Liquid Silicone Rubber(LSR) Injection Molding
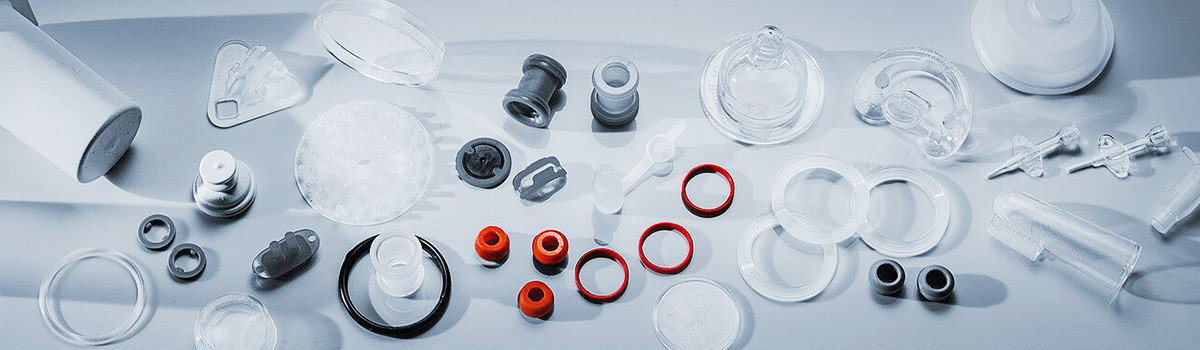
What is the Liquid Silicone Rubber(LSR) Injection Molding?
Injection molding of Liquid Silicone Rubber (LSR) is a process used to produce pliable, durable parts in high volumes. During the process, several components are necessary: an injector, a metering unit, a supply drum, a mixer, a nozzle, and a mold clamp, among others.
Injection molding of Liquid Silicone Rubber (LSR) is a common technology used for the production of different products for medical and electrical applications, among others. In addition to the innate properties of the material, the parameters of the process are critical too. LSR injection molding is a multistep process that is presented.
The first step is the preparation of the mixture. LSR usually consists of two components, pigment, and additives (fillers for example), depending on the desired properties of the final product. In this step, the ingredients of the mixture are homogenized and can be combined with the temperature stabilization system for a better control of silicone temperature (ambient temperature or silicone preheating).
Nowadays, the application range of silicone rubber products is getting wider and wider, and LSR injection molding is an important role in this industry.
How Does Liquid Silicone Rubber Molding Work?
LSR molding differs slightly from thermoplastic injection molding due to its flexibility. Like a standard aluminum tool, an LSR molding tool is fabricated using CNC machining to create a high-temperature tool built to withstand the LSR molding process. After milling, the tool is polished by hand to customer specifications, which allows six standard surface finish options.
From there, the finished tool is loaded into an advanced LSR-specific injection molding press that is precision geared for accurate control of shot size to produce the most consistent LSR parts. At Mold-Making, LSR parts are manually removed from the mold, as injector pins can impact part quality. LSR materials include standard silicones and specific grades to fit various part applications and industries like medical, automotive, and lighting. Since LSR is a thermosetting polymer, its molded state is permanent—once it is set, it can’t be melted again like a thermoplastic. When the run is complete, parts (or the initial sample run) are boxed and shipped shortly thereafter.
Here let us explore it, first, we have to talk about the liquid silicone rubber material, the main points you should know as follows:
Liquid silicone rubber(LSR) is excellent insulation, suitable for high-quality or high-tech electronic plugs.
Liquid silicone rubber(LSR) materials are suitable for use in high temperature or low-temperature environments. The insulation properties, mechanical properties, and physical properties of the materials remain unchanged at 200 ℃ or as low as -40 ℃.
It is resistant to gasification and aging, so it is suitable for outdoor applications.
Liquid silicone rubber(LSR) is oil resistant, can be used in the oil mining industry. There are two models: vertical double slide liquid silicone injection molding machine, vertical single slide liquid silicone injection machine, used to produce all kinds of high-demand, high-precision silicone rubber products; lower cylinder angle injection machine, is the production of composite suspension insulators, Post insulators and traditional models of arresters.
The Advantages of LSR Injection Molding (LIM).
There are many advantages to LSR Injection Molding (LIM). It’s compared with silicone compression molding.
The liquid silicone rubber(LSR) material is safer, silicone gel has food grade or medical grade. The LSR injection molding(LIM) has higher precision, can make very high precision silicone rubber parts. Also, it has a very thin parting line and a small flash.
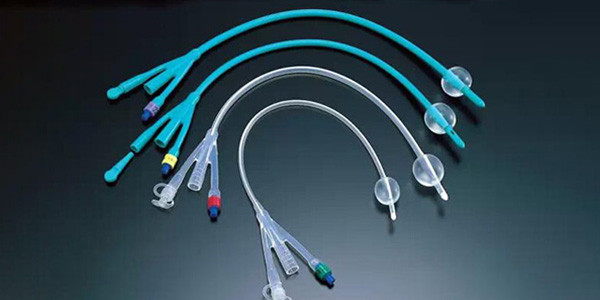
Advantages of LSR molded parts
Limitless design – Enables production of part geometries and technical solutions not possible otherwise
Consistent – Provides the highest consistency in product dimension, precision and overall quality
Pure – Silicone is one of the most extensively tested biomaterials with a long history of safe use
Precise – Flashless, wasteless tool design concepts for parts weighing from 0.002 grams to several hundred grams
Reliable – Using the latest technology in machinery, tooling and automation
Quality – Zero-defect quality level through in-process controls
Fast – Enables highest volume production due to short cycle times, from several thousand to millions
Clean – Utilizing state-of-the-art processing techniques and production in Class 7 and 8 cleanrooms
Cost-effective – Offers lowest Total Cost of Ownership (TCO)
LSR Injection Molding
Innovative technology meeting customer needs:
Liquid Silicone Rubber (LSR) can be processed in a liquid injection molding (LIM) process. The liquid raw material is mixed from two separate components in a ratio of 1:1 and injected via a cold-runner-system into a hot mold. Curing takes place within seconds, offering the advantage of fast cycling and production of large quantities.
Due to the flexibility in design and tooling, LSR injection molding is ideal for producing complex geometries and can consolidate various functional features into a single part. It also offers significant advantages in terms of product reliability and total cost of ownership.
LSR Liquid Silicone Rubber Injection Molding Process
DJmolding liquid silicone rubber injection molding machine appears to look just like thermoplastic injection molding machines. Both types of presses use the same basic machine parts, clamp unit, and injection unit.
The LSR injection molding machine clamp unit is identical for liquid silicone rubber and thermoplastic machines. The silicone injection molding machines typically have a hydraulic ram and may have a hydraulic toggle. Some presses are designed with an electric ram with toggle. Unlike the high pressures used to mold thermoplastic parts, liquid silicone injection pressure is in the range of 800 PSI. The purpose of the clamp is to contain the expansion force of the silicone material, by keeping the mold closed as the silicone cures.
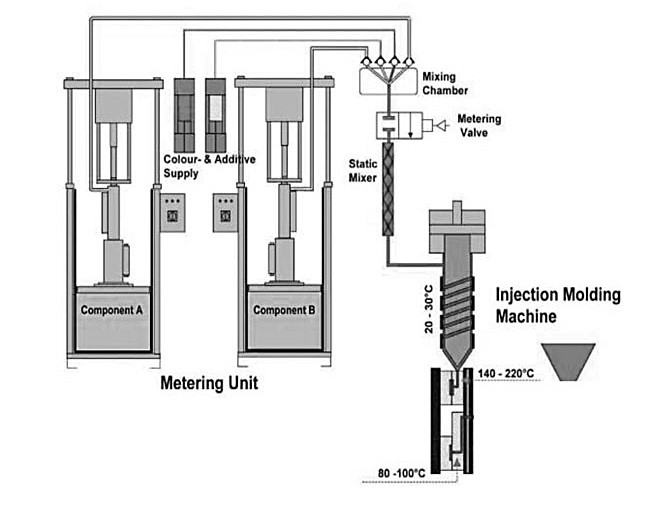
The injection unit for liquid silicone runs cool with a water cooled barrel and nozzle to prevent the liquid silicone from curing. Thermoplastic injection units run the opposite way, they need the barrel and nozzle to be heated to 300F or more to keep the material moving. Liquid injection molding units also run at lower pressures (under 1,000 PSI), while their thermoplastic counterparts run at tens of thousands of PSI.
Liquid silicone is typically provided in 5 gallon pail or 55 gallon drums. There is a part A and Part B. Colorants come in the form of dispersions and are normally 1-3% by weight of mixed silicone. The silicone dousing unit pumps one part A silicone and one part B silicone via separate hoses to the static mixer. In addition, color is pumped to the static mixer via another hose. The mixed components are then fed into the throat of the injection molding barrel by way of a shut-off valve.
DJmolding is a professional liquid silicone rubber(LSR) injection molding and liquid silicone rubber parts manufacturer from china.
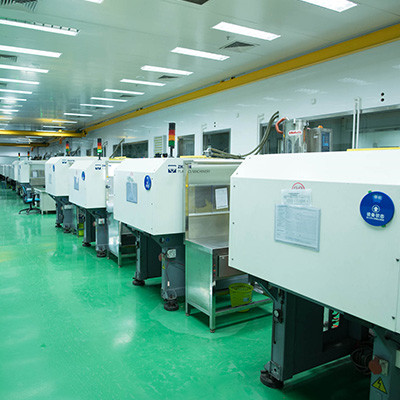
Liquid Silicone Rubber Injection Workshop
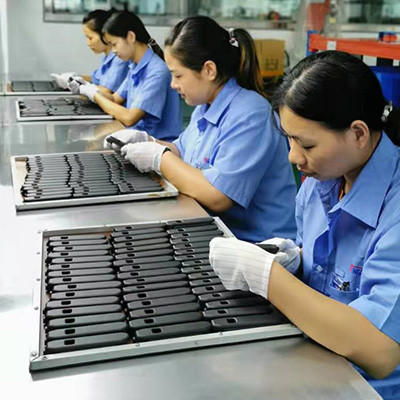
LSR Injection Prodcuts QC
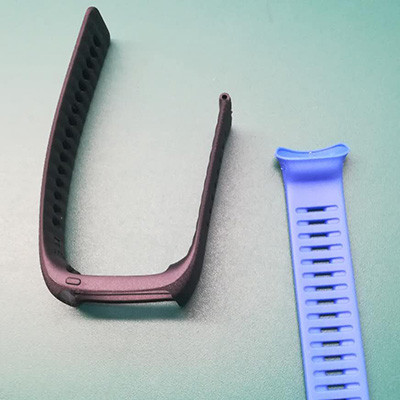
LSR Products
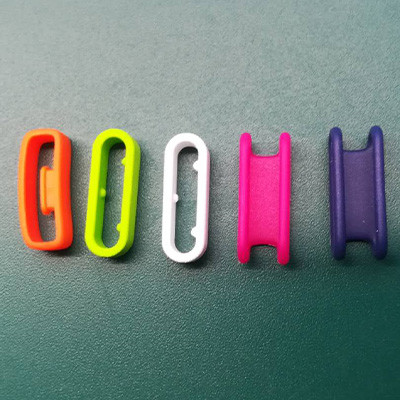
LSR Products
Our liquid silicone rubber molding process produces custom prototypes and end-use production parts in 15 days or less. We use aluminum molds that offer cost-efficient tooling and accelerated manufacturing cycles, and stock various grades and durometers of LSR materials.
Providing the highest consistency in dimensions, precision, overall quality.
Our holistic approach to Liquid Silicone Rubber molding relies on partnering with customers to develop innovative solutions based on unique specifications and requirements.
Liquid Silicone Rubber (LSR) Injection Molding is a manufacturing process involving injecting liquid silicone rubber into a mold to create various products. LSR is a versatile material that has become increasingly popular due to its unique properties, including biocompatibility, thermal stability, and chemical resistance. In this article, we will discuss the benefits of LSR injection molding and explore the various applications of this technology.
How Does LSR Injection Molding Work?
LSR (Liquid Silicone Rubber) injection molding is a manufacturing process that produces high-quality, precision silicone rubber parts. It is beneficial for creating complex shapes and designs with excellent detail and consistency. The process involves injecting liquid silicone rubber into a mold cavity, allowing it to cure and solidify into the desired shape. Here’s a brief overview of how LSR injection molding works:
Mold Preparation: The process begins with preparing the mold. The mold typically consists of two halves, an injection side, and a clamping side, which fit together to create a cavity for the silicone. After curing, the mold is cleaned and coated with a release agent to facilitate easy part removal.
Silicone Preparation: Liquid silicone rubber is a two-component material that consists of a base silicone and a curing agent. These components are mixed together in a precise ratio. The mixture is degassed to remove any air bubbles that could affect the quality of the final part.
Injection: The mixed and degassed liquid silicone rubber is transferred to an injection unit. The injection unit heats the material to a specific temperature to reduce its viscosity and make it easier to flow. The material is injected into the mold cavity through a nozzle or sprue.
Curing: Once the liquid silicone rubber is injected into the mold cavity, it begins to heal. The curing process is typically initiated by heat, although some molds may utilize other methods, such as UV light. The heat causes the silicone to cross-link and solidify, forming the mold cavity. The curing time varies depending on the part design and silicone material.
Cooling and Part Removal: After the curing process, the mold is cooled to allow the silicone to be fully set. The cooling time can vary but is typically shorter than the curing time. Once cooled, the mold is opened, and the finished part is removed. The position may require additional post-processing steps, such as trimming excess material or inspecting for any defects.
LSR injection molding offers several advantages, including producing intricate and complex geometries, excellent part consistency, high precision, and resistance to extreme temperatures, chemicals, and aging. It is commonly used in various medical, automotive, electronics, and consumer products industries.
It’s important to note that this is a simplified explanation of the LSR injection molding process, and the actual operation may vary depending on the specific equipment, materials, and part requirements.
Advantages of LSR Injection Molding
LSR (liquid silicone rubber) injection molding is a versatile manufacturing process that offers several advantages over traditional molding methods. LSR injection molding involves injecting liquid silicone into a mold and curing it into a solid form to create a finished product. Here are some of the main advantages of LSR injection molding:
Precision and Consistency
LSR injection molding offers exceptional precision and consistency in creating complex, intricate parts with fine details. The liquid silicone is injected into a mold under high pressure, filling even the tiniest crevices and corners to produce highly complex parts. Additionally, LSR molding allows for greater consistency and repeatability, reducing the chance of defects and inconsistencies in the final product.
High-Quality Parts
LSR injection molding can produce high-quality, durable parts resistant to wear and tear, heat, and UV radiation. LSR materials have excellent physical properties, including high elasticity, low compression set, and resistance to extreme temperatures. This makes LSR injection molding an ideal choice for producing parts that require high precision and durability, such as medical devices, automotive components, and consumer products.
Cost-Effective
LSR injection molding can be a cost-effective manufacturing method for producing large parts. The process’s high precision and consistency help reduce waste and scrap material, while the low labor requirements and efficient production times minimize manufacturing costs. Additionally, LSR materials have a long lifespan, reducing the need for frequent replacement or repair of parts.
Versatility
LSR injection molding can produce various parts with varying sizes, shapes, and geometries. The liquid silicone can be molded into intricate and complex shapes with refined details, making it ideal for producing parts requiring high precision and accuracy. Additionally, LSR injection molding can have features with varying degrees of hardness and softness, allowing for more extraordinary product design and function flexibility.
Reduced Cycle Times
LSR injection molding has fast cycle times, allowing for producing large quantities of parts in a relatively short period. The liquid silicone is injected into the mold and cured into a solid form in seconds, making it an ideal choice for high-volume production runs.
Low Waste Generation
LSR injection molding produces very little waste material, as the liquid silicone is injected directly into the mold and cured to form the desired shape. This contrasts with other manufacturing processes, such as machining or casting, which generate significant scrap material. Additionally, LSR materials can be recycled and reused, reducing the need for new materials and reducing waste generation.
Improved Safety
LSR materials are generally free of harmful chemicals such as phthalates, BPA, and PVC, making them safer for workers and consumers. Additionally, the low-temperature process used in LSR injection molding does not require harmful solvents or other chemicals, reducing the risk of exposure to hazardous materials.
Reduced Time to Market
LSR injection molding can reduce the time to market for new products, as it allows for rapid prototyping and fast production runs. The process’s high precision and consistency help ensure that the final product meets the desired specifications, reducing the need for multiple rounds of prototyping and testing.
Automation
LSR injection molding can be highly automated, reducing the need for manual labor and lowering energy consumption. Additionally, automation can improve efficiency, reduce labor costs, and improve the consistency and quality of the final product.
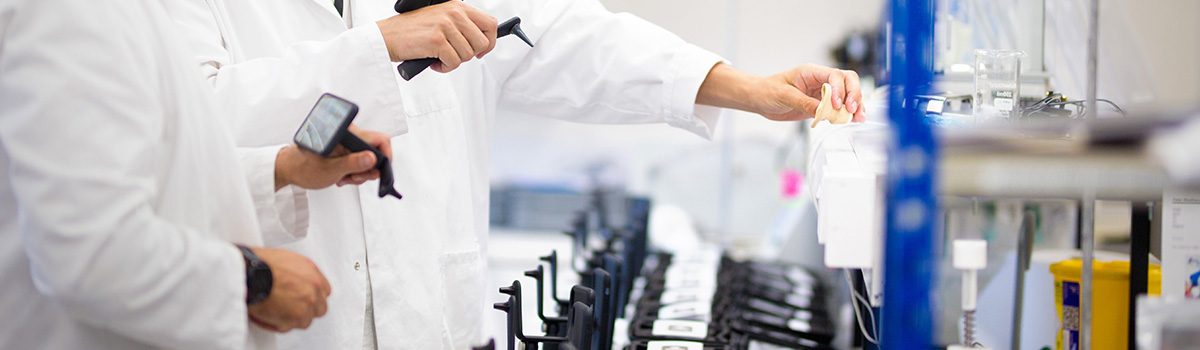
Disadvantages of LSR Injection Molding
While LSR (liquid silicone rubber) injection molding offers numerous advantages, there are also a few disadvantages to consider when deciding whether to use this manufacturing process. Here are some of the main disadvantages of LSR injection molding:
High Initial Investment
One of the main disadvantages of LSR injection molding is the high initial investment required to set up the equipment and molds. LSR injection molding machines and tooling can be expensive, particularly for custom molds or smaller production runs. This can make LSR injection molding less cost-effective for companies with smaller budgets or products with limited demand.
Limited Material Selection
While LSR materials offer excellent physical properties, they are limited in material selection. Unlike traditional thermoplastics, a limited number of silicone-based materials are available for use in LSR injection molding. Finding suitable materials for specific applications or products can make it challenging.
Longer Curing Times
LSR injection molding requires longer curing times than traditional injection molding processes. The liquid silicone needs time to cure and solidify, which can result in longer production times and reduced efficiency. Additionally, longer healing times can make producing certain parts with intricate or complex geometries challenging.
Specialized Skill Set Required
LSR injection molding requires specialized knowledge and expertise, including a deep understanding of the properties and behavior of liquid silicone. This can make it challenging for companies to find qualified personnel to operate and maintain the equipment, particularly in areas where LSR injection molding is less common.
Molding Challenges
LSR injection molding can present a few challenges that must be addressed to ensure the production of high-quality parts. For example, liquid silicone can be prone to flash or burrs, affecting the final product’s quality. Additionally, mold release agents may be required to remove the parts from the mold, which can affect the final product’s surface finish and mechanical properties.
Limited Surface Finishes
LSR injection molding is limited regarding surface finishes, as liquid silicone is incompatible with certain coatings or finishes. This can make achieving the desired aesthetic or functional properties for specific products or applications challenging.
Limited Color Options
LSR injection molding is also limited in color options, as the liquid silicone material is generally translucent or opaque. While some color additives are available, they can be challenging to incorporate into the material without affecting the physical properties or consistency of the final product.
Potential for Part Contamination
LSR injection molding can present a risk of contamination if the equipment or molds are not adequately maintained or cleaned. Contamination can affect the final product’s physical properties, leading to defects or failures over time.
Precision and Accuracy in LSR Injection Molding
Precision and accuracy are essential aspects of LSR (Liquid Silicone Rubber) injection molding, which produces high-quality silicone rubber parts with tight tolerances and exacting specifications. Here are some key factors that contribute to precision and accuracy in LSR injection molding:
- Mold Design and Construction: The mold is a critical component of the LSR injection molding process, as it determines the final shape and dimensions of the part. The mold must be designed and constructed precisely to ensure the last part meets the desired specifications. The mold must be made of high-quality materials and built to tight tolerances to minimize errors and ensure accuracy.
- Injection Unit Control: The injection unit controls the flow of the liquid silicone rubber into the mold. Precise control of the injection unit is critical to achieving accurate and consistent parts. The injection unit must be calibrated and controlled to ensure the material is injected into the mold cavity with the correct speed, pressure, and volume.
- Temperature Control: Temperature control is a critical factor in the LSR injection molding process, as it affects the viscosity of the material and the curing time. The temperature must be carefully controlled to ensure that the material flows smoothly into the mold and that the curing process occurs at the correct rate.
- Material Quality: The quality of the LSR material is critical to achieving precision and accuracy in the final part. To ensure proper curing and consistency, the material must be free of impurities and mixed to the correct ratio.
- Post-Processing: Post-processing steps such as trimming and inspection are essential for achieving precision and accuracy in LSR injection molding. The part must be trimmed to the correct dimensions and inspected for defects or imperfections.
LSR injection molding offers excellent precision and accuracy, allowing for the creation of parts with tight tolerances and exacting specifications. It can produce parts with consistent quality and minimal variations from piece to detail. This makes it an ideal choice for applications where precision and accuracy are critical, such as in medical devices, automotive components, and electronic products.
Faster Production Times
Liquid silicone rubber (LSR) injection molding is a popular manufacturing process that produces high-quality silicone products with excellent properties such as chemical resistance, temperature resistance, and biocompatibility. However, the production times for LSR injection molding can sometimes be slow, which can delay the manufacturing process and increase costs. Here are some ways to improve the production times of LSR injection molding:
- Use an efficient injection molding machine: Choosing a suitable machine is crucial to speeding up production. Look for a device that can inject LSR rapidly without sacrificing quality. Consider using a high injection speed machine, reducing the cycle time and improving production efficiency.
- Optimize the mold design: The mold design is also an essential factor affecting the production time of LSR injection molding. Optimize the mold design to ensure the LSR is injected efficiently and uniformly. Consider using a mold with a larger gate size to improve the flow of the LSR and reduce the cycle time.
- Use a hot runner system: A hot runner system can improve the efficiency of LSR injection molding by keeping the LSR at the ideal temperature throughout the injection process. This can reduce the cycle time and improve the quality of the final product.
- Preheat the LSR: Preheating the LSR before injection can also help reduce production time. Preheating the LSR can improve its flow and reduce the injection time, leading to faster cycle times and improved efficiency.
- Reduce the curing time: The curing time of LSR can be reduced by increasing the curing temperature or using a faster curing agent. However, it’s essential to maintain the quality of the final product while reducing the curing time.
Cost-Effective Manufacturing
Liquid silicone rubber (LSR) injection molding is a popular manufacturing process for producing high-quality silicone products. However, the cost of LSR injection molding can concern manufacturers, mainly when producing large quantities. Here are some ways to make LSR injection molding more cost-effective:
- Optimize the design of the product: The product’s design can significantly impact the cost of LSR injection molding. By optimizing the design, manufacturers can reduce the amount of material used, which can lower the overall cost of production. Additionally, simplifying the procedure can reduce the complexity of the mold, reducing tooling costs.
- Use automated processes: Using automated processes can improve the efficiency of LSR injection molding and reduce labor costs. Automated processes such as robotic handling and automatic material feeding can reduce the cycle time and improve overall productivity.
- Use a high-quality mold: A high-quality mold can improve the efficiency of LSR injection molding and reduce waste. Using a durable and high-precision mold can reduce the need for frequent repairs or replacements, saving money in the long run.
- Optimize the production process: Optimizing the production process can reduce waste and improve efficiency, reducing costs. This can include optimizing the injection moldings parameters, such as the injection speed, temperature, and pressure, to minimize material waste and reduce cycle time.
- Reduce material waste: Reducing material waste can significantly reduce the cost of LSR injection molding. This can be achieved by using a precision metering system to control the material used, ensuring that the mold is adequately designed and optimized to minimize excess material, and recycling extra material for future use.
High-Quality Surface Finishes
Liquid silicone rubber (LSR) injection molding is a popular manufacturing process for producing high-quality silicone products with excellent properties such as temperature resistance, chemical resistance, and biocompatibility. In addition to these properties, achieving a high-quality surface finish is essential for many applications. Here are some ways to achieve high-quality surface finishes in LSR injection molding:
- Use a high-quality mold: A high-quality mold is crucial for achieving a high-quality surface finish. The mold should be made from high-quality materials and have a smooth surface finish. Additionally, the mold should be designed with proper venting to prevent air bubbles from forming, which can negatively impact the surface finish.
- Use a high-quality LSR material: Using a high-quality LSR material can also improve the surface finish. High-quality LSR materials are formulated to have a low viscosity, which can improve the flow of the material and reduce the appearance of flow marks and other imperfections.
- Optimize the injection molding parameters: Optimizing the parameters such as temperature, injection speed, and pressure can also improve the surface finish. The injection speed should be optimized to prevent any material buildup or streaking. The temperature and pressure should also be carefully controlled to avoid material degradation or warping.
- Use post-molding processes: Post-molding processes such as trimming, polishing, and coating can also improve the surface finish of LSR products. Trim can remove any flash or excess material from the part. Polishing can smooth out any imperfections on the surface. The coating can provide an additional layer of protection and improve the character’s appearance.
- Conduct regular maintenance of the injection molding machine: Regular maintenance is essential to ensure consistent and high-quality production. The device should be cleaned regularly to prevent contamination, and the molds should be checked for signs of wear or damage.
LSR Injection Molding for Medical Applications
LSR injection molding is a manufacturing process that involves injecting liquid silicone rubber (LSR) into a mold to create a final product. This process is widely used in the medical industry due to the unique properties of LSR, which make it an ideal material for medical applications.
LSR is a biocompatible and hypoallergenic material that contains no harmful chemicals, making it safe for medical devices and implants. It is also resistant to bacteria growth and easy to sterilize, which is crucial in medical settings where cleanliness and infection control are paramount.
LSR injection molding is an exact and efficient process that allows for creation of complex and intricate medical parts with tight tolerances. This is important in medical applications where precision and accuracy are critical, such as in manufacturing implantable devices like catheters, pacemaker components, and artificial joints.
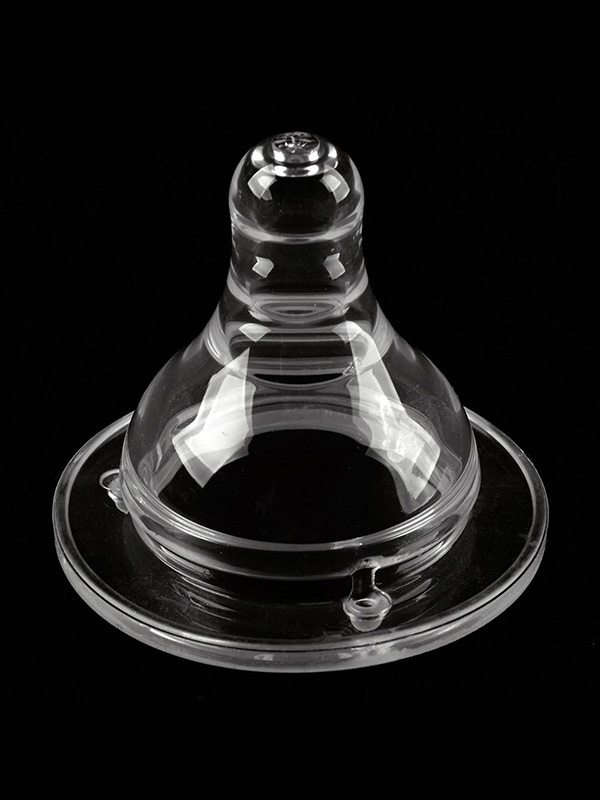
In addition to its biocompatibility and precision, LSR has excellent mechanical properties making it a suitable material for medical applications. LSR is resistant to wear and tear, withstands extreme temperatures, and has excellent electrical insulation properties. These properties make LSR a popular material for a wide range of medical applications, including:
- Catheters and tubing: LSR is often used to manufacture catheters and tubing due to its biocompatibility, flexibility, and kink resistance.
- Implantable devices: LSR is commonly used to produce implantable devices such as artificial joints, pacemaker components, and surgical tools due to its durability and biocompatibility.
- Medical seals and gaskets: LSR is often used to manufacture them due to its resistance to temperature extremes and ability to maintain its properties over time.
LSR injection molding is a highly versatile and efficient process for manufacturing medical devices and components. Its unique properties make it an ideal material for a wide range of medical applications, and its precision and accuracy ensure that products meet the highest standards of quality and safety.
Use of LSR in the Automotive Industry
Liquid Silicone Rubber (LSR) is increasingly used in the automotive industry for a wide range of applications due to the unique properties that make it an ideal material for automotive parts. LSR is a synthetic elastomer formed through injection molding, allowing for high precision and accuracy in manufacturing complex and intricate automotive parts.
LSR has excellent mechanical properties, making it suitable for automotive parts requiring durability, high-temperature resistance, and long service life. LSR is resistant to abrasion, wear, and tear, which makes it ideal for automotive parts that experience constant friction, such as seals, gaskets, and O-rings.
One of the most significant advantages of LSR in the automotive industry is its ability to withstand extreme temperature variations. LSR can operate efficiently in high- and low-temperature environments, making it an ideal material for automotive parts exposed to high temperatures, such as engine components, exhaust systems, and turbocharger hoses.
Another critical benefit of LSR in the automotive industry is its ability to provide an excellent seal against fluids and gases. LSR is a highly resistant material that provides a reliable seal, even under high pressure, making it ideal for use in automotive gaskets and seals.
LSR also has excellent electrical insulation properties, which make it ideal for use in electrical components in the automotive industry, such as connectors, sensors, and ignition systems. LSR can withstand high electrical voltages and has a low risk of electrical arcing or short circuits, making it a reliable material for electrical applications.
Overall, LSR has many advantages that make it an ideal material for automotive parts, including durability, high-temperature resistance, excellent sealing properties, and electrical insulation. The use of LSR in the automotive industry is expected to grow in the coming years as manufacturers seek to improve the reliability, safety, and performance of their products while reducing costs and improving production efficiency.
Electronics Industry Applications of LSR
Liquid Silicone Rubber (LSR) is a widely used material in the electronics industry due to its excellent thermal stability, chemical resistance, and electrical insulation properties. It is used in various applications such as encapsulation, sealing, and potting of electronic components.
One of the primary applications of LSR in the electronics industry is in the encapsulation of electronic components, such as integrated circuits (ICs), sensors, and connectors. Encapsulation protects these components from moisture, dust, and other contaminants, which can cause corrosion and degrade performance. LSR is an ideal material for encapsulation due to its low viscosity, high tear strength, and excellent adhesion to various substrates. It also offers good dielectric properties, which are essential in electrical applications.
LSR also seals electronic components to prevent moisture ingress and other contaminants. The material can be molded into custom shapes and sizes to fit various electronic components. LSR seals are often used in harsh environments, such as marine and automotive applications, where they must withstand extreme temperatures and chemical exposure.
Potting is another critical application of LSR in the electronics industry. Potting involves filling a cavity around a component with a liquid material to protect it from environmental factors such as shock, vibration, and moisture. LSR is an ideal material for potting due to its low viscosity, which allows it to flow easily around complex shapes, and its high thermal stability, which ensures that the component remains protected at high temperatures.
LSR is also used to manufacture keypads and buttons, standard components in electronic devices such as remote controls, calculators, and keyboards. The highly customizable material can be molded into various shapes and sizes with different textures and hardness levels.
Aerospace Industry Applications of LSR
Liquid Silicone Rubber (LSR) is a widely used material in the aerospace industry due to its unique properties, such as high thermal stability, chemical resistance, and excellent mechanical properties. It is used in various aerospace applications such as sealing, bonding, and potting electronic components and for fabricating gaskets, O-rings, and other critical details.
One of the primary applications of LSR in the aerospace industry is sealing and bonding aircraft components. The material can be easily molded into complex shapes and sizes, making it ideal for packing and connecting fuel tanks, engine components, and electrical systems. LSR provides excellent adhesion to various substrates and can withstand harsh environmental conditions, such as extreme temperatures and chemical exposure.
LSR is also used in the potting of electronic components in aerospace applications. The material’s low viscosity allows it to flow easily around complex shapes, providing excellent protection for sensitive electronic components against vibration, shock, and environmental factors such as humidity and temperature changes.
Another critical application of LSR in the aerospace industry is manufacturing gaskets, O-rings, and other sealing components. LSR can be customized to meet specific requirements, such as temperature and pressure resistance, and is often used in high-performance applications where traditional rubber materials may not be suitable.
In addition to sealing and bonding applications, LSR is also used to fabricate aircraft lighting components, such as lenses and diffusers. The material’s optical properties make it an ideal choice for these applications, providing excellent light transmission, while its mechanical properties ensure durability and resistance to environmental factors such as UV radiation and temperature fluctuations.
Food-Grade LSR Injection Molding
Food-Grade Liquid Silicone Rubber (LSR) is a specialized material used in the injection molding products that come into contact with food, such as kitchen utensils, baby products, and food packaging. It is a high-purity material that meets stringent regulatory standards for food safety.
One of the primary benefits of Food-Grade LSR is its resistance to high temperatures, which makes it ideal for use in kitchen utensils such as spatulas, spoons, and baking molds. It can withstand temperatures up to 450°F (232°C), making it safe for cooking and baking applications.
Food-Grade LSR is also used to manufacture baby products, such as pacifiers and bottle nipples. These products must meet strict safety standards to ensure they are safe for infants. LSR is an ideal material for these applications due to its excellent biocompatibility, softness, and durability.
Another important application of Food-Grade LSR is in food packaging. The material can be molded into various shapes and sizes, making it ideal for manufacturing food storage containers, ice cube trays, and other products. LSR is resistant to chemicals and has excellent sealing properties, ensuring that the contents of the package remain fresh and free from contamination.
Food-Grade LSR is also used to manufacture medical products such as dental impression materials and prosthetic devices. The material’s biocompatibility, durability, and ability to replicate fine details make it an ideal choice for these applications.
Overall, Food-Grade LSR is a specialized material ideal for manufacturing products that come into contact with food, such as kitchen utensils, baby products, and food packaging. Its resistance to high temperatures, biocompatibility, and excellent sealing properties make it an ideal material for these applications. The material is also used to manufacture medical products due to its biocompatibility and ability to replicate fine details.
LSR Injection Molding for Baby Products
LSR (Liquid Silicone Rubber) injection molding is a manufacturing process used to produce a wide range of products made of silicone rubber. One of the most popular applications of LSR injection molding is in producing baby products, and this is due to the many benefits that LSR offers for baby products, including safety, durability, and ease of cleaning.
LSR injection molding involves injecting a liquid silicone rubber into a mold, which is then cured and solidified. This process allows for the creation of complex shapes and designs and the use of different colors and textures. The result is a finished product that is soft, flexible, and resistant to heat and chemicals.
One of the main advantages of LSR injection molding for baby products is safety. Silicone rubber is non-toxic, hypoallergenic, and free of harmful chemicals such as BPA, phthalates, and PVC. This makes it a popular choice for products that come into contact with babies, such as pacifiers, teething rings, and bottle nipples. LSR injection molding also allows for the creation of products free of sharp edges or seams that can harm a baby’s delicate skin.
Durability is another benefit of LSR injection molding. Silicone rubber is resistant to wear and tear, making it ideal for products used frequently or subjected to rough handlings, such as pacifiers or teething rings. The soft and flexible nature of the material also makes it less likely to break or crack when dropped, reducing the risk of injury to a baby.
LSR injection molding also offers easy cleaning, which is essential for baby products that must be sanitized frequently. Silicone rubber is non-porous and can be easily cleaned with soap and water or put in the dishwasher for thorough cleaning.
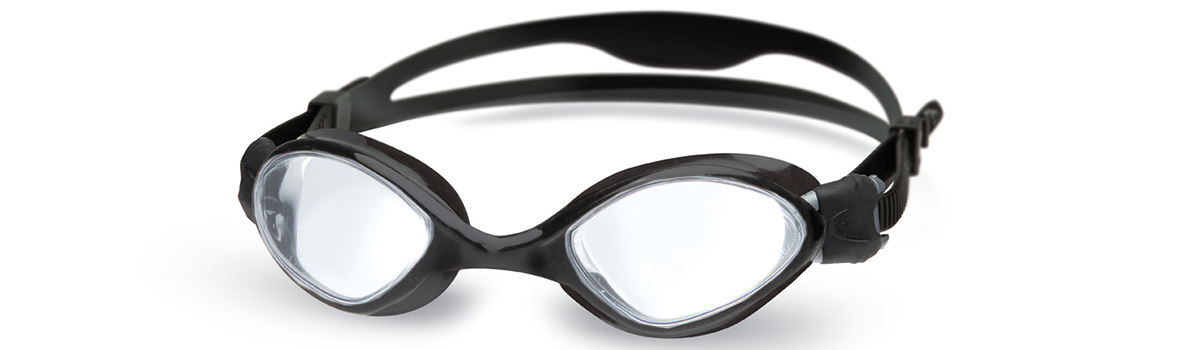
LSR Injection Molding for Sporting Goods
LSR (Liquid Silicone Rubber) injection molding is a popular manufacturing process for various products, including sporting goods. LSR injection molding offers several benefits for producing sporting goods, including flexibility, durability, and resistance to extreme temperatures and environmental conditions.
One of the main advantages of LSR injection molding for sporting goods is flexibility. Silicone rubber is a soft, pliable material that can be molded into various shapes and designs. This allows for creating of sporting goods that are comfortable to use and conform to the body, such as protective gear or grips for equipment.
Durability is another benefit of LSR injection molding for sporting goods. Silicone rubber is resistant to wear and tear, making it ideal for products used frequently or subjected to rough handlings, such as balls, paddles, or rackets. The material can also withstand extreme temperatures and environmental conditions, such as exposure to sunlight or water, without degrading or deteriorating.
LSR injection molding also allows for creating of products resistant to impact and abrasion. The material’s high tear strength and elongation at break make it ideal for producing protective gear such as helmet liners, mouthguards, and shin guards. In addition, LSR injection molding allows for the creation of non-slip surfaces or grips for equipment, such as handles or racquet grips.
Another benefit of LSR injection molding for sporting goods is creating products that are easy to clean and maintain. Silicone rubber is non-porous and can be easily wiped clean with a damp cloth or washed with soap and water. This makes it an ideal material for frequently used products, such as gym equipment or yoga mats.
LSR Injection Molding for Household Goods
LSR injection molding is a manufacturing process that uses Liquid Silicone Rubber (LSR) to create molded parts. This process is ideal for producing high-quality household goods such as kitchen utensils, baby products, and bathroom accessories. LSR injection molding offers several benefits, including high precision, consistency, and durability, making it an excellent choice for household products that require tight tolerances and superior performance.
The LSR injection molding process involves injecting a liquid silicone material into a mold. The mold is then heated, and the liquid silicone material cures and solidifies into the desired shape. The process is highly automated, allowing for consistent parts production with tight tolerances and excellent surface finishes. This process also allows for producing complex geometries that would be difficult or impossible to achieve with other molding processes.
Household goods commonly produced using LSR injection molding include kitchen utensils such as spatulas and cooking spoons, baby products such as pacifiers and bottle nipples, and bathroom accessories such as showerheads and toothbrushes. These products require precise molding to meet safety and performance standards, and LSR injection molding offers the precision and consistency needed to produce high-quality household goods that meet these standards.
One of the primary benefits of LSR injection molding for household goods is its durability. LSR materials are resistant to high temperatures, UV radiation, and chemicals, making them ideal for long-term durability products. Additionally, LSR materials are hypoallergenic, making them safe for use in baby products and other household goods that come into contact with the skin.
Another benefit of LSR injection molding is its ability to produce parts with excellent surface finishes. The process allows for creating features with a smooth, glossy finish resistant to scratches and scuffs. This makes LSR injection molding a perfect choice for producing household goods that require an attractive appearance, such as kitchen utensils and bathroom accessories.
Comparison with Other Types of Rubber Molding
LSR (Liquid Silicone Rubber) injection molding is a popular manufacturing process for producing various rubber products, and it offers several advantages over other types of rubber molding processes. Here are some comparisons between LSR injection molding and different types of rubber molding:
- Compression Molding: Compression molding is a standard process for producing large parts or parts with complex shapes. In compression molding, a pre-measured amount of rubber is placed in a heated mold, and pressure is applied until the rubber is cured. Compared to LSR injection molding, compression molding is a slower process and can result in variations in part dimensions due to uneven pressure distribution. LSR injection molding, on the other hand, allows for precise control of part dimensions and can produce complex shapes with tight tolerances.
- Transfer Molding: Transfer molding is similar to compression molding but involves using a plunger to transfer the rubber from the injection pot to the mold. Transfer molding can produce parts with high accuracy and is suitable for making medium-sized parts. However, it can be slower and more expensive than LSR injection molding.
- Injection Molding: Injection molding is a process that involves injecting molten rubber into a mold at high pressure. Injection molding can produce parts quickly and accurately, but it may not be suitable for making parts with intricate designs or details. Compared to injection molding, LSR injection molding allows for the creation of parts with precise details and intricate designs and patterns.
- Extrusion: Extrusion is a process used to produce parts with a continuous cross-sectional profile, such as hoses, seals, and gaskets. Extrusion is a fast and cost-effective process, but it may not be suitable for producing complex shapes or parts with tight tolerances. LSR injection molding, on the other hand, can have parts with complex shapes and tight tolerances, making it ideal for producing products such as medical devices, automotive components, and consumer goods.
Design Considerations for LSR Injection Molding
Several vital considerations must be considered when designing parts for LSR injection molding to ensure a successful manufacturing process. These considerations include material selection, mold design, part geometry, and post-molding operations.
Material selection is a critical consideration when designing parts for LSR injection molding. Liquid silicone rubber materials come in various durometers, viscosities, and colors, and selecting the appropriate material is essential for achieving the desired properties of the final product. The material selection should consider the application requirements, such as temperature resistance, chemical resistance, and durability.
Mold design is another critical consideration for LSR injection molding. The mold design should be optimized to produce the desired part geometry and consider material flow, cooling, and ejection. The mold should be designed with proper gating and venting systems and have sufficient cavities to achieve a high production rate.
Part geometry is also essential when designing parts for LSR injection molding. The part geometry should be optimized to achieve the final product’s desired mechanical properties and aesthetics. This can involve using draft angles to facilitate ejection from the mold, using ribs to increase stiffness, and placing gating and venting systems to optimize material flow.
Post-molding operations should also be considered when designing parts for LSR injection molding. Post-molding operations may include trimming, deburring, and secondary assembly operations. These operations should be optimized to minimize waste and reduce labor costs.
Other design considerations for LSR injection molding may include the use of undercuts, the placement of ejector pins, and the use of parting lines. These factors must be considered during the design process to ensure that the final product meets the desired specifications and can be manufactured efficiently.
Environmental and Sustainability Benefits of LSR Injection Molding
LSR injection molding offers several environmental and sustainability benefits over traditional manufacturing processes, making it an attractive option for companies looking to reduce their ecological footprint.
One of the primary environmental benefits of LSR injection molding is its low waste generation. The process produces very little waste material, as the liquid silicone rubber is injected directly into the mold and cured to form the desired shape. This contrasts with other manufacturing processes, such as machining or casting, which generate significant scrap material.
LSR injection molding also has the potential to reduce energy consumption and greenhouse gas emissions. The process can be highly automated, reducing the need for manual labor and lowering energy consumption. LSR injection molding is a low-temperature process that requires less energy than other molding processes, such as injection molding or blow molding. This can result in significant energy savings and reduced greenhouse gas emissions.
Another sustainability benefit of LSR injection molding is the potential to use recycled materials. LSR materials can be recycled and reused, reducing the need for new materials and reducing waste generation. Additionally, the long lifespan of LSR products means they can be reused or repurposed, further reducing waste and extending the product lifecycle.
LSR injection molding can also reduce the use of harmful chemicals in manufacturing. LSR materials are generally free of toxic chemicals such as phthalates, BPA, and PVC, making them safer for workers and consumers. Additionally, the low-temperature process used in LSR injection molding does not require harmful solvents or other chemicals.
Future of LSR Injection Molding
The future of LSR injection molding is bright, with the process offering several advantages over traditional manufacturing methods. LSR injection molding will become even more efficient, cost-effective, and environmentally friendly as technology advances.
One of the most promising areas for the future of LSR injection molding is the use of additive manufacturing techniques. Additive manufacturing, also known as 3D printing, allows for creation of complex geometries and customized parts that would be difficult or impossible to produce using traditional manufacturing methods. As the technology improves, LSR injection molding will become more integrated with additive manufacturing, allowing for even more advanced and innovative products to be produced.
Another area of future development for LSR injection molding is using advanced materials. As new materials are developed, LSR injection molding can take advantage of their unique properties, such as improved durability, temperature resistance, or biocompatibility. This will allow for even more specialized products, such as medical implants or high-performance industrial components.
The continued integration of automation and robotics into LSR injection molding processes is also likely to be a significant trend in the future. Automation can improve efficiency, reduce labor costs, and improve the consistency and quality of the final product. As technology improves, LSR injection molding will become even more automated, with robotics and artificial intelligence playing a more significant role in manufacturing.
Finally, sustainability and environmental responsibility will likely continue to be significant drivers in the future of LSR injection molding. As consumers and businesses increasingly focus on reducing waste and minimizing their ecological impact, LSR injection molding will become an even more attractive option for producing high-quality products with a low environmental footprint. The development of more sustainable materials, recycling and repurposing of materials, and using renewable energy sources are likely to play a more significant role in the future of LSR injection molding.
Conclusion:
In conclusion, LSR injection molding is a reliable and efficient manufacturing process with numerous benefits for various industries. LSR is a versatile material with distinctive performance characteristics, making it ideal for multiple applications. With continued advances in LSR technology and increased demand for sustainable manufacturing practices, the future of LSR injection molding is bright.