Low Volume Injection Molding — Low Volume Manufacturing Service
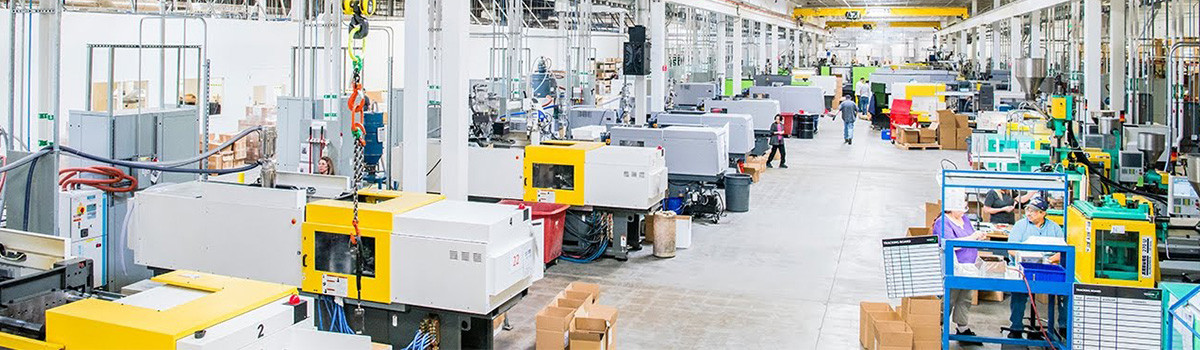
How to Leverage Low-Volume Injection Molding(Low Volume Manufacturing Service)
Use on-demand manufacturing to reduce production costs and mitigate demand volatility
Whether you’re designing a lifesaving medical device or a high-flying drone, investing $100,000 or more—often much more—in high-volume steel tooling is an inherent financial risk that comes with a move to large-scale production. Compounding the risk is months of idle time as you wait on your steel tool to be ready when you could be iterating part design or even producing products that generate revenue. There is a better way: on-demand manufacturing.
What is On-Demand Manufacturing(low volume injection molding)?
At DJmolding, our on-demand, low-volume production offering with injection molding—which uses aluminum tooling—is a fast, cost-effective way to produce hundreds of thousands of end-use molded parts.
Use this process as the primary production method for your products. On-demand manufacturing is also an excellent way to move from prototyping to low-volume production for molded parts. DJmolding is actually a full-service manufacturing provider. Low-volume runs can also help you validate part design and manage inventory overhead with production of parts only when demand dictates. In addition, even if you need to eventually shift into mass production of plastic parts, you can still use our cost-effective aluminum tooling as a bridge before committing to a capital expense with steel tooling. Finally, this on-demand approach also optimizes your supply chain, making it more adept in managing demand volatility.
Call out Critical-to-Quality Features
When you use our on-demand manufacturing option, you’ll be able to indicate in your part design the dimensions that are most critical to the part’s function. By calling out these Critical-to-Quality (CTQ) features in your 3D CAD model, you can be assured that the parts ordered are consistent with the model. In addition, that means the next time you order those parts, we can follow those precise steps to manufacture consistent, repeatable parts that adhere to your CTQ specifications.
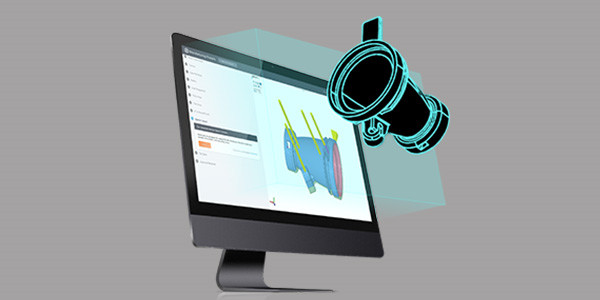
Inspections are key pieces of this CTQ process. Accordingly, our applications engineering team will review your model and email you an Inspection Statement of Work (ISOW), which lets you know if any features you circled have issues with tolerances and moldability. Once we send the ISOW, we manufacture and inspect your order.
Once we have completed molding process development, which ensures we have a consistent and repeatable process to produce quality parts, we will inspect the first three shots from the tool, using an automated Coordinate-measuring Machine (CMM), and provide you with a three-part First Article Inspection (FAI) report, and a Process Capability Report.
Gain supply chain flexibility from DJmolding low volume injection molding service
These days, as we all continue to navigate a global pandemic, supply chain considerations are critical. An on-demand manufacturing approach can help you create a more nimble supply chain by:
* Procuring parts on demand without any Minimum Order Quantity (MOQ)
* Lowering inventory costs and warehousing expenses with on-demand sourcing
* Managing increases in demand volatility without going on back-order
* Mitigating the risk of domestic and global shipping delays
* Minimizing downtime and reducing the risk of stock-outs when large-scale tools are being repaired
DJmolding’s Low-Volume Production
This is a specialized service offering full production-quality parts but in volumes usually limited to 10,000 pieces or fewer, depending on the process used. Our low-volume molding, also called short runs, are monitored and controlled so you can be assured of all aspects of mold design and build. This type of production is ideal for small and medium-sized businesses or small-batch manufacturing.
Low volume manufacturing is a fairly new field in the manufacturing industry that is all about outsourcing parts, products, and materials to third parties.
This allows your company to focus more on the production aspect while the smaller businesses handle the design and branding of the products. This growing trend will be prevalent in every industry as small businesses look to grow their business by outsourcing to other companies and keeping costs down.
DJmolding’s Small Volume Injection Molding
A lot of people hear the words “China” and “molding” in the same sentence and they assume the worst. They think of cheap, low-quality products that are made using substandard manufacturing practices that put the lives of workers at risk.
But that,s not always the case.
DJmolding from China has a long history of producing quality goods for export. In fact, some of the best-made products in the world come from China! And when it comes to plastic injection molding, China is actually one of the most sophisticated countries in the world.
Injection molding is a popular way to manufacture plastic parts and devices. DJmolding is a good manufacturer to get low volume injection molds made because the cost of labor is much less than in the United States or Europe. DJmolding has minimum order quantities (MOQs) of only 1,000 pieces and lead times as short as 3-4 weeks. This can be extremely helpful for small companies that want to get started with their own product line but don’t want to invest a lot of money in tooling and production costs up front.
So how do you know if you’re dealing with a reliable supplier? You need to look at the details
Minimum Order Quantity (MOQ) – A reputable supplier won’t ask you for a huge order before they’ve even had a chance to meet with you or see your product. Instead, we’ll want to make sure that you’re serious about your project before committing too much time or money into it.
Lead Time – The best suppliers will have fast lead times so they can deliver your product as quickly as possible (and still meet quality standards).
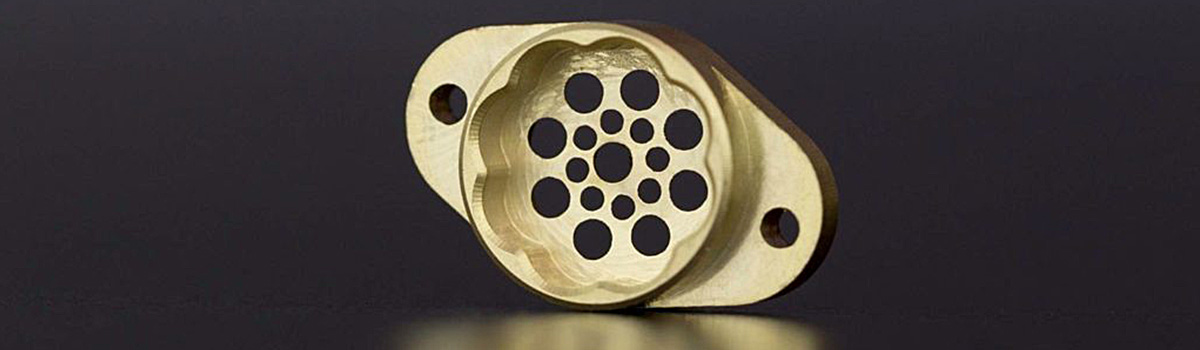
Injection molding is a popular manufacturing process for mass-producing plastic products, but what if you need a small number of parts for your project? That’s where low volume injection molding comes in. It’s a cost-effective way to produce a small batch of plastic parts without breaking the bank. In this blog post, we’ll dive into the benefits and applications of low volume injection molding, how it differs from high volume injection molding, and how it can benefit your business.
Understanding Low Volume Injection Molding
Low volume injection molding is a manufacturing process that allows for producing small quantities of plastic parts. It is an efficient and cost-effective solution for companies that require smaller production runs or have limited budgets.
- The process of low volume injection molding begins with creating a mold. Typically, manufacturers make the mold from steel or aluminum and design it to achieve the desired shape of the plastic part. During the injection molding process, manufacturers hold together the two halves of the mold: the cavity and the core.
- Before the injection molding occurs, the plastic material is heated and melted in a separate chamber. Manufacturers inject the plastic into the mold under high pressure once it reaches the desired temperature. The plastic fills the cavity and takes on the shape of the mold.
- After the plastic has cooled and solidified, manufacturers open the mold and eject the finished part. The cycle time for low volume injection molding is relatively short, allowing for faster production than other manufacturing processes.
- Low volume injection molding offers several advantages. Firstly, it will enable for production of complex and intricate parts with high precision and repeatability. Industries that require complex components, like automotive, electronics, and medical devices, would be beneficial to choose this option.
- Additionally, low volume injection molding provides cost savings compared to traditional high-volume production methods. Since the initial investment in tooling is lower, it is more accessible to smaller businesses or startups. It also enables faster time-to-market, as the lead time for tooling is shorter.
- Another benefit of low volume injection molding is its flexibility. It allows for design modifications and iterations without incurring significant additional costs. That’s why design changes expected during the early stages significantly benefit product development and prototyping.
- Despite its advantages, low volume injection molding does have some limitations. As the name suggests, it is not suitable for high-volume production. The cost per part can be higher than mass production methods due to the higher cost of tooling and setup. Therefore, it is more suitable for small to medium production runs.
- Material selection is also a consideration in low volume injection molding. Limited material options are available compared to high-volume production processes. However, many thermoplastic materials, including ABS, polycarbonate, nylon, and polypropylene, can still be utilized.
- Working with an experienced and knowledgeable injection molding manufacturer is crucial for low volume production. They can guide material selection, mold design, and process optimization to ensure the best results.
Advantages of Low Volume Injection Molding
Low volume injection molding offers several advantages for companies with small to medium production needs. Some of the key benefits of this manufacturing process include:
Cost-effective production
- The lower initial investment in tooling compared to traditional high-volume production methods.Accessible to smaller businesses or startups.
- Faster time-to-market due to shorter lead time for tooling, reducing overall production costs.
Complex and precise parts
- The process enables the production of complex and intricate parts with high precision and repeatability. Ideal for industries such as automotive, electronics, and medical devices that require complicated components.
- The process allows for tight tolerances and the incorporation of fine details in the design.
Design flexibility
- The process allows for easy design modifications and iterations without significant additional costs.
- Particularly beneficial for product development and prototyping, where design adjustments and refinements are standard during the early stages.
Material versatility
- The process offers various thermoplastic materials, including ABS, polycarbonate, nylon, and polypropylene.
- Meets specific requirements and desired properties of the end product.
Faster production cycles
- The process boasts relatively short cycle times, enabling faster production than other manufacturing processes.
- Helpful in meeting tight project deadlines or responding to market demand quickly.
- Increases productivity and provides faster turnaround times.
Reduced waste and environmental impact
- The process minimizes material waste by using only the necessary amount of plastic.
- The process reduces energy consumption and emissions compared to high-volume production methods.
- Environmentally-friendly manufacturing option.
Quality and consistency
- The process ensures high-quality parts with consistent dimensions and properties.
- The process provides excellent control over temperature, pressure, and cooling variables.
- Reliable in industries where product performance and reliability are critical factors.
Customization and personalization
- The process provides an opportunity for customization and personalization of products.
- Production of unique parts tailored to specific customer requirements.
- The process enhances product differentiation and customer satisfaction.
Risk mitigation and market testing
- The process is a lower-risk option for new product development or market testing.
- The process produces limited parts for testing, validation, and market feedback.
- Minimizes the risk of investing in large quantities of parts that may require modifications or not meet market demands.
Low Volume vs. High Volume Injection Molding
You can adapt injection molding, a versatile manufacturing process, to suit various production needs. Two common variations of injection molding are low volume and high volume. Let’s compare these two approaches and explore their differences:
Low Volume Injection Molding
- It is suited for companies with small to medium production needs.
- Offers cost-effective production, making it accessible to smaller businesses or startups.
- The process requires a lower initial investment in tooling compared to high-volume production.
- Allows for faster time-to-market due to shorter lead time for tooling, reducing overall production costs.
- The process enables the production of complex and intricate parts with high precision and repeatability.
- Provides design flexibility, allowing for easy design modifications and iterations without significant additional costs.
- Supports material versatility, offering a wide range of thermoplastic materials to meet specific requirements.
- Provides faster production cycles compared to other manufacturing processes, contributing to increased productivity and shorter turnaround times.
- Minimizes material waste by using only the necessary amount of plastic, reducing environmental impact.
- Ensuring high-quality parts with consistent dimensions and properties is crucial in industries where product performance and reliability are critical.
- Offers customization and personalization options, allowing for the production of unique parts tailored to specific customer requirements.
- Mitigates risks during new product development and market testing, allowing companies to produce a limited quantity of parts for validation and feedback before committing to full-scale production.
High Volume Injection Molding
- Suited for companies with large-scale production needs.
- The higher production volume involves more initial investment in tooling and molds.
- Requires longer lead times for tooling, which may extend the time to market.
- It provides cost advantages due to economies of scale, as the higher volume spreads the fixed costs over larger units.
- The process enables the efficient production of large parts within a shorter period.
- Ideal for industries with high-demand products and established market presence.
- It may offer a narrower range of material options compared to low volume injection molding.
- Requires careful planning and forecasting to optimize production efficiency and minimize waste.
- The process supports consistent quality control and adherence to specifications throughout the high-volume production process.
- Offers limited design flexibility, as design changes may incur significant additional costs.
Applications of Low Volume Injection Molding
Low volume injection molding is a versatile manufacturing process that finds applications across various industries. Its ability to provide cost-effective production, design flexibility, and customization options makes it suitable for multiple applications. Let’s explore some typical applications of low volume injection molding:
Automotive Industry
- Production of complex and precise components for automotive interiors, exteriors, and under-the-hood applications.
- Manufacturing of custom dashboard panels, trim pieces, knobs, and switches.
- Prototyping and production of specialized automotive parts with specific material properties.
- Creation of air vents, ducts, and connectors for vehicle HVAC systems.
Electronics and Electrical Industry
- Production of intricate components for consumer electronics such as smartphones, tablets, and laptops.
- Manufacturing of connectors, housings, and enclosures for electronic devices.
- Customization of keypads, buttons, and switches with various textures and colors.
- Production of electrical connectors and sockets for industrial equipment.
- Prototyping and production of microelectromechanical systems (MEMS) devices.
Medical and Healthcare Industry
- Manufacturing medical device components such as syringe barrels, IV connectors, and surgical instruments.
- Production of customized parts for medical equipment and diagnostic devices.
- Prototyping and production of biocompatible parts for medical implants and prosthetics.
- Production of drug delivery devices and packaging components.
- Manufacturing dental products such as custom trays, orthodontic aligners, and surgical guides.
Consumer Goods
- Customization of consumer products such as toys, household appliances, and personal care items.
- Production of unique packaging designs with branding elements.
- Manufacturing of the small-scale output runs for limited edition products or niche markets.
- Production of intricate and decorative components for home decor items.
- Creation of customized promotional products and giveaways.
Industrial Equipment
- Prototyping and production of specialized parts for industrial machinery and equipment.
- Manufacturing of tooling components, jigs, and fixtures.
- Customization of industrial equipment parts to meet specific requirements.
- Production of durable and high-performance components for heavy-duty applications.
- Creation of protective covers, guards, and mounts for machinery.
Sports and Recreation
- Production of equipment components such as handles, grips, and protective gear.
- Manufacturing of custom parts for bicycles, kayaks, and other sporting goods.
- Creation of specialized components for fitness equipment.
- Prototyping and production of components for outdoor recreational products.

Industries That Benefit from Low Volume Injection Molding
Low volume injection molding offers significant advantages for several industries, including medical devices, aerospace, automotive, electronics, consumer goods, industrial equipment, prototyping, specialty products, and replacement parts. This versatile manufacturing process facilitates the cost-effective production of small quantities, enabling customization, innovation, and efficient product development.
- Medical Devices:Low volume injection molding is ideal for producing customized medical devices and components with precise specifications. It allows for the cost-effective production of small quantities, enabling medical manufacturers to meet diverse patient needs.
- Aerospace:The aerospace industry requires complex parts with high precision and strict quality standards. Low volume injection molding enables the production of lightweight, durable components, reducing weight and improving fuel efficiency in aircraft.
- Automotive:Low volume injection molding is valuable for prototyping and producing specialized automotive parts. It allows manufacturers to quickly iterate and refine designs, ensuring optimal performance and functionality before full-scale production.
- Electronics:The electronics industry benefits from low volume injection molding for producing intricate parts, such as connectors and casings. This process enables the efficient production of small batches, accommodating the fast-paced nature of electronics manufacturing.
- Consumer Goods: Low volume injection molding is advantageous for creating customized consumer goods with unique designs and features. It enables rapid production of small quantities, facilitating market testing and customization to meet consumer preferences.
- Industrial Equipment: Low volume injection molding produces industrial equipment components, such as gears, valves, and housings. This process allows for cost-effective manufacturing of small quantities, meeting the specific requirements of industrial applications.
- Prototyping and Product Development: Companies widely use low-volume injection molding in the prototyping and product development stages. It provides a cost-effective way to produce functional prototypes, enabling design verification, testing, and refinement before mass production.
- Specialty Products: Many niche industries require specialized parts not produced in large quantities. Low volume injection molding offers a viable solution for creating these unique components efficiently, catering to specific market demands.
- Replacement Parts:Low volume injection molding is beneficial for manufacturing replacement parts for various industries. It allows for the on-demand production of small quantities, ensuring a steady supply of critical components without needing a large inventory.
Types of Materials Used in Low Volume Injection Molding
Low volume injection molding utilizes various materials to accommodate diverse manufacturing needs.
- Thermoplastics: Thermoplastics are the most commonly used materials in low volume injection molding. They can be melted, cooled, and re-melted multiple times without significantly changing their properties. Examples of thermoplastics include polyethylene (PE), polypropylene (PP), polystyrene (PS), and polycarbonate (PC).
- Elastomers:Elastomers, also known as rubber-like materials, produce flexible components in low volume injection molding. They offer excellent elasticity, resilience, and impact resistance. Standard elastomers include silicone, polyurethane (PU), and thermoplastic elastomers (TPE).
- Engineering Plastics:Engineering plastics are high-performance materials that exhibit exceptional mechanical, thermal, and chemical properties. Industries widely use them for their strong and durable parts. Some commonly used engineering plastics in low volume injection molding are acrylonitrile butadiene styrene (ABS), nylon (PA), polyethylene terephthalate (PET), and polyoxymethylene (POM).
- Biodegradable and Sustainable Materials: With the growing emphasis on sustainability, low volume injection molding also utilizes biodegradable and sustainable materials. These materials can be derived from renewable resources and offer environmental benefits. Examples include polylactic acid (PLA), bio-based polyethylene (PE), and bio-based polypropylene (PP).
- Metal and Ceramic Powders: In addition to plastics, low volume injection molding can incorporate metal and ceramic powders to produce metal or ceramic parts. The process, known as metal injection molding (MIM) or ceramic injection molding (CIM), involves mixing the powders with a binder and injecting them into molds. Afterward, the parts undergo debinding and sintering to achieve their final properties.
- Composite Materials:Composite materials combine different materials to achieve desired properties. Mixed materials can enhance strength, stiffness, or heat resistance in low volume injection molding. Examples include carbon fiber-reinforced polymers (CFRP), glass fiber-reinforced polymers (GFRP), and mineral-filled polymers.
- Liquid Silicone Rubber (LSR): LSR is a specialized material for producing flexible, heat-resistant, and biocompatible parts. It is particularly suitable for applications requiring excellent sealing properties, such as in the medical and automotive industries.
How Low Volume Injection Molding Works
Low volume injection molding is a manufacturing process that benefits various industries and allows for producing small quantities of customized parts. It involves the design and fabrication of a mold and the preparation of material which is then melted and injected into the mold cavity under high pressure.
- Mold Design:The process begins with designing and fabricating a mold corresponding to the desired part geometry. The mold consists of two halves, the cavity and the core, which form the shape of the final part when brought together.
- Material Preparation: The chosen material, typically in the form of pellets, is loaded into a hopper and fed into the injection molding machine. The shells are then heated and melted to a molten state.
- Injection:The molten material is injected into the mold cavity under high pressure using a reciprocating screw or a plunger. This pressure ensures that the material fills all the intricate details of the mold and maintains its shape during solidification.
- Cooling and Solidification:After filling the mold cavity, the molten material is allowed to cool and solidify within the mold. Cooling channels integrated into the mold dissipate heat and accelerate the solidification process.
- Mold Opening and Ejection:The mold opens once the material has sufficiently solidified, separating the two halves. Ejector pins or plates push the part out of the mold cavity, into a collection bin, or onto a conveyor belt.
- Finishing:The ejected part may undergo different processes to achieve the desired surface finish and dimensional accuracy. These operations may include trimming excess material, removing flash or burrs, and performing secondary operations like machining or painting.
- Repeat Process:The mold closes, and the cycle repeats to produce the next part. Low volume injection molding allows for multiple iterations and adjustments to the mold and process, enabling flexibility in production and design improvements.
- Quality Control:Quality control measures are implemented throughout the process to ensure the produced parts meet the required specifications. These activities may involve regular inspections, dimensional measurements, and functional testing.
- Scalability:Low volume injection molding primarily focuses on producing smaller quantities, but it can also serve as a stepping stone for larger-scale production.Companies can optimize the process for higher volumes if demand increases by employing larger machines or multiple molds.
Types of Low Volume Injection Molding Machines
Various low-volume injection molding machines are available and designed to cater to different manufacturing needs. Factors such as the material used, the complexity of producing the part, and the desired precision and efficiency determine the choice of the machine. Choosing the correct type of machine is crucial for achieving the desired results and ensuring cost-effectiveness in production.
- Hydraulic Machines:Hydraulic low volume injection molding machines utilize hydraulic pumps to generate the pressure required for injecting the material into the mold cavity. They can produce parts with high precision and repeatability and handle various materials.
- Electric Machines:Electric low volume injection molding machines use electric motors instead of hydraulic pumps to drive the injection process. They offer greater energy efficiency, reduced maintenance, and quieter operation than hydraulic machines.
- Hybrid Machines:Hybrid low volume injection molding machines combine the benefits of both hydraulic and electric devices. They combine hydraulic and electric drives, improving precision, energy efficiency, and reduced noise levels.
- Vertical Machines:Vertical low volume injection molding machines use gravity to feed the material into the mold cavity, and the mold is mounted vertically. They are ideal for producing parts with complex geometries and can save floor space in manufacturing facilities.
- Micro-Molding Machines:Micro-molding low volume injection molding machines are specifically designed for producing parts with small dimensions and high precision. They use specialized equipment to achieve the desired results, including micro-injection units and micro-mold cavities.
- Multi-Shot Machines:Multi-shot low volume injection molding machines utilize multiple injection units to produce parts with various materials or colors. This capability allows for creating complex parts with varying textures and finishes.
- Cleanroom Machines:Designers create cleanroom low-volume injection molding machines for use in sterile environments, such as medical or pharmaceutical manufacturing facilities. Manufacturers construct them from materials that are easy to clean, sanitize, and incorporate features to minimize contamination.
Factors That Affect Low Volume Injection Molding
Several factors influence the outcome and efficiency of low volume injection molding. Considering these factors and optimizing each aspect of the process helps ensure successful low volume injection molding production.
- Design Considerations:The part’s design plays a significant role in low volume injection molding. Factors such as wall thickness, draft angles, and undercuts’ presence affect the part’s moldability and overall quality. Well-designed features with proper geometry can help achieve better results.
- Material Selection:The choice of material for low volume injection molding is crucial. Different materials have varying properties, such as melt flow characteristics, shrinkage rates, and temperature sensitivities. The appropriate material that met the functional requirements and desired aesthetics is essential for successful molding.
- Mold Design and Construction:The design and construction of the mold directly impact the quality and feasibility of low volume injection molding. To ensure proper part filling, cooling, and ejection, one must carefully consider mold material, cooling channels, venting, and gating system.
- Process Parameters:For low volume injection molding, one must optimize several process parameters, including injection speed, temperature, pressure, and cooling time. Finding the right balance of these parameters is crucial for achieving optimal part quality, minimizing defects, and ensuring consistent production.
- Quality Control:Implementing quality control measures throughout the low volume injection molding process is essential. Regular inspections, dimensional checks, and functional testing help identify and address any issues or defects early, ensuring that the produced parts meet the required specifications.
- Tooling and Equipment Maintenance:Regular maintenance and upkeep of the injection molding machine and the molds are necessary for consistent and efficient production. Proper cleaning, lubrication, and inspection of the equipment and molds help prevent breakdowns, reduce downtime, and ensure the longevity of the tools.
- Production Volume:Even though manufacturers design low volume injection molding for smaller quantities, the production volume can still influence factors such as cost per part, lead time, and tooling options. Understanding the anticipated production volume is essential for optimizing the process and selecting the appropriate manufacturing strategy.
- Cost Considerations: The cost of low volume injection molding involves various factors, including material costs, mold fabrication costs, machine setup and operation costs, and post-processing expenses. Balancing cost-effectiveness with the desired quality and functionality of the parts is crucial for successful low volume production.
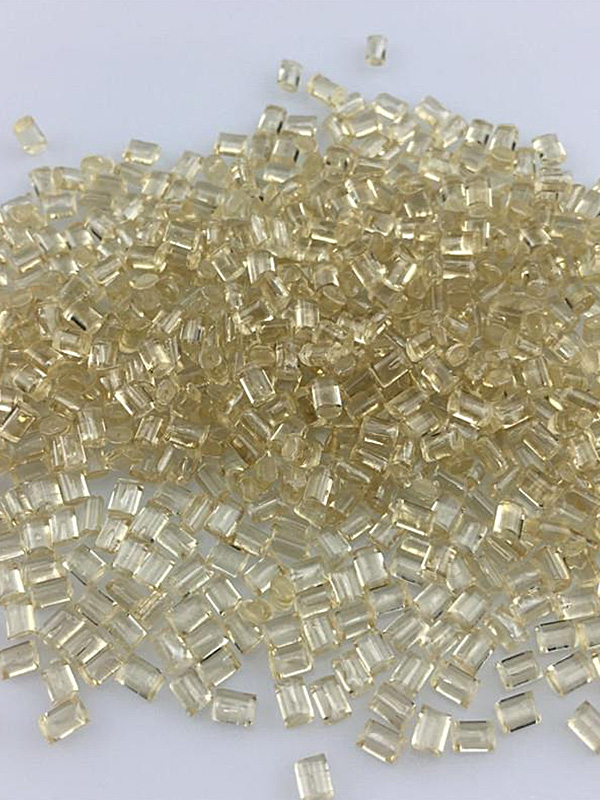
Design Considerations for Low Volume Injection Molding
Designing parts for low volume injection molding requires careful consideration of various factors. These include:
Wall Thickness
- Maintaining consistent and appropriate wall thickness is crucial
- Thick walls can lead to longer cooling times and potential warping.
- Thin walls may result in poor part strength.
- Designing with uniform wall thickness ensures proper material flow and optimal part quality.
Draft Angles
- Incorporating draft angles in the design is essential for easy part ejection
- Draft angles allow for the smooth removal of the part without causing damage.
- Adequate draft angles help prevent sticking and facilitate efficient production.
Undercuts and Side Actions
- Minimizing undercuts and side actions is advisable
- Undercuts make ejection challenging and may require complex mold designs or secondary operations.
- Simplifying the part geometry and avoiding intricate features improves moldability and reduces costs.
Gate Placement
- Proper gate placement is crucial for optimal material flow and minimizing defects
- Gate location affects part appearance, strength, and warpage.
- Placing gates at appropriate locations improves part quality and aesthetics.
Parting Line and Parting Surface
- Defining a suitable parting line and surface is necessary for mold design and assembly
- A clean and well-defined parting line facilitates mold construction and reduces the risk of defects.
Ribs and Bosses
- Incorporating ribs and bosses improves structural integrity and functionality
- Ribs provide strength and stiffness to thin sections.
- Bosses serve as attachment points or inserts for secondary operations.
Surface Finish and Texture
- Considering the desired surface finish and texture is essential
- Mold treatments or cavity texture can achieve smooth or textured surfaces.
- Proper selection and communication of surface finish requirements contribute to desired aesthetics and functionality.
Tolerance and Dimensional Accuracy
- Specifying appropriate tolerances and dimensional accuracy is crucial
- Understanding the capabilities of low volume injection molding is essential.
By considering these design factors, manufacturers can optimize low volume injection molding, resulting in high-quality parts, efficient production, and cost-effectiveness.
Quality Control in Low Volume Injection Molding
Quality control is critical in low volume injection molding to ensure the production of high-quality parts that meet the required specifications. Here are some key factors to consider for effective quality control in low volume injection molding:
- Inspection and Testing:Regular inspections and testing throughout manufacturing help identify defects or issues early on. To ensure the parts meet the specifications, one must perform dimensional checks, visual inspections, and functional testing.
- Material Verification: Ensuring the quality and consistency of the material used in low volume injection molding is crucial. Material verification involves checking the material properties, such as melt flow, viscosity, and color, to confirm that they match the desired specifications.
- Mold Maintenance:Proper maintenance and upkeep of the molds are essential for consistent and high-quality production. Regular cleaning, lubrication, and inspection of the molds help prevent defects, reduce downtime, and extend the lifespan of the molds.
- Process Monitoring:Continuous monitoring of the injection molding process parameters is essential for maintaining quality. It is necessary to monitor variables such as temperature, pressure, and cycle time to ensure they are within the specified ranges and detect deviations or abnormalities.
- Statistical Process Control (SPC):Implementing SPC techniques helps monitor and control the variability in the manufacturing process. It involves collecting and analyzing data from the production process to identify trends, patterns, and potential sources of variation, allowing for proactive adjustments and improvements.
- Corrective and Preventive Actions:Implementing corrective and preventive actions is crucial for addressing quality issues or non-conformities. Upon identifying defects or deviations, the team promptly makes an effort to correct them and prevent their recurrence, ensuring continuous improvement in the manufacturing process.
- Documentation and Traceability:Maintaining proper documentation and traceability of the production process is essential for quality control. To facilitate traceability and quality assurance, recording process parameters, inspection results, and material information, as well as tracking the history of each produced part, is essential.
- Supplier Quality Management:Ensuring the quality of components and materials sourced from suppliers is essential. Establishing robust supplier quality management processes, including qualification, evaluation, and ongoing monitoring, helps ensure the utilization of only high-quality inputs in manufacturing.
By implementing effective quality control measures, manufacturers can produce high-quality, consistent, and reliable parts through low volume injection molding.
Tooling for Low Volume Injection Molding
Tooling for low volume injection molding requires careful consideration of mold material selection, design, construction, maintenance, repair, inserts, testing, and storage.
Mold Material Selection
Choosing the suitable mold material is crucial for low volume injection molding. Consider factors like durability, heat resistance, and compatibility when selecting a material. Common mold materials include steel alloys, aluminum alloys, and composite materials.
Mold Design
Designing the mold for low volume injection molding requires careful consideration of factors like part geometry, gating system, cooling channels, and ejection mechanism.
- Optimal part geometry facilitates proper filling, cooling, and ejection of the part.
- A well-designed gating system ensures efficient material flow and minimizes defects.
- Properly designed cooling channels help control cycle times and ensure consistent part quality.
- An effective ejection mechanism allows for easy removal of the part from the mold.
Mold Construction
Carry out the mold construction with precision and attention to detail.
- Skilled toolmakers use machining, CNC milling, and EDM (Electrical Discharge Machining) techniques to create the mold components.
- Careful assembly and alignment of mold components are essential for optimal performance and part quality.
Mold Maintenance and Repair
Regular maintenance and timely repair of molds are crucial to ensure their longevity and consistent performance.
- Operators should conduct regular cleaning, lubrication, and inspection to prevent issues and optimize production.
- Prompt repair of any damage or wear in the mold components helps avoid defects and production interruptions.
Mold Inserts and Interchangeable Components
Using mold inserts and interchangeable components allows for flexibility and cost-effectiveness in low volume injection molding.
- Operators can modify or replace inserts to adjust to design changes or other requirements—variations of the part.
- Interchangeable components enable quick mold changeovers, reducing downtime and increasing production efficiency.
Mold Testing and Validation
Thorough testing and validation of the mold are essential before commencing production.
- We conduct mold trials to optimize process parameters, ensure part quality, and identify necessary adjustments.
- We may perform mold flow analysis and computer simulations to predict and optimize the molding process.
Mold Storage and Preservation
Proper storage and preservation practices are essential to maintain quality and performance when molds are unused.
- Molds should be stored in a controlled environment to prevent damage from temperature fluctuations, humidity, and contaminants.
- Even during periods of non-use, operators should conduct regular inspections and maintenance.
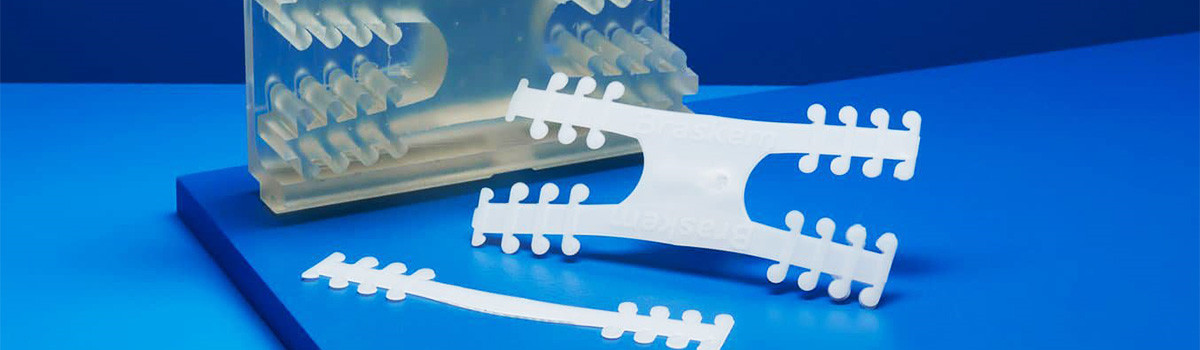
Cost-Effective Strategies for Low Volume Injection Molding
Adopting cost-effective strategies for low volume injection molding requires a holistic approach that encompasses mold design, material selection, process optimization, automation, and supplier partnerships. By implementing these strategies, companies can achieve high-quality results while minimizing costs and maximizing efficiency in their low-volume manufacturing operations.
- Efficient mold design:Efficiently designing the mold for low volume injection molding can significantly reduce costs. Simplifying the mold design and minimizing the number of cavities can lower tooling costs and reduce production time.
- Material selection:Choosing a suitable material is crucial for cost-effective low-volume injection molding. Opting for less expensive resins or exploring alternative materials that meet the required specifications can lead to substantial cost savings without compromising quality.
- Automation and robotics:Implementing automation and robotics in injection molding can enhance efficiency and reduce labor costs. Automated systems can handle repetitive tasks, minimize errors, and increase production output, making them ideal for low-volume manufacturing.
- Process optimization:Fine-tuning the injection molding process can result in cost savings. Analyzing and optimizing parameters such as temperature, pressure, and cycle times can reduce material waste, improve part quality, and increase productivity.
- On-demand manufacturing:Embracing on-demand manufacturing allows for more flexibility and cost-effectiveness in low volume injection molding. By producing parts only when needed, companies can avoid excess inventory costs and minimize the risk of obsolescence.
- Tooling alternatives:Exploring alternative tooling options, such as 3D-printed molds or soft tooling, can be cost-effective for low volume production. These alternatives often have lower upfront costs and shorter lead times than traditional steel molds.
- Supplier partnerships:Collaborating closely with reliable and experienced injection molding suppliers can help optimize costs. Suppliers with expertise in low volume production can offer valuable insights, suggest cost-saving measures, and provide competitive pricing on materials and tooling.
- Post-processing optimization:Streamlining post-processing operations, such as trimming, assembly, and finishing, can reduce costs. Investing in efficient post-processing equipment and techniques can reduce labor requirements and minimize secondary operation expenses.
Benefits of Using 3D Printing for Low Volume Injection Molding
Utilizing 3D printing for low volume injection molding offers several advantages. It enables rapid prototyping, allowing for quick iterations and reduced design errors. 3D printing minimizes waste generation and helps mitigate risks by allowing testing and validation before committing to full-scale production.
- Rapid prototyping: 3D printing offers the advantage of rapid prototyping, allowing designers to iterate and refine their product designs quickly. This approach enables companies to bring products to the market faster and avoid expensive design mistakes.
- Cost-effective tooling:3D printing can be a cost-effective alternative for low volume injection molding tooling. By using 3D-printed molds or inserts, companies can save on the upfront costs of traditional steel molds, especially for small production runs.
- Design flexibility: 3D printing allows for intricate and complex designs that may not be feasible with traditional machining methods. This flexibility enables the production of customized and unique parts, catering to specific customer requirements.
- Reduced lead times: By utilizing 3D printing, manufacturers can significantly reduce lead times compared to traditional manufacturing methods. The absence of tooling and the ability to produce parts on demand expedite the production process, enabling faster customer delivery.
- Material variety:3D printing offers a wide range of materials, including thermoplastics, resins, and composites. This material versatility allows for producing parts with different properties, catering to specific functional and aesthetic requirements.
- Waste reduction:3D printing is an additive manufacturing process, meaning it only uses the material required to build the part, resulting in minimal waste generation. Reducing material costs also helps in promoting sustainability efforts.
- Risk mitigation: Using 3D printing for low volume injection molding allows companies to mitigate risks associated with investing in expensive tooling for unproven designs or uncertain market demand. It will enable testing the market with smaller production volumes before committing to full-scale production.
- Bridge to production:3D printing can serve as a bridge to production, allowing companies to quickly validate their designs and test the functionality of parts before investing in expensive injection molding tooling. Identifying design flaws early on can save costs in the long run.
Sustainability of Low Volume Injection Molding
Low volume injection molding can be a sustainable manufacturing option when approached with environmentally conscious practices.
- Material efficiency:Low volume injection molding promotes material efficiency by producing only the required parts, minimizing waste generation. This approach helps reduce the environmental impact associated with excessive material consumption.
- Energy conservation:Compared to high-volume production methods, low volume injection molding consumes less energy due to shorter production runs and reduced machine operation time. By doing this, we can conserve energy and reduce greenhouse gas emissions.
- Waste reduction:Low volume injection molding allows for precise production quantities, reducing the need for excess inventory and minimizing waste. Companies can reduce waste generation and disposal costs by optimizing production planning and forecasting demand.
- Recycling opportunities:Low volume injection molding often utilizes recyclable materials such as thermoplastics. We can reuse materials and reduce reliance on virgin resources by integrating recycling practices into the production process. Integrating recycling practices into the production process allows for the reuse of materials and reduces reliance on pure resources.
- Sustainable material choices:Companies can prioritize using sustainable and eco-friendly materials in low volume injection molding. Bio-based plastics, recycled materials, and biodegradable resins offer viable alternatives that reduce the environmental impact and promote a circular economy.
- Localized production:Low volume injection molding allows for localized production, reducing transportation distances and associated carbon emissions. By producing closer to the end market, companies can minimize the environmental footprint of their supply chain.
- Design for sustainability:Low volume injection molding allows one to incorporate sustainable design principles. Designing parts with lightweight structures, optimized geometries, and efficient use of materials can further enhance the sustainability of the manufacturing process.
- Life Cycle Assessment:Conducting a life cycle assessment of low volume injection molding processes helps identify areas for improvement and sustainability optimization. Analyzing the environmental impacts at each stage, from raw material extraction to end-of-life disposal, enables companies to make informed decisions and implement sustainable practices.
Regulations and Standards for Low Volume Injection Molding
Adhering to regulations and standards in low volume injection molding is vital to ensure product safety, environmental responsibility, workplace safety, and compliance with legal and industry requirements. Companies must stay informed about the applicable regulations and standards and integrate them into their manufacturing processes.
- Product safety standards:Low volume injection molding must comply with relevant product safety standards to ensure that the produced parts meet quality and safety requirements. These standards may vary depending on the industry, such as automotive, medical, or consumer goods.
- Material regulations:Following specific rules and standards in selecting and using materials for low volume injection molding is necessary to ensure proper manufacturing processes. These regulations govern material composition, toxicity levels, and environmental impact. Compliance with laws such as REACH (Registration, Evaluation, Authorization, and Restriction of Chemicals) is crucial for ensuring the use of safe and sustainable materials.
- Environmental regulations:Low volume injection molding operations must comply with environmental regulations to minimize their ecological impact. These regulations address issues such as air emissions, wastewater management, waste disposal, and energy consumption. Adhering to limitations such as ISO 14001 (Environmental Management Systems) demonstrates a commitment to environmental responsibility.
- Occupational health and safety standards:Ensuring a safe working environment is essential in low volume injection molding facilities. Compliance with occupational health and safety standards, such as OSHA (Occupational Safety and Health Administration) regulations, helps protect workers from potential hazards associated with machinery, materials, and processes.
- Quality management systems:Implementing quality management systems, such as ISO 9001, is essential for low volume injection molding operations. These systems provide a framework for consistently delivering products that meet customer requirements and comply with applicable regulations and standards.
- Traceability and labeling requirements:Traceability measures may be necessary for low volume injection molding to track the origin of materials and components used in production. Labeling requirements, such as product identification, batch numbers, and safety warnings, ensure clear communication and compliance with relevant regulations.
- Intellectual property considerations:Protecting intellectual property rights is crucial in low volume injection molding, mainly when producing parts for proprietary products. Companies must respect patent rights and ensure their manufacturing processes do not infringe on intellectual property.
- International trade regulations:If engaged in international trade, low volume injection molding operations must comply with trade regulations and standards specific to the countries involved. Following customs regulations and import/export restrictions may be necessary to ensure compliance with international trade agreements.
Choosing the Right Low Volume Injection Molding Service Provider
A reliable and capable partner will contribute to the success of your low-volume manufacturing endeavors.
- Expertise and experience:Look for a service provider specializing in low volume injection molding, with knowledge and experience handling projects of similar scale and complexity. A provider with a proven track record can offer valuable insights, efficient processes, and high-quality results.
- Customization capabilities: Assess the provider’s ability to offer customized solutions that align with your project requirements. Look for their flexibility in accommodating design modifications, material options, and production volumes to ensure a tailored approach.
- Quality assurance:Verify that the service provider has robust quality assurance processes. To ensure the reliability and consistency of the parts, we adhere to industry standards and certifications (such as ISO 9001) and conduct thorough inspections and tests.
- Production capacity and scalability:Evaluate the service provider’s capability and scalability to meet your low-volume manufacturing needs. They should be able to handle your desired production volumes, whether small or medium-sized, and scale up if required.
- Technology and equipment:Assess the provider’s technological capabilities and the state-of-the-art equipment they employ. Advanced injection molding machinery and technology improve process efficiency, part consistency, and faster production cycles.
- Material expertise:Consider the service provider’s expertise in working with a wide range of materials suitable for low volume injection molding. They should know different resins and their properties and be able to suggest material options that meet your project requirements.
- Value-added services:Evaluate the additional services offered by the provider, such as post-processing, assembly, and finishing. Value-added services can streamline your production process, reduce logistics complexities, and provide a comprehensive solution from start to finish.
- Supply chain management:Assess the provider’s supply chain management capabilities, including sourcing materials and components. A well-managed supply chain ensures the timely availability of materials, reduces production delays, and optimizes cost efficiency.
- Customer support and communication:Consider the service provider’s customer support and communication level. Precise and responsive communication, regular project updates, and a collaborative approach are crucial for a successful partnership.
- Cost-effectiveness:While cost should not be the sole determining factor, evaluating the provider’s pricing structure and overall cost-effectiveness is essential. Compare quotes, assess the value for money, and ensure transparency regarding any additional fees or charges.
Common Challenges in Low Volume Injection Molding
Addressing these challenges in low volume injection molding requires a thorough understanding of the project requirements, close collaboration with suppliers and partners, and continuous improvement of processes.
- Tooling costs:Low volume injection molding often involves smaller production runs, making the upfront tooling costs a significant challenge. Designing and manufacturing molds can be proportionally higher per part than high-volume production, requiring careful cost analysis and optimization.
- Design complexity:Low volume production runs may involve complex and intricate designs. The challenge lies in ensuring that the method is feasible for injection molding and that the mold can accurately reproduce the desired geometry. Design modifications and iterations may be necessary to achieve optimal results.
- Material selection:Selecting the appropriate material for low volume injection molding can be challenging. We must consider cost, functionality, durability, and availability. Finding a balance between material properties and project requirements is essential to achieve the desired quality and performance.
- Part quality consistency:Maintaining consistent part quality throughout low volume production runs can be challenging. Variations in process parameters, mold wear, and material characteristics can impact part dimensions, surface finish, and mechanical properties. Rigorous quality control measures and continuous monitoring are necessary to mitigate variations.
- Lead times:Low volume injection molding often requires shorter lead times than high-volume production. Efficient planning and coordination are crucial to optimize production schedules, minimize downtime, and ensure timely delivery of parts. Effective communication with suppliers and partners is essential to meet tight timelines.
- Scalability limitations:Low volume injection molding processes may have limits when it comes to scalability. Transitioning from low volume to higher-volume production may require tooling, equipment, and process adjustments. Anticipating scalability challenges and planning for future production needs is essential.
- Cost per part:The cost per part in low volume injection molding tends to be higher compared to high-volume production because we spread out the cost of tools over smaller pieces. Balancing cost considerations while maintaining quality standards and meeting project requirements is crucial.
- Risk of obsolescence:Low volume production runs often cater to niche markets or specific product variants. The risk of parts becoming obsolete or demand fluctuating can pose challenges. Careful market analysis, demand forecasting, and inventory management strategies are necessary to minimize the risk of obsolescence.
Future of Low Volume Injection Molding
The future of low volume injection molding is bright, with new opportunities emerging from advancements in automation, additive manufacturing, sustainable materials and processes, customization, and digitalization. Manufacturers that embrace these trends and invest in new technologies and procedures will be well-positioned to succeed in a rapidly evolving market.
- Automation and Industry 4.0:Low volume injection molding is poised to benefit from automation and Industry 4.0 technologies such as robotics, artificial intelligence, and IoT. Automation can help reduce lead times, improve quality consistency, and increase productivity while minimizing labor costs.
- Additive Manufacturing and Hybrid Processes: To further enhance the capabilities of low-volume production, additive manufacturing and hybrid processes, such as combining 3D printing and injection molding, can be employed. These technologies can enable faster prototyping, greater design freedom, and improved part quality.
- Sustainable Materials and Processes:Sustainability is an increasing focus for manufacturing operations. The future of low volume injection molding lies in adopting sustainable materials and processes. Biodegradable and renewable materials can reduce environmental impact, while eco-friendly processing techniques can minimize waste and energy consumption.
- Customization and Personalization:Consumer demand for customization and personalization drives innovation in low volume injection molding. Advanced software and automation technologies can enable mass customization of parts with minimal tooling costs, opening up new opportunities in niche markets.
- Digitalization and Connectivity:Digitalization and connectivity are the future of low volume injection molding. Manufacturers can optimize production, improve quality, and enhance supply chain transparency by leveraging data analytics and cloud-based platforms. These technologies can also enable remote monitoring and predictive maintenance.
Conclusion
Low volume injection molding offers significant advantages for small production runs. 3D printing technology enables rapid prototyping, cost-effective tooling, and design flexibility. It allows businesses to reduce lead times, choose from a wide range of materials, minimize waste, and mitigate risks. By embracing these benefits, small businesses can optimize their manufacturing processes, meet customer demands, and maintain a competitive edge in the market. Low volume injection molding provides an efficient, cost-effective solution that empowers small production runs to thrive in today’s dynamic manufacturing landscape.