Cas en Corée
Conception structurelle de l'épaisseur de paroi des pièces d'injection plastique pour les constructeurs automobiles coréens
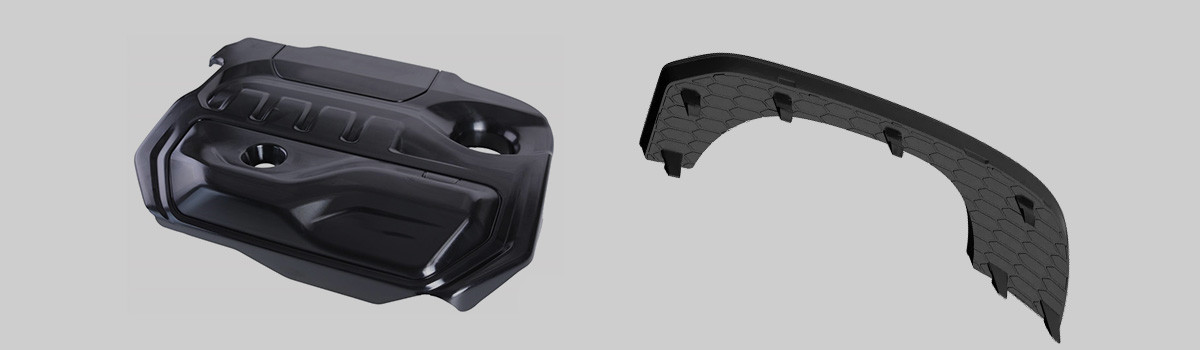
Les pièces en plastique sont très importantes pour une voiture, et sa structure solide aura un effet sur la durée de vie et la sécurité de conduite, de sorte que les constructeurs automobiles coréens achètent des pièces en plastique très strictes. L'industrie automobile utilisera beaucoup de pièces en plastique dans une voiture, les sociétés d'injection locales coréennes ne peuvent pas offrir l'approvisionnement important, et ces fabricants automobiles achèteront des pièces en plastique à l'étranger, tout comme DJmolding en Chine.
Les pièces en plastique sont si importantes pour une voiture, alors comment concevoir l'épaisseur de paroi des pièces d'injection plastique structurelles pour les entreprises automobiles coréennes ? Maintenant, DJmolding vous montrera la conception de l'épaisseur structurelle des pièces d'injection plastique.
Définition de l'épaisseur de paroi
L'épaisseur de paroi est une caractéristique structurelle de base des pièces en plastique. Si la surface extérieure des pièces en plastique s'appelle la paroi extérieure, la surface intérieure s'appelle la paroi intérieure, il existe alors une valeur d'épaisseur entre les parois extérieure et intérieure. La valeur est appelée épaisseur de paroi. La valeur saisie lors de l'extraction de la coque sur le logiciel lors de la conception de la structure peut également être considérée comme l'épaisseur de paroi.
Fonction de l'épaisseur de paroi
Pour la paroi extérieure des produits
La paroi extérieure des pièces est comme la peau extérieure des pièces. La paroi intérieure est constituée des squelettes structurels des pièces. Différents effets d'apparence peuvent être obtenus par le traitement de surface de la paroi extérieure des pièces. La paroi intérieure relie simplement les structures (nervures, barres à vis, boucle, etc.) entre elles et permet une certaine résistance aux pièces. Entre-temps, d'autres structures peuvent être remplies pendant le processus de moulage par infection. Il n'y a pas d'exigences spécifiques pour les murs intérieurs et extérieurs (refroidissement, assemblage). Normalement, il est constitué d'un tout afin que les pièces puissent avoir une résistance suffisante pour protéger les pièces internes contre les dommages ou les interférences de l'environnement.
Pour les parties internes du produit
En tant que support d'appui ou de connexion, il n'y a pas d'exigences strictes pour les murs intérieurs et extérieurs, qui peuvent établir d'autres structures (nervures, barres à vis, boucles, etc.) sur le mur extérieur en fonction des conditions réelles. Cependant, pour des raisons de fabrication pratique (se réfère principalement au moment où les moules avant et arrière sont séparés, afin de maintenir les pièces en plastique dans le moule arrière, la face avant du moule, dont la paroi extérieure doit être conçue aussi simple que possible Sinon, ajuster l'angle de dessin des moules avant et arrière, même avoir un dé à coudre dans le moule avant ou une certaine petite contre-dépouille dans le moule arrière), et généralement concevoir d'autres structures sur la paroi intérieure.
Qu'il s'agisse de pièces de coque ou de pièces internes, l'épaisseur de paroi est essentielle en tant que surface de réception de l'éjecteur du moule, permettant une éjection en douceur des pièces.
Principes de conception de l'épaisseur de paroi :
Lors de la conception des pièces en plastique, l'épaisseur de paroi est la priorité, ce qui est essentiel en tant que fondation d'un bâtiment. Les autres structures doivent être construites dessus. En attendant, cela impacte également les propriétés mécaniques, la formabilité, l'aspect, le coût des pièces plastiques. Ainsi, l'épaisseur de paroi doit être basée sur les facteurs ci-dessus pour la conception.
Il a mentionné que l'épaisseur de paroi doit être une valeur spécifique. S'il y a une valeur, elle fait référence à l'épaisseur de paroi paire. S'il y a plusieurs valeurs, cela fait référence à l'épaisseur de paroi inégale. La différence entre pair et impair sera introduite après. Maintenant, nous allons parler du Le principe de la conception de l'épaisseur de paroi doit être suivi.
1. Basé sur le principe des propriétés mécaniques :
Il a mentionné que peu importe qu'il s'agisse de pièces de coque ou de pièces internes, les deux ont besoin d'un certain niveau de résistance. Outre d'autres facteurs, la force de libération de la réserve est nécessaire lors de l'examen de la formation des pièces. Il se déforme facilement si la pièce est trop fine. D'une manière générale, plus l'épaisseur de paroi est épaisse, plus la résistance des pièces est élevée (l'épaisseur de paroi augmente de 10 %, la résistance augmentera d'environ 33 %). Si l'épaisseur de paroi dépasse une certaine plage, l'ajout à l'épaisseur de paroi réduira la résistance des pièces en raison du retrait et de la porosité. L'augmentation de l'épaisseur de paroi réduira la résistance des pièces et augmentera le poids, étendra le cercle de moulage par injection, le coût, etc. évidemment, augmenter la résistance des pièces en augmentant simplement l'épaisseur de paroi n'est pas le programme optimal. Il est préférable d'utiliser les caractéristiques géométriques pour augmenter la rigidité, telles que les nervures, les courbes, les surfaces ondulées, les raidisseurs, etc.
Il n'est pas exclu qu'en raison des limitations d'espace et d'autres facteurs, la résistance de certaines pièces soit principalement réalisée par l'épaisseur de la paroi. Ainsi, il est recommandé de déterminer une épaisseur de paroi appropriée en imitant la simulation mécanique si la résistance est un facteur important. En effet, la valeur de l'épaisseur de paroi doit également être respectée avec les principes de formalité suivants.
2. Basé sur le principe de formabilité :
L'épaisseur de paroi réelle est l'épaisseur de la cavité du moule entre les moules avant et arrière. Lorsque la résine fondue remplit la cavité du moule et refroidie, l'épaisseur de paroi est obtenue.
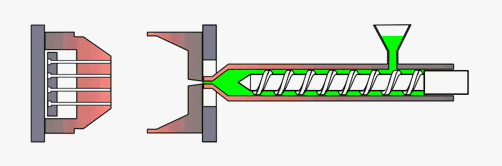
1) Comment la résine fondue s'écoule-t-elle pendant le processus d'injection et de remplissage ?
L'écoulement du plastique à l'intérieur de la cavité peut être considéré comme un écoulement laminaire. Selon la théorie de la mécanique des fluides, le fluide laminaire peut être considéré comme les couches de liquide les unes à côté des autres glissant sous l'action d'une force de cisaillement.
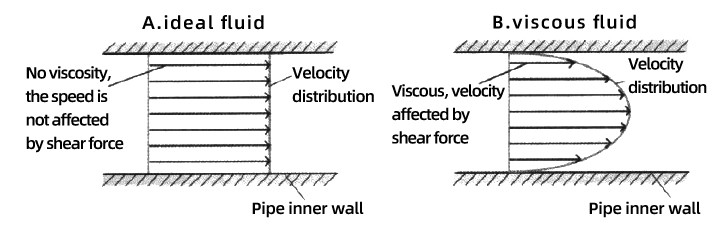
Pendant le processus de moulage par injection, la résine fondue entre en contact avec la paroi des canaux (paroi de la cavité du moule), faisant adhérer les couches de flux à la paroi des canaux (ou paroi de la cavité du moule) refroidie en premier. La vitesse est nulle et une résistance au frottement est produite avec sa couche liquide adjacente. Passez ainsi, la vitesse de la couche intermédiaire est la plus élevée. La forme d'écoulement dans laquelle la vitesse laminaire diminue près de la paroi du canal (ou de la paroi de la cavité du moule) des deux côtés.
La couche intermédiaire est la couche fluide et la couche de peau est la couche solidifiée. Au fur et à mesure que le temps de refroidissement passe, la couche de malédiction augmentera. La section transversale de la couche de fluide sera progressivement réduite. Plus le remplissage est dur, plus la force d'injection est importante. En effet, il est plus difficile de pousser la masse fondue dans la cavité du moule pour réaliser l'injection.
Par conséquent, la taille de l'épaisseur de paroi a une grande influence sur l'écoulement et le remplissage des pièces moulées par injection pendant le processus de moulage par injection, et sa valeur ne peut pas être trop petite.
2) La viscosité du plastique fondu a également une grande influence sur la fluidité
Lorsque la masse fondue est sous l'action externe et qu'il y a un mouvement relatif entre les couches, une force de frottement interne sera générée pour interférer avec le mouvement relatif entre les couches de fluide. La force de frottement interne produite par le fluide est appelée viscosité. Évaluer la résistance à la viscosité avec la viscosité dynamique (ou coefficient de viscosité). Numériquement, le rapport entre la contrainte de cisaillement et le taux de cisaillement de la masse fondue.
La viscosité des masses fondues reflète les caractéristiques de la facilité avec laquelle la matière plastique fondue s'écoule. C'est une mesure de la résistance à l'écoulement à l'état fondu. Plus la viscosité est élevée, plus la résistance du fluide est grande, plus l'écoulement est difficile. Les facteurs influents de la viscosité à l'état fondu affectent non seulement la structure moléculaire, mais également la température, la pression, le taux de cisaillement, les additifs, etc. (après avoir décidé des types de matières plastiques, la température, la pression, le taux de cisaillement, les additifs et d'autres facteurs au cours du processus de moulage par injection peuvent être modifiés pour modifier la fluidité du plastique dans le processus de moulage par injection. À l'avenir, nous écrirons un article sur le sujet de la liquidité en fonction de la situation.)
Alors que, dans l'application réelle, l'indice de fusion indique la fluidité des matières plastiques lors du traitement. Plus la valeur est élevée, meilleure est la fluidité du matériau. Au contraire, la fluidité du matériau sera moins bonne.
Par conséquent, le plastique avec une bonne fluidité est plus facile à remplir la cavité du moule, en particulier pour les pièces moulées par injection avec des structures complexes.
La fluidité des plastiques couramment utilisés peut être grossièrement divisée en trois catégories selon les exigences de conception du moule :
①Bonne fluidité : PA, PE, PS, PP, CA, poly(4) méthylpentylène ;
② Fluidité moyenne : résines de la série polystyrène (telles que ABS, AS), PMMA, POM, PPO ;
③Mauvaise fluidité : PC, PVC dur, PPO, PSF, PASF, fluoroplastiques.
Comme nous pouvons le voir sur la figure ci-dessus, le matériau avec la fluidité la plus faible, les exigences pour l'épaisseur de paroi minimale seront plus élevées. Ceci a été introduit dans la théorie du flux laminaire.
La valeur recommandée de l'épaisseur de paroi ci-dessus n'est qu'un nombre conservateur. Dans l'application réelle, les tailles des pièces incluent petites, moyennes et grandes, l'image ci-dessus ne précise pas la plage de référence.
3) Nous pouvons calculer par le rapport de longueur d'écoulement
Le rapport de longueur d'écoulement du plastique fait référence au rapport de la longueur (L) à l'épaisseur de paroi (T) de l'écoulement du plastique à l'état fondu. Cela signifie que pour une épaisseur de paroi donnée, plus le rapport de longueur d'écoulement est élevé, plus le plastique fondu s'écoule loin. Ou lorsque la longueur de l'écoulement du plastique à l'état fondu est certaine, plus le rapport de longueur d'écoulement est grand, plus l'épaisseur de paroi peut être petite. Ainsi, le rapport de longueur d'écoulement du plastique affecte directement le nombre d'alimentation et de distribution de produits en plastique. En outre, cela affecte l'épaisseur de paroi du plastique.
Pour être plus précis, la plage de valeurs spécifiques de l'épaisseur de paroi peut être obtenue par le calcul du rapport de longueur d'écoulement. En effet, cette valeur est liée à la température du matériau, à la température du moule, au degré de polissage, etc. ce n'est qu'une valeur de plage approximative, différentes conditions sont différentes, il est difficile d'être précis, mais elle peut être utilisée comme valeur de référence.
Calcul du rapport de longueur d'écoulement :
L/T (total) = L1/T1 (canal principal) + L2/T2 (canal divisé) + L3/T3 (produit) Le rapport de longueur d'écoulement calculé doit être inférieur à la valeur indiquée dans le tableau des propriétés physiques, sinon il peut y avoir be Le phénomène de mauvais remplissage.
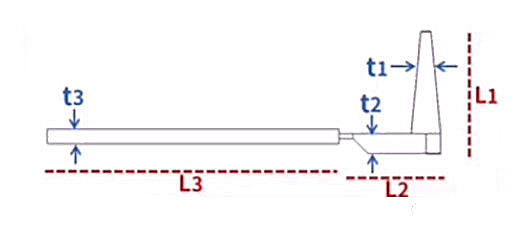
Par exemple
Une coque en caoutchouc, matériau PC, l'épaisseur de paroi est de 2, la distance de remplissage est de 200, le coureur est de 100, le diamètre des coureurs est de 5.
Calculation: L/T(total)=100/5+200/2=120
La valeur de référence pour le rapport de longueur d'écoulement de PC est de 90, ce qui est évidemment supérieur à la valeur de référence. La vitesse et la pression d'injection doivent être augmentées car il est difficile à injecter, voire nécessitent des presses à injecter spécifiques à hautes performances. Si adopte deux points d'alimentation ou change la position des points d'alimentation, la distance de remplissage des produits peut être réduite à 100, ce qui est L/T (total) = 100/5 + 100/2 = 70. Le rapport de longueur est maintenant inférieur à la valeur de référence et est facile pour le moulage par injection. L/T(total)=100/5+200/3=87 lorsque l'épaisseur de paroi est changée en 3, ce qui permet le moulage par injection normal.
3. Basé sur le principe d'apparence :
Les performances spécifiques de l'épaisseur de paroi affectant l'apparence des pièces sont les suivantes :
1) Épaisseur de paroi inégale : rétrécissement de la surface (y compris les défauts d'aspect tels que le rétrécissement, les piqûres, les impressions épaisses et fines), la déformation par gauchissement, etc.
2) Épaisseur de paroi excessive : défauts tels que retrait de surface et trous de retrait internes.
3) L'épaisseur de paroi est trop faible : défauts tels que manque de colle, impression de dé à coudre, gauchissement et déformation.
retrait ou porosité
le retrait ou la porosité se produit normalement dans les zones d'épaisseur de paroi épaisse. Le mécanisme : selon le principe de solidification du matériau, la porosité interne et le retrait de surface pendant le processus de moulage par injection sont dus à la contraction constante pendant le processus de refroidissement. Lorsque le rétrécissement est concentré à la position gelée derrière, mais ne peut pas être compensé immédiatement, le rétrécissement et la porosité sont plus susceptibles de se produire à l'intérieur.
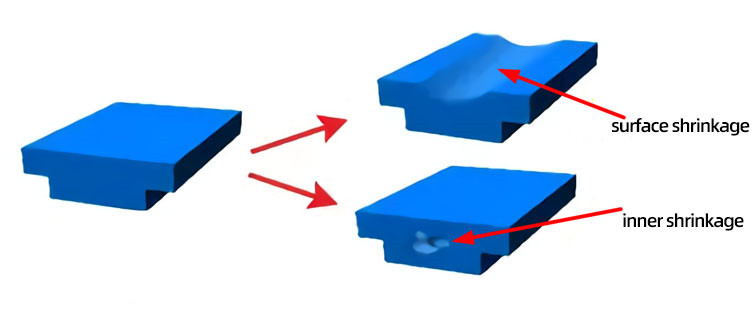
Les principes de conception de l'épaisseur de paroi ci-dessus sont présentés sous quatre aspects, à savoir les propriétés mécaniques, la formabilité, l'apparence et le coût. Si vous utilisez une phrase pour décrire la conception de l'épaisseur de paroi, c'est-à-dire que la valeur de l'épaisseur de paroi des pièces moulées par injection doit être aussi petite que possible et aussi uniforme que possible à condition de satisfaire aux propriétés mécaniques et aux performances de traitement. Si ce n'est pas le cas, la transition doit être uniforme.
DJmolding propose des services de conception et de fabrication de pièces en plastique pour le marché mondial. Si vous souhaitez démarrer votre projet, veuillez nous contacter dès maintenant.