Какво е шприцване на пластмаса
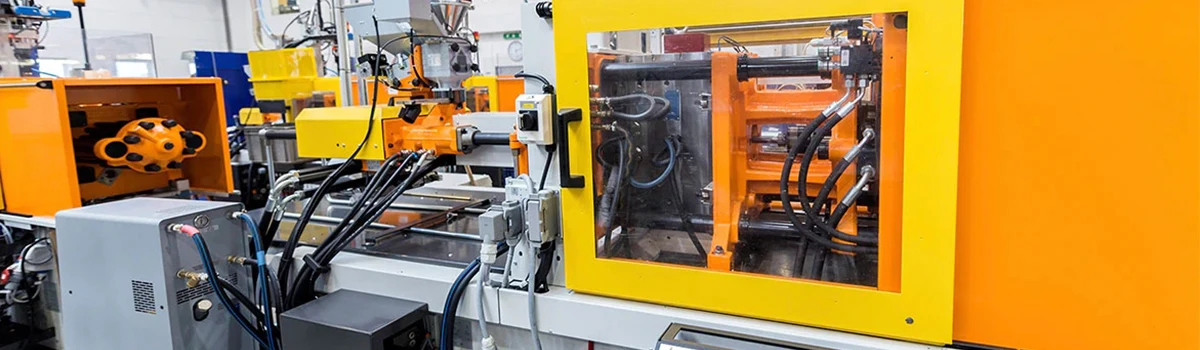
Термопластичното леене под налягане е метод за производство на детайли с голям обем от пластмасови материали. Благодарение на своята надеждност и гъвкавост в дизайнерските опции, леенето под налягане се използва в много индустрии, включително: опаковки, потребителска и електроника, автомобилостроене, медицина и много други.
Шприцоването е един от най-широко използваните производствени процеси в света. Термопластите са полимери, които се размекват и текат при нагряване и се втвърдяват при охлаждане.
Приложения
Шприцоването е най-разпространеният модерен метод за производство на пластмасови части; той е идеален за производство на големи обеми от един и същи обект. Шприцоването се използва за създаване на много неща, включително телени макари, опаковки, капачки за бутилки, автомобилни части и компоненти, игрови конзоли, джобни гребени, музикални инструменти, столове и малки маси, контейнери за съхранение, механични части и много други пластмасови продукти.
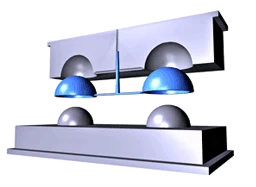
Дизайн на мухъл
След като даден продукт е проектиран със софтуер като CAD пакет, формите се създават от метал, обикновено стомана или алуминий, и се обработват прецизно, за да се оформят характеристиките на желаната част. Формата се състои от два основни компонента, шприцформа (A плоча) и ежекторна форма (B плоча). Пластмасовата смола навлиза във формата през леяк или порта и се влива в кухината на матрицата през канали или канали, които са машинно изработени в челата на плочите A и B.
Процес на леене под налягане
Когато термопластите се формоват, обикновено гранулираната суровина се подава през бункер в нагрят варел с възвратно-постъпателен винт. Шнекът доставя суровината напред през възвратен клапан, където се събира в предната част на винта в обем, известен като изстрел.
Изстрелът е количеството смола, необходимо за запълване на леяк, канал и кухини на матрица. Когато се събере достатъчно материал, материалът се изтласква при високо налягане и скорост в кухината, образуваща частта.
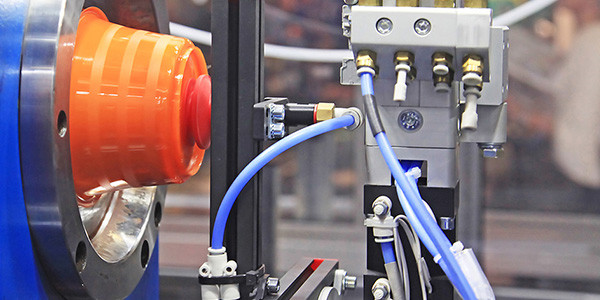
Как работи леенето под налягане?
След като пластмасата е напълнила матрицата, включително нейните канали, канали, врати и т.н., формата се поддържа при зададена температура, за да се позволи равномерно втвърдяване на материала във формата на детайла. При охлаждане се поддържа налягане за задържане, за да се спре обратният поток в цевта и да се намалят ефектите на свиване. В този момент към бункера се добавят повече пластмасови гранули в очакване на следващия цикъл (или изстрел). Когато се охлади, плочата се отваря и позволява готовата част да бъде изхвърлена, а винтът се изтегля отново, което позволява на материала да влезе в цевта и да започне процеса отначало.
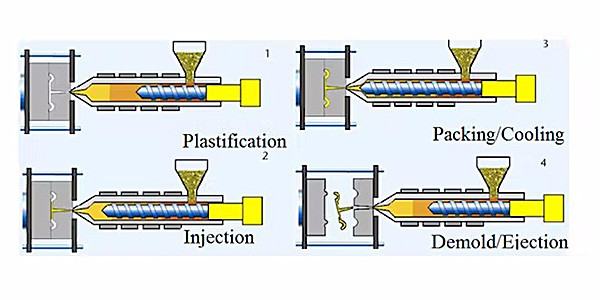
Цикълът на леене под налягане работи чрез този непрекъснат процес - затваряне на формата, подаване/нагряване на пластмасовите гранули, поставянето им под налягане във формата, охлаждането им в твърда част, изваждане на частта и затваряне на матрицата отново. Тази система позволява бързото производство на пластмасови части и повече от 10,000 XNUMX пластмасови части могат да бъдат направени за един работен ден в зависимост от дизайна, размера и материала.
Цикъл на леене под налягане
Цикълът на леене под налягане е много кратък, обикновено между 2 секунди и 2 минути. Има няколко етапа:
1.Затягане
Преди шприцването на материала във формата, двете половини на формата се затварят здраво от затягащия блок. Хидравлично задвижваният затягащ модул избутва половинките на формата заедно и упражнява достатъчна сила, за да държи формата затворена, докато материалът се инжектира.
2.Инжектиране
При затворена форма, полимерният изстрел се инжектира в кухината на формата.
3. Охлаждане
Когато кухината се запълни, се прилага задържащо налягане, което позволява на повече полимер да навлезе в кухината, за да компенсира свиването на пластмасата, докато се охлажда. Междувременно винтът се завърта и подава следващия изстрел към предния винт. Това води до прибиране на винта, докато се подготвя следващият изстрел.
4.Изтласкване
Когато детайлът се охлади достатъчно, формата се отваря, детайлът се изхвърля и цикълът започва отново.
Предимства
1.Бързо производство; 2.Гъвкавост на дизайна; 3.Точност; 4.Ниски разходи за труд; 5. Ниски отпадъци