Moulage par injection thermoplastique
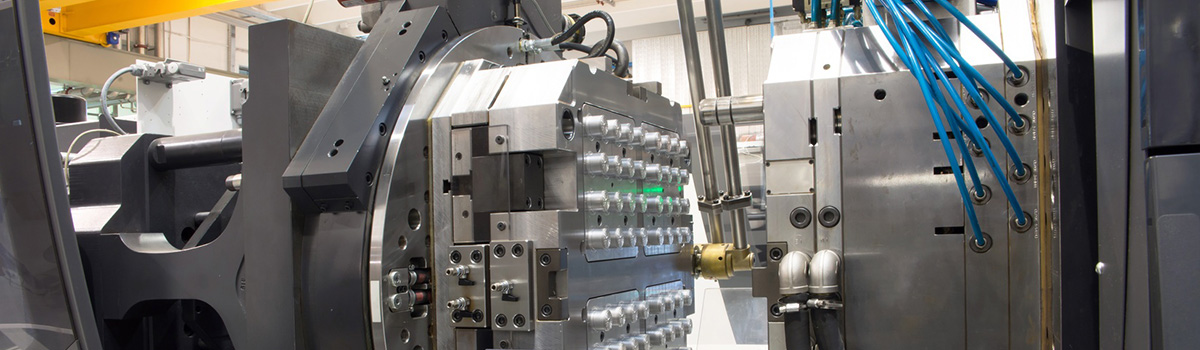
Le moulage par injection thermoplastique est un processus de fabrication populaire utilisé pour créer diverses pièces en plastique pour de multiples industries. Ce processus consiste à faire fondre des granulés de plastique et à les injecter dans un moule pour produire une forme tridimensionnelle. Le moulage par injection thermoplastique est très efficace et rentable pour produire de grands volumes de pièces en plastique de haute qualité avec des tolérances serrées. Ce guide complet explorera les différents aspects du moulage par injection thermoplastique, y compris ses avantages et ses inconvénients, les types de thermoplastiques utilisés, le processus de moulage par injection, les considérations de conception et bien plus encore.
Histoire du moulage par injection thermoplastique
L'histoire du moulage par injection thermoplastique s'étend sur plus d'un siècle d'avancées technologiques, de développements de matériaux et d'applications industrielles. Depuis ses humbles débuts en tant que processus de moulage de celluloïd jusqu'à la technologie sophistiquée actuelle, le moulage par injection continue d'être une technique de fabrication vitale, stimulant l'innovation et façonnant diverses industries.
- Premiers développements :John Wesley Hyatt et son frère Isaiah ont développé la première machine de moulage par injection pratique, retraçant les origines du moulage par injection thermoplastique à la fin du 19e siècle. En 1872, ils ont breveté un appareil qui utilisait un piston pour injecter du celluloïd dans une cavité de moule, créant ainsi des objets solides. Cette percée a jeté les bases du processus moderne de moulage par injection.
- Progrès dans les matériaux :Au début du XXe siècle, l'introduction de nouveaux polymères synthétiques a ouvert de nouvelles possibilités pour le moulage par injection. La bakélite, une résine phénolique, est devenue un matériau populaire pour le moulage en raison de ses excellentes propriétés d'isolation électrique. Tout au long des années 20 et 1930, les progrès de la chimie des polymères ont conduit au développement d'autres thermoplastiques, tels que le polystyrène et le polyéthylène, qui ont encore élargi la gamme de matériaux adaptés au moulage par injection.
- Adoption industrielle : L'adoption généralisée du moulage par injection thermoplastique a commencé dans les années 1950 lorsque les fabricants ont reconnu sa rentabilité et sa polyvalence. L'introduction de machines à haute pression a permis d'accélérer les temps de cycle et d'augmenter les volumes de production. En conséquence, une sélection variée de produits à usage personnel et industriel a vu le jour. Ceux-ci comprenaient des composants automobiles, des appareils électroménagers et des jouets.
- Innovations technologiques :Au fil des décennies, la technologie de moulage par injection a continué d'évoluer. Dans les années 1960, des machines contrôlées par ordinateur sont apparues, permettant un contrôle précis du processus de moulage. L'introduction de systèmes de canaux chauds dans les années 1980 a réduit les déchets et amélioré l'efficacité en éliminant le besoin de canaux et de carottes. Ces dernières années, les progrès de l'automatisation, de la robotique et de l'impression 3D ont encore révolutionné l'industrie du moulage par injection, permettant des conceptions complexes et réduisant le temps de production.
- Durabilité et recyclage :Avec des préoccupations environnementales croissantes, l'industrie du moulage par injection a adopté des mesures de durabilité. Les fabricants ont développé des thermoplastiques biosourcés et recyclés, réduisant ainsi la dépendance aux matériaux à base de combustibles fossiles. De plus, des technologies de recyclage améliorées ont permis le retraitement des déchets post-consommation et post-industriels, minimisant l'impact environnemental du moulage par injection thermoplastique.
- Perspectives futures:L'avenir du moulage par injection thermoplastique semble prometteur. L'industrie explore des innovations telles que le moulage par micro-injection pour les composants miniatures, les techniques multi-matériaux et de surmoulage pour les pièces complexes, et l'intégration de technologies intelligentes pour la surveillance et l'optimisation des processus. De plus, les chercheurs s'attendent à ce que les progrès des matériaux biodégradables et de la fabrication additive révolutionnent le domaine, rendant le moulage par injection encore plus durable et polyvalent.
Avantages du moulage par injection thermoplastique
Le moulage par injection thermoplastique offre de nombreux avantages aux fabricants. Il offre une flexibilité de conception, permettant des conceptions complexes et complexes avec diverses fonctionnalités. Le processus est rentable, réduisant les déchets de matériaux et abaissant les coûts unitaires. Le moulage par injection thermoplastique prend en charge plusieurs matériaux, offrant une polyvalence pour différentes applications.
- Flexibilité de conception:Le moulage par injection thermoplastique permet des conceptions complexes et complexes avec des caractéristiques telles que des contre-dépouilles, des parois minces et des épaisseurs variables, offrant aux concepteurs une immense liberté.
- Rapport coût-efficacité: Le processus est très efficace, réduisant les déchets de matériaux et abaissant les coûts unitaires. Le moulage simultané de plusieurs pièces et les cycles de production rapides contribuent à réduire les coûts.
- Polyvalence des matériaux : Le moulage par injection thermoplastique prend en charge une large gamme de matériaux, permettant aux fabricants de choisir l'option la plus appropriée pour chaque application, y compris les matériaux rigides ou flexibles, transparents ou opaques et résistants aux produits chimiques.
- Solidité et durabilité :Les thermoplastiques moulés par injection peuvent présenter d'excellentes propriétés mécaniques, telles qu'une résistance élevée, une ténacité et une résistance aux chocs. Les options de renforcement, comme les fibres de verre ou de carbone, améliorent encore ces propriétés.
- Cohérence et qualité :Le moulage par injection garantit une qualité et une précision dimensionnelle constantes d'une pièce à l'autre, offrant des tolérances serrées et des produits fiables. Le processus fournit également une finition de surface lisse et uniforme, éliminant le besoin d'opérations de finition supplémentaires.
- Évolutivité et production de masse :Le moulage par injection est évolutif de volumes faibles à élevés, ce qui le rend adapté à la production de masse. Une fois que les fabricants ont créé le moule, ils peuvent produire de grandes quantités de pièces identiques avec des variations minimes.
- Intégration et assemblage :Les pièces moulées par injection peuvent incorporer plusieurs composants en une seule pièce, ce qui réduit le besoin de processus d'assemblage supplémentaires. Cette intégration améliore les performances du produit, réduit le temps d'assemblage et diminue les coûts.
- Durabilité:L'industrie du moulage par injection met de plus en plus l'accent sur la durabilité. La disponibilité de matériaux biosourcés et recyclés permet de produire des produits respectueux de l'environnement. L'utilisation efficace des matériaux et la recyclabilité des thermoplastiques contribuent à un processus de fabrication plus écologique.
Ces avantages en ont fait une méthode de fabrication largement adoptée dans diverses industries, offrant des solutions de haute qualité, rentables et respectueuses de l'environnement pour les exigences de produits complexes.
Inconvénients du moulage par injection thermoplastique
Bien que le moulage par injection thermoplastique offre de nombreux avantages, il existe également plusieurs inconvénients. Les fabricants doivent évaluer soigneusement ces facteurs et les peser par rapport aux avantages pour déterminer l'adéquation du moulage par injection thermoplastique à leurs applications spécifiques.
- Investissement initial élevé : La mise en place d'une opération de moulage par injection thermoplastique nécessite un investissement initial important dans la conception et la fabrication de moules et l'achat de machines spécialisées. Les coûts associés à la création de moules et d'outillage peuvent être considérables, en particulier pour les conceptions complexes et complexes.
- Limites de conception : Bien que le moulage par injection thermoplastique offre une flexibilité de conception, certaines limitations existent. Par exemple, obtenir une épaisseur de paroi uniforme dans toute la pièce peut être difficile, entraînant des variations dans la distribution des matériaux et des faiblesses structurelles potentielles. De plus, la présence de contre-dépouilles ou de géométries complexes peut nécessiter l'utilisation de caractéristiques de moule supplémentaires ou d'opérations secondaires, ce qui augmente les coûts et le temps de production.
- Longs délais:Le processus de conception et de fabrication de moules pour le moulage par injection peut prendre du temps, ce qui entraîne des délais plus longs pour le développement de produits. Le processus d'itération de conception, la production de moules et les tests peuvent ajouter un temps considérable au calendrier de production global, ce qui peut ne pas convenir aux projets avec des délais serrés.
- Contraintes de sélection de matériaux :Bien que le moulage par injection thermoplastique prenne en charge une large gamme de matériaux, il existe certaines limitations et contraintes. Certains matériaux peuvent avoir des exigences de traitement spécifiques ou une disponibilité limitée, ce qui a un impact sur les choix de conception et la sélection des matériaux pour une application particulière.
- Limites de taille de pièce :Les machines de moulage par injection ont des limites de taille, à la fois en termes de taille physique de l'appareil et de taille des moules qu'elles peuvent accueillir. La production de pièces volumineuses peut nécessiter un équipement spécialisé ou des méthodes de fabrication alternatives.
- Impact environnemental:Alors que l'industrie travaille vers la durabilité, le processus de moulage par injection thermoplastique génère toujours des déchets, y compris des déchets et des carottes. L'élimination et le recyclage appropriés de ces matériaux sont nécessaires pour minimiser l'impact environnemental.
- La complexité de l'optimisation des processus :L'obtention de paramètres de processus optimaux pour le moulage par injection de thermoplastiques peut être complexe et prendre du temps. Les fabricants doivent soigneusement contrôler et optimiser la température, la pression, les taux de refroidissement et les temps de cycle pour garantir une qualité constante des pièces et minimiser les défauts.
Types de thermoplastiques utilisés dans le moulage par injection
Ce ne sont là que quelques exemples des thermoplastiques couramment utilisés dans le moulage par injection. Chaque matériau possède des propriétés uniques, ce qui le rend adapté à des applications spécifiques basées sur la résistance, la flexibilité, la résistance chimique, la transparence et le coût. Les fabricants doivent tenir compte de ces propriétés et exigences lors de la sélection du thermoplastique approprié pour leurs projets de moulage par injection.
- Polypropylène (PP) :Le polypropylène est un thermoplastique polyvalent couramment utilisé dans le moulage par injection. Il offre une excellente résistance chimique, une faible densité et une bonne résistance aux chocs. Le PP (polypropylène) a de nombreuses applications dans les emballages, les composants automobiles, les appareils électroménagers et les dispositifs médicaux.
- Polyéthylène (PE) :Le polyéthylène est un autre thermoplastique largement utilisé dans le moulage par injection. Il est disponible sous diverses formes, telles que le polyéthylène haute densité (HDPE) et le polyéthylène basse densité (LDPE). Le PE offre une bonne résistance chimique, ténacité et flexibilité, ce qui le rend adapté aux bouteilles, conteneurs et tuyaux.
- Polystyrène (PS):Le polystyrène est un thermoplastique polyvalent connu pour sa clarté, sa rigidité et son prix abordable. Il trouve une utilisation courante dans les emballages, les biens de consommation et les produits jetables. Le PS (polystyrène) permet un traitement rapide et offre une bonne stabilité dimensionnelle, mais il peut être cassant et sensible à la fissuration sous contrainte environnementale.
- Acrylonitrile Butadiène Styrène (ABS) : L'ABS est un thermoplastique populaire connu pour son excellente résistance aux chocs et sa durabilité. Il combine les propriétés de l'acrylonitrile, du butadiène et du styrène pour créer un matériau polyvalent adapté aux pièces automobiles, aux boîtiers électroniques et aux jouets.
- Chlorure de polyvinyle (PVC) : Le PVC est un thermoplastique largement utilisé, connu pour son excellente résistance chimique, sa durabilité et son faible coût. Il peut être rigide ou souple selon la formulation et les additifs utilisés. Le PVC (chlorure de polyvinyle) est couramment utilisé dans la construction, l'isolation électrique, les produits de santé et l'emballage.
- Polycarbonate (PC) : Le polycarbonate est un thermoplastique transparent avec un impact extraordinaire et une résistance élevée à la chaleur. Il trouve une utilisation courante dans les applications qui nécessitent une clarté optique, telles que les composants automobiles, les casques de sécurité et les écrans électroniques.
- Nylon (Polyamide) :Le nylon est un thermoplastique solide et durable connu pour ses excellentes propriétés mécaniques et sa résistance chimique. Il trouve une utilisation courante dans les applications qui exigent une résistance élevée, telles que les pièces automobiles, les composants industriels et les biens de consommation.
- Polyéthylène téréphtalate (PET) :Le PET est un thermoplastique populaire pour la production de bouteilles, de contenants et de matériaux d'emballage. Il offre une bonne clarté, une bonne résistance chimique et des propriétés barrières, ce qui le rend adapté aux applications alimentaires et de boissons.
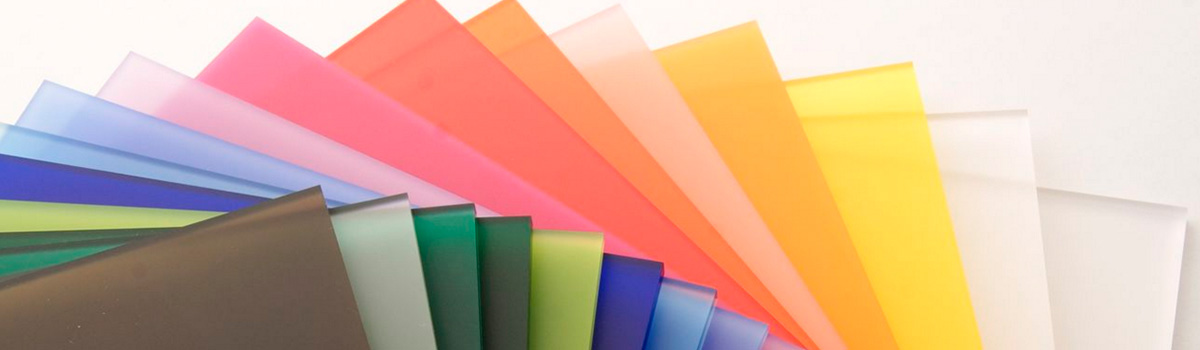
Propriétés des thermoplastiques utilisés dans le moulage par injection
Ces propriétés des thermoplastiques jouent un rôle crucial dans la détermination de leur adéquation à des applications spécifiques de moulage par injection. Les fabricants doivent examiner attentivement ces propriétés et sélectionner le thermoplastique approprié en fonction des performances souhaitées, des conditions environnementales et des exigences de coût.
- Propriétés mécaniques:Les thermoplastiques utilisés dans le moulage par injection peuvent présenter diverses propriétés mécaniques, notamment la résistance à la traction, la résistance aux chocs et la résistance à la flexion. Ces propriétés déterminent la capacité du matériau à résister aux forces appliquées et sa durabilité globale dans diverses applications.
- Résistance chimique:De nombreux thermoplastiques utilisés dans le moulage par injection possèdent une résistance remarquable aux produits chimiques, aux solvants et aux huiles. Cette propriété est cruciale pour les applications impliquant une exposition à des environnements difficiles ou à des substances corrosives.
- Stabilité thermique:La stabilité thermique des thermoplastiques fait référence à leur capacité à résister à des températures élevées sans dégradation significative. Certains thermoplastiques présentent une excellente résistance à la chaleur, ce qui leur permet de conserver leurs propriétés mécaniques même à des températures élevées.
- Propriétés électriques:Les thermoplastiques utilisés dans le moulage par injection peuvent avoir des propriétés électriques spécifiques, notamment l'isolation électrique, la conductivité ou la rigidité diélectrique. Ces propriétés sont essentielles pour les applications dans les industries électriques et électroniques, où les matériaux doivent fournir des performances électriques fiables.
- Transparence et Clarté :Certains thermoplastiques, tels que le polycarbonate et le PET, offrent une excellente transparence et clarté, ce qui les rend adaptés aux applications nécessitant des propriétés optiques. Les fabricants utilisent couramment ces matériaux dans des produits tels que des fenêtres transparentes, des lentilles et des écrans.
- Flexibilité et robustesse : La flexibilité et la ténacité sont des propriétés essentielles des thermoplastiques utilisés dans les applications qui nécessitent une résistance aux chocs et une durabilité. Certains thermoplastiques, tels que l'ABS et le nylon, offrent une excellente ténacité, leur permettant de résister à des impacts répétés sans se casser.
- Stabilité dimensionnelle:La stabilité dimensionnelle fait référence à la capacité d'un thermoplastique à conserver sa forme et sa taille dans des conditions variables, y compris les changements de température. Les matériaux avec une bonne stabilité dimensionnelle garantissent des dimensions de pièces constantes, minimisant le risque de gauchissement ou de distorsion.
- Compatibilité chimique :La compatibilité chimique des thermoplastiques fait référence à leur capacité à résister à la dégradation ou à l'interaction avec divers produits chimiques, notamment les acides, les bases et les solvants. Pour garantir des performances optimales, il est essentiel de sélectionner un thermoplastique capable de résister à l'environnement chimique spécifique qu'il rencontrera dans l'application prévue.
- Densité: Les thermoplastiques ont des épaisseurs variables, ce qui peut avoir un impact sur leur poids et les propriétés globales des pièces. Les matériaux à faible densité, tels que le polyéthylène, offrent des solutions légères, tandis que les matériaux à haute densité, tels que le polypropylène, offrent une résistance et une rigidité accrues.
Processus de moulage par injection : étape par étape
Le processus de moulage par injection suit ces étapes, permettant la production efficace et précise de pièces thermoplastiques de haute qualité. Chaque étape nécessite un contrôle et une surveillance minutieux pour garantir la cohérence des dimensions des pièces, des propriétés des matériaux et de la qualité globale.
- Conception et fabrication de moules : La première étape du processus de moulage par injection est la conception et la fabrication du moule. Les fabricants doivent créer une conception de moule précise et détaillée pour obtenir les spécifications de pièces souhaitées. Les fabricants fabriquent ensuite le moule en utilisant diverses techniques, telles que la CNC ou l'usinage par décharge électrique (EDM).
- Materielle préparation: La prochaine étape est la préparation une fois le moule prêt. Les pastilles ou granulés thermoplastiques sont sélectionnés en fonction des propriétés souhaitées du matériau et fondus dans une trémie. Les opérateurs introduisent ensuite le matériau dans le cylindre de la machine de moulage par injection, où il subit une fusion et une homogénéisation.
- Injection:Pendant la phase d'injection, les opérateurs injectent le thermoplastique fondu dans la cavité du moule sous haute pression. L'unité d'injection de la machine pousse le matériau fondu à travers une buse et dans le moule. Le matériau remplit la cavité du moule en prenant la forme de la pièce souhaitée.
- Refroidissement et solidification :Après avoir rempli le moule, les opérateurs permettent au plastique fondu de refroidir et de se solidifier. Le refroidissement est crucial pour obtenir une stabilité dimensionnelle et une formation correcte des pièces. Les opérateurs peuvent contrôler le processus de refroidissement en faisant circuler le liquide de refroidissement dans des canaux à l'intérieur du moule ou en utilisant des plaques de refroidissement.
- Ouverture et éjection du moule :Les opérateurs ouvrent le moule et éjectent la pièce de la cavité du moule une fois que le plastique se solidifie. Le système d'éjection de la machine utilise des broches, des plaques d'éjection ou des jets d'air pour retirer la région du moule. Le moule est alors prêt pour le prochain cycle d'injection.
- Post-traitement: Après éjection, la pièce peut subir des opérations de post-traitement, telles que détourage, ébavurage ou finition de surface. Ces étapes permettent d'éliminer l'excédent de matière, de lisser les bords rugueux et d'améliorer l'aspect final de la pièce.
- Contrôle de la qualité: La dernière étape consiste à inspecter la qualité des pièces injectées et à s'assurer qu'elles répondent aux exigences spécifiées. Diverses techniques de contrôle de la qualité, y compris la mesure dimensionnelle, l'inspection visuelle et les tests fonctionnels, peuvent être utilisées pour vérifier la qualité et l'intégrité de la pièce.
- Recyclage et réutilisation des matériaux :Tout matériau excédentaire ou de rebut généré lors du moulage par injection peut être recyclé et réutilisé. La réduction de l'utilisation de nouveaux matériaux thermoplastiques permet de minimiser les déchets et d'améliorer la durabilité.
Équipement utilisé dans le moulage par injection
Ces composants d'équipement facilitent le processus de moulage par injection, depuis la fusion et l'injection du matériau thermoplastique jusqu'à la mise en forme, le refroidissement et l'éjection de la pièce finale. Le bon fonctionnement et l'entretien de ces composants d'équipement sont cruciaux pour obtenir une production de moulage par injection efficace et de haute qualité.
- Machine de moulage par injection :L'équipement principal du moulage par injection est responsable de la fusion du matériau thermoplastique, de son injection dans le moule et du contrôle du processus.
- Mold: Le moule, conçu sur mesure pour créer la forme et les caractéristiques souhaitées de la pièce en plastique, comprend deux moitiés, la cavité et le noyau. Les opérateurs le montent sur l'unité de serrage de la machine de moulage par injection.
- Trémie:Récipient qui contient le matériau thermoplastique sous forme de pastilles ou de granulés et l'introduit dans le cylindre de la machine de moulage par injection pour la fusion et l'injection.
- Canon et vis : Le cylindre, une chambre cylindrique, fond et homogénéise le matériau thermoplastique lorsque la vis tourne à l'intérieur pour fondre, mélanger et standardiser le matériau.
- Systèmes de chauffage et de refroidissement :Les machines de moulage par injection ont des éléments chauffants, tels que des radiateurs électriques ou à huile chaude, pour élever la température du fourreau, et des systèmes de refroidissement, tels que la circulation d'eau ou d'huile, pour refroidir le moule et solidifier la pièce en plastique.
- Système d'éjecteur :Enlève la pièce moulée de la cavité du moule après la solidification, en utilisant généralement des éjecteurs, des plaques ou des jets d'air lors de l'ouverture du moule.
- Système de contrôle:Surveille et contrôle divers paramètres du processus de moulage par injection, permettant aux opérateurs de définir et d'ajuster des paramètres tels que la vitesse d'injection, la température, la pression et le temps de refroidissement.
Machines de moulage par injection : types et caractéristiques
Chaque type de machine de moulage par injection a ses caractéristiques et ses avantages, permettant aux fabricants de choisir l'appareil le mieux adapté à leurs exigences de production spécifiques.
- Machines de moulage par injection hydraulique : Ces machines utilisent des systèmes hydrauliques pour générer la pression nécessaire pour injecter du plastique fondu dans le moule. Ils sont connus pour leur force de serrage élevée, leur contrôle précis et leur polyvalence dans la manipulation de divers thermoplastiques. Les machines hydrauliques conviennent à la production à grande échelle et peuvent accueillir des moules complexes.
- Machines électriques de moulage par injection :Les machines électriques utilisent des servomoteurs électriques pour le fonctionnement de la machine, y compris les systèmes d'injection, de serrage et d'éjection. Ils offrent un contrôle précis, une efficacité énergétique et des temps de réponse plus rapides que les machines hydrauliques. Les machines électriques sont idéales pour les applications de moulage de précision qui nécessitent une répétabilité et une précision élevées.
- Machines hybrides de moulage par injection :Les machines hybrides combinent les avantages des dispositifs hydrauliques et électriques. Ils utilisent une combinaison de systèmes d'asservissement hydrauliques et électriques pour obtenir une précision, une efficacité énergétique et une rentabilité élevées. Les machines hybrides conviennent à une large gamme d'applications, offrant un équilibre entre performances et coûts d'exploitation.
- Machines de moulage par injection à deux plateaux : Les machines à deux plateaux ont une conception unique avec deux plateaux séparés pour le serrage du moule. Cette conception offre une stabilité accrue, une meilleure synchronisation des moules et permet des tailles de moules plus grandes et des forces de serrage plus élevées. Les machines à deux plateaux conviennent aux pièces volumineuses et complexes qui nécessitent un moulage précis.
- Machines de moulage par injection multi-composants :Les fabricants conçoivent ces machines pour produire des pièces avec plusieurs matériaux ou couleurs en un seul cycle de moulage. Ils disposent de différentes unités d'injection et de moules, permettant l'injection simultanée de différents matériaux. Les machines multi-composants offrent flexibilité et efficacité dans la fabrication de pièces complexes aux caractéristiques variées.
- Machines de moulage par micro-injection :Spécialement conçues pour produire des pièces petites et précises, les machines de moulage par micro-injection offrent une précision et une exactitude incroyablement élevées. Ils peuvent produire des détails complexes avec des tolérances serrées et un minimum de déchets de matériaux. L'électronique, les dispositifs médicaux et la micro-optique utilisent couramment des machines de moulage par micro-injection.
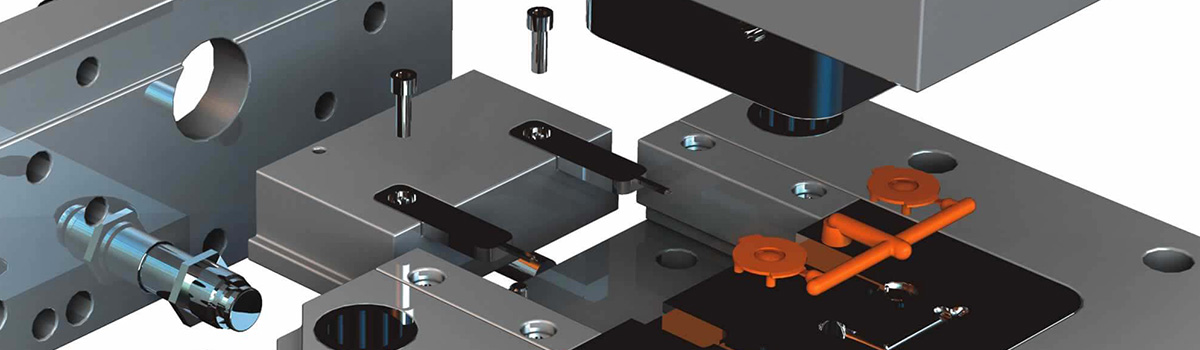
Considérations relatives à la conception de moules pour le moulage par injection
Des considérations de conception de moules minutieuses sont essentielles pour une production de moulage par injection réussie.
- Conception de pièce :La conception du moule doit répondre aux exigences spécifiques de la pièce, y compris sa forme, ses dimensions et ses caractéristiques fonctionnelles. Les fabricants doivent correctement prendre en compte les angles de dépouille, l'épaisseur des parois, les contre-dépouilles et tous les éléments nécessaires pour garantir la facilité d'éjection et la qualité des pièces.
- Matériel de moule: La sélection du matériau du moule est cruciale pour atteindre la durabilité, la stabilité dimensionnelle et la résistance à la chaleur. Les matériaux de moulage courants comprennent les alliages d'acier, les alliages d'aluminium et les aciers à outils. Le choix du matériau dépend de facteurs tels que le volume de production, la complexité de la pièce et la durée de vie prévue de l'outil.
- Système de refroidissement:Un refroidissement efficace est essentiel pour une bonne solidification des pièces et pour minimiser le temps de cycle. La conception du moule doit incorporer des canaux de refroidissement ou des inserts stratégiquement positionnés pour assurer un refroidissement uniforme du moule. Un refroidissement adéquat réduit le risque de gauchissement, de retrait et de défauts de pièces.
- Ventilation:Une ventilation adéquate est nécessaire pour permettre l'échappement de l'air et des gaz pendant le processus d'injection. Une ventilation insuffisante peut entraîner des pièges à gaz, des marques de brûlure ou un remplissage incomplet des pièces. Les fabricants peuvent réaliser la ventilation en incorporant des rainures de ventilation, des broches ou d'autres mécanismes dans la conception du moule.
- Système d'éjection :La conception du moule doit inclure un système d'éjection efficace pour retirer de manière sûre et efficace la pièce moulée de la cavité du moule. Le système d'éjection peut consister en des broches d'éjection, des manchons ou d'autres mécanismes, stratégiquement positionnés pour éviter toute interférence avec la fonction ou les caractéristiques critiques.
- Conception de porte :La porte est l'endroit où le plastique fondu pénètre dans la cavité du moule. La conception de la porte doit garantir un remplissage correct des pièces, minimiser les conduites d'écoulement et empêcher le gel prématuré du matériau. Les conceptions de porte standard comprennent des portes de bord, des portes de tunnel et des systèmes de canaux chauds, selon les exigences de la pièce et les propriétés des matériaux.
- Ligne de séparation:La conception du moule doit définir une ligne de séparation appropriée, qui est la ligne où les deux moitiés du moule se rejoignent. Le placement correct de la ligne de séparation garantit un décalage minimal entre la bavure et la ligne de séparation et facilite l'assemblage efficace du moule.
- Maintenance et entretien des moules : Les fabricants doivent tenir compte de la facilité d'entretien, de réparation et d'entretien des moules. Les composants du moule doivent être facilement accessibles pour le nettoyage, l'inspection et le remplacement. L'intégration de fonctionnalités telles que des inserts à changement rapide ou des conceptions de moules modulaires peut améliorer la facilité d'entretien des moules.
Matériaux de moulage utilisés dans le moulage par injection
La collaboration avec des spécialistes des matériaux de moulage et la prise en compte des besoins spécifiques de l'application de moulage peuvent aider à déterminer le matériau le plus approprié pour obtenir des performances de moule et une qualité de pièce optimales.
- Alliages d'acier : Les alliages d'acier, tels que les aciers à outils (par exemple, P20, H13) et les aciers inoxydables, sont couramment utilisés pour les moules de moulage par injection en raison de leur excellente durabilité, résistance à la chaleur et résistance à l'usure. Ces matériaux peuvent résister aux températures et pressions élevées du processus de moulage par injection et offrent une bonne stabilité dimensionnelle pour produire des pièces de haute qualité.
- Alliages d'aluminium :Les alliages d'aluminium, tels que 7075 et 6061, sont légers et offrent une bonne conductivité thermique, ce qui les rend adaptés aux moules qui nécessitent un refroidissement efficace. Les fabricants utilisent souvent des moules en aluminium pour le prototypage, la production à faible volume ou les applications où la réduction de poids est essentielle. Cependant, les moules en aluminium peuvent avoir une durabilité inférieure à celle des alliages d'acier.
- Alliages de Cuivre :Les alliages de cuivre, tels que le cuivre au béryllium, présentent une conductivité thermique élevée et une bonne usinabilité. Ils trouvent une utilisation dans les moules qui nécessitent un excellent transfert de chaleur pour un refroidissement efficace. Les alliages de cuivre peuvent aider à réduire les temps de cycle en dissipant rapidement la chaleur de la pièce moulée, ce qui entraîne une solidification plus rapide.
- Aciers à outils :Les aciers à outils, y compris H13, S7 et D2, sont conçus pour des applications d'outillage à haute performance. Ces aciers offrent une combinaison de haute résistance, dureté et résistance à l'usure. Les aciers à outils conviennent aux moules avec des volumes de production élevés, des matériaux abrasifs ou des conditions de moulage exigeantes.
- Alliages de nickel :Les alliages de nickel, tels que l'Inconel et l'Hastelloy, sont connus pour leur résistance à la corrosion, leur résistance à haute température et leur stabilité thermique exceptionnelles. Les fabricants utilisent ces alliages dans des moules qui manipulent des matériaux corrosifs ou qui nécessitent une résistance aux températures extrêmes et aux environnements de moulage agressifs.
- Matériaux composites:Les matériaux composites, tels que les plastiques renforcés ou les composites avec inserts métalliques, sont parfois utilisés pour des applications de moulage spécifiques. Ces matériaux offrent un équilibre de propriétés, telles qu'une résistance élevée, une stabilité thermique et un poids réduit. Les moules composites peuvent être des alternatives rentables pour des exigences de production spécifiques.
Types de moules d'injection
Le moulage par injection est un procédé de fabrication polyvalent et largement utilisé pour les pièces en plastique.
- Moule à deux plaques :Le moule à deux plaques est le type de moule à injection le plus courant. Il est constitué de deux plaques, la plaque empreinte et la plaque noyau, qui se séparent pour permettre l'éjection de la pièce moulée. La plaque de cavité contient le côté cavité du moule, tandis que la plaque de noyau abrite le côté noyau. Les fabricants utilisent des moules à deux plaques pour produire une large gamme de pièces en raison de leur conception relativement simple.
- Moule à trois plaques :Le moule à trois plaques est une version avancée du moule à deux plaques. Il comprend une plaque supplémentaire, la glissière ou la plaque de coulée. La plaque de glissière crée un canal séparé pour la carotte, les glissières et les portes, permettant un retrait plus facile de la pièce moulée. Les fabricants utilisent couramment des moules à trois plaques pour les détails avec des systèmes de porte complexes ou lorsqu'il est souhaitable d'éviter un vestige de porte sur la pièce.
- Moule à canaux chauds :Le système de canaux et de portes est chauffé dans des moules à canaux chauds, éliminant ainsi le besoin de solidification et de refusion du matériau à chaque cycle. Le système de canaux chauds se compose de collecteurs et de buses chauffés qui maintiennent l'état fondu du plastique. Les moules à canaux chauds offrent des avantages tels qu'un temps de cycle réduit, une réduction des déchets de matériau et une qualité de pièce améliorée en minimisant les vestiges de porte.
- Moule à canaux froids : Les moules à canaux froids ont un système traditionnel de canaux et de portes où le plastique fondu s'écoule à travers des canaux froids qui se solidifient à chaque cycle. Les opérateurs retirent ensuite les canaux solidifiés, ce qui entraîne un gaspillage de matériau. Les fabricants utilisent généralement des moules à canaux complexes pour une production à faible volume ou lorsque les coûts des matériaux sont moins critiques en raison de leur conception plus simple.
- Insérer le moule :Les moules à insert incorporent des inserts en métal ou en plastique dans la cavité du moule pendant le moulage par injection. Les inserts peuvent être pré-placés dans le moule ou insérés par des processus automatisés. Ce moule permet d'intégrer des composants supplémentaires ou des éléments de renforcement dans la pièce moulée, améliorant sa fonctionnalité ou sa résistance.
- Surmoulage : Le surmoulage consiste à mouler un matériau sur un autre, généralement en liant un substrat en plastique rigide avec un élastomère ou un thermoplastique plus souple. Ce processus permet de créer des pièces avec plusieurs matériaux ou textures dans un seul moule, offrant une meilleure adhérence, un meilleur amorti ou des caractéristiques esthétiques.
Facteurs affectant les coûts de moulage par injection
La prise en compte de ces facteurs peut aider les fabricants à estimer et à optimiser le coût du moulage par injection, en garantissant un équilibre entre qualité, efficacité et rentabilité pour leurs besoins de production spécifiques.
- Complexité de la pièce :La complexité de la conception de la pièce joue un rôle important dans la détermination du coût du moulage par injection. Les géométries complexes, les contre-dépouilles, les parois minces ou les caractéristiques complexes peuvent nécessiter des outils supplémentaires, des moules spécialisés ou des cycles plus longs, ce qui augmente le coût de fabrication global.
- Sélection du matériau:Le choix du matériau thermoplastique affecte le coût du moulage par injection. Différents matériaux ont des prix variables par kilogramme, et des facteurs tels que la disponibilité des matériaux, les propriétés et les exigences de traitement peuvent influencer le coût global des matériaux.
- Conception d'outillage et de moule : Les coûts initiaux d'outillage et de conception de moules sont importants dans les coûts de moulage par injection. Des facteurs tels que la complexité du moule, le nombre de cavités, la taille du moule et le matériau du moule contribuent aux dépenses d'outillage et de fabrication du moule. Des moules plus complexes ou des moules nécessitant des fonctionnalités avancées peuvent augmenter l'investissement initial.
- Volume de production: Le volume de production a un impact direct sur le coût par pièce dans le moulage par injection. Des livres plus hauts entraînent souvent des économies d'échelle, réduisant le coût par pièce. À l'inverse, les cycles de production à faible volume peuvent entraîner des frais plus élevés en raison de la configuration, de l'outillage et des déchets de matériaux.
- Temps d'un cycle: Le temps de cycle, qui comprend les phases de refroidissement et d'éjection, affecte la capacité de production et le coût global. Des temps de cycle plus longs entraînent une production réduite et des prix potentiellement plus élevés. L'optimisation de la conception du moule, du système de refroidissement et des paramètres de processus peut réduire les temps de cycle et améliorer l'efficacité.
- Exigences de qualité :Des exigences de qualité strictes ou des certifications spécifiques peuvent avoir un impact sur le coût du moulage par injection. Le respect des tolérances exactes, des exigences de finition de surface ou des tests supplémentaires peut nécessiter d'autres ressources, processus ou inspections, ce qui augmente le coût global.
- Opérations secondaires :Si les pièces moulées nécessitent des opérations de post-traitement telles que l'assemblage, la peinture ou des étapes de finition supplémentaires, ces opérations peuvent augmenter le coût global du moulage par injection.
- Fournisseur et emplacement :Le choix du fournisseur de moulage par injection et son emplacement peuvent affecter les coûts. Les coûts de main-d'œuvre, les frais généraux, la logistique et les frais de transport varient en fonction de l'emplacement du fournisseur, ce qui a une incidence sur le coût de fabrication global.
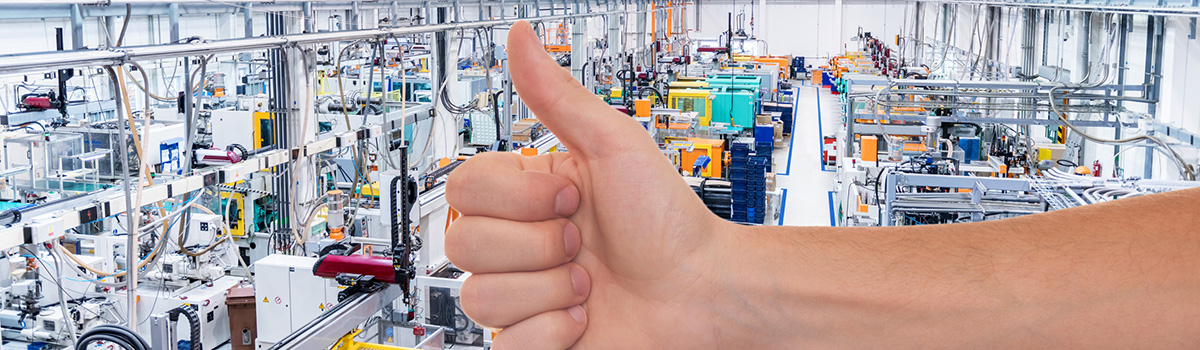
Contrôle de la qualité dans le moulage par injection
La mise en œuvre de mesures de contrôle qualité robustes tout au long du processus de moulage par injection permet d'identifier et de traiter les défauts, écarts ou incohérences potentiels, garantissant ainsi la production de pièces de haute qualité qui répondent aux spécifications et exigences des clients.
- Surveillance du processus : La surveillance continue des paramètres de processus clés, tels que la température de fusion, la pression d'injection, le temps de refroidissement et le temps de cycle, garantit la cohérence et la répétabilité de la production de pièces. La surveillance en temps réel et les systèmes automatisés peuvent détecter les variations ou les écarts par rapport aux paramètres définis, permettant des ajustements en temps opportun et le maintien de la stabilité du processus.
- Inspection et mesure :L'examen et la mesure réguliers des pièces moulées sont essentiels pour vérifier la précision dimensionnelle, la qualité des pièces et le respect des spécifications. Nos services couvrent une gamme de méthodes de contrôle de la qualité, telles que la mesure des dimensions, l'analyse de la qualité de surface, la réalisation d'inspections visuelles et la réalisation de tests fonctionnels. Diverses techniques d'inspection, telles que les machines de mesure de coordonnées (CMM) et les systèmes d'inspection optique et visuelle, sont utilisées pour une évaluation précise.
- Contrôle statistique des processus (SPC) : Le SPC implique la collecte et l'analyse des données de processus pour surveiller et contrôler la qualité du moulage par injection. Les méthodes statistiques, telles que les cartes de contrôle et l'analyse de la capabilité des processus, aident à identifier les tendances, à détecter les variations de processus et à garantir que le processus reste dans les limites de contrôle définies. SPC permet l'identification proactive des problèmes et facilite l'optimisation des processus.
- Test des matériaux: Le test des matières premières, telles que les thermoplastiques, les additifs et les colorants, garantit leur qualité et leur adéquation au moulage par injection. Les tests de matériaux peuvent inclure l'analyse de l'indice de fluidité (MFI), les propriétés mécaniques, les caractéristiques thermiques et la composition des matériaux. La vérification de la qualité des matériaux aide à prévenir les défauts et les incohérences dans les pièces moulées.
- Entretien et inspection de l'outillage :Un bon entretien et une inspection régulière des moules d'injection sont essentiels pour garantir la qualité du moulage par injection. Un nettoyage, une lubrification et une évaluation réguliers des composants du moule aident à prévenir l'usure, les dommages ou la dégradation qui pourraient affecter la qualité des pièces. La réparation ou le remplacement en temps opportun des composants de moule usés ou endommagés est essentiel pour maintenir des performances de moulage constantes.
- Documentation et Traçabilité :Le maintien d'une documentation complète et d'enregistrements de traçabilité est essentiel pour le contrôle de la qualité dans le moulage par injection. Il est essentiel d'enregistrer les paramètres de processus, les résultats d'inspection, les informations sur les matériaux et tous les changements ou ajustements effectués pendant la production. Une documentation appropriée permet la traçabilité des pièces, facilite l'analyse des causes profondes et garantit la cohérence de la qualité.
- Formation et développement des compétences : Fournir des programmes de formation et de développement des compétences adéquats aux opérateurs, aux techniciens et au personnel de contrôle de la qualité améliore leur compréhension des processus de moulage par injection, des exigences de qualité et des techniques d'inspection. Un personnel bien formé peut détecter les défauts, résoudre les problèmes et mettre en œuvre des mesures correctives efficacement, garantissant une production de haute qualité.
Défauts courants de moulage par injection et comment les éviter
Une inspection, une surveillance et une analyse régulières des processus de moulage par injection ainsi qu'un entretien et un réglage appropriés de l'équipement et des moules peuvent aider à identifier et à résoudre ces défauts courants.
- Marques d'évier :Les retassures sont des dépressions ou des indentations sur la surface de la pièce moulée causées par un refroidissement ou un retrait irrégulier. Il faut envisager un emplacement et une conception appropriés de la porte, une conception optimale du système de refroidissement et une répartition uniforme de l'épaisseur des parois pour éviter les marques de chute. L'augmentation de la pression d'injection ou le réglage du temps de refroidissement peuvent également aider à minimiser les retassures.
- Déformation :Le gauchissement fait référence à la déformation ou à la flexion d'une pièce moulée après son éjection en raison d'un refroidissement irrégulier ou de contraintes résiduelles. Le maintien d'une épaisseur de paroi uniforme, l'utilisation de canaux de refroidissement appropriés et la garantie d'un remplissage et d'un garnissage équilibrés du moule sont essentiels pour éviter le gauchissement. L'optimisation de la température du moule, l'utilisation d'angles de dépouille appropriés et le contrôle de la température du matériau et de la vitesse d'injection peuvent aider à minimiser le gauchissement.
- Flash:La bavure se produit lorsqu'un excès de matériau s'écoule dans la ligne de séparation du moule, ce qui entraîne des projections fines et indésirables ou un surplus de matériau sur la pièce finale. On peut prévenir efficacement les bavures en assurant une conception appropriée du moule, notamment en appliquant une force de serrage adéquate, un alignement précis et en utilisant des techniques de ventilation appropriées. L'optimisation des paramètres de processus tels que la pression d'injection, la température et le temps de cycle réduit le flash.
- Tir court:Un tir rapide se produit lorsque le matériau injecté ne remplit pas la cavité du moule, ce qui entraîne une pièce incomplète. Une sélection appropriée des matériaux, une température de fusion et une viscosité adéquates et le maintien d'une pression et d'un temps d'injection appropriés sont essentiels pour éviter les photos courtes. De plus, la vérification de la conception du moule pour une taille suffisante du canal et de la porte et une ventilation appropriée peuvent aider à prévenir les tirs rapides.
- Lignes de soudure :Les lignes de soudure se produisent lorsque deux ou plusieurs fronts d'écoulement de matière fondue se rencontrent et se solidifient, ce qui entraîne une ligne ou une marque visible sur la surface de la pièce. Une bonne conception de la porte et des canaux, une température de fusion optimale, une vitesse d'injection et un réglage du flux de matière et de la géométrie de la pièce peuvent minimiser les lignes de soudure. L'analyse du flux de moulage et l'optimisation du placement de la porte peuvent également aider à prévenir ou à atténuer les lignes de soudure.
- Des marques de brûlure:Les marques de brûlure sont des décolorations ou des taches noires sur la surface de la pièce moulée causées par une chaleur excessive ou une surchauffe du matériau. Éviter les températures de fusion extrêmes, utiliser des canaux de refroidissement appropriés et optimiser le temps de cycle peut aider à prévenir les marques de brûlure. Une ventilation adéquate, une conception de porte appropriée et le contrôle de la température du moule contribuent également à minimiser les marques de brûlure.
Opérations post-moulage : finition et assemblage
Après le moulage par injection, de nombreuses pièces moulées peuvent nécessiter des opérations de finition et d'assemblage supplémentaires pour obtenir le produit final souhaité. Ces opérations de post-moulage peuvent comprendre :
- Garniture:Enlevez tout excès de matériau ou bavure autour de la pièce moulée à l'aide d'outils de rognage ou de coupe.
- Traitement de surface:Améliorer l'apparence ou la fonctionnalité de la surface de la pièce à l'aide de diverses techniques telles que la peinture, le revêtement ou la texturation.
- Assemblée:Assemblage de plusieurs pièces moulées ou ajout de composants tels que des fixations, des inserts ou des étiquettes pour compléter le produit final.
- Test:Vérification de la qualité et de la fonctionnalité des pièces grâce à diverses méthodes de test telles que l'analyse dimensionnelle, les tests de propriétés des matériaux ou les tests de performance.
- Emballage et expédition:Emballage et étiquetage appropriés du produit fini pour l'expédition aux clients ou aux utilisateurs finaux.
La sélection des opérations de post-moulage dépend de l'application spécifique et des caractéristiques souhaitées du produit final. Une étroite collaboration entre les experts en moulage par injection, les spécialistes de la finition et de l'assemblage et le client est cruciale pour obtenir la qualité et la fonctionnalité absolues souhaitées du produit. Une bonne planification et l'intégration des opérations de post-moulage dans le processus de fabrication peuvent aider à assurer une production efficace et une livraison rapide de produits de haute qualité.
Moulage par injection vs autres procédés de fabrication de plastique
Chaque procédé de fabrication de plastique présente des avantages et des limites, ce qui les rend adaptés à différentes applications.
- Moulage par injection: Le moulage par injection est un procédé de fabrication très polyvalent et largement utilisé pour produire des pièces en plastique. Il offre des avantages tels qu'une efficacité de production élevée, une reproduction précise des pièces et la possibilité de créer des géométries complexes. Le moulage par injection convient aux cycles de production à grand volume et permet d'utiliser une large gamme de matériaux thermoplastiques. Il offre une précision dimensionnelle et une finition de surface excellentes, ce qui le rend idéal pour diverses industries telles que l'automobile, les biens de consommation et les dispositifs médicaux.
- Soufflage: Le moulage par soufflage est un processus utilisé principalement pour produire des pièces en plastique creuses, telles que des bouteilles, des conteneurs et des composants automobiles. Il s'agit de faire fondre du plastique et de le gonfler dans une cavité de moule, créant ainsi la forme souhaitée. Le moulage par soufflage convient à la production à grand volume et peut produire de grandes pièces légères avec une épaisseur de paroi uniforme. Cependant, il est limité en termes de complexité des pièces et de sélection des matériaux par rapport au moulage par injection.
- Thermoformage :Le thermoformage est un procédé utilisé pour produire des pièces en plastique en chauffant une feuille thermoplastique et en la façonnant à l'aide de moules ou de formage sous vide. Il trouve une utilisation courante dans les emballages, les produits jetables et les produits à grande échelle tels que les plateaux et les couvercles. Le thermoformage offre une production rentable pour les grandes pièces et permet un prototypage rapide. Cependant, il présente des limites concernant la complexité des pièces, la sélection des matériaux et la précision dimensionnelle par rapport au moulage par injection.
- Extrusion:L'extrusion est un processus continu pour produire des profilés, des feuilles, des tubes et des films en plastique. Il s'agit de faire fondre de la résine plastique et de la forcer à travers une matrice pour créer la forme souhaitée. L'extrusion convient à la production de grandes longueurs continues de produits en plastique avec une section transversale constante. Bien que l'extrusion offre des taux de production et une rentabilité élevés, elle est limitée en termes de géométries de pièces complexes et de contrôle dimensionnel précis par rapport au moulage par injection.
- Moulage par compression:Le moulage par compression consiste à placer une quantité prémesurée de matériau thermodurcissable dans une cavité de moule chauffée et à la comprimer sous haute pression jusqu'à ce qu'elle durcisse. Il trouve une utilisation courante dans la production de pièces à haute résistance et stabilité dimensionnelle, telles que les composants automobiles et l'isolation électrique. Le moulage par compression offre une bonne cohérence des pièces, une efficacité de production élevée et la possibilité d'utiliser une large gamme de matériaux. Cependant, il est limité en termes de complexité des pièces et de temps de cycle par rapport au moulage par injection.
Applications du moulage par injection thermoplastique
Diverses industries utilisent largement le moulage par injection thermoplastique en raison de sa polyvalence, de son efficacité et de sa rentabilité. Certaines des applications du moulage par injection thermoplastique comprennent :
- Industrie automobile: L'industrie automobile utilise largement le moulage par injection thermoplastique pour fabriquer divers composants, notamment les garnitures intérieures et extérieures, les tableaux de bord, les panneaux de porte, les pare-chocs et les connecteurs électriques. Le processus permet une reproduction précise des pièces, des géométries complexes et des matériaux légers, améliorant ainsi l'efficacité énergétique et la flexibilité de conception.
- Biens de consommation:Le moulage par injection trouve de nombreuses applications dans la production de biens de consommation tels que les appareils électroménagers, les appareils électroniques, les emballages et les jouets. Le processus permet la production en série de produits durables et de haute qualité avec des dimensions et une finition de surface constantes. Il permet également des options de personnalisation et des itérations rapides de produits.
- Équipement médical:Le moulage par injection joue un rôle crucial dans l'industrie médicale pour produire une large gamme de dispositifs, notamment des seringues, des instruments chirurgicaux, des composants implantables et des systèmes d'administration de médicaments. Le processus garantit la production de pièces stériles, précises et biocompatibles qui répondent aux exigences réglementaires strictes du secteur de la santé.
- Industrie électronique et électrique :L'industrie électronique utilise le moulage par injection pour fabriquer des connecteurs électriques, des boîtiers, des commutateurs et d'autres composants. Le processus offre une précision dimensionnelle élevée, une excellente finition de surface et la possibilité d'incorporer des fonctionnalités telles que le moulage par insertion et le surmoulage, permettant une production efficace d'assemblages électroniques complexes.
- Industrie de l'emballage:Diverses industries, y compris l'alimentation et les boissons, les produits pharmaceutiques et les soins personnels, utilisent couramment le moulage par injection pour produire des contenants d'emballage en plastique, des bouchons, des fermetures et des bouteilles. Le processus permet la création de solutions d'emballage légères, durables et esthétiques avec des cycles de fabrication efficaces.
- Industrie aérospaciale:Le secteur aérospatial utilise le moulage par injection pour fabriquer des composants légers et performants tels que des conduits d'air, des supports, des panneaux intérieurs et des pièces structurelles. Le processus permet d'utiliser des matériaux avancés et des géométries de pièces complexes, contribuant à la réduction de poids et à l'amélioration de l'efficacité énergétique.
Impact environnemental du moulage par injection thermoplastique
Le moulage par injection thermoplastique est un procédé de fabrication populaire en raison de ses nombreux avantages, mais il est également essentiel de tenir compte de son impact environnemental. Voici quelques points à considérer :
- Efficacité matérielle :Le moulage par injection thermoplastique favorise l'efficacité des matériaux en minimisant les déchets. Le processus utilise un contrôle précis de la quantité de matériau injecté dans le moule, réduisant ainsi le besoin de matériau en excès. Les fabricants peuvent également utiliser des techniques de réaffûtage et de recyclage pour réutiliser les rebuts ou les pièces rejetées, réduisant ainsi davantage les déchets de matériaux.
- Consommation d'énergie:Les fabricants conçoivent des machines de moulage par injection économes en énergie, avec des modèles modernes intégrant des technologies avancées telles que des servomoteurs et des variateurs de vitesse. Ces caractéristiques optimisent la consommation d'énergie en réduisant la consommation d'énergie pendant le moulage, ce qui se traduit par des besoins énergétiques inférieurs et un impact environnemental réduit.
- La gestion des déchets:Tout en minimisant les déchets de matériaux, les fabricants doivent mettre en œuvre des pratiques de gestion des déchets appropriées pour gérer les restes de matériaux, de carottes ou de glissières. Les fabricants peuvent mettre en place des programmes de recyclage pour collecter et réutiliser les déchets plastiques générés lors du moulage par injection, réduisant ainsi les déchets envoyés aux décharges.
- Réduction des émissions : Le moulage par injection thermoplastique génère généralement moins d'émissions que les autres procédés de fabrication. Les fabricants peuvent réduire les émissions en utilisant des matériaux respectueux de l'environnement, en mettant en œuvre des équipements économes en énergie et en utilisant des systèmes d'échappement et de filtration avancés pour capturer toutes les émissions libérées.
- Choix de matériaux durables :Le choix des matériaux thermoplastiques peut avoir un impact significatif sur la durabilité environnementale du moulage par injection. Opter pour des plastiques biodégradables ou biosourcés, ainsi que des matériaux recyclés ou recyclables, peut contribuer à réduire l'empreinte écologique globale du processus.
Considérations sur le cycle de vie : La prise en compte de l'ensemble du cycle de vie du produit moulé est essentielle pour évaluer son impact sur l'environnement. Lors des étapes de conception et de sélection des matériaux, les fabricants doivent tenir compte de facteurs tels que la durabilité de la pièce, sa recyclabilité et le potentiel d'élimination ou de réutilisation en fin de vie.
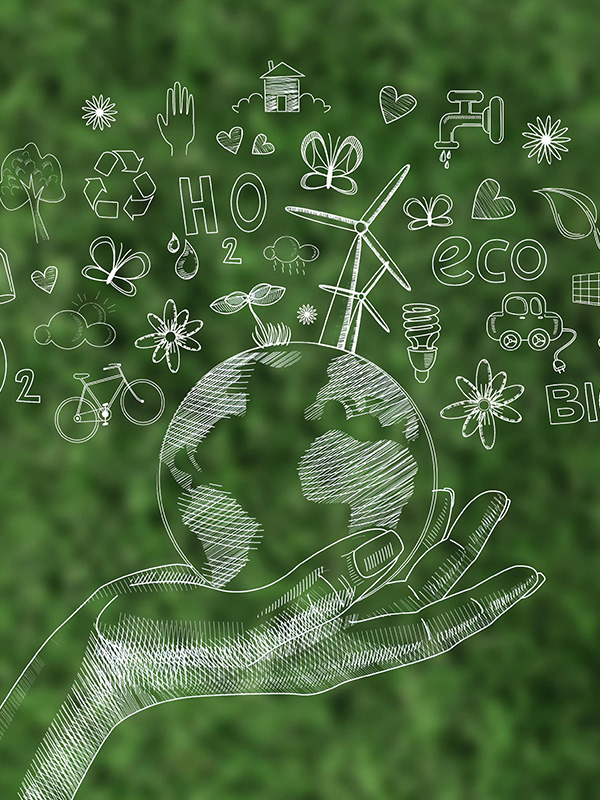
L'avenir du moulage par injection thermoplastique
L'avenir du moulage par injection thermoplastique semble prometteur, avec des progrès technologiques continus et une demande accrue de pièces de précision de haute qualité dans diverses industries. Parmi les principaux développements attendus dans les années à venir, citons :
- Utilisation accrue de l'automatisation et de la robotique pour améliorer l'efficacité et réduire les coûts.
- Les efforts se concentrent sur le développement de nouveaux matériaux et procédés pour améliorer les performances des pièces et permettre de nouvelles applications.
- Il s'agit d'une adoption croissante de pratiques durables, telles que l'utilisation de matériaux recyclés et l'optimisation de la consommation d'énergie, pour réduire l'impact environnemental du moulage par injection.
- Une plus grande intégration des technologies numériques, telles que l'impression 3D et les logiciels de simulation, pour améliorer les processus de conception et de production.
Le marché mondial du moulage par injection est en expansion, en particulier dans les économies émergentes, stimulé par la demande croissante de produits en plastique dans diverses industries.
Choisir le bon partenaire de moulage par injection
Choisir le bon partenaire de moulage par injection est crucial pour la réussite de votre projet. Prenez le temps d'évaluer plusieurs options, d'effectuer des visites sur place et d'engager des discussions approfondies pour assurer un partenariat compatible et durable.
- Expertise et expérience:Recherchez un partenaire de moulage par injection possédant une connaissance et une expérience approfondies de l'industrie. Ils doivent avoir fait leurs preuves dans la fourniture de produits et de solutions de haute qualité à des clients de divers secteurs. Tenez compte de leur compréhension des différents matériaux, conceptions de moules et processus de fabrication.
- Capacités de fabrication : Évaluer les capacités de fabrication du partenaire de moulage par injection. Assurez-vous qu'ils disposent d'installations bien équipées avec des machines et des technologies modernes pour gérer les exigences de votre projet. Tenez compte de leur capacité de production, de leur capacité à gérer différentes tailles et complexités de pièces et de leur capacité à respecter les volumes et les délais de production souhaités.
- Assurance Qualité:La qualité est primordiale dans le moulage par injection. Évaluer les systèmes de contrôle de la qualité et les certifications du partenaire potentiel. Recherchez des partenaires qui respectent des normes de qualité strictes, disposent de processus d'inspection robustes et effectuent des tests complets pour garantir la qualité et la cohérence des pièces.
- Assistance à la conception et à l'ingénierie :Un partenaire de moulage par injection fiable doit offrir une assistance en matière de conception et d'ingénierie pour optimiser la conception de votre pièce pour la fabricabilité. Ils doivent avoir des ingénieurs qualifiés qui peuvent fournir des informations précieuses sur la sélection des matériaux, la conception des moules et l'optimisation des processus pour améliorer la qualité et l'efficacité des pièces.
- Compétitivité des coûts :Bien que le coût ne doive pas être le seul facteur déterminant, il est essentiel d'évaluer la compétitivité des prix et des coûts du partenaire de moulage par injection. Demandez des devis détaillés et tenez compte des coûts d'outillage, des coûts des matériaux, des coûts de main-d'œuvre et de tout service supplémentaire qu'ils fournissent.
- Communication et collaboration :Une communication et une collaboration efficaces sont essentielles pour un partenariat réussi. Assurez-vous que le partenaire de moulage par injection dispose de bons canaux de communication, répond à vos demandes et peut fournir des mises à jour régulières sur le projet. Une approche collaborative nous aidera à répondre à vos exigences et à relever rapidement tous les défis.
- Références et avis clients :Recherchez des références de clients ou lisez des critiques/témoignages pour avoir un aperçu des expériences d'autres clients avec le partenaire de moulage par injection. L'obtention de ces informations peut aider à déterminer leur fiabilité, leur rapidité et le niveau général de satisfaction des clients.
Conclusion
Le moulage par injection thermoplastique est une méthode polyvalente et économique pour fabriquer des pièces en plastique en grandes quantités. Sa capacité à produire des formes complexes avec une précision et une cohérence élevées est devenue un choix populaire pour diverses industries, notamment l'automobile, le médical, l'électronique et les biens de consommation. En comprenant les différents aspects du moulage par injection thermoplastique, y compris ses avantages, ses inconvénients et ses considérations de conception, vous pouvez prendre des décisions éclairées sur le choix du bon partenaire de moulage par injection pour les besoins de votre entreprise.