Formim me injeksion plastik me porosi
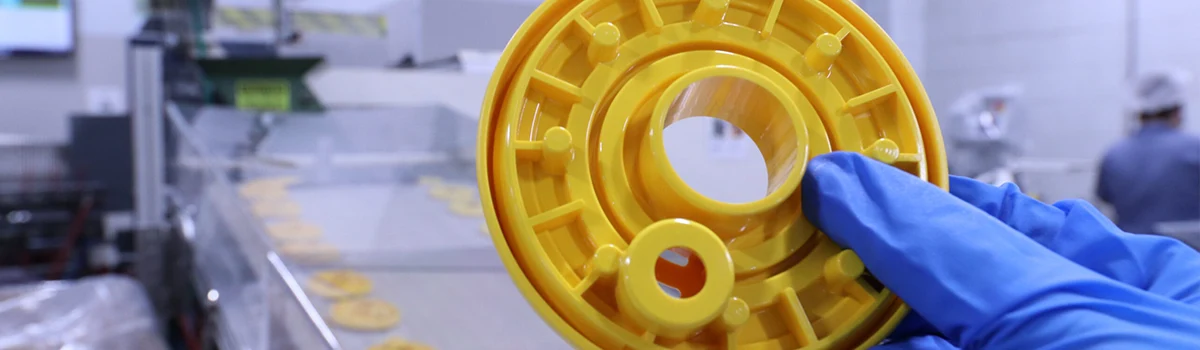
Formimi me injeksion me porosi është ideal për pjesët plastike ku suksesi mbështetet në arritjen e veçorive specifike mekanike ose estetike. Formimi me injeksion plastik DJmolding drejtohet nga qëllimi themelor për të ndihmuar klientët të prodhojnë pjesët më të mira plastike. Nuk është i panjohur për kompleksitetin, sfidat e dizajnit me të vërtetë nxisin dëshirën tonë për të inovuar për ju. Përfshirja e hershme na mundëson të shtojmë vlerë në procesin e projektimit.
Përfitimet e derdhjes me injeksion plastik
Karakteristikat e hollësishme
Merrni parasysh detajet estetike ose funksionale për të përmirësuar markën tuaj: tekst të stampuar, sipërfaqe kozmetike ose me teksturë, dekorim në kallëp, përshtatje të parakohshme, mentesha fleksibël, fortësi të ndryshme.
Efikasitet i lartë
Efikasiteti i formimit me injeksion plastik është i pakrahasueshëm. Ne krijojmë kosto të panevojshme nga pjesa dhe mjeti juaj. Inxhinierët tanë të projektimit me mandat të gjatë dhe mjeshtrit e modelimit shkëlqejnë vërtet në këtë.
Përmirësim i performancës
Ne punojmë shumë për të kuptuar funksionin e synuar të pjesës suaj dhe për të përmbushur objektivat tuaja kryesore duke zbatuar shkencën e materialit, parimet e projektimit, mjetet analitike dhe kontrollet e procesit.
Larmia e materialeve
Zgjidhni nga më shumë se 200 materiale, produkte dhe rrëshira inxhinierike. Ne do t'ju ndihmojmë të balanconi performancën dhe çmimin dhe të identifikoni ekuivalentët e materialeve alternative për të ulur kostot.
Procesi i derdhjes me injeksion
Formimi me injektim të plastikës është një nga metodat më të vjetra të prodhimit të plastikës dhe një hap kritik në zhvillimin e pjesëve për prodhuesit e produkteve. Është gjithashtu një zgjidhje e shkëlqyer për prodhuesit që kërkojnë të konvertojnë pjesët e metaleve të rënda në plastikë. I shpjeguar në formën e tij më të thjeshtë, procesi përdor polimere ose rrëshira plastike që kur nxehen, shkrihen dhe injektohen nën presion të lartë në një kallëp të personalizuar, do të prodhojnë pjesë plastike që do të përdoren në prodhimin e produktit.
Ndërsa ky proces duket i drejtpërdrejtë, ai në fakt mund të jetë mjaft kompleks dhe kërkon një nivel të lartë eksperience nga një partner i modelit të injektimit që mund të plotësojë nevojat tuaja unike të industrisë, specifikimet, përdorimet përfundimtare dhe kufizimet kohore / buxhetore. Vendi më i mirë për të filluar është duke fituar njohuri bazë për procesin e formimit të plastikës dhe praktikat më të mira të projektimit.
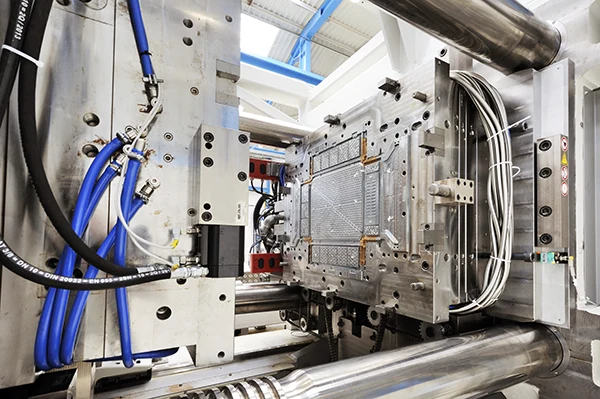
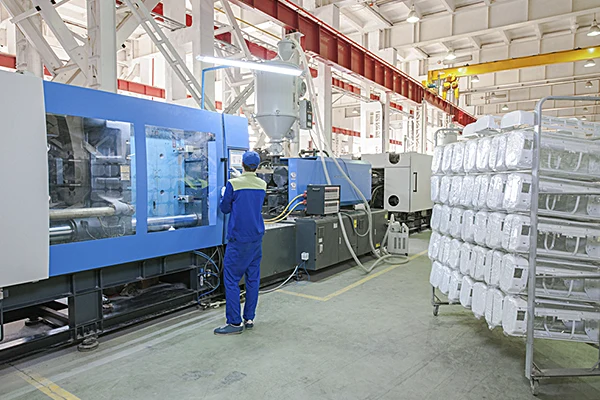
Formimi shkencor
Një qasje e formimit shkencor përfiton prodhimin e pjesëve kritike që kërkojnë performancë specifike dhe saktësi të lartë. Teknologjia jonë e avancuar e formimit siguron përsëritshmëri dhe qëndrueshmëri. Kjo do të thotë se produkti që bëjmë për ju sot, është produkti që bëjmë për ju nesër.
Formimi shkencor me injeksion fillon gjatë zhvillimit të veglave. Faktorë të tillë si presioni, temperatura, koha e mbushjes së zgavrës janë optimizuar në mënyrë që dizajni i kallëpit të minimizojë mundësitë për ndryshim. Analiza e rrjedhës së mykut tregon zonat e fundit të pjesës që duhet të mbushet, si do të orientohet materiali me mykun dhe ekspozon pikat e mundshme të shtrembërimit dhe stresit. Është një hap proaktiv që ofron analiza dhe matje parashikuese inxhinierike dhe lejon përcaktimin e lehtë të suksesit ose dështimit të një pjese ose projekti.
Proceset e fuqishme të prodhimit përdorin më tej një qasje shkencore përmes monitorimit dhe kontrolleve të automatizuara të procesit, gjë që redukton skrapin dhe kohën e përpunimit. Nëse ndodh një ndryshim ose mosfunksionim, ai identifikohet dhe izolohet shpejt përpara se të bëhen pjesë jo konformuese.
overmolding
Dy (ose më shumë) materiale mund të kombinohen në një pjesë të vetme me mbiformim. Ky proces përdoret shpesh për një sipërfaqe të veçantë prekëse, të tilla si një zonë më e butë e kapjes. Mbiformimi mund të jetë plastik mbi nënshtresën plastike ose gome mbi nënshtresën plastike, zakonisht realizohet nga një proces formimi me injeksion me dy goditje. Formulimi dhe ngjyrat e rrëshirës mund të ndryshojnë. Përparësitë estetike të mbiformimit janë të lehta për t'u vërejtur, por ato gjithashtu eliminojnë operacionet dytësore. Mbiformimi është i përsosur për veglat me dore, objekte dore, robotikë ku nevojiten kapëse gome ose thjesht për të përmirësuar pamjen e një pjese me ngjyra të dallueshme.
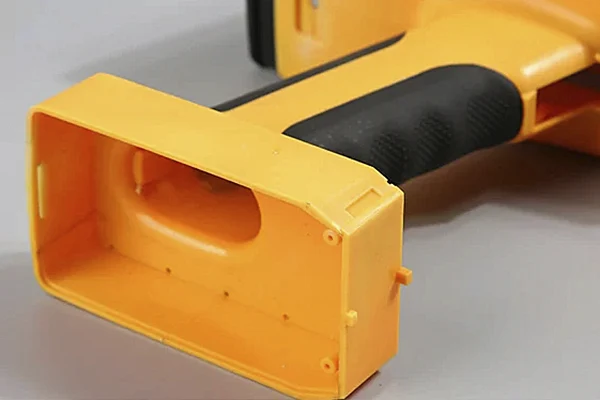
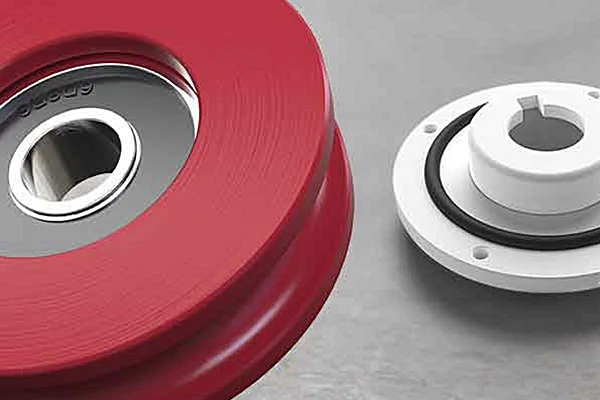
Insert Moulding
Formimi i futur është i ngjashëm me formimin e tepërt, por përfshin një objekt që vendoset brenda një zgavër myku. Vendosni lidhjet e derdhura plastike në futje, zakonisht metalike ose plastike. Futjet e filetuara janë të zakonshme. Kjo eliminon punën kur përdoret si një alternativë ndaj lidhësve, ngjitësve ose vendosjes së nxehtësisë. Insertet gjithashtu forcojnë pjesën. Insertet ngarkohen me dorë ose me automatizim robotik.
Dekorimi dhe etiketimi i pjesëve
Dekorimi në myk (IMD) dhe etiketimi në kallëp (IML) përdoren për të krijuar një pamje të mrekullueshme vizualisht me grafikë ose etiketa. Lehtësuar nga robotika dhe kapja elektrostatike ose me vakum, një shtresë e printuar e filmit shtohet në zgavrën e kallëpit përpara injektimit të rrëshirës plastike të shkrirë. Ky proces krijon një lidhje të përhershme midis etiketës dhe pjesës së përfunduar, zakonisht duke eliminuar çdo nevojë për operacione pas përpunimit. Një gamë e gjerë e zgjedhjeve të teksturës, ngjyrës dhe veshjes së sipërfaqes lë derën e hapur për mundësi krijuese. Ne ju inkurajojmë të flisni me menaxherin e projektit tuaj rreth opsioneve për të përmirësuar markën tuaj.
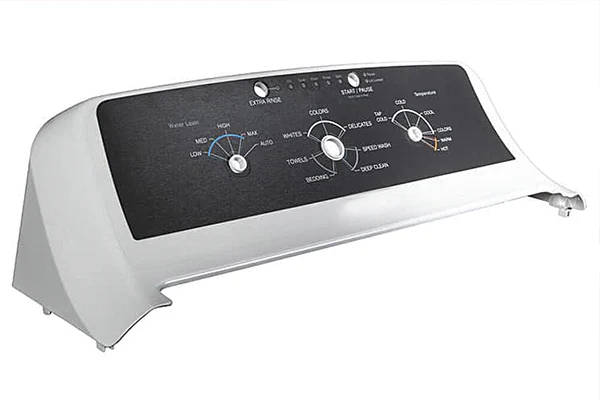
Shërbimi i derdhur me injeksion plastik me porosi Kinë
DJmolding Operon që nga viti 2010 | Certifikatat AFAQ ISO/TS 16949, UL dhe ISO, kryesisht furnizohen me shumë kompani të printimit 3D në botë tani.
Në Djmolding ne jemi të specializuar në prodhimin e pjesëve të derdhura me injeksion plastike me cilësi të lartë dhe mjeteve të mykut. Ne kryesisht furnizojmë prodhimin tonë me injeksion plastik për shumë kompani të printimit 3D në botë. Ne kemi 55 makina për robotikë dhe prodhim automatik të injektimit të plastikës. Ne ofrojmë të gjitha shërbimet e përpunimit dhe përfundimit për të bërë vegla nga një shumëllojshmëri materialesh dhe mund të prodhojmë 100 deri në 200 mijë+ pjesë të përfunduara në të gjitha plastika kryesore. Ajo që vërtet na dallon është verifikimi, inspektimi dhe testimi ynë i avancuar i materialit për të siguruar që pjesët tuaja të përmbushin dhe tejkalojnë pritshmëritë tuaja më të larta. Kontaktoni ekspertët tanë ndërkombëtarë të derdhjes me injeksion për një ofertë falas sot.
Procesi i derdhur me injeksion plastik DJmolding
Pasi mjetet tuaja të mykut të injektimit të plastikës janë gati, procesi i formimit përbëhet nga hapat bazë të mëposhtëm:
Hapi 1. Rrëshira plastike vjen në fishekë të papërpunuar. Këto thahen në përmbajtjen e duhur të lagështisë dhe më pas, nëse është e nevojshme, ato mund të përzihen me pigmente ose ngjyrues të grupit kryesor.
Hapi 2. Peletat e thara derdhen në pleshtin e makinës së derdhjes. Një vidë reciproke brenda fuçisë së makinës do t'i transportojë këto fishekë drejt kallëpit.
Hapi 3. Brenda fuçisë, fishekët përzihen dhe nxehen derisa të shkrihen plotësisht, duke formuar rrëshirën e lëngshme.
Hapi 4. Forma e ngrohur mbyllet automatikisht dhe rrëshira, nën presion të madh, injektohet përmes një porte dhe në zgavrën e kallëpit.
Hapi 5. Forma ftohet për të ngurtësuar pjesën brenda.
Hapi 6. Forma hapet dhe pjesa nxirret për të filluar një cikël të ri.
Tolerancat e derdhjes me injeksion plastik
I gjithë materiali plastik do të zgjerohet dhe tkurret nën ndikimin e nxehtësisë dhe lagështisë. Udhëzuesi ynë i tolerancës do të japë informacion më të përgjithshëm mbi karakteristikat e llojeve më të zakonshme të rrëshirës për veçoritë tipike të pjesëve.
Ne do të punojmë ngushtë me ju për të optimizuar planet tuaja për prodhim. Ne do të tregojmë çdo zonë ku dizajni i dobët mund të shkaktojë stres termik, tkurrje, shtrembërim, etj. Konsultohuni me udhëzuesin tonë të projektimit për më shumë informacion mbi defektet e zakonshme dhe si t'i shmangni ato.
Nëse nuk specifikohet ndryshe, ne jemi në përputhje me tolerancat standarde DIN 16742 për formacionet me injeksion plastik. Lexoni për standardet e cilësisë vizuale që zbatojmë për pjesët e derdhura me injeksion.
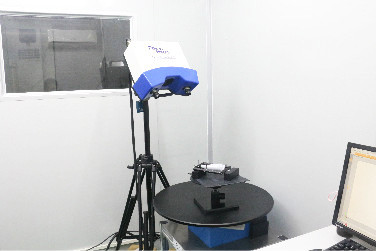
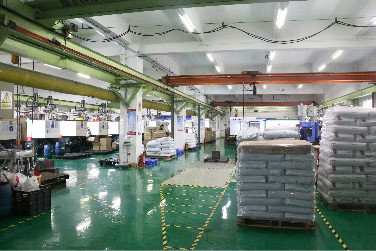
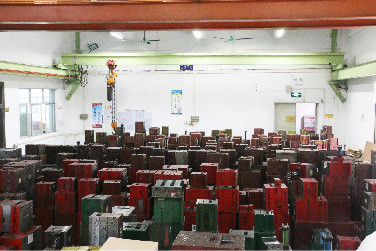
Materialet e derdhura me injeksion plastik
Djmolding prodhon vegla për formim me injeksion dhe materie nga çeliqet gjysmë të ngurtësuar nga alumini 7075, P20 dhe NAK80 dhe çeliku i ngurtësuar plotësisht H13. Për më tepër, ne ofrojmë përfundime standarde SPI, teksturë EDM dhe një sërë tekstesh të gdhendura.
Secili prej këtyre llojeve të materialeve do të ketë avantazhe të dallueshme për aplikime të caktuara. *Konsideratat përfshijnë:
*Kostoja e lëndës së parë
* Qëndrueshmëri dhe rezistencë ndaj korrozionit ose gërryerjes
* Përpunueshmëria
*Aftësia për të marrë një lustrim të lartë të sipërfaqes
*Koha e nevojshme për trajtimin termik
*Jeta e pritshme e mjetit
Kontaktoni specialistët tanë teknikë për të mësuar më shumë se cili është i duhuri për ju.
Pjesë të injektuara plastike
Ka mijëra plastika termoformuese dhe termofikse për të zgjedhur për projektin tuaj. Përveç kësaj, karakteristikat mekanike dhe kimike mund të përmirësohen edhe me aditivë si fibra xhami, stabilizues UV dhe lubrifikantë. Fleta jonë e materialeve do t'ju japë informacion më të detajuar në lidhje me llojet standarde dhe tolerancat që priten me secilin.
Zgjedhja juaj e rrëshirave mund të varet nga një ose më shumë nga konsideratat e mëposhtme:
*Rezistencë ndaj rrezeve ultraviolet, kimike, gërryerjes dhe goditjes
*Kosto e lëndës së parë
*Forca mekanike
* Pesha dhe dendësia
*Fleksibilitet
*Transparencë
*Riciklimi
Kontaktoni një nga specialistët tanë teknikë për të mësuar më shumë rreth vetive të materialit.
Dyqan injeksioni DJmolding:
Prodhuesi kryesor i kallëpit të injektimit të plastikës dhe i shërbimit të prototipit të shpejtë
Djmolding është një nga kompanitë më të njohura të derdhjes me injeksion plastik në Kinë. Dyqani ynë i derdhjes me injeksion është i pajisur me 50 grupe makinerish të derdhjes me precizion të lartë, që variojnë nga 30 ton në 800 ton, ato importohen kryesisht nga Tajvani dhe Japonia, dyqani ynë i injektimit funksionon 24 orë në ditë, 7 ditë në javë, dhe ofron prodhim shërbimet.
Ne kemi përvojë me produkte të ndryshme plastike për shumë industriale, duke përfshirë: automobila, mjekësi, ndriçim, pajisje sportive, pajisje shtëpiake dhe bujqësi. Djmolding ka kaluar certifikatat AFAQ ISO/TS 16949, UL dhe ISO 9001 që nga viti 2010, ne gjithashtu kemi 15 njerëz IPQC që shikojnë vazhdimisht prodhimin tonë dhe kontrollojnë cilësinë e pjesëve, Kjo siguron që prodhimi ynë të mbajë një nivel më të lartë të cilësisë. Në 9 vitet e fundit, Djmolding ka krijuar një reputacion të fortë për prodhimin e mjeteve dhe pjesëve me cilësi të lartë me një çmim të arsyeshëm. Ne mbajmë marrëdhënie të forta biznesi me appx. 50 klientë, kryesisht nga SHBA dhe Evropa.
Formim me injeksion plastik me porosi
Formimi me injektim i plastikës me porosi është një mënyrë inovative dhe efikase për të prodhuar pjesë plastike me cilësi të lartë. Ky proces prodhimi përdor një kallëp për të formuar materialet plastike në forma dhe madhësi komplekse, duke e bërë atë një zgjidhje ideale për industri të ndryshme. Ky postim në blog do të zhytet thellë në formimin e personalizuar të injektimit të plastikës dhe do të eksplorojë përfitimet, aplikimet dhe praktikat më të mira të tij.
Kuptimi i procesit të formimit me injeksion me porosi
Formimi me injeksion me porosi është një proces prodhimi që përdoret për të prodhuar pjesë plastike në vëllime të mëdha. Ai përfshin shkrirjen e peletave ose granulave plastike dhe injektimin e tyre në një kallëp nën presion të lartë, ku ato ftohen dhe ngurtësohen për të formuar një formë të dëshiruar. Ja se si funksionon procesi i formimit të injektimit:
- Mbërthimi: Dy gjysmat e kallëpit, të quajtura "vegla", janë të shtrënguara së bashku me forcë të mjaftueshme për t'i bërë ballë presionit të injektimit.
- Injeksion: Peletat plastike shkrihen në një fuçi të nxehtë dhe injektohen në kallëp përmes një sistemi vrapues nën presion të lartë. Plastika mbush zgavrën e mykut dhe merr formën e kallëpit.
- Ftohja: Plastika mund të ftohet dhe të ngurtësohet brenda kallëpit për të ruajtur formën e dëshiruar.
- Nxjerrja: myku hapet pasi plastika të jetë ftohur dhe pjesa e përfunduar të hidhet.
- Përsëriteni: Procesi përsëritet më pas për të krijuar pjesë të shumta identike.
Formimi me injeksion prodhon produkte plastike, nga komponentët e vegjël deri te artikujt e mëdhenj si pjesët e automobilave dhe pajisjet shtëpiake. Procesi është shumë efikas dhe mund të prodhojë pjesë me gjeometri komplekse dhe toleranca të ngushta, dhe është gjithashtu i saktë, me humbje minimale dhe shkallë të ulët të skrapit.
Procesi kërkon pajisje të specializuara, duke përfshirë një kallëp, makinë formimi me injeksion dhe një sistem kontrolli për të siguruar rezultate të sakta dhe të qëndrueshme. Forma është bërë zakonisht prej çeliku dhe mund të projektohet për të prodhuar pjesë të shumta duke përdorur formimin me shumë zgavra.
Formimi me injeksion mund të përdoret gjithashtu me materiale të ndryshme, duke përfshirë termoplastikë, termoset dhe elastomerë. Çdo material ka veti unike dhe mund të përshtatet për aplikime specifike.
Në përgjithësi, derdhja me injeksion është një proces prodhimi shumë i gjithanshëm dhe efikas që përdoret gjerësisht në shumë industri.
Avantazhet e formimit me injeksion plastik me porosi
Formimi me injeksion plastik me porosi është një proces prodhimi që përdoret për të krijuar pjesë plastike me porosi në vëllime të mëdha. Këtu janë disa nga avantazhet e këtij procesi:
Efikasitet dhe produktivitet i lartë: Formimi me injektim i plastikës me porosi është një proces shumë efikas që mund të prodhojë vëllime të mëdha të pjesëve identike shpejt dhe vazhdimisht. Kjo e bën atë një zgjedhje ideale për prodhimin masiv të pjesëve plastike.
shkathtësi: Procesi mund të përdoret me një gamë të gjerë materialesh plastike, duke përfshirë termoplastikë, termoset dhe elastomerë. Kjo lejon një shumëllojshmëri të gjerë të dizajneve dhe aplikimeve të pjesëve.
Konsistenca dhe saktësia: Formimi me injeksion siguron rezultate të qëndrueshme dhe të sakta, me toleranca të ngushta dhe ndryshime minimale midis pjesëve. Kjo siguron që çdo pjesë të jetë identike me tjetrën, gjë që është thelbësore për shumë aplikacione.
Kosto-efektive: Formimi me injeksion plastik me porosi mund të jetë me kosto efektive për prodhime me vëllim të lartë. Kostot fillestare të veglave mund të jenë të larta, por kostoja për pjesë zvogëlohet me rritjen e vëllimit.
kompleksiteti: Formimi me injeksion mund të prodhojë pjesë me forma dhe gjeometri komplekse, duke përfshirë mure të hollë dhe karakteristika të ndërlikuara. Kjo mundëson fleksibilitet më të madh të projektimit dhe mundëson prodhimin e faktorëve që do të ishte e vështirë ose e pamundur të prodhoheshin duke përdorur metoda të tjera.
Mbetjet minimale: Formimi me injeksion gjeneron mbetje minimale në krahasim me proceset e tjera të prodhimit, pasi çdo plastikë e tepërt mund të riciklohet dhe ripërdoret.
Përfundojë sipërfaqe: Formimi me injeksion mund të prodhojë pjesë me një përfundim sipërfaqësor me cilësi të lartë pa operacione shtesë pas përpunimit ose përfundimit. Kjo e bën atë një zgjidhje me kosto efektive për krijimin e pjesëve me një pamje të lëmuar dhe të lëmuar.
Automatizimi: Formimi me injeksion mund të automatizohet lehtësisht, me robotë që ngarkojnë dhe shkarkojnë pjesë nga kallëpi dhe inspektojnë dhe renditin veçoritë. Kjo zvogëlon nevojën për punë manuale dhe rrit efikasitetin.
Formimi me injektim i plastikës me porosi është një proces prodhimi shumë i gjithanshëm dhe efikas që ofron shumë përparësi ndaj metodave të tjera. Aftësia e tij për të prodhuar me shpejtësi dhe saktësi vëllime të mëdha të pjesëve identike e bën atë ideal për shumë industri, duke përfshirë automobilat, hapësirën ajrore, mjekësore dhe mallrat e konsumit.
Aplikimet e derdhjes me injeksion
Formimi me injeksion është një proces prodhimi i përdorur gjerësisht për të krijuar produkte të ndryshme plastike industriale. Këtu janë disa nga aplikimet më të zakonshme të derdhjes me injeksion:
- Industria e automobilave: Formimi me injeksion prodhon pjesë të ndryshme të automobilave, duke përfshirë veshjet e brendshme dhe të jashtme, komponentët e pultit, dorezat e dyerve dhe pjesët e motorit. Preferohet sepse mund të ketë karakteristika me forcë të lartë dhe saktësi dimensionale.
- Mallrat e konsumit: Formimi me injeksion krijon produkte të ndryshme të konsumit, duke përfshirë lodrat, pajisjet shtëpiake dhe pajisjet elektronike. Ai lejon prodhimin e formave dhe gjeometrive komplekse dhe përfundime të sipërfaqes me cilësi të lartë.
- Pajisjet mjekësore: Formimi me injeksion përdoret për të prodhuar një sërë pajisjesh mjekësore, duke përfshirë shiringat, komponentët IV dhe pajisjet diagnostikuese. Ofron saktësi të lartë, prodhim të pastër dhe aftësi për të prodhuar pjesë me gjeometri komplekse, të cilat janë thelbësore në industrinë mjekësore.
- Industria e paketimit: Formimi me injeksion prodhon materiale paketimi, duke përfshirë shishe, kavanoza dhe kapakë. Ai lejon krijimin e kontejnerëve të lehtë dhe të qëndrueshëm dhe përshtatjen e ngjyrave, teksturave dhe formave.
- Industria e hapësirës ajrore: Formimi me injeksion përdoret për të prodhuar përbërës të ndryshëm të pjesëve të hapësirës ajrore, duke përfshirë elementë strukturorë dhe pajisje të brendshme. Ai lejon krijimin e materialeve me performancë të lartë që mund të përballojnë temperaturat dhe presionet ekstreme.
- Industria e ndërtimit: Formimi me injeksion prodhon materiale të ndryshme ndërtimi, duke përfshirë gypat PVC, sistemet e ulluqeve dhe materialet e çatisë. Ofron qëndrueshmëri të lartë, rezistencë ndaj motit dhe kimikateve dhe aftësi për të prodhuar pjesë në vëllime të mëdha.
- Industria elektronike: Formimi me injeksion prodhon komponentë të ndryshëm elektronikë, duke përfshirë strehimin, lidhësit dhe çelsat. Ofron saktësi të lartë, uniformitet dhe aftësi për të prodhuar pjesë me gjeometri komplekse, gjë që është thelbësore në industrinë e elektronikës.
Në përgjithësi, derdhja me injeksion është një proces i gjithanshëm prodhimi që mund të prodhojë shumë pjesë plastike për shumë industri. Aftësia e tij për të prodhuar pjesë me gjeometri komplekse, saktësi të lartë dhe cilësi të qëndrueshme e bën atë një zgjedhje popullore për shumë prodhues.
Llojet e materialeve të përdorura në formimin me injeksion
Formimi me injeksion është një proces prodhimi që përfshin injektimin e plastikës së shkrirë në një zgavër të mykut për të krijuar një formë specifike. Materiale të ndryshme mund të përdoren në formimin me injeksion, në varësi të vetive të dëshiruara të produktit përfundimtar. Këtu janë disa nga llojet më të zakonshme të materialeve të përdorura në formimin me injeksion:
- Termoplastikë: Këto janë materialet më të përdorura në formimin me injeksion. Ato janë një lloj plastik që bëhet i butë dhe i formueshëm kur nxehet dhe ngurtësohet kur ftohet. Termoplastikët mund të formohen dhe riformohen disa herë pa humbur vetitë e tyre. Termoplastikët e zakonshëm të përdorur në formimin me injeksion përfshijnë polipropilen, polietileni, polistiren dhe najlon.
- Termoset: Këto janë plastikë që mund të formohen vetëm një herë. Ato nxehen dhe zhvillohen në një formë specifike dhe pasi të ngurtësohen, nuk mund të riformohen. Termoset përdoren për aplikime ku kërkohet forcë dhe qëndrueshmëri e lartë. Termoset e zakonshme që përdoren në formimin me injeksion përfshijnë rrëshirat epoksi, melaminë dhe fenolike.
- Elastomerët: Këto materiale kanë veti elastike dhe mund të shtrihen dhe të kthehen në formën e tyre origjinale. Elastomerët përdoren për aplikime ku kërkohet fleksibilitet dhe thithja e goditjeve. Elastomerët standardë të përdorur në formimin me injeksion përfshijnë gomën, silikonin dhe poliuretani.
- Materialet e biodegradueshme: Këto mund të shpërbëhen natyrshëm në mjedis pa lënë mbetje të dëmshme. Ato përdoren për aplikime ku qëndrueshmëria mjedisore është një shqetësim. Materialet e zakonshme të biodegradueshme të përdorura në formimin me injeksion përfshijnë acidin polilaktik (PLA) dhe polihidroksialkanoatet (PHA).
- Kompozitat janë materiale të bëra duke kombinuar dy ose më shumë materiale të ndryshme për të krijuar një material të ri me veti specifike. Kompozitat përdoren për aplikime ku kërkohet forcë dhe ngurtësi e lartë. Kompozitat standarde të përdorura në formimin me injeksion përfshijnë plastikë të përforcuar me fibra qelqi (GRP) dhe plastikë të përforcuar me fibër karboni (CFRP).
- Plastika e mbushur me metal është plastika e mbushur me grimca metalike për të krijuar materiale me përçueshmëri të lartë elektrike dhe termike dhe veti të tjera specifike. Plastika e mbushur me metal përdoret për aplikime me përçueshmëri të nevojshme elektrike ose termike. Plastika e zakonshme e mbushur me metal që përdoret në formimin me injeksion përfshijnë plastikë të mbushur me bakër dhe plastikë të mbushur me nikel.
Në përgjithësi, zgjedhja e materialit të formimit me injeksion varet nga kërkesat specifike të produktit përfundimtar, duke përfshirë forcën, fleksibilitetin, përçueshmërinë dhe qëndrueshmërinë. Prodhuesit shpesh zgjedhin materiale bazuar në koston, disponueshmërinë, lehtësinë e përpunimit dhe vetitë e kërkuara për produktin përfundimtar.
Faktorët që duhen marrë parasysh kur zgjidhni një material të derdhur me injeksion
Zgjedhja e një materiali të përshtatshëm është thelbësore kur bëhet fjalë për formimin me injeksion, pasi mund të ndikojë në vetitë dhe performancën e produktit përfundimtar. Këtu janë disa nga faktorët që duhen marrë parasysh kur zgjidhni një material të derdhur me injeksion:
- Vetitë mekanike: Një nga faktorët më të rëndësishëm që duhet marrë parasysh kur zgjidhni një material janë vetitë e tij mekanike. Kjo përfshin forcën, ngurtësinë, qëndrueshmërinë dhe rezistencën ndaj konsumit. Vetitë mekanike të kërkuara për produktin përfundimtar do të varen nga aplikimi dhe streset ndaj të cilave produkti do të ekspozohet.
- Vetitë termike: Vetitë termike të një materiali janë gjithashtu të rëndësishme, veçanërisht nëse produkti përfundimtar do të ekspozohet ndaj temperaturave të larta ose ciklit termik. Kjo përfshin pikën e shkrirjes së materialit, përçueshmërinë termike dhe koeficientin e zgjerimit termik.
- Rezistenca kimike: Nëse produkti përfundimtar është i ekspozuar ndaj kimikateve, zgjedhja e një materiali që mund t'i rezistojë degradimit kimik është thelbësor. Materiali duhet t'i rezistojë ekspozimit ndaj acideve, bazave, tretësve dhe kimikateve të tjera pa u prishur ose humbur vetitë e tij.
- Faktorët mjedisorë: Faktorët mjedisorë, të tillë si lagështia dhe ekspozimi ndaj ultravjollcës, mund të ndikojnë gjithashtu në vetitë dhe performancën e një materiali. Është thelbësore të merren parasysh kushtet mjedisore të produktit përfundimtar dhe të zgjidhni një material që mund t'i rezistojë atyre.
- Kostoja: Kostoja e materialit është gjithashtu një konsideratë e rëndësishme, veçanërisht për prodhimet me volum të lartë. Kostoja e materialit duhet të peshohet kundrejt performancës dhe vetive të tij për të siguruar që ai është një zgjedhje me kosto efektive për produktin përfundimtar.
- Kërkesat e përpunimit: Kërkesat e përpunimit për një material mund të ndikojnë gjithashtu në procesin e përzgjedhjes. Disa materiale mund të kërkojnë pajisje ose teknika specifike përpunimi dhe disa mund të jenë më të vështira për t'u përpunuar. Kërkesat e përpunimit duhet të merren parasysh për të siguruar që materiali të përdoret me sukses në procesin e formimit me injeksion.
- Pajtueshmëria rregullatore: Së fundi, është thelbësore të merren parasysh çdo kërkesë rregullatore që produkti përfundimtar duhet të plotësojë. Disa industri, si industria mjekësore dhe ushqimore, kanë rregulla specifike për materialet e përdorura në produktet e tyre. Zgjedhja e një materiali që plotëson këto kërkesa rregullatore është thelbësore për të siguruar që produkti përfundimtar të jetë i sigurt dhe në përputhje.
Në përgjithësi, zgjedhja e materialit të përshtatshëm për formimin me injeksion kërkon shqyrtim të kujdesshëm të faktorëve të ndryshëm, duke përfshirë vetitë mekanike dhe termike, rezistencën kimike, faktorët mjedisorë, koston, kërkesat e përpunimit dhe pajtueshmërinë rregullatore. Prodhuesit duhet t'i peshojnë këta faktorë me njëri-tjetrin për të zgjedhur materialin që është më i përshtatshmi për produktin përfundimtar.
Rëndësia e dizajnit të mykut në formimin me injeksion
Dizajni i mykut është një aspekt kritik i procesit të formimit me injeksion. Dizajni i kallëpit mund të ndikojë në cilësinë e produktit përfundimtar, si dhe në efikasitetin dhe kosto-efektivitetin e procesit të prodhimit. Këtu janë disa nga arsyet pse dizajni i mykut është thelbësor në formimin me injeksion:
- Cilësia e produktit: Dizajni i kallëpit mund të ndikojë në cilësinë e produktit përfundimtar. Nëse kallëpi nuk është projektuar siç duhet, mund të rezultojë në defekte të tilla si deformime, shenja lavamani dhe ndezje. Këto defekte mund ta bëjnë produktin përfundimtar të papërdorshëm, të ulin performancën dhe të rrisin normat e skrapit dhe kostot e prodhimit.
- Efikasiteti i prodhimit: Dizajni i kallëpit mund të ndikojë gjithashtu në efikasitetin e procesit të prodhimit. Nëse kallëpi nuk është projektuar për rrjedhje dhe ftohje optimale, mund të rezultojë në kohë më të gjata cikli, rritje të konsumit të energjisë dhe reduktim të xhiros. Një dizajn i optimizuar i kallëpit mund të përmirësojë efikasitetin dhe të zvogëlojë kostot e prodhimit.
- Kosto-efektiviteti: Dizajni i mykut mund të ndikojë gjithashtu në kosto-efektivitetin e procesit të formimit të injektimit. Një kallëp i projektuar mirë mund të reduktojë mbetjet materiale, të përmirësojë cilësinë e pjesëve dhe të rrisë xhiros, duke ulur kostot e prodhimit. Për më tepër, një kallëp i projektuar për prodhim me volum të lartë mund të zvogëlojë koston për pjesë dhe të rrisë kthimin e investimit.
- Përshtatja: Dizajni i mykut luan gjithashtu një rol jetik në personalizimin e produktit përfundimtar. Duke projektuar kallëpin për forma dhe veçori specifike, prodhuesit mund të krijojnë produkte të përshtatura për nevojat e klientëve të tyre. Kjo mundëson fleksibilitet dhe diferencim më të madh në treg, duke çuar në rritjen e kënaqësisë dhe besnikërisë së klientit.
- Zgjedhja e materialit: Dizajni i kallëpit mund të ndikojë gjithashtu në zgjedhjen e materialit të përdorur në formimin me injeksion. Metoda e formimit mund të ndikojë në rrjedhën dhe ftohjen e materialit, gjë që mund të ndikojë në vetitë mekanike dhe termike të produktit përfundimtar. Duke zgjedhur modelin e duhur të kallëpit, prodhuesit mund të optimizojnë përzgjedhjen e materialit dhe të sigurojnë që produkti përfundimtar të plotësojë kërkesat e dëshiruara të performancës.
Në përgjithësi, dizajni i mykut është një faktor kritik në procesin e derdhjes me injeksion. Një kallëp i projektuar mirë mund të përmirësojë cilësinë e produktit, efikasitetin e prodhimit, efektivitetin e kostos, personalizimin dhe përzgjedhjen e materialit. Prodhuesit duhet të investojnë kohë dhe burime në projektimin e kallëpeve të optimizuara për nevojat e tyre specifike për të arritur rezultatet më të mira të mundshme në procesin e formimit me injeksion.
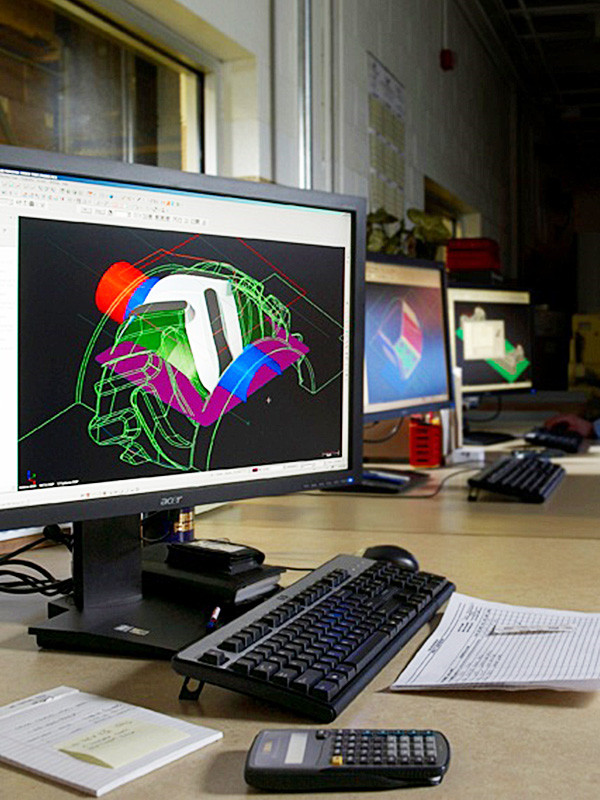
Lloje të ndryshme kallëpësh të përdorur në formimin me injeksion
Formimi me injeksion është një proces i gjithanshëm prodhimi që mund të prodhojë produkte të ndryshme plastike. Një faktor kritik që përcakton cilësinë dhe efikasitetin e formimit me injeksion është lloji i mykut të përdorur. Këtu janë disa nga llojet e ndryshme të kallëpeve të përdorura në formimin me injeksion:
- Kallëp me dy pllaka: Kallëpet me dy pllaka janë kallëpi më i zakonshëm që përdoret në formimin me injeksion. Ato përbëhen nga dy pllaka që ndahen nga një zgavër myku. Materiali plastik injektohet në zgavër, duke kombinuar dy pllakat për të formuar produktin përfundimtar.
- Kallëp me tre pllaka: Format me tre pllaka janë të ngjashëm me kallëpet me dy pllaka, por kanë një pllakë shtesë që ndan sistemin e kalimit nga pjesa e derdhur. Kjo lejon nxjerrjen më të lehtë të pjesës dhe mund të zvogëlojë kohën e ciklit.
- Myku i vrapuesit të nxehtë: Format e nxehta të vrapuesve përdoren për prodhime me volum të lartë, pasi ato mund të reduktojnë kohën e ciklit dhe mbetjet materiale. Forma përmban një sistem vrapues të nxehtë që dërgon plastikë të shkrirë drejtpërdrejt në zgavrën e mykut, duke eliminuar nevojën për një vrapues të ftohtë.
- Myku i vrapuesit të ftohtë: Format e vrapuesit të ftohtë janë lloji më themelor i mykut dhe përbëhen nga një sprue, vrapues dhe një zgavër myku. Plastika e shkrirë injektohet në sprue, e cila e ushqen plastikën në vrapues dhe më pas në zgavrën e mykut.
- Myku familjar: Kallëpet familjare prodhojnë pjesë të shumta në një cikël të vetëm. Myku përmban kavitete të shumta, secila prej të cilave ka një pjesë të ndryshme. Format familjare shpesh përdoren për komponentë të vegjël me volum të lartë.
- Kallëpi i pirgut: Format e pirgut prodhojnë shtresa të shumta plastike në një cikël të vetëm. Kallëpi përmban shtresa të shumta zgavrash, të cilat vendosen njëra mbi tjetrën. Plastika injektohet në vrima dhe shtresat më pas bashkohen për të formuar një produkt të vetëm me shumë shtresa.
- Insert myk: Kallëpët e futur përdoren për të futur përbërës metalikë ose plastikë në pjesën e derdhur gjatë procesit të formimit. Futja vendoset në zgavrën e kallëpit përpara se plastika të injektohet, dhe plastika më pas e rrethon futjen.
Në përgjithësi, lloji i mykut të përdorur në formimin me injeksion varet nga kërkesat specifike të produktit që prodhohet. Duke zgjedhur llojin e duhur të mykut, prodhuesit mund të optimizojnë efikasitetin, cilësinë dhe efektivitetin e procesit të formimit me injeksion.
Praktikat më të mira për formimin me injeksion
Formimi me injeksion është një proces kompleks prodhimi që kërkon planifikim dhe ekzekutim të kujdesshëm për të arritur rezultatet e dëshiruara. Këtu janë disa praktika më të mira për formimin me injeksion që mund të ndihmojnë në sigurimin e cilësisë, efikasitetit dhe kostos optimale:
- Dizajni për prodhueshmëri: Dizajni i produktit duhet të optimizohet për formimin me injeksion. Kjo përfshin minimizimin e numrit të pjesëve, sigurimin e trashësisë uniforme të murit dhe shmangien e prerjeve dhe veçorive të tjera që komplikojnë formimin.
- Përzgjedhja e materialit: Materiali i përdorur në formimin me injeksion duhet të zgjidhet në bazë të kërkesave të produktit. Duhet të merren parasysh faktorë të tillë si vetitë mekanike, vetitë termike dhe rezistenca mjedisore.
- Dizajni i kallëpit: Dizajni i kallëpit duhet të optimizohet për produktin specifik. Kjo përfshin sigurimin e ftohjes, ventilimit dhe mbylljes së duhur, si dhe zgjedhjen e llojit të duhur të mykut.
- Parametrat e injektimit: Parametrat e injektimit, si presioni, temperatura dhe shpejtësia e injektimit, duhet të kontrollohen dhe monitorohen me kujdes për të siguruar cilësi dhe qëndrueshmëri optimale.
- Mirëmbajtja: Makina e rregullt e formimit me injeksion dhe mirëmbajtja e mykut janë kritike për të siguruar performancën optimale dhe për të parandaluar kohën e ndërprerjes.
- Kontrolli i cilësisë: Kontrolli i cilësisë duhet të zbatohet gjatë gjithë procesit të formimit me injeksion, nga inspektimi i materialit në hyrje deri te inspektimi i produktit përfundimtar. Kjo përfshin monitorimin e defekteve të tilla si shtrembërimi, shenjat e lavamanit dhe blici.
- Optimizimi i procesit: Përmirësimi i vazhdueshëm i procesit duhet të jetë fokusi kryesor i operacioneve të formimit me injeksion. Kjo përfshin monitorimin e matjeve të performancës së procesit si koha e ciklit, shkalla e skrapit dhe përdorimi i makinës dhe bërjen e rregullimeve sipas nevojës për të optimizuar efikasitetin dhe cilësinë.
Në përgjithësi, derdhja me injeksion kërkon vëmendje të kujdesshme ndaj detajeve dhe fokus në përmirësimin e vazhdueshëm. Duke ndjekur praktikat më të mira për formimin me injeksion, prodhuesit mund të sigurojnë cilësi optimale, efikasitet dhe kosto-efektivitet dhe të prodhojnë produkte plastike me cilësi të lartë që plotësojnë nevojat e klientëve të tyre.
Masat e kontrollit të cilësisë për formimin me injeksion
Kontrolli i cilësisë është kritik për formimin me injeksion, pasi siguron që produkti përfundimtar të plotësojë specifikimet dhe standardet e kërkuara. Këtu janë disa masa të kontrollit të cilësisë për formimin me injeksion:
- Inspektimi i materialit në hyrje: Procesi i kontrollit të cilësisë duhet të fillojë me një rishikim të lëndës së parë të përdorur për formimin me injeksion. Kjo përfshin verifikimin që materiali është i llojit, klasës dhe ngjyrës së duhur dhe plotëson specifikimet e kërkuara të vetive mekanike dhe termike.
- Inspektimi gjatë procesit: Gjatë formimit me injeksion, personeli i kontrollit të cilësisë duhet të inspektojë rregullisht produktin për t'u siguruar që ai është derdhur në mënyrë korrekte. Kjo përfshin monitorimin për defekte të tilla si shenjat e lavamanit, deformimin dhe ndezjen dhe verifikimin që produkti plotëson tolerancat e kërkuara dimensionale.
- Inspektimi i produktit përfundimtar: Pasi të përfundojë procesi i formimit të injektimit, produkti përfundimtar duhet të inspektohet për t'u siguruar që ai plotëson specifikimet dhe standardet e kërkuara. Kjo përfshin verifikimin që produkti nuk ka defekte, të tilla si çarje, flluska dhe zbrazëtira dhe plotëson tolerancat e kërkuara dimensionale.
- Kontrolli statistikor i procesit: Kontrolli i procesit statistikor (SPC) është një metodë e monitorimit dhe kontrollit të një procesi për të siguruar që ai prodhon rezultate të vazhdueshme me cilësi të lartë. SPC përfshin mbledhjen e të dhënave për parametrat kritikë të procesit, të tilla si presioni dhe temperatura e injektimit, dhe përdorimin e analizave statistikore për të identifikuar tendencat dhe modelet që tregojnë ndryshueshmërinë e procesit.
- Përmirësimi i vazhdueshëm: Kontrolli i cilësisë duhet të jetë një proces i vazhdueshëm i përmirësimit të vazhdueshëm. Kjo përfshin analizimin e të dhënave mbi performancën e procesit, identifikimin e fushave për përmirësim dhe bërjen e ndryshimeve në proces për të optimizuar cilësinë dhe efikasitetin.
- Dokumentacioni dhe gjurmueshmëria: Personeli i kontrollit të cilësisë duhet të mbajë dokumentacion të detajuar të procesit të formimit me injeksion, duke përfshirë parametrat e procesit, rezultatet e inspektimit dhe veprimet korrigjuese. Ky dokumentacion ofron gjurmueshmëri dhe ndihmon për të siguruar që çdo problem i cilësisë mund të identifikohet dhe korrigjohet shpejt.
Në përgjithësi, kontrolli i cilësisë është një aspekt kritik i formimit me injeksion dhe duhet të integrohet në çdo aspekt të procesit të prodhimit. Duke zbatuar këto masa të kontrollit të cilësisë, prodhuesit mund të prodhojnë produkte plastike me cilësi të lartë që plotësojnë nevojat e klientëve të tyre.
Defektet e zakonshme në formimin me injeksion dhe si t'i parandaloni ato
Formimi me injeksion është një proces kompleks që mund të rezultojë në defekte nëse ekzekutohet në mënyrë jo të duhur. Këtu janë disa defekte të zakonshme në formimin me injeksion dhe si t'i parandaloni ato:
- Shenjat e lavamanit janë depresione ose gërvishtje në sipërfaqen e produktit. Ato shkaktohen nga ftohja e pabarabartë ose presioni i pamjaftueshëm i paketimit. Sigurohuni që dizajni i kallëpit të përfshijë trashësi uniforme të murit dhe kënde të mjaftueshme rryme për të parandaluar shenjat e lavamanit. Rregullimi i presionit të paketimit dhe kohës së ftohjes mund të ndihmojë gjithashtu në parandalimin e shenjave të lavamanit.
- Warpage: Deformimi është shtrembërimi i produktit pasi të jetë hequr nga kallëpi. Shkaktohet nga ftohja e pabarabartë ose streset e brendshme në produkt. Për të parandaluar shtrembërimin, sigurohuni që dizajni i kallëpit të përfshijë trashësi uniforme të murit dhe kohë të mjaftueshme ftohjeje. Shmangni qoshet e mprehta ose ndryshimet e papritura në gjeometrinë e produktit, të cilat mund të krijojnë pika stresi.
- Blic: Flash është plastika e tepërt që shtrihet përtej kufijve të produktit, zakonisht ndodh rreth skajeve të mykut. Shkaktohet nga presioni i tepërt i injektimit, forca e pamjaftueshme shtrënguese ose myku i konsumuar. Për të parandaluar ndezjen, rregulloni presionin e injektimit dhe forcën shtrënguese dhe kontrolloni rregullisht kallëpin për shenja konsumimi.
- Të shtëna të shkurtra: Të shtëna të shkurtra ndodhin kur kallëpi është pjesërisht i mbushur me plastikë. Kjo mund të shkaktohet nga presioni ose temperatura e pamjaftueshme e injektimit ose nga një kanal i bllokuar ose i kufizuar i rrjedhës. Për të parandaluar shkrepjet e shkurtra, rregulloni presionin dhe temperaturën e injektimit dhe sigurohuni që kanali i rrjedhës të jetë i pastër dhe i papenguar.
- Shenjat e djegies: Shenjat e djegies janë njolla të errëta në sipërfaqen e produktit të shkaktuara nga mbinxehja ose fërkimi i tepërt në myk. Për të parandaluar shenjat e djegies, sigurohuni që myku të jetë ftohur dhe lubrifikuar siç duhet dhe rregulloni shpejtësinë dhe presionin e injektimit sipas nevojës.
- Boshllëqet dhe flluskat: Boshllëqet dhe flluskat janë zona të produktit ku mungon materiali ose përmbajnë xhepa ajri. Ato shkaktohen nga ajri ose gazi i bllokuar në myk ose rrjedha e pamjaftueshme e materialit. Për të parandaluar zbrazëtitë dhe flluskat, sigurohuni që kallëpi të ajroset siç duhet dhe që shpejtësia dhe presioni i injektimit të jenë të mjaftueshme për të siguruar rrjedhje uniforme të materialit.
Këshilla për mirëmbajtjen e pajisjeve të derdhjes me injeksion
Pajisjet e formimit me injeksion janë një investim i rëndësishëm për prodhuesit dhe mirëmbajtja e duhur është thelbësore për të siguruar performancën dhe jetëgjatësinë optimale. Këtu janë disa këshilla për mirëmbajtjen e pajisjeve të derdhjes me injeksion:
- Kryeni inspektime të rregullta: Inspektoni rregullisht pajisjet për të identifikuar çdo konsumim, dëmtim ose çështje të tjera. Inspektoni zorrët hidraulike, vulat dhe komponentët e tjerë kritikë për t'u siguruar që janë në gjendje të mirë.
- Pastroni dhe lubrifikoni pajisjet: Pastroni dhe lubrifikoni rregullisht pajisjet për të parandaluar korrozionin dhe konsumimin. Përdorni produktet e rekomanduara të pastrimit dhe lubrifikimit dhe ndiqni udhëzimet e prodhuesit.
- Monitoroni dhe mirëmbani vajin hidraulik: Monitoroni rregullisht për t'u siguruar që është i pastër dhe me viskozitetin e duhur. Ndryshoni vajin sipas nevojës dhe përdorni llojin e rekomanduar të vajit.
- Mirëmbani brezat e ngrohësit: Kontrolloni rregullisht për t'u siguruar që janë në gjendje të mirë dhe ngrohen siç duhet. Zëvendësoni menjëherë çdo brez ngrohës të dëmtuar ose të konsumuar.
- Monitoroni dhe mirëmbani sistemin e ftohjes: Është kritik për formimin me injeksion, pasi parandalon mbinxehjen dhe shtrembërimin. Monitoroni rregullisht sistemin e ftohjes për t'u siguruar që funksionon siç duhet dhe pastroni kanalet e ftohjes sipas nevojës.
- Operatorët e trenave: Trajnoni operatorët për funksionimin e duhur të pajisjeve dhe procedurat e mirëmbajtjes për të parandaluar dëmtimin dhe për të siguruar performancën optimale.
- Programoni mirëmbajtjen e rregullt: Vendosni një orar mirëmbajtjeje dhe përmbahuni në të. Programoni detyrat rutinë të mirëmbajtjes, të tilla si lubrifikimi dhe ndryshimet e vajit, dhe dokumentoni të gjitha aktivitetet e mirëmbajtjes.
- Mbani në dorë pjesët e këmbimit: Siguroni pjesë rezervë, të tilla si zorrë hidraulike, vula dhe shirita ngrohës. Kjo do të zëvendësojë shpejt pjesët e dëmtuara ose të konsumuara dhe do të minimizojë kohën e ndërprerjes.
Mirëmbajtja e duhur e pajisjeve të derdhjes me injeksion është thelbësore për të siguruar që ato të funksionojnë në mënyrë efikase, të prodhojnë produkte me cilësi të lartë dhe të kenë një jetëgjatësi të gjatë. Duke ndjekur këto këshilla për mirëmbajtjen, prodhuesit mund t'i mbajnë pajisjet e tyre në gjendje të mirë dhe të minimizojnë kohën e ndërprerjes dhe kostot e riparimit.
Si të zgjidhni prodhuesin e duhur të derdhjes me injeksion
Zgjedhja e prodhuesit të duhur të derdhjes me injeksion është një vendim i rëndësishëm që mund të ndikojë ndjeshëm në cilësinë dhe koston e produkteve tuaja. Këtu janë disa faktorë që duhen marrë parasysh kur zgjidhni një prodhues të derdhjes me injeksion:
- Përvoja dhe ekspertiza: Kërkoni një prodhues me përvojë dhe ekspertizë të gjerë në formimin me injeksion. Pyesni për proceset e tyre të prodhimit, masat e kontrollit të cilësisë dhe certifikatat.
- Teknologjia dhe pajisjet: Kërkoni për një prodhues që përdor teknologji dhe pajisje moderne. Kjo mund të ndihmojë në sigurimin e cilësisë së qëndrueshme, kohë më të shkurtër të ofrimit dhe efektivitetin e kostos.
- Materialet dhe aftësitë: Merrni parasysh llojet e materialeve me të cilat mund të punojë prodhuesi dhe aftësitë e tyre. Kërkoni për një prodhues që mund të trajtojë një gamë të gjerë materialesh, duke përfshirë materiale të specializuara, dhe mund të prodhojë një shumëllojshmëri të madhësive dhe formave të produkteve.
- Masat e kontrollit të cilësisë: Kërkoni një prodhues që fokusohet fuqishëm në kontrollin e cilësisë. Pyesni për masat e tyre të kontrollit të cilësisë, të tilla si procedurat e inspektimit dhe testimit, dhe çdo certifikim që mund të kenë.
- Shërbimi ndaj klientit: Kërkoni për një prodhues që ofron shërbim të shkëlqyer ndaj klientit. Merrni parasysh përgjegjshmërinë, komunikimin dhe gatishmërinë për të punuar me ju për të përmbushur nevojat tuaja specifike.
- Kostoja dhe koha e realizimit: Merrni parasysh koston e prodhuesit dhe kohën e realizimit për projektin tuaj. Kërkoni një prodhues që ofron çmime konkurruese dhe kohë reale të prodhimit që plotësojnë kërkesat tuaja.
- Referencat dhe rishikimet: Kërkoni referenca dhe kontrolloni rishikimet në internet të prodhuesit. Kjo mund t'ju ndihmojë të kuptoni më mirë reputacionin e tyre dhe përvojat e klientëve të tjerë.
Ju mund të zgjidhni prodhuesin e duhur të formimit të injektimit për projektin tuaj duke marrë parasysh këta faktorë dhe duke kryer një hulumtim të plotë. Një prodhues me reputacion me përvojën, aftësitë dhe përkushtimin e duhur ndaj cilësisë mund të ndihmojë që produktet tuaja të prodhohen me efikasitet, me kosto efektive dhe sipas specifikave tuaja të sakta.
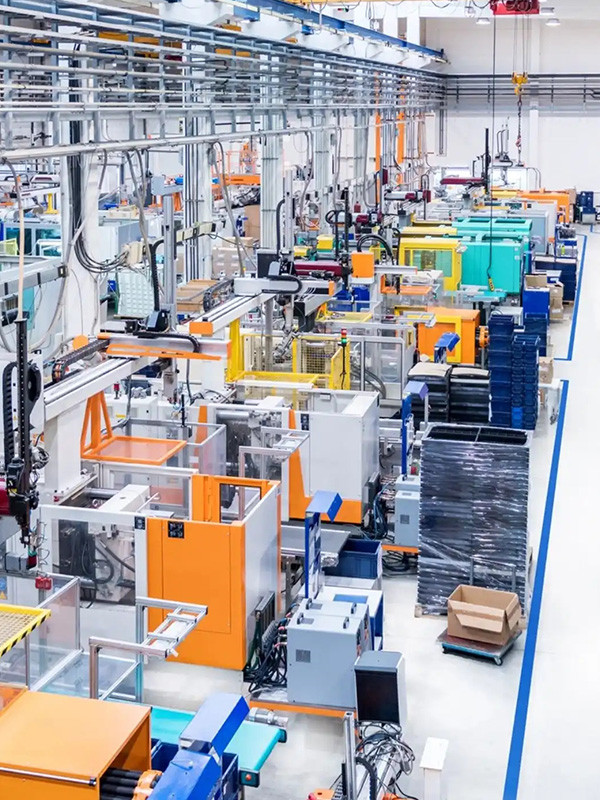
Konsideratat e kostos në formimin me injeksion plastik me porosi
Formimi me injektim i plastikës me porosi është një proces prodhimi shumë i gjithanshëm që mund të prodhojë pjesë komplekse dhe me cilësi të lartë në shkallë. Megjithatë, konsideratat e kostos janë një faktor kritik në përdorimin e këtij procesi të prodhimit. Këtu janë disa konsiderata kryesore të kostos në formimin me injeksion plastik me porosi:
- Kostot materiale: Lloji dhe sasia e materialit të përdorur në procesin e derdhjes me injeksion do të ndikojë në çmim. Disa materiale, të tilla si plastika inxhinierike me performancë të lartë, janë më të shtrenjta se të tjerët. Kostoja e materialeve mund të ndikohet gjithashtu nga ndërprerjet e zinxhirit të furnizimit, kërkesa e tregut dhe luhatjet e çmimeve.
- Kostot e veglave: Kostoja e përpunimit të veglave, ose kallëpeve të përdorura për prodhimin e pjesëve, është një shpenzim i rëndësishëm në formimin me injeksion plastik me porosi. Kompleksiteti i pjesës, numri i zgavrave në kallëp dhe materiali i përdorur për krijimin e kallëpit do të ndikojnë të gjitha në koston e veglave. Veglat e punës mund të jenë të shtrenjta në fillim, por mund të ndihmojnë në uljen e kostove për njësi me kalimin e kohës duke rritur efikasitetin e prodhimit.
- Vëllimi i prodhimit: Vëllimi i pjesëve të prodhuara do të ndikojë në koston e derdhjes me injeksion. Prodhimi me volum të lartë mund të ndihmojë në uljen e kostove për njësi, ndërsa prodhimi me vëllim të ulët mund të ketë kosto më të larta për njësi për shkak të nevojës për më shumë vegla pune dhe kohë konfigurimi.
- Kostot e punës: Kostot e punës janë një faktor i rëndësishëm në formimin me injeksion, veçanërisht për pjesët më komplekse që kërkojnë më shumë punë manuale. Niveli i aftësive të operatorëve dhe kompleksiteti i pjesës do të ndikojë në koston e dorëzimit.
- Kostot e kontrollit të cilësisë: Ruajtja e kontrollit të cilësisë është thelbësore për të siguruar integritetin e pjesëve. Çmimi i kontrollit të cilësisë mund të përfshijë pajisjet e inspektimit, testimin dhe punën.
- Kostot e transportit: Dërgimi i pjesëve te klienti ose vende të tjera mund të jetë një shpenzim i rëndësishëm, veçanërisht për detaje të mëdha ose të rënda.
Prodhuesit mund të prodhojnë pjesë me cilësi të lartë me një kosto më të ulët duke marrë parasysh këta faktorë të kostos dhe duke optimizuar procesin e formimit me injeksion. Kjo mund të arrihet duke reduktuar mbetjet materiale, duke rritur efikasitetin e prodhimit dhe duke minimizuar kohën e konfigurimit dhe ndërrimit. Puna me një prodhues me përvojë dhe njohuri të formimit të injektimit mund të ndihmojë gjithashtu në optimizimin e procesit dhe uljen e kostove.
Tendencat dhe risitë në teknologjinë e derdhjes me injeksion
Teknologjia e derdhjes me injeksion ka ekzistuar për shumë vite, por ka ende shumë risi dhe tendenca që i japin formë të ardhmes së këtij procesi prodhimi. Këtu janë disa nga tendencat dhe risitë kryesore në teknologjinë e derdhjes me injeksion:
- Printimi 3D dhe prodhimi i aditivëve: Printimi 3D dhe prodhimi i aditivëve po bëhen gjithnjë e më të njohura në industrinë e formimit me injeksion. Kjo teknologji lejon krijimin e formave dhe gjeometrive komplekse që janë të vështira ose të pamundura për t'u arritur me formimin tradicional me injeksion.
- Formimi me injeksion me shumë materiale: Formimi me injeksion me shumë materiale lejon krijimin e pjesëve me materiale ose ngjyra të shumta në një shkrepje të vetme. Ky proces mund të zvogëlojë kohën dhe kostot e prodhimit dhe të krijojë funksione me veti dhe pamje unike.
- Automatizimi dhe Industria 4.0: Teknologjitë e automatizimit dhe industrisë 4.0, të tilla si sensorët e IoT dhe robotika, janë duke u integruar në makinat dhe proceset e formimit me injeksion. Kjo mund të përmirësojë efikasitetin e prodhimit, të zvogëlojë kostot e punës dhe të përmirësojë kontrollin e cilësisë.
- Materialet dhe proceset e qëndrueshme: Ndërsa kompanitë kërkojnë të reduktojnë ndikimin e tyre mjedisor, materialet dhe metodat e qëndrueshme po bëhen më të rëndësishme në industrinë e derdhjes me injeksion. Kjo përfshin përdorimin e materialeve dhe proceseve të biodegradueshme ose të riciklueshme që minimizojnë mbetjet dhe konsumin e energjisë.
- Prodhimi i zgjuar dhe mirëmbajtja parashikuese: Teknologjitë inteligjente të prodhimit, të tilla si mësimi i makinerive dhe mirëmbajtja parashikuese, po përdoren për të optimizuar proceset e formimit me injeksion dhe për të zvogëluar kohën e ndërprerjes. Kjo mund të përmirësojë efikasitetin e përgjithshëm dhe të zvogëlojë kostot e mirëmbajtjes.
- Materiale me performancë të lartë: Materialet e reja me performancë të lartë janë duke u zhvilluar për formimin me injeksion, duke përfshirë materiale me forcë, qëndrueshmëri dhe rezistencë të përmirësuar ndaj nxehtësisë. Këto materiale mund të përdoren në aplikime të ndryshme, nga pjesët e automobilave deri te pajisjet mjekësore.
Duke qëndruar të përditësuar për këto tendenca dhe risi, prodhuesit e formimit me injeksion mund të mbeten konkurrues dhe të vazhdojnë të ofrojnë pjesë me cilësi të lartë për klientët e tyre. Ndërsa teknologjitë dhe materialet e reja zhvillohen, industria e derdhjes me injeksion do të vazhdojë të zhvillohet dhe të përshtatet për të përmbushur nevojat në ndryshim të konsumatorëve dhe bizneseve.
Qëndrueshmëria në formimin me injeksion: reduktimi i mbetjeve dhe konsumit të energjisë
Qëndrueshmëria po bëhet gjithnjë e më e rëndësishme në industrinë e derdhjes me injeksion pasi kompanitë kërkojnë të reduktojnë ndikimin e tyre mjedisor dhe të plotësojnë kërkesën në rritje për produkte miqësore me mjedisin. Këtu janë disa mënyra se si prodhuesit e derdhjes me injeksion mund të reduktojnë konsumin e mbeturinave dhe energjisë:
- Përdorni materiale të qëndrueshme: Zgjedhja e materialit është një faktor kritik në qëndrueshmëri. Prodhuesit e formimit me injeksion mund të përdorin materiale të biodegradueshme ose të riciklueshme për të reduktuar ndikimin mjedisor. Plastika e biodegradueshme, për shembull, mund të shpërbëhet natyrshëm me kalimin e kohës dhe të zvogëlojë sasinë e mbetjeve në deponi. Materialet e ricikluara, të tilla si plastika e ricikluar pas konsumit, mund të ndihmojnë gjithashtu në uljen e konsumit të mbeturinave dhe energjisë.
- Reduktoni mbetjet materiale: Prodhuesit e formimit me injeksion mund të reduktojnë gjithashtu mbetjet materiale duke optimizuar dizajnin e pjesës dhe mykut. Kjo përfshin reduktimin e sasisë së materialit të tepërt të përdorur, minimizimin e numrit të zgavrave në myk dhe reduktimin e peshës së përgjithshme të pjesës. Duke reduktuar mbetjet materiale, prodhuesit mund të kursejnë në kostot materiale dhe të zvogëlojnë ndikimin e tyre mjedisor.
- Optimizoni efikasitetin e prodhimit: Prodhuesit e derdhjes me injeksion mund të optimizojnë proceset e tyre të prodhimit për të reduktuar konsumin e energjisë. Kjo përfshin përdorimin e makinerive të formimit me injeksion me efikasitet të lartë, optimizimin e parametrave të procesit të formimit dhe minimizimin e kohës së ndërprerjes. Duke reduktuar konsumin e energjisë, prodhuesit mund të kursejnë në kostot e energjisë dhe të zvogëlojnë gjurmën e tyre të karbonit.
- Zbatimi i praktikave të qëndrueshme: Prodhuesit e formimit me injeksion mund të zbatojnë gjithashtu praktika të qëndrueshme në operacionet e tyre, të tilla si programet e riciklimit dhe reduktimit të mbetjeve, duke përdorur burime të rinovueshme të energjisë dhe duke promovuar qëndrueshmërinë midis punonjësve dhe furnitorëve të tyre. Duke promovuar praktika të qëndrueshme në të gjithë zinxhirin e furnizimit, prodhuesit mund të ndihmojnë në krijimin e një industrie më të qëndrueshme në përgjithësi.
- Përdorni paketim të qëndrueshëm: Së fundi, prodhuesit e formimit me injeksion mund të përdorin materiale dhe dizajne të qëndrueshme paketimi për të reduktuar mbetjet dhe ndikimin mjedisor. Kjo përfshin përdorimin e materialeve paketuese të biodegradueshme ose të riciklueshme, minimizimin e mbetjeve të paketimit dhe dizajnimin e paketimeve të ripërdorshme ose të rimbushshme.
Duke zbatuar këto praktika të qëndrueshme, prodhuesit e formimit me injeksion mund të zvogëlojnë ndikimin e tyre mjedisor dhe të krijojnë një industri më të qëndrueshme në përgjithësi. Ndërsa qëndrueshmëria bëhet gjithnjë e më e rëndësishme për konsumatorët dhe bizneset, prodhuesit e formimit me injeksion që i japin përparësi qëndrueshmërisë do të jenë të pozicionuar mirë për të përmbushur kërkesën në rritje për produkte miqësore me mjedisin.
Si krahasohet formimi me injeksion plastik me porosi me proceset e tjera të prodhimit
Formimi me injektim i plastikës me porosi është një proces prodhimi popullor për prodhimin e pjesëve plastike me cilësi të lartë në sasi të mëdha. Megjithatë, disa procese të tjera të prodhimit mund të përdoren për të bërë pjesë plastike, secila me avantazhe dhe disavantazhe. Këtu është një krahasim i formimit me injeksion plastik me porosi me proceset e tjera të prodhimit:
- Printimi 3D: Printimi 3D është një teknologji me rritje të shpejtë që lejon krijimin e formave dhe gjeometrive komplekse. Ndërsa printimi 3D mund të përdoret për prodhim në shkallë të vogël, derdhja me injeksion është përgjithësisht më pak me kosto efektive dhe efikase sesa derdhja me injeksion për prodhimin e pjesëve të mëdha.
- Formimi me fryrje: Formimi me fryrje është një proces prodhimi që krijon pjesë të zbrazëta plastike, të tilla si shishe dhe kontejnerë. Ndërsa formimi me fryrje është i përshtatshëm për prodhimin e vëllimeve të larta të veçorive, formimi me injeksion është përgjithësisht më pak i saktë se ai me injeksion dhe mund të mos jetë ideal për krijimin e formave dhe gjeometrive më komplekse.
- Përpunimi me CNC: Përpunimi me CNC është një proces prodhimi zbritës që përfshin prerjen dhe formësimin e pjesëve nga një bllok i fortë materiali. Ndërsa përpunimi CNC është i përshtatshëm për prodhimin e pjesëve me precizion të lartë në sasi të vogla, në përgjithësi nuk është aq me kosto efektive apo efikase sa formimi me injeksion.
- Formimi rrotullues: Formimi rrotullues është një proces prodhimi që përfshin rrotullimin e një myku rreth dy akseve pingul gjatë ngrohjes së tij. Ndërsa formimi rrotullues mund të prodhojë pjesë të mëdha me gjeometri komplekse, formimi me injeksion është përgjithësisht më pak i saktë se ai me injeksion dhe mund të mos jetë i përshtatshëm për të bërë pjesë më të vogla.
- Termoformimi: Termoformimi është një proces prodhimi që përfshin ngrohjen e një fletë plastike dhe më pas formimin e saj mbi një kallëp. Ndërsa termoformimi mund të prodhojë pjesë të mëdha me gjeometri të thjeshta, formimi me injeksion është përgjithësisht më pak i saktë se ai me injeksion dhe mund të mos jetë i përshtatshëm për krijimin e formave dhe gjeometrive më komplekse.
Formimi me injektim i plastikës me porosi është një proces prodhimi shumë i gjithanshëm dhe me kosto efektive për prodhimin e pjesëve plastike me cilësi të lartë në sasi të mëdha. Ndërsa proceset e tjera të prodhimit mund të jenë më të përshtatshme për aplikime specifike ose vëllime prodhimi, formimi me injeksion është përgjithësisht zgjedhja e preferuar për shumë prodhues për shkak të shpejtësisë, saktësisë dhe efektivitetit të kostos. Në fund të fundit, zgjedhja e procesit të prodhimit do të varet nga faktorë të ndryshëm, duke përfshirë dizajnin e pjesës, vëllimin e prodhimit dhe buxhetin.
Të mirat dhe të këqijat e kontraktimit të formimit me injeksion
Transferimi i derdhjes me injeksion është një praktikë e zakonshme për kompanitë që kërkojnë të prodhojnë pjesë plastike pa investuar në pajisjet ose ekspertizën e tyre të derdhjes me injeksion. Ndërsa kontraktimi i jashtëm mund të ofrojë disa përfitime, ai gjithashtu ka disa të meta të mundshme. Këtu janë disa të mirat dhe të këqijat e kontraktimit të formimit me injeksion:
Pro:
- Kursimet e kostos: Transferimi i derdhjes me injeksion është shpesh më kosto-efektiv sesa ngritja e një objekti prodhimi në shtëpi. Kjo është veçanërisht e vërtetë për kompanitë e vogla dhe të mesme që kanë nevojë për më shumë para ose vëllim për të justifikuar investimin në pajisje dhe personel të shtrenjtë.
- Ekspertiza: Kompanitë e derdhjes me injeksion specializohen në prodhim dhe kanë ekspertizën për të siguruar që pjesët të prodhohen në një standard të cilësisë së lartë. Duke kontraktuar formimin me injeksion, kompanitë mund të përfitojnë nga ekspertiza e profesionistëve me përvojë.
- Kapaciteti: Kompanitë e derdhjes me injeksion mund të prodhojnë sasi të mëdha pjesësh shpejt dhe me efikasitet. Kjo është veçanërisht e dobishme për kompanitë që duhet të bëjnë rregullisht vëllime të mëdha funksionesh.
- Fleksibiliteti: Transferimi i formimit me injeksion lejon kompanitë të jenë më fleksibël në oraret e tyre të prodhimit. Kompanitë mund të rregullojnë vëllimet e tyre të prodhimit ose të kalojnë në pjesë të ndryshme pa u shqetësuar për kostot kapitale të ndryshimit të pajisjeve dhe kallëpeve.
Cons:
- Komunikimi: Transferimi i formimit me injeksion mund të krijojë sfida komunikimi midis klientit dhe kompanisë. Keqkuptimet ose vonesat në komunikim mund të rezultojnë në gabime ose vonesa në prodhim.
- Kontrolli i cilësisë: Transferimi i derdhjes me injeksion do të thotë të mbështetesh te një kompani e jashtme për të prodhuar pjesë sipas standardeve të kërkuara të cilësisë. Kontrolli i cilësisë mund të jetë sfidues kur punoni me një kompani të jashtme dhe gjithmonë ekziston rreziku i marrjes së veçorive që duhet të plotësojnë specifikimet e kërkuara.
- Varësia: Transferimi i derdhjes me injeksion nënkupton varësinë nga një kompani e jashtme e prodhimit. Kjo mund të krijojë rreziqe në lidhje me besueshmërinë, stabilitetin dhe kohën e dorëzimit të furnizuesit.
- Pronësia intelektuale: Transferimi i formimit me injeksion mund të krijojë rreziqe për mbrojtjen e pronës intelektuale. Kompanitë duhet të sigurojnë që dizajnet dhe teknologjia e tyre të mbrohen nga masat e duhura ligjore.
Perspektivat e ardhshme për formimin me injeksion plastik me porosi
Formimi me injeksion plastik me porosi ka qenë një proces prodhimi i besueshëm dhe i gjithanshëm për disa dekada. Në vitet e fundit, përparimet në teknologji dhe materiale kanë vazhduar të rrisin aftësitë dhe potencialin e formimit me injeksion. Këtu janë disa perspektiva të ardhshme për formimin me injeksion plastik me porosi:
- Adoptimi i teknologjive të Industry 4.0: Integrimi i teknologjive të Industry 4.0, të tilla si inteligjenca artificiale, mësimi i makinerive dhe Interneti i Gjërave (IoT), pritet të rrisë automatizimin, të përmirësojë kontrollin e cilësisë dhe të optimizojë proceset e prodhimit në formimin me injeksion.
- Rritja e përdorimit të materialeve të biodegradueshme: Shqetësimet mjedisore nxisin adoptimin e materialeve të biodegradueshme në formimin me injeksion. Materialet e biodegradueshme ofrojnë një alternativë të qëndrueshme ndaj plastikës tradicionale dhe mund të ndihmojnë në reduktimin e mbetjeve dhe ndikimin mjedisor.
- Kërkesa në rritje për prodhimin e pajisjeve mjekësore: Nevoja për pajisje mjekësore po rritet për shkak të plakjes së popullsisë dhe përparimeve në teknologjinë mjekësore. Formimi me injeksion është një proces i njohur prodhimi për pajisjet mjekësore për shkak të saktësisë, shpejtësisë dhe kostos së tij.
- Zgjerimi i aftësive të printimit 3D: Zhvillimi i teknologjisë së printimit 3D ka mundësuar prodhimin e pjesëve komplekse dhe të ndërlikuara që më parë ishin të pamundura për t'u prodhuar duke përdorur formimin me injeksion. Megjithatë, printimi 3D është ende relativisht i ngadaltë dhe i shtrenjtë në krahasim me formimin me injeksion, dhe të dy teknologjitë ka të ngjarë të vazhdojnë të plotësojnë njëra-tjetrën në vend që të zëvendësojnë njëra-tjetrën.
- Rritja e formimit me injeksion me shumë materiale: Formimi me injeksion me shumë materiale përfshin përdorimin e dy ose më shumë materialeve të ndryshme në një proces të vetëm formimi me injeksion. Kjo teknologji ofron disa përfitime, duke përfshirë performancën e përmirësuar të pjesëve, peshën e reduktuar dhe kursimin e kostos.
- Përparimet në teknologjinë e veglave: Zhvillimi i materialeve dhe modeleve të reja për vegla pune pritet të rrisë shpejtësinë, efikasitetin dhe saktësinë e formimit me injeksion. Për shembull, kanalet konformale të ftohjes në vegla pune mund të përmirësojnë kohën e ciklit dhe të zvogëlojnë konsumin e energjisë.
Përfundim:
Formimi me injektim i plastikës me porosi është një proces i fuqishëm prodhimi që mundëson prodhimin e pjesëve plastike me cilësi të lartë me saktësi dhe efikasitet të madh. Duke kuptuar procesin e derdhjes me injeksion, duke zgjedhur materiale të përshtatshme dhe modele kallëp, dhe duke zbatuar praktikat më të mira për kontrollin e cilësisë dhe mirëmbajtjen e pajisjeve, bizneset mund të optimizojnë operacionet e tyre të derdhjes me injeksion dhe të arrijnë sukses të jashtëzakonshëm. Ndërsa prirjet dhe risitë e reja shfaqen në industri, është thelbësore të qëndroni të përditësuar dhe të eksploroni mundësi të reja për të rritur qëndrueshmërinë, efikasitetin dhe përfitimin e formimit me injeksion plastik me porosi.