Case in Korea
Plastic Injection Parts’ Wall Thickness Structural Design for Korean Auto Companies
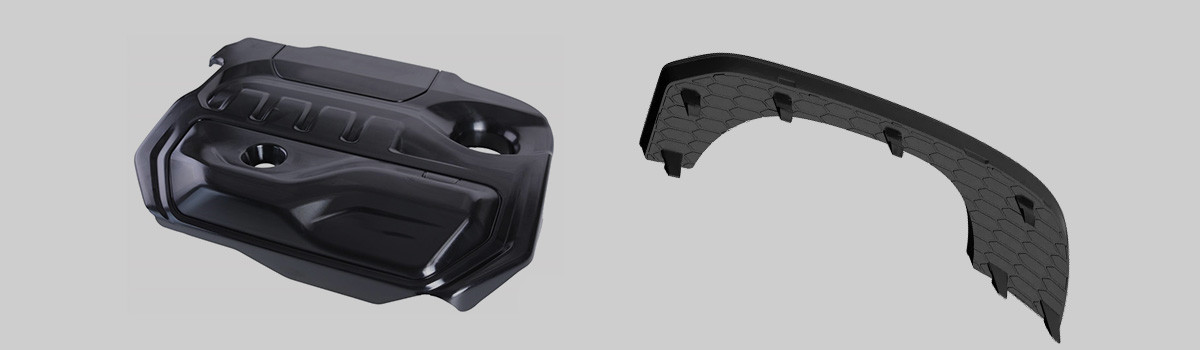
The plastic parts are very import for a car, and it’s structural strong will be effect on the lifetime and drive safe, so the Korean Auto manufacturers purchase plastic parts very strict. The Auto industry will use a lot of plastic parts in a car, the Korea local injection companies can’t offer the large supply, and these Auto manufacturers will purchase plastic parts oversea, just like DJmolding from China.
The plastic parts are so important for a car, so how to design the plastic injection parts’ wall thickness structural for the Korean Auto companies? Now, DJmolding will show you the design of plastic injection parts’ thickness structural.
Definition of wall thickness
Wall thickness is a basic structural characteristic of plastic parts. If the outer surface of plastic parts is called the outer wall, the inner surface is called the inner wall, then there is a thickness value between outer and inner walls. The value is called the wall thickness. The value entered when the shell is extracted on the software during structural design can also be said to be the wall thickness.
Function of wall thickness
For the outer wall of products
The outer wall of parts is like the outer skin of parts. The inner wall is the structural skeletons of parts. Different appearance effects can be achieved by surface treatment of outer wall of parts. The inner wall just connects the structures (ribs, screw bars, buckle etc.) together and enables a certain strength to the parts. In the meantime, other structures may be filled out during the infection molding process. There is no specific requirements for the inner and outer walls (cooling, assembly). Normally, it is made into a whole so that parts can have sufficient strength to protect the inner parts from damaging or interfering by the environment.
For the internal parts of the product
As a bearing or connecting bracket, there is no strict requirements for the inner and outer walls, which can establish other structures (ribs, screw bars, buckles etc) at the outer wall according to the actual conditions. However, for the sake of convenient manufacturing (mainly refers to when the front and rear molds are separated, in order to keep the plastic parts in the rear mold, the front face of mold, which the outer wall should be designed as simple as possible. If not, adjusting the drafting angle of front and rear molds, even have a thimble in the front mold or a certain small undercut in the rear mold), and generally design other structures on the inner wall.
No matter it is shell parts or internal parts, the wall thickness is essential as the receiving surface of the ejector pin of the mold, enabling the parts to be ejected smoothly.
Design principles of wall thickness:
In designing of the plastic parts, wall thickness is the priority, which is essential as the foundation of a building. The other structures need to be build up on it. In the meantime, it also impacts the mechanical properties, formability, appearance, cost of plastic parts. Thus, wall thickness should be based on the above factors to design.
It mentioned that wall thickness needs to be a specific value. If there is a value, it refers to the even wall thickness. If there are many values, it refers to the uneven wall-thickness. The difference between even or uneven will be introduced after. Now, we will talk about the The principle of wall thickness design should be followed.
1. Based on the principle of mechanical properties:
It mentioned that no matter it is shell parts or internal parts, both need a certain level of strength. Apart from other factors, the resist release force is required when considering the formation of parts. It is easily to be deformed if the part is too thin. Generally speaking, the thicker the wall thickness, the higher the parts strength (wall thickness increase for 10%, the strength will increase by about 33%). If the wall thickness exceeds a certain range, adding up to the wall thickness will lower the strength of parts due to the shrinkage and porosity. The increase of wall thickness will lower the strength of parts and increase the weight, extends the injection molding circle, cost, etc. obviously, increasing the strength of parts by merely increasing the wall thickness is not the optimal program. It is best to utilize the geometric features to increase the stiffness, such as ribs, curves, corrugated surfaces, stiffeners, etc.
It is not ruled out that due to the limitations of space and other factors, the strength of some parts is mainly realized by the wall thickness. So, it is recommended to determine an appropriate wall thickness by imitating the mechanical simulation if strength is an important factor. Indeed, the value for wall thickness should also be complied with the following formality principles.
2. Based on the principle of formability:
The actual wall thickness is the thickness of mold cavity between front and rear molds. When the molten resin fills out the mold cavity and cooled, the wall thickness is obtained.
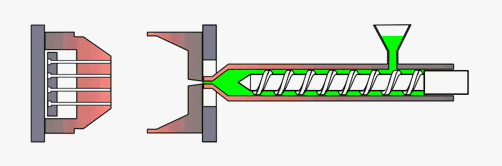
1) How does the molten resin flow during the injection and filling process?
The flow of plastic inside the cavity can be regarded as laminar flow. According to the fluid mechanics theory, the laminar fluid can be regarded as the layers of liquid next to each other slipping under the action of shearing force.
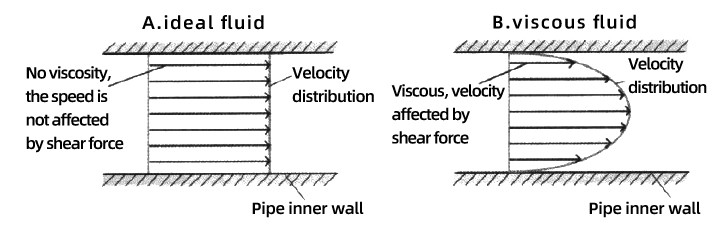
During the injection molding process, the molten resin contacts with the wall of runners (wall of mold cavity), making the stream layers adhere to the wall of runners (or wall of mold cavity) cooled firstly. The speed is zero, and there is friction resistance produced with its adjacent liquid layer. Pass on like this, the speed of the mid-stream layer is the highest. The flow form in which the laminar velocity decreases near the runner wall (or mold cavity wall) on both sides.
The middle layer is the fluid layer, and the skin layer is the solidified layer. As the cooling time goes by, the layer of curse will increase. The cross section area of fluid layer will be smaller gradually. The harder the filling, the larger the injection force. Indeed, it is more difficult to push the melt into the mold cavity to fulfill the injection.
Therefore, the size of the wall thickness has a great influence on the flow and filling of the injection molded parts during the injection molding process, and its value cannot be too small.
2) The viscosity of the plastic melt also has a great influence on the fluidity
When the melt is under the external action, and there is relative motion between the layers, there will be internal friction force generated to interfere the relative movement between the fluid layers. The inner friction force produced by the fluid is called viscosity. Evaluating the viscosity strength with the dynamic viscosity (or viscosity coefficient). Numerically the ratio of shear stress to shear rate of the melt.
The viscosity of melts reflects the characteristics of the ease with which the plastic melt flows. It is a measure of melt flow resistance. The higher the viscosity, the larger the fluid resistance, the more difficult the flow. The influential factors of melt viscosity affects not only is associated with the molecular structure, but also related to the temperature, pressure, shear rate, additives, etc. (after deciding the types of plastic materials, the temperature, pressure, shearing rate, additives and other factors during the injection molding process may be altered to change the fluidity of plastic in the injection molding process. In the future, we will write an article on the topic of liquidity depending on the situation.)
While, in the actual application, melt Index indicates to the fluidity of plastic materials in processing. The higher the value, the better the fluidity of material. On the contrary, the fluidity of material will be worse.
Therefore, plastic with good fluidity is easier to fill the mold cavity, especially for injection molding parts with complex structures.
The fluidity of commonly used plastics can be roughly divided into three categories according to the mold design requirements:
①Good fluidity: PA, PE, PS, PP, CA, poly(4) methyl pentylene;
②Medium fluidity: polystyrene series resins (such as ABS, AS), PMMA, POM, PPO;
③Poor fluidity: PC, hard PVC, PPO, PSF, PASF, fluoroplastics.
As we can see from the Fig. above, the material with the poorest fluidity, the requirements for the minimum wall thickness will be higher. This has been introduced in the laminar flow theory.
The recommended value of wall thickness above is just a conservative number. In the actual application, the sizes of the parts include small, medium and large, the above picture does not specify the reference range.
3) We can calculate by the flow length ratio
The flow length ration of plastic refers to the ratio of length (L) to wall thickness (T) of the plastic melt flow. That means for a given wall thickness, the higher the flow length ratio, the farther the plastic melt flows. Or when the length of the plastic melt flow is certain, the larger the flow length ratio, the smaller the wall thickness can be. Thus, the flow length ratio of plastic directly affects the number of feeding and distribution of plastic products. Also, it affects the wall thickness of plastic.
To be more accurate, the specific value range of the wall thickness can be obtained through the calculation of the flow length ratio. Indeed, this value is related to material temperature, mold temperature, polishing degree, etc. it is only an approximate range value, different conditions are different, it is difficult to be precise, but it can be used as a reference value.
Calculation of flow length ratio:
L/T (total) = L1/T1 (main channel) + L2/T2 (split channel) + L3/T3 (product) The calculated flow length ratio should be less than the value given in the physical property table, otherwise there may be The phenomenon of poor filling.
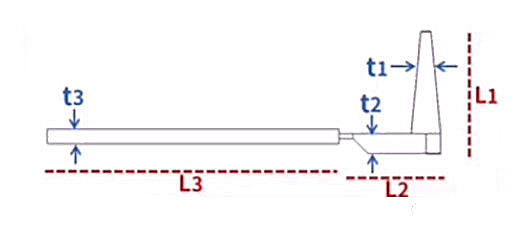
For example
A rubber shell, PC material, wall thickness is 2, the filling distance is 200, runner is 100, diameter of runners is 5.
Calculation: L/T(total)=100/5+200/2=120
The reference value for flow length ratio of PC is 90, which is obviously higher than the referent value. The injection speed and pressure need to be increased as it is difficult to inject, or even require specific high performance injection molding machines. If adopts two feeding points or changes the feeding points position, the filling distance of products can be reduced to 100, which is L/T(total)=100/5+100/2=70. The length ratio now is less than the reference value and is easy for injection molding. L/T(total)=100/5+200/3=87 when the wall thickness is changed into 3, which allows the normal injection molding.
3. Based on the appearance principle:
The specific performance of wall thickness affecting the appearance of parts is as follows:
1) Uneven wall thickness: surface shrinkage (including appearance defects such as shrinkage, pits, thick and thin prints), warping deformation, etc.
2) Excessive wall thickness: defects such as surface shrinkage and internal shrinkage holes.
3) The wall thickness is too small: defects such as lack of glue, thimble printing, warpage and deformation.
shrinkage or porosity
shrinkage or porosity normally occurs at the thick wall thickness areas. The mechanism: according to the material solidification principle, the internal porosity and surface shrinkage during injection molding process is due to the constant contraction during the cooling process. When the shrinkage is concentrated at the frozen position behind, but cannot get be made up immediately, shrinkage and porosity are more likely to occur inside.
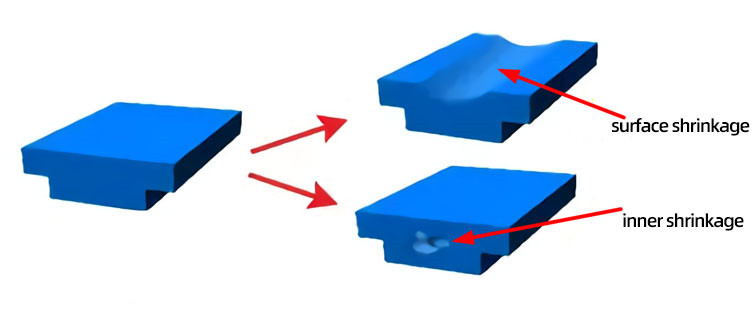
The designing principles of wall thickness above are introduce from four aspects, which are mechanical properties, formability, appearance, cost. If use one sentence to describe the design of wall thickness, that is the value of the wall thickness of the injection molded parts should be as small as possible and as uniform as possible under the condition of satisfying the mechanical properties and processing performance. If not, it should be uniformly transitioned.
DJmolding offers the plastic parts’ design and manufacturing services for the global markte, if you want to start your project, please contact us right now.