Solutions aux défauts de moulage courants du moulage par injection
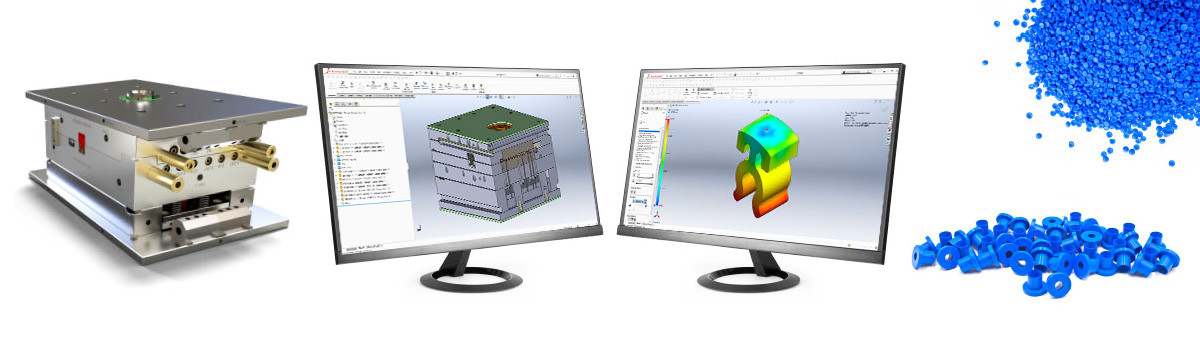
Les défauts sont courants lors de l'utilisation de moules pour traiter des pièces moulées par injection de plastique, ce qui affecte largement l'efficacité du traitement. Voici les défauts de moulage courants et les solutions pour les pièces moulées par injection de plastique.
Coups courts
Les plans courts font référence aux produits fabriqués qui sont incomplets car les moules ne sont pas entièrement remplis.
Ce défaut apparaît généralement à l'endroit le plus éloigné de la porte ou des pièces qui ne peuvent être atteintes que par les zones étroites du moule car les zones étroites peuvent affecter l'écoulement des matières fondues.
Une injection courte peut provoquer des micro-marques d'écoulement ou entraîner le manque évident d'une grande partie du produit.
Cause:
Les causes des tirs courts incluent :
La matière première injectée dans le moule ne suffit pas.
La résistance des masses fondues est grande, ce qui fait que le moule ne peut pas être rempli complètement.
La ventilation de la moisissure est médiocre et provoque la génération de cavitation qui bloque la fonte, empêchant la fonte de s'écouler vers certaines zones de la moisissure.
Bavures
Les bavures sont générées par l'adhérence des matières premières excédentaires extrudées de la cavité du moule au produit.
Ce défaut se retrouvera sur les bords du produit ou de chaque partie composée de moule. La matière première peut déborder du moule ou des sites de liaison des moules mobiles et de fixation.
Des bavures peuvent également être trouvées sur le noyau du moule, qui sont dues à la pression hydraulique ou à la goupille angulaire.
La gravité des bavures varie, parfois fines, parfois plus épaisses.
Cause:
Les causes des bavures comprennent :
La surface du moule de serrage est endommagée ou fortement usée.
Le moule mobile et le moule de fixation sont disloqués lorsqu'ils sont verrouillés.
La pression de la matière première dans le moule est supérieure à la force de serrage du moule.
La troisième condition mentionnée ci-dessus résulterait de diverses raisons. Dans les situations suivantes, la pression de la matière première est supérieure à la force de serrage du moule.
Lors de la première étape du moule à injection (étape de remplissage du moule), trop de matière première est remplie, ce qui augmente la pression à l'intérieur du moule.
Pendant le processus de remplissage du moule, une grande résistance à l'écoulement à l'état fondu augmentera également la pression à l'intérieur du moule.
La pression de la cavité du moule est trop élevée pendant la phase de maintien de la pression.
La force de serrage du moule n'est pas suffisante.
Dégradation
La décomposition pourrait conduire à de nombreux résultats. L'étendue et la gravité du problème varient également. Dans le cas le plus grave, cela peut entraîner une décoloration complète du produit et de mauvaises propriétés mécaniques. La dégradation locale ne provoquera que des rayures ou des taches sombres.
Cause:
La dégradation est causée par l'endommagement de la matière première. Les molécules à longue chaîne qui forment les plastiques se décomposeront sous l'action d'une chaleur excessive ou d'une contrainte de cisaillement excessive. Lors de la décomposition des molécules, le gaz volatil va accélérer le processus de dégradation, ce qui va provoquer la décoloration de la matière première. La décomposition d'une grande quantité de molécules finira par casser le contenu de la matière première et aura une influence négative sur les propriétés mécaniques.
Une dégradation locale peut résulter d'une température inégale du tube de matériau.
Une dégradation peut se produire dans les situations suivantes :
La matière première est surchauffée dans le baril de matériau ou le système de canaux chauds.
La matière première reste trop longtemps dans le fût.
Lors du processus de moulage par injection, la contrainte de cisaillement exercée sur la matière première est trop importante. Si les buses sont bloquées ou si les vannes et le canal sont trop étroits, cela augmentera la contrainte de cisaillement.
Déformation
Dans les situations normales, les formes des produits doivent être conformes à celles des moules. La déformation fait référence à la déformation des produits.
Lorsque la condition s'aggrave, les produits se déforment complètement lorsqu'ils sont éjectés du moule. Lorsque la condition n'est pas grave, la forme du produit apparaîtra de petites irrégularités.
Les zones longues mais sans arêtes d'appui ou les grands plans sont les plus sujettes à la déformation.
Cause:
Causes de déformation :
La température est trop élevée lors du démoulage.
Comme le temps de refroidissement est différent dans les zones épaisses et minces, ou la différence de température du moule dans le moule mobile et le moule de fixation, le rétrécissement à l'intérieur des produits est différent.
L'écoulement du moule n'est pas régulier lors du remplissage (ce que l'on appelle «l'orientation de congélation») ou la pression à l'intérieur de la cavité du moule est trop élevée à l'étape de maintien de la pression.
Impuretés
Les impuretés apparaissent souvent sous la forme de taches de différentes couleurs, taches ou rayures. La plus courante est la tache noire.
Les impuretés peuvent n'être que de minuscules taches, mais peuvent aussi être des rayures évidentes ou une grande partie de la décoloration quand c'est grave.
Cause:
Les impuretés sont causées par les articles divers mélangés aux matières premières, tels que :
La matière première mélangée à des articles divers lorsqu'elle est transportée dans les fûts.
La décomposition de la matière première peut provenir de tous les mécanismes de coupe et être mélangée aux matières premières, telles que les boulons mécaniques, la paroi intérieure du tambour de séchage, les joints/buses.
Laminage
La stratification générera «l'effet de peau» à la surface des produits, qui est causé par la différence de propriétés et de textures de la surface des produits et d'autres matières premières, et il forme une peau qui pèle et peut être enlevée.
Lorsque la stratification est sérieuse, toute la section transversale est composée de différentes couches et n'a pas été fondue ensemble. Lorsque les défauts sont moins évidents, l'apparence des produits peut répondre aux exigences, mais casse les propriétés mécaniques des produits.
Cause:
Il existe deux principales causes de laminage. Le premier est que lorsque deux types différents de matières premières se mélangent de manière incorrecte. Les deux matières premières seront transportées dans le tonneau en même temps sous la pression. Cependant, lorsque le moule ne peut pas être fondu ensemble lorsqu'il est refroidi, tout comme différentes couches sont pressées ensemble de force pour former des produits.
Deuxièmement : si la matière fondue à froid est forcée de passer à travers la porte étroite, la contrainte de cisaillement sera générée. Une contrainte de cisaillement trop élevée entraînera que la couche fondue fondue à l'avance ne peut pas être complètement fusionnée.
Risque de mélange :
Une chose dont il faut être conscient est que certaines matières premières mélangées entraîneront une forte réaction chimique, comme le PVC et l'Avetal ne doivent pas être mélangés.
Argent linéaire
Le ruban linéaire peut n'être qu'un phénomène local, mais peut s'étendre à toute la surface lorsqu'il est grave.
L'argent linéaire affectera l'apparence des produits et endommagera également les propriétés mécaniques des produits.
Cause:
Les deux points suivants provoquent la linéaire d'argent :
La matière première est humide et certaines d'entre elles vont absorber la vapeur de l'air. Si la matière première est trop humide, la vapeur sous pression peut être générée sous la haute température et la haute pression du baril. Ces vapeurs traversent la surface du produit et forment des rayures argentées.
Le bain de fusion subit des dommages thermiques et génère une dégradation locale. Le gaz volatil généré sera bloqué à la surface des moisissures et générera des rayures à la surface des produits.
Ce n'est pas aussi pire que la dégradation. Tant que la température de fusion est élevée ou qu'elle est soumise à une contrainte de cisaillement lors de la plastification ou de l'injection dans le moule, cela peut arriver.
Brillance/ombre
La finition de surface des produits doit être la même que celle des moules. Lorsque la finition de surface de deux est différente, les défauts de brillance/ombre se sont produits.
La surface sera sombre lorsque des défauts se produiront et la surface rugueuse sera lisse et brillante.
Cause:
Les causes de brillance/ombre incluent :
La masse fondue s'écoule de manière irrégulière ou la température de la surface du moule est basse, ce qui fait que la finition de la surface du moule ne peut pas être dupliquée lors du moulage du matériau.
Pendant le maintien de la pression, la pression dans la cavité n'est pas suffisamment élevée pour que le matériau adhère à la surface du moule lors du processus de refroidissement, laissant des marques de retrait.
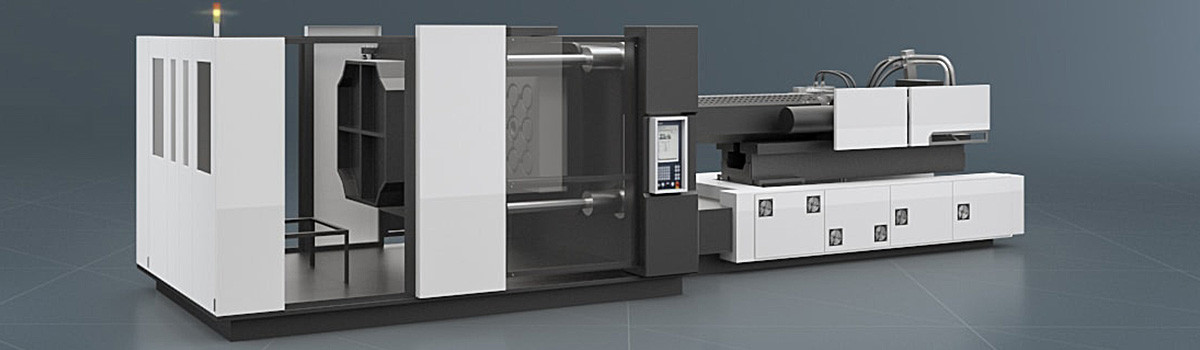
Marques d'écoulement
Les marques de flux peuvent être trouvées sur la surface des produits sous de multiples formes. Généralement, il formera une zone d'ombre.
Les marques de flux ne produisent aucun relief ou dépression sur la surface des produits, qui ne peuvent pas être ressentis avec les doigts. Ce défaut est également appelé marques de traînée, images fantômes et ombres.
Lorsque les marques de flux sont évidentes, cela génère des rainures et laisse des défauts comme des marques sur la surface des produits.
Cause:
Les marques de flux peuvent être trouvées lorsque :
La fluidité de la matière fondue est médiocre ou la température de surface du moule est basse, ce qui entraîne une grande résistance à l'écoulement du plastique lors du processus de remplissage du moule.
Dans le remplissage du moule, l'écoulement à l'état fondu avec résistance, qui peut être causé par la surface inégale de la matrice, les marques ou les motifs imprimés sur la surface de la matrice, ou le changement de direction de l'écoulement à l'état fondu pendant le processus de remplissage.
Ligne de jonction
La ligne de jonction est générée lorsque deux fronts de fusion se rencontrent pendant le remplissage du moule et apparaîtra sur la surface du produit comme une ligne.
La ligne de jointure est comme la ligne de fissuration à la surface des produits, ce qui n'est pas évident à détecter.
Lors de la conception de moules, certaines lignes de joint visibles sont inévitables. Dans ce cas, raccourcir au maximum la ligne de jointage pour éviter d'endommager la résistance et l'aspect des produits.
Cause:
Il existe de nombreuses raisons à la génération d'un front de fusion. La raison la plus probable pourrait être l'écoulement de la matière fondue le long des bords du noyau du moule. Lorsque les deux fontes se rencontrent, cela produit les lignes de jonction. La température de deux fronts de fonte doit être suffisamment élevée pour leur permettre de fusionner avec succès et n'affecte pas la résistance et l'apparence des produits.
Lorsque les deux fontes ne peuvent pas fusionner complètement, les défauts seront produits.
Causes des défauts :
Le moule a des parties plus épaisses et plus minces, et la vitesse d'écoulement des fontes est différente, lorsque la fonte coule à travers la partie mince du moule, la température est basse.
La longueur de chaque coureur est différente. Les coureurs solitaires seront faciles à refroidir.
La pression de la cavité du moule n'est pas suffisante pour permettre à la masse fondue de fusionner complètement pendant l'étape de maintien de la pression.
Les bulles restantes rendent le front de fusion incapable de fusionner, ce qui entraînera également une brûlure.
Brûlant
La combustion est similaire à celle d'un tir court, mais avec des bords de décoloration irréguliers et une légère odeur de brûlé. Les zones de noir de carbone apparaîtront sur le produit, lorsque la condition est grave, accompagnées d'une odeur de plastique brûlé.
Si les défauts ne sont pas éliminés, il y a souvent un dépôt noir sur le moule. Si les substances gazeuses ou pétrolières produites par la combustion ne sont pas contrôlées immédiatement, elles peuvent obstruer les trous d'aération. Le brûlage se trouve généralement au bout des allées.
Cause:
La combustion est causée par l'effet de combustion interne. Lorsque la pression dans l'air augmente fortement en très peu de temps, la température augmente et provoque des brûlures. Selon les données recueillies, l'effet de combustion interne dans le processus de moulage par injection peut produire une température élevée jusqu'à 600 degrés.
Une brûlure peut se produire lorsque :
La vitesse de remplissage du moule est rapide, de sorte que l'air ne peut pas être évacué de la cavité du moule, et génère des bulles d'air dues au bloc du plastique entrant, et conduit à un effet de combustion interne après avoir été comprimé.
Les orifices d'aération sont bouchés ou la ventilation n'est pas fluide.
L'air dans le moule doit être évacué des trous d'air. Si la ventilation est affectée par la position, le nombre, la taille ou les fonctions, l'air restera dans le moule et provoquera des brûlures. Une grande force de serrage du moule entraînera également une mauvaise ventilation.
rétrécissement
Le rétrécissement fait référence aux légers creux à la surface des produits.
Lorsque les défauts sont légers, la surface des produits est inégale. Quand c'est grave, la grande surface de produits s'effondrera. Les produits avec des arcs, des poignées et des saillies souffrent souvent de défauts de retrait.
Cause:
Le rétrécissement est causé par un rétrécissement sur une grande surface des matières premières pendant le refroidissement.
Dans la zone épaisse des produits (comme l'arche), la température centrale du matériau est faible, de sorte que le rétrécissement se produira plus tard que celui de la surface, ce qui produira une force de contraction à l'intérieur de la matière première et tirera le côté extérieur dans la dépression vers l'intérieur pour produire le rétrécissement.
Les rétrécissements se produisent dans les situations suivantes :
La pression dans la cavité du moule est inférieure à la force générée par le rétrécissement de la matière première lors du processus de refroidissement.
Temps de pressurisation insuffisant de la cavité du moule pendant le processus de refroidissement, entraînant l'écoulement de la matière première hors de la cavité depuis la porte.
La matière première n'a pas une capacité tampon suffisante pendant l'étape de moulage et de maintien de la pression car la vis est complètement retirée avant l'injection de la matière première en excès.
Les sections transversales des portes et des glissières sont beaucoup plus petites que l'épaisseur des produits, ce qui signifie que les portes sont déjà congelées avant le processus d'extrusion des produits.
Bubbles
Les bulles de vide se présentent sous forme de bulles d'air, que l'on retrouve facilement sur les produits transparents. On peut également le voir sur la section transversale des produits opaques.
Cause:
Les bulles d'air sont la partie sous vide des produits, qui sont produites lorsque la matière première rétrécit pendant le processus de refroidissement.
Semblable au rétrécissement, l'intérieur de la matière première produit la force contractile. La différence est que l'apparence extérieure des produits a été solidifiée lorsque les bulles se forment et qu'il n'y a pas d'effondrement, de sorte que les bulles creuses sont générées.
Les causes des bulles sont les mêmes que celles de la réduction, notamment :
Pression de cavité de moule inefficace
Temps de pressurisation de la cavité insuffisant
La taille du coureur et de la porte est trop petite
Marques de pulvérisation
Les marques de pulvérisation se réfèrent à la zone filetée opposée à la porte. Les marques de pulvérisation affectent non seulement l'apparence des produits, mais affectent également la résistance des produits.
Cause:
Les marques de pulvérisation sont causées par le flux de matière fondue hors de contrôle pendant le processus de remplissage du moule.
Le plastique fondu pénètre dans le moule sous l'énorme pression. Si la vitesse de remplissage du moule est trop élevée, le plastique s'éjectera de l'espace ouvert de la cavité du moule, puis reviendra rapidement et refroidira. À ce moment-là, les fils se forment, ce qui bloque l'entrée du plastique fondu dans les portes.
La principale cause des marques de pulvérisation est la position incorrecte des portes ou la conception de la porte. Les deux situations suivantes aggravent la situation des défauts :
Grande vitesse de remplissage du moule
Mauvaise fluidité lors du remplissage du moule