Derdhur plastike për injeksion
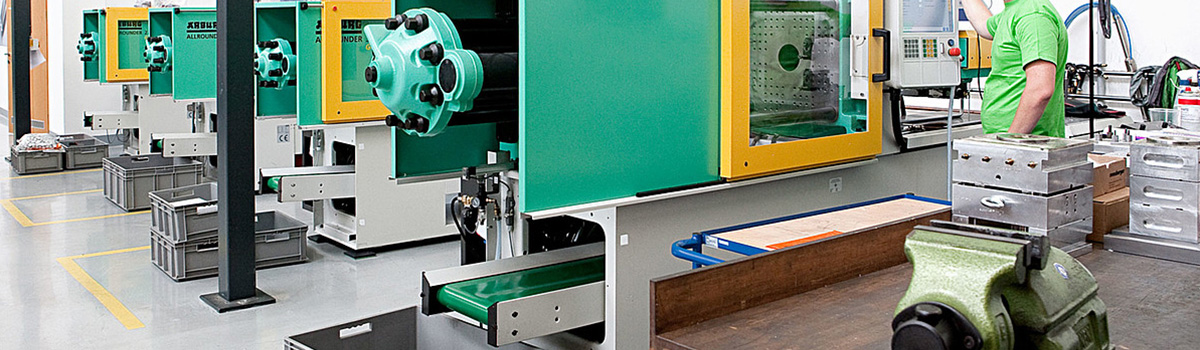
Formimi me injeksion plastik është një proces prodhimi që përfshin shkrirjen e peletave plastike dhe injektimin e tyre në një zgavër të mykut për të krijuar një objekt tredimensional. Ky proces fillon me shumë produkte, nga pjesët e vogla të saktësisë deri te komponentët e rëndësishëm të automobilave. Formimi me injektim të plastikës ofron shumë përparësi ndaj proceseve të tjera të prodhimit, duke përfshirë shkallën e lartë të prodhimit, fleksibilitetin e projektimit dhe efektivitetin e kostos. Ky udhëzues do të shikojë në thellësi formimin me injeksion plastik dhe do të eksplorojë aplikimet, përfitimet dhe kufizimet e ndryshme të tij.
Historia e derdhjes me injeksion plastik
Formimi me injeksion plastik është një proces prodhimi që përfshin injektimin e plastikës së shkrirë në një zgavër të mykut për të krijuar një formë specifike. Historia e formimit të injektimit të plastikës mund të gjurmohet në fund të viteve 1800 kur u shpik për herë të parë celuloidi, një lloj plastik. Megjithatë, ishte në vitet 1940 që formimi me injeksion plastik u përdor gjerësisht si një teknikë prodhimi.
Gjatë Luftës së Dytë Botërore, kërkesa për produkte plastike të prodhuara në masë u rrit dhe prodhuesit filluan të kërkonin mënyra të reja dhe më efikase për t'i prodhuar ato. Në vitin 1946, James Watson Hendry, një shpikës amerikan, zhvilloi makinën e parë të derdhjes me vidhos, e cila revolucionarizoi industrinë e derdhjes me injeksion plastik. Kjo makinë lejoi një kontroll më të saktë dhe të qëndrueshëm të procesit të injektimit, duke e bërë prodhimin e sasive të mëdha të pjesëve plastike më të aksesueshme dhe efikase.
Gjatë gjithë viteve 1950 dhe 1960, përparimet në teknologjinë e plastikës vazhduan të përmirësonin procesin e formimit të injektimit të plastikës. Futja e materialeve të reja, si polistireni dhe polietileni, krijoi pjesë plastike më komplekse dhe më të qëndrueshme. Për më tepër, përmirësimet në teknologjinë e makinerive të derdhur, duke përfshirë përdorimin e sistemeve hidraulike, e bënë procesin e derdhjes me injeksion edhe më efikas dhe me kosto efektive.
Sot, derdhja e plastikës me injeksion është një proces shumë i automatizuar që përdoret për të prodhuar një gamë të gjerë produktesh plastike, nga lodrat dhe mallrat e konsumit deri te pjesët e automobilave dhe pajisjet mjekësore. Me zhvillimin e materialeve dhe teknologjive të reja, procesi i formimit me injeksion plastik vazhdon të evoluojë dhe përmirësohet, duke siguruar që do të mbetet një teknikë jetike e prodhimit për shumë vite.
Bazat e derdhjes me injeksion plastik
Formimi me injeksion plastik është një proces prodhimi për të krijuar pjesë dhe produkte të bëra nga materiale plastike. Procesi përfshin injektimin e plastikës së shkrirë në një kallëp, i cili ftohet dhe ngurtësohet për të formuar formën e dëshiruar.
Hapat bazë të përfshirë në procesin e formimit të injektimit të plastikës janë si më poshtë:
- Dizajni i kallëpit: Hapi i parë në proces është dizajnimi i kallëpit që do të përdoret për të krijuar pjesën e dëshiruar. Forma është bërë zakonisht nga metali dhe duhet të përgatitet për të marrë parasysh tkurrjen ndërsa plastika ftohet dhe ngurtësohet.
- Përgatitja e materialit: Materiali plastik i përdorur në procesin e derdhjes me injeksion vjen në formën e peletave ose granulave, të cilat duhet të shkrihen dhe të përgatiten për injektim në kallëp. Kjo zakonisht bëhet në një plesht, ku plastika nxehet në një temperaturë specifike dhe shkrihet në një gjendje të lëngshme.
- Injeksion: Pasi plastika të shkrihet, ajo injektohet në myk duke përdorur një makinë të specializuar të derdhjes me injeksion. Makina ushtron presion ndaj plastikës së shkrirë, duke e detyruar atë në zgavrën e kallëpit, ku merr formën e kallëpit.
- Ftohja dhe ngurtësimi: Pasi plastika të injektohet në kallëp, ajo mund të ftohet dhe të ngurtësohet. Kjo mund të zgjasë nga disa sekonda deri në disa minuta, në varësi të madhësisë dhe kompleksitetit të pjesës.
- Nxjerrja: Pasi plastika të jetë ftohur dhe ngurtësuar, forma hapet dhe pjesa nxirret. Pozicioni mund të kërkojë punë shtesë përfundimi, si prerje ose lëmim, për të hequr skajet e tepërta plastike ose të vrazhda.
Formimi me injeksion plastik është një proces i saktë dhe i përsëritshëm, duke e bërë atë ideal për prodhimin në masë të pjesëve dhe produkteve me cilësi të qëndrueshme. Është gjithashtu shumë i gjithanshëm, pasi mund të krijojë pjesë dhe produkte në madhësi, forma dhe kompleksitete të ndryshme. Disa nga aplikimet më të zakonshme të formimit me injeksion plastik përfshijnë prodhimin e lodrave, mallrave të konsumit, pjesëve të automobilave dhe pajisjeve mjekësore.
Procesi i derdhjes së plastikës: hap pas hapi
Formimi me injeksion plastik është një proces kompleks që përfshin disa hapa. Këtu është një udhëzues hap pas hapi për procesin e formimit të injektimit të plastikës:
- Dizajnimi i kallëpit: Hapi i parë është dizajnimi i kallëpit të përdorur për të krijuar pjesën. Forma është bërë zakonisht prej çeliku ose alumini dhe duhet të përgatitet për të përshtatur tkurrjen e materialit plastik ndërsa ftohet.
- Krijimi i kallëpit: Pasi dizajni i kallëpit të përfundojë, ai prodhohet duke përdorur softuerin e dizajnit të ndihmuar nga kompjuteri (CAD) dhe makineritë e prodhimit me ndihmën e kompjuterit (CAM). Forma duhet të përpunohet dhe lëmohet me kujdes për të siguruar saktësinë dhe përfundimin e produktit përfundimtar.
- Përzgjedhja e materialit: Materiali i rrëshirës plastike i përdorur për procesin e derdhjes me injeksion duhet të zgjidhet bazuar në kërkesat e pjesës, të tilla si forca, fleksibiliteti, ngjyra dhe cilësi.
- Përgatitja e materialit: Materiali plastik i zgjedhur më pas nxehet në një temperaturë specifike dhe shkrihet në një lëng. Materiali më pas injektohet në pleshtin e makinës së derdhur.
- Formimi me injeksion: Materiali plastik i shkrirë injektohet në zgavrën e mykut duke përdorur një makinë të specializuar të derdhjes me injeksion. Makina ushtron presion mbi materialin plastik, duke e detyruar atë në zgavrën e kallëpit, ku merr formën e kallëpit.
- Ftohja: Pasi zgavra e mykut të mbushet me plastikë, ajo mund të ftohet dhe të ngurtësohet. Koha e ftohjes përcaktohet nga karakteristikat e materialit plastik, madhësia dhe trashësia e pjesës dhe temperatura e kallëpit.
- Nxjerrja: Pasi plastika të jetë ngurtësuar, kallëpi hapet dhe pjesa nxirret nga kallëpi duke përdorur kunjat e nxjerrjes.
- Mbarimi: Pjesa e nxjerrë mund të kërkojë punë shtesë përfundimi, si prerje, lëmim ose lyerje, për të hequr çdo skaj të tepërt plastike ose të ashpër.
- Kontrolli i cilësisë: Pjesa e përfunduar i nënshtrohet një inspektimi të plotë për të përmbushur specifikimet e kërkuara dhe standardet e cilësisë.
Formimi me injeksion plastik mund të prodhojë pjesë dhe produkte të ndryshme në madhësi, forma dhe kompleksitete të shumëfishta. Procesi përdoret gjerësisht në disa industri, duke përfshirë automobila, mjekësi, mallra të konsumit dhe elektronikë.
Llojet e plastikës që përdoren në formimin me injeksion
Shumë lloje të plastikës mund të përdoren në formimin me injeksion. Zgjedhja e materialit plastik do të varet nga kërkesat specifike të produktit ose pjesës që prodhohet, si forca, fleksibiliteti, qëndrueshmëria dhe pamja. Këtu janë disa nga llojet më të zakonshme të plastikës që përdoren në formimin me injeksion:
- Polietileni (PE): PE është një material plastik i përdorur gjerësisht i njohur për forcën dhe fleksibilitetin e tij. Përdoret për të prodhuar produkte të ndryshme, duke përfshirë materiale paketimi, lodra dhe pajisje mjekësore.
- Polipropileni (PP): PP është një material plastik i lehtë dhe i qëndrueshëm që përdoret zakonisht në industrinë e automobilave për pjesët e brendshme, si p.sh. pulti dhe panelet e dyerve. Ajo gjithashtu prodhon materiale paketimi, të tilla si kontejnerë dhe shishe.
- Polikarbonat (PC): PC është një material plastik i ngurtë dhe transparent që përdoret zakonisht për të prodhuar komponentë elektronikë, të tillë si kutitë e kompjuterit dhe telefonit. Përdoret gjithashtu për lentet e fenerëve dhe komponentët e pultit në industrinë e automobilave.
- Akrilonitril butadien stiren (ABS): ABS është një material plastik i gjithanshëm i njohur për forcën, qëndrueshmërinë dhe rezistencën ndaj nxehtësisë. Zakonisht përdoret për prodhimin e pjesëve të automobilave, të tilla si pultet, flakët e parafangove, lodrat dhe mallrat e konsumit.
- Poliamidi (PA): PA, i njohur gjithashtu si najloni, është një material plastik i fortë dhe i lehtë që përdoret zakonisht në prodhimin e pjesëve të automobilave, si mbulesat e motorit dhe sistemet e marrjes së ajrit. Ajo gjithashtu prodhon pajisje sportive, të tilla si çizmet e skive dhe raketa tenisi.
- Polistireni (PS): PS është një material plastik i lehtë dhe i ngurtë që përdoret zakonisht në prodhimin e materialeve të paketimit, të tilla si gota, tabaka dhe kontejnerë ushqimi. Ajo gjithashtu prodhon mallra të konsumit, të tilla si lodra dhe komponentë elektronikë.
- Polietileni tereftalat (PET): PET është një material plastik i fortë dhe transparent që përdoret zakonisht për të prodhuar materiale paketimi, të tilla si shishe dhe kontejnerë. Përdoret gjithashtu në industrinë e tekstilit për të prodhuar fibra dhe pëlhura.
Këto janë vetëm disa nga llojet më të zakonshme të plastikës që përdoren në formimin me injeksion. Ka shumë lloje të tjera materialesh plastike, secila me veti dhe karakteristika unike. Zgjedhja e materialit plastik do të varet nga kërkesat specifike të pjesës ose produktit që prodhohet.
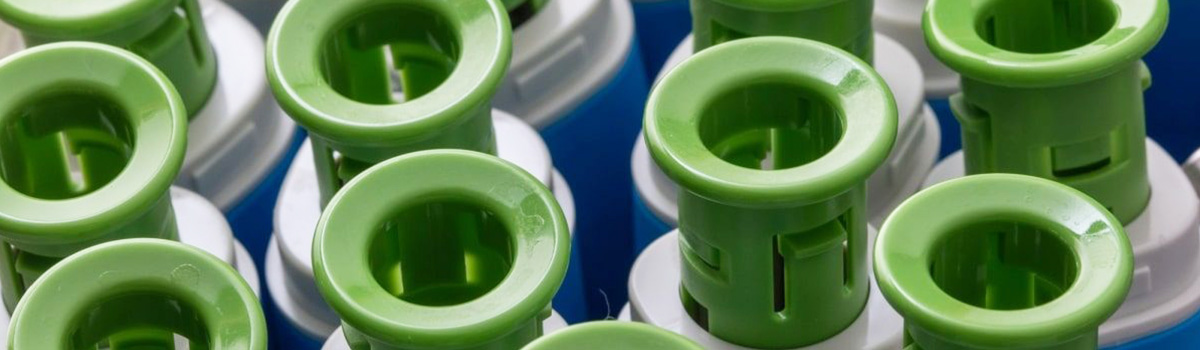
Llojet e makinave të derdhura me injeksion
Makinat e derdhjes me injeksion vijnë në lloje dhe madhësi të ndryshme, secila e projektuar për të përmbushur kërkesat specifike të prodhimit. Këtu janë disa nga llojet më të zakonshme të makinave të derdhjes me injeksion:
- Makina e derdhur me injeksion hidraulik: Kjo makinë përdor fuqi hidraulike për të gjeneruar presion për të injektuar plastikë në myk. Makinat hidraulike zakonisht përdoren për pjesë më të rëndësishme që kërkojnë forcë të lartë shtrënguese.
- Makina e derdhjes me injeksion elektrik: Makinat elektrike përdorin motorë elektrikë për të fuqizuar njësinë e injektimit dhe mekanizmin e kapëses. Ata janë të njohur për saktësinë e tyre të lartë dhe efikasitetin e energjisë, duke i bërë ata të famshëm për prodhimin e pjesëve të vogla dhe të ndërlikuara.
- Makina hibride e derdhjes me injeksion: Makinat hibride kombinojnë përfitimet e pajisjeve hidraulike dhe elektrike, duke përdorur energjinë hidraulike dhe elektrike për të gjeneruar presionin dhe fuqinë e nevojshme. Makinat hibride ofrojnë një ekuilibër të mirë të shpejtësisë, saktësisë dhe efikasitetit të energjisë.
- Makina e derdhjes vertikale me injeksion: Makinat vertikale prodhojnë pjesë që kërkojnë formim të futur ose mbi-derdhur. Ata kanë një njësi shtrënguese vertikale që lejon qasje të lehtë në kallëp, duke i bërë ato ideale për krijimin e pjesëve të vogla ose komplekse.
- Makina e derdhur me injeksion me dy goditje: Makinat me dy goditje prodhojnë pjesë me materiale ose ngjyra të ndryshme. Pajisja ka dy njësi injeksioni, secila e aftë për të injektuar materiale të huaja në myk. Ky lloj makinerie përdoret zakonisht për të prodhuar pjesë të automobilave, të tilla si doreza dhe pulla.
- Makina e derdhur me injeksion me shumë goditje: Makinat me shumë goditje prodhojnë pjesë me më shumë se dy materiale ose ngjyra. Pajisja ka njësi të shumta injektimi, secila e aftë për të injektuar një material të ndryshëm në kallëp. Kjo lloj makinerie përdoret zakonisht për prodhimin e mallrave të konsumit, si furçat e dhëmbëve dhe brisqet.
- Makina e derdhur me injeksion tërësisht elektrik: Makinat tërësisht elektrike përdorin motorë elektrikë për të fuqizuar njësinë e injektimit, mekanizmin e kapëses dhe kallëpin. Ata janë të njohur për saktësinë e tyre të lartë, shpejtësinë dhe efikasitetin e energjisë, duke i bërë ata të famshëm për prodhimin e pjesëve të vogla me precizion të lartë.
Këto janë vetëm disa nga llojet më të zakonshme të makinerive të derdhjes me injeksion. Çdo makinë ka veçori dhe avantazhe unike, duke e bërë thelbësore zgjedhjen e pajisjes së përshtatshme për kërkesat specifike të prodhimit.
Pjesë të një makine të derdhur me injeksion
Makinat e derdhjes me injeksion kanë disa pjesë që krijojnë pjesë plastike nga lëndët e para. Këtu janë përbërësit kritikë të një makine të derdhur me injeksion:
Hopper: Rezervuari mban lëndën e parë plastike përpara se të futet në makinën e derdhjes me injeksion. Materiali është zakonisht në formën e fishekëve ose pluhurit.
Fuçi: Fuçi është pjesa e gjatë cilindrike e makinës së derdhjes me injeksion që strehon vidën, e cila shkrin dhe përzien materialin plastik.
Vidha: Vidha është një pajisje rrotulluese brenda fuçisë që e shtyn materialin plastik përpara dhe e shkrin atë nga fërkimi dhe nxehtësia.
Njësia e injektimit: Njësia e injektimit përfshin pleshtin, fuçinë dhe vidën dhe është përgjegjëse për shkrirjen dhe injektimin e plastikës në kallëp.
Njësia shtrënguese: Njësia shtrënguese është përgjegjëse për mbajtjen e sigurt të kallëpit dhe ushtrimin e presionit të nevojshëm gjatë procesit të formimit me injeksion.
Kallëpi: Kallëpi është mjeti që krijon formën dhe madhësinë e pjesës plastike. Forma është bërë zakonisht prej çeliku dhe përbëhet nga dy gjysma që përshtaten së bashku.
Grykë: Gryka është pjesa e njësisë së injektimit që lidh makinën e formimit të injektimit me kallëpin. Materiali plastik i shkrirë injektohet përmes grykës dhe në kallëp.
Sistemi i ftohjes: Sistemi i ftohjes është përgjegjës për ftohjen e pjesës plastike pasi të jetë injektuar në kallëp. Kjo siguron që pjesa të ngurtësohet dhe mund të hiqet nga kallëpi pa dëmtuar.
Paneli i kontrollit: Paneli i kontrollit është ndërfaqja që lejon operatorin të monitorojë dhe rregullojë cilësimet e makinës së derdhjes me injeksion, të tilla si temperatura, presioni dhe koha e ciklit.
Secila prej këtyre pjesëve luan një rol kritik në procesin e formimit të injektimit dhe është thelbësore të mirëmbahet dhe optimizohet çdo pjesë për të siguruar që pjesët me cilësi të lartë të prodhohen me efikasitet.
Injeksion Molding Tooling: Design and Manufacturing
Veglat e formimit me injeksion i referohen projektimit dhe prodhimit të kallëpeve të përdorura në makinat e derdhjes me injeksion për të prodhuar pjesë plastike. Cilësia dhe efikasiteti i kallëpeve ndikojnë drejtpërdrejt në cilësinë dhe produktivitetin e procesit të formimit me injeksion. Këtu janë hapat kritikë në projektimin dhe prodhimin e veglave të formimit me injeksion:
Dizajni i produktit: Hapi i parë në përpunimin e modelimit me injeksion është dizajnimi i produktit që do të prodhohet. Dizajni i produktit përfshin përcaktimin e madhësisë, formës dhe materialit të pjesës, si dhe çdo veçori ose kërkesë specifike.
Dizajni i kallëpit: Procesi i projektimit të kallëpit fillon pasi të përfundojë dizajni i produktit. Projektuesi i kallëpit do të përcaktojë llojin më të mirë të mykut, numrin e kaviteteve të nevojshme dhe madhësinë dhe formën e kallëpit.
Ndërtimi i kallëpit: Kallëpi është ndërtuar në bazë të dizajnit të kallëpit, duke përdorur materiale me cilësi të lartë si çeliku ose alumini. Forma zakonisht bëhet në dy gjysma, secila përmban një ose më shumë zgavra.
Montimi i kallëpit: Pasi të ndërtohet kallëpi, ai montohet dhe testohet për saktësi dhe funksionalitet. Forma duhet të përballojë presionin dhe nxehtësinë e procesit të formimit me injeksion.
Testimi dhe vlefshmëria e mykut: Pasi të montohet kallëpi, ai testohet dhe vërtetohet për t'u siguruar që prodhon pjesë me cilësi të lartë që plotësojnë specifikimet e produktit. Kallëpi mund të ketë nevojë të rregullohet ose modifikohet për të përmirësuar performancën e tij.
Mirëmbajtja e mykut: Mirëmbajtja dhe riparimi i rregullt i mykut janë kritike për të siguruar jetëgjatësinë dhe performancën e tij. Kjo përfshin pastrimin, lubrifikimin dhe zëvendësimin e çdo pjese të konsumuar ose të dëmtuar.
Veglat e formimit me injeksion kërkojnë saktësi dhe ekspertizë për të prodhuar pjesë me cilësi të lartë në mënyrë të qëndrueshme dhe efikase. Duke ndjekur një proces të plotë projektimi dhe prodhimi, prodhuesit mund të bëjnë kallëpe që plotësojnë kërkesat unike të produkteve të tyre dhe të optimizojnë proceset e tyre të formimit me injeksion.
Llojet e veglave të derdhura me injeksion
Formimi me injeksion është një proces prodhimi i përdorur gjerësisht për prodhimin e pjesëve në sasi të mëdha. Ai përfshin injektimin e plastikës së shkrirë në një zgavër të mykut dhe lejimin e saj të ftohet dhe të ngurtësohet në formën e dëshiruar. Vegla e derdhjes me injeksion është procesi i krijimit të kallëpeve të përdorura në formimin me injeksion. Ekzistojnë disa lloje të veglave të formimit me injeksion, secila me avantazhet dhe disavantazhet e veta.
- Kallëpët me dy pllaka Format me dy pllaka janë lloji më i thjeshtë i veglave të formimit me injeksion. Ato përbëhen nga dy pllaka të lidhura së bashku për të formuar një zgavër myku. Plastika e shkrirë injektohet në vrimë përmes një porte dhe lihet të ftohet dhe të ngurtësohet. Pasi të krijohet pjesa, dy pllakat ndahen dhe sasia nxirret. Format me dy pllaka përdoren zakonisht për komponentë të përmasave të vogla dhe të mesme me gjeometri të thjeshta.
- Format me tre pllaka Format me tre pllaka janë të ngjashëm me kallëpet me dy pllaka, por ato kanë një pllakë shtesë, të njohur si pllakë zhveshëse, e cila ndan pjesën e derdhur nga sistemi i kalimit. Sistemi vrapues është rrjeti i kanaleve që dërgon plastikën e shkrirë në zgavrën e kallëpit. Format me tre pllaka përdoren për pjesë më të rëndësishme dhe gjeometri më komplekse.
- Kallëpët e nxehtë të vrapuesit Në kallëpet e vrapuesve të nxehtë, plastika e shkrirë injektohet drejtpërdrejt në zgavrën e kallëpit përmes një sërë kanalesh të nxehta dhe jo përmes një porte. Kjo zvogëlon materialin e humbur në sistemin e kalimit, duke rezultuar në një proces më efikas. Format e vrapuesve të nxehtë përdoren për prodhimin me volum të lartë të pjesëve komplekse.
- Kallëpët e familjes Kallëpet familjare prodhojnë pjesë të shumta në një kallëp të vetëm. Ata kanë zgavra të ndryshme të rregulluara në një mënyrë që lejon prodhimin e domeneve të shumta në të njëjtën kohë. Kallëpet familjare përdoren zakonisht për pjesët me vëllime të vogla dhe të mesme.
- Kallëpët e futur Format e futura prodhojnë pjesë që kërkojnë futje metalike ose plastike. Insertet vendosen në zgavrën e kallëpit përpara se të injektohet plastika e shkrirë. Pasi plastika të jetë ftohur dhe ngurtësuar, pjesa dhe futja janë të lidhura përgjithmonë. Format e futjes përdoren për pozicione që kërkojnë forcë, qëndrueshmëri ose tërheqje estetike.
- Mbiformim Mbiformimi është një proces në të cilin një pjesë derdhet mbi një tjetër. Shpesh përdoret për pozicione që kërkojnë një prekje të butë ose kontroll të përmirësuar. Mbiformimi përfshin vendosjen e një pjese të nënshtresës ose bazës së pari dhe më pas derdhjen e një materiali të dytë mbi të. Materiali i dytë mund të jetë një lloj tjetër plastike, një material i ngjashëm me gomë ose një elastomer termoplastik.
Si përfundim, zgjedhja e veglave të formimit me injeksion varet nga lloji i pjesës që prodhohet, vëllimi i kërkuar i prodhimit dhe niveli i kompleksitetit të përfshirë në projektimin e pjesës. Zgjedhja e veglave të duhura është thelbësore për të siguruar që procesi të jetë efikas dhe me kosto efektive.
Udhëzimet e Dizajnit të Molding Injection
Formimi me injeksion është një proces prodhimi i përdorur gjerësisht për prodhimin e pjesëve plastike. Projektimi i pjesëve për formimin me injeksion kërkon një kuptim të mirë të procesit, materialeve dhe udhëzimeve të projektimit që duhet të ndiqen për të siguruar që detajet të mund të prodhohen me sukses. Këtu janë disa udhëzime të projektimit të derdhjes me injeksion për t'u mbajtur në mend:
Trashësia e murit, Trashësia e murit të pjesës duhet të jetë uniforme dhe sa më e hollë të jetë e mundur duke ruajtur forcën dhe funksionalitetin e kërkuar. Kjo ndihmon në reduktimin e kohës së ftohjes dhe ciklit dhe minimizon rrezikun e deformimeve dhe shenjave të fundosjes.
Brinjë dhe boss Brinjë dhe boss mund të përdoren për të rritur forcën dhe ngurtësinë e pjesës. Brinjët duhet të jenë jo më shumë se 60% e trashësisë nominale të murit, dhe bosat duhet të jenë 1.5 herë më shumë se trashësia nominale e murit.
Këndi i rrymës, Një kënd tërheqjeje prej të paktën 1-2 gradë duhet të përdoret në të gjitha sipërfaqet vertikale për të lehtësuar nxjerrjen e pjesëve dhe për të parandaluar dëmtimin e mykut.
Filetat dhe Radii Këndet dhe skajet e mprehta duhet të shmangen për të parandaluar përqendrimin e stresit, i cili mund të çojë në plasaritje dhe dështim. Në vend të kësaj, filetot dhe rrezet duhet të shpërndajnë stresin dhe të përmirësojnë forcën e pjesës.
Portat dhe vrapuesit Vendndodhja dhe dizajni i portave dhe vrapuesve janë kritike për arritjen e cilësisë së mirë të pjesëve. Hyrjet duhet të jenë sa më të vogla në pjesën më të trashë të pjesës. Vrapuesit duhet të projektohen për të minimizuar rënien e presionit dhe për të maksimizuar rrjedhën.
Mbarimi i sipërfaqes Mbarimi i sipërfaqes së pjesës duhet të specifikohet në bazë të kërkesave të aplikimit. Mund të kërkohet një përfundim më i lartë i sipërfaqes për pjesët e dukshme, ndërsa një sipërfaqe më e ulët mund të jetë e pranueshme për pjesët e fshehura.
Zgjedhja e materialit Materiali i përzgjedhur për pjesën duhet të jetë i përshtatshëm për formim me injeksion dhe të plotësojë vetitë e kërkuara mekanike, termike dhe kimike.
Operacionet dytësore në derdhjen me injeksion
Formimi me injeksion është një proces i gjithanshëm prodhimi që përdoret për të prodhuar pjesë të ndryshme plastike. Përveç procesit primar të formimit, shumë pozicione kërkojnë operacione dytësore për të arritur formën, përfundimin ose funksionalitetin e dëshiruar. Këtu janë disa operacione dytësore të përditshme në formimin me injeksion:
- Prerja është heqja e materialit të tepërt nga pjesa e derdhur pasi të jetë nxjerrë nga kallëpi. Kjo zakonisht bëhet duke përdorur një makinë prerëse ose një makinë CNC. Prerja shpesh kërkohet për të arritur formën dhe madhësinë përfundimtare të pjesës.
- Saldimi kombinon dy ose më shumë pjesë plastike duke përdorur nxehtësinë, presionin ose një kombinim të të dyjave. Kjo shpesh përdoret për të krijuar veçori më të mëdha ose më komplekse që nuk mund të prodhohen në një kallëp të vetëm.
- Dekorimi është procesi i shtimit të veçorive vizuale ose funksionale në sipërfaqen e pjesës së derdhur. Kjo mund të përfshijë pikturimin, printimin, etiketimin ose aplikimin e një teksture ose modeli.
- Montimi është procesi i bashkimit të shumë pjesëve për të krijuar një produkt të plotë. Kjo mund të bëhet duke përdorur mbërthyes, ngjitës ose teknika të tjera bashkimi.
- Formimi i futjes Formimi i futur është derdhja e plastikës rreth një futjeje metalike ose plastike të paraformuar. Kjo përdoret shpesh për të krijuar pjesë me një nivel të lartë të forcës ose qëndrueshmërisë.
- Mbiformim Mbiformimi është procesi i formimit të një materiali të dytë mbi një pjesë të paraformuar. Kjo mund të shtojë një sipërfaqe me prekje të butë, të përmirësojë kapjen ose të krijojë një pjesë me dy ngjyra ose shumë materiale.
- Veshja aplikon një shtresë të hollë materiali në sipërfaqen e pjesës për të përmirësuar pamjen, qëndrueshmërinë ose vetitë e tjera. Kjo mund të përfshijë veshje të tilla si veshjet e kromit, nikelit ose pluhurit.
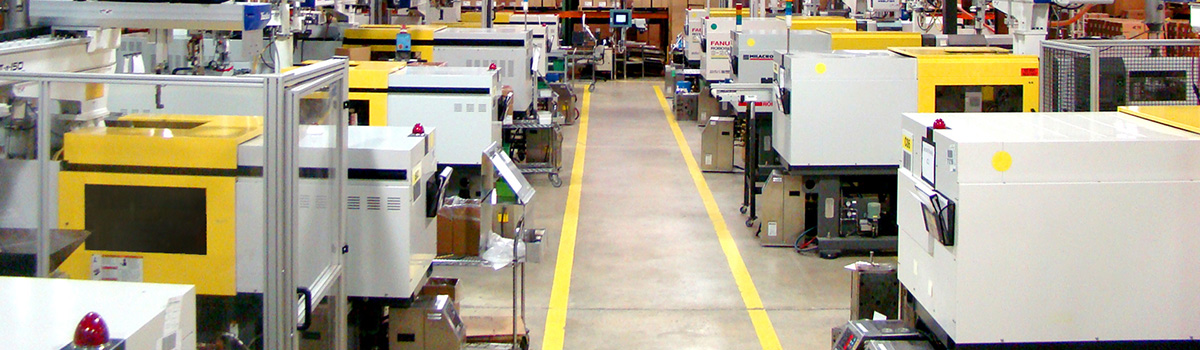
Përparësitë e formimit të injeksionit plastik
Formimi me injeksion plastik është një proces prodhimi i përdorur gjerësisht për prodhimin e pjesëve plastike me saktësi, qëndrueshmëri dhe cilësi të lartë. Ai përfshin injektimin e plastikës së shkrirë në një zgavër të mykut dhe lejimin e saj të ftohet dhe ngurtësohet. Këtu janë disa avantazhe të formimit me injeksion plastik:
- Efikasitet dhe produktivitet i lartë Formimi me injeksion plastik është një proces shumë efikas dhe i automatizuar që mund të prodhojë vëllime të mëdha pjesësh me qëndrueshmëri dhe cilësi të lartë. Me teknologjinë e avancuar të automatizimit, koha e ciklit të prodhimit mund të reduktohet në sekonda, gjë që lejon prodhimin me volum të lartë të pjesëve komplekse dhe të ndërlikuara.
- Formimi me injektim me saktësi dhe precizion të lartë rrit saktësinë dhe saktësinë në prodhimin e pjesëve komplekse dhe të ndërlikuara. Makineritë e kontrolluara nga kompjuteri dhe softueri i avancuar mundësojnë toleranca të ngushta me përsëritshmëri dhe saktësi të lartë.
- Shkathtësia Formimi me injeksion është një proces i gjithanshëm që mund të prodhojë një gamë të gjerë pjesësh plastike të madhësive, formave dhe kompleksitetit të ndryshëm. Procesi mund të përdoret për të bërë gjithçka, nga copa të vogla me detaje të ndërlikuara deri në sasi të mëdha me gjeometri komplekse.
- Fleksibiliteti i materialit Formimi me injeksion mund të përdorë një gamë të gjerë materialesh plastike, duke përfshirë termoplastikë, termoset dhe elastomerë. Kjo lejon prodhimin e pjesëve me veti të ndryshme mekanike, termike dhe kimike.
- Prodhimi i ulët i mbetjeve Formimi me injektim është një proces prodhimi me pak mbetje pasi gjeneron mbetje minimale gjatë prodhimit. Çdo material i tepërt mund të riciklohet dhe ripërdoret lehtësisht në prodhim, duke e bërë atë një proces prodhimi miqësor ndaj mjedisit.
- Kostot e reduktuara të punës Shkalla e lartë e automatizimit në formimin me injeksion minimizon nevojën për procese intensive të punës, duke ulur ndjeshëm kostot e punës. Kjo gjithashtu redukton rrezikun e gabimit njerëzor, duke përmirësuar cilësinë dhe qëndrueshmërinë e produktit përfundimtar.
- Operacione të reduktuara pas prodhimit Formimi me injeksion prodhon pjesë me saktësi dhe konsistencë të lartë, duke reduktuar nevojën për operacione pas prodhimit si prerje, shpim ose bluarje. Kjo zvogëlon kohën e prodhimit dhe koston e produktit përfundimtar.
- Konsistenca dhe Cilësia Formimi me injeksion prodhon pjesë me një nivel të lartë konsistence dhe cilësie. Teknologjia e avancuar dhe makineritë e kontrolluara nga kompjuteri sigurojnë që çdo detaj të jetë identik në formë, madhësi dhe cilësi.
- Fleksibiliteti i dizajnit Formimi me injeksion ofron një shkallë të lartë fleksibiliteti të projektimit, pasi lejon prodhimin e pjesëve me gjeometri komplekse, prerje të poshtme dhe detaje të ndërlikuara. Kjo do t'u mundësojë stilistëve të krijojnë pjesë me forma dhe funksione unike që nuk mund të bëhen duke përdorur procese të tjera prodhimi.
- Kosto-efektive për prodhimin me volum të lartë Formimi me injeksion është një proces me kosto efektive për prodhimin e pjesëve plastike. Kostoja fillestare e veglave mund të jetë e lartë, por kostoja për pjesë zvogëlohet me rritjen e vëllimit të prodhimit. Kjo e bën atë një proces ideal për prodhimin e sasive të mëdha të pjesëve.
Formimi me injektim të plastikës ofron shumë përparësi, duke e bërë atë një zgjedhje popullore për prodhimin e pjesëve plastike. Efikasiteti i lartë, saktësia, shkathtësia, fleksibiliteti i materialit, prodhimi i ulët i mbetjeve, kostot e reduktuara të punës dhe qëndrueshmëria dhe cilësia e bëjnë atë një proces ideal për aplikime të ndryshme. Aftësia për të prodhuar pjesë komplekse dhe të ndërlikuara me fleksibilitet të lartë të projektimit dhe kosto-efektivitet për prodhim me volum të lartë e bën atë një proces prodhimi shumë të kërkuar.
Disavantazhet e derdhjes me injeksion plastik
Formimi me injeksion plastik është një proces prodhimi i përdorur gjerësisht që përfshin injektimin e plastikës së shkrirë në një zgavër të mykut për të prodhuar një gamë të gjerë të pjesëve dhe produkteve plastike. Megjithëse formimi me injeksion plastik ka përfitime të shumta, ka edhe disa disavantazhe. Këtu janë disa nga disavantazhet kryesore të derdhjes me injeksion plastik:
- Kostot e larta të veglave: Kostoja e projektimit dhe prodhimit të një kallëpi për formimin me injeksion plastik mund të jetë shumë i lartë. Kjo për shkak se kallëpi duhet të bëhet nga materiale me cilësi të lartë dhe të përpunohet saktësisht për të krijuar pjesën e dëshiruar. Për më tepër, kostoja e projektimit dhe prodhimit të kallëpit mund të jetë penguese për prodhime në shkallë të vogël, duke e bërë formimin me injeksion plastik më pak ekonomik për prodhimin me vëllim të ulët.
- Kohë të gjata të prodhimit: Procesi i projektimit dhe prodhimit të një kallëpi për formimin me injeksion plastik mund të zgjasë shumë, gjë që mund të vonojë prodhimin e pjesëve plastike. Kjo mund të jetë veçanërisht problematike për bizneset që duhet t'i përgjigjen shpejt ndryshimeve në kërkesën e tregut ose të zhvillojnë me shpejtësi produkte të reja.
- Fleksibilitet i kufizuar: Pasi të projektohet dhe prodhohet kallëpi, është më e lehtë dhe më e lirë të ndryshohet dizajni ose të modifikohet procesi i prodhimit. Kjo mund të kufizojë fleksibilitetin e formimit me injeksion plastik dhe ta bëjë atë më pak të përshtatshëm për prodhimin e produkteve me porosi ose të një lloji.
- Shqetësimet mjedisore: Formimi me injektim të plastikës mbështetet në sasi të mëdha plastike, të cilat mund të kenë ndikime negative ekologjike. Mbetjet plastike janë një çështje e madhe mjedisore dhe formimi me injeksion plastik mund të kontribuojë në këtë problem. Për më tepër, procesi i prodhimit të produkteve plastike kërkon përdorimin e energjisë dhe burimeve natyrore, të cilat mund të ndikojnë më tej në mjedis.
- Shkalla e lartë e skrapit: Formimi me injeksion plastik mund të prodhojë një material të konsiderueshëm skrap, i cili mund të jetë i shtrenjtë për t'u asgjësuar ose ricikluar. Përveç kësaj, prodhimi i materialit skrap mund të rrisë koston e përgjithshme të prodhimit dhe të zvogëlojë efikasitetin e procesit të prodhimit.
- Opsionet e kufizuara të materialeve: Formimi me injeksion plastik përdoret kryesisht për prodhimin e pjesëve dhe produkteve nga materiale termoplastike, të cilat kanë veti të kufizuara në krahasim me materialet e tjera si metalet ose qeramika. Kjo mund ta bëjë formimin me injeksion plastik më pak të përshtatshëm për aplikime që kërkojnë forcë të lartë, rezistencë ndaj temperaturës ose veçori të tjera të avancuara.
Kufizimet e derdhjes me injeksion plastik
Ndërsa formimi me injeksion plastik ofron përparësi të shumta, kufizime të caktuara shoqërohen gjithashtu me procesin. Këtu janë disa kufizime të formimit me injeksion plastik:
Kostoja e lartë fillestare e veglave: Kostoja fillestare e projektimit dhe prodhimit të kallëpit mund të rritet. Forma duhet të jetë e saktë dhe e qëndrueshme për t'i bërë ballë procesit të përsëritur të derdhjes me injeksion dhe kjo mund të kërkojë një investim të konsiderueshëm paraprak, veçanërisht për kallëpe komplekse ose të mëdha.
Koha e udhëheqjes: Koha e prodhimit për prodhimin e kallëpit mund të jetë e rëndësishme, duke filluar nga javë në muaj, në varësi të kompleksitetit dhe madhësisë së mykut. Kjo mund të shkaktojë vonesa në afatin kohor të prodhimit, veçanërisht për projektet e ndjeshme ndaj kohës.
Kufizimet e projektimit: Formimi me injeksion ka kufizime të caktuara të projektimit që duhet të merren parasysh. Për shembull, arritja e trashësisë uniforme të murit në të gjithë pjesën është kritike për të siguruar mbushjen dhe ftohjen e duhur. Për më tepër, në sipërfaqet vertikale kërkohen kënde tërheqjeje për të mundësuar nxjerrjen e lehtë nga kallëpi.
Kufizimet e madhësisë së pjesës: Formimi me injeksion është më i përshtatshmi për prodhimin e pjesëve të vogla dhe të mesme. Pjesët e mëdha mund të kërkojnë pajisje të specializuara dhe kallëpe më të mëdha, duke shtuar koston dhe kompleksitetin.
Zgjedhja e materialit: Ndërsa derdhja me injeksion lejon një gamë të gjerë materialesh plastike, zgjedhja e materialit është ende e kufizuar në krahasim me proceset e tjera të prodhimit. Materialet me pika të larta shkrirjeje ose karakteristika të dobëta rrjedhëse mund të mos jenë të përshtatshme për formimin me injeksion.
Mbarimi i sipërfaqes: Procesi i derdhjes me injeksion mund të rezultojë në vija të dukshme të thurura ose vija ndarëse në sipërfaqen e pjesës. Arritja e një përfundimi të sipërfaqes me cilësi të lartë mund të jetë sfiduese dhe mund të kërkohen metoda të tjera, si lustrimi ose veshja.
Prerjet e kufizuara: Prerjet e poshtme janë veçori ose detaje në një pjesë që e pengojnë atë të hiqet lehtësisht nga kallëpi. Prerjet e poshtme mund të komplikojnë procesin e nxjerrjes dhe të kërkojnë veçori shtesë të kallëpit ose operacione dytësore për të arritur gjeometrinë e dëshiruar të pjesës.
Opsione të kufizuara riparimi: Nëse një myk është dëmtuar ose ka nevojë për modifikim, mund të jetë i kushtueshëm dhe kërkon kohë për të riparuar ose ndryshuar mykun ekzistues. Ndonjëherë, mund të duhet të prodhohet një kallëp krejtësisht i ri, duke çuar në shpenzime dhe vonesa shtesë.
Pavarësisht këtyre kufizimeve, derdhja me injeksion plastik mbetet një proces prodhimi shumë i gjithanshëm dhe i përdorur gjerësisht për prodhimin e pjesëve plastike. Duke i konsideruar me kujdes këto kufizime gjatë fazave të projektimit dhe planifikimit të prodhimit, është e mundur të zbutet ndikimi i tyre dhe të përdoren në mënyrë efektive avantazhet e formimit me injeksion.
Aplikimet e derdhjes me injeksion plastik
Formimi me injeksion plastik është një proces i gjithanshëm prodhimi që mund të prodhojë një gamë të gjerë pjesësh plastike. Këtu janë disa nga aplikimet e derdhjes me injeksion plastik:
- Produktet e konsumit: Formimi me injeksion përdoret gjerësisht për të prodhuar produkte të ndryshme, të tilla si lodra, enë gatimi dhe elektronikë. Procesi mund të prodhojë pjesë me cilësi të lartë me gjeometri të ndërlikuara dhe dimensione të sakta, duke e bërë atë ideal për produktet që kërkojnë toleranca të ngushta dhe forma komplekse.
- Pjesët e automobilave: Shumë komponentë plastikë të automobilave, të tilla si komponentët e pultit, dorezat e dyerve dhe ndriçimi, prodhohen duke përdorur derdhje me injeksion. Procesi lejon vëllime të larta prodhimi dhe cilësi të qëndrueshme, duke e bërë atë një opsion me kosto efektive për prodhuesit e automobilave.
- Pajisjet mjekësore: Formimi me injeksion përdoret zakonisht për të prodhuar pajisje mjekësore, të tilla si shiringa, inhalatorë dhe pajisje diagnostikuese. Procesi mund të prodhojë pjesë me saktësi dhe qëndrueshmëri të lartë, duke siguruar cilësinë dhe besueshmërinë e pajisjeve.
- Paketimi: Formimi me injeksion përdoret gjerësisht për prodhimin e ambalazheve plastike, të tilla si kontejnerë, kapakë dhe kapakë. Procesi mund të ketë pjesë me dimensione të qëndrueshme dhe përfundime me cilësi të lartë, duke e bërë atë ideal për paketim me një pamje tërheqëse dhe një përshtatje të sigurt.
- Hapësira ajrore dhe mbrojtja: Formimi me injeksion prodhon komponentë të ndryshëm të hapësirës ajrore dhe mbrojtëse, të tilla si ambientet e brendshme të avionëve, ndriçimi dhe sistemet e komunikimit. Procesi mund të ketë pjesë me materiale të lehta dhe të qëndrueshme, duke i bërë ato të përshtatshme për aplikime që kërkojnë raporte të larta forcë-peshë.
- Ndërtimi: Formimi me injeksion mund të prodhojë materiale të ndryshme ndërtimi, të tilla si pllaka plastike, çati dhe mur anësor. Procesi mund të ketë pjesë me dimensione konsistente dhe përfundime me cilësi të lartë, duke e bërë atë një opsion tërheqës për kompanitë e ndërtimit.
- Sporti dhe argëtimi: Formimi me injeksion përdoret gjerësisht në prodhimin e pajisjeve sportive, të tilla si shkopinj golfi, raketat e tenisit dhe komponentët e biçikletave. Procesi mund të prodhojë pjesë me materiale të lehta dhe gjeometri të sakta, duke siguruar performancën dhe qëndrueshmërinë e pajisjes.
Në përgjithësi, derdhja me injeksion plastik është një proces prodhimi i gjithanshëm dhe i përdorur gjerësisht që mund të prodhojë pjesë plastike me cilësi të lartë për aplikime të ndryshme. Procesi mund të përshtatet për të përmbushur kërkesat specifike të dizajnit dhe prodhimit, duke e bërë atë një opsion tërheqës për prodhuesit në industri të shumta.
Industria e automobilave dhe derdhja me injeksion plastik
Industria e automobilave është një përdorues i rëndësishëm i teknologjisë së formimit me injeksion plastik. Procesi i formimit të plastikës me injektim ka revolucionarizuar prodhimin e pjesëve dhe komponentëve të automobilave, duke bërë të mundur prodhimin e formave komplekse me saktësi dhe saktësi të lartë. Këtu janë disa nga mënyrat se si përdoret derdhja me injeksion plastik në industrinë e automobilave:
- Pjesët e brendshme: Formimi me injeksion plastik prodhon shumë faktorë të brendshëm, duke përfshirë komponentët e pultit, panelet e dyerve, pjesët e zbukurimit dhe më shumë. Këto pjesë mund të dizajnohen me forma dhe tekstura të ndërlikuara dhe të personalizohen për t'iu përshtatur stilit dhe funksionalitetit të secilit model automjeti.
- Pjesët e jashtme: Formimi me injeksion plastik përdoret gjithashtu për të prodhuar veçori të ndryshme të jashtme, duke përfshirë parakolpët, grilat, pasqyrat anësore dhe më shumë. Këto pjesë mund të projektohen për t'i bërë ballë kushteve ekstreme të motit dhe janë bërë në shumë ngjyra dhe përfundime.
- Komponentët nën kapuç: Formimi me injeksion plastik prodhon shumë karakteristika nën kapuç, duke përfshirë mbulesat e motorit, sistemet e marrjes së ajrit dhe pjesët e sistemit të ftohjes. Këta komponentë kërkojnë temperaturë të lartë dhe rezistencë kimike, e cila mund të arrihet me materiale termoplastike.
- Komponentët elektrikë dhe elektronikë: Formimi me injeksion plastik prodhon komponentë të ndryshëm elektrikë dhe elektronikë, duke përfshirë lidhës, strehë dhe sensorë. Këta komponentë kërkojnë saktësi dhe besueshmëri të lartë, të cilat mund të arrihen me saktësinë dhe qëndrueshmërinë e derdhjes me injeksion plastik.
- Pesha e lehtë: Formimi me injeksion plastik përdoret shpesh për të prodhuar pjesë të lehta që ndihmojnë në reduktimin e peshës së përgjithshme të një automjeti, duke përmirësuar efikasitetin e karburantit dhe duke reduktuar emetimet. Pesha e lehtë mund të përmirësojë gjithashtu trajtimin dhe performancën e një automjeti.
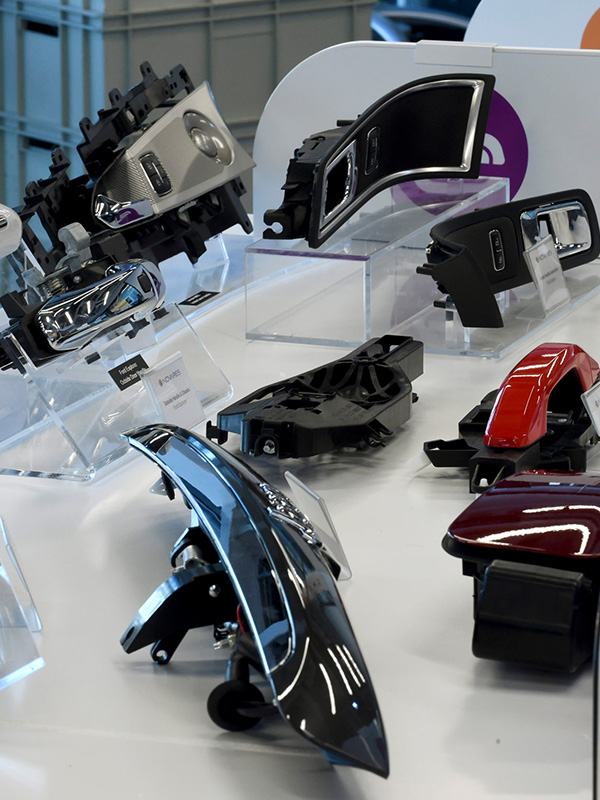
Industria Mjekësore dhe Formimi me Injeksion Plastik
Formimi me injeksion plastik përdoret gjerësisht në industrinë mjekësore për të prodhuar një sërë pajisjesh dhe përbërësish mjekësorë. Procesi i formimit me injeksion plastik lejon prodhimin e formave komplekse me saktësi dhe saktësi të lartë, duke e bërë atë një metodë prodhimi ideale për shumë aplikime mjekësore. Këtu janë disa nga mënyrat se si përdoret derdhja me injeksion plastik në industrinë mjekësore:
- Pajisjet mjekësore: Formimi me injeksion plastik prodhon pajisje të ndryshme mjekësore, duke përfshirë instrumente kirurgjikale, mjete diagnostikuese, sisteme të shpërndarjes së barnave, etj. Këto pajisje shpesh kërkojnë saktësi dhe saktësi të lartë, dhe formimi me injeksion plastik mund t'i plotësojë këto kërkesa.
- Implantet: Formimi me injeksion plastik përdoret gjithashtu për të prodhuar një sërë implantesh, duke përfshirë zëvendësimet e kyçeve, implantet dentare dhe më shumë. Këto implante mund të dizajnohen që të përputhen me anatominë e pacientit dhe të prodhohen me materiale biokompatibile.
- Pajisjet laboratorike: Formimi me injeksion plastik prodhon pipeta, mikropllaka dhe epruveta. Këta komponentë kërkojnë saktësi dhe saktësi të lartë për të siguruar rezultate të besueshme.
- Paketimi: Formimi me injeksion plastik përdoret për prodhimin e ambalazheve për pajisjet mjekësore, duke përfshirë sistemet e barrierave sterile dhe paketimin me porosi për produkte individuale. Këto zgjidhje paketimi mund të ndihmojnë në ruajtjen e sterilitetit dhe integritetit të pajisjes mjekësore.
- Pajisjet me përdorim të vetëm: Formimi me injeksion plastik shpesh prodhon pajisje me përdorim të vetëm si shiringa, gjilpëra dhe kateterë. Këto pajisje mund të bëhen në vëllim të lartë me një kosto të ulët dhe mund të ndihmojnë në parandalimin e përhapjes së infeksioneve në mjediset e kujdesit shëndetësor.
Produktet e konsumit dhe derdhja me injeksion plastik
Formimi me injeksion plastik përdoret gjerësisht në prodhimin e produkteve të konsumit për shkak të shkathtësisë, efikasitetit dhe kostos së tij. Procesi i derdhjes së plastikës me injektim lejon prodhimin e formave komplekse me saktësi dhe saktësi të lartë, duke e bërë atë një metodë prodhimi ideale për shumë aplikacione konsumatore. Këtu janë disa nga mënyrat se si përdoret derdhja me injeksion plastik në prodhimin e produkteve të konsumit:
- Lodrat: Formimi me injeksion plastik prodhon një gamë të gjerë lodrash, nga figurina të vogla deri tek grupe lojërash më të mëdha. Procesi ju lejon të krijoni dizajne dhe detaje të ndërlikuara dhe të bëni lodra në ngjyra dhe materiale të ndryshme.
- Mallrat shtëpiake: Formimi me injeksion plastik prodhon mallra të ndryshme shtëpiake, duke përfshirë enët e kuzhinës, kontejnerët e magazinimit dhe furnizimet e pastrimit. Këto produkte mund të dizajnohen të jenë të qëndrueshme, të lehta dhe të lehta për t'u përdorur.
- Elektronika: Formimi me injeksion plastik prodhon shumë komponentë elektronikë, duke përfshirë kutitë e kompjuterit, kutitë e telefonit dhe karikuesit. Saktësia dhe saktësia e procesit sigurojnë që këta komponentë të bëhen me një shkallë të lartë konsistence dhe besueshmërie.
- Produktet e kujdesit personal: Formimi me injeksion plastik prodhon produkte unike të kujdesit, duke përfshirë furçat e dhëmbëve, brisqet dhe furçat e flokëve. Këto produkte kërkojnë saktësi dhe saktësi të lartë për të siguruar lehtësinë e përdorimit dhe sigurinë.
- Aksesorë automobilistik: Formimi me injeksion plastik prodhon një sërë aksesorësh automobilistik, duke përfshirë komponentët e pultit, mbajtëset e filxhanëve dhe më shumë. Këta komponentë mund të projektohen për të qenë të lehtë, të qëndrueshëm dhe rezistent ndaj konsumit të përdorimit të përditshëm.
Konsiderata mjedisore në derdhjen me injeksion plastik
Formimi me injeksion plastik është një proces prodhimi i përdorur gjerësisht, por ka implikime të rëndësishme mjedisore. Këtu janë disa nga konsideratat ekologjike në formimin me injeksion plastik:
- Zgjedhja e materialit: Zgjedhja e materialit plastik të përdorur në formimin me injeksion mund të ndikojë ndjeshëm në mjedis. Disa materiale janë të biodegradueshme ose të riciklueshme, ndërsa të tjerët jo. Përdorimi i materialeve të biodegradueshme ose të riciklueshme mund të ndihmojë në reduktimin e ndikimit mjedisor të formimit me injeksion plastik.
- Konsumi i energjisë: Formimi me injektim të plastikës kërkon energji të konsiderueshme për të shkrirë plastikën dhe për ta injektuar atë në kallëp. Pajisjet dhe proceset me efikasitet energjetik, të tilla si makinat elektrike dhe sistemet me qark të mbyllur, mund të reduktojnë konsumin e energjisë dhe ndikimin mjedisor.
- Menaxhimi i mbetjeve: Formimi me injektim të plastikës gjeneron mbetje nga materiali i tepërt, pjesët me defekt dhe paketimi. Praktikat e duhura të menaxhimit të mbetjeve, të tilla si riciklimi dhe ripërdorimi i materialeve të mbeturinave, mund të ndihmojnë në reduktimin e ndikimit mjedisor të formimit me injeksion plastik.
- Përdorimi kimik: Disa kimikate në formacionet me injeksion plastik, të tilla si agjentët e çlirimit të mykut dhe tretësit pastrues, mund të dëmtojnë mjedisin. Përdorimi i alternativave miqësore me mjedisin ose minimizimi i përdorimit të këtyre kimikateve mund të ndihmojë në uljen e ndikimit mjedisor.
- Konsideratat e fundit të jetës: Produktet plastike të prodhuara përmes formimit me injeksion shpesh përfundojnë në deponi, të cilave mund të duhen qindra vjet për t'u degraduar. Projektimi i produkteve për riciklueshmëri ose biodegradueshmëri mund të zvogëlojë ndikimin mjedisor të formimit me injeksion plastik.
E ardhmja e derdhjes me injeksion plastik
E ardhmja e formimit me injeksion plastik duket premtuese, pasi përparimet në teknologji dhe materiale pritet ta bëjnë procesin edhe më efikas, me kosto efektive dhe të qëndrueshëm. Këtu janë disa nga tendencat dhe zhvillimet që ka të ngjarë të formojnë të ardhmen e derdhjes me injeksion plastik:
- Prodhimi i aditivëve: Prodhimi i aditivëve, i njohur gjithashtu si printimi 3D, është një teknologji në zhvillim që mund të transformojë potencialisht formimin me injeksion plastik. Duke përdorur printimin 3D për të krijuar kallëpe, prodhuesit mund të reduktojnë ndjeshëm kohën dhe koston e lidhur me teknikat tradicionale të prodhimit të mykut.
- Prodhimi inteligjent: Prodhimi inteligjent, i cili përfshin automatizimin, analitikën e të dhënave dhe mësimin e makinerive, pritet të revolucionarizojë formimin me injeksion plastik. Prodhuesit mund të përmirësojnë efikasitetin, të reduktojnë mbeturinat dhe të rrisin produktivitetin duke përdorur sensorë dhe analitikë të të dhënave për të optimizuar proceset.
- Materialet e qëndrueshme: Materialet e qëndrueshme, të tilla si bioplastika dhe plastika e ricikluar, po bëhen gjithnjë e më të njohura në industrinë e formimit të injektimit të plastikës. Këto materiale ofrojnë përfitime mjedisore dhe mund të ndihmojnë prodhuesit për të përmbushur qëllimet e qëndrueshmërisë.
- Mikroformimi: Mikroformimi, i cili përfshin prodhimin e pjesëve të vogla me saktësi të lartë, po bëhet më kritik në industri të tilla si kujdesi shëndetësor dhe elektronika. Përparimet në teknologji dhe materiale pritet ta bëjnë formimin mikro më të aksesueshëm dhe me kosto efektive.
- Personalizimi: Ndërsa konsumatorët kërkojnë produkte më të personalizuara, formimi me injeksion plastik pritet të bëhet më fleksibël dhe i personalizueshëm. Përparimet në teknologji, si reagimet në kohë reale dhe mësimi i makinerive, do t'u mundësojnë prodhuesve të prodhojnë produkte të personalizuara shpejt dhe me efikasitet.
Përfundim:
Formimi me injeksion plastik është një proces prodhimi shumë i gjithanshëm dhe efikas që ka revolucionarizuar prodhimin e një game të gjerë produktesh. Nga pajisjet mjekësore te komponentët e automobilave, formimi me injeksion plastik ofron avantazhe të shumta mbi proceset e tjera të prodhimit, duke përfshirë normat e larta të prodhimit, fleksibilitetin e dizajnit dhe efektivitetin e kostos. Me përparime të vazhdueshme në teknologji dhe materiale, e ardhmja e formimit me injeksion plastik duket e ndritshme dhe ky proces ka të ngjarë të luajë një rol edhe më të rëndësishëm në industrinë e prodhimit në vitet e ardhshme.