Термопластично леене под налягане
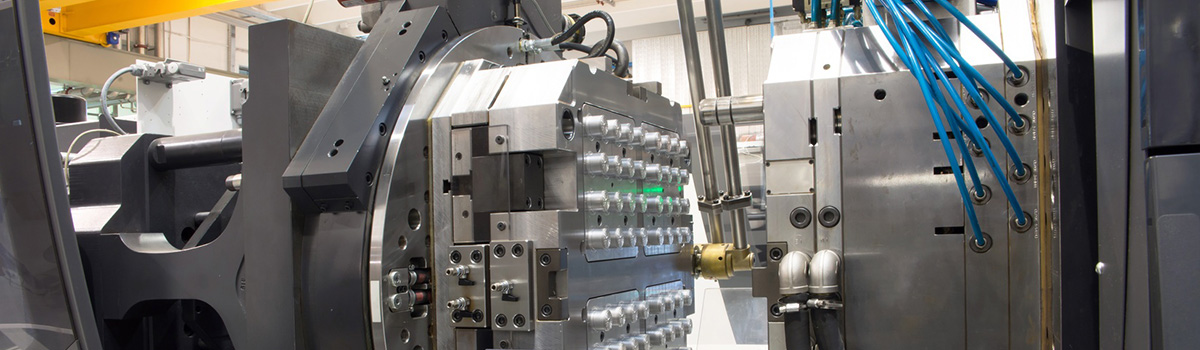
Термопластичното шприцване е популярен производствен процес, използван за създаване на различни пластмасови части за множество индустрии. Този процес включва топенето на пластмасови пелети и шприцването им във форма за получаване на триизмерна форма. Термопластичното леене под налягане е високоефективно и рентабилно за производство на големи обеми висококачествени пластмасови части с тесни допуски. Това изчерпателно ръководство ще изследва различните аспекти на термопластичното леене под налягане, включително неговите предимства и недостатъци, видовете използвани термопласти, процеса на леене под налягане, съображения за дизайн и много други.
История на термопластичното леене под налягане
Историята на термопластичното леене под налягане обхваща повече от век на технологичен напредък, развитие на материалите и индустриални приложения. От своето скромно начало като процес на формоване на целулоид до днешната сложна технология, леенето под налягане продължава да бъде жизненоважна производствена техника, движеща иновациите и оформяйки различни индустрии.
- Ранни разработки:Джон Уесли Хаят и неговият брат Исая разработиха първата практична машина за леене под налягане, проследявайки произхода на термопластичното леене под налягане до края на 19 век. През 1872 г. те патентоват устройство, което използва бутало за инжектиране на целулоид в кухина на матрицата, създавайки твърди предмети. Този пробив постави основата на съвременния процес на леене под налягане.
- Напредък в материалите:В началото на 20-ти век въвеждането на нови синтетични полимери отвори нови възможности за леене под налягане. Бакелитът, фенолна смола, стана популярен материал за формоване поради отличните си електроизолационни свойства. През 1930-те и 1940-те години на миналия век напредъкът в химията на полимерите доведе до разработването на други термопласти, като полистирен и полиетилен, които допълнително разшириха гамата от материали, подходящи за леене под налягане.
- Индустриално приемане: Широкото разпространение на термопластичното леене под налягане започва през 1950-те години на миналия век, когато производителите признават неговата рентабилност и гъвкавост. Въвеждането на машини с високо налягане позволи по-бързи времена на цикъла и увеличени производствени обеми. В резултат на това се появи разнообразна селекция от продукти за лична и промишлена употреба. Те включват компоненти за автомобили, домакински уреди и играчки.
- Технологични иновации:През десетилетията технологията за леене под налягане продължи да се развива. През 1960-те години се появяват машини с компютърно управление, позволяващи прецизен контрол върху процеса на формоване. Въвеждането на системи с горещи канали през 1980-те години на миналия век намали отпадъците и подобри ефективността, като елиминира нуждата от канали и канали. През последните години напредъкът в автоматизацията, роботиката и 3D печата допълнително революционизираха индустрията за леене под налягане, позволявайки сложни дизайни и намалявайки времето за производство.
- Устойчивост и рециклиране:С нарастващите опасения за околната среда индустрията за леене под налягане възприе мерки за устойчивост. Производителите са разработили био-базирани и рециклирани термопласти, намалявайки зависимостта от материали, базирани на изкопаеми горива. Освен това, подобрените технологии за рециклиране позволиха повторна обработка на пост-потребителски и постиндустриални отпадъци, минимизирайки въздействието върху околната среда на термопластичното шприцване.
- Бъдещи перспективи:Бъдещето на термопластичното леене под налягане изглежда обещаващо. Индустрията проучва иновации като микроинжекционно формоване за миниатюрни компоненти, многоматериални техники и техники за формоване върху сложни части и интегриране на интелигентни технологии за наблюдение и оптимизация на процеси. Освен това изследователите очакват напредъкът в биоразградимите материали и производството на добавки да революционизират областта, правейки леенето под налягане още по-устойчиво и гъвкаво.
Предимства на термопластичното шприцване
Термопластичното шприцване предлага множество предимства за производителите. Той осигурява гъвкавост на дизайна, позволявайки сложни и сложни дизайни с различни функции. Процесът е рентабилен, намалява материалните отпадъци и намалява разходите за единица продукция. Термопластичното шприцване поддържа множество материали, осигурявайки гъвкавост за различни приложения.
- Гъвкавост на дизайна:Термопластичното шприцване позволява сложни и сложни дизайни с характеристики като подрязвания, тънки стени и различни дебелини, предоставяйки на дизайнерите огромна свобода.
- Ефективност на разходите: Процесът е високоефективен, намалява материалните отпадъци и намалява разходите за единица продукция. Едновременното формоване на множество части и бързите производствени цикли допринасят за спестяване на разходи.
- Универсалност на материала: Термопластичното шприцоване поддържа широка гама от материали, което позволява на производителите да изберат най-подходящата опция за всяко приложение, включително твърди или гъвкави, прозрачни или непрозрачни и химически устойчиви материали.
- Сила и издръжливост:Инжекционно формованите термопласти могат да проявят отлични механични свойства, като висока якост, издръжливост и устойчивост на удар. Опциите за подсилване, като стъклени или въглеродни влакна, допълнително подобряват тези свойства.
- Последователност и качество:Инжекционното формоване гарантира постоянно качество от част до част и точност на размерите, осигурявайки строги толеранси и надеждни продукти. Процесът също така осигурява гладко и равномерно покритие на повърхността, елиминирайки необходимостта от допълнителни довършителни операции.
- Мащабируемост и масово производство:Шприцоването е мащабируемо от малки до големи обеми, което го прави подходящо за масово производство. След като производителите създадат формата, те могат да произвеждат големи количества идентични части с минимални вариации.
- Интегриране и сглобяване:Инжекционно формованите части могат да включват множество компоненти в една част, намалявайки необходимостта от допълнителни процеси на сглобяване. Тази интеграция подобрява производителността на продукта, намалява времето за сглобяване и намалява разходите.
- Устойчивост:Индустрията за леене под налягане показва нарастващ фокус върху устойчивостта. Наличието на био базирани и рециклирани материали позволява производството на екологично чисти продукти. Ефективното използване на материалите и възможността за рециклиране на термопластмасите допринасят за по-екологичния производствен процес.
Тези предимства го превърнаха в широко възприет производствен метод в различни индустрии, осигуряващ висококачествени, рентабилни и екологично чисти решения за сложни продуктови изисквания.
Недостатъци на термопластичното шприцване
Докато термопластичното шприцване предлага множество предимства, има и няколко недостатъка. Производителите трябва внимателно да оценят тези фактори и да ги претеглят спрямо ползите, за да определят пригодността на термопластичното леене под налягане за техните специфични приложения.
- Висока първоначална инвестиция: Създаването на операция за термопластично леене под налягане изисква значителна първоначална инвестиция в дизайна и производството на матрицата и закупуване на специализирани машини. Разходите, свързани със създаването на форми и инструменти, могат да бъдат значителни, особено за сложни и сложни дизайни.
- Ограничения на дизайна: Докато термопластичното леене под налягане предлага гъвкавост на дизайна, съществуват определени ограничения. Например, постигането на еднаква дебелина на стената в цялата част може да бъде предизвикателство, което води до вариации в разпределението на материала и потенциални структурни слабости. Освен това наличието на подрязвания или сложни геометрии може да изисква използването на допълнителни характеристики на формата или вторични операции, увеличавайки разходите и времето за производство.
- Дълги срокове:Процесът на проектиране и производство на форми за леене под налягане може да отнеме много време, което води до по-дълги срокове за разработване на продукта. Процесът на повторение на дизайна, производството на матрици и тестването могат да добавят значително време към цялостната производствена линия, което може да не е подходящо за проекти с кратки срокове.
- Ограничения за избор на материал:Въпреки че термопластичното шприцоване поддържа широка гама от материали, има определени ограничения и ограничения. Някои материали може да имат специфични изисквания за обработка или ограничена наличност, което оказва влияние върху избора на дизайн и избора на материал за конкретно приложение.
- Ограничения за размера на частите:Машините за леене под налягане имат ограничения на размера, както по отношение на физическия размер на устройството, така и на размера на формите, които могат да поемат. Производството на огромни части може да изисква специализирано оборудване или алтернативни методи на производство.
- Влияние върху околната среда:Въпреки че индустрията работи за устойчивост, процесът на термопластично шприцоване все още генерира отпадъчен материал, включително скрап и лейки. Правилното изхвърляне и рециклиране на тези материали е необходимо за минимизиране на въздействието върху околната среда.
- Сложността на оптимизацията на процеса:Постигането на оптимални параметри на процеса за термопластично шприцоване може да бъде сложно и отнема много време. Производителите трябва внимателно да контролират и оптимизират температурата, налягането, скоростите на охлаждане и времената на цикъла, за да осигурят постоянно качество на частите и минимизиране на дефектите.
Видове термопласти, използвани при леене под налягане
Това са само няколко примера за термопласти, които обикновено се използват при леене под налягане. Всеки материал има уникални свойства, което го прави подходящ за специфични приложения въз основа на здравина, гъвкавост, химическа устойчивост, прозрачност и цена. Производителите трябва да вземат предвид тези свойства и изисквания, когато избират подходящия термопласт за своите проекти за леене под налягане.
- Полипропилен (PP):Полипропиленът е универсален термопласт, който обикновено се използва при леене под налягане. Предлага отлична химическа устойчивост, ниска плътност и добра ударна якост. PP (полипропилен) има широко приложение в опаковки, автомобилни компоненти, домакински уреди и медицински устройства.
- Полиетилен (PE):Полиетиленът е друг широко използван термопласт при леене под налягане. Предлага се в различни форми, като полиетилен с висока плътност (HDPE) и полиетилен с ниска плътност (LDPE). PE предлага добра химическа устойчивост, издръжливост и гъвкавост, което го прави подходящ за бутилки, контейнери и тръби.
- Полистирен (PS):Полистиролът е универсален термопласт, известен със своята чистота, твърдост и достъпност. Намира обичайна употреба в опаковки, потребителски стоки и продукти за еднократна употреба. PS (полистирен) позволява бърза обработка и осигурява добра стабилност на размерите, но може да бъде крехък и податлив на напукване при въздействие на околната среда.
- Акрилонитрил бутадиен стирен (ABS): ABS е популярен термопласт, известен със своята отлична устойчивост на удар и издръжливост. Той съчетава свойствата на акрилонитрил, бутадиен и стирен, за да създаде универсален материал, подходящ за автомобилни части, електронни корпуси и играчки.
- Поливинилхлорид (PVC): PVC е широко използван термопласт, известен със своята отлична химическа устойчивост, издръжливост и ниска цена. Може да бъде твърд или гъвкав в зависимост от формулировката и използваните добавки. PVC (поливинилхлорид) намира широко приложение в строителството, електрическа изолация, продукти за здравеопазване и опаковки.
- Поликарбонат (PC): Поликарбонатът е прозрачен термопласт с изключителна удароустойчивост и висока устойчивост на топлина. Намира обичайна употреба в приложения, които изискват оптична яснота, като автомобилни компоненти, предпазни каски и електронни дисплеи.
- Найлон (полиамид):Найлонът е здрав и издръжлив термопласт, известен със своите отлични механични свойства и химическа устойчивост. Намира обичайна употреба в приложения, които изискват висока якост, като автомобилни части, промишлени компоненти и потребителски стоки.
- Полиетилен терефталат (PET):PET е популярен термопласт за производство на бутилки, контейнери и опаковъчни материали. Предлага добра прозрачност, химическа устойчивост и бариерни свойства, което го прави подходящ за приложения в храни и напитки.
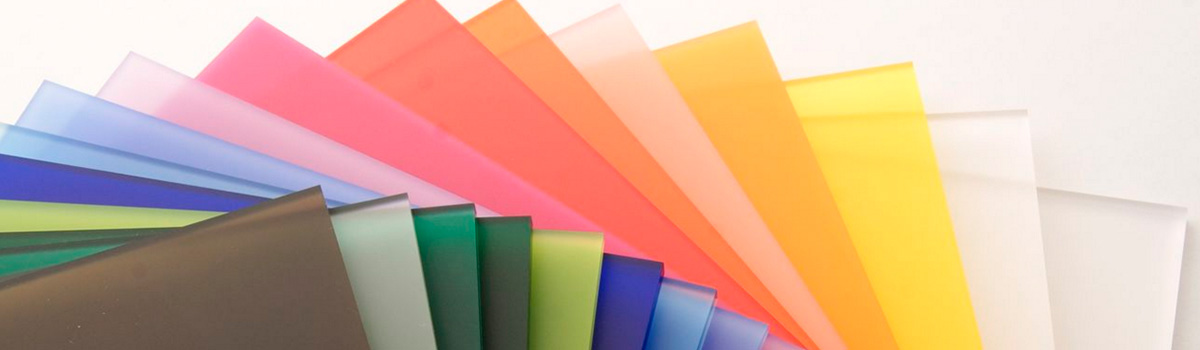
Свойства на термопластите, използвани при леене под налягане
Тези свойства на термопластмасите играят решаваща роля при определяне на тяхната пригодност за специфични приложения за леене под налягане. Производителите трябва внимателно да обмислят тези свойства и да изберат подходящия термопласт въз основа на желаната производителност, условията на околната среда и изискванията за цена.
- Механични свойства:Термопластите, използвани при леене под налягане, могат да проявяват различни механични свойства, включително якост на опън, устойчивост на удар и якост на огъване. Тези свойства определят способността на материала да издържа на приложените сили и цялостната му издръжливост при различни приложения.
- Химическа устойчивост:Много термопласти, използвани при леене под налягане, притежават забележителна устойчивост на химикали, разтворители и масла. Това свойство е от решаващо значение за приложения, които включват излагане на тежки среди или корозивни вещества.
- Термична стабилност:Термичната стабилност на термопластмасите се отнася до тяхната способност да издържат на високи температури без значително разграждане. Някои термопласти показват отлична устойчивост на топлина, което им позволява да запазят механичните си свойства дори при високи температури.
- Електрически свойства:Термопластите, използвани при леене под налягане, могат да имат специфични електрически свойства, включително електрическа изолация, проводимост или диелектрична якост. Тези свойства са от съществено значение за приложения в електрическата и електронната промишленост, където материалите трябва да осигурят надеждни електрически характеристики.
- Прозрачност и яснота:Някои термопласти, като поликарбонат и PET, предлагат отлична прозрачност и яснота, което ги прави подходящи за приложения, които изискват оптични свойства. Производителите обикновено използват тези материали в продукти като прозрачни прозорци, лещи и дисплеи.
- Гъвкавост и издръжливост: Гъвкавостта и издръжливостта са основни свойства на термопластите, използвани в приложения, които изискват устойчивост на удар и издръжливост. Някои термопласти, като ABS и найлон, предлагат отлична здравина, което им позволява да издържат на повтарящи се удари, без да се счупят.
- Стабилност на размерите:Стабилността на размерите се отнася до способността на термопласта да поддържа своята форма и размер при различни условия, включително температурни промени. Материалите с добра стабилност на размерите осигуряват постоянни размери на частите, минимизирайки риска от деформация или изкривяване.
- Химическа съвместимост:Химическата съвместимост на термопластмасите се отнася до способността им да издържат на разграждане или взаимодействие с различни химикали, включително киселини, основи и разтворители. За да се осигури оптимална производителност, изборът на термопласт, който може да издържи на специфичната химическа среда, която ще срещне при предвиденото приложение, е от съществено значение.
- Плътност: Термопластичните пластмаси имат различна дебелина, което може да повлияе на теглото им и цялостните свойства на частта. Материали с ниска плътност, като полиетилен, предлагат леки решения, докато материали с висока плътност, като полипропилен, осигуряват допълнителна здравина и твърдост.
Процес на леене под налягане: Стъпка по стъпка
Процесът на леене под налягане следва тези стъпки, позволявайки ефективно и прецизно производство на висококачествени термопластични части. Всяка стъпка изисква внимателен контрол и наблюдение, за да се осигурят постоянни размери на детайлите, свойства на материала и цялостно качество.
- Дизайн и изработка на мухъл: Първата стъпка в процеса на леене под налягане е проектирането и производството на формата. Производителите трябва да създадат прецизен и подробен дизайн на формата, за да постигнат желаните спецификации на частта. След това производителите произвеждат формата, използвайки различни техники, като CNC или електроерозионна обработка (EDM).
- Подготовка на материала: Следващата стъпка е подготовката, след като формата е готова. Термопластичните пелети или гранули се избират въз основа на желаните свойства на материала и се разтопяват в бункер. След това операторите подават материала в цилиндъра на машината за леене под налягане, където той се подлага на топене и хомогенизиране.
- инжектиране:По време на фазата на инжектиране операторите инжектират разтопения термопласт в кухината на формата под високо налягане. Инжекционният модул на машината изтласква разтопения материал през дюза във формата. Материалът запълва кухината на формата, като приема формата на желаната част.
- Охлаждане и втвърдяване:След напълване на матрицата операторите оставят разтопената пластмаса да се охлади и втвърди. Охлаждането е от решаващо значение за постигане на стабилност на размерите и правилно формиране на детайлите. Операторите могат да контролират процеса на охлаждане чрез циркулация на охлаждащата течност през канали във формата или чрез използване на охлаждащи плочи.
- Отваряне и изваждане на матрицата:Операторите отварят матрицата и изваждат частта от кухината на матрицата, след като пластмасата се втвърди. Системата за изхвърляне в машината използва щифтове, ежекторни плочи или въздушни струи за отстраняване на областта от формата. След това формата е готова за следващия цикъл на шприцване.
- Последваща обработка: След изваждането частта може да претърпи операции за последваща обработка, като подрязване, премахване на ръбове или повърхностна обработка. Тези стъпки помагат да се премахне излишният материал, да се изгладят грапавите ръбове и да се подобри окончателният вид на частта.
- Инспекция на качеството: Последната стъпка включва инспекция на инжектираните части за качество и гарантиране, че отговарят на определените изисквания. Могат да се използват различни техники за контрол на качеството, включително измерване на размерите, визуална проверка и функционално тестване, за да се провери качеството и целостта на частта.
- Рециклиране и повторна употреба на материали:Всеки излишък или остатъчен материал, генериран по време на шприцването, може да бъде рециклиран и използван повторно. Намаляването на използването на нови термопластични материали помага за минимизиране на отпадъците и подобряване на устойчивостта.
Оборудване, използвано при леене под налягане
Тези компоненти на оборудването улесняват процеса на леене под налягане, от топенето и шприцването на термопластичния материал до оформянето, охлаждането и изхвърлянето на крайната част. Правилната експлоатация и поддръжка на тези компоненти на оборудването са от решаващо значение за постигане на ефективно и висококачествено производство на леене под налягане.
- Машина за шприцоване:Основното оборудване при леене под налягане е отговорно за топенето на термопластичния материал, шприцването му във формата и контролирането на процеса.
- Мухъл: Формата, проектирана по поръчка, за да създаде желаната форма и характеристики на пластмасовата част, се състои от две половини, кухина и сърцевина. Операторите го монтират върху затягащия блок на машината за леене под налягане.
- Хопър:Контейнер, който държи термопластичния материал под формата на пелети или гранули и го подава в цевта на машината за леене под налягане за топене и инжектиране.
- Варел и винт: Варелът, цилиндрична камера, разтапя и хомогенизира термопластичния материал, докато винтът се върти в него, за да разтопи, смеси и стандартизира материала.
- Системи за отопление и охлаждане:Машините за леене под налягане имат нагревателни елементи, като електрически нагреватели или нагреватели, използващи горещо масло, за повишаване на температурата на цевта и системи за охлаждане, като циркулация на вода или масло, за охлаждане на формата и втвърдяване на пластмасовата част.
- Ежекторна система:Отстранява формованата част от кухината на матрицата след втвърдяване, като обикновено използва ежекторни щифтове, плочи или въздушни струи по време на отварянето на формата.
- Контролна система:Наблюдава и контролира различни параметри на процеса на леене под налягане, позволявайки на операторите да задават и регулират параметри като скорост на впръскване, температура, налягане и време за охлаждане.
Машини за леене под налягане: Видове и характеристики
Всеки тип машина за леене под налягане има своите характеристики и предимства, което позволява на производителите да изберат най-подходящото устройство за техните специфични производствени изисквания.
- Хидравлични машини за леене под налягане: Тези машини използват хидравлични системи за генериране на необходимото налягане за инжектиране на разтопена пластмаса във формата. Те са известни със своята висока сила на затягане, прецизен контрол и гъвкавост при работа с различни термопласти. Хидравличните машини са подходящи за широкомащабно производство и могат да поемат сложни форми.
- Електрически машини за леене под налягане:Електрическите машини използват електрически серво мотори за работата на машината, включително системите за впръскване, затягане и ежектор. Те предлагат прецизен контрол, енергийна ефективност и по-бързо време за реакция от хидравличните машини. Електрическите машини са идеални за приложения за прецизно формоване, които изискват висока повторяемост и точност.
- Хибридни машини за леене под налягане:Хибридните машини комбинират предимствата както на хидравличните, така и на електрическите устройства. Те използват комбинация от хидравлични и електрически серво системи за постигане на висока прецизност, енергийна ефективност и рентабилност. Хибридните машини са подходящи за широк спектър от приложения, като осигуряват баланс между производителност и оперативни разходи.
- Машини за леене под налягане с две плочи: Машините с две плочи имат уникален дизайн с две отделни плочи за захващане на формата. Този дизайн осигурява повишена стабилност, подобрена синхронизация на формата и позволява по-големи размери на матрицата и по-високи сили на затягане. Машините с две плочи са подходящи за големи и сложни детайли, които изискват прецизно формоване.
- Многокомпонентни машини за леене под налягане:Производителите проектират тези машини за производство на части с множество материали или цветове в един цикъл на формоване. Имат различни шприц единици и форми, позволяващи едновременно шприцване на различни материали. Многокомпонентните машини предлагат гъвкавост и ефективност при производството на сложни части с различни характеристики.
- Машини за микрошприцване:Специално проектирани за производство на малки и прецизни части, машините за микрошприцване предлагат невероятно висока прецизност и точност. Те могат да произвеждат сложни детайли с тесни допуски и минимални материални отпадъци. Електрониката, медицинските устройства и микрооптиката обикновено използват машини за микрошприцване.
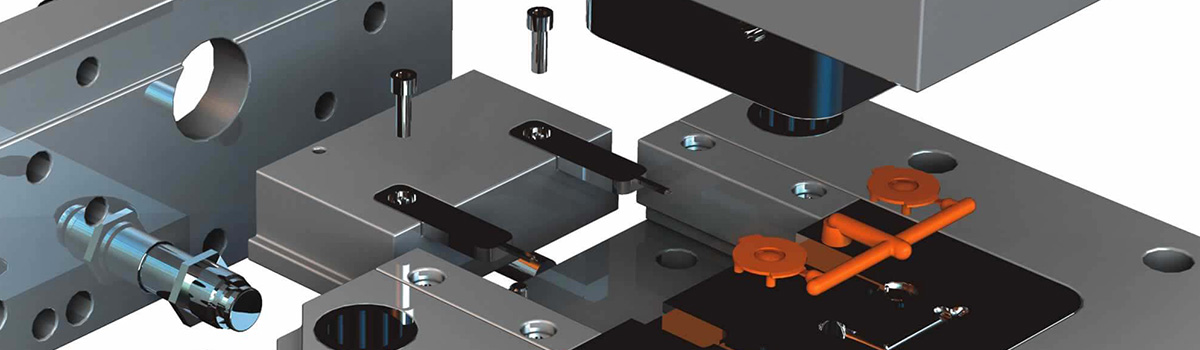
Съображения за дизайн на матрицата за леене под налягане
Внимателното проектиране на формата е от съществено значение за успешното производство на шприцване.
- Дизайн на части:Дизайнът на матрицата трябва да отговаря на специфичните изисквания на детайла, включително неговата форма, размери и функционални характеристики. Производителите трябва правилно да обмислят ъглите на теглене, дебелината на стената, подрязванията и всички необходими елементи, за да осигурят лесно изхвърляне и качество на частта.
- Мухъл материал: Изборът на материал за формата е от решаващо значение за постигане на издръжливост, стабилност на размерите и устойчивост на топлина. Обичайните материали за формоване включват стоманени сплави, алуминиеви сплави и инструментални стомани. Изборът на материал зависи от фактори като производствен обем, сложност на детайла и очакван живот на инструмента.
- Охладителна система:Ефективното охлаждане е от съществено значение за правилното втвърдяване на детайлите и минимизиране на времето на цикъла. Дизайнът на формата трябва да включва охлаждащи канали или стратегически разположени вложки, за да се осигури равномерно охлаждане на формата. Правилното охлаждане намалява риска от деформация, свиване и дефекти на частите.
- Вентилация:Необходима е подходяща вентилация, за да се позволи изтичането на въздух и газове по време на процеса на инжектиране. Недостатъчното вентилиране може да доведе до газови капани, следи от изгаряне или непълно запълване на частите. Производителите могат да постигнат вентилация чрез вграждане на вентилационни канали, щифтове или други механизми в дизайна на формата.
- Система за изхвърляне:Конструкцията на формата трябва да включва ефективна система за изхвърляне за безопасно и ефикасно отстраняване на формованата част от кухината на формата. Системата за изхвърляне може да се състои от изхвърлящи щифтове, ръкави или други механизми, стратегически разположени, за да се избегне смущение във функцията или критичните характеристики.
- Дизайн на портата:Портата е мястото, където разтопената пластмаса влиза в кухината на формата. Конструкцията на вратата трябва да осигурява правилно запълване на частите, да минимизира линиите на потока и да предотвратява преждевременното замръзване на материала. Стандартните дизайни на порти включват ръбове, тунелни врати и системи с горещи канали, в зависимост от изискванията на частта и свойствата на материала.
- Разделителна линия:Дизайнът на формата трябва да определи подходяща разделителна линия, която е линията, където двете половини на матрицата се събират. Правилното поставяне на линията на разделяне гарантира минимално несъответствие на линията на изплакване и линията на разделяне и улеснява ефективното сглобяване на формата.
- Поддръжка и обслужване на матрицата: Производителите трябва да обмислят лекотата на поддръжка, ремонт и обслужване на матрицата. Компонентите на формата трябва да са лесно достъпни за почистване, проверка и подмяна. Включването на функции като бързосменяеми вложки или модулен дизайн на матрицата може да подобри обслужването на матрицата.
Материали за формоване, използвани при леене под налягане
Сътрудничеството със специалисти по формовъчни материали и отчитането на специфичните нужди на формовъчното приложение може да помогне при определянето на най-подходящия материал за постигане на оптимална производителност на матрицата и качество на детайлите.
- Стоманени сплави: Стоманени сплави, като инструментални стомани (напр. P20, H13) и неръждаеми стомани, обикновено се използват за формите за леене под налягане поради тяхната отлична издръжливост, устойчивост на топлина и устойчивост на износване. Тези материали могат да издържат на високи температури и налягания в процеса на леене под налягане и предлагат добра стабилност на размерите за производство на висококачествени части.
- Алуминиеви сплави:Алуминиевите сплави, като 7075 и 6061, са леки и предлагат добра топлопроводимост, което ги прави подходящи за форми, които изискват ефективно охлаждане. Производителите често използват алуминиеви форми за създаване на прототипи, производство в малък обем или приложения, където намаляването на теглото е критично. Алуминиевите форми обаче може да имат по-ниска издръжливост в сравнение със стоманените сплави.
- Медни сплави:Медните сплави, като берилиевата мед, показват висока топлопроводимост и добра обработваемост. Те намират приложение във форми, които изискват отличен топлопренос за ефективно охлаждане. Медните сплави могат да помогнат за намаляване на времето на цикъла чрез бързо разсейване на топлината от формованата част, което води до по-бързо втвърдяване.
- Инструментални стомани:Инструменталните стомани, включително H13, S7 и D2, са предназначени за приложения с високопроизводителни инструменти. Тези стомани предлагат комбинация от висока якост, твърдост и устойчивост на износване. Инструменталните стомани са подходящи за форми с големи производствени обеми, абразивни материали или взискателни условия на формоване.
- Никелови сплави:Никеловите сплави, като Inconel и Hastelloy, са известни със своята изключителна устойчивост на корозия, устойчивост при висока температура и термична стабилност. Производителите използват тези сплави във форми, които обработват корозивни материали или изискват устойчивост на екстремни температури и агресивни среди за формоване.
- Композитни материали:Композитни материали, като подсилени пластмаси или композити с метални вложки, понякога се използват за специфични приложения за формоване. Тези материали предлагат баланс от свойства, като висока якост, термична стабилност и намалено тегло. Композитните форми могат да бъдат рентабилни алтернативи за специфични производствени изисквания.
Видове шприцформи
Шприцоването е универсален и широко използван производствен процес за пластмасови части.
- Форма с две плочи:Формата с две плочи е най-често срещаният тип шприцформа. Състои се от две плочи, кухината и сърцевината, които се разделят, за да позволят изхвърлянето на формованата част. Плочата с кухина съдържа страната на формата с кухина, докато плочата на сърцевината съдържа страната на сърцевината. Производителите използват пресформи с две плочи за производство на широка гама от части поради сравнително простия им дизайн.
- Форма с три плочи:Формата с три плочи е усъвършенствана версия на формата с две плочи. Включва допълнителна плоча, плъзгач или леяк. Плочата на водача създава отделен канал за леяк, водачи и порти, което позволява по-лесно отстраняване на формованата част. Производителите обикновено използват матрици с три плочи за детайли със сложни системи за затваряне или когато е желателно избягването на следи от врата върху детайла.
- Форма за горещ канал:Системата за канали и затвори се нагрява в горещи форми за канали, елиминирайки необходимостта от втвърдяване и повторно топене на материала по време на всеки цикъл. Системата с горещ канал се състои от нагрети колектори и дюзи, които поддържат разтопеното състояние на пластмасата. Формите за горещ канал предлагат предимства като намалено време на цикъл, по-малко отпадъци от материали и подобрено качество на детайлите чрез минимизиране на остатъците от затвора.
- Студена форма за бягане: Формите за студени канали имат традиционна система за канали и затвори, където разтопената пластмаса протича през студени канали, които се втвърдяват с всеки цикъл. Впоследствие операторите отстраняват втвърдените канали, което води до материални отпадъци. Производителите обикновено използват сложни формовъчни форми за по-малко обемно производство или когато материалните разходи са по-малко критични поради по-простия им дизайн.
- Вмъкване на плесен:Формите за вмъкване включват метални или пластмасови вложки в кухината на матрицата по време на леенето под налягане. Вложките могат да бъдат предварително поставени във формата или вмъкнати чрез автоматизирани процеси. Тази форма позволява интегриране на допълнителни компоненти или подсилващи елементи в формованата част, подобрявайки нейната функционалност или здравина.
- Покритие: Формоването включва формоване на един материал върху друг, обикновено свързване на твърда пластмасова основа с по-мек еластомер или термопластмаса. Този процес позволява създаването на части с множество материали или текстури в един калъп, осигурявайки подобрено сцепление, омекотяване или естетически характеристики.
Фактори, влияещи върху разходите за леене под налягане
Отчитането на тези фактори може да помогне на производителите да оценят и оптимизират разходите за леене под налягане, осигурявайки баланс между качество, ефективност и рентабилност за техните специфични производствени изисквания.
- Сложност на частта:Сложността на конструкцията на частта играе важна роля при определяне на цената на шприцването. Сложни геометрии, подрязвания, тънки стени или сложни елементи може да изискват допълнителни инструменти, специализирани форми или по-дълги цикли, което увеличава общите производствени разходи.
- Избор на материал:Изборът на термопластичен материал влияе на разходите за леене под налягане. Различните материали имат различни цени за килограм и фактори като наличността на материала, свойствата и изискванията за обработка могат да повлияят на общата цена на материала.
- Инструментална екипировка и дизайн на матрица: Първоначалните разходи за инструментална екипировка и дизайн на матрицата са значителни при разходите за леене под налягане. Фактори като сложност на матрицата, брой кухини, размер на матрицата и материал на матрицата допринасят за разходите за инструментална екипировка и производство на матрица. По-сложните форми или формите, изискващи разширени функции, могат да увеличат първоначалната инвестиция.
- Обем на продукцията: Производственият обем пряко влияе върху цената на част при леене под налягане. По-високите книги често водят до икономии от мащаба, намалявайки цената на част. Обратно, производствените серии с малък обем могат да наложат по-високи такси поради настройка, инструменти и отпадъци от материали.
- Време за цикъл: Времето на цикъла, което включва фазите на охлаждане и изхвърляне, влияе върху производствения капацитет и общите разходи. По-дългите времена на цикъла водят до намалено производство и потенциално по-високи цени. Оптимизирането на дизайна на формата, охладителната система и параметрите на процеса може да минимизира времената на цикъла и да подобри ефективността.
- Изисквания за качество:Строгите изисквания за качество или специфичните сертификати могат да повлияят на разходите за леене под налягане. Покриването на точни допустими отклонения, изисквания за повърхностно покритие или допълнителни тестове може да изисква други ресурси, процеси или проверки, добавяйки към общите разходи.
- Вторични операции:Ако формованите части изискват операции за последваща обработка, като сглобяване, боядисване или допълнителни довършителни стъпки, тези операции могат да увеличат общите разходи за леене под налягане.
- Доставчик и местоположение:Изборът на доставчик на леене под налягане и тяхното местоположение могат да повлияят на разходите. Разходите за труд, режийните, логистичните и транспортните разходи варират в зависимост от местоположението на доставчика, което оказва влияние върху общите производствени разходи.
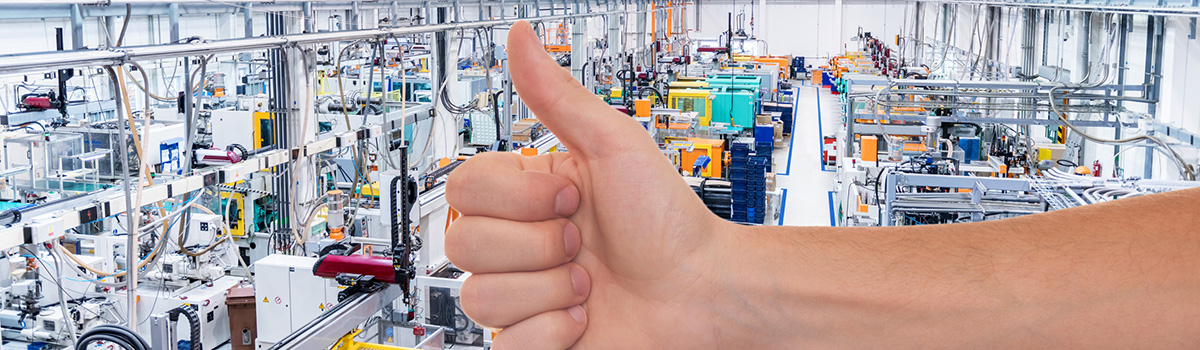
Контрол на качеството при леене под налягане
Прилагането на стабилни мерки за контрол на качеството по време на процеса на леене под налягане помага за идентифициране и адресиране на потенциални дефекти, отклонения или несъответствия, като гарантира производството на висококачествени части, които отговарят на спецификациите и изискванията на клиента.
- Мониторинг на процеса: Непрекъснатото наблюдение на ключовите параметри на процеса, като температура на стопилката, налягане на впръскване, време за охлаждане и време на цикъл, гарантира последователност и повторяемост при производството на части. Мониторингът в реално време и автоматизираните системи могат да открият вариации или отклонения от зададените параметри, което позволява навременни корекции и поддържане на стабилността на процеса.
- Проверка и измерване:Редовният преглед и измерване на формованите части са от съществено значение за проверка на точността на размерите, качеството на частите и спазването на спецификациите. Нашите услуги обхващат набор от методи за контрол на качеството, като измерване на размери, анализиране на качеството на повърхността, провеждане на визуални проверки и извършване на функционални тестове. За точна оценка се използват различни техники за проверка, като машини за измерване на координати (CMM) и оптични и визуални системи за проверка.
- Статистически контрол на процеса (SPC): SPC включва събиране и анализиране на данни за процеса за наблюдение и контрол на качеството на леене под налягане. Статистическите методи, като контролни диаграми и анализ на възможностите на процеса, помагат да се идентифицират тенденциите, да се открият вариации на процеса и да се гарантира, че процесът остава в рамките на дефинирани контролни граници. SPC дава възможност за проактивно идентифициране на проблеми и улеснява оптимизацията на процеса.
- Тестване на материали: Тестването на суровините, като термопласти, добавки и оцветители, гарантира тяхното качество и годност за леене под налягане. Тестването на материала може да включва анализ на индекса на потока на стопилката (MFI), механични свойства, термични характеристики и състав на материала. Проверката на качеството на материала помага за предотвратяване на дефекти и несъответствия в формованите части.
- Поддръжка и проверка на инструментите:Правилната поддръжка и редовната проверка на шприцформите са от решаващо значение за осигуряване на качество при шприцформата. Редовното почистване, смазване и оценка на компонентите на формата помагат за предотвратяване на износване, повреда или влошаване, което може да повлияе на качеството на частта. Навременният ремонт или подмяна на износени или повредени компоненти на формата е от съществено значение за поддържане на постоянна производителност на формоване.
- Документация и проследимост:Поддържането на изчерпателна документация и записи за проследяване е от съществено значение за контрола на качеството при леене под налягане. От жизненоважно значение е да се записват параметрите на процеса, резултатите от проверката, информацията за материала и всички промени или корекции, направени по време на производството. Правилната документация позволява проследимост на частите, улеснява анализа на първопричината и гарантира последователност в качеството.
- Обучение и развитие на уменията: Осигуряването на адекватно обучение и програми за развитие на умения за оператори, техници и персонал за контрол на качеството подобрява разбирането им за процесите на леене под налягане, изискванията за качество и техниките за проверка. Добре обученият персонал може да открие дефекти, да отстрани проблеми и да приложи ефективно коригиращи мерки, като гарантира висококачествена продукция.
Често срещани дефекти при леене под налягане и как да ги избегнете
Редовната инспекция, наблюдение и анализ на процесите на леене под налягане и правилната поддръжка и настройка на оборудването и формите могат да помогнат за идентифицирането и отстраняването на тези често срещани дефекти.
- Марки на мивката:Следите от мивка са вдлъбнатини или вдлъбнатини по повърхността на формованата част, причинени от неравномерно охлаждане или свиване. Човек трябва да вземе предвид правилното местоположение и дизайн на вратата, оптималния дизайн на охладителната система и равномерното разпределение на дебелината на стените, за да се избегнат следи от мивка. Увеличаването на налягането на впръскване или регулирането на времето за охлаждане също може да помогне за минимизиране на следите от потъване.
- Деформация:Изкривяването се отнася до деформация или огъване на формована част след изваждане поради неравномерно охлаждане или остатъчни напрежения. Поддържането на еднаква дебелина на стената, използването на подходящи охлаждащи канали и осигуряването на балансирано пълнене и опаковане на формата са от решаващо значение за предотвратяване на изкривяване. Оптимизирането на температурата на матрицата, използването на подходящи ъгли на теглене и контролирането на температурата на материала и скоростта на инжектиране може да помогне за минимизиране на деформацията.
- Flash:Светкавицата възниква, когато излишният материал потече в разделителната линия на матрицата, което води до тънки, нежелани издатини или допълнителен материал върху крайната част. Човек може ефективно да предотврати светкавицата, като осигури правилен дизайн на формата, включително прилагане на адекватна сила на затягане, прецизно подравняване и използване на подходящи техники за вентилация. Оптимизирането на параметри на процеса, като налягане на впръскване, температура и време на цикъл, намалява светкавицата.
- Кратък изстрел:Бърз изстрел се получава, когато инжектираният материал не запълни кухината на формата, което води до непълна част. Правилният избор на материал, осигуряването на адекватна температура и вискозитет на стопилката и поддържането на подходящо налягане и време за инжектиране са от съществено значение за избягване на къси снимки. Освен това, проверката на дизайна на формата за достатъчен размер на плъзгача и вратата и правилното вентилиране може да помогне за предотвратяване на бързи изстрели.
- Заваръчни линии:Заваръчните линии се появяват, когато два или повече фронта на потока от разтопен материал се срещнат и се втвърдят, което води до видима линия или белег върху повърхността на детайла. Добрият дизайн на шибъра и каналите, оптималната температура на стопилката, скоростта на впръскване и регулирането на потока на материала и геометрията на частта могат да намалят до минимум заваръчните линии. Анализът на потока на матрицата и оптимизирането на разположението на шибъра също могат да помогнат за предотвратяване или смекчаване на заваръчните линии.
- Белези от изгаряне:Следите от изгаряне са обезцветяване или черни петна по повърхността на формованата част, причинени от прекомерна топлина или прегряване на материала. Избягването на екстремни температури на стопяване, използването на подходящи охлаждащи канали и оптимизирането на времето на цикъла може да помогне за предотвратяване на следи от изгаряне. Адекватната вентилация, правилният дизайн на вратата и контролирането на температурата на формата също допринасят за минимизиране на следите от изгаряне.
Операции след формоване: Довършителни работи и монтаж
След леенето под налягане, много формовани части може да изискват допълнителни довършителни и монтажни операции за постигане на желания краен продукт. Тези операции след формоване могат да включват:
- Подрязване:Отстранете всеки излишен материал или флаш около формованата част, като използвате инструменти за подстригване или рязане.
- Повърхностна обработка:Подобряване на външния вид или функционалността на повърхността на частта с помощта на различни техники като боядисване, покритие или текстуриране.
- Монтаж:Съединяване на множество формовани части или добавяне на компоненти като крепежни елементи, вложки или етикети за завършване на крайния продукт.
- Тестване:Проверка на качеството и функционалността на частта чрез различни методи за тестване като анализ на размерите, тестване на свойствата на материала или тестване на производителността.
- Опаковка и доставка:Правилно опаковане и етикетиране на крайния продукт за изпращане до клиенти или крайни потребители.
Изборът на операциите след формоване зависи от конкретното приложение и желаните характеристики на крайния продукт. Тясното сътрудничество между експерти по леене под налягане, специалисти по довършителни работи и сглобяване и клиента е от решаващо значение за постигане на желаното абсолютно качество и функционалност на продукта. Правилното планиране и интегрирането на операциите след формоване в производствения процес може да помогне за осигуряване на ефективно производство и навременна доставка на висококачествени продукти.
Инжекционно формоване срещу други процеси за производство на пластмаса
Всеки процес на производство на пластмаса има предимства и ограничения, което ги прави подходящи за различни приложения.
- Инжекционно формоване: Шприцоването е много гъвкав и широко използван производствен процес за производство на пластмасови части. Той предлага предимства като висока производствена ефективност, прецизна репликация на детайли и възможност за създаване на сложни геометрии. Шприцоването е подходящо за големи производствени серии и позволява използването на широка гама от термопластични материали. Той предлага отлична точност на размерите и повърхностно покритие, което го прави идеален за различни индустрии като автомобилостроене, потребителски стоки и медицински устройства.
- Издухване: Издухването е процес, използван предимно за производство на кухи пластмасови части, като бутилки, контейнери и автомобилни компоненти. Това включва разтопяване на пластмаса и надуване в кухина на матрицата, създавайки желаната форма. Формоването чрез издуване е подходящо за производство в голям обем и може да произвежда големи, леки части с еднаква дебелина на стената. Той обаче е ограничен по отношение на сложността на частите и избора на материали в сравнение с леенето под налягане.
- Термоформоване:Термоформоването е процес, използван за производство на пластмасови части чрез нагряване на термопластичен лист и оформянето му с помощта на форми или вакуумно формоване. Намира обичайна употреба в опаковки, продукти за еднократна употреба и големи продукти като тави и капаци. Термоформоването предлага рентабилно производство на големи части и позволява бързо създаване на прототипи. Той обаче има ограничения по отношение на сложността на частите, избора на материал и точността на размерите в сравнение с леенето под налягане.
- Екструзия:Екструдирането е непрекъснат процес за производство на пластмасови профили, листове, тръби и филми. Това включва разтопяване на пластмасова смола и принуждаването й през матрица, за да се създаде желаната форма. Екструдирането е подходящо за производство на дълги, непрекъснати дължини на пластмасови продукти с постоянно напречно сечение. Докато екструзията предлага високи производствени нива и рентабилност, тя е ограничена по отношение на сложни геометрии на частите и прецизен контрол на размерите в сравнение с леенето под налягане.
- Компресионно формоване:Компресионното формоване включва поставяне на предварително измерено количество термореактивен материал в нагрята кухина на формата и компресирането му под високо налягане, докато се втвърди. Намира обичайна употреба при производството на части с висока якост и стабилност на размерите, като например автомобилни компоненти и електрическа изолация. Компресионното формоване предлага добра консистенция на частите, висока производствена ефективност и възможност за използване на широка гама от материали. Той обаче е ограничен по отношение на сложността на детайлите и времето на цикъла в сравнение с леенето под налягане.
Приложения на термопластично леене под налягане
Различни индустрии широко използват термопластично леене под налягане поради неговата гъвкавост, ефективност и рентабилност. Някои от приложенията на термопластичното шприцване включват:
- Автомобилна индустрия: Автомобилната индустрия широко използва термопластично леене под налягане за производство на различни компоненти, включително вътрешна и външна облицовка, табла, панели на вратите, брони и електрически конектори. Процесът позволява прецизно копиране на части, сложни геометрии и леки материали, подобрявайки горивната ефективност и гъвкавостта на дизайна.
- Потребителски стоки:Шприцоването намира широки приложения в производството на потребителски стоки като домакински уреди, електронни устройства, опаковъчни контейнери и играчки. Процесът позволява масовото производство на издръжливи, висококачествени продукти с постоянни размери и повърхностно покритие. Той също така позволява опции за персонализиране и бързи итерации на продукта.
- Медицински устройства:Инжекционното формоване играе решаваща роля в медицинската индустрия за производството на широка гама от устройства, включително спринцовки, хирургически инструменти, имплантируеми компоненти и системи за доставяне на лекарства. Процесът осигурява производството на стерилни, прецизни и биосъвместими части, които отговарят на строгите регулаторни изисквания на сектора на здравеопазването.
- Електроника и електрическа промишленост:Електронната промишленост използва леене под налягане за производство на електрически конектори, кутии, превключватели и други компоненти. Процесът предлага висока точност на размерите, отлична повърхностна обработка и възможност за включване на функции като формоване на вложки и формоване, което позволява ефективно производство на сложни електронни модули.
- Опаковъчна индустрия:Различни индустрии, включително храни и напитки, фармацевтични продукти и лична хигиена, обикновено използват леене под налягане за производство на пластмасови опаковъчни контейнери, капачки, капачки и бутилки. Процесът позволява създаването на леки, издръжливи и естетически привлекателни опаковъчни решения с ефективни производствени цикли.
- Аерокосмическа индустрия:Аерокосмическият сектор използва леене под налягане за производство на леки и високоефективни компоненти като въздуховоди, скоби, вътрешни панели и структурни части. Процесът позволява използването на усъвършенствани материали и сложни геометрии на частите, което допринася за намаляване на теглото и подобрена горивна ефективност.
Въздействие върху околната среда на термопластично леене под налягане
Термопластичното шприцоване е популярен производствен процес поради многобройните си предимства, но също така е важно да се вземе предвид въздействието му върху околната среда. Ето някои точки, които трябва да имате предвид:
- Материална ефективност:Термопластичното шприцване насърчава ефективността на материала чрез минимизиране на отпадъците. Процесът използва прецизен контрол върху количеството материал, инжектиран във формата, намалявайки необходимостта от излишен материал. Производителите могат също така да използват техники за повторно смилане и рециклиране, за да използват повторно скрап или отхвърлени части, като допълнително намаляват материалните отпадъци.
- Консумация на енергия:Производителите проектират машините за леене под налягане, за да бъдат енергийно ефективни, като модерните модели включват усъвършенствани технологии като серво мотори и задвижвания с променлива скорост. Тези функции оптимизират използването на енергия чрез намаляване на консумацията на енергия по време на формоване, което води до по-ниски енергийни изисквания и намалено въздействие върху околната среда.
- Управление на отпадъците:Докато свеждат до минимум отпадъците от материали, производителите трябва да прилагат подходящи практики за управление на отпадъците, за да се справят с остатъци от материали, лейки или канали. Производителите могат да създадат програми за рециклиране за събиране и повторно използване на пластмасови отпадъци, генерирани по време на леене под налягане, като по този начин намаляват отпадъците, изпращани на депата.
- Намаляване на емисиите: Термопластичното леене под налягане обикновено генерира по-ниски емисии в сравнение с други производствени процеси. Производителите могат да намалят емисиите чрез използване на екологични материали, внедряване на енергийно ефективно оборудване и използване на усъвършенствани изпускателни и филтриращи системи за улавяне на всички отделени емисии.
- Избор на устойчив материал:Изборът на термопластични материали може значително да повлияе на екологичната устойчивост на леенето под налягане. Изборът на биоразградими или на биологична основа пластмаси, както и рециклирани или рециклируеми материали, може да помогне за намаляване на цялостния екологичен отпечатък на процеса.
Съображения за жизнения цикъл: Отчитането на целия жизнен цикъл на формования продукт е от съществено значение за оценката на неговото въздействие върху околната среда. По време на етапите на проектиране и избор на материал производителите трябва да вземат предвид фактори като издръжливостта на частта, възможността за рециклиране и потенциала за изхвърляне или повторна употреба в края на жизнения цикъл.
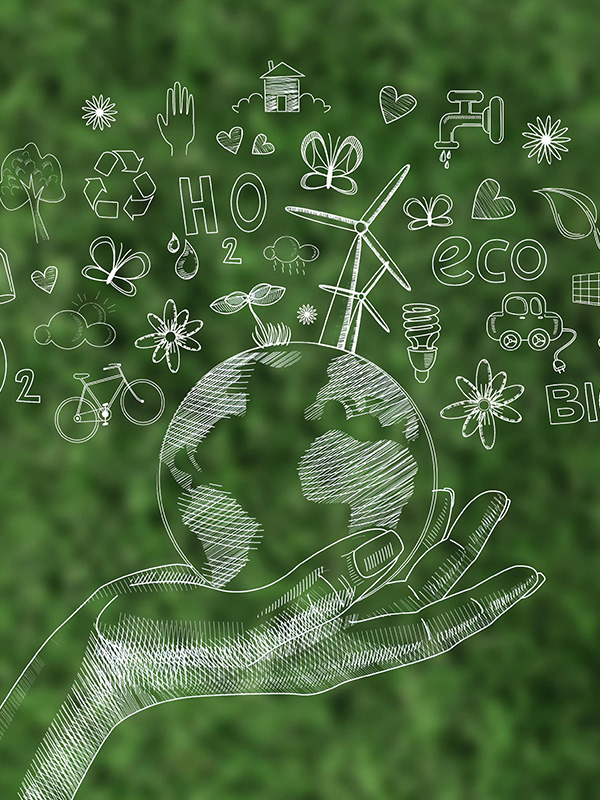
Бъдещето на термопластичното леене под налягане
Бъдещето на термопластичното леене под налягане изглежда обещаващо, с непрекъснатия напредък в технологиите и увеличеното търсене на висококачествени, прецизни части в различни индустрии. Някои от основните развития, които се очакват през следващите години, включват:
- Повишено използване на автоматизация и роботика за подобряване на ефективността и намаляване на разходите.
- Усилията са насочени към разработването на нови материали и процеси за подобряване на производителността на частите и създаване на нови приложения.
- Това е нарастващо възприемане на устойчиви практики, като използване на рециклирани материали и оптимизиране на потреблението на енергия, за намаляване на въздействието върху околната среда от шприцоването.
- По-голяма интеграция на цифрови технологии, като 3D печат и софтуер за симулация, за подобряване на процесите на проектиране и производство.
Глобалният пазар на леене под налягане се разширява, особено в развиващите се икономики, воден от нарастващото търсене на пластмасови продукти в различни индустрии.
Избор на правилния партньор за леене под налягане
Изборът на правилния партньор за леене под налягане е от решаващо значение за успеха на вашия проект. Отделете време, за да оцените множество опции, да извършите посещения на място и да участвате в задълбочени дискусии, за да осигурите съвместимо и дълготрайно партньорство.
- Опит и опит:Потърсете партньор за леене под налягане с обширни познания и опит в индустрията. Те трябва да имат доказан опит в предоставянето на висококачествени продукти и решения на клиенти в различни сектори. Помислете за тяхното разбиране за различни материали, дизайн на матрици и производствени процеси.
- Производствени възможности: Оценете производствените възможности на партньора за леене под налягане. Уверете се, че разполагат с добре оборудвано съоръжение с модерни машини и технологии, за да се справят с изискванията на вашия проект. Помислете за техния производствен капацитет, способността да се справят с различни размери и сложност на детайлите и способността да отговарят на желаните производствени обеми и срокове.
- Осигуряване на качеството:Качеството е от първостепенно значение при леенето под налягане. Оценете системите за контрол на качеството и сертификатите на потенциалния партньор. Потърсете партньори, които следват стриктни стандарти за качество, имат стабилни процеси на проверка и извършват цялостни тестове, за да гарантират качество и последователност на частите.
- Проектиране и инженерна поддръжка:Надеждният партньор за леене под налягане трябва да предлага проектантска и инженерна поддръжка, за да оптимизира дизайна на вашата част за технологичност. Те трябва да разполагат с квалифицирани инженери, които могат да осигурят ценна информация за избора на материал, дизайна на матрицата и оптимизирането на процесите, за да подобрят качеството и ефективността на детайлите.
- Конкурентоспособност на разходите:Въпреки че цената не трябва да бъде единственият определящ фактор, важно е да се оцени ценообразуването и конкурентоспособността на разходите на партньора за леене под налягане. Поискайте подробни оферти и вземете предвид разходите за инструменти, материалите, разходите за труд и всички допълнителни услуги, които предоставят.
- Комуникация и сътрудничество:Ефективната комуникация и сътрудничество са от съществено значение за успешното партньорство. Уверете се, че партньорът за леене под налягане има добри канали за комуникация, отговаря на вашите запитвания и може да предоставя редовни актуализации на проекта. Подходът на сътрудничество ще ни помогне да отговорим на вашите изисквания и бързо да отговорим на всички предизвикателства.
- Референции и рецензии на клиенти:Потърсете референции от клиенти или прочетете рецензии/отзиви, за да получите представа за опита на други клиенти с партньора за леене под налягане. Получаването на тази информация може да помогне да се определи тяхната надеждност, бързина и общото ниво на удовлетвореност на клиентите.
Заключение
Термопластичното леене под налягане е универсален и рентабилен метод за производство на пластмасови части в големи количества. Способността му да произвежда сложни форми с висока прецизност и последователност се превърна в популярен избор за различни индустрии, включително автомобилостроене, медицина, електроника и потребителски стоки. Като разберете различните аспекти на термопластичното шприцване, включително неговите предимства, недостатъци и съображения за дизайн, можете да вземете информирани решения относно избора на правилния партньор за шприцване за вашите бизнес нужди.