Çfarë është derdhja me injeksion plastik
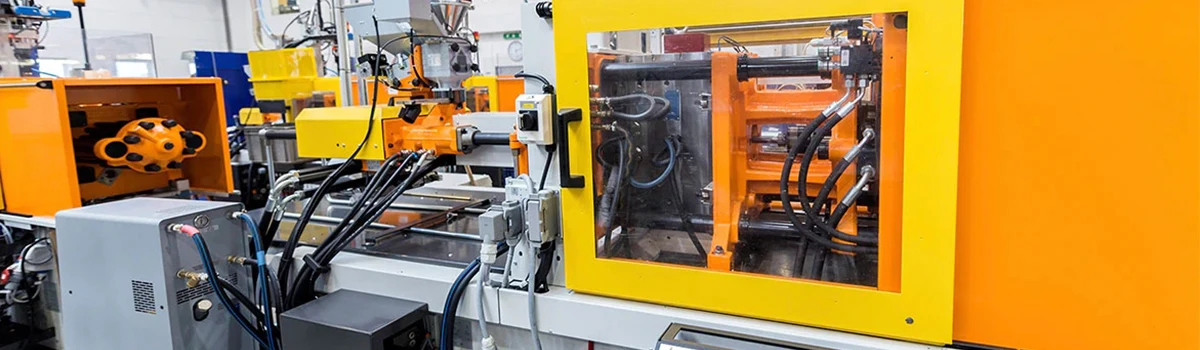
Formimi me injeksion termoplastik është një metodë për prodhimin e pjesëve me volum të lartë me materiale plastike. Për shkak të besueshmërisë dhe fleksibilitetit në opsionet e projektimit, formimi me injeksion përdoret në shumë industri, duke përfshirë: paketimin, konsumatorin dhe elektronikën, automobilat, mjekësinë dhe shumë të tjera.
Formimi me injeksion është një nga proceset e prodhimit më të përdorur në botë. Termoplastikët janë polimerë që zbuten dhe rrjedhin kur nxehen dhe ngurtësohen ndërsa ftohen.
Aplikime
Formimi me injeksion është metoda më e zakonshme moderne e prodhimit të pjesëve plastike; është ideale për prodhimin e vëllimeve të larta të të njëjtit objekt. Formimi me injeksion përdoret për të krijuar shumë gjëra, duke përfshirë bobinat e telit, paketimin, tapat e shisheve, pjesët dhe komponentët e automobilave, konzolat e lojërave, krehër xhepi, instrumente muzikore, karrige dhe tavolina të vogla, kontejnerë magazinimi, pjesë mekanike dhe shumë produkte të tjera plastike.
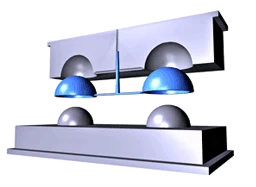
Dizajni i mykut
Pasi një produkt është projektuar në Softuer si një paketë CAD, formacionet krijohen nga metali, zakonisht çeliku ose alumini, dhe përpunohen me saktësi për të formuar tiparet e pjesës së dëshiruar. Kallëpi përbëhet nga dy përbërës kryesorë, kallëpi i injektimit (pllakë A) dhe kallëpi i nxjerrjes (pllakë B). Rrëshira plastike hyn në kallëp përmes një sprue ose porte dhe derdhet në zgavrën e kallëpit nëpërmjet kanaleve ose rrëshqitjeve që përpunohen në faqet e pllakave A dhe B.
Procesi i formimit me injeksion
Kur formohen termoplastikë, lënda e parë zakonisht e peletizuar futet përmes një pleshti në një fuçi të nxehtë me një vidë reciproke. Vidha e dërgon lëndën e parë përpara, përmes një valvule kontrolli, ku ajo grumbullohet në pjesën e përparme të vidës në një vëllim të njohur si një goditje.
Gjuajtja është sasia e rrëshirës që kërkohet për të mbushur sprue, vrapues dhe zgavra të një myku. Kur materiali është grumbulluar mjaftueshëm, materiali futet me presion dhe shpejtësi të lartë në zgavrën e pjesës formuese.
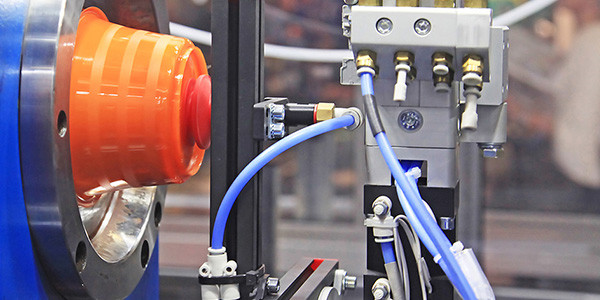
Si funksionon derdhja me injeksion?
Pasi plastika të ketë mbushur kallëpin duke përfshirë sprutat e saj, rrotat, portat, etj., myku mbahet në një temperaturë të caktuar për të lejuar ngurtësimin uniform të materialit në formën e pjesës. Një presion mbajtës mbahet gjatë ftohjes për të ndaluar rrjedhën e kundërt në fuçi dhe për të zvogëluar efektet e tkurrjes. Në këtë pikë, më shumë granula plastike i shtohen pleshtit në pritje të ciklit (ose gjuajtjes) tjetër. Kur ftohet, pllaka hapet dhe lejon që pjesa e përfunduar të nxirret dhe vida tërhiqet edhe një herë, duke lejuar që materiali të hyjë në fuçi dhe të fillojë procesin përsëri.
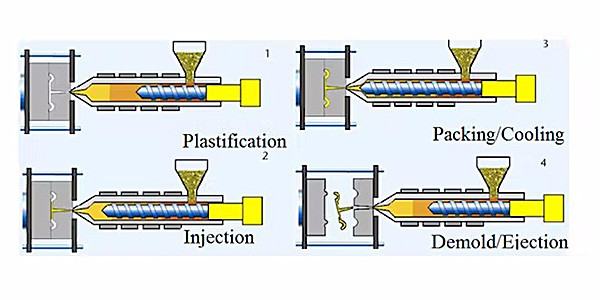
Cikli i derdhjes me injeksion funksionon nga ky proces i vazhdueshëm - mbyllja e kallëpit, ushqyerja/ngrohja e kokrrizave plastike, presioni i tyre në kallëp, ftohja e tyre në një pjesë të fortë, nxjerrja e pjesës dhe mbyllja e kallëpit përsëri. Ky sistem lejon prodhimin e shpejtë të pjesëve plastike dhe mbi 10,000 pjesë plastike mund të bëhen në një ditë pune në varësi të dizajnit, madhësisë dhe materialit.
Cikli i derdhjes me injeksion
Cikli i derdhjes me injeksion është shumë i shkurtër, zakonisht nga 2 sekonda deri në 2 minuta. Ka disa faza:
1.Mbërthimi
Para injektimit të materialit në kallëp, dy gjysmat e kallëpit mbyllen, mirë, nga njësia shtrënguese. Njësia shtrënguese me fuqi hidraulike i shtyn gjysmat e kallëpit së bashku dhe ushtron forcë të mjaftueshme për ta mbajtur mykun të mbyllur ndërsa materiali injektohet.
2.Injeksion
Me kallëp të mbyllur, e shtëna polimer injektohet në zgavrën e kallëpit.
3.Ftohja
Kur zgavra mbushet, aplikohet një presion mbajtës i cili lejon më shumë polimer të hyjë në zgavër për të kompensuar tkurrjen plastike ndërsa ftohet. Ndërkohë, vidhosja kthehet dhe ushqen goditjen tjetër në vidhën e përparme. Kjo bën që vidhosja të tërhiqet ndërsa përgatitet gjuajtja e radhës.
4.Ejeksioni
Kur pjesa të jetë ftohur mjaftueshëm, forma hapet, pjesa nxirret dhe cikli fillon përsëri.
Përparësitë
1.Prodhimi i shpejtë; 2.Fleksibiliteti i projektimit; 3. Saktësia; 4. Kostot e ulëta të punës; 5. Mbeturinat e ulëta