Пластмасово леене под налягане
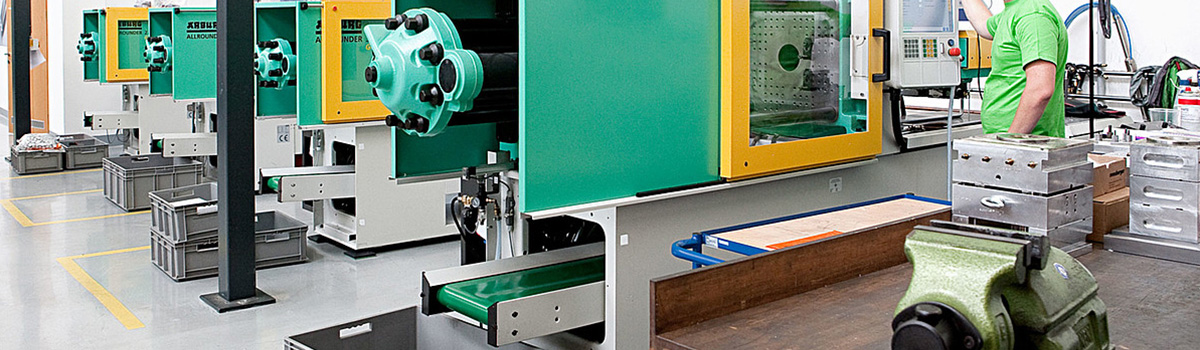
Пластмасовото леене под налягане е производствен процес, който включва топенето на пластмасови пелети и инжектирането им в кухината на формата, за да се създаде триизмерен обект. Този процес започва с много продукти, от малки прецизни части до значителни автомобилни компоненти. Пластмасовото леене под налягане предлага много предимства пред други производствени процеси, включително високи производствени нива, гъвкавост на дизайна и рентабилност. Това ръководство ще разгледа в дълбочина шприцоването на пластмаса и ще проучи различните му приложения, предимства и ограничения.
Историята на леенето под налягане на пластмаса
Пластмасовото леене под налягане е производствен процес, който включва инжектиране на разтопена пластмаса в кухината на формата, за да се създаде специфична форма. Историята на формоването под налягане на пластмаса може да бъде проследена до края на 1800 г., когато за първи път е изобретен целулоидът, вид пластмаса. Въпреки това през 1940-те години на миналия век шприцоването на пластмаса става широко използвано като производствена техника.
По време на Втората световна война търсенето на масово произвеждани пластмасови продукти нараства и производителите започват да търсят нови и по-ефективни начини за производството им. През 1946 г. Джеймс Уотсън Хендри, американски изобретател, разработи първата винтова машина за леене под налягане, която революционизира индустрията за леене под налягане на пластмаси. Тази машина позволи по-прецизен и последователен контрол на процеса на инжектиране, правейки производството на големи количества пластмасови части по-достъпно и ефективно.
През 1950-те и 1960-те години на миналия век напредъкът в пластмасовата технология продължи да подобрява процеса на леене под налягане на пластмаса. Въвеждането на нови материали, като полистирен и полиетилен, създаде по-сложни и издръжливи пластмасови части. Освен това подобренията в технологията на машината за формоване, включително използването на хидравлични системи, направиха процеса на формоване под налягане още по-ефективен и рентабилен.
Днес шприцоването на пластмаса е силно автоматизиран процес, използван за производството на широка гама пластмасови продукти, от играчки и потребителски стоки до автомобилни части и медицински устройства. С развитието на нови материали и технологии, процесът на леене под налягане на пластмаса продължава да се развива и подобрява, като гарантира, че ще остане жизненоважна производствена техника в продължение на много години.
Основите на шприцоването на пластмаса
Пластмасовото леене под налягане е производствен процес за създаване на части и продукти, изработени от пластмасови материали. Процесът включва инжектиране на разтопена пластмаса във форма, която се охлажда и втвърдява, за да образува желаната форма.
Основните стъпки, включени в процеса на шприцване на пластмаса, са следните:
- Дизайн на матрицата: Първата стъпка в процеса е да се проектира матрицата, която ще се използва за създаване на желаната част. Формата обикновено е направена от метал и трябва да бъде подготвена за отчитане на свиването, докато пластмасата се охлажда и втвърдява.
- Подготовка на материала: Пластмасовият материал, използван в процеса на леене под налягане, идва под формата на пелети или гранули, които трябва да бъдат разтопени и подготвени за шприцване във формата. Това обикновено се прави в бункер, където пластмасата се нагрява до определена температура и се разтопява до течно състояние.
- Инжектиране: След като пластмасата се разтопи, тя се шприцова във формата с помощта на специализирана машина за леене под налягане. Машината прилага натиск върху разтопената пластмаса, принуждавайки я да влезе в кухината на матрицата, където тя приема формата на матрицата.
- Охлаждане и втвърдяване: След като пластмасата се инжектира във формата, тя може да се охлади и втвърди. Това може да отнеме от няколко секунди до няколко минути, в зависимост от размера и сложността на частта.
- Изваждане: След като пластмасата се охлади и втвърди, формата се отваря и частта се изхвърля. Позицията може да изисква допълнителна довършителна работа, като подрязване или шлайфане, за отстраняване на излишната пластмаса или грапави ръбове.
Пластмасовото шприцване е точен и повтарящ се процес, което го прави идеален за масово производство на части и продукти с постоянно качество. Освен това е много гъвкав, тъй като може да създава парчета и продукти в различни размери, форми и сложност. Някои от най-често срещаните приложения на шприцването на пластмаси включват производството на играчки, потребителски стоки, автомобилни части и медицински устройства.
Процес на леене под налягане на пластмаса: Стъпка по стъпка
Пластмасовото леене под налягане е сложен процес, който включва няколко стъпки. Ето ръководство стъпка по стъпка за процеса на шприцване на пластмаса:
- Проектиране на матрицата: Първата стъпка е да проектирате матрицата, използвана за създаване на детайла. Формата обикновено е изработена от стомана или алуминий и трябва да бъде подготвена да поеме свиването на пластмасовия материал, докато се охлажда.
- Създаване на матрицата: След като дизайнът на матрицата е завършен, тя се произвежда с помощта на софтуер за компютърно проектиране (CAD) и машини за компютърно подпомагано производство (CAM). Формата трябва да бъде внимателно обработена и полирана, за да се гарантира точността и завършеността на крайния продукт.
- Избор на материал: Пластмасовата смола, използвана за процеса на леене под налягане, трябва да бъде избрана въз основа на изискванията на частта, като нейната здравина, гъвкавост, цвят и текстура.
- Подготовка на материала: След това избраният пластмасов материал се нагрява до определена температура и се разтопява в течност. След това материалът се инжектира в бункера на формовъчната машина.
- Инжекционно формоване: Разтопеният пластмасов материал се инжектира в кухината на формата с помощта на специализирана машина за леене под налягане. Машината упражнява натиск върху пластмасовия материал, принуждавайки го да влезе в кухината на матрицата, където приема формата на матрицата.
- Охлаждане: След като кухината на матрицата се напълни с пластмаса, тя може да се охлади и втвърди. Времето за охлаждане се определя от характеристиките на пластмасовия материал, размера и дебелината на детайла и температурата на формата.
- Изваждане: След като пластмасата се втвърди, формата се отваря и частта се изважда от матрицата с помощта на ежекторни щифтове.
- Завършване: Изхвърлената част може да изисква допълнителна довършителна работа, като подрязване, шлайфане или боядисване, за да се отстрани излишната пластмаса или грапави ръбове.
- Контрол на качеството: Завършената част се подлага на щателна проверка, за да отговаря на изискваните спецификации и стандарти за качество.
Пластмасовото шприцване може да произвежда различни части и продукти в множество размери, форми и сложност. Процесът се използва широко в няколко индустрии, включително автомобилна, медицинска, потребителски стоки и електроника.
Видове пластмаси, използвани при леене под налягане
Много видове пластмаса могат да се използват при леене под налягане. Изборът на пластмасов материал ще зависи от специфичните изисквания на продукта или частта, която се произвежда, като здравина, гъвкавост, издръжливост и външен вид. Ето някои от най-често срещаните видове пластмаси, използвани при леене под налягане:
- Полиетилен (PE): PE е широко използван пластмасов материал, известен със своята здравина и гъвкавост. Използва се за производството на различни продукти, включително опаковъчни материали, играчки и медицински изделия.
- Полипропилен (PP): PP е лек и издръжлив пластмасов материал, който обикновено се използва в автомобилната индустрия за вътрешни части, като арматурни табла и панели на вратите. Произвежда и опаковъчни материали, като контейнери и бутилки.
- Поликарбонат (PC): PC е твърд и прозрачен пластмасов материал, който обикновено се използва за производство на електронни компоненти, като кутии за компютри и телефони. Използва се и за лещи на фарове и компоненти на таблото в автомобилната индустрия.
- Акрилонитрил бутадиен стирен (ABS): ABS е универсален пластмасов материал, известен със своята здравина, издръжливост и устойчивост на топлина. Обикновено се използва за производство на автомобилни части, като арматурни табла, фланци за калници, играчки и потребителски стоки.
- Полиамид (PA): PA, известен също като найлон, е здрав и лек пластмасов материал, който обикновено се използва в производството на автомобилни части, като капаци на двигатели и системи за всмукване на въздух. Произвежда и спортно оборудване, като ски обувки и тенис ракети.
- Полистирен (PS): PS е лек и твърд пластмасов материал, който обикновено се използва в производството на опаковъчни материали, като чаши, тави и контейнери за храна. Той също така произвежда потребителски стоки, като играчки и електронни компоненти.
- Полиетилен терефталат (PET): PET е здрав и прозрачен пластмасов материал, който обикновено се използва за производство на опаковъчни материали, като бутилки и контейнери. Използва се и в текстилната промишленост за производство на влакна и тъкани.
Това са само няколко от най-често срещаните видове пластмаси, използвани при леене под налягане. Предлагат се много други видове пластмасови материали, всеки с уникални свойства и характеристики. Изборът на пластмасов материал ще зависи от специфичните изисквания на произвежданата част или продукт.
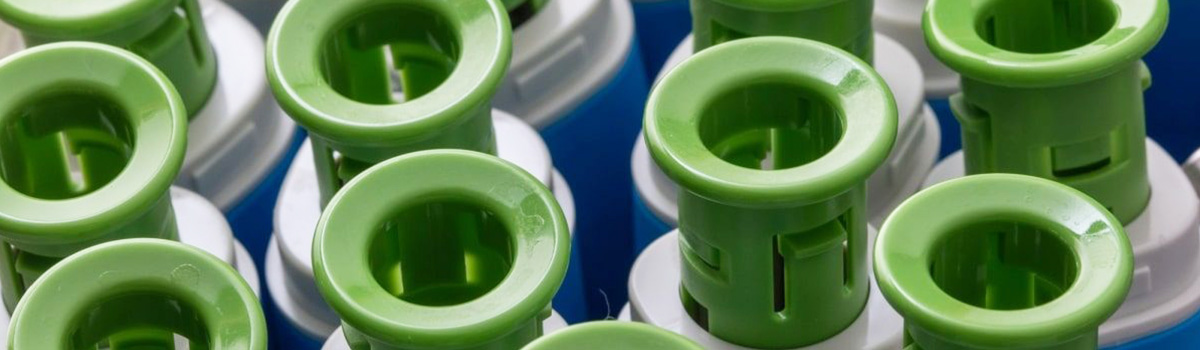
Видове машини за леене под налягане
Машините за леене под налягане се предлагат в различни видове и размери, всяка от които е проектирана да отговаря на специфични производствени изисквания. Ето някои от най-често срещаните видове машини за шприцване:
- Хидравлична машина за леене под налягане: Тази машина използва хидравлична мощност, за да генерира налягане за инжектиране на пластмаса във формата. Хидравличните машини обикновено се използват за по-важни части, които изискват висока сила на затягане.
- Електрическа машина за леене под налягане: Електрическите машини използват електрически двигатели за захранване на инжекционния модул и механизма за затягане. Те са известни със своята висока прецизност и енергийна ефективност, което ги прави известни с производството на малки, сложни части.
- Хибридна машина за леене под налягане: Хибридните машини комбинират предимствата на хидравличните и електрическите устройства, като използват както хидравлична, така и електрическа енергия за генериране на необходимото налягане и мощност. Хибридните машини предлагат добър баланс между скорост, прецизност и енергийна ефективност.
- Вертикална машина за леене под налягане: Вертикалните машини произвеждат части, които изискват формоване с вложки или формоване отгоре. Те имат вертикален затягащ блок, който позволява лесен достъп до формата, което ги прави идеални за създаване на малки или сложни части.
- Машина за леене под налягане с две инжекции: Машините с две инжекции произвеждат части с различни материали или цветове. Устройството има две инжекционни единици, всяка от които може да инжектира чужд материал във формата. Този тип машина обикновено се използва за производство на автомобилни части, като дръжки и копчета.
- Машина за леене под налягане с няколко изстрела: Машините с много изстрели произвеждат части с повече от два материала или цвята. Устройството има множество инжекционни модули, всеки от които може да инжектира различен материал във формата. Този тип машини обикновено се използват за производство на потребителски стоки, като четки за зъби и бръсначи.
- Изцяло електрическа машина за леене под налягане: Изцяло електрическите машини използват електрически двигатели за захранване на инжекционния модул, затягащия механизъм и формата. Те са известни със своята висока прецизност, скорост и енергийна ефективност, което ги прави известни с производството на малки, високопрецизни части.
Това са само няколко от най-разпространените видове машини за леене под налягане. Всяка машина има уникални характеристики и предимства, което прави от съществено значение изборът на подходящо устройство за конкретните производствени изисквания.
Части от машина за леене под налягане
Машините за леене под налягане имат няколко части, които създават пластмасови части от суровини. Ето основните компоненти на машината за леене под налягане:
Бункер: Резервоарът съдържа суровия пластмасов материал, преди да бъде подаден в машината за леене под налягане. Материалът обикновено е под формата на пелети или прах.
Цев: Цевта е дългата, цилиндрична част на машината за леене под налягане, в която се намира винтът, който разтопява и смесва пластмасовия материал.
Винт: Винтът е въртящо се устройство вътре в цевта, което избутва пластмасовия материал напред и го разтапя чрез триене и топлина.
Инжекционен модул: Инжекционният модул включва бункер, варел и шнек и отговаря за топенето и инжектирането на пластмаса във формата.
Затягащо устройство: Затягащото устройство е отговорно за сигурното задържане на матрицата и прилагането на необходимото налягане по време на процеса на леене под налягане.
Форма: Формата е инструментът, който създава формата и размера на пластмасовата част. Формата обикновено е изработена от стомана и се състои от две половини, които пасват една към друга.
Дюза: Дюзата е частта от инжекционния модул, която свързва машината за леене под налягане с матрицата. Разтопеният пластмасов материал се впръсква през дюзата и във формата.
Охладителна система: Охладителната система е отговорна за охлаждането на пластмасовата част, след като се инжектира във формата. Това гарантира, че парчето е втвърдено и може да бъде извадено от формата без повреда.
Контролен панел: Контролният панел е интерфейсът, който позволява на оператора да наблюдава и регулира настройките на машината за леене под налягане, като температура, налягане и време на цикъл.
Всяка от тези части играе критична роля в процеса на леене под налягане и е от съществено значение да се поддържа и оптимизира всяка част, за да се гарантира, че висококачествените части се произвеждат ефективно.
Инструменти за леене под налягане: проектиране и производство
Инструментите за леене под налягане се отнасят до проектиране и производство на форми, използвани в машини за леене под налягане за производство на пластмасови части. Качеството и ефективността на формите пряко влияят върху качеството и производителността на процеса на леене под налягане. Ето основните стъпки в проектирането и производството на инструменти за леене под налягане:
Дизайн на продукта: Първата стъпка в инструментите за леене под налягане е проектирането на продукта, който ще бъде произведен. Дизайнът на продукта включва определяне на размера, формата и материала на частта, както и всякакви специфични характеристики или изисквания.
Дизайн на матрицата: Процесът на проектиране на матрицата започва, след като дизайнът на продукта бъде финализиран. Дизайнерът на матрицата ще определи най-добрия тип форма, броя на необходимите кухини и размера и формата на матрицата.
Конструкция на матрицата: Формата е конструирана въз основа на дизайна на матрицата, като се използват висококачествени материали като стомана или алуминий. Формата обикновено се прави от две половини, всяка от които съдържа една или повече кухини.
Сглобяване на матрицата: След като матрицата е конструирана, тя се сглобява и тества за точност и функционалност. Формата трябва да издържа на налягането и топлината на процеса на леене под налягане.
Тестване и валидиране на матрицата: След като матрицата е сглобена, тя се тества и валидира, за да се гарантира, че произвежда висококачествени части, които отговарят на продуктовите спецификации. Формата може да се наложи да се коригира или модифицира, за да се подобри нейната ефективност.
Поддръжка на матрицата: Редовната поддръжка и ремонт на матрицата са от решаващо значение за гарантиране на нейната дълготрайност и ефективност. Това включва почистване, смазване и подмяна на всякакви износени или повредени части.
Инструментите за леене под налягане изискват прецизност и опит за последователно и ефективно производство на висококачествени части. Като следват цялостен процес на проектиране и производство, производителите могат да направят форми, които отговарят на уникалните изисквания на техните продукти и да оптимизират своите процеси на леене под налягане.
Видове инструменти за леене под налягане
Шприцоването е широко използван производствен процес за производство на части в големи количества. Това включва инжектиране на разтопена пластмаса в кухината на формата и оставянето й да се охлади и втвърди в желаната форма. Инструментите за леене под налягане са процесът на създаване на формите, използвани при леене под налягане. Има няколко вида инструменти за леене под налягане, всеки със своите предимства и недостатъци.
- Форми с две плочи Формите с две плочи са най-простият тип инструменти за леене под налягане. Те се състоят от две плочи, захванати заедно, за да образуват кухина на формата. Разтопената пластмаса се инжектира в отвора през порта и се оставя да се охлади и втвърди. След като частта е създадена, двете плочи се разделят и количеството се изхвърля. Формите с две плочи обикновено се използват за малки до средни по размер компоненти с проста геометрия.
- Форми с три плочи. Формите с три плочи са подобни на формите с две плочи, но имат допълнителна плоча, известна като плоча за отстраняване, която отделя формованата част от системата на плъзгача. Системата за плъзгачи е каналната мрежа, която доставя разтопената пластмаса в кухината на формата. Формите с три плочи се използват за по-значими части и по-сложни геометрии.
- Форми за горещ канал В калъпите за горещ канал разтопената пластмаса се инжектира директно в кухината на формата през серия от нагрети канали, а не през шибър. Това намалява загубата на материал в системата на циркуляра, което води до по-ефективен процес. Формите за горещ канал се използват за производство на големи обеми на сложни части.
- Семейни форми Семейните форми произвеждат множество части в една форма. Те имат различни кухини, подредени по начин, който позволява производството на множество домейни едновременно. Семейните форми обикновено се използват за части с малки до средни обеми.
- Форми за вложки. Формите за вложки произвеждат части, които изискват метални или пластмасови вложки. Вложките се поставят в кухината на формата, преди да се инжектира разтопената пластмаса. След като пластмасата се охлади и втвърди, частта и вложката са трайно свързани. Формите за вложки се използват за позиции, които изискват здравина, издръжливост или естетическа привлекателност.
- Формоване върху формоването върху формовката върху формовката е процес, при който една част се формова върху друга. Често се използва за позиции, които изискват мек допир или подобрен захват. Формоването включва първо поставяне на субстрат или основна част и след това формоване на втори материал върху него. Вторият материал може да бъде различен вид пластмаса, материал, подобен на гума, или термопластичен еластомер.
В заключение, изборът на инструменти за леене под налягане зависи от вида на произвежданата част, необходимия производствен обем и нивото на сложност, включено в дизайна на частта. Изборът на подходящ инструмент е от съществено значение, за да се гарантира, че процесът е ефективен и рентабилен.
Насоки за проектиране на леене под налягане
Шприцоването е широко използван производствен процес за производство на пластмасови части. Проектирането на части за леене под налягане изисква добро разбиране на процеса, материалите и насоките за проектиране, които трябва да се следват, за да се гарантира, че детайлите могат да бъдат успешно произведени. Ето някои насоки за проектиране на леене под налягане, които трябва да имате предвид:
Дебелина на стената, Дебелината на стената на частта трябва да бъде еднаква и възможно най-тънка, като същевременно поддържа необходимата здравина и функционалност. Това помага да се намали времето за охлаждане и цикъл и минимизира риска от изкривяване и следи от потъване.
Ребра и издатини Ребрата и издатините могат да се използват за увеличаване на здравината и твърдостта на частта. Ребрата трябва да са не повече от 60% от номиналната дебелина на стената, а издатините трябва да са 1.5 пъти номиналната дебелина на стената.
Ъгъл на теглене, Ъгъл на теглене от поне 1-2 градуса трябва да се използва върху всички вертикални повърхности, за да се улесни изхвърлянето на частта и да се предотврати повреда на формата.
Филтри и радиуси Трябва да се избягват остри ъгли и ръбове, за да се предотврати концентрацията на напрежение, което може да доведе до напукване и повреда. Вместо това, филетата и радиусите трябва да разпределят напрежението и да подобрят здравината на частта.
Порти и плъзгачи Разположението и дизайнът на вратовете и водачите са критични за постигане на добро качество на детайлите. Входовете трябва да са възможно най-малки в най-дебелата част на детайла. Пътеките трябва да бъдат проектирани така, че да минимизират спада на налягането и да увеличат максимално потока.
Повърхностно покритие Повърхностното покритие на частта трябва да бъде определено въз основа на изискванията за приложение. Може да се изисква по-висока повърхностна обработка за видими части, докато по-ниска повърхност може да е приемлива за скрити части.
Избор на материал Материалът, избран за частта, трябва да е подходящ за леене под налягане и да отговаря на изискваните механични, термични и химични свойства.
Вторични операции при леене под налягане
Шприцоването е универсален производствен процес, използван за производството на различни пластмасови части. В допълнение към първичния процес на формоване, много позиции изискват вторични операции за постигане на желаната форма, покритие или функционалност. Ето някои ежедневни вторични операции при леене под налягане:
- Изрязването е отстраняване на излишния материал от формованата част, след като е бил изваден от матрицата. Това обикновено се прави с помощта на преса за подрязване или CNC машина. Често се налага подрязване, за да се постигне крайната форма и размер на детайла.
- Заваряването комбинира две или повече пластмасови части с помощта на топлина, налягане или комбинация от двете. Това често се използва за създаване на по-големи или по-сложни елементи, които не могат да бъдат произведени в една матрица.
- Декорирането е процес на добавяне на визуални или функционални характеристики към повърхността на формованата част. Това може да включва рисуване, отпечатване, етикетиране или прилагане на текстура или модел.
- Сглобяването е процес на съединяване на множество части за създаване на цялостен продукт. Това може да стане с помощта на крепежни елементи, лепила или други техники за свързване.
- Формоване на вложка Формоването на вложка е формоване на пластмаса около предварително формована метална или пластмасова вложка. Това често се използва за създаване на части с високо ниво на здравина или издръжливост.
- Формоване върху формоване върху формоване върху формоване върху предварително формован детайл. Това може да добави мека на допир повърхност, да подобри сцеплението или да създаде двуцветно или многоматериално парче.
- Покритието нанася тънък слой материал върху повърхността на частта, за да подобри нейния външен вид, издръжливост или други свойства. Това може да включва покрития като хром, никел или прахови покрития.
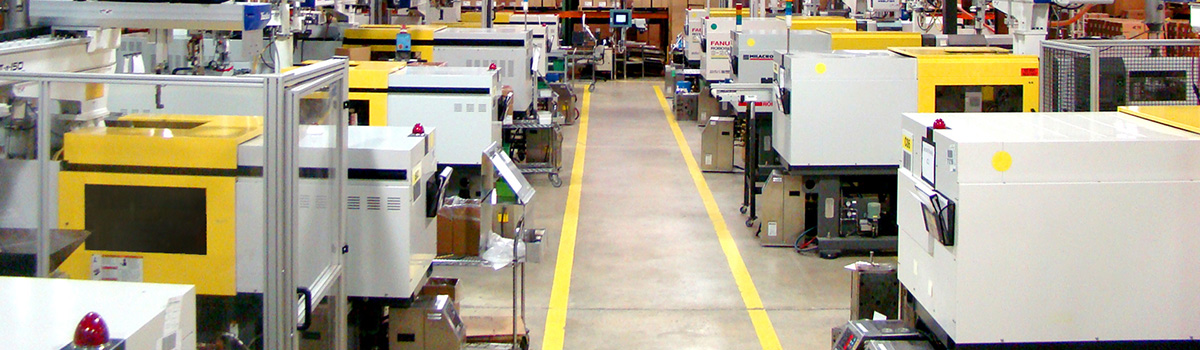
Предимства на пластмасовото шприцоване
Пластмасовото леене под налягане е широко използван производствен процес за производство на пластмасови части с висока точност, последователност и качество. Това включва инжектиране на разтопена пластмаса в кухината на формата и оставянето й да се охлади и втвърди. Ето някои предимства на шприцването на пластмаса:
- Висока ефективност и производителност Пластмасовото леене под налягане е високоефективен и автоматизиран процес, който може да произвежда големи обеми части с висока консистенция и качество. С усъвършенствана технология за автоматизация, времето на производствения цикъл може да бъде намалено до секунди, което позволява производство на голям обем на сложни и сложни части.
- Висока точност и прецизност Инжекционното формоване повишава точността и прецизността при производството на сложни и сложни части. Компютърно контролирани машини и усъвършенстван софтуер позволяват тесни допуски с висока повторяемост и точност.
- Универсалност Инжекционното формоване е универсален процес, който може да произвежда широка гама от пластмасови части с различни размери, форми и сложност. Процесът може да се използва за направата на всичко - от малки парчета със сложни детайли до големи количества със сложна геометрия.
- Гъвкавост на материала Инжекционното формоване може да използва широка гама от пластмасови материали, включително термопласти, реактивни термореактивни материали и еластомери. Това позволява да се произвеждат части с различни механични, термични и химични свойства.
- Производство с ниски отпадъци Инжекционното формоване е производствен процес с ниски отпадъци, тъй като генерира минимални отпадъци по време на производството. Всеки излишен материал може лесно да се рециклира и използва повторно в производството, което го прави екологичен производствен процес.
- Намалени разходи за труд Високата степен на автоматизация при леене под налягане свежда до минимум необходимостта от трудоемки процеси, като значително намалява разходите за труд. Това също така намалява риска от човешка грешка, подобрявайки качеството и консистенцията на крайния продукт.
- Намалени постпроизводствени операции Инжекционното формоване произвежда части с висока точност и последователност, намалявайки необходимостта от постпроизводствени операции като подрязване, пробиване или фрезоване. Това намалява времето за производство и цената на крайния продукт.
- Съгласуваност и качество Инжекционното формоване произвежда части с високо ниво на съгласуваност и качество. Усъвършенстваната технология и компютърно управляваните машини гарантират, че всеки детайл е идентичен по форма, размер и качество.
- Гъвкавост на дизайна Инжекционното формоване предлага висока степен на гъвкавост на дизайна, тъй като позволява производството на части със сложни геометрии, подрязвания и сложни детайли. Това ще позволи на дизайнерите да създават изделия с уникални форми и функции, които не могат да бъдат направени чрез други производствени процеси.
- Рентабилно за производство на голям обем Инжекционното формоване е рентабилен процес за производство на пластмасови части. Първоначалните разходи за инструментална екипировка могат да бъдат високи, но разходите за част намаляват с увеличаване на обема на производството. Това го прави идеален процес за производство на големи количества части.
Пластмасовото шприцване предлага много предимства, което го прави популярен избор за производство на пластмасови части. Неговата висока ефективност, точност, гъвкавост, гъвкавост на материала, ниско производство на отпадъци, намалени разходи за труд и последователност и качество го правят идеален процес за различни приложения. Способността да се произвеждат сложни и сложни части с висока гъвкавост на дизайна и рентабилност за производство в голям обем го прави много търсен производствен процес.
Недостатъци на шприцоването на пластмаса
Пластмасовото леене под налягане е широко използван производствен процес, който включва инжектиране на разтопена пластмаса в кухината на формата за производство на широка гама от пластмасови части и продукти. Въпреки че шприцоването на пластмаса има много предимства, има и няколко недостатъка. Ето някои от основните недостатъци на пластмасовото шприцване:
- Високи разходи за инструментална екипировка: Цената за проектиране и производство на матрица за пластмасово леене под налягане може да бъде много висока. Това е така, защото формата трябва да бъде направена от висококачествени материали и прецизно обработена, за да се създаде желаната част. В допълнение, разходите за проектиране и производство на матрицата може да са непосилни за малки производствени серии, което прави шприцването на пластмаса по-малко икономично за производство в малък обем.
- Дълги времена за изпълнение: Процесът на проектиране и производство на матрица за пластмасово леене под налягане може да отнеме много време, което може да забави производството на пластмасови части. Това може да бъде особено проблематично за предприятия, които трябва бързо да реагират на промените в пазарното търсене или бързо да разработват нови продукти.
- Ограничена гъвкавост: След като формата е проектирана и произведена, е по-лесно и по-евтино да промените дизайна или да модифицирате производствения процес. Това може да ограничи гъвкавостта на пластмасовото шприцване и да го направи по-малко подходящо за производство на продукти по поръчка или единствени по рода си.
- Загриженост за околната среда: Инжекционното формоване на пластмаса разчита на големи количества пластмаса, което може да има отрицателно въздействие върху околната среда. Пластмасовите отпадъци са основен екологичен проблем и шприцоването на пластмаса може да допринесе за този проблем. Освен това процесът на производство на пластмасови продукти изисква използването на енергия и природни ресурси, което може допълнително да повлияе на околната среда.
- Висок процент скрап: Пластмасовото шприцване може да произведе значителен скрап, чието изхвърляне или рециклиране може да бъде скъпо. Освен това, производството на скрап може да увеличи общите производствени разходи и да намали ефективността на производствения процес.
- Ограничени възможности за материали: Пластмасовото шприцване се използва предимно за производство на части и продукти от термопластични материали, които имат ограничени свойства в сравнение с други материали като метали или керамика. Това може да направи формоването под налягане на пластмаса по-малко подходящо за приложения, които изискват висока якост, температурна устойчивост или други усъвършенствани свойства.
Ограничения на леенето под налягане на пластмаса
Въпреки че шприцоването на пластмаса предлага множество предимства, някои ограничения също са свързани с процеса. Ето някои ограничения на пластмасовото шприцване:
Високи първоначални разходи за инструменти: Първоначалните разходи за проектиране и производство на формата могат да бъдат увеличени. Формата трябва да бъде прецизна и издръжлива, за да издържи многократния процес на леене под налягане, а това може да изисква значителна предварителна инвестиция, особено за сложни или големи форми.
Време за изпълнение: Времето за производство на матрицата може да бъде значително, вариращо от седмици до месеци, в зависимост от сложността и размера на матрицата. Това може да доведе до забавяне на производствения график, особено за чувствителни към времето проекти.
Ограничения на дизайна: Инжекционното формоване има определени ограничения на дизайна, които трябва да се вземат предвид. Например, постигането на еднаква дебелина на стената в цялата част е от решаващо значение за осигуряване на правилно пълнене и охлаждане. Освен това са необходими ъгли на теглене на вертикални повърхности, за да се позволи лесно изваждане от формата.
Ограничения за размера на частите: Шприцоването е най-подходящо за производство на малки до средни по размер части. Големите части може да изискват специализирано оборудване и по-големи форми, което увеличава разходите и сложността.
Избор на материал: Докато леенето под налягане позволява широка гама от пластмасови материали, изборът на материал все още е ограничен в сравнение с други производствени процеси. Материали с високи точки на топене или лоши характеристики на течливост може да не са подходящи за леене под налягане.
Повърхностно покритие: Процесът на леене под налягане може да доведе до видими плетени линии или разделителни линии на повърхността на частта. Постигането на висококачествено покритие на повърхността може да бъде предизвикателство и може да са необходими други методи, като полиране или покритие.
Ограничени подрязвания: Подрязванията са характеристики или детайли на детайл, които не позволяват лесното му отстраняване от матрицата. Подрязванията могат да усложнят процеса на изхвърляне и да изискват допълнителни характеристики на матрицата или вторични операции за постигане на желаната геометрия на детайла.
Ограничени възможности за ремонт: Ако матрицата е повредена или се нуждае от модификация, ремонтът или промяната на съществуващата форма може да бъде скъпо и отнема много време. Понякога може да се наложи производството на изцяло нова форма, което води до допълнителни разходи и забавяния.
Въпреки тези ограничения, леенето под налягане на пластмаса остава много гъвкав и широко използван производствен процес за производство на пластмасови части. Чрез внимателно разглеждане на тези ограничения по време на етапите на проектиране и планиране на производството е възможно да се смекчи тяхното въздействие и ефективно да се използват предимствата на леенето под налягане.
Приложения на леене под налягане на пластмаса
Пластмасовото леене под налягане е универсален производствен процес, който може да произвежда широка гама от пластмасови части. Ето някои от приложенията на шприцването на пластмаса:
- Потребителски продукти: Шприцоването се използва широко за производството на различни продукти, като играчки, кухненски прибори и електроника. Процесът може да произвежда висококачествени части със сложни геометрии и прецизни размери, което го прави идеален за продукти, които изискват строги толеранси и сложни форми.
- Автомобилни части: Много автомобилни пластмасови компоненти, като компоненти на арматурното табло, дръжки на вратите и осветление, се произвеждат чрез леене под налягане. Процесът позволява големи производствени обеми и постоянно качество, което го прави рентабилен вариант за производителите на автомобили.
- Медицински устройства: Инжекционното формоване обикновено се използва за производство на медицински устройства, като спринцовки, инхалатори и диагностично оборудване. Процесът може да произвежда части с висока прецизност и последователност, гарантирайки качеството и надеждността на устройствата.
- Опаковка: Шприцоването се използва широко за производство на пластмасови опаковки, като контейнери, капаци и капачки. Процесът може да има части с постоянни размери и висококачествени покрития, което го прави идеален за опаковане с привлекателен външен вид и сигурно прилягане.
- Аерокосмическа промишленост и отбрана: Инжекционното формоване произвежда различни аерокосмически и отбранителни компоненти, като интериор на самолети, осветление и комуникационни системи. Процесът може да има части с леки, издръжливи материали, което ги прави подходящи за приложения, които изискват високи съотношения на якост към тегло.
- Строителство: Инжекционното формоване може да произвежда различни строителни материали, като пластмасови плочки, покриви и сайдинг. Процесът може да има части с постоянни размери и висококачествени покрития, което го прави привлекателна опция за строителните компании.
- Спорт и отдих: Шприцоването се използва широко в производството на спортно оборудване, като стикове за голф, тенис ракети и компоненти за велосипеди. Процесът може да произвежда части с леки материали и прецизни геометрии, гарантирайки производителността и издръжливостта на оборудването.
Като цяло леенето под налягане на пластмаса е универсален и широко използван производствен процес, който може да произвежда висококачествени пластмасови части за различни приложения. Процесът може да бъде пригоден да отговаря на специфични изисквания за проектиране и производство, което го прави привлекателна опция за производители в множество индустрии.
Автомобилна индустрия и леене под налягане на пластмаса
Автомобилната индустрия е значителен потребител на технологията за леене под налягане на пластмаса. Процесът на леене под налягане на пластмаса направи революция в производството на автомобилни части и компоненти, правейки възможно производството на сложни форми с висока прецизност и точност. Ето някои от начините, по които шприцването на пластмаса се използва в автомобилната индустрия:
- Вътрешни части: Пластмасовото шприцване произвежда много вътрешни фактори, включително компоненти на арматурното табло, панели на вратите, декоративни елементи и др. Тези части могат да бъдат проектирани със сложни форми и текстури и персонализирани, за да отговарят на изискванията за стил и функционалност на всеки модел превозно средство.
- Външни части: Пластмасовото шприцване се използва и за производството на различни външни елементи, включително брони, решетки, странични огледала и др. Тези части могат да бъдат проектирани да издържат на екстремни метеорологични условия и са направени в множество цветове и покрития.
- Компоненти под капака: Пластмасовото шприцване произвежда много елементи под капака, включително капаци на двигателя, системи за всмукване на въздух и части на охладителната система. Тези компоненти изискват висока температурна и химическа устойчивост, което може да се постигне с термопластични материали.
- Електрически и електронни компоненти: Пластмасовото шприцване произвежда различни електрически и електронни компоненти, включително конектори, корпуси и сензори. Тези компоненти изискват висока прецизност и надеждност, които могат да бъдат постигнати с точността и последователността на пластмасовото леене под налягане.
- Олекотяване: Пластмасовото шприцоване често се използва за производство на леки части, които помагат за намаляване на общото тегло на превозното средство, подобрявайки горивната ефективност и намалявайки емисиите. Олекотяването може също така да подобри управлението и работата на превозното средство.
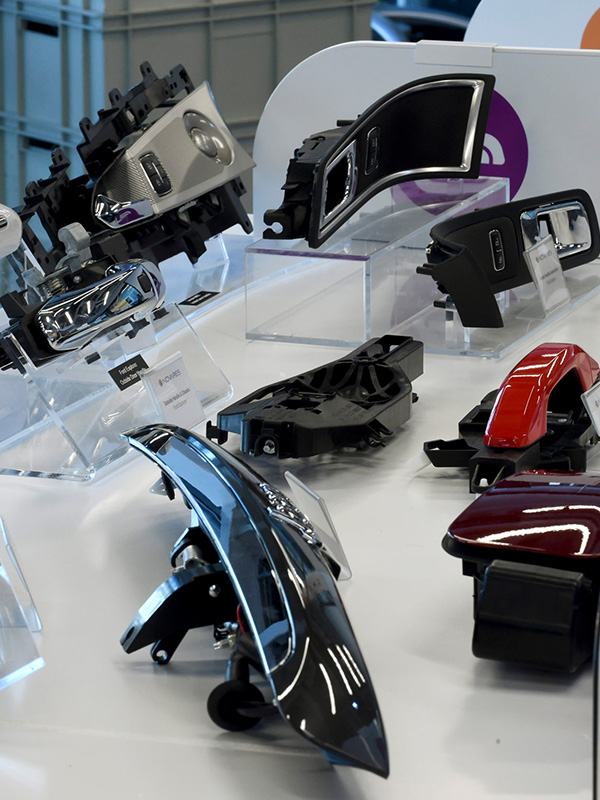
Медицинска индустрия и леене под налягане на пластмаса
Пластмасовото леене под налягане се използва широко в медицинската индустрия за производство на различни медицински устройства и компоненти. Процесът на леене под налягане на пластмаса позволява производството на сложни форми с висока прецизност и точност, което го прави идеален метод за производство за много медицински приложения. Ето някои от начините, по които шприцването на пластмаса се използва в медицинската индустрия:
- Медицински устройства: Пластмасовото шприцоване произвежда различни медицински устройства, включително хирургически инструменти, диагностични инструменти, системи за доставяне на лекарства и т.н. Тези устройства често изискват висока прецизност и точност, а пластмасовото шприцоване може да отговори на тези изисквания.
- Импланти: Пластмасовото шприцване се използва и за производството на различни импланти, включително ставни заместители, зъбни импланти и др. Тези импланти могат да бъдат проектирани така, че да съответстват на анатомията на пациента и да бъдат произведени от биосъвместими материали.
- Лабораторно оборудване: Пластмасовото шприцване произвежда пипети, микроплаки и епруветки. Тези компоненти изискват висока прецизност и точност, за да осигурят надеждни резултати.
- Опаковка: Пластмасовото шприцване се използва за производство на опаковки за медицински изделия, включително стерилни бариерни системи и персонализирани опаковки за отделни продукти. Тези решения за опаковане могат да помогнат за поддържане на стерилността и целостта на медицинското изделие.
- Устройства за еднократна употреба: Пластмасовото шприцване често произвежда устройства за еднократна употреба като спринцовки, игли и катетри. Тези устройства могат да бъдат направени в голям обем на ниска цена и могат да помогнат за предотвратяване на разпространението на инфекции в здравните заведения.
Потребителски продукти и леене под налягане на пластмаса
Пластмасовото шприцване се използва широко в производството на потребителски продукти поради своята гъвкавост, ефективност и рентабилност. Процесът на леене под налягане на пластмаса позволява производството на сложни форми с висока прецизност и точност, което го прави идеален метод за производство за много потребителски приложения. Ето някои от начините, по които шприцването на пластмаса се използва в производството на потребителски продукти:
- Играчки: Пластмасовото шприцване произвежда широка гама от играчки, от малки фигурки до по-големи комплекти за игра. Процесът позволява създаване на сложни дизайни и детайли и изработка на играчки в различни цветове и материали.
- Домакински стоки: Пластмасовото шприцване произвежда различни домакински стоки, включително кухненски прибори, контейнери за съхранение и почистващи препарати. Тези продукти могат да бъдат проектирани да бъдат издръжливи, леки и лесни за използване.
- Електроника: Пластмасовото шприцване произвежда много електронни компоненти, включително компютърни корпуси, калъфи за телефони и зарядни устройства. Прецизността и точността на процеса гарантират, че тези компоненти са направени с висока степен на последователност и надеждност.
- Продукти за лична хигиена: Пластмасовото шприцване произвежда уникални продукти за грижа, включително четки за зъби, бръсначи и четки за коса. Тези продукти изискват висока прецизност и точност, за да осигурят лесна употреба и безопасност.
- Автомобилни аксесоари: Пластмасовото шприцоване произвежда набор от автомобилни аксесоари, включително компоненти на таблото, поставки за чаши и др. Тези компоненти могат да бъдат проектирани да бъдат леки, издръжливи и устойчиви на износване при ежедневна употреба.
Екологични съображения при леене под налягане на пластмаса
Пластмасовото леене под налягане е широко използван производствен процес, но има значителни последици за околната среда. Ето някои от екологичните съображения при шприцването на пластмаса:
- Избор на материал: Изборът на пластмасов материал, използван при леене под налягане, може значително да повлияе на околната среда. Някои материали са биоразградими или рециклируеми, докато други не са. Използването на биоразградими или рециклируеми материали може да помогне за намаляване на въздействието върху околната среда от шприцването на пластмаси.
- Консумация на енергия: Пластмасовото шприцване изисква значителна енергия за разтопяване на пластмасата и инжектирането й във формата. Енергийно ефективно оборудване и процеси, като например електрически машини и затворени системи, могат да намалят потреблението на енергия и въздействието върху околната среда.
- Управление на отпадъците: Пластмасовото шприцване генерира отпадъци от излишен материал, дефектни части и опаковки. Правилните практики за управление на отпадъците, като рециклиране и повторно използване на отпадъчни материали, могат да помогнат за намаляване на въздействието върху околната среда от шприцването на пластмаса.
- Употреба на химикали: Някои химикали в пластмасовите шприцовани форми, като например отделящи агенти за плесени и почистващи разтворители, могат да навредят на околната среда. Използването на екологични алтернативи или минимизирането на употребата на тези химикали може да помогне за намаляване на въздействието върху околната среда.
- Съображения за края на жизнения цикъл: Пластмасовите продукти, произведени чрез леене под налягане, често се озовават на сметища, чието разграждане може да отнеме стотици години. Проектирането на продукти за рециклиране или биоразградимост може да намали въздействието върху околната среда от шприцването на пластмаса.
Бъдещето на шприцоването на пластмаса
Бъдещето на формоването под налягане на пластмаса изглежда обещаващо, тъй като напредъкът в технологиите и материалите се очаква да направи процеса още по-ефективен, рентабилен и устойчив. Ето някои от тенденциите и разработките, които вероятно ще оформят бъдещето на шприцването на пластмаса:
- Адитивно производство: Адитивното производство, известно още като 3D принтиране, е нововъзникваща технология, която потенциално може да трансформира шприцването на пластмаса. Използвайки 3D печат за създаване на форми, производителите могат значително да намалят времето и разходите, свързани с традиционните техники за производство на форми.
- Интелигентно производство: Интелигентното производство, което включва автоматизация, анализ на данни и машинно обучение, се очаква да революционизира шприцоването на пластмаса. Производителите могат да подобрят ефективността, да намалят отпадъците и да увеличат производителността, като използват сензори и анализ на данни за оптимизиране на процесите.
- Устойчиви материали: Устойчивите материали, като биопластмаси и рециклирани пластмаси, стават все по-популярни в индустрията за леене под налягане на пластмаси. Тези материали предлагат ползи за околната среда и могат да помогнат на производителите да постигнат целите за устойчивост.
- Микро формоване: Микро формоването, което включва производство на малки части с висока точност, става все по-критично в индустрии като здравеопазване и електроника. Очаква се напредъкът в технологиите и материалите да направи микро формоването по-достъпно и рентабилно.
- Персонализиране: Тъй като потребителите изискват по-персонализирани продукти, шприцоването на пластмаса се очаква да стане по-гъвкаво и персонализирано. Напредъкът в технологиите, като обратна връзка в реално време и машинно обучение, ще позволи на производителите да произвеждат персонализирани продукти бързо и ефективно.
Заключение:
Пластмасовото леене под налягане е много гъвкав и ефективен производствен процес, който революционизира производството на широка гама от продукти. От медицински устройства до автомобилни компоненти, леенето под налягане на пластмаса предлага множество предимства пред други производствени процеси, включително високи производствени нива, гъвкавост на дизайна и рентабилност. С непрекъснатия напредък в технологиите и материалите бъдещето на шприцоването на пластмаса изглежда светло и този процес вероятно ще играе още по-важна роля в производствената индустрия през следващите години.