањето со инјектирање се користи во многу индустрии, вклучувајќи: пакување, потрошувачка и електроника, автомобилска, медицинска и многу повеќе.
Калапот со инјектирање е еден од најкористените производни процеси во светот. Термопластиките се полимери кои омекнуваат и течат кога се загреваат и се зацврстуваат додека се ладат.
апликации
Калапот со инјектирање е најчестиот модерен метод за производство на пластични делови; тој е идеален за производство на големи количини на ист објект. Калапот со вбризгување се користи за создавање на многу работи, вклучувајќи жичани калеми, амбалажа, капачиња за шишиња, автомобилски делови и компоненти, конзоли за игри, џебни чешли, музички инструменти, столици и мали маси, контејнери за складирање, механички делови и многу други пластични производи.
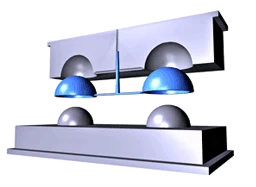
Дизајн на мувла
Откако производот е дизајниран во софтвер како пакет CAD, калапи се создаваат од метал, обично челик или алуминиум, и се обработуваат прецизно за да се формираат карактеристиките на саканиот дел. Калапот се состои од две основни компоненти, калапот за инјектирање (А плоча) и мувлата за исфрлање (плоча Б). Пластичната смола влегува во калапот преку спру, или портата, и се влева во шуплината на мувлата преку канали, или тркачи, кои се обработуваат во лицата на плочите А и Б.
Процес на калапи со инјектирање
Кога термопластиката се обликува, типично пелетизираната суровина се внесува преку бункер во загреана буре со клипна завртка. Завртката ја испорачува суровината напред, преку обратен вентил, каде што се собира на предниот дел од завртката во волумен познат како шут.
Истрелот е количината на смола потребна за да се пополни шприцот, тркачот и шуплините на мувла. Кога ќе се собере доволно материјал, материјалот се присилува под висок притисок и брзина во шуплината на делот.
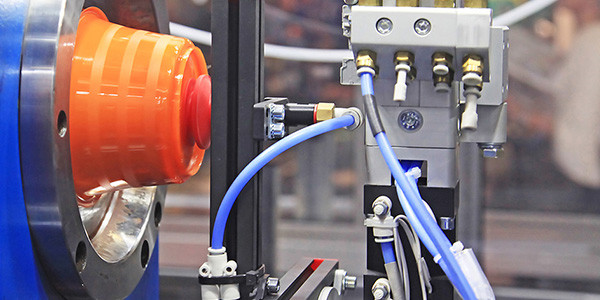
Како работи обликувањето со инјектирање?
Откако пластиката ќе го наполни калапот, вклучувајќи ги и неговите шприцови, тркалца, порти итн., калапот се чува на одредена температура за да се овозможи рамномерно зацврстување на материјалот во обликот на делот. Притисокот на задржување се одржува додека се лади за да се запре повратниот проток во цевката и да се намалат ефектите на собирање. Во овој момент, повеќе пластични гранули се додаваат во бункерот во очекување на следниот циклус (или истрел). Кога ќе се олади, плочата се отвора и дозволува готовиот дел да се исфрли, а завртката се повлекува уште еднаш, дозволувајќи му на материјалот да влезе во бурето и да го започне процесот одново.
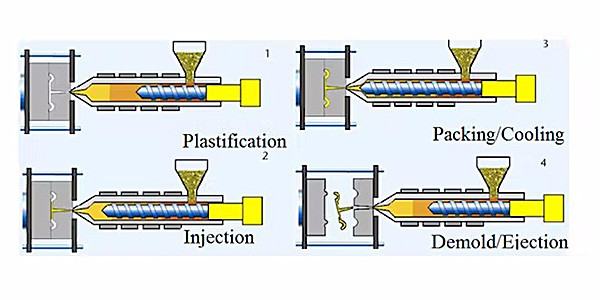
Циклусот на калапи со инјектирање функционира со овој континуиран процес - затворање на калапот, хранење/загревање на пластичните гранули, нивно притискање во калапот, ладење во цврст дел, исфрлање на делот и повторно затворање на калапот. Овој систем овозможува брзо производство на пластични делови, а повеќе од 10,000 пластични делови може да се направат во работен ден во зависност од дизајнот, големината и материјалот.
Циклус на калапи со инјектирање
Циклусот на обликување со инјектирање е многу краток, обично трае помеѓу 2 секунди и 2 минути. Постојат неколку фази:
1.Стегање
Пред да се вбризга материјалот во калапот, двете половини од калапот се затвораат безбедно со единицата за стегање. Единицата за стегање со хидраулично напојување ги турка половините на калапот заедно и врши доволна сила за да го држи калапот затворен додека материјалот се инјектира.
2. Инјекција
Со затворен калапот, полимерниот шут се вбризгува во шуплината на мувлата.
3.Ладење
Кога шуплината е исполнета, се применува притисок на задржување што овозможува повеќе полимер да влезе во шуплината за да го компензира пластичното собирање додека се лади. Во меѓувреме, завртката се врти и го напојува следниот истрел на предната завртка. Ова предизвикува повлекување на завртката додека се подготвува следниот удар.
4.Исфрлање
Кога делот доволно ќе се излади, калапот се отвора, делот се исфрла и циклусот започнува повторно.
Предности
1.Брзо производство; 2.Дизајн флексибилност; 3. Точност; 4. Ниски трошоци за работна сила; 5. Низок отпад