Formimi me injeksion termoplastik
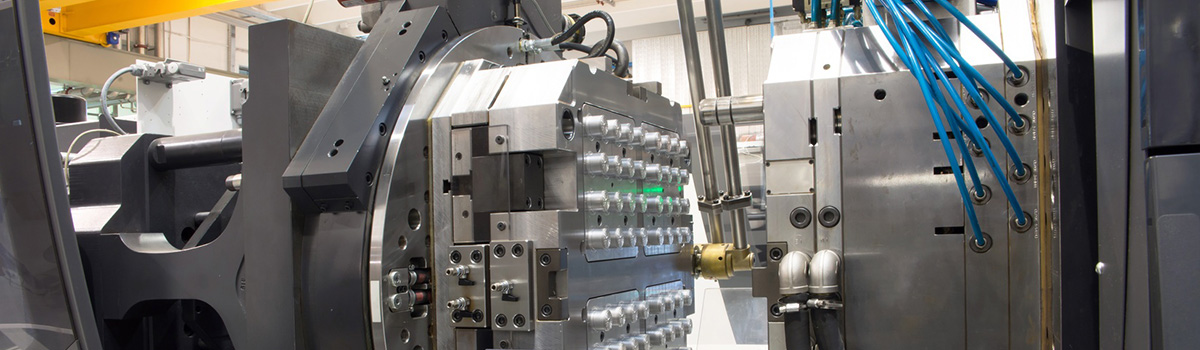
Formimi me injeksion termoplastik është një proces prodhimi popullor që përdoret për të krijuar pjesë të ndryshme plastike për industri të shumta. Ky proces përfshin shkrirjen e peletave plastike dhe injektimin e tyre në një kallëp për të prodhuar një formë tre-dimensionale. Formimi me injeksion termoplastik është shumë efikas dhe me kosto efektive për prodhimin e vëllimeve të mëdha të pjesëve plastike me cilësi të lartë me toleranca të ngushta. Ky udhëzues gjithëpërfshirës do të eksplorojë aspekte të ndryshme të formimit me injeksion termoplastik, duke përfshirë avantazhet dhe disavantazhet e tij, llojet e termoplastikës së përdorur, procesin e formimit të injektimit, konsideratat e projektimit dhe shumë më tepër.
Historia e derdhjes me injeksion termoplastik
Historia e formimit me injeksion termoplastik përfshin mbi një shekull përparime teknologjike, zhvillime materiale dhe aplikime industriale. Nga fillimet e tij modeste si një proces formimi celuloid deri në teknologjinë moderne të sofistikuar, derdhja me injeksion vazhdon të jetë një teknikë jetike e prodhimit, duke nxitur inovacionin dhe formësimin e industrive të ndryshme.
- Zhvillimet e hershme:John Wesley Hyatt dhe vëllai i tij Isaiah zhvilluan makinën e parë praktike të formimit me injeksion, duke gjurmuar origjinën e derdhjes me injeksion termoplastik që nga fundi i shekullit të 19-të. Në vitin 1872, ata patentuan një pajisje që përdorte një piston për të injektuar celuloid në një zgavër të mykut, duke krijuar objekte të forta. Ky zbulim hodhi themelet për procesin modern të formimit me injeksion.
- Përparimet në materiale:Në fillim të shekullit të 20-të, futja e polimerëve të rinj sintetikë hapi mundësi të reja për formimin me injeksion. Bakeliti, një rrëshirë fenolike, u bë një material popullor për formim për shkak të vetive të tij të shkëlqyera izoluese elektrike. Përgjatë viteve 1930 dhe 1940, përparimet në kiminë e polimerit çuan në zhvillimin e termoplasteve të tjera, të tilla si polistiren dhe polietileni, të cilat zgjeruan më tej gamën e materialeve të përshtatshme për derdhje me injeksion.
- Adoptimi industrial: Miratimi i gjerë i formimit me injeksion termoplastik filloi në vitet 1950 pasi prodhuesit e njohën efektivitetin e kostos dhe shkathtësinë e tij. Futja e makinerive me presion të lartë lejoi kohë më të shpejta të ciklit dhe rritje të vëllimeve të prodhimit. Si rezultat, u krijua një përzgjedhje e larmishme e produkteve për përdorim personal dhe industrial. Këto përfshinin komponentët e makinës, pajisjet shtëpiake dhe gjërat e lojës.
- Inovacionet teknologjike:Gjatë dekadave, teknologjia e derdhjes me injeksion vazhdoi të evoluojë. Në vitet 1960, u shfaqën makina të kontrolluara nga kompjuteri, duke mundësuar kontroll të saktë mbi procesin e formimit. Futja e sistemeve të vrapuesve të nxehtë në vitet 1980 reduktoi mbetjet dhe përmirësoi efikasitetin duke eliminuar nevojën për vrapues dhe sprues. Vitet e fundit, avancimet e automatizimit, robotikës dhe printimit 3D kanë revolucionarizuar më tej industrinë e formimit me injeksion, duke mundësuar dizajne komplekse dhe duke reduktuar kohën e prodhimit.
- Qëndrueshmëria dhe riciklimi:Me shqetësimet mjedisore në rritje, industria e derdhjes me injeksion ka përqafuar masat e qëndrueshmërisë. Prodhuesit kanë zhvilluar termoplastikë me bazë bio dhe të ricikluar, duke reduktuar varësinë nga materialet e bazuara në lëndë djegëse fosile. Për më tepër, teknologjitë e përmirësuara të riciklimit kanë mundësuar ripërpunimin e mbetjeve post-konsumatore dhe post-industriale, duke minimizuar ndikimin mjedisor të formimit me injeksion termoplastik.
- Perspektivat e ardhshme:E ardhmja e formimit me injeksion termoplastik duket premtuese. Industria po eksploron risi të tilla si formimi me mikro-injektim për komponentët në miniaturë, teknikat e shumë materialeve dhe të mbiformimit për pjesët komplekse dhe duke integruar teknologji inteligjente për monitorimin dhe optimizimin e procesit. Për më tepër, studiuesit presin që përparimet në materialet e biodegradueshme dhe prodhimin e aditivëve të revolucionarizojnë fushën, duke e bërë formimin me injeksion edhe më të qëndrueshëm dhe të gjithanshëm.
Avantazhet e derdhjes me injeksion termoplastik
Formimi me injeksion termoplastik ofron përparësi të shumta për prodhuesit. Ofron fleksibilitet dizajni, duke lejuar dizajne komplekse dhe të ndërlikuara me karakteristika të ndryshme. Procesi është me kosto efikase, duke reduktuar mbetjet materiale dhe duke ulur kostot për njësi. Formimi me injeksion termoplastik mbështet materiale të shumta, duke ofruar shkathtësi për aplikime të ndryshme.
- Fleksibiliteti i dizajnit:Formimi me injeksion termoplastik lejon dizajne të ndërlikuara dhe komplekse me veçori si prerje, mure të hollë dhe trashësi të ndryshme, duke u ofruar projektuesve liri të pamasë.
- Efikasiteti i kostos: Procesi është shumë efikas, duke reduktuar mbetjet materiale dhe duke ulur kostot për njësi. Formimi i njëkohshëm i pjesëve të shumta dhe ciklet e shpejta të prodhimit kontribuojnë në kursimin e kostos.
- Shkathtësia e materialit: Formimi me injeksion termoplastik mbështet një gamë të gjerë materialesh, duke u mundësuar prodhuesve të zgjedhin opsionin më të përshtatshëm për çdo aplikim, duke përfshirë materiale të ngurtë ose fleksibël, transparente ose të errët dhe rezistente kimikisht.
- Forca dhe qëndrueshmëria:Termoplastikët e derdhur me injeksion mund të shfaqin veti të shkëlqyera mekanike, të tilla si forca e lartë, qëndrueshmëria dhe rezistenca ndaj goditjes. Opsionet e përforcimit, si fibrat e qelqit ose të karbonit, i rrisin më tej këto veti.
- Konsistenca dhe cilësia:Formimi me injeksion siguron cilësi të qëndrueshme pjesë-pjesë dhe saktësi dimensionale, duke ofruar toleranca të ngushta dhe produkte të besueshme. Procesi gjithashtu siguron një sipërfaqe të lëmuar dhe uniforme, duke eliminuar nevojën për operacione shtesë të përfundimit.
- Shkallueshmëria dhe prodhimi masiv:Formimi me injeksion është i shkallëzueshëm nga vëllimet e ulëta në ato të larta, duke e bërë atë të përshtatshëm për prodhim masiv. Pasi prodhuesit krijojnë kallëpin, ata mund të prodhojnë sasi të mëdha pjesësh identike me variacione minimale.
- Integrimi dhe Kuvendi:Pjesët e derdhura me injeksion mund të përfshijnë përbërës të shumtë në një pjesë, duke reduktuar nevojën për procese shtesë montimi. Ky integrim rrit performancën e produktit, redukton kohën e montimit dhe ul kostot.
- qëndrueshmëria:Industria e derdhjes me injeksion po tregon një fokus në rritje në qëndrueshmëri. Disponueshmëria e materialeve me bazë bio dhe të riciklueshme lejon prodhimin e produkteve miqësore me mjedisin. Përdorimi efikas i materialit dhe riciklimi i termoplastikës kontribuojnë në një proces prodhimi më të gjelbër.
Këto përfitime e kanë bërë atë një metodë prodhimi të miratuar gjerësisht në industri të ndryshme, duke ofruar zgjidhje me cilësi të lartë, me kosto efektive dhe miqësore me mjedisin për kërkesat komplekse të produktit.
Disavantazhet e derdhjes me injeksion termoplastik
Ndërsa formimi me injektim termoplastik ofron përparësi të shumta, ka edhe disa disavantazhe. Prodhuesit duhet t'i vlerësojnë me kujdes këta faktorë dhe t'i peshojnë ato kundrejt përfitimeve për të përcaktuar përshtatshmërinë e formimit me injeksion termoplastik për aplikimet e tyre specifike.
- Investime të larta fillestare: Vendosja e një operacioni formimi me injeksion termoplastik kërkon një investim fillestar të konsiderueshëm në projektimin dhe fabrikimin e kallëpit dhe blerjen e makinerive të specializuara. Kostot që lidhen me krijimin e kallëpeve dhe mjeteve mund të jenë të konsiderueshme, veçanërisht për dizajne komplekse dhe të ndërlikuara.
- Kufizimet e dizajnit: Ndërsa formimi me injeksion termoplastik ofron fleksibilitet të projektimit, ekzistojnë disa kufizime. Për shembull, arritja e trashësisë uniforme të murit në të gjithë pjesën mund të jetë sfiduese, duke çuar në ndryshime në shpërndarjen e materialit dhe dobësi të mundshme strukturore. Për më tepër, prania e shkurtimeve ose gjeometrive komplekse mund të kërkojë përdorimin e veçorive shtesë të kallëpit ose operacioneve dytësore, duke rritur kostot dhe kohën e prodhimit.
- Kohët e gjata të plumbit:Procesi i projektimit dhe fabrikimit të kallëpeve për formimin me injeksion mund të marrë kohë, duke çuar në kohë më të gjata për zhvillimin e produktit. Procesi i përsëritjes së projektimit, prodhimi i mykut dhe testimi mund të shtojnë kohë të konsiderueshme në afatin kohor të përgjithshëm të prodhimit, i cili mund të mos jetë i përshtatshëm për projekte me afate të ngushta.
- Kufizimet e përzgjedhjes së materialit:Megjithëse formimi me injeksion termoplastik mbështet një gamë të gjerë materialesh, ka kufizime dhe kufizime të caktuara. Disa materiale mund të kenë kërkesa specifike përpunimi ose disponueshmëri të kufizuar, duke ndikuar në zgjedhjet e dizajnit dhe përzgjedhjen e materialit për një aplikim të caktuar.
- Kufizimet e madhësisë së pjesës:Makineritë e formimit me injeksion kanë kufizime në madhësi, si për sa i përket madhësisë fizike të pajisjes ashtu edhe madhësisë së kallëpeve që mund të akomodojnë. Prodhimi i pjesëve të mëdha mund të kërkojë pajisje të specializuara ose metoda alternative të prodhimit.
- Ndikim mjedisor:Ndërsa industria po punon drejt qëndrueshmërisë, procesi i formimit me injeksion termoplastik ende gjeneron materiale të mbeturinave, duke përfshirë skrap dhe sprues. Hedhja dhe riciklimi i duhur i këtyre materialeve është i nevojshëm për të minimizuar ndikimin mjedisor.
- Kompleksiteti i Optimizimit të Procesit:Arritja e parametrave optimale të procesit për formimin me injeksion termoplastik mund të jetë kompleks dhe kërkon kohë. Prodhuesit duhet të kontrollojnë dhe optimizojnë me kujdes temperaturën, presionin, shkallët e ftohjes dhe kohën e ciklit për të siguruar cilësi të qëndrueshme të pjesës dhe për të minimizuar defektet.
Llojet e termoplastikës që përdoren në formimin me injeksion
Këto janë vetëm disa shembuj të termoplastikës që përdoren zakonisht në formimin me injeksion. Çdo material ka veti unike, duke e bërë atë të përshtatshëm për aplikime specifike bazuar në forcën, fleksibilitetin, rezistencën kimike, transparencën dhe koston. Prodhuesit duhet t'i marrin parasysh këto veti dhe kërkesa kur zgjedhin termoplastikën e duhur për projektet e tyre të formimit me injeksion.
- Polipropileni (PP):Polipropileni është një termoplastik i gjithanshëm që përdoret zakonisht në formimin me injeksion. Ofron rezistencë të shkëlqyer kimike, densitet të ulët dhe forcë të mirë ndikimi. PP (polipropileni) ka aplikime të gjera në paketim, komponentë automobilistikë, pajisje shtëpiake dhe pajisje mjekësore.
- Polietileni (PE):Polietileni është një tjetër termoplastik i përdorur gjerësisht në formimin me injeksion. Është në dispozicion në forma të ndryshme, si polietileni me densitet të lartë (HDPE) dhe polietileni me densitet të ulët (LDPE). PE ofron rezistencë të mirë kimike, rezistencë dhe fleksibilitet, duke e bërë atë të përshtatshëm për shishe, kontejnerë dhe tuba.
- Polistireni (PS):Polistireni është një termoplastik i gjithanshëm i njohur për qartësinë, ngurtësinë dhe përballueshmërinë e tij. Ajo gjen përdorim të zakonshëm në paketim, mallra të konsumit dhe produkte të disponueshme. PS (polistireni) lejon përpunim të shpejtë dhe siguron stabilitet të mirë dimensionale, por mund të jetë i brishtë dhe i ndjeshëm ndaj plasaritjes së stresit mjedisor.
- Akrilonitril butadien stiren (ABS): ABS është një termoplastik i njohur i njohur për rezistencën e shkëlqyer ndaj goditjes dhe qëndrueshmërinë. Ai kombinon vetitë e akrilonitrilit, butadienit dhe stirenit për të krijuar një material të gjithanshëm të përshtatshëm për pjesët e automobilave, strehimet elektronike dhe lodrat.
- Klorur polivinil (PVC): PVC është një termoplastik i përdorur gjerësisht i njohur për rezistencën e shkëlqyer kimike, qëndrueshmërinë dhe koston e ulët. Mund të jetë i ngurtë ose fleksibël në varësi të formulimit dhe aditivëve të përdorur. PVC (klorur polivinil) gjen përdorim të zakonshëm në ndërtim, izolim elektrik, produkte të kujdesit shëndetësor dhe paketim.
- Polikarbonat (PC): Polikarbonati është një termoplastik transparent me ndikim të jashtëzakonshëm dhe rezistencë të lartë ndaj nxehtësisë. Ajo gjen përdorim të zakonshëm në aplikacionet që kërkojnë qartësi optike, të tilla si komponentët e automobilave, helmetat e sigurisë dhe ekranet elektronike.
- Najloni (poliamid):Najloni është një termoplastik i fortë dhe i qëndrueshëm i njohur për vetitë e tij të shkëlqyera mekanike dhe rezistencën kimike. Ai gjen përdorim të zakonshëm në aplikacionet që kërkojnë forcë të lartë, të tilla si pjesët e automobilave, komponentët industrialë dhe mallrat e konsumit.
- Polietileni tereftalat (PET):PET është një termoplastik i njohur për prodhimin e shisheve, kontejnerëve dhe materialeve të paketimit. Ofron qartësi të mirë, rezistencë kimike dhe veti penguese, duke e bërë atë të përshtatshëm për aplikime në ushqim dhe pije.
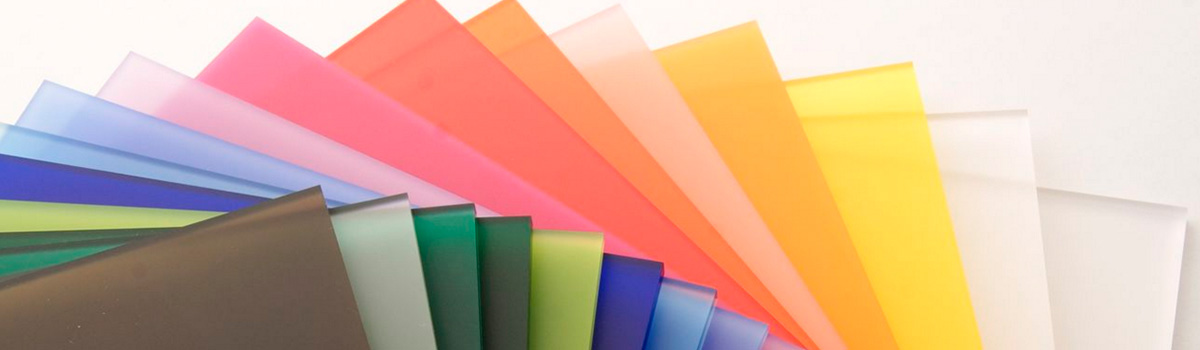
Vetitë e termoplastikës së përdorur në formimin me injeksion
Këto veti të termoplastikës luajnë një rol vendimtar në përcaktimin e përshtatshmërisë së tyre për aplikime specifike të derdhjes me injeksion. Prodhuesit duhet t'i marrin parasysh me kujdes këto veti dhe të zgjedhin termoplastikën e duhur bazuar në performancën e dëshiruar, kushtet mjedisore dhe kërkesat e kostos.
- Karakteristikat mekanike:Termoplastikët e përdorur në formimin me injeksion mund të shfaqin veti të ndryshme mekanike, duke përfshirë forcën në tërheqje, rezistencën ndaj goditjes dhe forcën në përkulje. Këto veti përcaktojnë aftësinë e materialit për t'i bërë ballë forcave të aplikuara dhe qëndrueshmërinë e tij të përgjithshme në aplikime të ndryshme.
- Rezistenca kimike:Shumë termoplastikë të përdorur në formimin me injeksion kanë rezistencë të jashtëzakonshme ndaj kimikateve, tretësve dhe vajrave. Kjo veti është thelbësore për aplikimet që përfshijnë ekspozimin ndaj mjediseve të ashpra ose substancave gërryese.
- Stabiliteti termik:Stabiliteti termik i termoplastikës i referohet aftësisë së tyre për të përballuar temperaturat e ngritura pa degradim të konsiderueshëm. Disa termoplastikë shfaqin rezistencë të shkëlqyer ndaj nxehtësisë, duke i lejuar ato të ruajnë vetitë e tyre mekanike edhe në temperatura të larta.
- Vetitë elektrike:Termoplastika e përdorur në formimin me injeksion mund të ketë veti elektrike specifike, duke përfshirë izolimin elektrik, përçueshmërinë ose forcën dielektrike. Këto veti janë thelbësore për aplikimet në industritë elektrike dhe elektronike, ku materialet duhet të ofrojnë performancë të besueshme elektrike.
- Transparenca dhe qartësia:Disa termoplastikë, të tillë si polikarbonati dhe PET, ofrojnë transparencë dhe qartësi të shkëlqyer, duke i bërë ato të përshtatshme për aplikime që kërkojnë veti optike. Prodhuesit zakonisht i përdorin këto materiale në produkte të tilla si dritaret transparente, lentet dhe ekranet.
- Fleksibiliteti dhe qëndrueshmëria: Fleksibiliteti dhe qëndrueshmëria janë veti thelbësore të termoplastikës që përdoren në aplikime që kërkojnë rezistencë ndaj goditjes dhe qëndrueshmëri. Disa termoplastikë, si ABS dhe najloni, ofrojnë rezistencë të shkëlqyer, duke i lejuar ata të përballojnë goditjet e përsëritura pa u thyer.
- Stabiliteti dimensional:Stabiliteti dimensional i referohet aftësisë së një termoplastiku për të ruajtur formën dhe madhësinë e tij në kushte të ndryshme, duke përfshirë ndryshimet e temperaturës. Materialet me qëndrueshmëri të mirë dimensionale sigurojnë dimensione të qëndrueshme të pjesës, duke minimizuar rrezikun e shtrembërimit ose shtrembërimit.
- Përputhshmëria kimike:Pajtueshmëria kimike e termoplastikës i referohet aftësisë së tyre për t'i rezistuar degradimit ose ndërveprimit me kimikate të ndryshme, duke përfshirë acidet, bazat dhe tretësit. Për të siguruar performancën optimale, është thelbësore zgjedhja e një termoplastiku që mund të përballojë mjedisin kimik specifik që do të hasë në aplikimin e synuar.
- Dendësia: Termoplastikët kanë trashësi të ndryshme, të cilat mund të ndikojnë në peshën e tyre dhe vetitë e përgjithshme të pjesës. Materialet me densitet të ulët, si polietileni, ofrojnë zgjidhje të lehta, ndërsa materialet me densitet të lartë, si polipropileni, ofrojnë forcë dhe ngurtësi të shtuar.
Procesi i derdhjes me injeksion: hap pas hapi
Procesi i formimit me injeksion ndjek këto hapa, duke lejuar prodhimin efikas dhe të saktë të pjesëve termoplastike me cilësi të lartë. Çdo hap kërkon kontroll dhe monitorim të kujdesshëm për të siguruar dimensione të qëndrueshme të pjesës, vetitë e materialit dhe cilësinë e përgjithshme.
- Dizajni dhe fabrikimi i mykut: Hapi i parë në procesin e formimit me injeksion është dizenjimi dhe fabrikimi i kallëpit. Prodhuesit duhet të krijojnë një dizajn të saktë dhe të detajuar të kallëpit për të arritur specifikimet e dëshiruara të pjesës. Prodhuesit më pas fabrikojnë kallëpin duke përdorur teknika të ndryshme, të tilla si CNC ose përpunimi i shkarkimit elektrik (EDM).
- Përgatitja e materialit: Hapi tjetër është përgatitja pasi myku të jetë gati. Peletat termoplastike ose granula zgjidhen në bazë të vetive të dëshiruara të materialit dhe shkrihen në një plesht. Operatorët më pas e fusin materialin në fuçinë e makinës së derdhjes me injeksion, ku ai i nënshtrohet shkrirjes dhe homogjenizimit.
- Injeksion:Gjatë fazës së injektimit, operatorët injektojnë termoplastikën e shkrirë në zgavrën e kallëpit nën presion të lartë. Njësia e injektimit të makinës e shtyn materialin e shkrirë përmes një gryke dhe në kallëp. Materiali mbush zgavrën e mykut, duke marrë formën e pjesës së dëshiruar.
- Ftohja dhe ngurtësimi:Pas mbushjes së kallëpit, operatorët lejojnë që plastika e shkrirë të ftohet dhe të ngurtësohet. Ftohja është thelbësore për arritjen e stabilitetit dimensional dhe formimin e duhur të pjesëve. Operatorët mund të kontrollojnë procesin e ftohjes duke qarkulluar ftohësin përmes kanaleve brenda kallëpit ose duke përdorur pllaka ftohëse.
- Hapja dhe nxjerrja e mykut:Operatorët e hapin kallëpin dhe e nxjerrin pjesën nga zgavra e kallëpit pasi plastika të ngurtësohet. Sistemi i nxjerrjes brenda makinës përdor kunjat, pllakat e nxjerrjes ose shpërthimet e ajrit për të hequr zonën nga myku. Më pas kallëpi është gati për ciklin tjetër të injektimit.
- Pas përpunimit: Pas nxjerrjes, pjesa mund t'i nënshtrohet operacioneve të pas-përpunimit, të tilla si shkurtimi, heqja e gërvishtjeve ose mbarimi i sipërfaqes. Këto hapa ndihmojnë në heqjen e materialit të tepërt, lëmimin e skajeve të vrazhda dhe përmirësimin e pamjes përfundimtare të pjesës.
- Inspektimi i Cilësisë: Hapi i fundit përfshin inspektimin e pjesëve të injektuara për cilësi dhe sigurimin që ato plotësojnë kërkesat e specifikuara. Teknika të ndryshme të kontrollit të cilësisë, duke përfshirë matjen dimensionale, inspektimin vizual dhe testimin funksional, mund të përdoren për të verifikuar cilësinë dhe integritetin e pjesës.
- Riciklimi dhe ripërdorimi i materialeve:Çdo material i tepërt ose skrap i krijuar gjatë formimit me injeksion mund të riciklohet dhe ripërdoret. Reduktimi i përdorimit të materialit të ri termoplastik ndihmon në minimizimin e mbetjeve dhe përmirësimin e qëndrueshmërisë.
Pajisjet e përdorura në derdhje me injeksion
Këta komponentë pajisjesh lehtësojnë procesin e formimit me injeksion, nga shkrirja dhe injektimi i materialit termoplastik deri te formimi, ftohja dhe nxjerrja e pjesës përfundimtare. Funksionimi dhe mirëmbajtja e duhur e këtyre komponentëve të pajisjeve janë thelbësore për arritjen e prodhimit efikas dhe me cilësi të lartë të formimit me injeksion.
- Makina e derdhur me injeksion:Pajisja kryesore në formimin me injeksion është përgjegjëse për shkrirjen e materialit termoplastik, injektimin e tij në myk dhe kontrollin e procesit.
- Mold: Kallëpi, i projektuar me porosi për të krijuar formën dhe veçoritë e dëshiruara të pjesës plastike, përbëhet nga dy gjysma, zgavrën dhe bërthamën. Operatorët e montojnë atë në njësinë shtrënguese të makinës së derdhjes me injeksion.
- Hopper:Enë që mban materialin termoplastik në formë peleti ose grimcimi dhe e fut atë në fuçinë e makinës së derdhjes me injeksion për shkrirje dhe injektim.
- Fuçi dhe vidë: Fuçi, një dhomë cilindrike, shkrin dhe homogjenizon materialin termoplastik ndërsa vidha rrotullohet brenda saj për të shkrirë, përzier dhe standardizuar materialin.
- Sistemet e ngrohjes dhe ftohjes:Makineritë e derdhjes me injeksion kanë elemente ngrohëse, të tilla si ngrohës elektrik ose ngrohës që përdorin vaj të nxehtë, për të rritur temperaturën e fuçisë, dhe sisteme ftohjeje, si qarkullimi i ujit ose vajit, për të ftohur mykun dhe për të ngurtësuar pjesën plastike.
- Sistemi i nxjerrjes:Heq pjesën e derdhur nga zgavra e kallëpit pas ngurtësimit, duke përdorur zakonisht kunjat e nxjerrjes, pllakat ose shpërthimet e ajrit gjatë hapjes së kallëpit.
- Sistemi I kontrollit:Monitoron dhe kontrollon parametra të ndryshëm të procesit të formimit të injektimit, duke i lejuar operatorët të vendosin dhe rregullojnë parametra të tillë si shpejtësia e injektimit, temperatura, presioni dhe koha e ftohjes.
Makinat e derdhura me injeksion: Llojet dhe karakteristikat
Çdo lloj makinerie formimi me injeksion ka karakteristikat dhe avantazhet e veta, duke i lejuar prodhuesit të zgjedhin pajisjen më të përshtatshme për kërkesat e tyre specifike të prodhimit.
- Makinat e derdhjes hidraulike me injeksion: Këto makina përdorin sisteme hidraulike për të gjeneruar presionin e nevojshëm për të injektuar plastikë të shkrirë në kallëp. Ata janë të njohur për forcën e tyre të lartë shtrënguese, kontrollin e saktë dhe shkathtësinë në trajtimin e termoplasteve të ndryshme. Makinat hidraulike janë të përshtatshme për prodhim në shkallë të gjerë dhe mund të akomodojnë kallëpe komplekse.
- Makinat e derdhjes elektrike me injeksion:Makinat elektrike përdorin servo motorë elektrikë për funksionimin e makinës, duke përfshirë sistemet e injektimit, shtrëngimit dhe nxjerrjes. Ato ofrojnë kontroll të saktë, efikasitet energjetik dhe kohë më të shpejtë reagimi sesa makinat hidraulike. Makinat elektrike janë ideale për aplikime të derdhura precize që kërkojnë përsëritshmëri dhe saktësi të lartë.
- Makinat e derdhjes hibride me injeksion:Makinat hibride kombinojnë përfitimet e pajisjeve hidraulike dhe elektrike. Ata përdorin një kombinim të sistemeve servo hidraulike dhe elektrike për të arritur saktësi të lartë, efikasitet të energjisë dhe kosto-efektivitet. Makinat hibride janë të përshtatshme për një gamë të gjerë aplikimesh, duke siguruar një ekuilibër midis performancës dhe kostove operacionale.
- Makinat e derdhjes me dy pllaka: Makinat me dy pllakë kanë një dizajn unik me dy pllaka të veçanta për shtrëngimin e kallëpit. Ky dizajn siguron stabilitet të përmirësuar, sinkronizim të përmirësuar të mykut dhe lejon përmasa më të mëdha të kallëpit dhe forca më të larta shtrënguese. Makinat me dy pllaka janë të përshtatshme për pjesë të mëdha dhe komplekse që kërkojnë formim të saktë.
- Makinat e derdhjes me injeksion me shumë komponentë:Prodhuesit i projektojnë këto makina për të prodhuar pjesë me materiale ose ngjyra të shumta në një cikël të vetëm formimi. Ato kanë njësi dhe kallëpe të ndryshme injektimi, duke mundësuar injektimin e njëkohshëm të materialeve të ndryshme. Makineritë me shumë komponentë ofrojnë fleksibilitet dhe efikasitet në prodhimin e pjesëve komplekse me karakteristika të ndryshme.
- Makinat e derdhjes me mikro-injektim:Të projektuara posaçërisht për prodhimin e pjesëve të vogla dhe të sakta, makinat e formimit me mikro-injektim ofrojnë saktësi dhe saktësi tepër të lartë. Ato mund të prodhojnë detaje të ndërlikuara me toleranca të ngushta dhe mbetje materiale minimale. Elektronika, pajisjet mjekësore dhe mikro-optika zakonisht përdorin makineri të derdhura me mikro-injeksion.
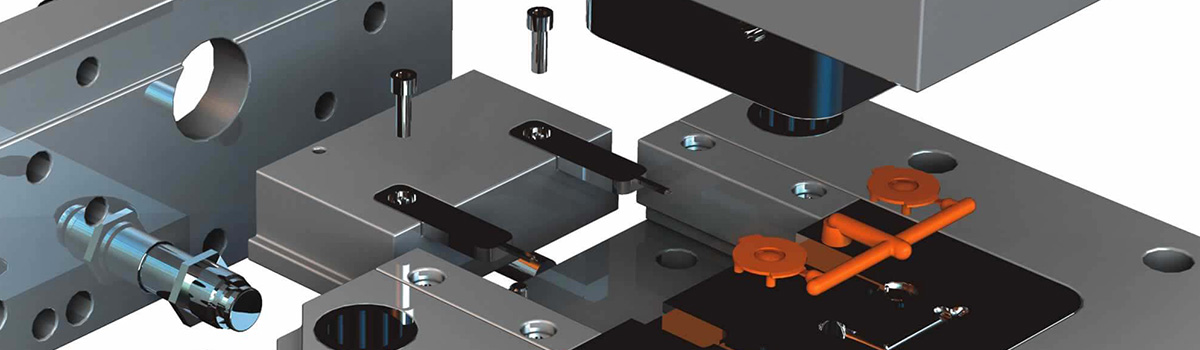
Konsideratat e dizajnit të mykut për derdhjen me injeksion
Konsideratat e kujdesshme të dizajnit të mykut janë thelbësore për prodhimin e suksesshëm të formimit me injeksion.
- Dizajni i pjesës:Dizajni i kallëpit duhet të përputhet me kërkesat specifike të pjesës, duke përfshirë formën, dimensionet dhe veçoritë funksionale. Prodhuesit duhet të marrin parasysh siç duhet këndet e rrymës, trashësinë e murit, prerjet e poshtme dhe çdo element të nevojshëm për të siguruar lehtësinë e nxjerrjes dhe cilësinë e pjesës.
- Materiali i mykut: Përzgjedhja e materialit të mykut është thelbësore për arritjen e qëndrueshmërisë, stabilitetit dimensional dhe rezistencës ndaj nxehtësisë. Materialet e zakonshme të mykut përfshijnë lidhjet e çelikut, lidhjet e aluminit dhe çeliqet e veglave. Zgjedhja e materialit varet nga faktorë të tillë si vëllimi i prodhimit, kompleksiteti i pjesës dhe jeta e pritshme e mjetit.
- Sistemi i ftohjes:Ftohja efikase është thelbësore për ngurtësimin e duhur të pjesëve dhe minimizimin e kohës së ciklit. Dizajni i kallëpit duhet të përfshijë kanale ftohëse ose futje të pozicionuara në mënyrë strategjike për të siguruar ftohje uniforme të mykut. Ftohja e duhur zvogëlon rrezikun e shtrembërimit, tkurrjes dhe defekteve të pjesëve.
- venting:Është i nevojshëm ventilimi adekuat për të lejuar daljen e ajrit dhe gazrave gjatë procesit të injektimit. Ajrimi i pamjaftueshëm mund të çojë në kurthe gazi, shenja djegieje ose mbushje jo të plotë të pjesëve. Prodhuesit mund të arrijnë ajrimin duke përfshirë brazdat e ventilimit, kunjat ose mekanizmat e tjerë në modelin e kallëpit.
- Sistemi i nxjerrjes:Dizajni i kallëpit duhet të përfshijë një sistem nxjerrjeje efektive për të hequr në mënyrë të sigurtë dhe efikase pjesën e derdhur nga zgavra e mykut. Sistemi i nxjerrjes mund të përbëhet nga kunjat e nxjerrjes, mëngët ose mekanizmat e tjerë, të pozicionuar në mënyrë strategjike për të shmangur ndërhyrjen me funksionin ose karakteristikat kritike.
- Dizajni i portës:Porta është vendi ku plastika e shkrirë hyn në zgavrën e mykut. Dizajni i portës duhet të sigurojë mbushjen e duhur të pjesëve, të minimizojë linjat e rrjedhës dhe të parandalojë ngrirjen e parakohshme të materialit. Modelet standarde të portave përfshijnë portat e skajit, portat e tunelit dhe sistemet e nxehta, në varësi të kërkesave të pjesës dhe vetive të materialit.
- Linja e ndarjes:Dizajni i kallëpit duhet të përcaktojë një vijë të përshtatshme ndarëse, e cila është linja ku bashkohen dy gjysmat e kallëpit. Vendosja e duhur e linjës ndarëse siguron mospërputhje minimale të blicit dhe linjës ndarëse dhe lehtëson montimin efikas të kallëpit.
- Mirëmbajtja dhe shërbimi i mykut: Prodhuesit duhet të marrin parasysh lehtësinë e mirëmbajtjes, riparimit dhe servisimit të mykut. Komponentët e mykut duhet të jenë lehtësisht të aksesueshëm për pastrim, inspektim dhe zëvendësim. Përfshirja e veçorive si futjet me ndryshim të shpejtë ose dizajnet modulare të kallëpeve mund të përmirësojnë shërbimin e mykut.
Materialet e mykut të përdorura në formimin me injeksion
Bashkëpunimi me specialistë të materialeve të mykut dhe marrja në konsideratë e nevojave specifike të aplikimit të formimit mund të ndihmojë në përcaktimin e materialit më të përshtatshëm për arritjen e performancës optimale të mykut dhe cilësisë së pjesës.
- Lidhjet e çelikut: Lidhjet e çelikut, të tilla si çeliqet e veglave (p.sh. P20, H13) dhe çeliqet inox, përdoren zakonisht për kallëpet e formimit me injeksion për shkak të qëndrueshmërisë së tyre të shkëlqyer, rezistencës ndaj nxehtësisë dhe rezistencës ndaj konsumit. Këto materiale mund të përballojnë temperaturat dhe presionet e larta në procesin e formimit me injeksion dhe ofrojnë stabilitet të mirë dimensionale për prodhimin e pjesëve me cilësi të lartë.
- Lidhjet e aluminit:Lidhjet e aluminit, të tilla si 7075 dhe 6061, janë të lehta dhe ofrojnë përçueshmëri të mirë termike, duke i bërë ato të përshtatshme për kallëpe që kërkojnë ftohje efikase. Prodhuesit shpesh përdorin kallëpe alumini për prototipe, prodhim me volum të ulët ose aplikacione ku reduktimi i peshës është kritik. Sidoqoftë, kallëpet e aluminit mund të kenë qëndrueshmëri më të ulët në krahasim me lidhjet e çelikut.
- Lidhjet e bakrit:Lidhjet e bakrit, të tilla si bakri berilium, shfaqin përçueshmëri të lartë termike dhe përpunueshmëri të mirë. Ato përdoren në kallëpe që kërkojnë transferim të shkëlqyer të nxehtësisë për ftohje efektive. Lidhjet e bakrit mund të ndihmojnë në reduktimin e kohës së ciklit duke shpërndarë shpejt nxehtësinë nga pjesa e derdhur, duke rezultuar në ngurtësim më të shpejtë.
- Çeliqet e veglave:Çeliqet e veglave, duke përfshirë H13, S7 dhe D2, janë të dizajnuara për aplikime për vegla pune me performancë të lartë. Këta çeliqe ofrojnë një kombinim të forcës së lartë, fortësisë dhe rezistencës ndaj konsumit. Çeliqet e veglave u përshtaten kallëpeve me vëllime të larta prodhimi, materiale gërryese ose kushte të vështira formimi.
- Lidhjet e nikelit:Lidhjet e nikelit, si Inconel dhe Hastelloy, njihen për rezistencën e tyre të jashtëzakonshme ndaj korrozionit, forcën në temperaturë të lartë dhe stabilitetin termik. Prodhuesit përdorin këto lidhje në kallëpe që trajtojnë materiale korrozive ose kërkojnë rezistencë ndaj temperaturave ekstreme dhe mjediseve agresive të formimit.
- Materialet e përbëra:Materialet e përbëra, të tilla si plastika e përforcuar ose përbërësit me futje metalike, përdoren herë pas here për aplikime specifike të formimit. Këto materiale ofrojnë një ekuilibër të vetive, të tilla si forca e lartë, stabiliteti termik dhe pesha e reduktuar. Format e përbëra mund të jenë alternativa me kosto efektive për kërkesat specifike të prodhimit.
Llojet e kallëpeve të injektimit
Formimi me injeksion është një proces i gjithanshëm dhe i përdorur gjerësisht i prodhimit për pjesët plastike.
- Kallëp me dy pllaka:Kallëpi me dy pllaka është lloji më i zakonshëm i mykut të injektimit. Përbëhet nga dy pllaka, pllaka e zgavrës dhe pllaka bërthamore, të cilat ndahen për të lejuar nxjerrjen e pjesës së derdhur. Pllaka e zgavrës përmban anën e zgavrës së kallëpit, ndërsa pllaka e bërthamës strehon anën e bërthamës. Prodhuesit përdorin kallëpe me dy pllaka për prodhimin e një game të gjerë pjesësh për shkak të dizajnit të tyre relativisht të thjeshtë.
- Kallëp me tre pllaka:Kallëpi me tre pllaka është një version i avancuar i kallëpit me dy pllaka. Ai përfshin një pjatë shtesë, një pllakë vrapuese ose pllakë sprue. Pllaka mbajtëse krijon një kanal të veçantë për sprue, vrapues dhe porta, duke lejuar heqjen më të lehtë të pjesës së derdhur. Prodhuesit zakonisht përdorin kallëpe me tre pllaka për detaje me sisteme komplekse portash ose kur është e dëshirueshme shmangia e mbetjeve të portës në copë.
- Forma e nxehtë e vrapuesit:Sistemi i kontrabandës dhe i portës nxehet në kallëpe të nxehta vrapuese, duke eliminuar nevojën për ngurtësim dhe ri-shkrirje të materialit gjatë çdo cikli. Sistemi i kontrabandës së nxehtë përbëhet nga kolektorë dhe grykë të nxehtë që ruajnë gjendjen e shkrirë të plastikës. Kallëpët e nxehtë të vrapuesit ofrojnë përparësi të tilla si koha e reduktuar e ciklit, më pak mbetje materiale dhe cilësi e përmirësuar e pjesëve duke minimizuar mbetjet e portës.
- Kallëp për vrapues të ftohtë: Format e vrapuesve të ftohtë kanë një sistem kontrabandist dhe portash tradicionale ku plastika e shkrirë rrjedh nëpër vrapues të ftohtë që ngurtësohen me çdo cikël. Operatorët më pas heqin rrëshqitësit e ngurtësuar, duke rezultuar në mbetje materiale. Prodhuesit zakonisht përdorin kallëpe komplekse vrapuese për prodhim me vëllim më të ulët ose kur kostot e materialeve janë më pak kritike për shkak të dizajnit të tyre më të drejtpërdrejtë.
- Fut kallëp:Format e futjes përfshijnë futje metalike ose plastike në zgavrën e kallëpit gjatë formimit me injeksion. Insertet mund të vendosen paraprakisht në kallëp ose të futen me procese të automatizuara. Ky kallëp lejon integrimin e komponentëve shtesë ose elementëve përforcues në pjesën e derdhur, duke rritur funksionalitetin ose forcën e saj.
- Mbi myk: Mbjellja përfshin formimin e një materiali mbi një tjetër, zakonisht duke lidhur një nënshtresë të ngurtë plastike me një elastomer ose termoplastik më të butë. Ky proces lejon krijimin e pjesëve me materiale ose tekstura të shumta në një kallëp të vetëm, duke siguruar mbërthim të përmirësuar, zbutje ose veçori estetike.
Faktorët që ndikojnë në kostot e derdhjes me injeksion
Marrja në konsideratë e këtyre faktorëve mund t'i ndihmojë prodhuesit të vlerësojnë dhe optimizojnë koston e formimit me injeksion, duke siguruar një ekuilibër midis cilësisë, efikasitetit dhe efektivitetit të kostos për kërkesat e tyre specifike të prodhimit.
- Kompleksiteti i pjesës:Kompleksiteti i dizajnit të pjesës luan një rol të rëndësishëm në përcaktimin e kostos së formimit me injeksion. Gjeometritë e ndërlikuara, prerjet, muret e hollë ose veçoritë komplekse mund të kërkojnë vegla shtesë, kallëpe të specializuara ose cikle më të gjata, duke rritur koston e përgjithshme të prodhimit.
- Përzgjedhja e materialit:Zgjedhja e materialit termoplastik ndikon në koston e derdhjes me injeksion. Materialet e ndryshme kanë çmime të ndryshme për kilogram dhe faktorë të tillë si disponueshmëria e materialit, vetitë dhe kërkesat e përpunimit mund të ndikojnë në koston e përgjithshme të materialit.
- Veglat dhe dizajni i kallëpit: Kostot fillestare të veglave dhe projektimit të kallëpit janë të rëndësishme në kostot e formimit me injeksion. Faktorë të tillë si kompleksiteti i mykut, numri i zgavrave, madhësia e mykut dhe materiali i mykut kontribuojnë në shpenzimet e përpunimit dhe prodhimit të mykut. Kallëpe më komplekse ose kallëpe që kërkojnë veçori të avancuara mund të rrisin investimin paraprak.
- Vëllimi i prodhimit: Vëllimi i prodhimit ndikon drejtpërdrejt në koston për pjesë në formimin me injeksion. Librat më të lartë shpesh rezultojnë në ekonomi të shkallës, duke ulur koston për pjesë. Në të kundërt, prodhimi me volum të ulët mund të shkaktojë tarifa më të larta për shkak të konfigurimit, veglave dhe mbetjeve materiale.
- Koha e ciklit: Koha e ciklit, e cila përfshin fazat e ftohjes dhe nxjerrjes, ndikon në kapacitetin e prodhimit dhe koston e përgjithshme. Kohët më të gjata të ciklit rezultojnë në ulje të prodhimit të prodhimit dhe çmime potencialisht më të larta. Optimizimi i modelit të kallëpit, sistemit të ftohjes dhe parametrave të procesit mund të minimizojë kohën e ciklit dhe të përmirësojë efikasitetin.
- Kërkesat e cilësisë:Kërkesat e rrepta të cilësisë ose çertifikatat specifike mund të ndikojnë në koston e derdhjes me injeksion. Përmbushja e tolerancave të sakta, kërkesave për përfundimin e sipërfaqes ose testimi shtesë mund të kërkojë burime, procese ose inspektime të tjera, duke shtuar koston e përgjithshme.
- Operacionet dytësore:Nëse pjesët e derdhura kërkojnë operacione të pas-përpunimit si montimi, lyerja ose hapat shtesë të përfundimit, këto operacione mund të rrisin koston e përgjithshme të derdhjes me injeksion.
- Furnizuesi dhe Vendndodhja:Zgjedhja e furnizuesit të derdhjes me injeksion dhe vendndodhja e tyre mund të ndikojë në kostot. Kostot e punës, shpenzimet e përgjithshme, logjistika dhe shpenzimet e transportit ndryshojnë në bazë të vendndodhjes së furnizuesit, duke ndikuar në koston e përgjithshme të prodhimit.
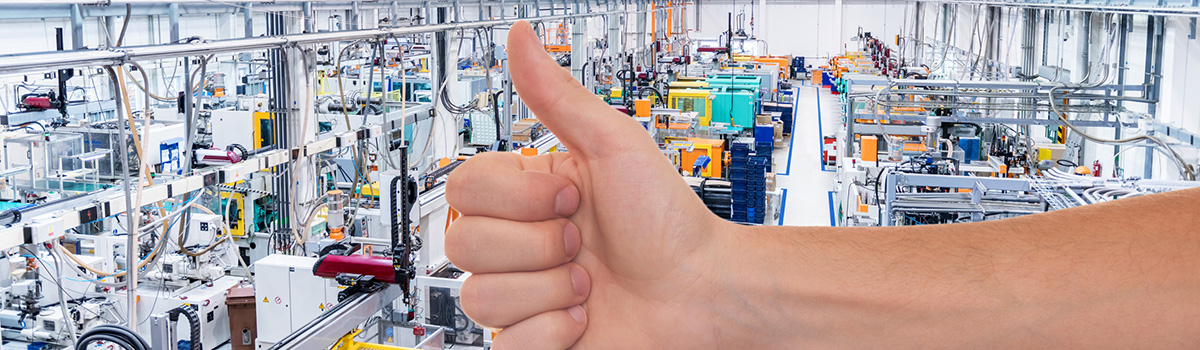
Kontrolli i cilësisë në derdhje me injeksion
Zbatimi i masave të fuqishme të kontrollit të cilësisë gjatë gjithë procesit të formimit me injeksion ndihmon në identifikimin dhe adresimin e defekteve, devijimeve ose mospërputhjeve të mundshme, duke siguruar prodhimin e pjesëve me cilësi të lartë që plotësojnë specifikimet dhe kërkesat e klientit.
- Monitorimi i procesit: Monitorimi i vazhdueshëm i parametrave kyç të procesit, si temperatura e shkrirjes, presioni i injektimit, koha e ftohjes dhe koha e ciklit, siguron qëndrueshmëri dhe përsëritshmëri në prodhimin e pjesëve. Monitorimi në kohë reale dhe sistemet e automatizuara mund të zbulojnë ndryshime ose devijime nga parametrat e caktuar, duke lejuar rregullime në kohë dhe duke ruajtur stabilitetin e procesit.
- Inspektimi dhe matja:Rishikimi dhe matja e rregullt e pjesëve të derdhura janë thelbësore për të verifikuar saktësinë e dimensioneve, cilësinë e pjesës dhe respektimin e specifikimeve. Shërbimet tona mbulojnë një sërë metodash të kontrollit të cilësisë, të tilla si matja e dimensioneve, analizimi i cilësisë së sipërfaqes, kryerja e inspektimeve vizuale dhe kryerja e testeve funksionale. Teknika të ndryshme inspektimi, të tilla si makinat matëse të koordinatave (CMM) dhe sistemet e inspektimit optik dhe vizual, përdoren për vlerësim të saktë.
- Kontrolli i Procesit Statistikor (SPC): SPC përfshin mbledhjen dhe analizimin e të dhënave të procesit për të monitoruar dhe kontrolluar cilësinë e derdhjes me injeksion. Metodat statistikore, të tilla si grafikët e kontrollit dhe analiza e aftësive të procesit, ndihmojnë në identifikimin e tendencave, zbulimin e variacioneve të procesit dhe sigurojnë që procesi të mbetet brenda kufijve të përcaktuar të kontrollit. SPC mundëson identifikimin proaktiv të çështjeve dhe lehtëson optimizimin e procesit.
- Testimi i materialit: Testimi i lëndëve të para, të tilla si termoplastikët, aditivët dhe ngjyruesit, siguron cilësinë dhe përshtatshmërinë e tyre për formimin me injeksion. Testimi i materialit mund të përfshijë analizën e indeksit të rrjedhës së shkrirjes (MFI), vetitë mekanike, karakteristikat termike dhe përbërjen e materialit. Verifikimi i cilësisë së materialit ndihmon në parandalimin e defekteve dhe mospërputhjeve në pjesët e derdhura.
- Mirëmbajtja dhe inspektimi i veglave:Mirëmbajtja e duhur dhe inspektimi i rregullt i kallëpeve të injektimit janë thelbësore për sigurimin e cilësisë në formimin me injeksion. Pastrimi, lubrifikimi dhe vlerësimi i rregullt i përbërësve të mykut ndihmojnë në parandalimin e konsumimit, dëmtimit ose degradimit që mund të ndikojë në cilësinë e pjesës. Riparimi ose zëvendësimi në kohë i komponentëve të mykut të konsumuar ose të dëmtuar është thelbësor për të ruajtur performancën e qëndrueshme të formimit.
- Dokumentacioni dhe gjurmueshmëria:Mbajtja e dokumentacionit gjithëpërfshirës dhe regjistrimeve të gjurmueshmërisë është thelbësore për kontrollin e cilësisë në formimin me injeksion. Është jetike të regjistrohen parametrat e procesit, rezultatet e inspektimit, informacioni i materialit dhe çdo ndryshim apo rregullim i bërë gjatë prodhimit. Dokumentacioni i duhur mundëson gjurmueshmërinë e pjesëve, lehtëson analizën e shkakut rrënjësor dhe siguron qëndrueshmëri në cilësi.
- Trajnimi dhe zhvillimi i aftësive: Ofrimi i programeve adekuate të trajnimit dhe zhvillimit të aftësive për operatorët, teknikët dhe personelin e kontrollit të cilësisë rrit të kuptuarit e tyre për proceset e formimit me injeksion, kërkesat e cilësisë dhe teknikat e inspektimit. Personeli i trajnuar mirë mund të zbulojë defekte, të zgjidhë problemet dhe të zbatojë masa korrigjuese në mënyrë efektive, duke siguruar prodhim me cilësi të lartë.
Defektet e zakonshme të derdhjes me injeksion dhe si t'i shmangni ato
Inspektimi, monitorimi dhe analiza e rregullt e proceseve të formimit me injeksion dhe mirëmbajtja dhe rregullimi i duhur i pajisjeve dhe kallëpeve mund të ndihmojnë në identifikimin dhe adresimin e këtyre defekteve të zakonshme.
- Shenjat e lavamanit:Shenjat e lavamanit janë zhytje ose dhëmbëzime në sipërfaqen e pjesës së derdhur të shkaktuar nga ftohja ose tkurrja e pabarabartë. Duhet të merret parasysh vendndodhja dhe dizajni i duhur i portës, dizajni optimal i sistemit të ftohjes dhe shpërndarja uniforme e trashësisë së murit për të shmangur shenjat e lavamanit. Rritja e presionit të injektimit ose rregullimi i kohës së ftohjes mund të ndihmojë gjithashtu në minimizimin e shenjave të lavamanit.
- Lufta:Deformimi i referohet deformimit ose përkuljes së një pjese të derdhur pas nxjerrjes për shkak të ftohjes së pabarabartë ose streseve të mbetura. Ruajtja e trashësisë uniforme të murit, përdorimi i kanaleve të duhura ftohëse dhe sigurimi i mbushjes dhe paketimit të ekuilibruar të mykut janë thelbësore për të parandaluar shtrembërimin. Optimizimi i temperaturës së mykut, përdorimi i këndeve të përshtatshme të rrymës dhe kontrolli i temperaturës së materialit dhe shpejtësisë së injektimit mund të ndihmojnë në minimizimin e shtrembërimit.
- Flash:Ndezja ndodh kur materiali i tepërt derdhet në vijën e ndarjes së mykut, duke rezultuar në projeksione të holla, të padëshiruara ose materiale shtesë në pjesën përfundimtare. Dikush mund të parandalojë në mënyrë efektive ndezjen duke siguruar dizajnin e duhur të mykut, duke përfshirë aplikimin e forcës adekuate shtrënguese, shtrirjen e saktë dhe përdorimin e teknikave të përshtatshme të ventilimit. Optimizimi i parametrave të procesit si presioni i injektimit, temperatura dhe koha e ciklit redukton blicin.
- Gjuajtje e shkurtër:Një goditje e shpejtë ndodh kur materiali i injektuar nuk mbush zgavrën e mykut, duke rezultuar në një pjesë jo të plotë. Zgjedhja e duhur e materialit, sigurimi i temperaturës dhe viskozitetit adekuat të shkrirjes dhe mbajtja e presionit dhe kohës së duhur të injektimit janë thelbësore për të shmangur fotot e shkurtra. Për më tepër, verifikimi i dizajnit të kallëpit për madhësinë e mjaftueshme të vrapuesit dhe portës dhe ventilimin e duhur mund të ndihmojë në parandalimin e goditjeve të shpejta.
- Linjat e saldimit:Linjat e saldimit ndodhin kur dy ose më shumë fronte të rrjedhës së materialit të shkrirë takohen dhe ngurtësohen, duke rezultuar në një vijë ose shenjë të dukshme në sipërfaqen e pjesës. Dizajni i mirë i portës dhe kontrabandës, temperatura optimale e shkrirjes, shpejtësia e injektimit dhe rregullimi i rrjedhës së materialit dhe gjeometrisë së pjesëve mund të minimizojnë linjat e saldimit. Analiza e rrjedhës së mykut dhe optimizimi i vendosjes së portës mund të ndihmojnë gjithashtu në parandalimin ose zbutjen e linjave të saldimit.
- Shenjat e djegies:Shenjat e djegies janë njolla ose njolla të zeza në sipërfaqen e pjesës së derdhur të shkaktuar nga nxehtësia e tepërt ose mbinxehja e materialit. Shmangia e temperaturës ekstreme të shkrirjes, përdorimi i kanaleve të përshtatshme të ftohjes dhe optimizimi i kohës së ciklit mund të ndihmojnë në parandalimin e shenjave të djegies. Ventilimi i duhur, dizajni i duhur i portës dhe kontrolli i temperaturës së mykut kontribuojnë gjithashtu në minimizimin e shenjave të djegies.
Operacionet pas derdhjes: Mbarimi dhe montimi
Pas formimit me injeksion, shumë pjesë të derdhura mund të kërkojnë operacione shtesë përfundimi dhe montimi për të arritur produktin përfundimtar të dëshiruar. Këto operacione pas derdhjes mund të përfshijnë:
- Shkurtimi:Hiqni çdo material të tepërt ose blic rreth pjesës së derdhur duke përdorur mjete prerëse ose prerëse.
- Trajtim sipërfaqësor:Përmirësimi i pamjes ose funksionalitetit të sipërfaqes së pjesës duke përdorur teknika të ndryshme si lyerja, veshja ose teksturimi.
- Kuvendi:Bashkimi i shumë pjesëve të derdhura ose shtimi i komponentëve të tillë si mbërthyes, futje ose etiketa për të përfunduar produktin përfundimtar.
- Duke testuar:Verifikimi i cilësisë dhe funksionalitetit të pjesës përmes metodave të ndryshme të testimit si analiza dimensionale, testimi i vetive të materialit ose testimi i performancës.
- Paketimi dhe Transporti:Paketimi dhe etiketimi i duhur i produktit të përfunduar për dërgim tek klientët ose përdoruesit fundorë.
Zgjedhja e operacioneve pas derdhjes varet nga aplikimi specifik dhe karakteristikat e dëshiruara të produktit përfundimtar. Bashkëpunimi i ngushtë ndërmjet ekspertëve të derdhjes me injeksion, specialistëve të përfundimit dhe montimit dhe klientit është thelbësor për arritjen e cilësisë dhe funksionalitetit të dëshiruar absolut të produktit. Planifikimi i duhur dhe integrimi i operacioneve pas derdhjes në procesin e prodhimit mund të ndihmojë në sigurimin e prodhimit efikas dhe shpërndarjen në kohë të produkteve me cilësi të lartë.
Formimi me injeksion kundrejt proceseve të tjera të prodhimit të plastikës
Çdo proces i prodhimit të plastikës ka avantazhe dhe kufizime, duke i bërë ato të përshtatshme për aplikime të ndryshme.
- Formimi me injeksion: Formimi me injeksion është një proces prodhimi shumë i gjithanshëm dhe i përdorur gjerësisht për prodhimin e pjesëve plastike. Ai ofron avantazhe të tilla si efikasiteti i lartë i prodhimit, përsëritja e saktë e pjesëve dhe aftësia për të krijuar gjeometri komplekse. Formimi me injeksion është i përshtatshëm për prodhime me volum të lartë dhe lejon përdorimin e një game të gjerë materialesh termoplastike. Ofron saktësi të shkëlqyer dimensionale dhe përfundim sipërfaqësor, duke e bërë atë ideal për industri të ndryshme si automobilat, mallrat e konsumit dhe pajisjet mjekësore.
- Formimi me fryrje: Formimi me fryrje është një proces që përdoret kryesisht për prodhimin e pjesëve të zbrazëta plastike, të tilla si shishet, kontejnerët dhe komponentët e automobilave. Ai përfshin shkrirjen e plastikës dhe fryrjen e saj në një zgavër myku, duke krijuar formën e dëshiruar. Formimi me fryrje është i përshtatshëm për prodhim me volum të lartë dhe mund të prodhojë pjesë të mëdha, të lehta me trashësi uniforme të murit. Sidoqoftë, ai është i kufizuar për sa i përket kompleksitetit të pjesës dhe përzgjedhjes së materialit në krahasim me formimin me injeksion.
- Termoformimi:Termoformimi është një proces që përdoret për të prodhuar pjesë plastike duke ngrohur një fletë termoplastike dhe duke i dhënë formë duke përdorur kallëpe ose formim me vakum. Ajo gjen përdorim të zakonshëm në paketim, produkte të disponueshme dhe produkte në shkallë të gjerë si tabaka dhe mbulesa. Thermoforming ofron prodhim me kosto efektive për pjesë të mëdha dhe lejon prototipimin e shpejtë. Sidoqoftë, ai ka kufizime në lidhje me kompleksitetin e pjesës, përzgjedhjen e materialit dhe saktësinë e dimensioneve në krahasim me formimin me injeksion.
- nxjerrje:Nxjerrja është një proces i vazhdueshëm për të prodhuar profile plastike, fletë, tuba dhe filma. Ai përfshin shkrirjen e rrëshirës plastike dhe shtyrjen e saj përmes një mbulesë për të krijuar formën e dëshiruar. Ekstrudimi është i përshtatshëm për prodhimin e produkteve plastike me gjatësi të gjatë dhe të vazhdueshme me një seksion kryq të qëndrueshëm. Ndërsa nxjerrja ofron shkallë të lartë prodhimi dhe kosto-efektivitet, ai është i kufizuar në aspektin e gjeometrive komplekse të pjesëve dhe kontrollit të saktë të dimensioneve në krahasim me formimin me injeksion.
- Formimi me kompresim:Formimi me ngjeshje përfshin vendosjen e një sasie të para-matur të materialit termofiksues në një zgavër të nxehtë të mykut dhe ngjeshjen e tij nën presion të lartë derisa të shërohet. Ai gjen përdorim të zakonshëm në prodhimin e pjesëve me qëndrueshmëri të lartë dhe stabilitet dimensionale, të tilla si komponentët e automobilave dhe izolimi elektrik. Formimi me ngjeshje ofron qëndrueshmëri të mirë të pjesës, efikasitet të lartë prodhimi dhe aftësi për të përdorur një gamë të gjerë materialesh. Sidoqoftë, ai është i kufizuar për sa i përket kompleksitetit të pjesës dhe kohës së ciklit në krahasim me formimin me injeksion.
Aplikimet e derdhjes me injeksion termoplastik
Industri të ndryshme përdorin gjerësisht formimin me injeksion termoplastik për shkak të shkathtësisë, efikasitetit dhe kostos së tij. Disa nga aplikimet e formimit me injeksion termoplastik përfshijnë:
- Industrinë e automobilave: Industria e automobilave përdor gjerësisht formimin me injeksion termoplastik për të prodhuar komponentë të ndryshëm, duke përfshirë veshjet e brendshme dhe të jashtme, panelet e dyerve, parakolpët dhe lidhësit elektrikë. Procesi lejon përsëritje të saktë të pjesëve, gjeometri komplekse dhe materiale të lehta, duke përmirësuar efikasitetin e karburantit dhe fleksibilitetin e dizajnit.
- Mallrat e konsumit:Formimi me injeksion gjen aplikime të gjera në prodhimin e mallrave të konsumit si pajisjet shtëpiake, pajisjet elektronike, kontejnerët e paketimit dhe lodrat. Procesi mundëson prodhimin masiv të produkteve të qëndrueshme, me cilësi të lartë, me dimensione të qëndrueshme dhe përfundim sipërfaqësor. Ai gjithashtu lejon opsionet e personalizimit dhe përsëritjet e shpejta të produktit.
- Pajisjet mjekësore:Formimi me injeksion luan një rol vendimtar në industrinë mjekësore për prodhimin e një game të gjerë pajisjesh, duke përfshirë shiringat, instrumentet kirurgjikale, komponentët e implantueshëm dhe sistemet e shpërndarjes së barnave. Procesi siguron prodhimin e pjesëve sterile, precize dhe biokompatibile që plotësojnë kërkesat e rrepta rregullatore të sektorit të kujdesit shëndetësor.
- Industria Elektronike dhe Elektrike:Industria e elektronikës përdor formimin me injeksion për të prodhuar lidhëse elektrike, mbyllje, çelsat dhe komponentë të tjerë. Procesi ofron saktësi të lartë dimensionale, përfundim të shkëlqyeshëm të sipërfaqes dhe aftësinë për të inkorporuar veçori të tilla si formimi i futjes dhe formimi i tepërt, duke lejuar prodhimin efikas të montimeve komplekse elektronike.
- Industria e paketimit:Industri të ndryshme, duke përfshirë ushqimin dhe pijet, farmaceutikën dhe kujdesin personal, zakonisht përdorin formimin me injeksion për prodhimin e kontejnerëve, tapave, mbylljeve dhe shisheve të paketimit plastik. Procesi mundëson krijimin e zgjidhjeve të paketimit të lehta, të qëndrueshme dhe estetikisht tërheqëse me cikle prodhimi efikas.
- Industria e hapësirës ajrore:Sektori i hapësirës ajrore përdor formimin me injeksion për prodhimin e komponentëve të lehtë dhe me performancë të lartë si kanalet e ajrit, kllapat, panelet e brendshme dhe pjesët strukturore. Procesi lejon përdorimin e materialeve të avancuara dhe gjeometritë e ndërlikuara të pjesëve, duke kontribuar në uljen e peshës dhe përmirësimin e efikasitetit të karburantit.
Ndikimi mjedisor i derdhjes me injeksion termoplastik
Formimi me injeksion termoplastik është një proces prodhimi popullor për shkak të përfitimeve të shumta, por është gjithashtu thelbësore të merret parasysh ndikimi i tij mjedisor. Këtu janë disa pika për t'u marrë parasysh:
- Efikasiteti i materialit:Formimi me injeksion termoplastik promovon efikasitetin e materialit duke minimizuar mbetjet. Procesi përdor kontroll të saktë mbi sasinë e materialit të injektuar në kallëp, duke reduktuar nevojën për material të tepërt. Prodhuesit mund të përdorin gjithashtu teknika ripërpunimi dhe riciklimi për të ripërdorur skrapin ose pjesët e refuzuara, duke reduktuar më tej mbetjet materiale.
- Konsumim i energjise:Prodhuesit projektojnë makineritë e derdhjes me injeksion që të jenë efikase ndaj energjisë, me modele moderne që përfshijnë teknologji të avancuara si servo motorët dhe disqet me shpejtësi të ndryshueshme. Këto veçori optimizojnë përdorimin e energjisë duke reduktuar konsumin e energjisë gjatë formimit, duke rezultuar në kërkesa më të ulëta për energji dhe reduktim të ndikimit mjedisor.
- Menaxhimi i mbeturinave:Ndërsa minimizojnë mbetjet materiale, prodhuesit duhet të zbatojnë praktikat e duhura të menaxhimit të mbetjeve për të trajtuar materialet e mbetura, sprutat ose rrëshqitësit. Prodhuesit mund të krijojnë programe riciklimi për të mbledhur dhe ripërdorur mbetjet plastike të krijuara gjatë derdhjes me injeksion, duke reduktuar kështu mbetjet e dërguara në deponi.
- Reduktimi i emetimeve: Formimi me injektim termoplastik përgjithësisht gjeneron emetime më të ulëta se proceset e tjera të prodhimit. Prodhuesit mund të reduktojnë emetimet duke përdorur materiale miqësore me mjedisin, duke zbatuar pajisje me efikasitet energjetik dhe duke përdorur sisteme të avancuara të shkarkimit dhe filtrimit për të kapur çdo emetim të lëshuar.
- Zgjedhje të qëndrueshme materiale:Përzgjedhja e materialeve termoplastike mund të ndikojë ndjeshëm në qëndrueshmërinë mjedisore të formimit me injeksion. Zgjedhja për plastikë të biodegradueshme ose me bazë bio, si dhe materiale të riciklueshme ose të riciklueshme, mund të ndihmojë në reduktimin e gjurmës së përgjithshme ekologjike të procesit.
Konsideratat e ciklit jetësor: Marrja në konsideratë e të gjithë ciklit jetësor të produktit të derdhur është thelbësore për vlerësimin e ndikimit të tij mjedisor. Gjatë fazave të projektimit dhe përzgjedhjes së materialit, prodhuesit duhet të marrin në konsideratë faktorë të tillë si qëndrueshmëria e pjesës, riciklimi i saj dhe potenciali për asgjësimin ose ripërdorimin në fund të jetës.
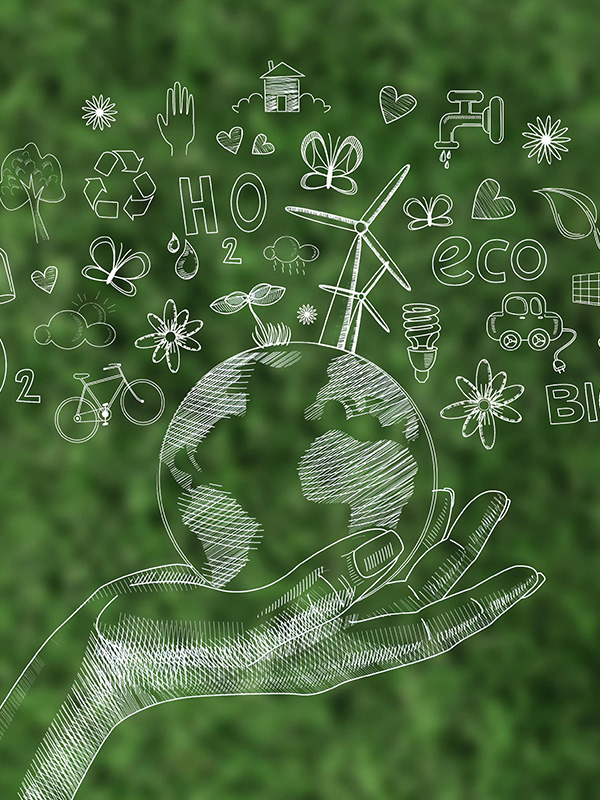
E ardhmja e derdhjes me injeksion termoplastik
E ardhmja e formimit me injeksion termoplastik duket premtuese, me përparime të vazhdueshme në teknologji dhe rritje të kërkesës për pjesë me cilësi të lartë dhe precize në industri të ndryshme. Disa nga zhvillimet kryesore që priten në vitet e ardhshme përfshijnë:
- Rritja e përdorimit të automatizimit dhe robotikës për të përmirësuar efikasitetin dhe për të ulur kostot.
- Përpjekjet janë të përqendruara në zhvillimin e materialeve dhe proceseve të reja për të përmirësuar performancën e pjesëve dhe për të mundësuar aplikime të reja.
- Është një adoptim në rritje i praktikave të qëndrueshme, të tilla si përdorimi i materialeve të ricikluara dhe optimizimi i konsumit të energjisë, për të reduktuar ndikimin mjedisor të derdhjes me injeksion.
- Integrim më i madh i teknologjive dixhitale, të tilla si printimi 3D dhe softueri simulues, për të përmirësuar proceset e projektimit dhe prodhimit.
Tregu global i derdhjes me injeksion po zgjerohet, veçanërisht në ekonomitë në zhvillim, i nxitur nga kërkesa në rritje për produkte plastike në industri të ndryshme.
Zgjedhja e partnerit të duhur të derdhjes me injeksion
Zgjedhja e partnerit të duhur të derdhjes me injeksion është thelbësore për suksesin e projektit tuaj. Merrni kohë për të vlerësuar opsionet e shumta, për të kryer vizita në terren dhe për t'u angazhuar në diskutime të plota për të siguruar një partneritet të pajtueshëm dhe afatgjatë.
- Ekspertiza dhe përvoja:Kërkoni një partner të derdhjes me injeksion me njohuri dhe përvojë të gjerë në industri. Ata duhet të kenë një histori të dëshmuar për ofrimin e produkteve dhe zgjidhjeve me cilësi të lartë për klientët në sektorë të ndryshëm. Merrni parasysh të kuptuarit e tyre për materialet e ndryshme, modelet e mykut dhe proceset e prodhimit.
- Aftësitë e prodhimit: Vlerësoni aftësitë prodhuese të partnerit të derdhjes me injeksion. Sigurohuni që ata të kenë një strukturë të pajisur mirë me makineri dhe teknologji moderne për të përballuar kërkesat e projektit tuaj. Merrni parasysh kapacitetin e tyre të prodhimit, aftësinë për të trajtuar madhësi dhe kompleksitete të ndryshme të pjesëve, dhe aftësinë për të përmbushur vëllimet dhe afatet kohore të dëshiruara të prodhimit.
- Sigurimi i Cilësisë:Cilësia është parësore në formimin me injeksion. Vlerësoni sistemet e kontrollit të cilësisë dhe certifikatat e partnerit të mundshëm. Kërkoni partnerë që ndjekin standarde strikte të cilësisë, kanë procese të forta inspektimi dhe kryejnë testime gjithëpërfshirëse për të siguruar cilësinë dhe qëndrueshmërinë e pjesëve.
- Dizajn dhe mbështetje inxhinierike:Një partner i besueshëm i derdhjes me injeksion duhet të ofrojë mbështetje të projektimit dhe inxhinierisë për të optimizuar dizajnin tuaj të pjesës për prodhimtari. Ata duhet të kenë inxhinierë të aftë që mund të ofrojnë të dhëna të vlefshme për zgjedhjen e materialit, dizajnin e kallëpeve dhe optimizimin e procesit për të rritur cilësinë dhe efikasitetin e pjesëve.
- Konkurrueshmëria e kostos:Ndërsa kostoja nuk duhet të jetë faktori i vetëm përcaktues, është thelbësore të vlerësohet çmimi dhe konkurrueshmëria e kostos së partnerit të derdhjes me injeksion. Kërkoni kuota të detajuara dhe merrni parasysh kostot e veglave, kostot e materialeve, kostot e punës dhe çdo shërbim shtesë që ato ofrojnë.
- Komunikimi dhe Bashkëpunimi:Komunikimi dhe bashkëpunimi efektiv janë thelbësore për një partneritet të suksesshëm. Sigurohuni që partneri i formimit të injektimit të ketë kanale të mira komunikimi, të përgjigjet ndaj pyetjeve tuaja dhe mund të sigurojë përditësime të rregullta të projektit. Një qasje bashkëpunuese do të ndihmojë që ne të përmbushim kërkesat tuaja dhe të adresojmë menjëherë çdo sfidë.
- Referencat dhe vlerësimet e klientëve:Kërkoni referenca të klientëve ose lexoni komente / dëshmi për të fituar njohuri mbi përvojat e klientëve të tjerë me partnerin e formimit të injektimit. Marrja e këtij informacioni mund të ndihmojë në përcaktimin e besueshmërisë, shpejtësisë dhe nivelit të përgjithshëm të kënaqësisë së klientit.
Përfundim
Formimi me injeksion termoplastik është një metodë e gjithanshme dhe me kosto efektive për prodhimin e pjesëve plastike në sasi të mëdha. Aftësia e tij për të prodhuar forma komplekse me saktësi dhe konsistencë të lartë është bërë një zgjedhje popullore për industri të ndryshme, duke përfshirë automobila, mjekësi, elektronikë dhe mallra të konsumit. Duke kuptuar aspektet e ndryshme të formimit me injeksion termoplastik, duke përfshirë avantazhet, disavantazhet dhe konsideratat e dizajnit të tij, ju mund të merrni vendime të informuara për zgjedhjen e partnerit të duhur të derdhjes me injeksion për nevojat e biznesit tuaj.