소량 맞춤형 플라스틱 사출 성형: 정밀 부품 제조에 대한 포괄적인 가이드
소량 맞춤형 플라스틱 사출 성형: 정밀 부품 제조에 대한 포괄적인 가이드
자세히 알아보기 맞춤형 플라스틱 사출 성형, 정밀 부품을 만드는 다목적 제조 공정. 프로세스와 관련된 이점, 응용 프로그램 및 주요 고려 사항에 대해 알아보십시오.
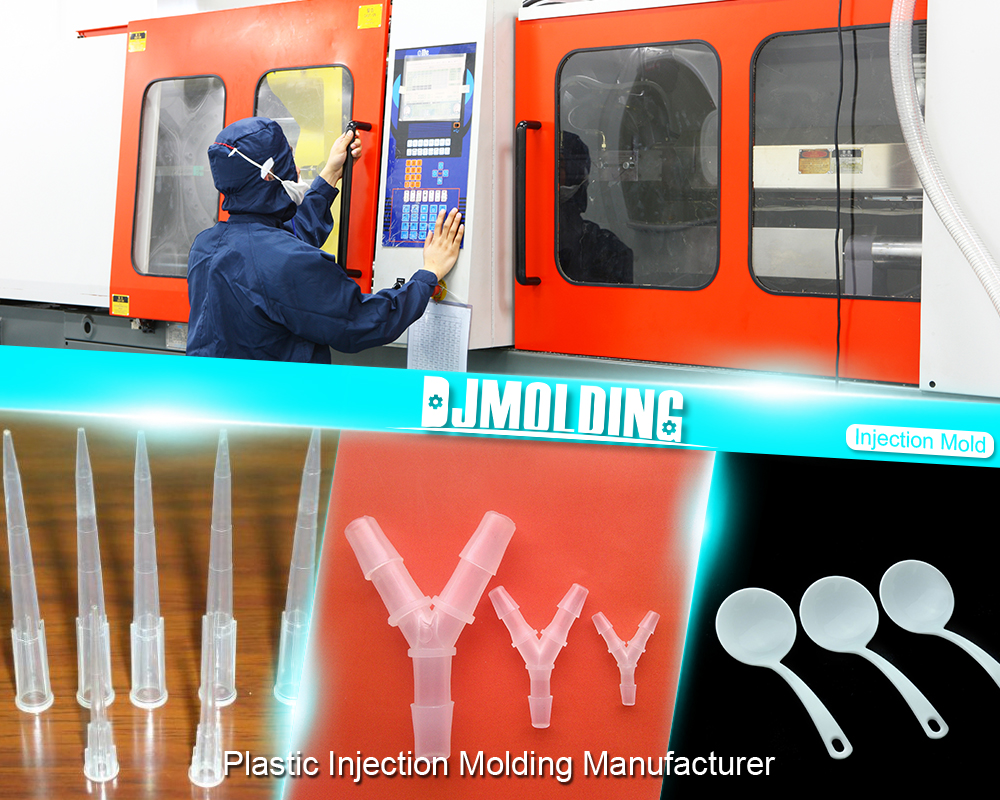
개요
맞춤형 플라스틱 사출 성형은 수많은 산업에서 중요한 매우 효율적이고 널리 채택된 제조 공정입니다. 제조업체는 용융 플라스틱을 맞춤 설계된 금형에 주입하여 정밀하고 일관성 있는 고품질의 복잡한 부품을 생산할 수 있습니다. 이 포괄적인 가이드는 성공적인 구현에 영향을 미치는 정의, 장점, 적용 및 요인을 탐구하면서 맞춤형 플라스틱 사출 성형의 세계를 탐구합니다.
맞춤형 플라스틱 사출 성형 이해
정의 및 프로세스 개요
맞춤형 플라스틱 사출 성형에는 용융 플라스틱을 금형 캐비티에 주입하여 플라스틱 부품을 생산하는 작업이 포함됩니다. 녹은 플라스틱은 금형 내에서 응고되어 원하는 모양을 형성합니다. 이 프로세스에는 일반적으로 금형 설계, 재료 선택, 사출 성형기 작동, 냉각 및 후처리를 포함한 몇 가지 주요 단계가 포함됩니다.
맞춤형 플라스틱 사출 성형의 장점
- 비용 효율성 및 높은 생산 속도: 사출 성형은 재료 낭비를 최소화하면서 부품을 대량 생산할 수 있어 대규모 제조를 위한 비용 효율적인 옵션입니다.
- 설계 유연성 및 복잡한 형상: 이 프로세스를 통해 복잡한 디자인, 복잡한 모양 및 여러 구성 요소를 단일 부품으로 통합할 수 있습니다.
- 재료 옵션 및 성능 특성: 맞춤형 플라스틱 사출 성형은 특정 응용 분야에 적합한 고유한 특성을 지닌 다양한 열가소성 재료를 지원합니다.
맞춤형 플라스틱 사출 성형의 일반적인 응용
맞춤형 플라스틱 사출 성형은 자동차, 전자, 의료 기기, 소비재 등 다양한 산업에서 광범위하게 사용됩니다. 하우징, 인클로저, 기어, 버튼 및 공차가 엄격한 복잡한 부품과 같은 구성 요소를 제조하는 데 사용됩니다.
사출 성형 공정의 필수 구성 요소 및 단계
금형 설계 및 개발
- 형 유형: XNUMX판 금형, XNUMX판 금형 및 핫 러너 금형과 같은 다양한 금형 종류는 부품 및 생산량의 요구 사항에 따라 뚜렷한 이점을 제공합니다.
- 금형 재료 및 구성에 대한 고려 사항: 금형 수명, 비용, 내열성 및 내구성과 같은 요소는 금형 재료 선택에 영향을 미칩니다.
재료 선택 및 준비
적절한 열가소성 수지 재료를 선택하는 것은 원하는 부품 특성, 내구성 및 성능을 달성하는 데 매우 중요합니다. 기계적 특성, 내화학성 및 환경 고려 사항은 재료 선택에 영향을 미칩니다. 재료 준비에는 건조, 혼합 및 때로는 첨가제 추가가 포함됩니다.
사출 성형기 작동
- 클램핑 및 사출 장치: 클램핑 장치는 금형을 제자리에 고정하고 사출 장치는 플라스틱을 녹여 금형에 주입합니다.
- 온도 및 압력 제어: 정밀한 온도 및 압력 매개변수 제어는 최적의 금형 충진 및 부품 품질을 보장합니다.
냉각 및 배출
플라스틱을 주입한 후 냉각하여 굳히고 금형을 성형합니다. 결함을 방지하고 치수 정확도를 달성하려면 적절한 냉각이 필수적입니다. 냉각된 부품은 이젝터 핀 또는 기타 메커니즘을 사용하여 금형에서 이젝트됩니다.
후처리 및 마무리
최종적으로 원하는 부품 사양을 달성하려면 잉여 재료 트리밍, 표면 처리 및 조립과 같은 후처리 활동이 필요할 수 있습니다.
성공적인 맞춤형 플라스틱 사출 성형에 영향을 미치는 요인
설계시 고려 사항
- 부품 복잡성 및 형상: 복잡한 부품 설계에는 적절한 충진 및 부품 배출을 보장하기 위해 금형 설계 및 재료 흐름을 신중하게 고려해야 합니다.
- 기울기 각도 및 벽 두께: 적절한 드래프트 각도와 균일한 벽 두께는 몰드 이형과 싱크 마크 및 뒤틀림과 같은 결함을 방지하는 데 매우 중요합니다.
재료 선택 및 특성
적합한 열가소성 수지 재료를 선택하려면 강도, 강성, 유연성, 내화학성, 내열성 및 원하는 표면 마감과 같은 요소를 고려해야 합니다. 부품의 특정 요구 사항과 해당 용도를 이해하면 정보에 입각한 재료를 선택하는 데 도움이 됩니다.
툴링 및 금형 설계
금형의 설계 및 구성은 맞춤형 플라스틱 사출 성형의 성공에 중요한 역할을 합니다. 엔지니어는 금형 설계 중에 부품 복잡성, 언더컷, 게이트 위치, 환기 및 냉각 채널과 같은 요소를 고려해야 합니다. 일관된 생산을 보장하고 가동 중지 시간을 최소화하려면 적절한 툴링 유지 관리 및 정기 검사가 필수적입니다.
품질 관리 및 검사
강력한 품질 관리 조치를 구현하는 것은 고품질 부품을 생산하는 데 필수적입니다. 사출 성형 공정의 다양한 단계에서 검사 및 테스트를 수행하면 모든 문제를 신속하게 식별하고 해결하는 데 도움이 됩니다. 치수 검사, 육안 검사 및 재료 테스트는 맞춤형 플라스틱 사출 성형에 사용되는 표준 품질 관리 관행입니다.
맞춤형 플라스틱 사출 성형의 장점과 한계
장점
비용 효율성 및 높은 생산 속도
사출 성형은 단기간에 많은 부품을 생산할 수 있어 단위당 비용이 절감됩니다. 프로세스의 높은 반복성과 효율성은 비용 절감에 기여합니다.
설계 유연성 및 복잡한 형상
맞춤형 플라스틱 사출 성형 얇은 벽, 내부 기능 및 다양한 두께를 포함하여 복잡하고 복잡한 부품 설계가 가능합니다. 이 프로세스는 다른 제조 방법으로는 어렵거나 불가능한 언더컷, 나사산 및 복잡한 모양이 있는 부품 생성을 수용합니다.
재료 옵션 및 성능 특성
사출 성형은 범용 플라스틱, 엔지니어링 플라스틱 및 고성능 폴리머를 비롯한 다양한 열가소성 수지 재료를 지원합니다. 이러한 다양성을 통해 제조업체는 특정 기계적, 열적, 전기적 또는 화학적 특성을 가진 재료를 선택하여 의도한 응용 분야의 요구 사항을 충족할 수 있습니다.
제한 사항
초기 툴링 비용
몰드의 설계 및 구성에는 상당한 초기 비용이 포함될 수 있으며 복잡한 부품이나 여러 개의 캐비티가 필요한 경우 툴링 비용이 더 높을 수 있습니다. 그러나 생산량이 증가함에 따라 부품당 비용은 크게 감소합니다.
설계 제약 및 제한 사항
사출 성형에는 드래프트 각도, 균일한 벽 두께, 양호한 게이트 및 이젝터 핀 위치를 포함하여 설계 제한이 있습니다. 부품 설계 단계에서 설계자는 성공적인 몰딩을 보장하고 부품 품질을 유지하기 위해 이러한 제약 조건을 고려해야 합니다.
시간 및 생산량 고려 사항
금형 설계, 툴링 및 재료 준비를 포함한 사출 성형 프로세스 설정에는 시간이 걸립니다. 맞춤형 플라스틱 사출 성형은 중대형 생산량에 가장 비용 효율적입니다. 3D 인쇄 또는 기계 가공과 같은 대체 방법이 소량 생산에 더 적합할 수 있습니다.
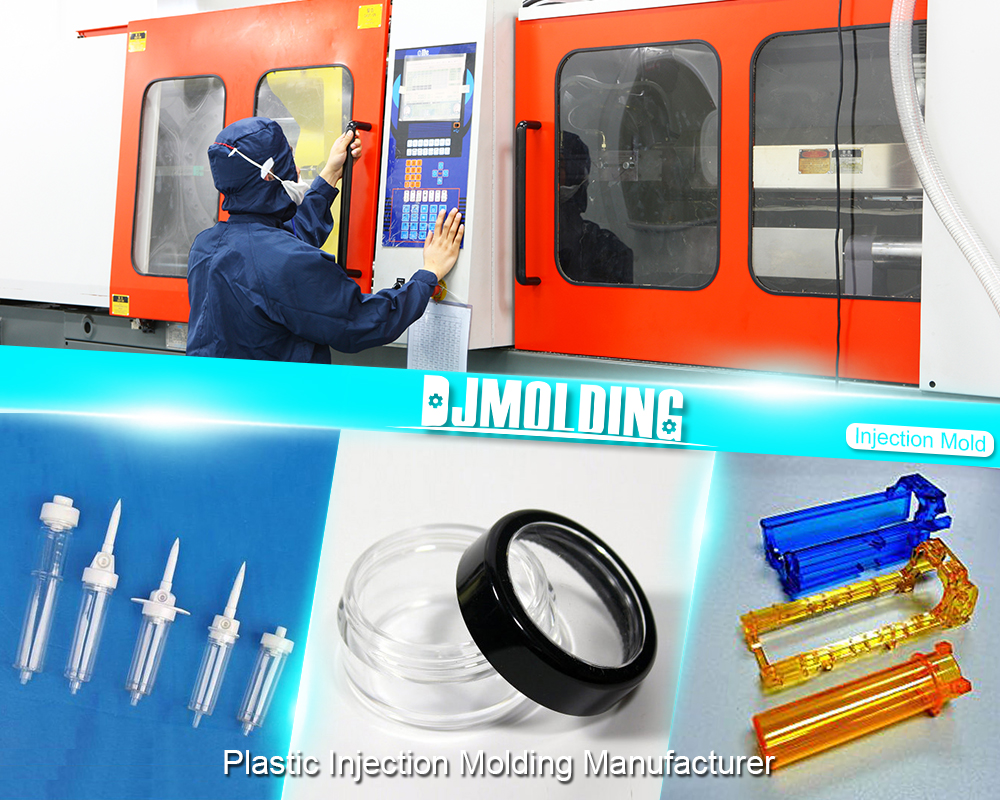
결론
맞춤형 플라스틱 사출 성형은 고품질의 정밀 부품을 생산하기 위해 다양한 산업 분야에서 사용되는 다재다능하고 효율적인 제조 공정입니다. 이 포괄적인 가이드는 맞춤형 플라스틱 사출 성형의 정의, 이점 및 일반적인 응용 분야를 탐구했습니다. 또한 사출 성형 프로세스와 관련된 주요 구성 요소 및 단계, 성공적인 구현에 영향을 미치는 요소, 프로세스의 이점과 제한 사항에 대해서도 논의했습니다. 맞춤형 플라스틱 사출 성형의 기능과 고려 사항을 이해하면 제조업체는 정보에 입각한 결정을 내리고 특정 제조 요구 사항에 대한 잠재력을 활용할 수 있습니다.
추가 정보 소량 맞춤형 플라스틱 사출 성형, Djmolding을 방문할 수 있습니다. https://www.djmolding.com/ 자세한 정보입니다.