Case in France
The Benefits of Custom Plastic Components in the French Auto Industry
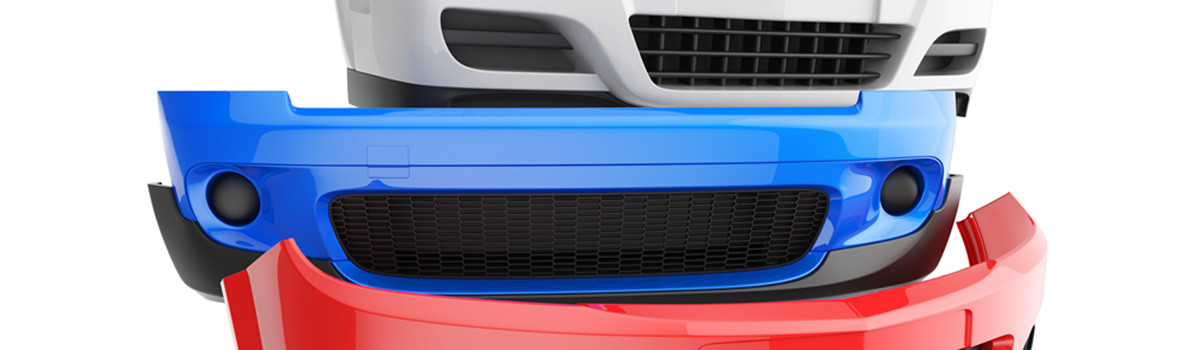
Sustainability is a growing concern among consumers and manufacturers in the auto industry. In the past, plastic components were not a great option due to the difficulty in recycling them and problems with durability. Vehicles like electric cars make good use of newer polyethylene applications. Some French auto manufacturers customize the plastic components form DJmolding, and we do have a good and long corperationship.
Custom plastic components made through plastic injection molding are light and can be recycled. They can also improve a vehicle’s lifespan and fuel efficiency. For the auto industry, part of its growth in recent years can be attributed to injection molding suppliers.
These are just a few of the benefits that the French auto industry can expect from custom plastic components.
Speeds up the Design Process
First of all, plastic components can get your design to market faster. They do so through the creation of prototypes.
Functional prototypes allow developers to see what works with a component and whether or not the final product will meet their expectations. If there are any design elements that need tweaking, they can always make the necessary changes and create another prototype.
More importantly, prototypes allow you to save money and reduce risk to your company. They’re inexpensive, and you can find any errors or problem areas before you go into mass production. This pairs well with the shorter timeframe that the auto industry is known for.
Reduced Costs
Custom plastic components can save you money in more areas than just prototyping. The process of creating these components is more energy-efficient and cost-effective than alternative materials. This is partly due to how light plastic is and how affordable they are to produce.
In addition, plastic can be used in a surprising amount of areas on a car. Bumpers, wheel trims, and body panels can all be constructed out of plastic.
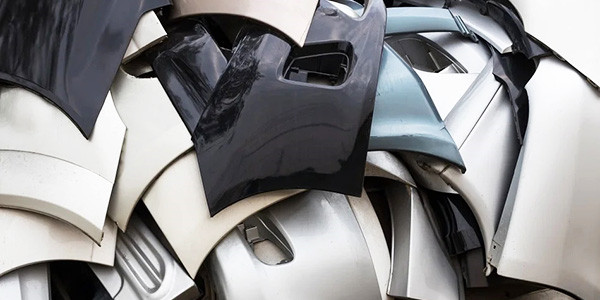
Keep in mind that the cost of your plastic injection molding will depend on various factors such as the item’s complexity, tooling costs, and the mold’s classification.
More Flexibility
Plastic components these days are much better than the ones made years ago. While there are some benefits to metal parts, plastic components have their own unique qualities.
They’re more durable, can handle higher temperatures, and resist corrosion. Plastic’s light weight also makes vehicles more fuel-efficient.
On top of that, custom components are better for meeting specific design requirements for different vehicles. Manufacturers can produce precise parts in all kinds of shapes and sizes, using whatever types of thermoplastics fit the job.
For example, polycarbonate is impact-resistant and works for car bumpers. Polyvinyl chloride is a flame retardant and is often used for the body of the car.
Try Out Custom Plastic Components
If you aren’t already using custom plastic components, then it’s time to step up your game. With plastic injection molding, you can save money, speed up production, and get ahead of the competition.
DJmolding is here to help you with your next project. As world-class producer of plastic molded components, we’ll work closely with you throughout the entire process. Contact us to request a quote or if you have any questions.