تھرمو پلاسٹک انجکشن مولڈنگ
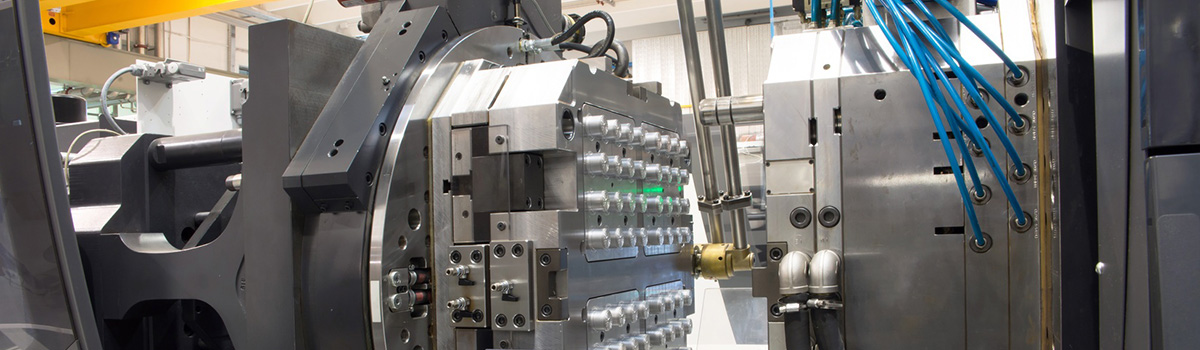
تھرمو پلاسٹک انجکشن مولڈنگ ایک مقبول مینوفیکچرنگ عمل ہے جو متعدد صنعتوں کے لیے پلاسٹک کے مختلف پرزے بنانے کے لیے استعمال ہوتا ہے۔ اس عمل میں پلاسٹک کے چھروں کو پگھلا کر تین جہتی شکل پیدا کرنے کے لیے ایک سانچے میں انجیکشن لگانا شامل ہے۔ تھرمو پلاسٹک انجیکشن مولڈنگ سخت رواداری کے ساتھ اعلی معیار کے پلاسٹک کے پرزوں کی بڑی مقدار تیار کرنے کے لئے انتہائی موثر اور لاگت سے موثر ہے۔ یہ جامع گائیڈ تھرمو پلاسٹک انجیکشن مولڈنگ کے مختلف پہلوؤں کو تلاش کرے گا، بشمول اس کے فوائد اور نقصانات، استعمال شدہ تھرمو پلاسٹک کی اقسام، انجیکشن مولڈنگ کا عمل، ڈیزائن کے تحفظات اور بہت کچھ۔
تھرمو پلاسٹک انجکشن مولڈنگ کی تاریخ
تھرمو پلاسٹک انجیکشن مولڈنگ کی تاریخ تکنیکی ترقی، مادی ترقیات، اور صنعتی ایپلی کیشنز کی ایک صدی پر محیط ہے۔ سیلولائڈ مولڈنگ کے عمل کے طور پر اس کے شائستہ آغاز سے لے کر موجودہ جدید ترین ٹیکنالوجی تک، انجیکشن مولڈنگ ایک اہم مینوفیکچرنگ تکنیک بنی ہوئی ہے، جدت کو آگے بڑھاتی ہے اور مختلف صنعتوں کو تشکیل دیتی ہے۔
- ابتدائی ترقیات:جان ویزلی ہیاٹ اور ان کے بھائی یسعیاہ نے پہلی عملی انجیکشن مولڈنگ مشین تیار کی، جس میں تھرمو پلاسٹک انجیکشن مولڈنگ کی ابتدا 19ویں صدی کے آخر تک ہوئی۔ 1872 میں، انہوں نے ایک ایسا آلہ پیٹنٹ کیا جس نے ایک پلنجر کا استعمال کرتے ہوئے سیلولائڈ کو مولڈ گہا میں انجیکشن لگایا، جس سے ٹھوس چیزیں بنیں۔ اس پیش رفت نے جدید انجیکشن مولڈنگ کے عمل کی بنیاد رکھی۔
- مواد میں ترقی:20 ویں صدی کے اوائل میں، نئے مصنوعی پولیمر متعارف کروانے سے انجیکشن مولڈنگ کے نئے امکانات کھل گئے۔ بیکلائٹ، ایک فینولک رال، اپنی بہترین برقی موصل خصوصیات کی وجہ سے مولڈنگ کے لیے ایک مقبول مواد بن گیا۔ 1930 اور 1940 کی دہائیوں کے دوران، پولیمر کیمسٹری میں ہونے والی پیشرفت نے دیگر تھرموپلاسٹک کی ترقی کا باعث بنی، جیسے پولی اسٹیرین اور پولیتھیلین، جس نے انجیکشن مولڈنگ کے لیے موزوں مواد کی حد کو مزید وسیع کیا۔
- صنعتی اپنانا: تھرمو پلاسٹک انجیکشن مولڈنگ کو بڑے پیمانے پر اپنانا 1950 کی دہائی میں شروع ہوا کیونکہ مینوفیکچررز نے اس کی لاگت کی تاثیر اور استعداد کو تسلیم کیا۔ تیز رفتار سائیکل کے اوقات اور پیداوار کے حجم میں اضافے کے لیے ہائی پریشر مشینوں کا تعارف۔ نتیجے کے طور پر، ذاتی اور صنعتی استعمال کے لیے مصنوعات کا متنوع انتخاب وجود میں آیا۔ ان میں کار کے اجزاء، گھریلو آلات، اور کھیلنے کی چیزیں شامل تھیں۔
- تکنیکی اختراعات:دہائیوں کے دوران، انجکشن مولڈنگ ٹیکنالوجی تیار ہوتی رہی۔ 1960 کی دہائی میں، کمپیوٹر کے زیر کنٹرول مشینیں ابھریں، جو مولڈنگ کے عمل پر درست کنٹرول کو قابل بناتی ہیں۔ 1980 کی دہائی میں ہاٹ رنر سسٹمز کے تعارف نے فضلہ کو کم کیا اور رنرز اور اسپروز کی ضرورت کو ختم کرکے کارکردگی کو بہتر بنایا۔ حالیہ برسوں میں، آٹومیشن، روبوٹکس، اور 3D پرنٹنگ کی ترقی نے انجیکشن مولڈنگ کی صنعت میں مزید انقلاب برپا کر دیا ہے، جس سے پیچیدہ ڈیزائنوں کو قابل بنایا گیا ہے اور پیداوار کے وقت کو کم کیا گیا ہے۔
- پائیداری اور ری سائیکلنگ:بڑھتے ہوئے ماحولیاتی خدشات کے ساتھ، انجیکشن مولڈنگ انڈسٹری نے پائیداری کے اقدامات کو اپنا لیا ہے۔ مینوفیکچررز نے جیواشم ایندھن پر مبنی مواد پر انحصار کو کم کرتے ہوئے، بائیو بیسڈ اور ری سائیکل تھرمو پلاسٹک تیار کیا ہے۔ مزید برآں، بہتر ری سائیکلنگ ٹیکنالوجیز نے صارفین کے بعد اور صنعتی فضلہ کے بعد کی دوبارہ پروسیسنگ کو قابل بنایا ہے، جس سے تھرمو پلاسٹک انجیکشن مولڈنگ کے ماحولیاتی اثرات کو کم کیا جا سکتا ہے۔
- مستقبل کے امکانات:تھرمو پلاسٹک انجیکشن مولڈنگ کا مستقبل امید افزا لگتا ہے۔ صنعت چھوٹے اجزاء کے لیے مائیکرو انجیکشن مولڈنگ، پیچیدہ حصوں کے لیے ملٹی میٹریل اور اوور مولڈنگ تکنیک، اور عمل کی نگرانی اور اصلاح کے لیے ذہین ٹیکنالوجیز کو مربوط کرنے جیسی اختراعات کی تلاش کر رہی ہے۔ مزید برآں، محققین بائیوڈیگریڈیبل مواد اور اضافی مینوفیکچرنگ میں پیشرفت کی توقع کرتے ہیں کہ وہ فیلڈ میں انقلاب برپا کریں گے، جس سے انجیکشن مولڈنگ اور بھی زیادہ پائیدار اور ورسٹائل بن جائے گی۔
تھرمو پلاسٹک انجکشن مولڈنگ کے فوائد
تھرمو پلاسٹک انجکشن مولڈنگ مینوفیکچررز کے لیے بے شمار فوائد پیش کرتی ہے۔ یہ مختلف خصوصیات کے ساتھ پیچیدہ اور پیچیدہ ڈیزائن کی اجازت دیتا ہے، ڈیزائن لچک فراہم کرتا ہے. یہ عمل لاگت سے موثر ہے، مواد کے فضلے کو کم کرتا ہے اور یونٹ کے اخراجات کو کم کرتا ہے۔ تھرمو پلاسٹک انجیکشن مولڈنگ متعدد مواد کی حمایت کرتی ہے، مختلف ایپلی کیشنز کے لیے استعداد فراہم کرتی ہے۔
- ڈیزائن لچک:تھرمو پلاسٹک انجیکشن مولڈنگ پیچیدہ اور پیچیدہ ڈیزائنوں کی اجازت دیتی ہے جیسے انڈر کٹس، پتلی دیواروں اور مختلف موٹائیوں کے ساتھ، ڈیزائنرز کو بے پناہ آزادی فراہم کرتے ہیں۔
- کارکردگی کا تخمینہ: یہ عمل انتہائی موثر ہے، مواد کے فضلے کو کم کرتا ہے اور یونٹ کے اخراجات کو کم کرتا ہے۔ متعدد حصوں کی بیک وقت مولڈنگ اور تیز پیداواری سائیکل لاگت کی بچت میں اہم کردار ادا کرتے ہیں۔
- مواد کی استعداد: تھرمو پلاسٹک انجیکشن مولڈنگ مواد کی ایک وسیع رینج کو سپورٹ کرتی ہے، جس سے مینوفیکچررز کو ہر ایپلیکیشن کے لیے موزوں ترین آپشن کا انتخاب کرنے میں مدد ملتی ہے، بشمول سخت یا لچکدار، شفاف یا مبہم، اور کیمیائی طور پر مزاحم مواد۔
- طاقت اور استحکام:انجکشن مولڈ تھرموپلاسٹک بہترین میکانی خصوصیات کی نمائش کر سکتے ہیں، جیسے کہ اعلی طاقت، سختی، اور اثر مزاحمت۔ کمک کے اختیارات، جیسے شیشے یا کاربن فائبر، ان خصوصیات کو مزید بڑھاتے ہیں۔
- مستقل مزاجی اور معیار:انجیکشن مولڈنگ مستقل جزوی معیار اور جہتی درستگی کو یقینی بناتی ہے، سخت رواداری اور قابل اعتماد مصنوعات فراہم کرتی ہے۔ یہ عمل ایک ہموار اور یکساں سطح کی تکمیل بھی فراہم کرتا ہے، اضافی فنشنگ آپریشنز کی ضرورت کو ختم کرتا ہے۔
- توسیع پذیری اور بڑے پیمانے پر پیداوار:انجکشن مولڈنگ کم سے زیادہ حجم تک توسیع پذیر ہے، جس سے یہ بڑے پیمانے پر پیداوار کے لیے موزوں ہے۔ ایک بار جب مینوفیکچررز سڑنا بناتے ہیں، تو وہ کم سے کم تغیرات کے ساتھ ایک جیسے حصوں کی بڑی مقدار تیار کر سکتے ہیں۔
- انضمام اور اسمبلی:انجیکشن سے ڈھلے ہوئے حصے ایک سے زیادہ اجزاء کو ایک ٹکڑے میں شامل کر سکتے ہیں، اضافی اسمبلی کے عمل کی ضرورت کو کم کر سکتے ہیں۔ یہ انضمام مصنوعات کی کارکردگی کو بڑھاتا ہے، اسمبلی کا وقت کم کرتا ہے، اور اخراجات کو کم کرتا ہے۔
- استحکام:انجیکشن مولڈنگ انڈسٹری پائیداری پر بڑھتی ہوئی توجہ دکھا رہی ہے۔ بائیو بیسڈ اور ری سائیکل مواد کی دستیابی ماحول دوست مصنوعات تیار کرنے کی اجازت دیتی ہے۔ تھرموپلاسٹک کا موثر مادی استعمال اور ری سائیکلیبلٹی ایک سبز مینوفیکچرنگ کے عمل میں حصہ ڈالتی ہے۔
ان فوائد نے اسے مختلف صنعتوں میں وسیع پیمانے پر اپنایا ہوا مینوفیکچرنگ طریقہ بنا دیا ہے، جو پیچیدہ مصنوعات کی ضروریات کے لیے اعلیٰ معیار، لاگت سے موثر اور ماحول دوست حل فراہم کرتا ہے۔
تھرمو پلاسٹک انجکشن مولڈنگ کے نقصانات
اگرچہ تھرمو پلاسٹک انجیکشن مولڈنگ بہت سے فوائد پیش کرتا ہے، اس کے کئی نقصانات بھی ہیں۔ مینوفیکچررز کو ان عوامل کا بغور جائزہ لینے اور ان کے فوائد کے مقابلے میں وزن کرنے کی ضرورت ہے تاکہ ان کی مخصوص ایپلی کیشنز کے لیے تھرمو پلاسٹک انجیکشن مولڈنگ کی موزوںیت کا تعین کیا جا سکے۔
- اعلیٰ ابتدائی سرمایہ کاری: تھرمو پلاسٹک انجیکشن مولڈنگ آپریشن کو ترتیب دینے کے لیے مولڈ ڈیزائن اور فیبریکیشن اور خصوصی مشینری کی خریداری میں اہم ابتدائی سرمایہ کاری کی ضرورت ہوتی ہے۔ سانچوں کی تخلیق اور ٹولنگ سے وابستہ اخراجات کافی ہوسکتے ہیں، خاص طور پر پیچیدہ اور پیچیدہ ڈیزائنوں کے لیے۔
- ڈیزائن کی حدود: جبکہ تھرمو پلاسٹک انجیکشن مولڈنگ ڈیزائن لچک پیش کرتی ہے، کچھ حدود موجود ہیں۔ مثال کے طور پر، پورے حصے میں دیوار کی یکساں موٹائی کو حاصل کرنا مشکل ہو سکتا ہے، جس کی وجہ سے مواد کی تقسیم میں تغیرات اور ممکنہ ساختی کمزوریاں پیدا ہوتی ہیں۔ مزید برآں، انڈر کٹس یا پیچیدہ جیومیٹریوں کی موجودگی کے لیے اضافی مولڈ فیچرز یا سیکنڈری آپریشنز، بڑھتے ہوئے لاگت اور پیداواری وقت کی ضرورت پڑ سکتی ہے۔
- لانگ لیڈ ٹائمز:انجیکشن مولڈنگ کے لیے سانچوں کو ڈیزائن کرنے اور بنانے کا عمل وقت طلب ہو سکتا ہے، جس کی وجہ سے پروڈکٹ کی نشوونما کے لیے لیڈ ٹائم زیادہ ہوتا ہے۔ ڈیزائن کی تکرار کا عمل، مولڈ پروڈکشن، اور ٹیسٹنگ مجموعی پروڈکشن ٹائم لائن میں اہم وقت کا اضافہ کر سکتی ہے، جو سخت ڈیڈ لائن والے پروجیکٹس کے لیے موزوں نہیں ہو سکتی۔
- مواد کے انتخاب کی پابندیاں:اگرچہ تھرمو پلاسٹک انجکشن مولڈنگ مواد کی ایک وسیع رینج کو سپورٹ کرتی ہے، لیکن کچھ حدود اور رکاوٹیں ہیں۔ کچھ مواد میں پروسیسنگ کے مخصوص تقاضے یا محدود دستیابی ہو سکتی ہے، جو کسی خاص ایپلی کیشن کے لیے ڈیزائن کے انتخاب اور مواد کے انتخاب کو متاثر کرتی ہے۔
- حصہ سائز کی حدود:انجکشن مولڈنگ مشینوں کے سائز کی حدود ہوتی ہیں، دونوں ڈیوائس کے جسمانی سائز اور ان کے سائز کے مولڈ کے لحاظ سے جو وہ ایڈجسٹ کر سکتے ہیں۔ بڑے حصوں کی تیاری کے لیے خصوصی آلات یا متبادل مینوفیکچرنگ طریقوں کی ضرورت پڑ سکتی ہے۔
- ماحول کا اثر:جب کہ صنعت پائیداری کی طرف کام کر رہی ہے، تھرمو پلاسٹک انجیکشن مولڈنگ کا عمل اب بھی فضلہ مواد پیدا کرتا ہے، بشمول سکریپ اور اسپروز۔ ماحولیاتی اثرات کو کم سے کم کرنے کے لیے ان مواد کو مناسب طریقے سے ضائع کرنا اور ری سائیکل کرنا ضروری ہے۔
- عمل کی اصلاح کی پیچیدگی:تھرمو پلاسٹک انجیکشن مولڈنگ کے لیے بہترین عمل کے پیرامیٹرز کو حاصل کرنا پیچیدہ اور وقت طلب ہو سکتا ہے۔ مینوفیکچررز کو لازمی طور پر درجہ حرارت، دباؤ، ٹھنڈک کی شرحوں، اور سائیکل کے اوقات کو احتیاط سے کنٹرول اور بہتر بنانا چاہیے تاکہ حصے کے مستقل معیار کو یقینی بنایا جا سکے اور نقائص کو کم کیا جا سکے۔
انجیکشن مولڈنگ میں استعمال ہونے والی تھرمو پلاسٹک کی اقسام
یہ عام طور پر انجیکشن مولڈنگ میں استعمال ہونے والے تھرمو پلاسٹک کی چند مثالیں ہیں۔ ہر مواد میں منفرد خصوصیات ہیں، جو اسے طاقت، لچک، کیمیائی مزاحمت، شفافیت اور لاگت کی بنیاد پر مخصوص ایپلی کیشنز کے لیے موزوں بناتے ہیں۔ مینوفیکچررز کو ان خصوصیات اور تقاضوں پر غور کرنا چاہیے جب ان کے انجیکشن مولڈنگ پروجیکٹس کے لیے مناسب تھرمو پلاسٹک کا انتخاب کریں۔
- پولی پروپیلین (پی پی):پولی پروپیلین ایک ورسٹائل تھرمو پلاسٹک ہے جو عام طور پر انجیکشن مولڈنگ میں استعمال ہوتا ہے۔ یہ بہترین کیمیائی مزاحمت، کم کثافت، اور اچھی اثر قوت پیش کرتا ہے۔ پی پی (پولی پروپیلین) میں پیکیجنگ، آٹوموٹیو اجزاء، گھریلو ایپلائینسز، اور طبی آلات میں وسیع پیمانے پر ایپلی کیشنز ہیں۔
- Polyethylene (PE):پولی تھیلین انجیکشن مولڈنگ میں ایک اور وسیع پیمانے پر استعمال ہونے والا تھرمو پلاسٹک ہے۔ یہ مختلف شکلوں میں دستیاب ہے، جیسے ہائی ڈینسٹی پولیتھیلین (HDPE) اور کم کثافت والی پولیتھیلین (LDPE)۔ PE اچھی کیمیائی مزاحمت، سختی اور لچک پیش کرتا ہے، جو اسے بوتلوں، کنٹینرز اور پائپوں کے لیے موزوں بناتا ہے۔
- پولیسٹیرین (PS):پولیسٹیرین ایک ورسٹائل تھرمو پلاسٹک ہے جو اس کی وضاحت، سختی، اور قابل استطاعت کے لیے جانا جاتا ہے۔ یہ پیکیجنگ، اشیائے صرف اور ڈسپوزایبل مصنوعات میں عام استعمال پایا جاتا ہے۔ PS (پولیسٹیرین) فوری پروسیسنگ کی اجازت دیتا ہے اور اچھی جہتی استحکام فراہم کرتا ہے، لیکن یہ ٹوٹنے والا اور ماحولیاتی تناؤ کے ٹوٹنے کے لیے حساس ہوسکتا ہے۔
- Acrylonitrile Butadiene Styrene (ABS): ABS ایک مقبول تھرمو پلاسٹک ہے جو اپنے بہترین اثر مزاحمت اور استحکام کے لیے جانا جاتا ہے۔ یہ ایکریلونائٹرائل، بوٹاڈین، اور اسٹائرین کی خصوصیات کو یکجا کر کے آٹوموٹو پرزوں، الیکٹرانک ہاؤسنگز اور کھلونوں کے لیے موزوں ایک ورسٹائل مواد تیار کرتا ہے۔
- پولی وینائل کلورائد (PVC): پیویسی ایک وسیع پیمانے پر استعمال ہونے والا تھرمو پلاسٹک ہے جو اپنی بہترین کیمیائی مزاحمت، استحکام اور کم قیمت کے لیے جانا جاتا ہے۔ یہ سخت یا لچکدار ہو سکتا ہے اس پر منحصر ہے کہ استعمال کی گئی تشکیل اور اضافی اشیاء۔ PVC (polyvinyl chloride) تعمیرات، برقی موصلیت، صحت کی دیکھ بھال کی مصنوعات، اور پیکیجنگ میں عام استعمال پایا جاتا ہے۔
- پولی کاربونیٹ (PC): پولی کاربونیٹ ایک شفاف تھرموپلاسٹک ہے جس میں غیر معمولی اثر اور زیادہ گرمی کی مزاحمت ہے۔ یہ ایپلی کیشنز میں عام استعمال کو تلاش کرتا ہے جس میں آپٹیکل وضاحت کی ضرورت ہوتی ہے، جیسے آٹوموٹو اجزاء، حفاظتی ہیلمیٹ، اور الیکٹرانک ڈسپلے۔
- نایلان (پولیامائڈ):نایلان ایک مضبوط اور پائیدار تھرمو پلاسٹک ہے جو اپنی بہترین مکینیکل خصوصیات اور کیمیائی مزاحمت کے لیے جانا جاتا ہے۔ یہ ایپلی کیشنز میں عام استعمال کو تلاش کرتا ہے جو اعلی طاقت کا مطالبہ کرتی ہے، جیسے آٹوموٹو پرزے، صنعتی اجزاء، اور صارفی سامان۔
- Polyethylene Terephthalate (PET):پی ای ٹی بوتلیں، کنٹینرز، اور پیکیجنگ مواد تیار کرنے کے لیے ایک مقبول تھرمو پلاسٹک ہے۔ یہ اچھی وضاحت، کیمیائی مزاحمت، اور رکاوٹ کی خصوصیات پیش کرتا ہے، جو اسے کھانے اور مشروبات کے استعمال کے لیے موزوں بناتا ہے۔
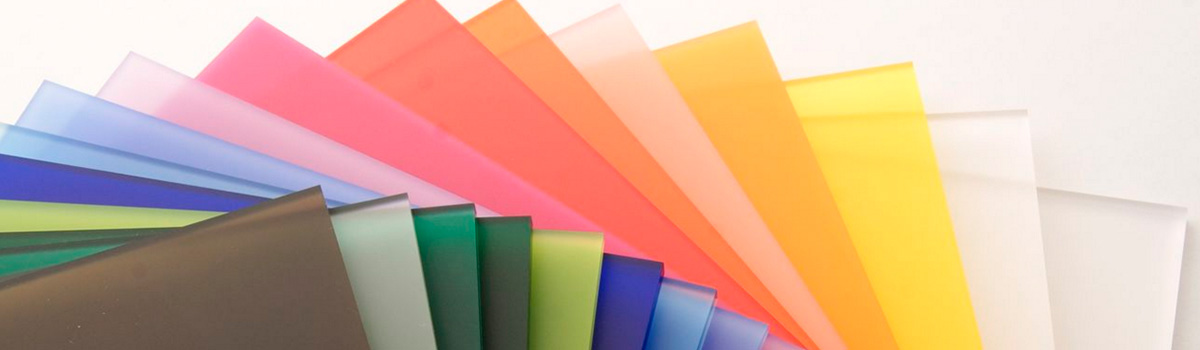
انجیکشن مولڈنگ میں استعمال ہونے والے تھرمو پلاسٹک کی خصوصیات
تھرمو پلاسٹک کی یہ خصوصیات مخصوص انجیکشن مولڈنگ ایپلی کیشنز کے لیے ان کی مناسبیت کا تعین کرنے میں اہم کردار ادا کرتی ہیں۔ مینوفیکچررز کو ان خصوصیات پر احتیاط سے غور کرنا چاہیے اور مطلوبہ کارکردگی، ماحولیاتی حالات اور لاگت کی ضروریات کی بنیاد پر مناسب تھرمو پلاسٹک کا انتخاب کرنا چاہیے۔
- مشینی خصوصیات:انجیکشن مولڈنگ میں استعمال ہونے والے تھرموپلاسٹک مختلف مکینیکل خصوصیات کو ظاہر کر سکتے ہیں، بشمول تناؤ کی طاقت، اثر مزاحمت، اور لچکدار طاقت۔ یہ خصوصیات مواد کی لاگو قوتوں کو برداشت کرنے کی صلاحیت اور مختلف ایپلی کیشنز میں اس کی مجموعی استحکام کا تعین کرتی ہیں۔
- کیمیائی مزاحمت:انجیکشن مولڈنگ میں استعمال ہونے والے بہت سے تھرموپلاسٹک کیمیکلز، سالوینٹس اور تیل کے خلاف قابل ذکر مزاحمت رکھتے ہیں۔ یہ خاصیت ان ایپلی کیشنز کے لیے بہت اہم ہے جس میں سخت ماحول یا سنکنرن مادوں کی نمائش شامل ہو۔
- تھرمل استحکام:تھرموپلاسٹک کے تھرمل استحکام سے مراد ان کی قابل قدر انحطاط کے بغیر بلند درجہ حرارت کو برداشت کرنے کی صلاحیت ہے۔ کچھ تھرموپلاسٹک بہترین گرمی کے خلاف مزاحمت کا مظاہرہ کرتے ہیں، جس سے وہ اعلی درجہ حرارت پر بھی اپنی مکینیکل خصوصیات کو برقرار رکھ سکتے ہیں۔
- بجلی کی خصوصیات:انجیکشن مولڈنگ میں استعمال ہونے والے تھرموپلاسٹک میں مخصوص برقی خصوصیات ہوسکتی ہیں، بشمول برقی موصلیت، چالکتا، یا ڈائی الیکٹرک طاقت۔ یہ خصوصیات الیکٹریکل اور الیکٹرانک صنعتوں میں ایپلی کیشنز کے لیے ضروری ہیں، جہاں مواد کو قابل اعتماد برقی کارکردگی فراہم کرنا ضروری ہے۔
- شفافیت اور وضاحت:بعض تھرمو پلاسٹک، جیسے پولی کاربونیٹ اور پی ای ٹی، بہترین شفافیت اور وضاحت پیش کرتے ہیں، انہیں ان ایپلی کیشنز کے لیے موزوں بناتے ہیں جن کے لیے آپٹیکل خصوصیات کی ضرورت ہوتی ہے۔ مینوفیکچررز عام طور پر ان مواد کو شفاف کھڑکیوں، لینز اور ڈسپلے جیسی مصنوعات میں استعمال کرتے ہیں۔
- لچک اور سختی: لچک اور سختی ان ایپلی کیشنز میں استعمال ہونے والی تھرمو پلاسٹک کی ضروری خصوصیات ہیں جن کے لیے اثر مزاحمت اور استحکام کی ضرورت ہوتی ہے۔ کچھ تھرمو پلاسٹک، جیسے ABS اور نایلان، بہترین سختی پیش کرتے ہیں، جس سے وہ بغیر ٹوٹے بار بار ہونے والے اثرات کو برداشت کر سکتے ہیں۔
- جہتی استحکام:جہتی استحکام سے مراد درجہ حرارت کی تبدیلیوں سمیت مختلف حالات میں اپنی شکل اور سائز کو برقرار رکھنے کی تھرمو پلاسٹک کی صلاحیت ہے۔ اچھی جہتی استحکام کے ساتھ مواد مسلسل حصہ کے طول و عرض کو یقینی بناتا ہے، وارپنگ یا مسخ ہونے کے خطرے کو کم کرتا ہے۔
- کیمیائی مطابقت:تھرموپلاسٹک کی کیمیائی مطابقت سے مراد مختلف کیمیکلز، بشمول تیزاب، اڈے اور سالوینٹس کے ساتھ انحطاط یا تعامل کے خلاف مزاحمت کرنے کی ان کی صلاحیت ہے۔ بہترین کارکردگی کو یقینی بنانے کے لیے، ایک ایسے تھرمو پلاسٹک کا انتخاب کرنا جو مخصوص کیمیائی ماحول کا مقابلہ کر سکے جس کا اسے مطلوبہ استعمال میں سامنا کرنا پڑے گا۔
- کثافت: تھرموپلاسٹک کی موٹائی مختلف ہوتی ہے، جو ان کے وزن اور حصہ کی مجموعی خصوصیات کو متاثر کر سکتی ہے۔ کم کثافت والے مواد، جیسے پولیتھیلین، ہلکے وزن کے حل پیش کرتے ہیں، جبکہ زیادہ کثافت والے مواد، جیسے پولی پروپیلین، اضافی طاقت اور سختی فراہم کرتے ہیں۔
انجکشن مولڈنگ کا عمل: مرحلہ وار
انجیکشن مولڈنگ کا عمل ان مراحل کی پیروی کرتا ہے، جس سے اعلیٰ معیار کے تھرموپلاسٹک حصوں کی موثر اور درست پیداوار ہوتی ہے۔ ہر قدم پر محتاط کنٹرول اور نگرانی کی ضرورت ہوتی ہے تاکہ حصے کے جہتوں، مادی خصوصیات اور مجموعی معیار کو یقینی بنایا جا سکے۔
- مولڈ ڈیزائن اور فیبریکیشن: انجیکشن مولڈنگ کے عمل میں پہلا قدم مولڈ کا ڈیزائن اور فیبریکیشن ہے۔ مینوفیکچررز کو مطلوبہ حصے کی وضاحتیں حاصل کرنے کے لیے ایک درست اور تفصیلی مولڈ ڈیزائن بنانا چاہیے۔ اس کے بعد مینوفیکچررز مختلف تکنیکوں، جیسے CNC یا الیکٹریکل ڈسچارج مشیننگ (EDM) کا استعمال کرتے ہوئے سڑنا بناتے ہیں۔
- مواد کی تیاری: اگلا مرحلہ مولڈ کے تیار ہونے کے بعد تیاری ہے۔ تھرمو پلاسٹک کے چھرے یا دانے دار مطلوبہ مادی خصوصیات کی بنیاد پر منتخب کیے جاتے ہیں اور اسے ہوپر میں پگھلا دیا جاتا ہے۔ آپریٹرز پھر مواد کو انجیکشن مولڈنگ مشین کے بیرل میں ڈالتے ہیں، جہاں یہ پگھلنے اور ہم آہنگی سے گزرتا ہے۔
- انجکشن:انجیکشن کے مرحلے کے دوران، آپریٹرز پگھلے ہوئے تھرمو پلاسٹک کو ہائی پریشر کے تحت مولڈ گہا میں انجیکشن لگاتے ہیں۔ مشین کا انجیکشن یونٹ پگھلے ہوئے مواد کو نوزل کے ذریعے اور سانچے میں دھکیلتا ہے۔ مواد مولڈ گہا کو بھرتا ہے، مطلوبہ حصے کی شکل اختیار کرتا ہے۔
- ٹھنڈک اور استحکام:سڑنا بھرنے کے بعد، آپریٹرز پگھلے ہوئے پلاسٹک کو ٹھنڈا اور ٹھنڈا ہونے دیتے ہیں۔ جہتی استحکام اور مناسب حصے کی تشکیل کے لیے کولنگ بہت ضروری ہے۔ آپریٹرز کولنگ کے عمل کو مولڈ کے اندر چینلز کے ذریعے یا کولنگ پلیٹوں کا استعمال کرکے سرکولیشن کر سکتے ہیں۔
- مولڈ کھولنا اور نکالنا:آپریٹرز مولڈ کو کھولتے ہیں اور پلاسٹک کے مضبوط ہونے کے بعد مولڈ کیویٹی سے حصہ نکال دیتے ہیں۔ مشین کے اندر انجیکشن سسٹم پنوں، ایجیکٹر پلیٹوں، یا ہوائی دھماکوں کا استعمال کرتے ہوئے علاقے کو سڑنا سے ہٹاتا ہے۔ پھر سڑنا اگلے انجیکشن سائیکل کے لیے تیار ہے۔
- پوسٹ پروسیسنگ: نکالنے کے بعد، حصہ پوسٹ پروسیسنگ آپریشنز سے گزر سکتا ہے، جیسے تراشنا، ڈیبرنگ، یا سطح کو ختم کرنا۔ یہ اقدامات اضافی مواد کو ہٹانے، کھردرے کناروں کو ہموار کرنے اور حصے کی حتمی شکل کو بہتر بنانے میں مدد کرتے ہیں۔
- معیار کی معائنہ: آخری مرحلے میں انجکشن والے حصوں کا معیار کے لیے معائنہ کرنا اور یہ یقینی بنانا شامل ہے کہ وہ مخصوص ضروریات کو پورا کرتے ہیں۔ کوالٹی کنٹرول کی مختلف تکنیکیں، بشمول جہتی پیمائش، بصری معائنہ، اور فنکشنل ٹیسٹنگ، کو اس حصے کے معیار اور سالمیت کی تصدیق کے لیے استعمال کیا جا سکتا ہے۔
- ری سائیکلنگ اور مواد کا دوبارہ استعمال:انجیکشن مولڈنگ کے دوران پیدا ہونے والا کوئی بھی اضافی یا سکریپ مواد ری سائیکل اور دوبارہ استعمال کیا جا سکتا ہے۔ نئے تھرمو پلاسٹک مواد کے استعمال کو کم کرنے سے فضلہ کو کم کرنے اور پائیداری کو بہتر بنانے میں مدد ملتی ہے۔
انجکشن مولڈنگ میں استعمال ہونے والا سامان
یہ سازوسامان اجزاء انجیکشن مولڈنگ کے عمل میں سہولت فراہم کرتے ہیں، تھرمو پلاسٹک مواد کو پگھلنے اور انجیکشن لگانے سے لے کر آخری حصے کو شکل دینے، ٹھنڈا کرنے اور نکالنے تک۔ ان آلات کے اجزاء کا مناسب آپریشن اور دیکھ بھال موثر، اعلیٰ معیار کے انجیکشن مولڈنگ کی پیداوار کے حصول کے لیے بہت ضروری ہے۔
- انجیکشن مولڈنگ مشین:انجیکشن مولڈنگ میں بنیادی سامان تھرمو پلاسٹک مواد کو پگھلانے، اسے مولڈ میں انجیکشن لگانے اور اس عمل کو کنٹرول کرنے کا ذمہ دار ہے۔
- سڑنا: پلاسٹک کے حصے کی مطلوبہ شکل اور خصوصیات بنانے کے لیے اپنی مرضی کے مطابق ڈیزائن کیا گیا مولڈ، دو حصوں، گہا اور کور پر مشتمل ہے۔ آپریٹرز اسے انجیکشن مولڈنگ مشین کے کلیمپنگ یونٹ پر لگاتے ہیں۔
- ہوپر:وہ کنٹینر جو تھرمو پلاسٹک مواد کو گولی یا دانے دار شکل میں رکھتا ہے اور اسے پگھلنے اور انجیکشن کے لیے انجیکشن مولڈنگ مشین کے بیرل میں ڈالتا ہے۔
- بیرل اور سکرو: بیرل، ایک بیلناکار چیمبر، تھرمو پلاسٹک مواد کو پگھلتا اور ہم آہنگ کرتا ہے کیونکہ اس کے اندر سکرو گھومتا ہے تاکہ مواد کو پگھلنے، مکس کرنے اور معیاری بنانے کے لیے۔
- حرارتی اور کولنگ سسٹم:انجکشن مولڈنگ مشینوں میں حرارتی عناصر ہوتے ہیں، جیسے برقی ہیٹر یا گرم تیل کا استعمال کرنے والے ہیٹر، بیرل کا درجہ حرارت بڑھانے کے لیے، اور کولنگ سسٹم، جیسے پانی یا تیل کی گردش، سڑنا کو ٹھنڈا کرنے اور پلاسٹک کے حصے کو ٹھوس کرنے کے لیے۔
- ایجیکٹر سسٹم:ٹھوس ہونے کے بعد مولڈ گہا سے ڈھالے ہوئے حصے کو ہٹاتا ہے، عام طور پر مولڈ کھولنے کے دوران ایجیکٹر پن، پلیٹوں یا ہوا کے دھماکوں کا استعمال کرتے ہیں۔
- کنٹرول سسٹم:انجیکشن مولڈنگ کے عمل کے مختلف پیرامیٹرز کی نگرانی اور کنٹرول کرتا ہے، جس سے آپریٹرز کو انجکشن کی رفتار، درجہ حرارت، دباؤ، اور ٹھنڈک کا وقت جیسے پیرامیٹرز کو سیٹ اور ایڈجسٹ کرنے کی اجازت ملتی ہے۔
انجکشن مولڈنگ مشینیں: اقسام اور خصوصیات
انجیکشن مولڈنگ مشین کی ہر قسم کی اپنی خصوصیات اور فوائد ہیں، جو مینوفیکچررز کو اپنی مخصوص پیداواری ضروریات کے لیے موزوں ترین ڈیوائس کا انتخاب کرنے کی اجازت دیتے ہیں۔
- ہائیڈرولک انجکشن مولڈنگ مشینیں: یہ مشینیں ہائیڈرولک سسٹم کا استعمال کرتی ہیں تاکہ پگھلے ہوئے پلاسٹک کو سانچے میں داخل کرنے کے لیے ضروری دباؤ پیدا کیا جا سکے۔ وہ اپنی ہائی کلیمپنگ فورس، عین مطابق کنٹرول، اور مختلف تھرمو پلاسٹک کو سنبھالنے میں استعداد کے لیے مشہور ہیں۔ ہائیڈرولک مشینیں بڑے پیمانے پر پیداوار کے لیے موزوں ہیں اور پیچیدہ سانچوں کو ایڈجسٹ کر سکتی ہیں۔
- الیکٹرک انجکشن مولڈنگ مشینیں:الیکٹرک مشینیں مشین کے آپریشن کے لیے الیکٹرک سرو موٹرز کا استعمال کرتی ہیں، بشمول انجیکشن، کلیمپنگ، اور ایجیکٹر سسٹم۔ وہ ہائیڈرولک مشینوں کے مقابلے میں عین مطابق کنٹرول، توانائی کی کارکردگی، اور تیز تر رسپانس ٹائم پیش کرتے ہیں۔ الیکٹرک مشینیں درست مولڈنگ ایپلی کیشنز کے لیے مثالی ہیں جن کے لیے اعلیٰ تکرار اور درستگی کی ضرورت ہوتی ہے۔
- ہائبرڈ انجکشن مولڈنگ مشینیں:ہائبرڈ مشینیں ہائیڈرولک اور برقی آلات دونوں کے فوائد کو یکجا کرتی ہیں۔ وہ ہائیڈرولک اور الیکٹرک سروو سسٹمز کے امتزاج کا استعمال کرتے ہیں تاکہ اعلیٰ درستگی، توانائی کی بچت، اور لاگت کی تاثیر حاصل کی جا سکے۔ ہائبرڈ مشینیں ایپلی کیشنز کی ایک وسیع رینج کے لیے موزوں ہیں، جو کارکردگی اور آپریشنل اخراجات کے درمیان توازن فراہم کرتی ہیں۔
- دو پلیٹن انجیکشن مولڈنگ مشینیں: دو پلیٹن مشینوں میں مولڈ کو کلیمپ کرنے کے لیے دو الگ پلیٹوں کے ساتھ ایک منفرد ڈیزائن ہوتا ہے۔ یہ ڈیزائن بہتر استحکام، بہتر مولڈ سنکرونائزیشن فراہم کرتا ہے اور مولڈ کے بڑے سائز اور زیادہ کلیمپنگ فورسز کی اجازت دیتا ہے۔ دو پلیٹن مشینیں بڑے اور پیچیدہ حصوں کے لیے موزوں ہیں جن کے لیے عین مطابق مولڈنگ کی ضرورت ہوتی ہے۔
- کثیر اجزاء انجکشن مولڈنگ مشینیں:مینوفیکچررز ان مشینوں کو ایک ہی مولڈنگ سائیکل میں متعدد مواد یا رنگوں کے ساتھ پرزے تیار کرنے کے لیے ڈیزائن کرتے ہیں۔ ان میں مختلف انجیکشن یونٹس اور مولڈ ہوتے ہیں، جو مختلف مواد کے بیک وقت انجیکشن کو قابل بناتے ہیں۔ کثیر اجزاء والی مشینیں مختلف خصوصیات کے ساتھ پیچیدہ حصوں کی تیاری میں لچک اور کارکردگی پیش کرتی ہیں۔
- مائیکرو انجیکشن مولڈنگ مشینیں:خاص طور پر چھوٹے اور درست حصوں کی تیاری کے لیے ڈیزائن کیا گیا، مائیکرو انجیکشن مولڈنگ مشینیں ناقابل یقین حد تک اعلیٰ درستگی اور درستگی پیش کرتی ہیں۔ وہ سخت رواداری اور کم سے کم مادی فضلہ کے ساتھ پیچیدہ تفصیلات تیار کر سکتے ہیں۔ الیکٹرانکس، طبی آلات، اور مائیکرو آپٹکس عام طور پر مائیکرو انجیکشن مولڈنگ مشینوں کا استعمال کرتے ہیں۔
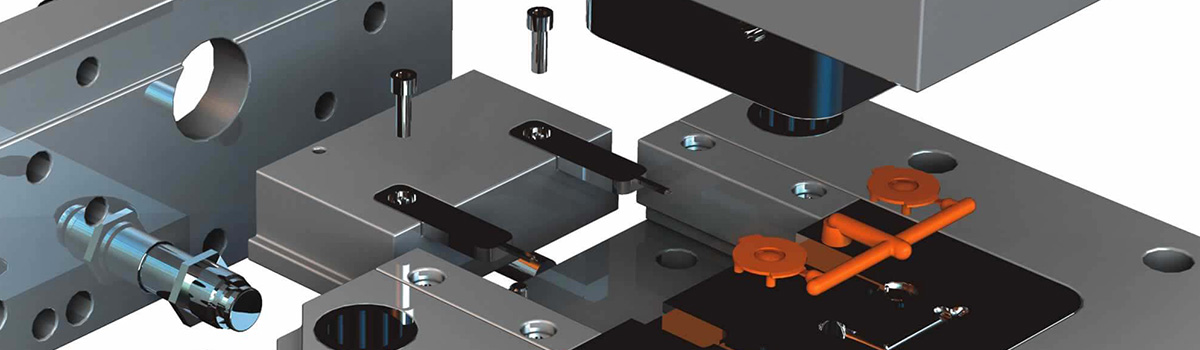
انجکشن مولڈنگ کے لیے مولڈ ڈیزائن کے تحفظات
انجکشن مولڈنگ کی کامیاب پیداوار کے لیے مولڈ ڈیزائن پر احتیاط ضروری ہے۔
- حصہ ڈیزائن:مولڈ ڈیزائن کو حصے کی مخصوص ضروریات کو ایڈجسٹ کرنا چاہئے، بشمول اس کی شکل، طول و عرض، اور فعال خصوصیات۔ مینوفیکچررز کو ڈرافٹ اینگلز، دیوار کی موٹائی، انڈر کٹس، اور کسی بھی ضروری عناصر پر مناسب طریقے سے غور کرنا چاہیے تاکہ اخراج میں آسانی اور حصے کے معیار کو یقینی بنایا جا سکے۔
- سڑنا مواد: استحکام، جہتی استحکام، اور گرمی کی مزاحمت کے حصول کے لیے مولڈ مواد کا انتخاب اہم ہے۔ عام مولڈ مواد میں سٹیل کے مرکب، ایلومینیم مرکب، اور ٹول اسٹیل شامل ہیں. مواد کا انتخاب پیداواری حجم، حصے کی پیچیدگی، اور متوقع آلے کی زندگی جیسے عوامل پر منحصر ہے۔
- کولنگ سسٹم:مناسب حصے کو مضبوط کرنے اور سائیکل کے وقت کو کم سے کم کرنے کے لیے موثر کولنگ ضروری ہے۔ مولڈ کے ڈیزائن میں کولنگ چینلز یا اسٹریٹجک پوزیشن والے انسرٹس کو شامل کرنا چاہیے تاکہ یکساں مولڈ کولنگ کو یقینی بنایا جا سکے۔ مناسب ٹھنڈک جنگ کے صفحے، سکڑنے اور جزوی نقائص کے خطرے کو کم کرتی ہے۔
- وینٹنگ:انجیکشن کے عمل کے دوران ہوا اور گیسوں کے فرار کی اجازت دینے کے لیے مناسب وینٹنگ ضروری ہے۔ ناکافی وینٹنگ گیس کے جال، جلنے کے نشان، یا نامکمل حصے کو بھرنے کا باعث بن سکتی ہے۔ مینوفیکچررز مولڈ ڈیزائن میں وینٹنگ گرووز، پن، یا دیگر میکانزم کو شامل کرکے وینٹنگ حاصل کرسکتے ہیں۔
- انجیکشن سسٹم:مولڈ ڈیزائن میں مولڈ گہا سے ڈھالے ہوئے حصے کو محفوظ طریقے سے اور مؤثر طریقے سے ہٹانے کے لیے ایک مؤثر انجیکشن سسٹم شامل ہونا چاہیے۔ انجیکشن سسٹم ایجیکٹر پن، آستین، یا دیگر میکانزم پر مشتمل ہو سکتا ہے، فنکشن یا اہم خصوصیات میں مداخلت سے بچنے کے لیے حکمت عملی کے مطابق پوزیشن میں ہے۔
- گیٹ ڈیزائن:گیٹ وہ جگہ ہے جہاں پگھلا ہوا پلاسٹک مولڈ گہا میں داخل ہوتا ہے۔ گیٹ کے ڈیزائن کو مناسب حصے کی بھرائی کو یقینی بنانا چاہیے، بہاؤ کی لکیروں کو کم سے کم کرنا چاہیے، اور وقت سے پہلے مواد کو جمنے سے روکنا چاہیے۔ معیاری گیٹ ڈیزائنز میں کنارے کے دروازے، ٹنل گیٹس، اور ہاٹ رنر سسٹم شامل ہیں، حصہ کی ضروریات اور مادی خصوصیات پر منحصر ہے۔
- علیحدگی کی لکیر:مولڈ ڈیزائن کو ایک مناسب علیحدگی کی لکیر کی وضاحت کرنی چاہئے، جو کہ وہ لائن ہے جہاں مولڈ کے دو حصے اکٹھے ہوتے ہیں۔ الگ کرنے والی لائن کی مناسب جگہ کا تعین کم سے کم فلیش اور الگ کرنے والی لائن کی مماثلت کو یقینی بناتا ہے اور موثر مولڈ اسمبلی کو سہولت فراہم کرتا ہے۔
- مولڈ کی بحالی اور خدمت کی اہلیت: مینوفیکچررز کو دیکھ بھال، مرمت اور مولڈ سروسنگ میں آسانی پر غور کرنا چاہیے۔ مولڈ کے اجزاء کو صفائی، معائنہ اور تبدیلی کے لیے آسانی سے قابل رسائی ہونا چاہیے۔ فوری تبدیلی کے داخلے یا ماڈیولر مولڈ ڈیزائن جیسی خصوصیات کو شامل کرنا مولڈ کی خدمت کو بہتر بنا سکتا ہے۔
انجکشن مولڈنگ میں استعمال ہونے والا مولڈ میٹریل
مولڈ میٹریل کے ماہرین کے ساتھ تعاون اور مولڈنگ ایپلی کیشن کی مخصوص ضروریات پر غور کرنے سے مولڈ کی بہترین کارکردگی اور جزوی معیار کو حاصل کرنے کے لیے موزوں ترین مواد کا تعین کرنے میں مدد مل سکتی ہے۔
- سٹیل مرکب: اسٹیل کے مرکب، جیسے کہ ٹول اسٹیل (مثال کے طور پر، P20، H13) اور سٹینلیس اسٹیل، عام طور پر انجیکشن مولڈنگ کے سانچوں کے لیے استعمال ہوتے ہیں کیونکہ ان کی بہترین پائیداری، گرمی کی مزاحمت، اور پہننے کی مزاحمت ہوتی ہے۔ یہ مواد انجیکشن مولڈنگ کے عمل میں اعلی درجہ حرارت اور دباؤ کو برداشت کر سکتے ہیں اور اعلی معیار کے پرزے تیار کرنے کے لیے اچھی جہتی استحکام پیش کرتے ہیں۔
- ایلومینیم مرکب:ایلومینیم کے مرکبات، جیسے 7075 اور 6061، ہلکے ہوتے ہیں اور اچھی تھرمل چالکتا پیش کرتے ہیں، جو انہیں ان سانچوں کے لیے موزوں بناتے ہیں جن میں موثر ٹھنڈک کی ضرورت ہوتی ہے۔ مینوفیکچررز اکثر ایلومینیم کے سانچوں کو پروٹو ٹائپنگ، کم حجم کی پیداوار، یا ایسی ایپلی کیشنز کے لیے استعمال کرتے ہیں جہاں وزن میں کمی ضروری ہے۔ تاہم، ایلومینیم کے سانچوں میں سٹیل کے مرکب کے مقابلے میں کم استحکام ہو سکتا ہے۔
- تانبے کے مرکب:تانبے کے مرکب، جیسے بیریلیم کاپر، اعلی تھرمل چالکتا اور اچھی مشینی صلاحیت کی نمائش کرتے ہیں۔ وہ ایسے سانچوں میں استعمال پاتے ہیں جن کو موثر ٹھنڈک کے لیے بہترین حرارت کی منتقلی کی ضرورت ہوتی ہے۔ تانبے کے مرکب ڈھلے ہوئے حصے سے گرمی کو تیزی سے ختم کرکے سائیکل کے اوقات کو کم کرنے میں مدد کر سکتے ہیں، جس کے نتیجے میں تیزی سے مضبوطی پیدا ہوتی ہے۔
- ٹول اسٹیل:ٹول اسٹیل، بشمول H13، S7، اور D2، اعلی کارکردگی والے ٹولنگ ایپلی کیشنز کے لیے ڈیزائن کیے گئے ہیں۔ یہ اسٹیل اعلی طاقت، سختی اور لباس مزاحمت کا مجموعہ پیش کرتے ہیں۔ ٹول اسٹیلز اعلی پروڈکشن والیوم، کھرچنے والے مواد، یا مولڈنگ حالات کا مطالبہ کرنے والے سانچوں کے مطابق ہیں۔
- نکل مرکب:نکل کے مرکب، جیسے انکونل اور ہیسٹیلوئے، اپنی غیر معمولی سنکنرن مزاحمت، اعلی درجہ حرارت کی طاقت، اور تھرمل استحکام کے لیے مشہور ہیں۔ مینوفیکچررز ان مرکب دھاتوں کو سانچوں میں استعمال کرتے ہیں جو سنکنرن مواد کو سنبھالتے ہیں یا انتہائی درجہ حرارت اور جارحانہ مولڈنگ ماحول کے خلاف مزاحمت کی ضرورت ہوتی ہے۔
- جامع مواد:جامع مواد، جیسے مضبوط پلاسٹک یا دھاتی داخلوں کے ساتھ مرکب، کبھی کبھار مخصوص مولڈنگ ایپلی کیشنز کے لیے استعمال ہوتے ہیں۔ یہ مواد خصوصیات کا توازن پیش کرتے ہیں، جیسے اعلی طاقت، تھرمل استحکام، اور کم وزن۔ جامع سانچے مخصوص پیداواری ضروریات کے لیے سرمایہ کاری مؤثر متبادل ہو سکتے ہیں۔
انجیکشن مولڈز کی اقسام
انجکشن مولڈنگ پلاسٹک کے پرزوں کے لیے ایک ورسٹائل اور بڑے پیمانے پر استعمال ہونے والا مینوفیکچرنگ عمل ہے۔
- دو پلیٹ مولڈ:دو پلیٹ مولڈ انجیکشن مولڈ کی سب سے عام قسم ہے۔ یہ دو پلیٹوں پر مشتمل ہوتا ہے، کیویٹی پلیٹ، اور کور پلیٹ، جو ڈھلے ہوئے حصے کے اخراج کی اجازت دینے کے لیے الگ ہوتی ہیں۔ کیویٹی پلیٹ میں مولڈ کی گہا کا حصہ ہوتا ہے، جبکہ کور پلیٹ کور سائیڈ پر مشتمل ہوتی ہے۔ مینوفیکچررز اپنے نسبتاً سادہ ڈیزائن کی وجہ سے پرزوں کی ایک وسیع رینج تیار کرنے کے لیے دو پلیٹ کے سانچوں کا استعمال کرتے ہیں۔
- تھری پلیٹ مولڈ:تھری پلیٹ مولڈ دو پلیٹ مولڈ کا جدید ورژن ہے۔ اس میں ایک اضافی پلیٹ، رنر، یا سپرو پلیٹ شامل ہے۔ رنر پلیٹ اسپریو، رنرز اور گیٹس کے لیے ایک الگ چینل بناتی ہے، جس سے ڈھلے ہوئے حصے کو آسانی سے ہٹایا جا سکتا ہے۔ مینوفیکچررز عام طور پر پیچیدہ گیٹنگ سسٹم کے ساتھ تفصیلات کے لیے تھری پلیٹ مولڈ استعمال کرتے ہیں یا جب ٹکڑے پر گیٹ ویسٹیج سے گریز کرنا ضروری ہوتا ہے۔
- گرم رنر مولڈ:رنر اور گیٹ سسٹم کو گرم رنر کے سانچوں میں گرم کیا جاتا ہے، جس سے ہر چکر کے دوران مواد کو مضبوط کرنے اور دوبارہ پگھلنے کی ضرورت ختم ہو جاتی ہے۔ ہاٹ رنر سسٹم گرم کئی گنا اور نوزلز پر مشتمل ہوتا ہے جو پلاسٹک کی پگھلی ہوئی حالت کو برقرار رکھتا ہے۔ ہاٹ رنر مولڈ فوائد کی پیشکش کرتے ہیں جیسے کہ سائیکل کا کم وقت، کم مواد کا فضلہ، اور گیٹ کے نشانات کو کم سے کم کرکے حصے کا معیار بہتر ہونا۔
- کولڈ رنر مولڈ: کولڈ رنر مولڈز میں روایتی رنر اور گیٹ سسٹم ہوتا ہے جہاں پگھلا ہوا پلاسٹک سرد رنر کے ذریعے بہتا ہے جو ہر چکر کے ساتھ مضبوط ہوتا ہے۔ آپریٹرز بعد میں ٹھوس رنرز کو ہٹا دیتے ہیں، جس کے نتیجے میں مادی فضلہ ہوتا ہے۔ مینوفیکچررز عام طور پر کم حجم کی پیداوار کے لیے پیچیدہ رنر مولڈ استعمال کرتے ہیں یا جب ان کے زیادہ سیدھے ڈیزائن کی وجہ سے مادی لاگت کم اہم ہوتی ہے۔
- مولڈ داخل کریں:انجیکشن مولڈنگ کے دوران مولڈ داخل کریں دھات یا پلاسٹک کے داخلوں کو مولڈ گہا میں شامل کریں۔ داخلوں کو مولڈ میں پہلے سے رکھا جا سکتا ہے یا خود کار طریقے سے داخل کیا جا سکتا ہے۔ یہ مولڈ اضافی اجزاء کو ضم کرنے یا مولڈ حصے میں عناصر کو تقویت دینے کی اجازت دیتا ہے، اس کی فعالیت یا طاقت کو بڑھاتا ہے۔
- اوور مولڈ: اوور مولڈنگ میں ایک مواد کو دوسرے پر ڈھالنا شامل ہوتا ہے، عام طور پر ایک سخت پلاسٹک سبسٹریٹ کو نرم ایلسٹومر یا تھرمو پلاسٹک کے ساتھ جوڑنا۔ یہ عمل ایک ہی سانچے میں متعدد مواد یا ساخت کے ساتھ حصوں کی تخلیق کی اجازت دیتا ہے، بہتر گرفت، کشن، یا جمالیاتی خصوصیات فراہم کرتا ہے۔
انجکشن مولڈنگ کے اخراجات کو متاثر کرنے والے عوامل
ان عوامل پر غور کرنے سے مینوفیکچررز کو انجیکشن مولڈنگ کی لاگت کا تخمینہ لگانے اور اسے بہتر بنانے میں مدد مل سکتی ہے، جس سے ان کی مخصوص پیداواری ضروریات کے لیے معیار، کارکردگی اور لاگت کی تاثیر کے درمیان توازن کو یقینی بنایا جا سکتا ہے۔
- حصہ کی پیچیدگی:حصے کے ڈیزائن کی پیچیدگی انجیکشن مولڈنگ کی لاگت کا تعین کرنے میں اہم کردار ادا کرتی ہے۔ پیچیدہ جیومیٹریوں، انڈر کٹس، پتلی دیواروں، یا پیچیدہ خصوصیات کے لیے اضافی ٹولنگ، خصوصی سانچوں، یا طویل سائیکلوں کی ضرورت پڑسکتی ہے، جس سے مجموعی مینوفیکچرنگ لاگت میں اضافہ ہوتا ہے۔
- مادی انتخاب:تھرمو پلاسٹک مواد کا انتخاب انجیکشن مولڈنگ لاگت کو متاثر کرتا ہے۔ مختلف مواد کی فی کلوگرام قیمتیں مختلف ہوتی ہیں، اور مواد کی دستیابی، خصوصیات، اور پروسیسنگ کی ضروریات جیسے عوامل مواد کی مجموعی لاگت کو متاثر کر سکتے ہیں۔
- ٹولنگ اور مولڈ ڈیزائن: انجکشن مولڈنگ کے اخراجات میں ابتدائی ٹولنگ اور مولڈ ڈیزائن کے اخراجات اہم ہیں۔ مولڈ کی پیچیدگی، گہاوں کی تعداد، مولڈ سائز، اور مولڈ میٹریل جیسے عوامل ٹولنگ اور مولڈ مینوفیکچرنگ کے اخراجات میں حصہ ڈالتے ہیں۔ زیادہ پیچیدہ سانچوں یا سانچوں کو جدید خصوصیات کی ضرورت ہوتی ہے جو پیشگی سرمایہ کاری کو بڑھا سکتے ہیں۔
- پیداوار کا حجم: پیداوار کا حجم انجیکشن مولڈنگ میں فی حصہ لاگت کو براہ راست متاثر کرتا ہے۔ اعلیٰ کتابوں کے نتیجے میں اکثر پیمانے کی معیشت ہوتی ہے، جس سے فی حصہ لاگت کم ہوتی ہے۔ اس کے برعکس، کم والیوم پروڈکشن رنز سیٹ اپ، ٹولنگ، اور مادی فضلہ کی وجہ سے زیادہ چارجز اٹھا سکتے ہیں۔
- سائیکل کا وقت: سائیکل کا وقت، جس میں کولنگ اور انجیکشن کے مراحل شامل ہیں، پیداواری صلاحیت اور مجموعی لاگت کو متاثر کرتا ہے۔ طویل سائیکل کے اوقات کا نتیجہ پیداواری پیداوار میں کمی اور ممکنہ طور پر زیادہ قیمتوں کا باعث بنتا ہے۔ مولڈ ڈیزائن، کولنگ سسٹم، اور عمل کے پیرامیٹرز کو بہتر بنانا سائیکل کے اوقات کو کم کر سکتا ہے اور کارکردگی کو بہتر بنا سکتا ہے۔
- معیار کے تقاضے:سخت معیار کے تقاضے یا مخصوص سرٹیفیکیشن انجیکشن مولڈنگ لاگت کو متاثر کر سکتے ہیں۔ درست رواداری، سطح کی تکمیل کی ضروریات، یا اضافی جانچ کے لیے دیگر وسائل، عمل، یا معائنہ کی ضرورت پڑ سکتی ہے، جس سے مجموعی لاگت میں اضافہ ہوتا ہے۔
- ثانوی آپریشنز:اگر مولڈ پارٹس کو پوسٹ پروسیسنگ آپریشنز جیسے اسمبلی، پینٹنگ، یا اضافی فنشنگ اقدامات کی ضرورت ہوتی ہے، تو یہ آپریشن انجیکشن مولڈنگ کی مجموعی لاگت میں اضافہ کر سکتے ہیں۔
- فراہم کنندہ اور مقام:انجیکشن مولڈنگ سپلائر کا انتخاب اور ان کا مقام لاگت کو متاثر کر سکتا ہے۔ لیبر کے اخراجات، اوور ہیڈز، لاجسٹکس، اور نقل و حمل کے اخراجات سپلائر کے مقام کی بنیاد پر مختلف ہوتے ہیں، جس سے مجموعی مینوفیکچرنگ لاگت متاثر ہوتی ہے۔
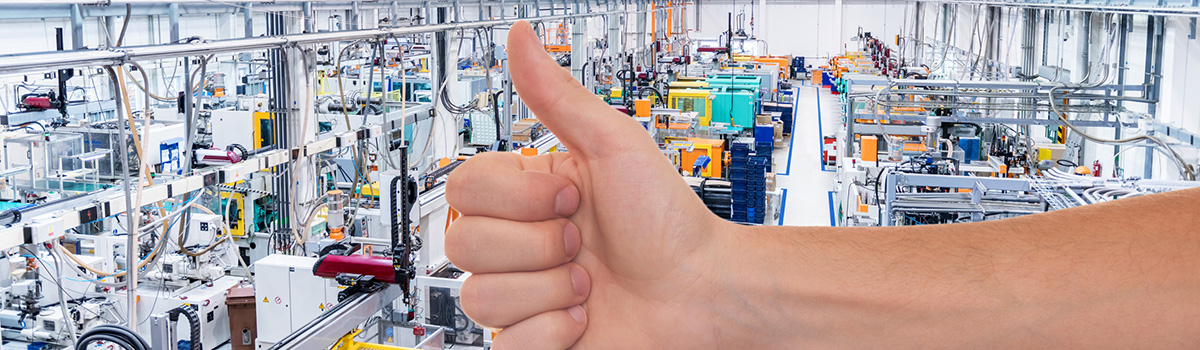
انجیکشن مولڈنگ میں کوالٹی کنٹرول
انجیکشن مولڈنگ کے پورے عمل میں کوالٹی کنٹرول کے مضبوط اقدامات کو لاگو کرنے سے ممکنہ نقائص، انحراف، یا عدم مطابقتوں کی شناخت اور ان کا ازالہ کرنے میں مدد ملتی ہے، اس بات کو یقینی بناتا ہے کہ اعلیٰ معیار کے پرزوں کی پیداوار جو گاہک کی تصریحات اور ضروریات کو پورا کرتی ہو۔
- عمل کی نگرانی: اہم عمل کے پیرامیٹرز کی مسلسل نگرانی، جیسے پگھلنے کا درجہ حرارت، انجیکشن پریشر، کولنگ ٹائم، اور سائیکل ٹائم، جزوی پیداوار میں مستقل مزاجی اور دہرائے جانے کو یقینی بناتا ہے۔ ریئل ٹائم مانیٹرنگ اور خودکار نظام متعین پیرامیٹرز سے تغیرات یا انحراف کا پتہ لگا سکتے ہیں، جس سے بروقت ایڈجسٹمنٹ اور عمل کے استحکام کو برقرار رکھا جا سکتا ہے۔
- معائنہ اور پیمائش:جہتی درستگی، جزوی معیار، اور تصریحات کی پابندی کی تصدیق کے لیے ڈھالے ہوئے حصوں کا باقاعدہ جائزہ اور پیمائش ضروری ہے۔ ہماری خدمات کوالٹی کنٹرول کے طریقوں کی ایک رینج کا احاطہ کرتی ہیں، جیسے طول و عرض کی پیمائش، سطح کے معیار کا تجزیہ کرنا، بصری معائنہ کرنا، اور فنکشنل ٹیسٹ کرنا۔ مختلف معائنہ کی تکنیکیں، جیسے کوآرڈینیٹ ماپنے والی مشینیں (سی ایم ایم) اور نظری اور بصری معائنہ کے نظام، درست تشخیص کے لیے استعمال کیے جاتے ہیں۔
- شماریاتی عمل کا کنٹرول (SPC): ایس پی سی میں انجیکشن مولڈنگ کے معیار کی نگرانی اور کنٹرول کے لیے عمل کے ڈیٹا کو اکٹھا کرنا اور تجزیہ کرنا شامل ہے۔ شماریاتی طریقے، جیسے کنٹرول چارٹس اور عمل کی صلاحیت کا تجزیہ، رجحانات کی شناخت کرنے، عمل کی مختلف حالتوں کا پتہ لگانے، اور یہ یقینی بنانے میں مدد کرتے ہیں کہ عمل متعین کنٹرول حدود کے اندر رہے۔ SPC مسائل کی فعال شناخت کو قابل بناتا ہے اور عمل کو بہتر بنانے میں سہولت فراہم کرتا ہے۔
- مادی جانچ: خام مال، جیسے تھرمو پلاسٹکس، ایڈیٹیو، اور رنگینٹس کی جانچ، ان کے معیار اور انجکشن مولڈنگ کے لیے موزوں ہونے کو یقینی بناتی ہے۔ مواد کی جانچ میں پگھلنے کا بہاؤ انڈیکس (MFI) تجزیہ، مکینیکل خصوصیات، تھرمل خصوصیات، اور مواد کی ساخت شامل ہوسکتی ہے۔ مواد کے معیار کی توثیق سے ڈھالے ہوئے حصوں میں نقائص اور عدم مطابقت کو روکنے میں مدد ملتی ہے۔
- ٹولنگ کی بحالی اور معائنہ:انجیکشن مولڈز کی مناسب دیکھ بھال اور باقاعدہ معائنہ انجیکشن مولڈنگ میں معیار کو یقینی بنانے کے لیے بہت ضروری ہے۔ مولڈ اجزاء کی باقاعدگی سے صفائی، چکنا، اور تشخیص پہننے، نقصان، یا انحطاط کو روکنے میں مدد کرتا ہے جو جزوی معیار کو متاثر کر سکتا ہے۔ مولڈنگ کی مستقل کارکردگی کو برقرار رکھنے کے لیے ٹوٹے ہوئے یا خراب شدہ مولڈ اجزاء کی بروقت مرمت یا تبدیلی ضروری ہے۔
- دستاویزی اور ٹریس ایبلٹی:انجیکشن مولڈنگ میں کوالٹی کنٹرول کے لیے جامع دستاویزات اور ٹریس ایبلٹی ریکارڈز کو برقرار رکھنا ضروری ہے۔ عمل کے پیرامیٹرز، معائنہ کے نتائج، مادی معلومات، اور پیداوار کے دوران کی گئی کسی بھی تبدیلی یا ایڈجسٹمنٹ کو ریکارڈ کرنا بہت ضروری ہے۔ مناسب دستاویزات حصوں کے سراغ لگانے کے قابل بناتی ہیں، بنیادی وجہ کے تجزیہ میں سہولت فراہم کرتی ہے، اور معیار میں مستقل مزاجی کو یقینی بناتی ہے۔
- تربیت اور مہارت کی ترقی: آپریٹرز، تکنیکی ماہرین، اور کوالٹی کنٹرول کے اہلکاروں کے لیے مناسب تربیت اور مہارت کی ترقی کے پروگرام فراہم کرنا انجکشن مولڈنگ کے عمل، معیار کی ضروریات، اور معائنہ کی تکنیکوں کے بارے میں ان کی سمجھ کو بڑھاتا ہے۔ اچھی طرح سے تربیت یافتہ اہلکار اعلی معیار کی پیداوار کو یقینی بناتے ہوئے نقائص کا پتہ لگا سکتے ہیں، مسائل کا ازالہ کر سکتے ہیں اور اصلاحی اقدامات کو مؤثر طریقے سے نافذ کر سکتے ہیں۔
عام انجیکشن مولڈنگ کی خرابیاں اور ان سے کیسے بچنا ہے۔
انجیکشن مولڈنگ کے عمل کا باقاعدہ معائنہ، نگرانی، اور تجزیہ اور سازوسامان اور سانچوں کی مناسب دیکھ بھال اور ایڈجسٹمنٹ ان عام نقائص کی شناخت اور ان کو دور کرنے میں مدد کر سکتی ہے۔
- سنک کے نشانات:سنک کے نشانات ناہموار ٹھنڈک یا سکڑنے کی وجہ سے ڈھالے ہوئے حصے کی سطح پر ڈپریشن یا انڈینٹیشن ہیں۔ سنک کے نشانات سے بچنے کے لیے گیٹ کی مناسب جگہ اور ڈیزائن، کولنگ سسٹم کے بہترین ڈیزائن، اور دیوار کی موٹائی کی یکساں تقسیم پر غور کرنا چاہیے۔ انجیکشن پریشر کو بڑھانا یا ٹھنڈک کے وقت کو ایڈجسٹ کرنا بھی سنک کے نشانات کو کم کرنے میں مدد کر سکتا ہے۔
- وار پیج:وار پیج سے مراد ناہموار ٹھنڈک یا بقایا دباؤ کی وجہ سے انجیکشن کے بعد مولڈ حصے کی خرابی یا موڑنا ہے۔ دیوار کی یکساں موٹائی کو برقرار رکھنا، مناسب کولنگ چینلز کا استعمال، اور مولڈ کی متوازن بھرائی اور پیکنگ کو یقینی بنانا وار پیج کو روکنے کے لیے بہت ضروری ہے۔ مولڈ کے درجہ حرارت کو بہتر بنانا، مناسب ڈرافٹ اینگل استعمال کرنا، اور مواد کے درجہ حرارت اور انجیکشن کی رفتار کو کنٹرول کرنا وار پیج کو کم سے کم کرنے میں مدد کر سکتا ہے۔
- فلیش:فلیش اس وقت ہوتی ہے جب اضافی مواد مولڈ پارٹنگ لائن میں بہہ جاتا ہے، جس کے نتیجے میں آخری حصے پر پتلی، ناپسندیدہ تخمینہ یا اضافی مواد ہوتا ہے۔ مناسب مولڈ ڈیزائن کو یقینی بنا کر فلیش کو مؤثر طریقے سے روک سکتا ہے، بشمول مناسب کلیمپنگ فورس، درست سیدھ، اور مناسب وینٹنگ تکنیک کا استعمال۔ عمل کے پیرامیٹرز کو بہتر بنانا جیسے انجیکشن پریشر، درجہ حرارت، اور سائیکل کا وقت فلیش کو کم کرتا ہے۔
- مختصر شاٹ:ایک فوری شاٹ اس وقت ہوتا ہے جب انجکشن شدہ مواد مولڈ گہا کو نہیں بھرتا ہے، جس کے نتیجے میں ایک نامکمل حصہ ہوتا ہے۔ مختصر تصویروں سے بچنے کے لیے مناسب مواد کا انتخاب، مناسب پگھلنے والے درجہ حرارت اور چپکنے کو یقینی بنانا، اور مناسب انجیکشن پریشر اور وقت کو برقرار رکھنا ضروری ہے۔ مزید برآں، کافی رنر اور گیٹ کے سائز کے لیے مولڈ ڈیزائن کی تصدیق اور مناسب وینٹنگ فوری شاٹس کو روکنے میں مدد کر سکتی ہے۔
- ویلڈ لائنز:ویلڈ لائنیں اس وقت ہوتی ہیں جب دو یا دو سے زیادہ پگھلے ہوئے مادے کے بہاؤ کے محاذ آپس میں ملتے ہیں اور مضبوط ہوتے ہیں، جس کے نتیجے میں حصے کی سطح پر نظر آنے والی لکیر یا نشان بن جاتا ہے۔ اچھا گیٹ اور رنر ڈیزائن، زیادہ سے زیادہ پگھلنے کا درجہ حرارت، انجیکشن کی رفتار، اور مواد کے بہاؤ اور حصے جیومیٹری کو ایڈجسٹ کرنے سے ویلڈ لائنوں کو کم کیا جا سکتا ہے۔ مولڈ فلو کا تجزیہ اور گیٹ پلیسمنٹ کی اصلاح بھی ویلڈ لائنوں کو روکنے یا کم کرنے میں مدد کر سکتی ہے۔
- جلنے کے نشانات:جلنے کے نشانات ڈھلے ہوئے حصے کی سطح پر رنگین یا سیاہ دھبے ہیں جو مواد کی ضرورت سے زیادہ گرمی یا زیادہ گرم ہونے کی وجہ سے ہوتے ہیں۔ انتہائی پگھلنے والے درجہ حرارت سے بچنا، مناسب کولنگ چینلز کا استعمال، اور سائیکل کے وقت کو بہتر بنانا جلنے کے نشانات کو روکنے میں مدد کر سکتا ہے۔ مناسب وینٹنگ، مناسب گیٹ ڈیزائن، اور مولڈ درجہ حرارت کو کنٹرول کرنا بھی جلنے کے نشانات کو کم کرنے میں معاون ہے۔
پوسٹ مولڈنگ آپریشنز: فنشنگ اور اسمبلی
انجیکشن مولڈنگ کے بعد، بہت سے مولڈ حصوں کو مطلوبہ حتمی مصنوع کے حصول کے لیے اضافی فنشنگ اور اسمبلی آپریشنز کی ضرورت پڑ سکتی ہے۔ یہ پوسٹ مولڈنگ آپریشنز میں شامل ہو سکتے ہیں:
- تراشنا:تراشنے یا کاٹنے والے ٹولز کا استعمال کرتے ہوئے ڈھالے ہوئے حصے کے ارد گرد کوئی اضافی مواد یا فلیش ہٹا دیں۔
- سطح کے علاج:مختلف تکنیکوں جیسے پینٹنگ، کوٹنگ، یا ٹیکسچرنگ کا استعمال کرتے ہوئے حصے کی سطح کی ظاہری شکل یا فعالیت کو بڑھانا۔
- اسمبلی:حتمی پروڈکٹ کو مکمل کرنے کے لیے متعدد مولڈ پارٹس کو جوڑنا یا فاسٹنرز، انسرٹس یا لیبل جیسے اجزاء شامل کرنا۔
- امتحان:مختلف جانچ کے طریقوں جیسے جہتی تجزیہ، مادی خصوصیات کی جانچ، یا کارکردگی کی جانچ کے ذریعے جزوی معیار اور فعالیت کی تصدیق۔
- پیکیجنگ اور شپنگ:گاہکوں یا اختتامی صارفین کو ترسیل کے لیے تیار شدہ مصنوعات کی مناسب پیکیجنگ اور لیبلنگ۔
پوسٹ مولڈنگ آپریشنز کا انتخاب مخصوص ایپلی کیشن اور مطلوبہ حتمی مصنوعات کی خصوصیات پر منحصر ہے۔ انجیکشن مولڈنگ کے ماہرین، فنشنگ اور اسمبلی ماہرین کے درمیان قریبی تعاون، اور صارف مطلوبہ مطلق مصنوعات کے معیار اور فعالیت کو حاصل کرنے کے لیے اہم ہے۔ مناسب منصوبہ بندی اور پوسٹ مولڈنگ آپریشنز کو مینوفیکچرنگ کے عمل میں ضم کرنے سے موثر پیداوار اور اعلیٰ معیار کی مصنوعات کی بروقت فراہمی کو یقینی بنانے میں مدد مل سکتی ہے۔
انجکشن مولڈنگ بمقابلہ دیگر پلاسٹک مینوفیکچرنگ کے عمل
ہر پلاسٹک مینوفیکچرنگ کے عمل کے فوائد اور حدود ہوتے ہیں، جو انہیں مختلف ایپلی کیشنز کے لیے موزوں بناتے ہیں۔
- انجکشن مولڈنگ: انجکشن مولڈنگ ایک انتہائی ورسٹائل اور بڑے پیمانے پر پلاسٹک کے پرزے تیار کرنے کے لیے استعمال ہونے والا مینوفیکچرنگ عمل ہے۔ یہ فوائد پیش کرتا ہے جیسے اعلی پیداواری کارکردگی، قطعی حصہ نقل، اور پیچیدہ جیومیٹریز بنانے کی صلاحیت۔ انجکشن مولڈنگ اعلی حجم کی پیداوار کے لیے موزوں ہے اور تھرمو پلاسٹک مواد کی ایک وسیع رینج استعمال کرنے کی اجازت دیتی ہے۔ یہ بہترین جہتی درستگی اور سطح کی تکمیل پیش کرتا ہے، جو اسے مختلف صنعتوں جیسے آٹوموٹیو، صارفی سامان، اور طبی آلات کے لیے مثالی بناتا ہے۔
- بلو مولڈنگ: بلو مولڈنگ ایک ایسا عمل ہے جو بنیادی طور پر پلاسٹک کے کھوکھلے پرزوں، جیسے بوتلیں، کنٹینرز اور آٹوموٹیو پرزوں کی تیاری کے لیے استعمال ہوتا ہے۔ اس میں پلاسٹک کو پگھلانا اور اسے مولڈ گہا میں فلانا، مطلوبہ شکل بنانا شامل ہے۔ بلو مولڈنگ اعلی حجم کی پیداوار کے لیے موزوں ہے اور دیوار کی یکساں موٹائی کے ساتھ بڑے، ہلکے وزن والے حصے تیار کر سکتی ہے۔ تاہم، یہ انجکشن مولڈنگ کے مقابلے میں جزوی پیچیدگی اور مواد کے انتخاب کے لحاظ سے محدود ہے۔
- تھرموفارمنگ:تھرموفارمنگ ایک ایسا عمل ہے جو پلاسٹک کے پرزوں کو تھرمو پلاسٹک شیٹ کو گرم کرکے اور اسے سانچوں یا ویکیوم کی تشکیل کے ذریعے تشکیل دینے کے لیے استعمال کیا جاتا ہے۔ یہ پیکیجنگ، ڈسپوزایبل مصنوعات، اور بڑے پیمانے پر مصنوعات جیسے ٹرے اور کور میں عام استعمال پایا جاتا ہے۔ تھرموفارمنگ بڑے حصوں کے لیے سرمایہ کاری مؤثر پیداوار پیش کرتی ہے اور فوری پروٹو ٹائپنگ کی اجازت دیتی ہے۔ تاہم، انجکشن مولڈنگ کے مقابلے میں جزوی پیچیدگی، مواد کے انتخاب، اور جہتی درستگی کے حوالے سے اس کی حدود ہیں۔
- اخراج:اخراج پلاسٹک پروفائلز، شیٹس، ٹیوبیں اور فلمیں بنانے کے لیے ایک مسلسل عمل ہے۔ اس میں پلاسٹک کی رال کو پگھلانا اور اسے ڈائی کے ذریعے مطلوبہ شکل بنانے کے لیے مجبور کرنا شامل ہے۔ اخراج ایک مسلسل کراس سیکشن کے ساتھ پلاسٹک کی مصنوعات کی طویل، مسلسل لمبائی پیدا کرنے کے لیے موزوں ہے۔ اگرچہ اخراج اعلی پیداواری شرح اور لاگت کی تاثیر پیش کرتا ہے، لیکن یہ انجیکشن مولڈنگ کے مقابلے میں پیچیدہ حصہ جیومیٹریز اور عین جہتی کنٹرول کے لحاظ سے محدود ہے۔
- کمپریشن مولڈنگ:کمپریشن مولڈنگ میں تھرموسیٹنگ مواد کی پہلے سے پیمائش شدہ مقدار کو گرم مولڈ گہا میں رکھنا اور اسے ٹھیک ہونے تک زیادہ دباؤ میں دبانا شامل ہے۔ یہ اعلی طاقت اور جہتی استحکام کے ساتھ حصوں کی پیداوار میں عام استعمال کو تلاش کرتا ہے، جیسے آٹوموٹو اجزاء اور برقی موصلیت۔ کمپریشن مولڈنگ اچھے حصے کی مستقل مزاجی، اعلی پیداواری کارکردگی اور وسیع پیمانے پر مواد کو استعمال کرنے کی صلاحیت پیش کرتی ہے۔ تاہم، یہ انجکشن مولڈنگ کے مقابلے میں جزوی پیچیدگی اور سائیکل کے وقت کے لحاظ سے محدود ہے۔
تھرمو پلاسٹک انجکشن مولڈنگ کی ایپلی کیشنز
مختلف صنعتیں وسیع پیمانے پر تھرمو پلاسٹک انجیکشن مولڈنگ کو اس کی استعداد، کارکردگی اور لاگت کی تاثیر کی وجہ سے استعمال کرتی ہیں۔ تھرمو پلاسٹک انجیکشن مولڈنگ کی کچھ ایپلی کیشنز میں شامل ہیں:
- گاڑیوں کی صنعت: آٹوموٹو انڈسٹری وسیع پیمانے پر تھرمو پلاسٹک انجیکشن مولڈنگ کا استعمال مختلف اجزاء کی تیاری کے لیے کرتی ہے، بشمول اندرونی اور بیرونی تراشیں، ڈیش بورڈ، دروازے کے پینل، بمپر، اور برقی کنیکٹر۔ یہ عمل عین مطابق حصے کی نقل، پیچیدہ جیومیٹریز، اور ہلکے وزن والے مواد کی اجازت دیتا ہے، ایندھن کی کارکردگی اور ڈیزائن کی لچک کو بہتر بناتا ہے۔
- صارفین کی اشیا:انجیکشن مولڈنگ صارفین کے سامان جیسے گھریلو آلات، الیکٹرانک آلات، پیکیجنگ کنٹینرز اور کھلونے بنانے میں وسیع ایپلی کیشنز تلاش کرتی ہے۔ یہ عمل پائیدار، اعلیٰ معیار کی مصنوعات کی مسلسل جہتوں اور سطح کی تکمیل کے ساتھ بڑے پیمانے پر پیداوار کو قابل بناتا ہے۔ یہ حسب ضرورت کے اختیارات اور فوری مصنوعات کی تکرار کی بھی اجازت دیتا ہے۔
- طبی آلات:انجکشن مولڈنگ طبی صنعت میں آلات کی ایک وسیع رینج تیار کرنے کے لیے ایک اہم کردار ادا کرتی ہے، بشمول سرنج، جراحی کے آلات، امپلانٹیبل اجزاء، اور منشیات کی ترسیل کے نظام۔ یہ عمل جراثیم سے پاک، عین مطابق، اور حیاتیاتی مطابقت پذیر حصوں کی پیداوار کو یقینی بناتا ہے جو صحت کی دیکھ بھال کے شعبے کی سخت ریگولیٹری ضروریات کو پورا کرتے ہیں۔
- الیکٹرانکس اور الیکٹریکل انڈسٹری:الیکٹرونکس انڈسٹری الیکٹریکل کنیکٹرز، انکلوژرز، سوئچز اور دیگر اجزاء کی تیاری کے لیے انجیکشن مولڈنگ کا استعمال کرتی ہے۔ یہ عمل اعلیٰ جہتی درستگی، بہترین سطح کی تکمیل، اور انسرٹ مولڈنگ اور اوور مولڈنگ جیسی خصوصیات کو شامل کرنے کی صلاحیت پیش کرتا ہے، جس سے پیچیدہ الیکٹرانک اسمبلیوں کی موثر پیداوار کی اجازت ملتی ہے۔
- پیکیجنگ انڈسٹری:مختلف صنعتیں، بشمول خوراک اور مشروبات، دواسازی، اور ذاتی نگہداشت، عام طور پر پلاسٹک کے پیکیجنگ کنٹینرز، ٹوپیاں، بندش اور بوتلیں بنانے کے لیے انجیکشن مولڈنگ کا استعمال کرتی ہیں۔ یہ عمل موثر مینوفیکچرنگ سائیکل کے ساتھ ہلکا پھلکا، پائیدار، اور جمالیاتی طور پر دلکش پیکیجنگ سلوشنز کی تخلیق کو قابل بناتا ہے۔
- ایرو اسپیس انڈسٹری:ایرو اسپیس سیکٹر ہلکے وزن اور اعلی کارکردگی والے اجزاء جیسے ایئر ڈکٹ، بریکٹ، اندرونی پینل، اور ساختی حصوں کی تیاری کے لیے انجیکشن مولڈنگ کا استعمال کرتا ہے۔ اس عمل سے وزن میں کمی اور ایندھن کی کارکردگی کو بہتر بنانے میں مدد کرتے ہوئے جدید مواد اور پیچیدہ حصہ جیومیٹریز استعمال کرنے کی اجازت ملتی ہے۔
تھرمو پلاسٹک انجکشن مولڈنگ کے ماحولیاتی اثرات
تھرمو پلاسٹک انجیکشن مولڈنگ اپنے بہت سے فوائد کی وجہ سے ایک مقبول مینوفیکچرنگ عمل ہے، لیکن اس کے ماحولیاتی اثرات پر غور کرنا بھی ضروری ہے۔ غور کرنے کے لیے کچھ نکات یہ ہیں:
- مواد کی کارکردگی:تھرمو پلاسٹک انجیکشن مولڈنگ فضلہ کو کم سے کم کرکے مواد کی کارکردگی کو فروغ دیتا ہے۔ یہ عمل مولڈ میں داخل ہونے والے مواد کی مقدار پر قطعی کنٹرول کا استعمال کرتا ہے، اضافی مواد کی ضرورت کو کم کرتا ہے۔ مینوفیکچررز اسکریپ یا مسترد شدہ پرزوں کو دوبارہ استعمال کرنے کے لیے ری گرائنڈنگ اور ری سائیکلنگ کی تکنیکوں کو بھی استعمال کر سکتے ہیں، جس سے مواد کے فضلے کو مزید کم کیا جا سکتا ہے۔
- توانائی کی کھپت:مینوفیکچررز انجیکشن مولڈنگ مشینوں کو توانائی کے قابل بنانے کے لیے ڈیزائن کرتے ہیں، جدید ماڈلز میں جدید ٹیکنالوجیز جیسے سروو موٹرز اور متغیر رفتار ڈرائیوز شامل ہیں۔ یہ خصوصیات مولڈنگ کے دوران بجلی کی کھپت کو کم کرکے توانائی کے استعمال کو بہتر بناتی ہیں، جس کے نتیجے میں توانائی کی ضروریات کم ہوتی ہیں اور ماحولیاتی اثرات کم ہوتے ہیں۔
- فضلے کے انتظام:مادی فضلہ کو کم سے کم کرتے ہوئے، مینوفیکچررز کو بچ جانے والے مواد، اسپروز، یا رنرز کو سنبھالنے کے لیے فضلہ کے انتظام کے مناسب طریقوں کو نافذ کرنا چاہیے۔ مینوفیکچررز انجیکشن مولڈنگ کے دوران پیدا ہونے والے پلاسٹک کے فضلے کو جمع کرنے اور دوبارہ استعمال کرنے کے لیے ری سائیکلنگ پروگرام قائم کر سکتے ہیں، اس طرح لینڈ فلز کو بھیجے جانے والے فضلہ کو کم کیا جا سکتا ہے۔
- اخراج میں کمی: تھرمو پلاسٹک انجکشن مولڈنگ عام طور پر دیگر مینوفیکچرنگ کے عمل کے مقابلے میں کم اخراج پیدا کرتی ہے۔ مینوفیکچررز ماحول دوست مواد کا استعمال کرکے، توانائی کے موثر آلات کو لاگو کرکے، اور خارج ہونے والے اخراج کو پکڑنے کے لیے جدید ایگزاسٹ اور فلٹریشن سسٹم کو استعمال کرکے اخراج کو کم کرسکتے ہیں۔
- پائیدار مواد کے انتخاب:تھرمو پلاسٹک مواد کا انتخاب انجیکشن مولڈنگ کی ماحولیاتی پائیداری کو نمایاں طور پر متاثر کر سکتا ہے۔ بائیوڈیگریڈیبل یا بائیو بیسڈ پلاسٹک کے ساتھ ساتھ ری سائیکل یا ری سائیکل مواد کا انتخاب کرنے سے اس عمل کے مجموعی ماحولیاتی اثرات کو کم کرنے میں مدد مل سکتی ہے۔
لائف سائیکل کے تحفظات: اس کے ماحولیاتی اثرات کا اندازہ لگانے کے لیے مولڈ پروڈکٹ کے پورے لائف سائیکل پر غور کرنا ضروری ہے۔ ڈیزائن اور مواد کے انتخاب کے مراحل کے دوران، مینوفیکچررز کو اس حصے کی پائیداری، اس کی ری سائیکلیبلٹی، اور زندگی کے آخر میں ضائع کرنے یا دوبارہ استعمال کرنے کی صلاحیت جیسے عوامل پر غور کرنا چاہیے۔
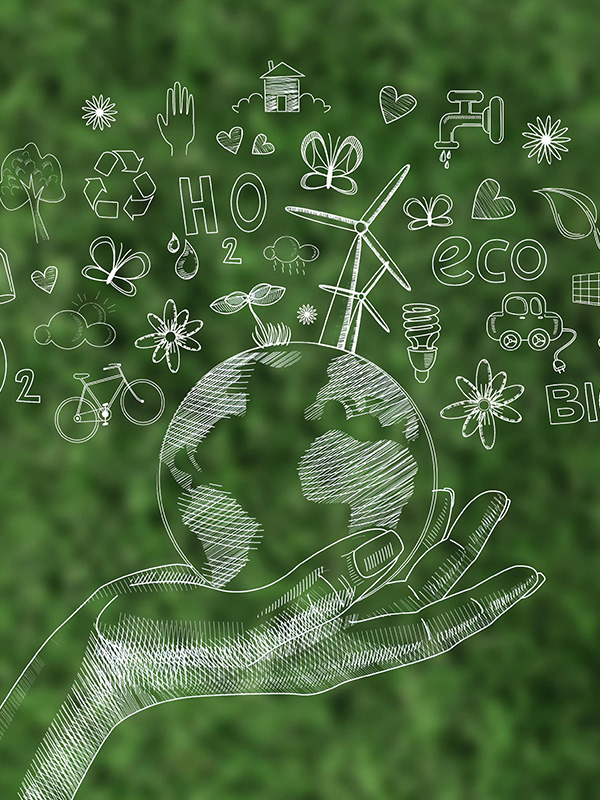
تھرمو پلاسٹک انجیکشن مولڈنگ کا مستقبل
تھرمو پلاسٹک انجیکشن مولڈنگ کا مستقبل امید افزا لگتا ہے، ٹیکنالوجی میں مسلسل ترقی اور مختلف صنعتوں میں اعلیٰ معیار کے، درست حصوں کی بڑھتی ہوئی مانگ کے ساتھ۔ آنے والے سالوں میں متوقع کچھ اہم پیش رفتوں میں شامل ہیں:
- کارکردگی کو بہتر بنانے اور اخراجات کو کم کرنے کے لیے آٹومیشن اور روبوٹکس کے استعمال میں اضافہ۔
- کوششیں حصہ کی کارکردگی کو بہتر بنانے اور نئی ایپلی کیشنز کو فعال کرنے کے لیے نئے مواد اور عمل کو تیار کرنے پر مرکوز ہیں۔
- یہ انجیکشن مولڈنگ کے ماحولیاتی اثرات کو کم کرنے کے لیے پائیدار طریقوں کو اپنانا ہے، جیسے کہ ری سائیکل مواد کا استعمال اور توانائی کی کھپت کو بہتر بنانا۔
- ڈیزائن اور پروڈکشن کے عمل کو بہتر بنانے کے لیے 3D پرنٹنگ اور سمولیشن سافٹ ویئر جیسی ڈیجیٹل ٹیکنالوجیز کا زیادہ سے زیادہ انضمام۔
عالمی انجیکشن مولڈنگ مارکیٹ پھیل رہی ہے، خاص طور پر ابھرتی ہوئی معیشتوں میں، مختلف صنعتوں میں پلاسٹک کی مصنوعات کی بڑھتی ہوئی مانگ کی وجہ سے۔
صحیح انجیکشن مولڈنگ پارٹنر کا انتخاب
صحیح انجیکشن مولڈنگ پارٹنر کا انتخاب آپ کے پروجیکٹ کی کامیابی کے لیے بہت ضروری ہے۔ ہم آہنگ اور دیرپا شراکت کو یقینی بنانے کے لیے متعدد اختیارات کا جائزہ لینے، سائٹ کے دورے کرنے، اور مکمل بات چیت میں مشغول ہونے کے لیے وقت نکالیں۔
- مہارت اور تجربہ:صنعت میں وسیع علم اور تجربے کے ساتھ انجکشن مولڈنگ پارٹنر کی تلاش کریں۔ ان کے پاس مختلف شعبوں میں گاہکوں کو اعلیٰ معیار کی مصنوعات اور حل فراہم کرنے کا ایک ثابت شدہ ٹریک ریکارڈ ہونا چاہیے۔ مختلف مواد، مولڈ ڈیزائن، اور مینوفیکچرنگ کے عمل کے بارے میں ان کی سمجھ پر غور کریں۔
- مینوفیکچرنگ کی صلاحیتیں: انجیکشن مولڈنگ پارٹنر کی مینوفیکچرنگ صلاحیتوں کا اندازہ لگائیں۔ اس بات کو یقینی بنائیں کہ آپ کے پراجیکٹ کی ضروریات کو سنبھالنے کے لیے ان کے پاس جدید مشینری اور ٹیکنالوجی سے لیس سہولت موجود ہے۔ ان کی پیداواری صلاحیت، مختلف حصوں کے سائز اور پیچیدگیوں کو سنبھالنے کی صلاحیت، اور اپنی مطلوبہ پیداوار کے حجم اور ٹائم لائنز کو پورا کرنے کی صلاحیت پر غور کریں۔
- کوالٹی اشورینس:انجیکشن مولڈنگ میں معیار سب سے اہم ہے۔ کوالٹی کنٹرول سسٹمز اور ممکنہ پارٹنر کے سرٹیفیکیشن کا جائزہ لیں۔ ایسے شراکت داروں کی تلاش کریں جو معیار کے سخت معیارات پر عمل کرتے ہیں، معائنہ کے مضبوط عمل رکھتے ہیں، اور جزوی معیار اور مستقل مزاجی کو یقینی بنانے کے لیے جامع جانچ کرتے ہیں۔
- ڈیزائن اور انجینئرنگ سپورٹ:ایک قابل اعتماد انجکشن مولڈنگ پارٹنر کو آپ کے حصے کے ڈیزائن کو مینوفیکچریبلٹی کے لیے بہتر بنانے کے لیے ڈیزائن اور انجینئرنگ سپورٹ پیش کرنا چاہیے۔ ان کے پاس ہنر مند انجینئرز ہونے چاہئیں جو جزوی معیار اور کارکردگی کو بڑھانے کے لیے مواد کے انتخاب، مولڈ ڈیزائن، اور عمل کی اصلاح پر قیمتی ان پٹ فراہم کر سکیں۔
- لاگت کی مسابقت:اگرچہ لاگت ہی واحد تعین کرنے والا عنصر نہیں ہونا چاہیے، لیکن انجیکشن مولڈنگ پارٹنر کی قیمتوں اور لاگت کی مسابقت کا جائزہ لینا ضروری ہے۔ تفصیلی اقتباسات کی درخواست کریں اور ٹولنگ کے اخراجات، مادی اخراجات، مزدوری کے اخراجات، اور ان کی فراہم کردہ کسی بھی اضافی خدمات پر غور کریں۔
- مواصلات اور تعاون:ایک کامیاب شراکت داری کے لیے موثر مواصلت اور تعاون ضروری ہے۔ اس بات کو یقینی بنائیں کہ انجیکشن مولڈنگ پارٹنر کے پاس مواصلات کے اچھے چینلز ہیں، وہ آپ کی پوچھ گچھ کے لیے جوابدہ ہے، اور باقاعدہ پروجیکٹ اپ ڈیٹ فراہم کر سکتا ہے۔ ایک باہمی تعاون کے ساتھ اس بات کو یقینی بنانے میں مدد ملے گی کہ ہم آپ کی ضروریات کو پورا کرتے ہیں اور کسی بھی چیلنج کو فوری طور پر حل کرتے ہیں۔
- کسٹمر حوالہ جات اور جائزے:انجیکشن مولڈنگ پارٹنر کے ساتھ دوسرے کلائنٹس کے تجربات کے بارے میں بصیرت حاصل کرنے کے لیے گاہک کے حوالہ جات تلاش کریں یا جائزے/ تعریفیں پڑھیں۔ اس معلومات کو حاصل کرنے سے ان کی قابل اعتمادی، فوری پن، اور گاہک کی اطمینان کی مجموعی سطح کا تعین کرنے میں مدد مل سکتی ہے۔
نتیجہ
تھرمو پلاسٹک انجکشن مولڈنگ پلاسٹک کے پرزوں کو بڑی مقدار میں تیار کرنے کا ایک ورسٹائل اور سرمایہ کاری مؤثر طریقہ ہے۔ اعلیٰ درستگی اور مستقل مزاجی کے ساتھ پیچیدہ شکلیں پیدا کرنے کی اس کی صلاحیت مختلف صنعتوں کے لیے ایک مقبول انتخاب بن گئی ہے، بشمول آٹوموٹیو، میڈیکل، الیکٹرانکس، اور اشیائے صرف۔ تھرمو پلاسٹک انجیکشن مولڈنگ کے مختلف پہلوؤں کو سمجھ کر، بشمول اس کے فوائد، نقصانات اور ڈیزائن کے تحفظات، آپ اپنی کاروباری ضروریات کے لیے صحیح انجیکشن مولڈنگ پارٹنر کے انتخاب کے بارے میں باخبر فیصلے کر سکتے ہیں۔