انجکشن مولڈنگ کے عام مولڈنگ نقائص کے حل
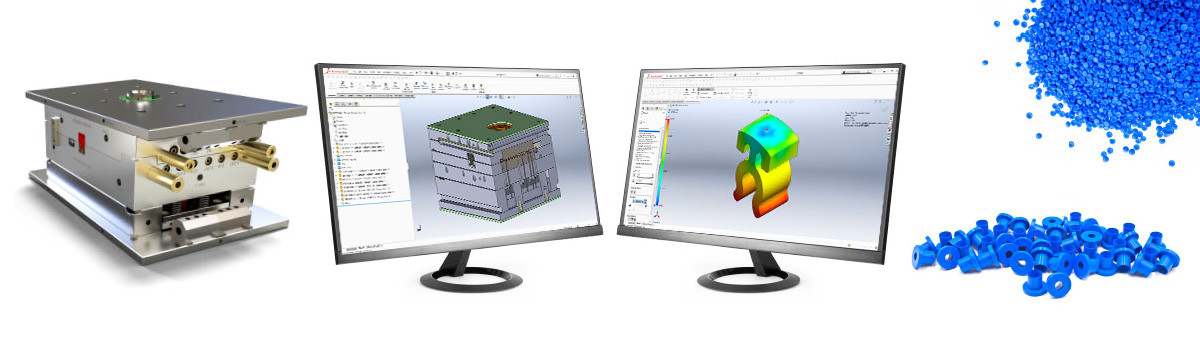
پلاسٹک انجیکشن مولڈنگ پرزوں کو پروسیس کرنے کے لیے سانچوں کا استعمال کرتے وقت نقائص عام ہیں، اور یہ بڑی حد تک پروسیسنگ کی کارکردگی کو متاثر کرتا ہے۔ مندرجہ ذیل عام مولڈنگ نقائص اور پلاسٹک انجیکشن مولڈ پارٹس کے حل ہیں۔
مختصر شاٹس
شارٹ شاٹس ان پروڈکٹس کا حوالہ دیتے ہیں جو سانچوں کو مکمل طور پر نہ بھرنے کی وجہ سے نامکمل ہیں۔
یہ نقص عام طور پر گیٹ یا ان حصوں سے دور دراز جگہ پر ظاہر ہوتا ہے جہاں صرف مولڈ کے تنگ علاقوں سے ہی پہنچا جا سکتا ہے کیونکہ تنگ علاقے پگھلنے کے بہاؤ کو متاثر کر سکتے ہیں۔
شارٹ شاٹ مائیکرو فلو مارکس کا سبب بن سکتا ہے یا اس کے نتیجے میں پروڈکٹ کا ایک بڑا حصہ واضح طور پر غائب ہو سکتا ہے۔
وجہ:
مختصر شاٹس کی وجوہات میں شامل ہیں:
سڑنا میں انجکشن خام مال کافی نہیں ہے.
پگھلنے کی مزاحمت بڑی ہے، جس کے نتیجے میں سڑنا مکمل طور پر نہیں بھرا جا سکتا۔
سڑنا کا نکلنا ناقص ہے اور اس کی وجہ سے کیویٹیشن پیدا ہوتی ہے جو پگھلنے کو روکتی ہے، جس سے پگھل سڑنا کے کچھ حصوں میں بہہ نہیں سکتا۔
دفن
گڑھے مولڈ گہا سے مصنوع میں نکالے گئے اضافی خام مال کے چپکنے سے پیدا ہوتے ہیں۔
یہ خرابی پروڈکٹ کے کناروں پر یا سڑنا کے ہر ایک حصے پر نظر آئے گی۔ خام مال مولڈ، یا حرکت پذیر اور فکسنگ مولڈ کی بانڈنگ سائٹس سے بہہ سکتا ہے۔
گڑ بھی مولڈ کور پر پایا جا سکتا ہے، جو ہائیڈرولک پریشر یا کونیی پن کی وجہ سے ہوتا ہے۔
burrs کی شدت مختلف ہوتی ہے، کبھی پتلی، کبھی کبھی موٹی.
وجہ:
burrs کی وجوہات میں شامل ہیں:
کلیمپنگ مولڈ کی سطح کو نقصان پہنچا ہے یا بہت زیادہ پہنا ہوا ہے۔
موونگ مولڈ اور فکسنگ مولڈ جب مقفل ہو جاتے ہیں تو ان کی جگہ نہیں ہوتی ہے۔
سڑنا میں خام مال کا دباؤ مولڈ کلیمپنگ فورس سے زیادہ ہے۔
اوپر بیان کی گئی تیسری شرط مختلف وجوہات کی بنا پر ہو گی۔ مندرجہ ذیل حالات میں، خام مال کا دباؤ مولڈ کلیمپنگ فورس سے زیادہ ہے۔
انجیکشن مولڈ (مولڈ فلنگ اسٹیج) کے پہلے مرحلے میں بہت زیادہ خام مال بھرا جاتا ہے، جس سے سڑنا کے اندر دباؤ بڑھ جاتا ہے۔
سڑنا بھرنے کے عمل کے دوران، پگھلنے کے بہاؤ کی بڑی مزاحمت بھی سڑنا کے اندر دباؤ کو بڑھا دے گی۔
دباؤ کے انعقاد کے مرحلے کے دوران سڑنا گہا دباؤ بہت زیادہ ہے۔
مولڈ کلیمپنگ فورس کافی نہیں ہے۔
انحطاط
گلنا بہت سے نتائج کا باعث بن سکتا ہے۔ مسئلہ کی حد اور شدت بھی مختلف ہوتی ہے۔ سب سے سنگین صورت میں، یہ مصنوعات کی مکمل رنگت اور خراب میکانی خصوصیات کا سبب بن سکتا ہے۔ مقامی تنزلی صرف سیاہ دھاریوں یا دھبوں کا سبب بنے گی۔
وجہ:
انحطاط خام مال کے خراب ہونے کی وجہ سے ہوتا ہے۔ لمبی زنجیر کے مالیکیول جو پلاسٹک بناتے ہیں وہ ضرورت سے زیادہ گرمی یا ضرورت سے زیادہ قینچ کے دباؤ کی وجہ سے گل جائیں گے۔ مالیکیولز کے گلنے کے دوران، غیر مستحکم گیس انحطاط کے عمل کو تیز کرے گی، جو خام مال کی رنگت کو ختم کرنے کا سبب بنے گی۔ بڑی مقدار میں مالیکیولز کا گلنا آخر کار خام مال کے مواد کو توڑ دے گا اور مکینیکل خصوصیات پر منفی اثر ڈالے گا۔
مقامی انحطاط مادی بیرل کے غیر مساوی درجہ حرارت کے نتیجے میں ہو سکتا ہے۔
انحطاط درج ذیل حالات میں ہو سکتا ہے:
مادی بیرل یا ہاٹ رنر سسٹم میں خام مال کو زیادہ گرم کیا جا رہا ہے۔
خام مال بیرل میں زیادہ دیر تک رہتا ہے۔
انجیکشن مولڈنگ کے عمل کے دوران، خام مال پر قینچ کا دباؤ بہت زیادہ ہوتا ہے۔ اگر نوزلز مسدود ہیں، یا گیٹ اور رنر بہت تنگ ہیں، تو یہ قینچ کے دباؤ میں اضافہ کرے گا۔
اخترتی
عام حالات میں، مصنوعات کی شکلیں سانچوں کے مطابق ہونی چاہئیں۔ اخترتی سے مراد مصنوعات کی خرابی ہے۔
جب حالت خراب ہو جاتی ہے، تو مصنوعات مکمل طور پر خراب ہو جائیں گی جب اسے سڑنا سے نکالا جائے گا۔ جب حالت سنگین نہیں ہے، تو مصنوعات کی شکل میں چھوٹی بے ضابطگیاں نظر آئیں گی۔
لمبے لیکن بغیر سپورٹ کناروں یا بڑے طیارے وہ علاقے ہیں جو خرابی کا سب سے زیادہ شکار ہیں۔
وجہ:
خرابی کی وجوہات:
جب سڑنا جاری ہوتا ہے تو درجہ حرارت بہت زیادہ ہوتا ہے۔
چونکہ موٹی اور پتلی جگہوں میں ٹھنڈک کا وقت مختلف ہوتا ہے، یا مولڈ کو حرکت دینے اور مولڈ کو ٹھیک کرنے میں سڑنا کے درجہ حرارت کا فرق ہوتا ہے، اس لیے مصنوعات کے اندر سکڑنا مختلف ہوتا ہے۔
بھرتے وقت مولڈ کا بہاؤ ہموار نہیں ہوتا ہے (نام نہاد "فریزنگ اورینٹیشن") یا مولڈ کیویٹی کے اندر پریشر ہولڈنگ اسٹیج پر بہت زیادہ ہوتا ہے۔
نجاست
نجاست اکثر مختلف رنگوں، دھبوں یا دھاریوں میں دھبوں کی شکل میں ظاہر ہوتی ہے۔ سب سے عام ایک سیاہ دھبہ ہے۔
نجاست صرف چھوٹے دھبے ہو سکتے ہیں، لیکن یہ واضح دھاریاں یا رنگ ختم کرنے کا بڑا حصہ بھی ہو سکتا ہے جب یہ سنگین ہو۔
وجہ:
نجاست خام مال کے ساتھ ملاوٹ کی وجہ سے ہوتی ہے، جیسے:
بیرل میں لے جانے پر خام مال کو مختلف اشیاء کے ساتھ ملایا جاتا ہے۔
خام مال کا گلنا کسی بھی کٹنگ میکانزم سے گر کر خام مال میں ملایا جا سکتا ہے، جیسے مشین کے بولٹ، ڈرائینگ ڈرم کی اندرونی دیوار، جوڑ/نوزل۔
چکنا
لیمینیشن مصنوعات کی سطح پر "جلد کا اثر" پیدا کرے گا، جو مصنوعات اور دیگر خام مال کی سطح کی خصوصیات اور ساخت میں فرق کی وجہ سے ہوتا ہے، اور یہ ایک چھلکی ہوئی جلد بناتا ہے جسے ہٹایا جا سکتا ہے۔
جب لیمینیشن سنجیدہ ہوتی ہے، تو کراس سیکشن کا پورا علاقہ مختلف تہوں سے بنا ہوتا ہے، اور ایک ساتھ نہیں پگھلا ہوتا۔ جب نقائص کم واضح ہوں تو، مصنوعات کی ظاہری شکل ضروریات کو پورا کر سکتی ہے، لیکن مصنوعات کی میکانکی خصوصیات کو توڑ دے گی۔
وجہ:
لیمینیشن کی دو اہم وجوہات ہیں۔ پہلا یہ ہے کہ جب دو مختلف قسم کے خام مال غلط طریقے سے آپس میں مل جاتے ہیں۔ دو خام مال کو دباؤ کے تحت ایک ہی وقت میں بیرل میں منتقل کیا جائے گا۔ تاہم، جب ٹھنڈا ہونے پر سڑنا ایک ساتھ نہیں پگھلا سکتا، بالکل اسی طرح جیسے مختلف تہوں کو زبردستی ایک ساتھ دبایا جاتا ہے تاکہ مصنوعات بن سکیں۔
دوسرا: اگر سرد پگھلنے کو تنگ دروازے سے گزرنے پر مجبور کیا جائے تو، قینچ کا تناؤ پیدا ہوگا۔ بہت زیادہ قینچ کا دباؤ پیشگی پگھل جانے والی پگھلنے والی پرت کو مکمل طور پر فیوز نہیں کر سکتا۔
اختلاط کا خطرہ:
ایک چیز جس کے بارے میں آگاہ ہونا چاہئے وہ یہ ہے کہ کچھ خام مال ایک ساتھ ملا کر مضبوط کیمیائی رد عمل کا باعث بنیں گے، جیسے کہ PVC اور Avetal کو نہیں ملایا جانا چاہیے۔
سلور لکیری
سلیور لکیری صرف مقامی رجحان ہو سکتا ہے، لیکن جب یہ سنجیدہ ہو تو اسے پوری سطح تک پھیلایا جا سکتا ہے۔
سلور لکیری مصنوعات کی ظاہری شکل کو متاثر کرے گا اور مصنوعات کی مکینیکل خصوصیات کو بھی نقصان پہنچائے گا۔
وجہ:
درج ذیل دو نکات چاندی کی لکیری کا سبب بنتے ہیں:
خام مال گیلا ہے اور ان میں سے کچھ ہوا میں بھاپ جذب کرے گا۔ اگر خام مال بہت گیلا ہے تو، دباؤ والے بخارات اعلی درجہ حرارت اور بیرل کے اعلی دباؤ کے تحت پیدا ہوسکتے ہیں۔ یہ بخارات مصنوعات کی سطح کو توڑ کر چاندی کی پٹیاں بناتے ہیں۔
پگھلنے سے تھرمل کو نقصان پہنچا اور مقامی انحطاط پیدا کرتا ہے۔ پیدا ہونے والی غیر مستحکم گیس کو سڑنا کی سطح پر بلاک کر دیا جائے گا اور مصنوعات کی سطح پر پٹیاں پیدا ہوں گی۔
یہ انحطاط جتنی بدتر نہیں ہے۔ جب تک پگھلنے کا درجہ حرارت زیادہ ہے یا اسے پلاسٹکائزیشن کے دوران قینچ کے دباؤ کا نشانہ بنایا جاتا ہے یا سڑنا میں انجیکشن لگایا جاتا ہے ، ایسا ہوسکتا ہے۔
چمک / سایہ
مصنوعات کی سطح کی تکمیل سانچوں کی طرح ہونی چاہئے۔ جب دو کی سطح کی تکمیل مختلف ہوتی ہے، تو چمک/سائے کے نقائص پیدا ہوتے ہیں۔
جب نقائص واقع ہوں گے تو سطح اداس ہو جائے گی، اور کھردری سطح ہموار اور چمکدار ہے۔
وجہ:
چمک/سائے کی وجوہات میں شامل ہیں:
پگھلنا غیر آسانی سے بہتا ہے یا مولڈ کی سطح کا درجہ حرارت کم ہے، جس کے نتیجے میں مٹیریل مولڈنگ کے وقت مولڈ کی سطح کی تکمیل کو نقل نہیں کیا جا سکتا۔
پریشر ہولڈنگ کے دوران، گہا میں دباؤ اتنا زیادہ نہیں ہوتا ہے کہ ٹھنڈک کے عمل میں مواد کو سانچے کی سطح سے چمٹ جائے، سکڑنے کے نشانات رہ جاتے ہیں۔
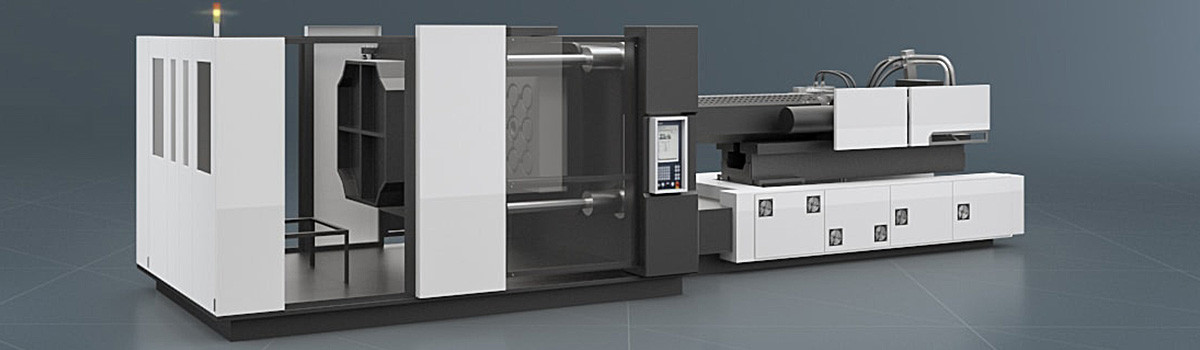
بہاؤ کے نشان
بہاؤ کے نشان مصنوعات کی سطح پر متعدد شکلوں میں پائے جا سکتے ہیں۔ عام طور پر، یہ ایک سایہ دار علاقہ بنائے گا۔
بہاؤ کے نشان مصنوعات کی سطح پر کوئی ابھار یا ڈپریشن پیدا نہیں کرتے، جسے انگلیوں سے محسوس نہیں کیا جا سکتا۔ اس نقص کو ڈریگ مارکس، گھوسٹنگ اور شیڈو بھی کہا جاتا ہے۔
جب بہاؤ کے نشانات واضح ہوں گے، تو یہ نالی پیدا کرے گا، اور مصنوعات کی سطح پر نشانات جیسے نقائص چھوڑے گا۔
وجہ:
بہاؤ کے نشانات مل سکتے ہیں جب:
پگھلنے کا بہاؤ ناقص ہے یا سڑنا کی سطح کا درجہ حرارت کم ہے، جس کے نتیجے میں سڑنا بھرنے کے عمل میں پلاسٹک کے بہاؤ کی بڑی مزاحمت ہوتی ہے۔
مولڈ فلنگ میں، مزاحمت کے ساتھ پگھلنے کا بہاؤ، جو ڈائی کی ناہموار سطح، ڈائی سطح پر چھپے ہوئے نشانات یا پیٹرن، یا بھرنے کے عمل کے دوران پگھلنے کے بہاؤ کی سمت میں تبدیلی کی وجہ سے ہو سکتا ہے۔
جوائنٹنگ لائن
جوائننگ لائن اس وقت بنتی ہے جب مولڈ بھرنے کے دوران دو پگھلنے والے محاذ ملتے ہیں، اور مصنوعات کی سطح پر ایک لکیر کی طرح ظاہر ہوں گے۔
جوائنٹنگ لائن مصنوعات کی سطح پر کریکنگ لائن کی طرح ہے، جس کا پتہ لگانا واضح نہیں ہے۔
سانچوں کو ڈیزائن کرتے وقت، کچھ نظر آنے والی جوائنٹنگ لائنیں ناگزیر ہوتی ہیں۔ اس صورت میں، مصنوعات کی مضبوطی اور ظاہری شکل کو خراب ہونے سے روکنے کے لیے جوائنٹنگ لائن کو جتنا ممکن ہو چھوٹا کریں۔
وجہ:
پگھل سامنے کی نسل کی بہت سی وجوہات ہیں۔ سب سے زیادہ ممکنہ وجہ مولڈ کور کے کناروں کے ساتھ پگھلنے کا بہاؤ ہو سکتا ہے۔ جب دونوں پگھلتے ہیں تو یہ جوائنٹنگ لائنیں پیدا کرتا ہے۔ دو پگھلنے والے سامنے کا درجہ حرارت اتنا زیادہ ہونا چاہئے کہ وہ کامیابی کے ساتھ ایک ساتھ فیوز ہو سکیں، اور مصنوعات کی طاقت اور ظاہری شکل کو متاثر نہ کریں۔
جب دونوں پگھلیں مکمل طور پر ایک ساتھ نہیں مل سکتے ہیں، تو نقائص پیدا ہوں گے۔
خرابیوں کی وجوہات:
سڑنا میں موٹے اور پتلے حصے ہوتے ہیں، اور پگھلنے کی رفتار مختلف ہوتی ہے، جب پگھل سڑنا کے پتلے حصے سے گزرتا ہے تو درجہ حرارت کم ہوتا ہے۔
ہر رنر کی لمبائی مختلف ہوتی ہے۔ تنہا بھاگنے والوں کو ٹھنڈا کرنا آسان ہوگا۔
مولڈ کیویٹی پریشر اتنا کافی نہیں ہے کہ پریشر ہولڈنگ اسٹیج کے دوران پگھلنے کی مکمل اجازت دے سکے۔
باقی بلبلے پگھلنے والے فرنٹ کو فیوز کرنے کے قابل نہیں بناتے ہیں، جو جلنے کا باعث بھی بنیں گے۔
جل رہا ہے
جلنا شارٹ شاٹ سے ملتا جلتا ہے، لیکن فاسد دھندلاہٹ کناروں اور ہلکی جلنے کی بو کے ساتھ۔ مصنوعات پر کاربن بلیک ایریاز نمودار ہوں گے، جب حالت سنگین ہو، پلاسٹک کے جلنے کی بو کے ساتھ۔
اگر نقائص کو ختم نہیں کیا جاتا ہے، تو اکثر سڑنا پر سیاہ جمع ہوتا ہے. اگر جلنے سے پیدا ہونے والی گیس یا تیل کے مادوں کو فوری طور پر چیک نہ کیا جائے تو وہ ہوا کے سوراخوں کو روک سکتے ہیں۔ جلنا عام طور پر راستوں کے آخر میں پایا جاتا ہے۔
وجہ:
جلنا اندرونی دہن کے اثر کی وجہ سے ہوتا ہے۔ جب ہوا میں دباؤ بہت کم وقت میں تیزی سے بڑھتا ہے تو درجہ حرارت بڑھ جاتا ہے اور جلنے کا سبب بنتا ہے۔ جمع کردہ اعداد و شمار کے مطابق، انجکشن مولڈنگ کے عمل میں اندرونی دہن کا اثر 600 ڈگری تک اعلی درجہ حرارت پیدا کر سکتا ہے.
جلن پیدا ہوسکتی ہے جب:
مولڈ بھرنے کی رفتار تیز ہے تاکہ ہوا کو مولڈ گہا سے خالی نہیں کیا جاسکتا، اور آنے والے پلاسٹک کے بلاک کی وجہ سے ہوا کے بلبلے پیدا ہوتے ہیں، اور کمپریس ہونے کے بعد اندرونی دہن کے اثر کا باعث بنتے ہیں۔
ہوا کے سوراخ مسدود ہیں یا وینٹیلیشن ہموار نہیں ہے۔
سڑنا میں ہوا کو ہوا کے سوراخوں سے خالی کرنا چاہئے۔ اگر وینٹیلیشن پوزیشن، نمبر، سائز یا افعال سے متاثر ہوتا ہے، تو ہوا مولڈ میں رہے گی اور جلنے کا باعث بنے گی۔ بڑی مولڈ کلیمپنگ فورس بھی خراب وینٹیلیشن کا باعث بنے گی۔
ہٹانے
سکڑنے سے مراد مصنوعات کی سطح پر موجود معمولی سوراخ ہیں۔
جب نقائص معمولی ہوتے ہیں، تو مصنوعات کی سطح ناہموار ہوتی ہے۔ جب یہ سنجیدہ ہے تو، مصنوعات کا بڑا علاقہ گر جائے گا. محرابوں، ہینڈلز اور پروٹریشن والی مصنوعات اکثر سکڑنے والے نقائص کا شکار ہوتی ہیں۔
وجہ:
سکڑاؤ کولنگ کے دوران خام مال کے بڑے رقبے کے سکڑنے کی وجہ سے ہوتا ہے۔
مصنوعات کے موٹے حصے میں (جیسے محراب)، مواد کا بنیادی درجہ حرارت کم ہوتا ہے، اس لیے سکڑنا سطح کے مقابلے میں بعد میں واقع ہو گا، جو خام مال کے اندر ایک سکڑاؤ کی قوت پیدا کرے گا، اور بیرونی طرف کو اندرونی دباؤ میں کھینچ لے گا۔ سکڑاؤ پیدا کرنے کے لیے۔
سکڑاؤ مندرجہ ذیل حالات میں ہوتا ہے:
مولڈ گہا میں دباؤ کولنگ کے عمل میں خام مال کے سکڑنے سے پیدا ہونے والی قوت سے کم ہے۔
کولنگ کے عمل کے دوران مولڈ گہا کا دباؤ کا ناکافی وقت، جس کے نتیجے میں خام مال گیٹ سے گہا سے باہر نکل جاتا ہے۔
مولڈنگ اور پریشر ہولڈنگ مرحلے کے دوران خام مال میں کافی بفرنگ کی گنجائش نہیں ہوتی ہے کیونکہ ضرورت سے زیادہ خام مال کے انجیکشن سے پہلے سکرو کو مکمل طور پر واپس لے لیا جاتا ہے۔
گیٹس اور رنرز کے کراس سیکشن والے حصے مصنوعات کی موٹائی سے بہت چھوٹے ہیں، جس کا مطلب ہے کہ پروڈکٹس کے اخراج کے عمل سے پہلے گیٹس پہلے ہی منجمد ہو چکے ہیں۔
بلبلے
ویکیوم بلبلوں کو ہوا کے بلبلوں کی شکل میں پیش کیا جاتا ہے، جو شفاف مصنوعات پر آسانی سے پایا جا سکتا ہے۔ یہ مبہم مصنوعات کے کراس سیکشن پر بھی دیکھا جا سکتا ہے۔
وجہ:
ہوا کے بلبلے مصنوعات کا ویکیوم حصہ ہیں، جو اس وقت پیدا ہوتے ہیں جب ٹھنڈک کے عمل کے دوران خام مال سکڑ جاتا ہے۔
سکڑنے کی طرح، خام مال کا اندرونی حصہ سکڑنے والی قوت پیدا کرتا ہے۔ فرق یہ ہے کہ جب بلبلے بنتے ہیں تو مصنوعات کی بیرونی ظاہری شکل مستحکم ہوتی ہے، اور کوئی گرا نہیں ہوتا، اس لیے کھوکھلے بلبلے پیدا ہوتے ہیں۔
بلبلوں کی وجوہات کمی کی طرح ہی ہیں، بشمول:
غیر موثر مولڈ گہا دباؤ
ناکافی گہا دباؤ کا وقت
رنر اور گیٹ کا سائز بہت چھوٹا ہے۔
چھڑکنے کے نشانات
چھڑکنے کے نشانات گیٹ کے سامنے دھاگے والے حصے کا حوالہ دیتے ہیں۔ چھڑکنے کے نشانات نہ صرف مصنوعات کی ظاہری شکل کو متاثر کرتے ہیں بلکہ مصنوعات کی طاقت کو بھی متاثر کرتے ہیں۔
وجہ:
چھڑکنے کے نشان سڑنا بھرنے کے عمل کے دوران پگھلنے کے بہاؤ کے قابو سے باہر ہونے کی وجہ سے ہوتے ہیں۔
پگھلا ہوا پلاسٹک بڑے دباؤ کے تحت سانچے میں داخل ہو جاتا ہے۔ اگر مولڈ بھرنے کی رفتار بہت زیادہ ہے تو، پلاسٹک مولڈ گہا کے کھلے خلا سے نکل جائے گا، اور تیزی سے واپس اور ٹھنڈا ہو جائے گا۔ اس وقت، دھاگے بنتے ہیں، جو پگھلے ہوئے پلاسٹک کو دروازوں میں داخل ہونے سے روکتے ہیں۔
چھڑکنے کے نشانات کی بنیادی وجہ گیٹس کی غلط پوزیشن یا گیٹ کا ڈیزائن ہے۔ درج ذیل دو حالتیں خرابیوں کی صورت حال کو مزید خراب کر دیں گی۔
ہائی مولڈ بھرنے کی رفتار
سڑنا بھرنے کے دوران پگھلنے کا ناقص بہاؤ