ہائی حجم انجکشن مولڈنگ
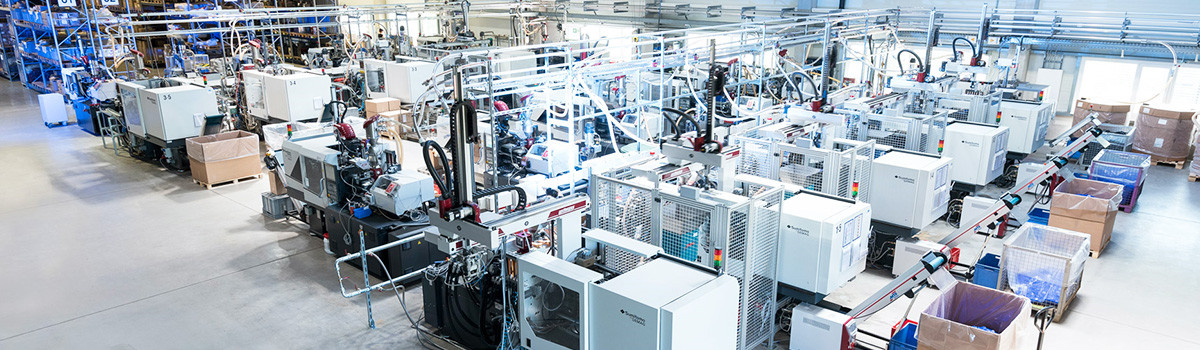
ہائی والیوم انجیکشن مولڈنگ (ہائی والیوم پروڈکشن): پلاسٹک انجیکشن مولڈنگ
ہزاروں سے زیادہ پلاسٹک انجیکشن مولڈنگ اور پلاسٹک مینوفیکچرنگ کی سہولیات کے ساتھ تمام لفظوں میں سے انتخاب کرنے کے لیے، مولڈنگ کمپنی کو نمایاں کرنے والی اعلیٰ خصوصیات میں سے ایک کیا ہے؟ فراہم کنندہ کا انتخاب کرتے وقت، بہت سے عوامل کو مدنظر رکھا جانا چاہیے۔ بشمول صلاحیتیں، کوالٹی اشورینس، کمپنی کی ساکھ، لاگت، اور ترسیل کا وقت۔ آپ کی ضروریات کو پورا کرنے کے لیے صحیح پلاسٹک انجیکشن مولڈر تلاش کرنا وقت لگتا ہے لیکن پہلے آپ کی کم اور زیادہ مقدار کی ضروریات کا تعین کرنا اور وہ وقت کے ساتھ کیسے بدل سکتے ہیں، آپ کے اختیارات کو کم کرنے میں مدد کرے گا۔
DJmolding کی ہائی والیوم انجیکشن مولڈنگ سروس
DJmolding میں، ہماری پیداواری سہولت کئی مشینوں اور ہنر مند آپریٹرز کے ساتھ ایک اعلیٰ درجے کا، موثر آپریشن ہے۔ ہمارے متنوع سازوسامان کی وجہ سے، ہم مختلف قسم کی ملازمتوں کو سنبھال سکتے ہیں جو ان کی صنعتوں، پلاسٹک کے معیار، اور تیار کردہ ٹکڑوں کی تعداد میں بہت زیادہ ہیں۔ کم اور زیادہ والیوم، ڈیزائن سے لے کر مینوفیکچرنگ کے ذریعے، اندرون ملک مکمل کیا جا سکتا ہے جو ہمارے صارفین کو قیمت، معیار اور لیڈ ٹائم میں مسابقتی فوائد فراہم کرتا ہے۔
ڈی جے مولڈنگ کی انجیکشن مولڈنگ ایک ثابت شدہ تکنیک ہے جو اعلی حجم کی تیاری کے عمل ہے۔ یہ ایک خصوصی سروس ہے جو ایک ماہ میں لاکھوں ٹکڑوں تک کی مقدار میں مکمل پیداواری معیار کے پرزے پیش کرتی ہے۔ ہائی والیوم پلاسٹک انجیکشن مولڈنگ اعلی رواداری کی درستگی، کم سکریپ نقصان، اور لاگت کی بچت کی اجازت دیتی ہے۔
ہمارے زیادہ تر اعلیٰ حجم کی مولڈنگ کا سامان کمپیوٹرائزڈ ہے اور کارکردگی کو بڑھانے اور معیار کی حفاظت کے لیے مکینیکل سسٹمز کا استعمال کرتا ہے۔ ہمارے "کوالٹی کنٹرول سسٹم" کو دیکھنا یقینی بنائیں کہ ہم کس طرح یہ یقینی بناتے ہیں کہ تمام ہائی والیوم پروڈکشن میں کوالٹی کنٹرول شامل ہے۔ اس قسم کی مینوفیکچرنگ درمیانے اور بڑے سائز کے کاروبار یا بڑے پیمانے پر پیداوار کے لیے مثالی ہے۔
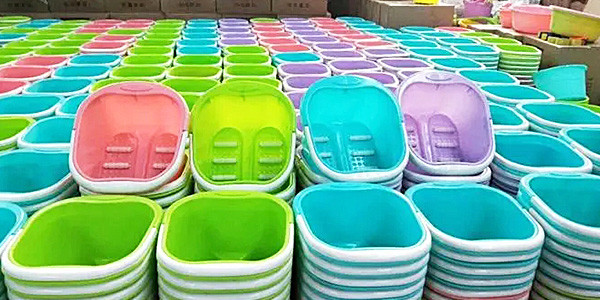
DJmolding کے ہائی والیوم انجکشن مولڈنگ کے فوائد
*تیز رفتار سے مزید پرزے تیار کرتا ہے۔
*کارخانہ دار کے لیے یونٹ کے اخراجات اور سائیکل کا وقت کم کریں۔
*پرزوں کی درست اور مستقل، اعلیٰ معیار کی بڑے پیمانے پر پیداوار
*پروڈکشن کو اکثر ٹھوس، قابل اعتماد مشینری کے ساتھ خودکار کیا جا سکتا ہے، یہاں تک کہ غیر کام کے اوقات میں بھی
* کم سے کم پوسٹ پروڈکشن کا کام
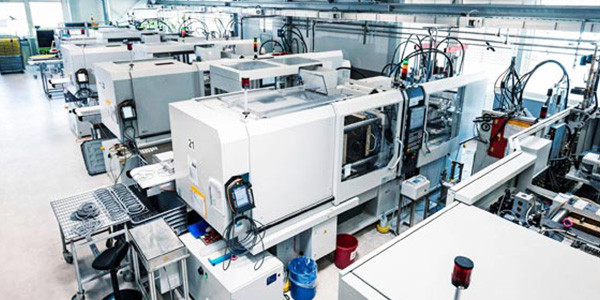
اپنی مرضی کے مطابق ہائی والیوم مولڈنگ (پلاسٹک انجیکشن پروڈکٹ)
DJmolding کے حسب ضرورت سانچوں اور ہائی والیوم مولڈنگ میں پروٹوٹائپ سے لے کر مکمل پیداواری مقدار تک سب کچھ شامل ہے۔ ہمارے ہائی والیوم مولڈز، چاہے شارٹ رن، ہائی والیوم، یا ملٹی کیویٹی، کی نگرانی اور کنٹرول کیا جاتا ہے تاکہ آپ کو مولڈ ڈیزائن اور تعمیر کے تمام پہلوؤں کے بارے میں یقین دلایا جا سکے۔ پیداوار کی تفصیل پر یہ توجہ اہداف، مقاصد، اور پیش سیٹ پراجیکٹ کے نتائج کی تصدیق کرتی ہے کہ عمل کے ہر مرحلے میں شیڈول پر ہیں۔ تمام ہائی والیوم مولڈنگ، ڈیزائن سے لے کر مینوفیکچرنگ تک، گھر میں مکمل ہوتی ہے اور ہمارے صارفین کو قیمت، معیار اور لیڈ ٹائم میں مسابقتی فوائد فراہم کرتی ہے۔
ڈی جے مولڈنگ کلائنٹ کے ساتھ مصنوعات کو ڈیزائن اور انجینئر کرنے کے لیے کام کرتی ہے، لاگت کی کارکردگی کے لیے سب سے زیادہ مؤثر ہائی والیوم مولڈ تیار کرتی ہے۔ ہم بہترین معیار کے ہائی والیوم مولڈز فراہم کرتے ہیں جو خصوصی طور پر پلاسٹک انجیکشن مولڈنگ انڈسٹری کو فراہم کرتے ہیں، خدمات کی ایک وسیع رینج پیش کرتے ہیں۔ کم والیوم مولڈنگ سے لے کر مولڈنگ داخل کرنے اور پیڈ پرنٹنگ تک، PTI, Inc. وہ برانڈ ہے جس پر آپ اپنی پلاسٹک انجیکشن مولڈنگ سروسز کے لیے بھروسہ کر سکتے ہیں۔
مختلف شعبوں جیسے کہ میڈیکل، الیکٹریکل، ہینڈ ٹول، کمیونیکیشنز، اور آٹوموٹو انڈسٹریز میں صارفین کے لیے DJmolding پروٹوٹائپ اجزاء۔ 85-500 ٹن تک کے انجیکشن اور کمپریشن پریس سمیت، DJmolding کا زیادہ تر ہائی والیوم مولڈنگ کا سامان کمپیوٹرائزڈ ہے اور کارکردگی کو بڑھانے اور معیار کی حفاظت کے لیے مکینیکل سسٹم کا استعمال کرتا ہے۔ DJmolding میں ہم ہر منصوبے پر شراکت داری کا رویہ اپناتے ہیں، پلاسٹک انجیکشن مولڈنگ کا ایک جامع تجربہ فراہم کرنے کے لیے ڈیزائن کی گئی ایک سہولت میں پلاسٹک انجیکشن مولڈنگ کے علم اور تکنیکی مہارت کے سالوں کو لاتے ہیں۔
ہائی والیوم مولڈ بلڈنگ کے لیے ٹیکنالوجی، آلات اور کوالیفائیڈ مولڈ بلڈرز کے امتزاج کی ضرورت ہوتی ہے تاکہ پلاسٹک کے اجزاء کے لیے تقریباً لامحدود جیومیٹری کے ساتھ تیزی سے انجیکشن مولڈ تیار کیا جا سکے۔
ڈیزائن سے لے کر ڈیلیوری تک، DJmolding شروع سے آخر تک آپ کے پورے ٹول بلڈنگ پروگرام کو مربوط کر سکتی ہے۔ اس کے کوالٹی اشورینس پروگرام کی مدد سے، پی ٹی آئی کا مشن ایسی مولڈ پراڈکٹس فراہم کرنا ہے جو اپنے صارفین کی ضروریات اور توقعات کو پوری طرح پورا کرتی ہوں یا اس سے زیادہ ہوں۔ کمپنی کی انتظامیہ مسلسل معیار کی ترقی کے لیے پرعزم ہے۔ اعلیٰ معیار اور موثر ہائی والیوم مولڈنگ سروسز کے لیے، DJmolding سے رابطہ کریں۔ آج
بہت سی کمپنیاں یہ صلاحیت نہیں رکھتی ہیں کہ وہ مولڈ بنانے کا تجربہ ختم کرنے کے لیے اتنی جامع شروعات فراہم کر سکیں۔ چاہے آپ چند تیز پروٹوٹائپس، ہزاروں مارکیٹ کے لیے تیار کنزیومر پلاسٹک، یا ایک ملین پروڈکشن پارٹس تلاش کر رہے ہوں، DJmolding آپ کی ضرورت فراہم کر سکتا ہے۔ کم اور زیادہ والیوم، ہم فخر کے ساتھ اصرار کرتے ہیں کہ ہر آرڈر ایک ہی سطح کے معیار کا ہے۔ آج ہی ہمارے ماہرین سے رابطہ کریں۔
ڈیزائن سے لے کر ڈیلیوری تک، DJmolding شروع سے آخر تک آپ کے پورے ٹول بلڈنگ پروگرام کو مربوط کر سکتی ہے۔ اعلیٰ معیار اور موثر خدمات کے لیے، اپنی معلومات بھیج کر ایک اقتباس کی درخواست کریں۔ info@jasonmolding.com
ہائی حجم انجیکشن مولڈنگ کی تیاری کا عمل بہت سے ایک جیسے پلاسٹک کے پرزے تیار کرتا ہے۔ یہ عمل مقبول ہے کیونکہ یہ لاگت سے موثر، موثر ہے، اور مسلسل، اعلیٰ معیار کے ٹکڑے فراہم کرتا ہے۔ یہ بلاگ پوسٹ ہائی والیوم انجیکشن مولڈنگ کے بارے میں آپ کو درکار ہر چیز کو دریافت کرے گی، بشمول اس کے فوائد، نقصانات، ایپلی کیشنز اور مزید۔
ہائی والیوم انجکشن مولڈنگ کیا ہے؟
ہائی والیوم انجیکشن مولڈنگ ایک مینوفیکچرنگ عمل ہے جو پلاسٹک کے بہت سے ایک جیسے پرزے تیار کرتا ہے۔ اس عمل میں پگھلے ہوئے پلاسٹک کے مواد کو ہائی پریشر اور درجہ حرارت پر ایک مولڈ گہا میں انجیکشن لگانا شامل ہے، جس سے یہ ٹھنڈا ہو کر مطلوبہ شکل میں مضبوط ہو سکتا ہے۔ یہ انتہائی خودکار عمل ایک ہی پروڈکشن رن میں ہزاروں یا یہاں تک کہ لاکھوں ایک جیسے حصے تیار کر سکتا ہے۔
ایک انتہائی موثر پیداواری عمل کامیاب ہائی والیوم انجیکشن مولڈنگ کی کلید ہے۔ اس عمل میں تیز رفتار انجیکشن مولڈنگ مشینوں اور خودکار نظاموں کا استعمال شامل ہے جو پرزوں کی تیز رفتار اور درست پیداوار کو قابل بناتے ہیں۔ مزید برآں، مینوفیکچررز اس بات کو یقینی بنا سکتے ہیں کہ وہ اعلیٰ معیار کے سانچوں کا استعمال کرتے ہوئے اور مخصوص انجیکشن پیرامیٹرز کو لاگو کر کے ہر عنصر کو تصریحات کے مطابق بناتے ہیں۔
ہائی والیوم انجیکشن مولڈنگ کے سب سے اہم فوائد میں سے ایک یہ ہے کہ اس کی بڑی مقدار میں ایک جیسے حصوں کو تیزی سے اور لاگت سے پیدا کرنے کی صلاحیت ہے۔ مینوفیکچرنگ کا عمل آٹوموٹو، صارفی سامان، طبی آلات اور الیکٹرانکس کی صنعتوں کے لیے بہترین ہے۔
اعلی حجم کے انجیکشن مولڈنگ کا ایک اور فائدہ سخت رواداری کے ساتھ پیچیدہ حصوں کو تیار کرنے کی صلاحیت ہے۔ انجیکشن مولڈنگ کا عمل درست اور مستقل ہے، جس کے نتیجے میں ٹکڑوں کے درمیان کم سے کم فرق کے ساتھ پیچیدہ تفصیلات ہوتی ہیں۔
اس کے بہت سے فوائد کے باوجود، اعلی حجم انجیکشن مولڈنگ میں کچھ حدود ہوتی ہیں۔ مثال کے طور پر، بہت بڑے یا کم سے کم پرزے تیار کرنے کے لیے بہتر انتخاب ہو سکتے ہیں، کیونکہ سانچوں کی لاگت اور پیچیدگی ممنوع ہو سکتی ہے۔ مزید برآں، پلاسٹک کی زیادہ مقدار ماحولیاتی اثرات مرتب کر سکتی ہے، جس سے مینوفیکچررز کے لیے پائیداری اور ری سائیکلنگ کی کوششوں پر غور کرنا ضروری ہو جاتا ہے۔
ہائی والیوم انجیکشن مولڈنگ ایک انتہائی کارآمد اور موثر مینوفیکچرنگ عمل ہے جو ایک جیسے پلاسٹک کے پرزہ جات کی بڑی مقدار تیزی سے اور لاگت سے پیدا کر سکتا ہے۔ یہ صنعتوں کی ایک وسیع رینج کے لیے ایک مثالی انتخاب ہے، اور اس کی درستگی اور مستقل مزاجی اسے سخت رواداری کے ساتھ پیچیدہ حصوں کی تیاری کے لیے ایک مقبول انتخاب بناتی ہے۔ اگرچہ اس کی کچھ حدود ہیں، لیکن اعلیٰ حجم کے انجیکشن مولڈنگ کے فوائد اسے مینوفیکچررز کے لیے ایک قیمتی ٹول بناتے ہیں جو بڑی مقدار میں اعلیٰ معیار کے پلاسٹک کے پرزے تیار کرنا چاہتے ہیں۔
ہائی والیوم انجکشن مولڈنگ کیسے کام کرتی ہے؟
اس عمل میں کئی اہم اقدامات شامل ہیں، جن میں سے ہر ایک اعلیٰ معیار کے پرزے تیار کرنے میں اہم ہے۔ یہ بلاگ پوسٹ اس بات کا خاکہ پیش کرے گی کہ کس طرح ہائی والیوم انجیکشن مولڈنگ کام کرتی ہے، بشمول اس کے اہم اقدامات اور غور و فکر۔
مولڈ ڈیزائن اور تیاری
ہائی والیوم انجیکشن مولڈنگ کا پہلا قدم اس مولڈ کو ڈیزائن اور تیار کرنا ہے جسے مینوفیکچررز پرزے تیار کرنے کے لیے استعمال کریں گے۔ ایک درست ڈیزائن بنانے کے لیے مولڈ بنانے والے کے ساتھ تعاون ضروری ہے جو مطلوبہ پرزے بنانے کے لیے تمام ضروری تصریحات کو پورا کرتا ہو۔ عام طور پر، مینوفیکچررز سٹیل یا ایلومینیم سے مولڈ بناتے ہیں اور انجیکشن مولڈنگ کے عمل کے ہائی پریشر اور درجہ حرارت کو برداشت کرنے کے لیے اسے ڈیزائن کرتے ہیں۔
مادی تیاری
اگلا مرحلہ مینوفیکچررز کے لیے پلاسٹک کا مواد تیار کرنا ہے جسے وہ پرزے تیار کرنے کے لیے استعمال کریں گے۔ مطلوبہ خصوصیات پیدا کرنے کے لیے موزوں پلاسٹک رال کا انتخاب بہت ضروری ہے، کیونکہ استعمال شدہ رال کی قسم مخصوص ضروریات پر منحصر ہے۔ اس کے بعد رال کو انجیکشن مولڈنگ مشین میں کھلایا جاتا ہے، گرم کیا جاتا ہے اور مائع میں پگھلا دیا جاتا ہے۔
انجکشن مولڈنگ کا عمل
انجیکشن مولڈنگ کا عمل اس وقت شروع ہوتا ہے جب پگھلے ہوئے پلاسٹک کے مواد کو ہائی پریشر اور درجہ حرارت پر مولڈ گہا میں داخل کیا جاتا ہے۔ سڑنا دباؤ کے تحت بند رکھا جاتا ہے جب تک کہ پلاسٹک ٹھنڈا اور مضبوط نہ ہو جائے۔ اس وقت، سڑنا کھول دیا جاتا ہے، اور حصہ نکال دیا جاتا ہے.
کوالٹی کنٹرول
پرزے تیار ہوجانے کے بعد، وہ کوالٹی کنٹرول کے سخت عمل سے گزرتے ہیں تاکہ یہ یقینی بنایا جاسکے کہ وہ مطلوبہ تصریحات پر پورا اترتے ہیں۔ اس میں بصری معائنہ، پیمائش اور جانچ شامل ہو سکتی ہے تاکہ اس بات کی تصدیق کی جا سکے کہ ہر حصہ سائز، شکل اور معیار میں مطابقت رکھتا ہے۔
ہائی والیوم انجکشن مولڈنگ کے لیے تحفظات
بہت سے تحفظات ہیں جو مینوفیکچررز کو اعلی حجم انجیکشن مولڈنگ کا استعمال کرتے وقت ذہن میں رکھنا چاہئے، بشمول:
- مشین کا انتخاب: تیز رفتار انجکشن مولڈنگ مشینیں عام طور پر ہائی والیوم پروڈکشن رن کے لیے استعمال ہوتی ہیں، کیونکہ وہ جلد اور درست طریقے سے پرزے تیار کر سکتی ہیں۔
- سڑنا ڈیزائن: انجیکشن مولڈنگ کے عمل کی کامیابی کے لیے مولڈ ڈیزائن بہت اہم ہے، کیونکہ یہ درست ہونا چاہیے اور عمل کے اعلی دباؤ اور درجہ حرارت کو برداشت کرنے کے قابل ہونا چاہیے۔
- مادی انتخاب: پلاسٹک رال کا انتخاب تیار کیے جانے والے پرزوں کے معیار اور کارکردگی کو متاثر کر سکتا ہے، جس سے کام کے لیے مناسب مواد کا انتخاب ضروری ہو جاتا ہے۔
- لاگت: اگرچہ اعلی حجم کے انجیکشن مولڈنگ ایک لاگت سے موثر مینوفیکچرنگ عمل ہے، لیکن اب بھی مولڈ ڈیزائن، مواد کے انتخاب، اور پیداوار سے وابستہ اخراجات ہیں جن پر غور کرنا ضروری ہے۔
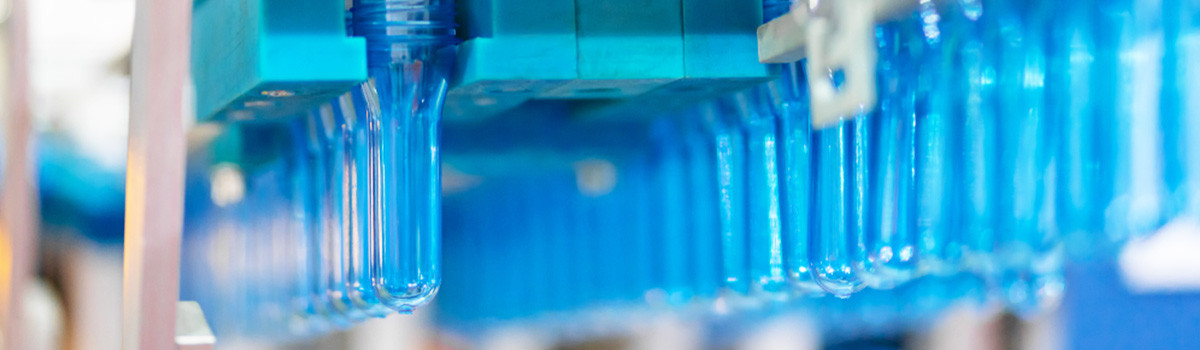
ہائی والیوم انجکشن مولڈنگ کے فوائد
ہائی والیوم انجیکشن مولڈنگ نے بے مثال رفتار اور کارکردگی کے ساتھ بڑی مقدار میں پلاسٹک کے ایک جیسے پرزوں کی تیاری کو قابل بنا کر مینوفیکچرنگ انڈسٹری میں انقلاب برپا کر دیا ہے۔ اس عمل نے اپنے بہت سے فوائد کی وجہ سے مختلف شعبوں میں مقبولیت حاصل کی ہے، جس سے یہ ان کمپنیوں کے لیے مینوفیکچرنگ کا طریقہ ہے جو لاگت میں کمی، فضلہ کو کم کرنے، اور پیداواری پیداوار میں اضافہ کرنا چاہتی ہیں۔
- لاگت سے موثر پیداوار: ہائی والیوم انجیکشن مولڈنگ انتہائی موثر اور خودکار ہے، جو اسے دیگر مینوفیکچرنگ کے عمل کے مقابلے میں لاگت سے موثر بناتی ہے۔ ایک بار جب مولڈ ڈیزائن اور تیار ہو جاتا ہے، تو پیداواری عمل مسلسل چل سکتا ہے، جس سے کم سے کم محنت یا مادی لاگت کے ساتھ ہزاروں یا لاکھوں ایک جیسے حصے تیار ہوتے ہیں۔
- اعلی پیداوار کی پیداوار: تیز رفتار انجیکشن مولڈنگ مشینوں کے ساتھ، مینوفیکچررز مختصر وقت میں بڑی مقدار میں عین مطابق پرزے تیار کر سکتے ہیں۔ اس کا مطلب یہ ہے کہ بدلتی ہوئی طلب کو پورا کرنے کے لیے پیداوار کی پیداوار تیزی سے بڑھ سکتی ہے یا کم ہو سکتی ہے۔
- مسلسل معیار: اعلی حجم کے انجیکشن مولڈنگ کی درستگی اور مستقل مزاجی اسے سخت رواداری اور پیچیدہ تفصیلات کے ساتھ حصوں کی تیاری کے لیے مثالی بناتی ہے۔ یہ عمل اعلیٰ درجے کی درستگی کی اجازت دیتا ہے، اس بات کو یقینی بناتا ہے کہ تیار کردہ ہر حصہ دوسروں سے مماثل ہے۔
- پارٹ ڈیزائن میں استرتا: ہائی والیوم انجیکشن مولڈنگ وسیع پیمانے پر ڈیزائن اور شکلوں کے ساتھ پرزے تیار کر سکتی ہے، بشمول پیچیدہ جیومیٹری والے۔ اس کا مطلب یہ ہے کہ مینوفیکچررز کے پاس ایسی خصوصیات ہو سکتی ہیں جو مخصوص گاہک کی ضروریات کو پورا کرتی ہیں اور آسانی سے ڈیزائن یا مصنوعات کی وضاحتوں میں ہونے والی تبدیلیوں کو ایڈجسٹ کر سکتی ہیں۔
- کم فضلہ: ہائی والیوم انجیکشن مولڈنگ میں اعلیٰ معیار کے سانچوں اور درست انجیکشن پیرامیٹرز کا استعمال مینوفیکچرنگ کے عمل کے دوران پیدا ہونے والے اسکریپ یا فضلہ کی مقدار کو کم کرتا ہے۔ اس کا مطلب یہ ہے کہ مینوفیکچررز کم سے کم مادی فضلہ کے ساتھ پرزے بنا سکتے ہیں، اخراجات کو کم کر سکتے ہیں اور ماحولیاتی اثرات۔
- پیداواری کارکردگی میں اضافہ: ہائی والیوم انجیکشن مولڈنگ انتہائی خودکار ہے، جس کا مطلب ہے کہ اس میں کم سے کم مشقت کی ضرورت ہوتی ہے اور تھوڑی مداخلت کے ساتھ مسلسل چل سکتا ہے۔ اس سے پیداواری کارکردگی میں اضافہ ہوتا ہے، کیونکہ مینوفیکچررز دستی کام یا نگرانی کی ضرورت کے بغیر جلد اور مؤثر طریقے سے پرزے تیار کر سکتے ہیں۔
ہائی والیوم انجکشن مولڈنگ کے نقصانات
ہائی والیوم انجیکشن مولڈنگ ایک بڑے پیمانے پر استعمال ہونے والا مینوفیکچرنگ عمل ہے جس میں پلاسٹک کے ایک جیسے پرزوں کی بڑی مقدار جلدی اور لاگت سے پیدا کی جاتی ہے۔ اگرچہ اس کے بہت سے فوائد ہیں، جیسے کہ لاگت کی تاثیر اور مستقل معیار، لیکن اس کے نقصانات بھی ہیں۔ یہ بلاگ پوسٹ ہائی والیوم انجیکشن مولڈنگ کے کچھ نقصانات کو تلاش کرے گی۔
- اعلیٰ ابتدائی سرمایہ کاری: ہائی والیوم انجیکشن مولڈنگ کے بنیادی نقصانات میں سے ایک مولڈ کو ڈیزائن اور تیار کرنے کے لیے درکار ابتدائی سرمایہ کاری میں اضافہ ہے۔ یہ قیمت خاص طور پر چھوٹے کاروباروں کے لیے یا ان لوگوں کے لیے اہم ہو سکتی ہے جنہیں مخصوص حصوں کے لیے حسب ضرورت سانچوں کی ضرورت ہوتی ہے۔
- لانگ لیڈ ٹائمز:ہائی والیوم انجیکشن مولڈنگ کے لیے سانچوں کی ڈیزائننگ اور مینوفیکچرنگ کے عمل میں کئی ہفتے یا مہینے بھی لگ سکتے ہیں، جس کے نتیجے میں لیڈ ٹائم طویل ہوتا ہے۔ یہ ان کمپنیوں کے لیے نقصان ہو سکتا ہے جنھیں جلد پرزے تیار کرنے یا طلب میں ہونے والی تبدیلیوں کا جواب دینے کی ضرورت ہوتی ہے۔
- محدود مواد کے انتخاب: اگرچہ ہائی حجم انجیکشن مولڈنگ کے لیے پلاسٹک کی رال کی بہت سی قسمیں دستیاب ہیں، لیکن انتخاب مخصوص ایپلی کیشن کے لحاظ سے محدود ہو سکتا ہے۔ کچھ پلاسٹک کی رالیں اپنی خصوصیات کی وجہ سے زیادہ حجم کی پیداوار کے لیے موزوں نہیں ہو سکتی ہیں، جو مادی انتخاب کو محدود کر سکتی ہیں۔
- محدود ڈیزائن لچک: ہائی والیوم انجیکشن مولڈنگ ایک درست عمل ہے جس میں سانچوں کو مخصوص خصوصیات کے ساتھ ڈیزائن کرنے کی ضرورت ہوتی ہے۔ اس کا مطلب ہے کہ اس عمل کے ذریعے تیار کردہ پرزوں کے ڈیزائن پر پابندیاں ہو سکتی ہیں، خاص طور پر اگر پوزیشن میں پیچیدہ جیومیٹریز یا دیگر مخصوص ڈیزائن کی ضروریات ہوں۔
- اعلی دیکھ بھال اور مرمت کے اخراجات: اعلیٰ حجم کے انجیکشن مولڈنگ میں استعمال ہونے والے سانچوں کو زیادہ سے زیادہ کارکردگی کو یقینی بنانے کے لیے باقاعدگی سے برقرار رکھا جانا چاہیے اور مرمت کی جانی چاہیے۔ دیکھ بھال اور مرمت کی لاگت اہم ہو سکتی ہے، خاص طور پر اگر سانچوں کو کثرت سے یا طویل مدت کے لیے استعمال کیا جائے۔
ان نقصانات کے باوجود، ہائی والیوم انجیکشن مولڈنگ ایک جیسی پلاسٹک کے پرزوں کی بڑی مقدار پیدا کرنے کے لیے ایک مقبول اور موثر مینوفیکچرنگ عمل ہے۔ اس عمل کے فوائد اور نقصانات پر احتیاط سے غور کرنے سے، مینوفیکچررز باخبر فیصلے کر سکتے ہیں کہ آیا یہ ان کی مخصوص پیداواری ضروریات کے لیے صحیح انتخاب ہے۔
ہائی والیوم انجیکشن مولڈنگ میں استعمال ہونے والا مواد
حتمی مصنوعات کے معیار اور کارکردگی کو یقینی بنانے کے لیے ہائی والیوم انجیکشن مولڈنگ کے لیے مناسب مواد کا انتخاب بہت ضروری ہے۔ یہ مضمون اعلیٰ حجم کے انجیکشن مولڈنگ میں استعمال ہونے والے مواد، ان کی خصوصیات اور ان کے استعمال پر روشنی ڈالتا ہے۔
پولپروپولین (پی پی)
پولی پروپیلین ایک عام طور پر استعمال ہونے والا تھرمو پلاسٹک پولیمر ہے جو اس کی کم قیمت، طاقت سے وزن کے تناسب، اور پائیداری کی وجہ سے ہائی والیوم انجیکشن مولڈنگ میں استعمال ہوتا ہے۔ پی پی آٹوموٹو، پیکیجنگ، اور اشیائے صرف کی پیداوار کے لیے ورسٹائل ہے۔ انجیکشن مولڈنگ میں پی پی کے استعمال کے فوائد میں اس کی ہلکی پھلکی نوعیت، کیمیائی مزاحمت، اور جہتی استحکام شامل ہیں، جو اسے درست حصوں کے لیے مثالی بناتے ہیں۔
اریریونلائٹریڈل بڈینین سٹیریئر (ABS)
ABS ایک تھرمو پلاسٹک پولیمر ہے جو اس کی سختی، اثر مزاحمت، اور اعلی چمک ختم کرنے کے لیے جانا جاتا ہے۔ یہ مواد عام طور پر کھلونوں، آٹوموٹو پارٹس اور الیکٹرانک ہاؤسنگ میں استعمال ہوتا ہے۔ ABS کی اثر مزاحمت اسے ان تفصیلات کے لیے موزوں بناتی ہے جو اثر یا صدمے کا شکار ہوتی ہیں۔ اس پر عملدرآمد کرنا بھی آسان ہے اور اس کی سطح بہترین ہے، جس سے یہ اعلیٰ حجم کی پیداوار کے لیے مثالی ہے۔
پولی کاربونیٹ (پی سی)
پولی کاربونیٹ ایک تھرمو پلاسٹک پولیمر ہے جو انتہائی اثر مزاحم، نظری طور پر صاف اور گرمی سے مزاحم ہے۔ یہ آٹوموٹو، ایرو اسپیس اور الیکٹرانکس کی صنعتوں کے لیے ایک مقبول مواد ہے۔ PC کے فوائد میں بہترین اثر مزاحمت، نظری وضاحت، اور گرمی کی مزاحمت شامل ہے، جو اسے اعلی درجہ حرارت کی ایپلی کیشنز، لینسز اور اسکرینوں کے لیے مثالی بناتی ہے۔
پولی تھین (PE)
Polyethylene ایک تھرمو پلاسٹک پولیمر ہے جو لچکدار، سخت اور کیمیائی مزاحم ہے۔ یہ عام طور پر پیکیجنگ مواد، پلاسٹک کے تھیلے، اور زرعی فلمیں بنانے کے لیے استعمال ہوتا ہے۔ PE کی کیمیائی مزاحمت، لچک، اور ہلکی پھلکی نوعیت اسے کیمیکل پروسیسنگ کے آلات، کیمیکلز کے لیے پیکیجنگ، اور ایسے ایپلی کیشنز کے لیے مثالی بناتی ہے جن کے پرزوں کو موڑنے یا موڑنے کی ضرورت ہوتی ہے۔
پولی تھیلین ٹیرفتھیلیٹ (پیئٹی)
پی ای ٹی ایک تھرمو پلاسٹک پولیمر ہے جس میں اعلی طاقت سے وزن کا تناسب، وضاحت، اور رکاوٹ کی خصوصیات ہیں۔ یہ مشروبات کی بوتلیں، کھانے کے کنٹینرز، اور پیکیجنگ مواد تیار کرتا ہے۔ PET کے فوائد میں اس کی طاقت سے وزن میں توازن، شفافیت، اور رکاوٹ کی خصوصیات شامل ہیں جو اسے ان ایپلی کیشنز کے لیے مثالی بناتی ہیں جہاں طاقت ضروری ہو، جیسے مشروبات کی بوتلیں اور پیکیجنگ جہاں مواد کو نمی اور آکسیجن سے محفوظ رکھنا ضروری ہے۔
پولسٹریئر (پی ایس)
پولیسٹیرین ایک تھرمو پلاسٹک پولیمر ہے جو ہلکا پھلکا، لاگت سے موثر اور اچھی موصلیت کی خصوصیات رکھتا ہے۔ PS عام طور پر ڈسپوزایبل کپ، پیکیجنگ مواد، اور موصلیت پیدا کرنے کے لیے استعمال ہوتا ہے، اور اس کے فوائد میں کم قیمت، ہلکا پھلکا فطرت، اور اچھی موصلیت کی خصوصیات شامل ہیں۔
اعلی حجم کی پیداوار کے لیے استعمال ہونے والی انجکشن مولڈنگ مشینوں کی اقسام
اس عمل میں پگھلے ہوئے پلاسٹک کے مواد کو مولڈ گہا میں داخل کرنا شامل ہے، جہاں یہ مضبوط ہو کر سڑنا کی شکل اختیار کر لیتا ہے۔ انجکشن مولڈنگ مشینیں مختلف اقسام میں آتی ہیں، اور ہر ایک مخصوص قسم کی پیداوار کے لیے موزوں ہے۔ اعلی حجم کی پیداوار کے لیے استعمال ہونے والی انجیکشن مولڈنگ مشینوں کی اہم اقسام یہ ہیں:
- ہائیڈرولک انجکشن مولڈنگ مشینیں: یہ مشینیں مولڈ کو منتقل کرنے اور پگھلے ہوئے پلاسٹک کو گہا میں داخل کرنے کے لیے ہائیڈرولک پریشر کا استعمال کرتی ہیں۔ وہ اپنی اعلی پیداواری پیداوار کے لیے جانے جاتے ہیں لیکن ان کا سائیکل کا وقت بھی سست ہے، جس سے ان کے استعمال کو زیادہ درستگی اور تیز رفتار ایپلی کیشنز کے لیے محدود کیا جاتا ہے۔
- الیکٹرک انجکشن مولڈنگ مشینیں: یہ مشینیں انجیکشن یونٹ اور مولڈ کو چلانے کے لیے الیکٹرک سروو موٹرز کا استعمال کرتی ہیں۔ وہ اعلیٰ درستگی اور رفتار پیش کرتے ہیں، جو انہیں طبی آلات اور الیکٹرانکس جیسی ہائی ٹیک صنعتوں کے لیے مثالی بناتے ہیں۔
- ہائبرڈ انجکشن مولڈنگ مشینیں: یہ مشینیں دونوں جہانوں کی بہترین چیزوں کو یکجا کرتی ہیں۔ وہ انجیکشن یونٹ اور مولڈ کو چلانے کے لیے ہائیڈرولک اور برقی نظام استعمال کرتے ہیں۔ ہائبرڈ انجن موثر اور تیز ہیں، اعلی پیداواری پیداوار کے ساتھ، انہیں اعلی حجم کی پیداوار کے لیے مثالی بناتے ہیں۔
- دو شاٹ انجکشن مولڈنگ مشینیں: یہ مشینیں پیچیدہ پرزے تیار کرتی ہیں جن کے لیے دو مختلف مواد یا رنگ درکار ہوتے ہیں۔ ڈیوائس میں دو انجیکشن یونٹس ہیں جو حتمی ٹکڑا بنانے کے لیے مل کر کام کرتے ہیں۔ دو شاٹ انجیکشن مولڈنگ مشینیں متعدد اجزاء کے ساتھ اعلی معیار کی مصنوعات تیار کرنے کے لئے مثالی ہیں۔
- ملٹی میٹریل انجکشن مولڈنگ مشینیں:یہ مشینیں مختلف مواد سے بنے پرزے تیار کرتی ہیں۔ ان کے پاس متعدد انجیکشن یونٹ ہیں جو انہیں بیک وقت دیگر مواد استعمال کرنے کی اجازت دیتے ہیں۔ ملٹی میٹریل انجیکشن مولڈنگ مشینیں ایسے ٹکڑے بنانے کے لیے مثالی ہیں جن کے لیے مختلف خصوصیات کی ضرورت ہوتی ہے، جیسے کہ طاقت، استحکام اور لچک۔
- مائع انجکشن مولڈنگ مشینیں: یہ مشینیں مائع سلیکون ربڑ (LSR) سے بنے حصے تیار کرنے کے لیے استعمال ہوتی ہیں۔ مشین LSR کو مولڈ گہا میں داخل کرتی ہے، جہاں یہ مضبوط ہو کر مولڈ کی شکل اختیار کر لیتی ہے۔ مائع انجیکشن مولڈنگ مشینیں ایسے پرزے تیار کرنے کے لیے مثالی ہیں جن کے لیے اعلیٰ درستگی اور پائیداری کی ضرورت ہوتی ہے، جیسے کہ طبی آلات اور آٹوموٹو پارٹس۔
اعلی حجم کی پیداوار کے لیے انجکشن مولڈنگ کے عمل کے اقدامات
اس عمل میں پگھلے ہوئے پلاسٹک کے مواد کو مولڈ گہا میں داخل کرنا شامل ہے، جہاں یہ مضبوط ہو کر سڑنا کی شکل اختیار کر لیتا ہے۔ اعلی حجم کی پیداوار کے لیے انجکشن مولڈنگ کے عمل میں شامل اقدامات یہ ہیں:
- مادی انتخاب: انجکشن مولڈنگ کے عمل میں پہلا قدم حصہ تیار کرنے کے لیے موزوں مواد کا انتخاب کرنا ہے۔ منتخب کردہ مواد میں مطلوبہ خصوصیات، جیسے کہ طاقت، استحکام، اور لچک ہونی چاہیے، اور انجیکشن مولڈنگ مشین کے ساتھ ہم آہنگ ہونا چاہیے۔
- سڑنا ڈیزائن: اگلا مرحلہ مواد کو منتخب کرنے کے بعد مولڈ کو ڈیزائن کرنا ہے۔ مولڈ کو تیار ہونے والے حصے کی درست وضاحتوں کے مطابق تیار کیا جانا چاہیے، بشمول اس کی شکل، سائز اور خصوصیات۔ مولڈ کو انجیکشن مولڈنگ مشین کی قسم اور پیداواری عمل کی مخصوص ضروریات کو بھی مدنظر رکھنا چاہئے۔
- مشین سیٹ اپ: سڑنا ڈیزائن کرنے کے بعد، انجکشن مولڈنگ مشین قائم کی جاتی ہے. اس میں مولڈ کو آلے کے ساتھ جوڑنا، مناسب درجہ حرارت اور دباؤ کی ترتیبات کو ترتیب دینا، اور اس بات کی تصدیق کرنا کہ سب کچھ صحیح طریقے سے کام کرتا ہے۔
- انجکشن: انجیکشن کا عمل اس وقت شروع ہوتا ہے جب پگھلے ہوئے پلاسٹک کے مواد کو مولڈ گہا میں داخل کیا جاتا ہے۔ یہ ایک ہائی پریشر انجیکشن یونٹ کا استعمال کرتے ہوئے کیا جاتا ہے جو مواد کو ایک مخصوص شرح اور دباؤ پر سانچے میں ڈالتا ہے۔
- کولنگ:پگھلے ہوئے پلاسٹک کے مواد کو مولڈ گہا میں داخل کرنے کے بعد، اسے ٹھنڈا اور ٹھوس ہونے دیا جانا چاہیے۔ یہ مواد کے درجہ حرارت کو کم کرنے کے لیے مولڈ گہا کے ذریعے ٹھنڈی ہوا یا پانی کو گردش کر کے کیا جاتا ہے۔
- اخراج: ایک بار جب پلاسٹک کا مواد ٹھنڈا اور مضبوط ہوجاتا ہے، تو سڑنا کھول دیا جاتا ہے، اور حصہ نکال دیا جاتا ہے. اخراج کے عمل میں مکینیکل یا ہائیڈرولک نظام کا استعمال شامل ہے تاکہ اس حصے کو سڑنا گہا سے باہر دھکیل سکے۔
- کوالٹی کنٹرول: حصہ نکالنے کے بعد، یہ کوالٹی کنٹرول چیک سے گزرتا ہے تاکہ یہ یقینی بنایا جا سکے کہ یہ مطلوبہ تصریحات پر پورا اترتا ہے۔ اس میں بصری معائنہ، پیمائش اور جانچ شامل ہو سکتی ہے تاکہ اس بات کی تصدیق کی جا سکے کہ یہ حصہ اعلیٰ معیار اور نقائص سے پاک ہے۔
ہائی والیوم انجکشن مولڈنگ کے لیے ڈیزائن کے تحفظات
ہائی والیوم انجیکشن مولڈنگ کے لیے پلاسٹک کے حصے کو ڈیزائن کرنے کے لیے کئی عوامل پر غور کرنے کی ضرورت ہوتی ہے تاکہ یہ یقینی بنایا جا سکے کہ اس ٹکڑے کو موثر اور لاگت سے بنایا جا سکتا ہے۔ اعلی حجم انجیکشن مولڈنگ کے لئے یہاں کچھ ڈیزائن تحفظات ہیں:
- دیوار کی موٹائی: پلاسٹک کے حصے کی دیوار کی موٹائی انجیکشن مولڈنگ کے لیے ایک ضروری خیال ہے۔ دیواروں کی موٹائی یکساں ہونی چاہیے تاکہ ٹکڑے کی ناہموار ٹھنڈک اور وارپنگ کو روکا جا سکے۔ پتلی دیواریں اعلیٰ حجم کی پیداوار کے لیے مثالی ہیں کیونکہ وہ مواد کے استعمال اور سائیکل کے وقت کو کم کرتی ہیں، جب کہ موٹی دیواریں ان حصوں کے لیے موزوں ہیں جنہیں اضافی طاقت کی ضرورت ہوتی ہے۔
- حصہ سائز اور شکل: حصے کا سائز اور شکل انجیکشن مولڈنگ کے عمل کو متاثر کرے گی۔ ایسے عوامل جو بہت بڑے یا پیچیدہ ہوتے ہیں ان کے لیے سائیکل کے طویل وقت یا خصوصی آلات کی ضرورت ہوتی ہے، جس سے پیداواری لاگت میں اضافہ ہوتا ہے۔ سادہ، ہندسی شکلیں اعلی حجم کی پیداوار کے لیے بہترین ہیں۔
- ڈرافٹ زاویہ: ڈرافٹ اینگل مولڈ گہا کی دیوار کا زاویہ ہے جو اس حصے کو آسانی سے نکالنے کی اجازت دیتا ہے۔ حصہ کے ڈیزائن میں ڈرافٹ اینگلز کو شامل کرنا اس بات کو یقینی بنانے کے لیے ضروری ہے کہ ٹکڑا جلد سے مولڈ سے باہر نکل سکے۔ بغیر مسودہ کے زاویوں کی مقدار مہنگی پیداواری مسائل جیسے کریکنگ یا ڈیفارمیشن کا باعث بن سکتی ہے۔
- گیٹ کا مقام اور سائز:گیٹ کا محل وقوع اور سائز، جہاں پگھلا ہوا پلاسٹک کا مواد مولڈ گہا میں داخل ہوتا ہے، انجیکشن مولڈنگ کے لیے ڈیزائن کا ایک اہم خیال ہے۔ گیٹ کا مقام ایک ایسے علاقے میں رکھا جانا چاہیے جو اس حصے کی ساختی سالمیت کو متاثر نہ کرے۔ گیٹ کا سائز اتنا بڑا ہونا چاہیے کہ مواد کو صحیح طریقے سے بہنے دے لیکن اتنا بڑا نہیں کہ اس سے پوزیشن میں نقائص پیدا ہوں۔
- مادی انتخاب: مواد کا انتخاب اس بات کو یقینی بنانے کے لیے ضروری ہے کہ اس حصے کو موثر اور کم لاگت سے تیار کیا جا سکے۔ مواد کا انتخاب ٹکڑے کی مخصوص ضروریات پر مبنی ہونا چاہیے، بشمول طاقت، استحکام، اور لچک۔
- سطح ختم: انجکشن مولڈنگ کے لیے حصے کی سطح کی تکمیل ایک ضروری خیال ہے۔ مقدار کی سطح ہموار اور نقائص سے پاک ہونی چاہیے، جیسے وارپنگ یا سنک کے نشانات۔ گیٹ کی مناسب جگہ کا تعین، مولڈ ڈیزائن، اور مواد کا انتخاب ہموار سطح کی تکمیل کو حاصل کر سکتا ہے۔
- رواداری: رواداری کسی حصے کے طول و عرض میں قابل اجازت تغیر کی ڈگری ہے۔ پارٹ ڈیزائن کے مرحلے کے دوران رواداری پر غور کیا جانا چاہیے تاکہ یہ یقینی بنایا جا سکے کہ ٹکڑا درست اور درست طریقے سے تیار کیا جا سکتا ہے۔
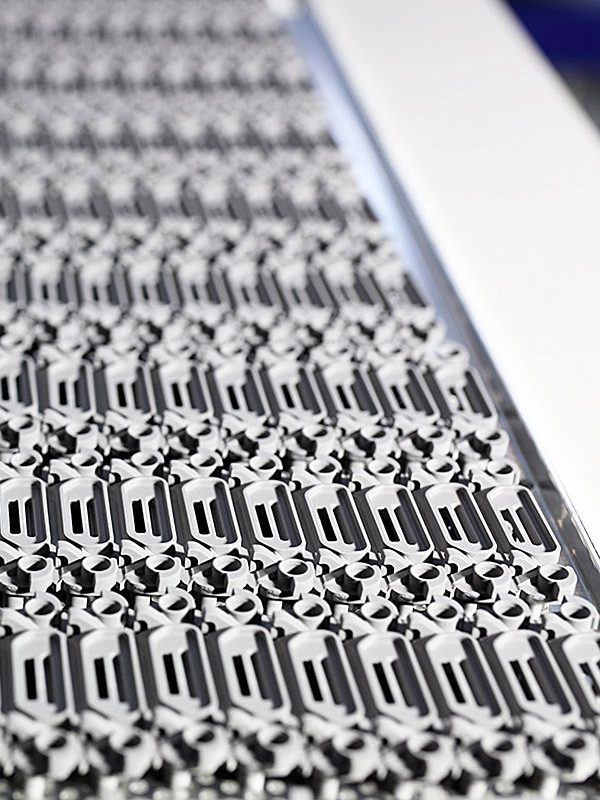
ہائی والیوم انجکشن مولڈنگ میں کوالٹی کنٹرول کے اقدامات
اعلی حجم کے انجیکشن مولڈنگ کے لیے کوالٹی کنٹرول ضروری ہے، کیونکہ یہ اس بات کو یقینی بناتا ہے کہ تیار کردہ پرزے مطلوبہ تصریحات پر پورا اترتے ہیں اور نقائص سے پاک ہیں۔ ہائی والیوم انجیکشن مولڈنگ میں استعمال ہونے والے کوالٹی کنٹرول کے کچھ اقدامات یہ ہیں:
- پیداوار کے عمل کے دوران معائنہ: پیداوار کے عمل کے دوران باقاعدگی سے جائزہ لینے سے نقائص کی جلد شناخت کرنے اور انہیں مزید اہم مسائل بننے سے روکنے میں مدد مل سکتی ہے۔ اس میں بصری معائنہ، پیمائش اور جانچ شامل ہو سکتی ہے تاکہ اس بات کی تصدیق کی جا سکے کہ حصہ صحیح طریقے سے تیار کیا جا رہا ہے۔
- شماریاتی عمل کا کنٹرول (SPC): SPC ایک شماریاتی طریقہ ہے جو پیداواری عمل کی نگرانی اور کنٹرول کے لیے استعمال ہوتا ہے۔ اس میں پیداواری عمل سے متعلق ڈیٹا اکٹھا کرنا اور رجحانات اور نمونوں کی نشاندہی کرنے کے لیے اس کا تجزیہ کرنا شامل ہے جو اس عمل کے ساتھ مسائل کی نشاندہی کر سکتے ہیں۔ SPC مسائل کا پتہ لگانے اور درست کرنے میں مدد کر سکتی ہے اس سے پہلے کہ ان کے نتیجے میں پرزے خراب ہوں۔
- خودکار آلات کا استعمال: خودکار آلات، جیسے روبوٹ اور سینسر، پیداواری عمل کی مستقل مزاجی اور درستگی کو بہتر بنانے میں مدد کر سکتے ہیں۔ مکینیکل آلات انسانی غلطی کے خطرے کو بھی کم کر سکتے ہیں جس کے نتیجے میں کم نقائص ہوتے ہیں۔
- سڑنا کی بحالی:مولڈ کی مناسب دیکھ بھال اس بات کو یقینی بنانے کے لیے ضروری ہے کہ تیار کردہ پرزے اعلیٰ معیار کے ہوں۔ اس میں مولڈ کو باقاعدگی سے صاف کرنا اور اس بات کو یقینی بنانے کے لیے ضروری مرمت یا تبدیلی کرنا شامل ہے کہ سانچہ صحیح طریقے سے کام کر رہا ہے۔
- پیداوار کے بعد معائنہ: پرزے تیار کرنے کے بعد، ان کا حتمی معائنہ کیا جاتا ہے تاکہ یہ یقینی بنایا جا سکے کہ وہ مطلوبہ تصریحات کو پورا کرتے ہیں۔ اس میں بصری معائنہ، پیمائش اور جانچ شامل ہو سکتی ہے تاکہ اس بات کی تصدیق کی جا سکے کہ پرزے نقائص سے پاک ہیں۔
- تربیت اور تعلیم: ملازمین کی مناسب تربیت اور تعلیم پیداواری عمل کے معیار کو بہتر بنا سکتی ہے۔ ملازمین کو مناسب پیداواری تکنیکوں اور کوالٹی کنٹرول کے اقدامات کے بارے میں تربیت دی جانی چاہیے تاکہ یہ یقینی بنایا جا سکے کہ وہ مسائل پیدا ہوتے ہی ان کی شناخت اور ان کو درست کر سکتے ہیں۔
- مسلسل بہتری: ہائی والیوم انجیکشن مولڈنگ میں کوالٹی کنٹرول کے لیے مسلسل بہتری ضروری ہے۔ پیداواری عمل کا باقاعدگی سے جائزہ لے کر اور بہتری کے لیے علاقوں کی نشاندہی کر کے، مینوفیکچررز نقائص کو کم کر سکتے ہیں اور تیار کردہ پرزوں کے معیار کو بہتر بنا سکتے ہیں۔
ہائی والیوم انجکشن مولڈنگ کی لاگت کا تجزیہ
بڑی مقدار میں پلاسٹک کے پرزے تیار کرنے کے لیے ہائی والیوم انجیکشن مولڈنگ ایک سرمایہ کاری مؤثر مینوفیکچرنگ عمل ہے۔ تاہم، انجکشن مولڈنگ کے ذریعے پرزوں کی پیداوار کی لاگت کئی عوامل کی بنیاد پر مختلف ہو سکتی ہے۔ اعلی حجم انجیکشن مولڈنگ کے لئے یہاں کچھ لاگت کے تجزیہ کے تحفظات ہیں:
- مواد کی قیمت: خام مال کی قیمت سب سے اہم عوامل میں سے ایک ہے جو انجیکشن مولڈنگ کی قیمت کو متاثر کرتی ہے۔ استعمال شدہ مواد کی قسم اور معیار قیمت کو متاثر کرے گا، کچھ مواد دوسروں سے زیادہ مہنگا ہونے کے ساتھ۔ مینوفیکچررز کو حصہ کی مخصوص ضروریات کی بنیاد پر مناسب مواد کا انتخاب کرنا چاہیے۔
- ٹولنگ لاگت: ٹولنگ کی لاگت، بشمول مولڈ اور انجیکشن مولڈنگ کے لیے درکار دیگر سامان، پیداواری لاگت کو متاثر کرنے والا ایک اور اہم عنصر ہے۔ ٹولنگ کی لاگت اس حصے کی پیچیدگی، سڑنا کے سائز، اور سانچے میں موجود گہاوں کی تعداد کے لحاظ سے مختلف ہو سکتی ہے۔
- لیبر کی قیمت: انجکشن مولڈنگ میں مزدوری کی لاگت ایک اہم عنصر ہے، کیونکہ اس عمل میں مشینوں کو چلانے اور پیداواری عمل کی نگرانی کے لیے ہنر مند کارکنوں کی ضرورت ہوتی ہے۔ مزدوروں کے محل وقوع اور تجربے کے لحاظ سے مزدوری کے اخراجات مختلف ہو سکتے ہیں۔
- اوور ہیڈ لاگت: اوور ہیڈ اخراجات، بشمول یوٹیلیٹیز، کرایہ، اور دیگر اخراجات، انجیکشن مولڈنگ لاگت کو بھی متاثر کر سکتے ہیں۔ یہ اخراجات مینوفیکچرنگ سہولت کے مقام اور آپریشن کے سائز کے لحاظ سے مختلف ہو سکتے ہیں۔
- پیداوار کا حجم: پیداوار کا حجم ایک لازمی عنصر ہے جو انجیکشن مولڈنگ لاگت کو متاثر کرتا ہے۔ پیمانہ کی معیشتوں کی وجہ سے زیادہ پیداواری حجم فی حصہ کم لاگت کا باعث بن سکتا ہے۔
- حصہ ڈیزائن: ڈیزائن انجیکشن مولڈنگ لاگت کو بھی متاثر کرسکتا ہے۔ وہ عوامل جو پیچیدہ ہیں یا خصوصی آلات کی ضرورت ہوتی ہے وہ پیداواری لاگت کو بڑھا سکتے ہیں۔
- کوالٹی کنٹرول: کوالٹی کنٹرول کے اقدامات کی لاگت، بشمول معائنہ اور جانچ، پیداوار کی لاگت کو بھی متاثر کر سکتی ہے۔ یہ اقدامات اس بات کو یقینی بنانے کے لیے ضروری ہیں کہ تیار کردہ پرزے مطلوبہ تصریحات کو پورا کرتے ہیں اور عیب سے پاک ہیں۔
وہ صنعتیں جو ہائی والیوم انجیکشن مولڈنگ کا استعمال کرتی ہیں۔
ہائی والیوم انجیکشن مولڈنگ ایک وسیع پیمانے پر استعمال ہونے والا مینوفیکچرنگ عمل ہے جو بڑی مقدار میں پلاسٹک کے پرزے جلدی اور موثر طریقے سے تیار کرنے کی صلاحیت رکھتا ہے۔ یہاں کچھ صنعتیں ہیں جو زیادہ مقدار میں انجیکشن مولڈنگ پر بھروسہ کرتی ہیں:
- گاڑیوں کی صنعت: آٹوموٹو انڈسٹری ہائی والیوم انجیکشن مولڈنگ کے سب سے اہم صارفین میں سے ایک ہے۔ یہ عمل پلاسٹک کے مختلف اجزاء جیسے ڈیش بورڈ کے پرزے، دروازے کے ہینڈلز، اور اندرونی تراش کے ٹکڑے تیار کرتا ہے۔
- کنزیومر گڈز انڈسٹری: ہائی والیوم انجیکشن مولڈنگ مختلف صارفی سامان تیار کرتی ہے، بشمول گھریلو آلات، کھلونے، اور الیکٹرانکس۔ اس عمل کو ترجیح دی جاتی ہے کیونکہ یہ مینوفیکچررز کو بڑے حصے سستے بنانے کی اجازت دیتا ہے۔
- طبی صنعت: طبی صنعت کو مختلف طبی آلات، جیسے کہ تشخیصی آلات، جراحی کے آلات، اور ڈسپوزایبل طبی سامان کے لیے اعلیٰ معیار کے اور درست پلاسٹک کے اجزاء کی ضرورت ہوتی ہے۔ ہائی والیوم انجیکشن مولڈنگ کو ترجیح دی جاتی ہے کیونکہ یہ ان حصوں کو درست اور مستقل طور پر تیار کر سکتا ہے۔.
- صنعت:پیکیجنگ انڈسٹری مختلف قسم کے پلاسٹک کے کنٹینرز، ڈھکنوں اور بندشوں کو تیار کرنے کے لیے ہائی والیوم انجیکشن مولڈنگ پر بہت زیادہ انحصار کرتی ہے۔ یہ عمل لاگت سے موثر ہے اور مینوفیکچررز کو تیزی سے مختلف شکلیں اور سائز بنانے کی اجازت دیتا ہے۔
- ایرو اسپیس انڈسٹری: ایرو اسپیس انڈسٹری کو اعلی کارکردگی والے پلاسٹک کے اجزاء کی ضرورت ہوتی ہے جو انتہائی حالات جیسے کہ اعلی درجہ حرارت اور دباؤ کا مقابلہ کر سکیں۔ ہائی والیوم انجیکشن مولڈنگ ان اجزاء کو تیار کرتی ہے، بشمول اندرونی اور بیرونی طیارے کے پرزے، ایویونکس اور الیکٹرانکس۔
- تعمیراتی صنعت: تعمیراتی صنعت پلاسٹک کے مختلف اجزاء جن میں کھڑکی کے فریم، پائپنگ اور موصلیت شامل ہیں، بنانے کے لیے ہائی والیوم انجیکشن مولڈنگ کا استعمال کرتی ہے۔ اس عمل کو ترجیح دی جاتی ہے کیونکہ یہ ایسے پرزوں کی بڑی مقدار کی پیداوار کی اجازت دیتا ہے جو پائیدار اور ماحولیاتی عوامل کے خلاف مزاحم ہوں۔
- کھیل اور تفریحی صنعت: ہائی والیوم انجیکشن مولڈنگ کھیلوں اور تفریحی صنعت کے لیے پلاسٹک کے مختلف اجزاء تیار کرتی ہے، بشمول ہیلمٹ، حفاظتی پوشاک، اور کھلونے۔ اس عمل کو ترجیح دی جاتی ہے کیونکہ یہ ہلکے وزن، پائیدار، اور جمالیاتی لحاظ سے خوش کن حصوں کو بنانے کی اجازت دیتا ہے۔
میڈیکل انڈسٹری کے لیے ہائی والیوم انجکشن مولڈنگ کے فوائد
طبی صنعت دنیا کی سب سے بڑی اور تیزی سے ترقی کرنے والی صنعتوں میں سے ایک ہے۔ ٹیکنالوجی میں ترقی اور طبی آلات اور آلات کی بڑھتی ہوئی مانگ کے ساتھ، موثر مینوفیکچرنگ کے عمل کی ضرورت ہے جو اعلیٰ معیار کے اجزاء تیار کر سکیں۔ ہائی والیوم انجیکشن مولڈنگ ایک ایسا عمل ہے جو طبی صنعت کے لیے کئی فوائد پیش کرتا ہے۔ آئیے میڈیکل انڈسٹری میں ہائی والیوم انجیکشن مولڈنگ کے کچھ فوائد کا جائزہ لیتے ہیں۔
- مؤثر لاگت: ہائی والیوم انجیکشن مولڈنگ ایک لاگت سے موثر مینوفیکچرنگ عمل ہے جو فی یونٹ کم قیمت پر بڑی مقدار میں پلاسٹک کے اجزاء تیار کرتا ہے۔
- مستقل مزاجی: ہائی والیوم انجیکشن مولڈنگ اعلی viscosity اور درستگی کے ساتھ پرزے تیار کرنے کی اجازت دیتی ہے، اس بات کو یقینی بناتی ہے کہ ہر ٹکڑا مطلوبہ تصریحات پر پورا اترتا ہے۔
- حسب ضرورت: یہ عمل رنگ، ساخت، اور مواد سمیت مخصوص تقاضوں کے مطابق خصوصیات کی تخصیص کی اجازت دیتا ہے۔
- رفتار: ہائی والیوم انجیکشن مولڈنگ پوزیشنوں کی فوری پیداوار، لیڈ ٹائم کو کم کرنے اور کارکردگی بڑھانے کی اجازت دیتی ہے۔
- : کوالٹی ہائی والیوم انجیکشن مولڈنگ کا عمل اعلیٰ معیار کے پرزے تیار کرتا ہے جو طبی آلات کے لیے درکار سخت معیارات پر پورا اترتے ہیں۔
- بانجھ پن: یہ عمل جراثیم سے پاک ماحول میں کیا جاتا ہے، اس بات کو یقینی بناتے ہوئے کہ تیار کردہ حصے آلودگی سے پاک اور طبی استعمال کے لیے محفوظ ہوں۔
- استحکام: ہائی والیوم انجیکشن مولڈنگ کا استعمال کرتے ہوئے تیار کردہ پرزے پائیدار ہوتے ہیں اور سخت ماحول کو برداشت کر سکتے ہیں، اس بات کو یقینی بناتے ہوئے کہ وہ زیادہ دیر تک چل سکیں اور متبادل کی ضرورت کو کم کریں۔ طبی صنعت میں پائیداری بہت اہم ہے، جہاں آلات اور آلات کو مسلسل استعمال اور کیمیکلز اور دیگر سخت عناصر کے ممکنہ نمائش کو برداشت کرنا چاہیے۔
- پیچیدگی: ہائی والیوم انجیکشن مولڈنگ کا عمل پیچیدہ ڈیزائنوں کے ساتھ پیچیدہ حصوں کی تیاری کی اجازت دیتا ہے، اس بات کو یقینی بناتا ہے کہ طبی آلات کو جدید ادویات کی درست ضروریات کو پورا کرنے کے لیے بنایا جا سکے۔ یہ عمل طبی آلات اور آلات کے لیے ضروری منفرد خصوصیات اور ڈیزائن کے ساتھ پیچیدہ اجزاء تیار کرنے کے لیے مثالی ہے۔
- استراحت: ہائی والیوم انجیکشن مولڈنگ مختلف شکلوں اور سائزوں کے ساتھ مختلف حصوں کو تیار کر سکتی ہے، جو اسے مختلف طبی ایپلی کیشنز میں اجزاء بنانے کے لیے مثالی بناتی ہے۔
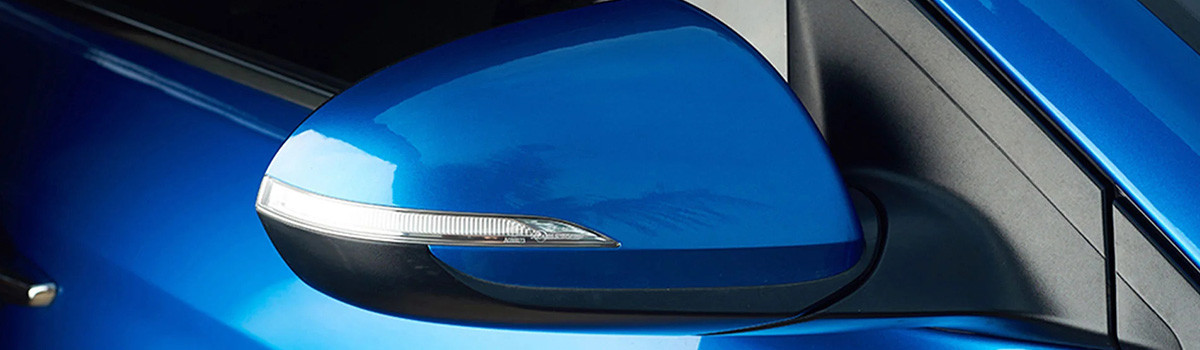
آٹوموٹو انڈسٹری کے لیے ہائی والیوم انجکشن مولڈنگ
انجکشن مولڈنگ ایک مینوفیکچرنگ عمل ہے جس میں پلاسٹک کے مختلف اجزاء بنانے کے لیے پگھلے ہوئے پلاسٹک کو مولڈ گہا میں انجیکشن لگانا شامل ہے۔ اس عمل کو آٹوموٹو انڈسٹری میں وسیع پیمانے پر استعمال کیا جاتا ہے تاکہ دروازے کے پینلز، ڈیش بورڈز، انسٹرومنٹ پینلز، اندرونی تراشوں اور جسم کے بیرونی حصوں جیسے متعدد حصوں کو تیار کیا جا سکے۔ ہائی والیوم انجیکشن مولڈنگ ایک خصوصی تکنیک ہے جو مینوفیکچررز کو ایک جیسے حصوں کی بڑی مقدار کو تیزی سے تیار کرنے کے قابل بناتی ہے۔
ہائی والیوم انجیکشن مولڈنگ ایک انتہائی موثر مینوفیکچرنگ تکنیک ہے جو آٹوموٹیو انڈسٹری کے لیے کئی فوائد پیش کرتی ہے۔ ان میں سے کچھ فوائد میں شامل ہیں:
- پیداواری لاگت میں کمی - یہ عمل انتہائی خودکار ہے، جو مزدوری کے اخراجات کو کم کرتا ہے، اور سانچوں سے مینوفیکچررز کو کم قیمت پر ایک جیسے پرزے تیار کرنے کی اجازت ملتی ہے۔
- بہتر حصے کی مستقل مزاجی - ہائی والیوم انجیکشن مولڈنگ ایک جیسے حصوں کی تیاری، تغیر کو کم کرنے اور مینوفیکچرنگ کے عمل میں ساخت کو بہتر بنانے کی اجازت دیتی ہے۔
- تیز تر پیداوار کے اوقات - یہ عمل انتہائی خودکار ہے، جو مینوفیکچررز کو اس قابل بناتا ہے کہ وہ تیزی سے پرزے تیار کر سکیں، جس سے لیڈ ٹائم کم ہو جاتا ہے۔
- اعلی معیار کے حصے - سانچوں کا استعمال اس بات کو یقینی بناتا ہے کہ تیار کردہ پرزے اعلیٰ معیار کے ہوں، جس میں کم سے کم نقائص اور تضادات ہوں۔
- ڈیزائن لچک -انجکشن مولڈنگ تیزی سے پیچیدہ شکلیں اور ڈیزائن تیار کرنے کی اجازت دیتی ہے، جس سے ڈیزائنرز کو ان کے منصوبوں میں زیادہ لچک ملتی ہے۔
انجیکشن مولڈنگ آٹوموٹیو انڈسٹری کے لیے ایک مثالی مینوفیکچرنگ تکنیک ہے، کیونکہ یہ بہت سے فوائد پیش کرتی ہے جو کارکردگی کو بہتر کرتی ہے، لاگت کو کم کرتی ہے، اور جزوی معیار کو بہتر بناتی ہے۔ ہائی والیوم انجیکشن مولڈنگ، خاص طور پر، ایک خصوصی تکنیک ہے جو مینوفیکچررز کو اس قابل بناتی ہے کہ وہ بڑی مقدار میں ایک جیسے پرزے جلدی اور مؤثر طریقے سے تیار کر سکیں۔
آٹوموٹو انڈسٹری کار اور گاڑی کے مختلف اجزاء تیار کرنے کے لیے انجیکشن مولڈنگ پر بہت زیادہ انحصار کرتی ہے۔ جسم کے بیرونی حصوں سے لے کر اندرونی تراشوں اور ڈیش بورڈز تک، انجیکشن مولڈنگ آٹوموٹیو انڈسٹری میں مینوفیکچرنگ کا ایک ضروری عمل بن گیا ہے۔ اعلی حجم کے انجیکشن مولڈنگ کے ساتھ، مینوفیکچررز بہتر مستقل مزاجی اور معیار کے ساتھ کم قیمت پر ایک جیسے حصوں کی بڑی مقدار تیار کر سکتے ہیں۔
کنزیومر گڈز انڈسٹری کے لیے ہائی والیوم انجکشن مولڈنگ
ہائی والیوم انجیکشن مولڈنگ ایک مینوفیکچرنگ عمل ہے جسے صارفین کی اشیا کی صنعت نے بڑے پیمانے پر اپنایا ہے جس کی وجہ یہ ہے کہ اس کی بہترین درستگی اور مستقل مزاجی کے ساتھ بڑی مقدار میں اعلیٰ معیار کے پرزے تیار کرنے کی صلاحیت ہے۔ یہ عمل عام طور پر صارفین کی اشیا جیسے کہ کھلونے، کچن کے سامان اور پیکیجنگ کے سامان کی تیاری میں استعمال ہوتا ہے۔ یہ بلاگ پوسٹ صارفین کے سامان کی صنعت کے لیے ہائی والیوم انجیکشن مولڈنگ کے فوائد کو تلاش کرے گی۔
ہائی والیوم انجکشن مولڈنگ کے فوائد:
- مؤثر لاگت: ہائی حجم انجیکشن مولڈنگ کے بنیادی فوائد میں سے ایک یہ ہے کہ یہ بڑی مقدار میں پرزے تیار کرنے کا ایک سستا طریقہ ہے۔ یہ عمل انتہائی خودکار ہے، جو مزدوری کے اخراجات کو کم کرتا ہے، اور سانچوں کو دوبارہ استعمال کیا جا سکتا ہے، جس سے مادی اخراجات کم ہوتے ہیں۔
- مستقل مزاجی اور درستگی:انجکشن مولڈنگ حصوں کی پیداوار میں بہترین درستگی اور مستقل مزاجی فراہم کرتی ہے۔ اس کی وجہ یہ ہے کہ سانچوں کو عناصر کے عین مطابق تصریحات کے مطابق ڈیزائن کیا گیا ہے، اس بات کو یقینی بناتے ہوئے کہ ہر ٹکڑا ایک ہی معیار اور سائز کا ہو۔
- تیز پیداوار:ہائی والیوم انجیکشن مولڈنگ ایک فوری عمل ہے، اور بڑی مقدار میں پرزے نسبتا تیزی سے تیار کیے جا سکتے ہیں۔ یہ صارفین کے سامان کی تیاری کے لیے مثالی بناتا ہے جس کے لیے فوری تبدیلی کے اوقات کی ضرورت ہوتی ہے۔
- حسب ضرورت: انجکشن مولڈنگ مختلف مواد، رنگوں اور سطح کی تکمیل کا استعمال کرتے ہوئے حصوں کو حسب ضرورت بنانے کی اجازت دیتی ہے۔ یہ لچک صارفین کی مخصوص ضروریات اور ضروریات کو پورا کرنے والے پرزے تیار کرنا ممکن بناتی ہے۔
کنزیومر گڈز انڈسٹری میں ہائی والیوم انجکشن مولڈنگ کی ایپلی کیشنز:
- پیکیجنگ مواد:انجکشن مولڈنگ بڑے پیمانے پر پیکیجنگ مواد جیسے پلاسٹک کی بوتلیں، جار اور کنٹینرز تیار کرنے کے لیے استعمال ہوتی ہے۔
- کھلونے: انجکشن مولڈنگ کھلونا بنانے کا ایک مقبول طریقہ ہے کیونکہ یہ جلد سے بڑی مقدار میں پرزے تیار کرنے کی اجازت دیتا ہے۔
- کچن کا سامان: انجیکشن مولڈنگ باورچی خانے کے مختلف سامان جیسے کپ، پلیٹیں اور برتن بناتی ہے۔
- الیکٹرانکس: انجکشن مولڈنگ کا استعمال مختلف الیکٹرانک اجزاء جیسے ہاؤسنگ، بٹن اور سوئچ بنانے کے لیے کیا جاتا ہے۔
ایرو اسپیس انڈسٹری کے لیے ہائی والیوم انجکشن مولڈنگ
ایرو اسپیس انڈسٹری ہوائی جہاز کی حفاظت اور کارکردگی کو یقینی بنانے کے لیے اعلیٰ معیار اور درست حصوں کا مطالبہ کرتی ہے۔ ہائی والیوم انجیکشن مولڈنگ ایرو اسپیس انڈسٹری کے لیے ایک ضروری عمل بن گیا ہے کیونکہ یہ مستقل معیار کے ساتھ اعلیٰ معیار کے اجزاء کی بڑی مقدار پیدا کرنے کے لیے ایک سرمایہ کاری مؤثر حل فراہم کرتا ہے۔ یہ بلاگ پوسٹ ایرو اسپیس انڈسٹری کے لیے ہائی حجم انجیکشن مولڈنگ پر بات کرے گی۔
ایرو اسپیس انڈسٹری کے لیے ہائی والیوم انجکشن مولڈنگ کے فوائد:
ایرو اسپیس انڈسٹری کو ہلکے، پائیدار اجزاء کی ضرورت ہوتی ہے جو انتہائی درجہ حرارت اور دباؤ کا مقابلہ کرتے ہیں۔ ہائی والیوم انجیکشن مولڈنگ ایسے عناصر کو پیدا کرنے کے لیے بہت سے فوائد پیش کرتی ہے، بشمول:
- لاگت سے موثر پیداوار: ہائی والیوم انجیکشن مولڈنگ تیزی سے بڑی مقدار میں پرزے تیار کر سکتی ہے، جس کے نتیجے میں مینوفیکچرنگ لاگت کم ہو جاتی ہے۔
- مسلسل معیار: خودکار عمل اس بات کو یقینی بناتا ہے کہ تیار ہونے والا ہر حصہ ایک ہی اعلیٰ معیار کا ہو، جو ہوائی جہاز کے اجزاء کی حفاظت اور بھروسے کے لیے اہم ہے۔
- پیچیدہ جیومیٹریز: انجیکشن مولڈنگ کا عمل پیچیدہ شکلیں اور جیومیٹریاں پیدا کرتا ہے، جنہیں مینوفیکچرنگ کے روایتی طریقوں سے حاصل کرنا مشکل ہو سکتا ہے۔
- مادی انتخاب: ہائی والیوم انجیکشن مولڈنگ مواد کی ایک وسیع رینج پر کارروائی کر سکتی ہے، بشمول کمپوزٹ، جو ایرو اسپیس ایپلی کیشنز کے لیے مثالی ہیں۔
- کم فضلہ: انجیکشن مولڈنگ کے عمل میں اعلیٰ سطح کی آٹومیشن اور درستگی کے نتیجے میں مادی فضلہ اور اسکریپ کم ہوتا ہے، جو لاگت میں نمایاں بچت اور ماحولیاتی فوائد کا باعث بن سکتا ہے۔
ایرو اسپیس انڈسٹری میں ہائی والیوم انجیکشن مولڈنگ کی ایپلی کیشنز:
ہائی والیوم انجیکشن مولڈنگ کو ایرو اسپیس انڈسٹری میں مختلف اجزاء کی تیاری کے لیے بڑے پیمانے پر استعمال کیا جاتا ہے، بشمول:
- ہوا کی نالیوں اور وینٹیلیشن کے نظام
- ہوائی جہاز کے اندرونی اور بیرونی اجزاء
- ساختی عناصر جیسے بریکٹ، کلپس، اور ہاؤسنگ
- الیکٹریکل اور وائرنگ کے اجزاء
- مہریں اور گسکیٹ
ہائی والیوم انجیکشن مولڈنگ میں عام نقائص
تاہم، کسی بھی مینوفیکچرنگ کے عمل کی طرح، انجیکشن مولڈنگ کے نتیجے میں بعض اوقات ایسے نقائص پیدا ہو سکتے ہیں جو حتمی مصنوعات کے معیار کو متاثر کر سکتے ہیں۔ اس بلاگ پوسٹ میں ہائی والیوم انجیکشن مولڈنگ میں کچھ عام خرابیوں اور ان سے کیسے بچا جا سکتا ہے اس پر تبادلہ خیال کیا جائے گا۔
- سنک کے نشانات: سنک کے نشانات ڈپریشن یا انڈینٹیشن ہیں جو ڈھالے ہوئے حصے کی سطح پر ہو سکتے ہیں۔ وہ پلاسٹک کے مواد کے سکڑنے کی وجہ سے ہوتے ہیں کیونکہ یہ ٹھنڈا ہوتا ہے، جس کے نتیجے میں مواد کی غیر مساوی تقسیم ہوتی ہے۔ سنک کے نشانات کو روکنے کے لیے، حصے کے ڈیزائن میں ترمیم کرنا اور پورے حصے میں دیوار کی موٹائی کو یقینی بنانا ضروری ہے۔
- وارپنگ:وارپنگ پلاسٹک کے مواد کی ناہموار ٹھنڈک کی وجہ سے ڈھالے ہوئے حصے کی خرابی ہے۔ اس کا نتیجہ ایک مڑا ہوا یا جھکا ہوا حصہ ہوتا ہے جو مطلوبہ تصریحات پر پورا نہیں اترتا۔ اس بات کو یقینی بنا کر کہ مولڈ کا درجہ حرارت مطابقت رکھتا ہے اور ٹھنڈک کے دوران اس حصے پر دباؤ کو کم کرنے والی ڈیزائن خصوصیات کو شامل کرکے وارپنگ کو روکا جا سکتا ہے۔
- فلیش: فلیش اضافی مواد ہے جو مولڈ جوائنٹ سے باہر نکلتا ہے اور اس وقت ہو سکتا ہے جب مولڈ کو صحیح طریقے سے سیدھ میں نہ کیا گیا ہو یا کلیمپ نہ ہو۔ اس بات کو یقینی بنا کر فلیش کو روکا جا سکتا ہے کہ مولڈ صحیح طریقے سے سیدھ میں ہے اور انجیکشن کے دوران مولڈ کو بند رکھنے کے لیے کلیمپنگ فورس کافی ہے۔
- مختصر شاٹس: شارٹ شاٹس اس وقت ہوتے ہیں جب پلاسٹک کا مواد پورے مولڈ گہا کو نہیں بھرتا، جس کے نتیجے میں ایک نامکمل حصہ ہوتا ہے۔ یہ انجکشن کے ناکافی دباؤ، کم پگھلنے والے درجہ حرارت، یا بند گیٹ کی وجہ سے ہو سکتا ہے۔ مختصر شاٹس کو انجیکشن کے پیرامیٹرز کو بہتر بنا کر اور گیٹ کو صحیح طریقے سے ڈیزائن اور پوزیشن کو یقینی بنا کر روکا جا سکتا ہے۔
- ویلڈ لائنز: ویلڈ لائنیں اس وقت ہوتی ہیں جب دو یا دو سے زیادہ بہاؤ کے محاذ آپس میں ملتے ہیں اور مضبوط ہوتے ہیں، جس کے نتیجے میں ڈھالے ہوئے حصے پر نظر آنے والی لکیر یا سیون بن جاتی ہے۔ ویلڈ لائنوں کو مولڈ ڈیزائن اور انجیکشن کے پیرامیٹرز کو بہتر بنا کر روکا جا سکتا ہے تاکہ اس بات کو یقینی بنایا جا سکے کہ پلاسٹک کا مواد گہا میں یکساں اور آسانی سے بہتا ہے۔
ہائی والیوم انجیکشن مولڈنگ کے لیے ٹربل شوٹنگ ٹپس
ہائی والیوم انجیکشن مولڈنگ ایک پیچیدہ عمل ہے جس میں تفصیل پر توجہ اور محتاط نگرانی کی ضرورت ہوتی ہے تاکہ یہ یقینی بنایا جا سکے کہ حتمی مصنوعات اعلیٰ ترین معیار کی ہے۔ انجیکشن مولڈنگ کے عمل کے دوران متعدد عام مسائل پیدا ہو سکتے ہیں، جو حتمی مصنوعات میں نقائص کا باعث بن سکتے ہیں۔ یہ پوسٹ ہائی والیوم انجیکشن مولڈنگ کے لیے سب سے عام ٹربل شوٹنگ ٹپس کو دریافت کرے گی۔
- انجکشن مولڈنگ مشین کی ترتیبات کو چیک کریں: ہائی والیوم انجیکشن مولڈنگ کا ازالہ کرتے وقت سب سے پہلے چیک کرنے والی چیزوں میں سے ایک انجیکشن مولڈنگ مشین کی سیٹنگز ہیں۔ اس بات کو یقینی بنائیں کہ استعمال شدہ مخصوص مواد کے لیے درجہ حرارت، دباؤ، اور سائیکل کا وقت درست طریقے سے ترتیب دیا گیا ہے۔
- مواد کے بہاؤ کے مسائل کی جانچ کریں: مواد کے بہاؤ کے مسائل ہائی حجم انجیکشن مولڈنگ کے ساتھ ایک اور عام مسئلہ ہیں۔ مشین کی غلط سیٹنگز یا انجیکشن مولڈنگ مشین میں رکاوٹ سمیت کئی عوامل اس کا سبب بن سکتے ہیں۔ اس بات کو یقینی بنائیں کہ مواد آلے کے ذریعے آسانی سے بہتا ہے اور انجیکشن مولڈنگ مشین میں کوئی رکاوٹ نہیں ہے۔
- وارپنگ اور سکڑنے کی جانچ کریں: ہائی حجم انجیکشن مولڈنگ کے دوران وارپنگ اور سکڑنا عام مسائل ہیں۔ یہ مسائل اکثر مواد کے غیر مساوی ٹھنڈک کی وجہ سے ہوتے ہیں، جو حتمی مصنوعات میں وارپنگ یا سکڑنے کا باعث بن سکتے ہیں۔ اس بات کو یقینی بنائیں کہ استعمال کیے جانے والے مخصوص مواد کے لیے ٹھنڈک کا وقت درست طریقے سے سیٹ کیا گیا ہے اور سسٹم ٹھیک طریقے سے کام کرتا ہے۔
- ایئر ٹریپس کی جانچ کریں: زیادہ مقدار میں انجیکشن مولڈنگ کے دوران ایئر ٹریپس ایک اور عام مسئلہ ہے۔ ایسا اس وقت ہوتا ہے جب ہوا مولڈ گہا میں پھنس جاتی ہے، جو کہ حتمی مصنوع میں خالی جگہوں یا بلبلوں کا سبب بن سکتی ہے۔ اس بات کو یقینی بنائیں کہ ہوا کے جال کو ہونے سے روکنے کے لیے مولڈ کو مناسب طریقے سے نکالا گیا ہے۔
- عمل کی نگرانی کریں: آخر میں، انجیکشن مولڈنگ کے عمل کی قریب سے نگرانی کرنا اس بات کو یقینی بنانے کے لیے بہت ضروری ہے کہ کسی بھی مسئلے کو پکڑا جائے اور اسے جلد حل کیا جائے۔ یہ مشین کی ترتیبات، مواد کے بہاؤ اور کولنگ کے عمل کی نگرانی کرکے کیا جا سکتا ہے۔ اس عمل کو قریب سے مانیٹر کرکے، کسی بھی مسئلے کی نشاندہی کی جا سکتی ہے اور اس سے پہلے کہ وہ حتمی مصنوع میں نقائص کا باعث بنیں۔
انجکشن مولڈنگ مشینوں کے لیے دیکھ بھال کے تقاضے
انجیکشن مولڈنگ مشینیں مینوفیکچرنگ انڈسٹری میں سامان کا لازمی حصہ ہیں۔ وہ پلاسٹک کے پرزوں سے لے کر دھات کے اجزاء تک مختلف مصنوعات تیار کرنے کے لیے استعمال ہوتے ہیں۔ تاہم، کسی بھی دوسری مشین کی طرح، انجیکشن مولڈنگ مشینوں کو زیادہ سے زیادہ کارکردگی کو یقینی بنانے اور مہنگی خرابیوں کو روکنے کے لیے باقاعدہ دیکھ بھال کی ضرورت ہوتی ہے۔ یہ پوسٹ انجیکشن مولڈنگ مشینوں کی دیکھ بھال کے کچھ تقاضوں کو تلاش کرے گی۔
- پھسلن: مناسب چکنا انجکشن مولڈنگ مشین کی دیکھ بھال کے سب سے ضروری پہلوؤں میں سے ایک ہے۔ مشین کے حرکت پذیر حصے، جیسے انجیکشن اور کلیمپنگ یونٹس کو رگڑ اور پہننے سے روکنے کے لیے باقاعدگی سے چکنا ہونا چاہیے۔ چکنا کرنے والے کی صحیح قسم کا استعمال کرنا اور چکنا کرنے والے وقفوں کے لیے مینوفیکچرر کی سفارشات پر عمل کرنا ضروری ہے۔
- صفائی: انجکشن مولڈنگ مشین کی دیکھ بھال کا ایک اور ضروری پہلو باقاعدہ صفائی ہے۔ کسی بھی دھول، ملبے، یا پلاسٹک کی باقیات کو ہٹانے کے لیے مشین کو باقاعدگی سے صاف کیا جانا چاہیے جو اس کے اجزاء پر جمع ہو سکتے ہیں۔ یہ مشین کے نوزلز اور فلٹرز کو بند ہونے سے روکنے میں مدد کرے گا، جو کارکردگی کے مسائل کا سبب بن سکتا ہے یا انجن کو بھی نقصان پہنچا سکتا ہے۔
- معائنہ: یہ یقینی بنانے کے لیے کہ مشین اچھی حالت میں ہے باقاعدہ معائنہ بھی ضروری ہے۔ تشخیص میں ٹوٹ پھوٹ کے کسی بھی نشان کی جانچ کرنا شامل ہونا چاہیے، جیسے کہ دراڑیں یا ٹوٹے ہوئے حصے۔ برقی اجزاء، جیسے سینسرز اور سوئچز کو بھی باقاعدگی سے چیک کیا جانا چاہیے تاکہ یہ یقینی بنایا جا سکے کہ وہ صحیح طریقے سے کام کر رہے ہیں۔
- انشانکن: انجیکشن مولڈنگ مشینوں کو بھی انشانکن کی ضرورت ہوتی ہے تاکہ یہ یقینی بنایا جا سکے کہ وہ صحیح پیرامیٹرز کے اندر کام کرتی ہیں۔ اس میں مشین کے درجہ حرارت، دباؤ، اور رفتار کی ترتیبات کو چیک کرنا شامل ہے تاکہ یہ یقینی بنایا جا سکے کہ وہ مینوفیکچرر کی تصریحات کے اندر ہیں۔ اس بات کو یقینی بنانے کے لیے کہ آلہ اپنی بہترین سطح پر کام کر رہا ہے، انشانکن کو باقاعدگی سے انجام دیا جانا چاہیے۔
- گھسے ہوئے حصوں کی تبدیلی: آخر میں، جلد از جلد کسی بھی پہنے یا خراب شدہ حصوں کو تبدیل کرنا ضروری ہے۔ اس سے مشین کو مزید نقصان سے بچنے اور مہنگے ٹوٹنے کے خطرے کو کم کرنے میں مدد مل سکتی ہے۔ بدلنے والے پرزے اصل پرزوں کی طرح معیار کے ہونے چاہئیں اور اہل تکنیکی ماہرین کے ذریعے انسٹال کیے جائیں۔
پائیداری اور اعلی حجم انجیکشن مولڈنگ
حالیہ برسوں میں مینوفیکچرنگ انڈسٹری میں پائیداری ایک اہم تشویش بن گئی ہے۔ جیسے جیسے دنیا صنعتی عمل کے ماحولیاتی اثرات سے زیادہ آگاہ ہوتی جارہی ہے، کمپنیاں پیداواریت اور منافع کو برقرار رکھتے ہوئے اپنے ماحولیاتی اثرات کو کم کرنے کے طریقے تلاش کر رہی ہیں۔ ہائی والیوم انجیکشن مولڈنگ ایک ایسا شعبہ ہے جہاں پائیداری ایک اہم اثر ڈال سکتی ہے۔
بہت سے طریقے ہیں جن میں پائیداری کو اعلی حجم کے انجیکشن مولڈنگ میں شامل کیا جا سکتا ہے:
- مواد کا انتخاب:انجیکشن مولڈنگ میں پائیداری حاصل کرنے کے لیے مناسب مواد کا انتخاب ضروری ہے۔ بہت سے اختیارات میں بائیو پلاسٹک، ری سائیکل پلاسٹک، اور بائیو بیسڈ مواد شامل ہیں۔ ایسے مواد کو منتخب کرکے جو ماحول دوست ہوں اور کم کاربن فوٹ پرنٹ ہوں، مینوفیکچررز ماحول پر اپنے اثرات کو نمایاں طور پر کم کرسکتے ہیں۔
- توانائی کی کارکردگی: ہائی والیوم انجیکشن مولڈنگ کو چلانے کے لیے اہم توانائی کی ضرورت ہوتی ہے۔ مینوفیکچررز توانائی کی بچت کے عمل اور آلات کو لاگو کرکے توانائی کی کھپت اور کاربن کے اخراج کو کم کرسکتے ہیں۔ یہ توانائی کی بچت والی مشینوں کے استعمال، پیداواری عمل کو بہتر بنانے، اور قابل تجدید توانائی کے ذرائع میں سرمایہ کاری کر کے حاصل کیا جا سکتا ہے۔
- فضلہ میں کمی: انجکشن مولڈنگ اہم فضلہ پیدا کر سکتی ہے، خاص طور پر اضافی پلاسٹک۔ فضلہ کو کم کرنے کی حکمت عملیوں کو نافذ کرنے سے، مینوفیکچررز پیدا ہونے والے فضلہ کی مقدار کو کم کر سکتے ہیں اور اپنی پائیداری کو بہتر بنا سکتے ہیں۔ یہ ری سائیکلنگ، مواد کو دوبارہ استعمال کرنے، اور فضلہ کو کم کرنے کے لیے پیداواری عمل کو بہتر بنانے کے ذریعے حاصل کیا جا سکتا ہے۔
- زندگی کے چکر کا تجزیہ: زندگی کے چکر کا تجزیہ کرنے سے مینوفیکچررز کو ان کی پوری زندگی کے دوران اپنی مصنوعات کے ماحولیاتی اثرات کو سمجھنے میں مدد مل سکتی ہے۔ یہ تجزیہ ان علاقوں کی نشاندہی کرنے میں مدد کر سکتا ہے جہاں پائیداری کو بہتر بنایا جا سکتا ہے اور ماحول دوست مصنوعات بنانے کے لیے فیصلہ سازی کی رہنمائی کی جا سکتی ہے۔
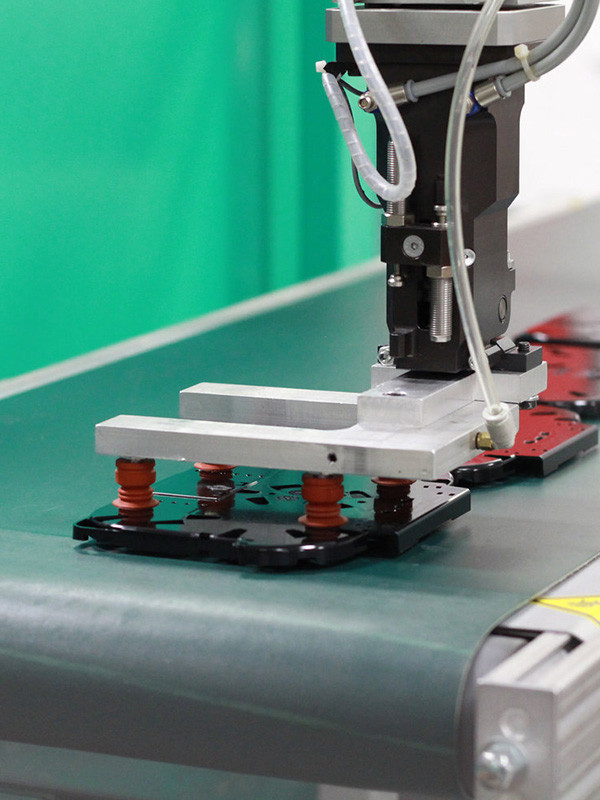
اہم نکات:
- انجکشن مولڈنگ میں پائیداری کے حصول میں مواد کا انتخاب ایک اہم کردار ادا کرتا ہے۔
- توانائی کے موثر عمل اور آلات توانائی کی کھپت اور کاربن کے اخراج کو کم کر سکتے ہیں۔
- فضلہ کو کم کرنے کی حکمت عملی، جیسے ری سائیکلنگ اور مواد کو دوبارہ استعمال کرنا، پیدا ہونے والے فضلہ کی مقدار کو کم کر سکتا ہے۔
- زندگی کے چکر کا تجزیہ ان علاقوں کی نشاندہی کرنے میں مدد کر سکتا ہے جہاں پائیداری کو بہتر بنایا جا سکتا ہے۔
- اعلیٰ حجم کے انجیکشن مولڈنگ میں پائیداری کو شامل کرنے سے مینوفیکچررز کو لاگت میں کمی اور ماحولیات کے حوالے سے باشعور صارفین کو اپیل کر کے فائدہ پہنچ سکتا ہے۔
- ہائی والیوم انجیکشن مولڈنگ کا مستقبل
ہائی والیوم انجیکشن مولڈنگ کئی صنعتوں کے لیے کئی دہائیوں سے ایک اہم مینوفیکچرنگ عمل رہا ہے، اور یہ پلاسٹک کی مصنوعات کی ایک وسیع رینج تیار کرنے میں ایک لازمی کردار ادا کر رہا ہے۔ جیسے جیسے ٹیکنالوجی کی ترقی اور صارفین کی مانگ زیادہ پائیدار اور حسب ضرورت مصنوعات کی طرف منتقل ہوتی ہے، ہائی والیوم انجیکشن مولڈنگ کا مستقبل روشن نظر آتا ہے۔ یہاں کچھ ایسے رجحانات اور اختراعات ہیں جو اس صنعت کے خاتمے کو تشکیل دے رہے ہیں۔
- استحکام: ماحول دوست مصنوعات کے لیے صارفین کی بڑھتی ہوئی مانگ کے ساتھ، ہائی والیوم انجیکشن مولڈنگ میں پائیداری بہت اہم ہو گئی ہے۔ مینوفیکچررز نئے مواد کی تلاش کر رہے ہیں، جیسے کہ بائیو پلاسٹک اور بائیو بیسڈ مواد، اور اپنی مصنوعات کے ماحولیاتی اثرات کو کم کرنے کے لیے فضلہ کم کرنے کی حکمت عملیوں پر عمل درآمد کر رہے ہیں۔
- حسب ضرورت: صارفین ان مصنوعات کی تلاش میں ہیں جو ان کی منفرد ضروریات اور ترجیحات کو پورا کرتی ہیں، اور اس مانگ کو پورا کرنے کے لیے ہائی والیوم انجیکشن مولڈنگ اچھی طرح سے موزوں ہے۔ ٹیکنالوجی میں ترقی، جیسے کہ 3D پرنٹنگ، اپنی مرضی کے مطابق حصوں اور مصنوعات کو بڑی مقدار میں تیار کرنا آسان اور زیادہ کفایت شعار بنا رہی ہے۔
- آٹومیشن: مینوفیکچرنگ انڈسٹری میں آٹومیشن تیزی سے رائج ہو رہی ہے، اور ہائی والیوم انجیکشن مولڈنگ بھی اس سے مستثنیٰ نہیں ہے۔ خودکار عمل، جیسے روبوٹک ہتھیار اور کمپیوٹر کی مدد سے ڈیزائن، پیداوار کی کارکردگی کو بہتر بنا سکتے ہیں اور اخراجات کو کم کر سکتے ہیں۔
- صنعت 4.0: چوتھا صنعتی انقلاب، Industry 4.0، مصنوعی ذہانت، انٹرنیٹ آف تھنگز (IoT) اور بڑے ڈیٹا اینالیٹکس جیسی جدید ٹیکنالوجیز کو یکجا کر کے مینوفیکچرنگ انڈسٹری کو تبدیل کر رہا ہے۔ یہ ٹیکنالوجیز مینوفیکچررز کے لیے پیداواری عمل کو بہتر بنانے اور مصنوعات کے معیار کو بہتر بنانے میں آسانی پیدا کرتی ہیں۔
- طبی صنعت:ہائی والیوم انجیکشن مولڈنگ اپنی درستگی اور مستقل مزاجی کی وجہ سے طبی آلات اور آلات تیار کرنے کے لیے موزوں ہے۔ طبی مصنوعات کی مانگ میں اضافہ متوقع ہے، جس سے یہ انجکشن مولڈنگ انڈسٹری کے لیے ایک اہم علاقہ بن جائے گا۔
- بجلی کی گاڑیاں:الیکٹرک کاروں کی طرف تبدیلی ہائی والیوم انجیکشن مولڈنگ انڈسٹری کے لیے نئے مواقع پیدا کرتی ہے۔ پلاسٹک کے اجزاء، جیسے بیٹری ہاؤسنگ اور الیکٹریکل کنیکٹر، الیکٹرک کاروں کے لیے ضروری ہیں، اور الیکٹرک گاڑیوں کے زیادہ مقبول ہونے کے ساتھ ہی ان اجزاء کی مانگ میں اضافہ متوقع ہے۔
نتیجہ:
بڑی مقدار میں پلاسٹک کے پرزے تیار کرنے کے لیے ہائی والیوم انجیکشن مولڈنگ ضروری ہے۔ فوائد، نقصانات، مواد، مشینوں، طریقوں، ڈیزائن کے تحفظات، کوالٹی کنٹرول کے اقدامات، اور اعلی حجم کے انجیکشن مولڈنگ کے استعمال کو سمجھ کر، کاروبار اپنے پیداواری عمل کو بہتر بنا سکتے ہیں، لاگت کو کم کر سکتے ہیں، اور اپنی مصنوعات کے معیار کو بہتر بنا سکتے ہیں۔ چاہے آپ میڈیکل، آٹوموٹیو، کنزیومر گڈز، یا ایرو اسپیس انڈسٹری میں ہوں، ہائی والیوم انجیکشن مولڈنگ آپ کے کاروبار کو لاگت سے مؤثر قیمت پر مستقل، اعلیٰ معیار کے پرزے فراہم کرکے فائدہ پہنچا سکتی ہے۔