Two Color Injection Molding
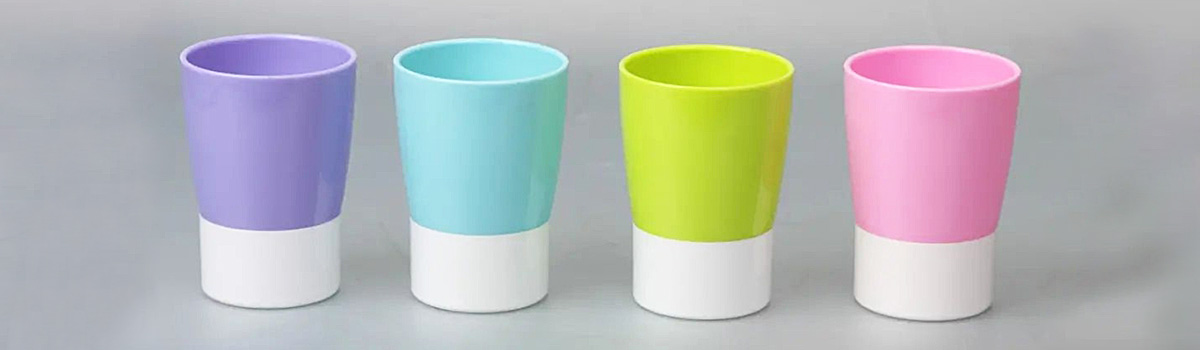
Two-color injection molding, or two-shot injection molding, is a manufacturing process used to produce plastic parts with two different colors or materials. This process involves injecting two other materials into a single mold to create a role with a two-tone finish or different functional properties. Two-color injection molding has many applications in various industries, including automotive, medical, and consumer products. This article will delve into the details of two-color injection molding, its advantages, limitations, and applications.
Two-color injection molding process
The two-color injection molding process involves two separate injections of different colored resins. The first injection molds the part’s base, while the second injection molds the final shape and color. The two injections are typically performed in the same machine, using two different barrels and nozzles.
You can break down the process into the following steps:
- The mold is closed, and the first resin injection is injected into the mold cavity to create the part’s base.
- The operator opens the mold and rotates or moves the region to a second station.
- The second resin injection is injected into the mold cavity, creating the final shape and color of the part.
- The operator opens the mold and ejects the part.
The two-color injection molding process has several advantages, including:
- Increased efficiency:Two-color injection molding eliminates the need for secondary operations, such as painting or assembly, which can save time and reduce costs.
- Improved aesthetics: The ability to create parts with multiple colors and intricate designs can improve the aesthetics of the final product, making it more visually appealing to consumers.
- Improved functionality:The two-color injection molding process can also enhance the final product’s functionality, as it allows using different materials for other parts.
There are also some challenges associated with the two-color injection molding process, such as:
- Design complexity: The process requires a complex mold design, making it more challenging to manufacture and maintain.
- Material compatibility: The two different resins used in the process must be compatible, or they may not adhere properly, leading to defects in the final product.
- Cost:The two-color injection molding process can be more expensive than traditional molding processes due to the complexity of the mold and the additional equipment required.
Materials used in two-color injection molding
Choosing suitable materials for two-color injection molding is crucial to create high-quality and functional parts. This blog post will discuss the materials commonly used in two-color injection molding.
Thermoplastic elastomers (TPE)
TPEs are famous for two-color injection molding because they are soft, flexible, and adhere well to other materials. They are also resistant to chemicals and have good weather ability. Manufacturers often use TPEs for grips, handles, and other parts that require a comfortable, non-slip surface.
Thermoplastic polyurethane (TPU)
TPU is another popular material for two-color injection molding because of its high flexibility and durability. TPU can withstand repeated bending and flexing, making it ideal for parts such as phone cases, medical devices, and sports equipment. It is also resistant to oils and chemicals.
Acrylonitrile butadiene styrene (ABS)
Manufacturers commonly use ABS, a rigid thermoplastic, in two-color injection molding. It has excellent mechanical properties, high impact resistance, and can adhere well to other materials. Manufacturers often use ABS for automotive parts, household appliances, and electronic devices.
Polypropylene (PP)
PP is a lightweight and rigid thermoplastic commonly used in two-color injection molding. It exhibits good chemical and fatigue resistance and allows for easy molding into various shapes. Manufacturers often use PP for containers, packaging, and automotive parts.
Polycarbonate (PC)
PC is a transparent thermoplastic commonly used in two-color injection molding for applications such as medical devices, automotive parts, and electronic components. It has excellent impact resistance, high optical clarity, and can withstand high temperatures. Manufacturers often use PC for lenses, light guides, and covers.
Polyamide (PA)
PA, known as nylon, is a versatile thermoplastic commonly used in two-color injection molding. It exhibits good mechanical properties, excellent resistance to abrasion and chemicals, and allows for easy molding into complex shapes. Manufacturers often use PA for gears, bearings, and structural parts.
Advantages of two-color injection molding
Injection molding is a widely used manufacturing process in which plastic materials are melted and injected into a mold to create complex and precise parts. One of the variations of this process is two-color injection molding, which allows for creation of parts with two different colors or materials in a single molding cycle. This blog post will discuss the advantages of two-color injection molding.
Advantages
- Cost Savings: One of the significant advantages of two-color injection molding is cost savings. Instead of creating and assembling two parts, this process begins with a part with two colors or materials in one molding cycle. Reducing the need for additional assembly tasks results in high cost and time savings.
- Improved Design Flexibility:Two-color injection molding provides design flexibility that is impossible with other manufacturing processes. Creating a part with two different materials or colors enables designers to achieve more complex and unique designs that other techniques cannot accomplish.
- Enhanced Product Aesthetics: Two-color injection molding provides enhanced product aesthetics by allowing for the creation of parts with different colors or materials. Products that require visual appeal, such as consumer electronics, medical devices, and automotive parts, can significantly benefit from this feature.
- Increased Durability: Two-color injection molding can also increase the durability of a part. By using two different materials with different properties, the region can have increased strength, flexibility, or other desired properties. This feature is convenient for products exposed to harsh conditions or experiencing frequent use.
- Improved Manufacturing Efficiency: Two-color injection molding can also improve manufacturing efficiency by reducing the number of steps required in the production process. By eliminating the need for additional assembly operations, two-color injection molding can reduce the time and labor required to produce a part.
Limitations of two-color injection molding
Two-color injection molding is a popular manufacturing process that creates complex and aesthetically pleasing parts with two or more colors. While this process has many advantages, there are also some limitations to consider when deciding if it is the right choice for your project.
One limitation of two-color injection molding is the cost. The equipment required for this process is often more expensive than traditional injection molding equipment. Additionally, the process requires more time and labor, which can drive up costs.
Another area for improvement is the complexity of the design. Two-color injection molding can create complex designs with multiple colors, but it may only be suitable for some procedures. Designers must carefully plan the structure to prevent color bleeding and ensure a high-quality final product.
Here are some other limitations to consider:
- Limited material selection:Two-color injection molding is typically limited to specific materials, such as thermoplastics. Limiting the options can affect the final product’s quality.
- Limited production volume:Manufacturers often use two-color injection molding for smaller production runs. Traditional injection molding is more cost-effective if many parts are needed.
- Difficulty with part alignment: When creating parts with multiple colors, it can be challenging to align the colors correctly. Achieving success in this task necessitates meticulous planning and accurate management of the injection molding process.
- Longer cycle times: Two-color injection molding often requires longer cycles than traditional injection molding. Limiting the production rate can lead to higher costs for the final product.
Despite these limitations, two-color injection molding can be an excellent choice for specific projects. The ability to create complex designs with multiple colors can be a significant advantage, especially in industries such as automotive, consumer goods, and medical devices.
Working with an experienced manufacturer who understands the process and its limitations is essential for the success of a two-color injection molding project. They can help with design, material selection, and injection molding to ensure the final product meets all requirements.
Design Considerations for two-color injection Molding
One important consideration is the design of the part itself. Designers must carefully plan the strategy to prevent color bleeding and ensure the final product is high quality. Here are some other design considerations to keep in mind:
- Wall thickness: The part’s thickness can affect the final product’s quality. Thicker walls can be more difficult to mold, resulting in uneven color distribution. It is essential to balance the walls’ thickness with the part’s overall design.
- Parting line: The parting line is where the two halves of the mold meet. It is essential to carefully consider the location of the parting line to ensure that it does not affect the design of the part or the quality of the final product.
- Draft angles: Draft angles assist in helping parts release from the mold. Including proper draft angles in the design is essential to ensure easy removal of the region from the mold without causing damage.
- Texture:The texture of the part can affect the final appearance of the region. It is essential to consider the surface of the role and how it will interact with the two colors during the injection molding process.
Another consideration is the selection of materials. Two-color injection molding is typically limited to specific materials, such as thermoplastics. Selecting materials that can handle the injection molding process’s stresses and provide the final product’s desired appearance and functionality is essential.
Here are some additional considerations for material selection:
- Color compatibility:To achieve optimal results, designers must actively select colors that demonstrate compatibility with each other and the material used. To ensure a consistent appearance of the final product, preventing color bleeding is crucial.
- Material compatibility:The two materials used in the injection molding process must be compatible. Following this process can avoid problems of adhesion and guarantee an excellent result.
- Material properties:The properties of the materials used in the injection molding process can affect the final product’s functionality. It is crucial to consider the properties of each material and how they will interact during the injection molding process.
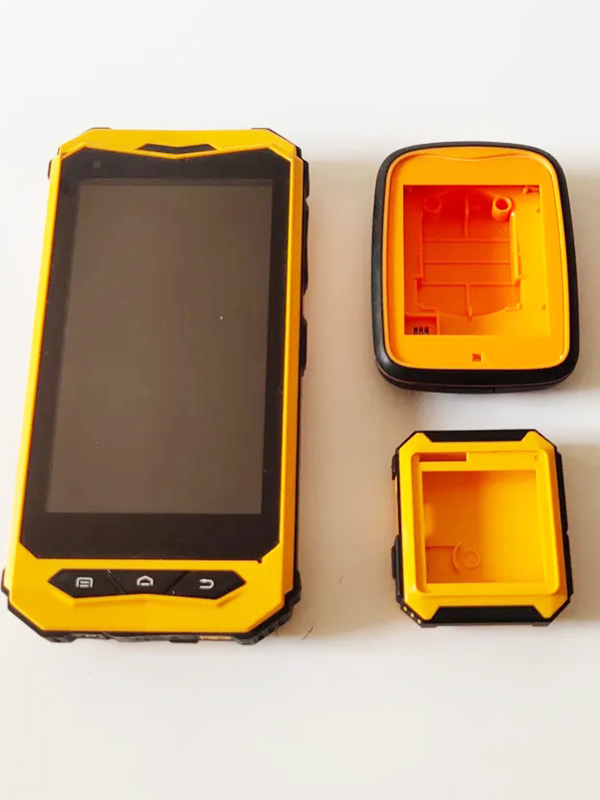
Equipment and tooling for two-color injection molding
Two-color injection molding is a manufacturing process that allows for creation of parts with two or more colors. This process requires specialized equipment and tooling to ensure the project’s success. This blog post will discuss the necessary equipment and tooling for two-color injection molding.
Equipment
- Two-shot injection molding machine: manufacturers specifically design this machine for two-color injection molding. It has two barrels and two nozzles, allowing the injection of two different materials into the same mold. The device also has specialized software that controls the injection of the two materials.
- Mold: The mold is the most critical component of the two-color injection molding process. Designers must ensure that the design allows for the injection of two different materials and precise alignment to prevent color bleeding between them. The mold is typically made from steel and can be quite expensive.
- Robotics: Robotics are often used in two-color injection molding to automate the process and improve efficiency. Robotics can move parts between the injection molding machine and the assembly line or remove the elements from the mold.
Tooling
- Core pins: Core pins are used in two-color injection molding to create voids or holes in the final part. They are typically made from steel and must be precisely aligned to ensure that the last part is high quality.
- Slide assemblies:Manufacturers use slide assemblies to create undercuts or other complex features in the final part. They are typically made from steel and can be quite tricky.
- Hot runner system: Manufacturers use a hot runner system to control the flow of the two different materials in the mold. It consists of a manifold, nozzles, and heaters that keep the materials at the correct temperature.
- Ejector pins: Manufacturers use ejector pins to remove the final part from the mold. Typically, manufacturers produce them from steel and align them with precision to ensure the region does not sustain any damage during ejection.
Working with an experienced manufacturer when using two-color injection molding is crucial. The manufacturer should have the equipment and tooling necessary to produce high-quality parts and be able to guide the region’s design, material selection, and injection molding process.
Differences between two-color injection molding and over molding
Two-color injection and over-molding are processes used to produce parts with multiple materials or colors. While these processes share some similarities, they also have several differences. This blog post will discuss the differences between two-color injection molding and over-molding.
Two-Color Injection Molding
- Two-color injection molding involves injecting two different materials or colors into a single mold cavity to create a part with two or more colors.
- Operators perform the injection process by injecting the two materials in a specific order. They inject the second material after the first material has partially cooled and solidified.
- The process requires specialized equipment and tooling, including a two-shot injection molding machine and a mold designed for two-color injection molding.
- Manufacturers often utilize two-color injection molding to produce parts with complex shapes or designs, such as automotive components and consumer products.
Overmolding
- Overmolding involves molding one material over another material or substrate to create a part with multiple layers or components.
- The process typically involves molding a base part or substrate, then molding a second material over the base part to create a finished piece with multiple layers or components.
- The process requires specialized equipment and tooling, including a multi-shot injection molding machine and a mold designed for over-molding.
- Manufacturers often employ over-molding to produce parts with improved grips, comforts, or durability, such as handles for power tools and consumer products.
Differences
- Materials: Typically, two-color injection molding involves using two different materials, while over-molding involves using one material as the base and a second as the overmold.
- Order of injection:In two-color injection molding, operators inject the materials in a specific order, whereas in over-molding, they first mold the base part and then add the overmold.
- Equipment and tooling: Two-color injection molding and over-molding require different equipment and tooling, with two-color injection molding requiring a two-shot injection molding machine and a mold designed for two-color injection molding, and over-molding requiring a multi-shot injection molding machine and a mold designed for over-molding.
- Applications:Manufacturers often use two-color injection molding to produce parts with complex shapes or designs, while they frequently employ over-molding to create regions with improved grip, comfort, or durability.
Applications of two-color injection molding in the automotive industry
Two-color injection molding is a versatile manufacturing process that has gained popularity in the automotive industry due to its ability to produce high-quality, multi-colored parts with complex designs. This blog post will discuss some of the applications of two-color injection molding in the automotive industry.
- Interior components:Manufacturers widely use two-color injection molding to produce internal automobile components, such as instrument panels, door panels, and center consoles. These components often require multiple colors or materials to achieve a premium appearance and enhance the vehicle’s overall aesthetic.
- Exterior components: Manufacturers also utilize two-color injection molding to produce external automobile components, such as front grilles, headlamp bezels, and tail lamp lenses. These components require high precision and durability to withstand harsh outdoor conditions, and two-color injection molding offers the perfect solution to achieve both.
- Functional components: Manufacturers can also use two-color injection molding to produce active automobile ingredients, such as air vents, cup holders, and knobs. These components require a combination of materials with different properties, such as rigidity and flexibility, to perform their functions effectively. Two-color injection molding allows for creation of complex shapes and designs while incorporating other materials to achieve the desired properties.
- Branding and customization: Two-color injection molding is an excellent tool for branding and customization in the automotive industry. By incorporating logos or unique designs into parts, manufacturers can enhance the brand identity of their vehicles and create a premium look and feel. Additionally, two-color injection molding allows for creating custom features unique to each vehicle, providing a personalized touch for customers.
Advantages of two-color injection molding in the automotive industry
- Offers design flexibility to produce complex shapes and designs
- Enables the use of multiple materials and colors in a single part
- Reduces assembly time and cost by combining multiple parts into one
- Enhances the overall appearance and aesthetic of the vehicle
- Improves functionality by incorporating materials with different properties
Applications of two-color injection molding in the medical industry
Two-color injection molding is a versatile manufacturing process with various applications in various industries, including the medical industry. This blog post will discuss some of the applications of two-color injection molding in the medical industry.
- Medical devices:Manufacturers widely utilize two-color injection molding to produce medical devices such as syringes, inhalers, and blood glucose meters. These devices require precise and accurate measurements and often need multiple materials to achieve the desired functionality.
- Implants: Manufacturers also employ two-color injection molding to produce medical implants such as dental crowns, orthopedic implants, and hearing aids. These implants require high precision and durability, and two-color injection molding allows for creation of complex shapes and designs while incorporating different materials to achieve the desired properties.
- Diagnostic equipment: Two-color injection molding can also produce diagnostic equipment such as test kits and medical imaging devices. These components require a combination of materials with different properties, such as transparency and rigidity, to perform their functions effectively.
- Drug delivery systems:Two-color injection molding is ideal for producing drug delivery systems such as inhalers, syringes, and insulin pens. These systems require high precision and accuracy to deliver the correct medication dosage, and two-color injection molding enables the creation of complex shapes and designs while incorporating different materials to achieve the desired properties.
Advantages of two-color injection molding in the medical industry
- Offers design flexibility to produce complex shapes and designs
- Enables the use of multiple materials and colors in a single part
- Reduces assembly time and cost by combining multiple parts into one
- Improves functionality by incorporating materials with different properties
- Enhances the overall safety and efficacy of medical devices
Applications of two-color injection molding in the consumer products industry
This process involves injecting two different materials into the same mold, creating a single part with two colors or fabrics. The consumer products industry has significantly benefited from this technology, as it allows for the creation of more visually appealing, functional, and cost-effective products. This blog post will explore the applications of two-color injection molding in the consumer products industry.
- Aesthetically pleasing designs: Two-color injection molding allows manufacturers to produce products with visually appealing designs that stand out on the shelves. With the ability to combine two different colors or materials in a single molding cycle, manufacturers can create products with intricate designs and patterns, such as phone cases, gaming controllers, and household items. This technology also allows manufacturers to develop products with branding and logos embedded in the design, creating a unique and recognizable product.
- Enhanced functionality: Two-color injection molding can improve the functionality of products by allowing for the integration of multiple components into a single part. For example, a phone case can be designed with complex and soft material, providing protection and shock absorption. In addition, manufacturers can use two-color injection molding to create parts with over-molded grips, improving user comfort and grip on products such as toothbrushes, razors, and tools.
- Reduced production costs:Using two-color injection molding can lead to significant cost savings in the production of consumer products. By combining two materials into one part, manufacturers can eliminate additional assembly steps, reducing labor costs and the need for other equipment. This technology can also reduce material waste by using only the necessary material in production.
- Improved product durability: Two-color injection molding can enhance the durability and lifespan of consumer products by creating parts with multiple materials. For example, a water bottle can be designed with a hard outer shell and a soft, flexible inner lining, providing both durability and ease of use. This technology can also create products with anti-slip properties, such as kitchen utensils and bath mats.
- Customization options:Two-color injection molding allows for customization options previously not possible with traditional manufacturing processes. Manufacturers can create products with unique designs and colors, allowing consumers to personalize their products. For example, sports equipment such as golf clubs and tennis rackets can be designed with custom grip colors, providing a personalized touch to the product.
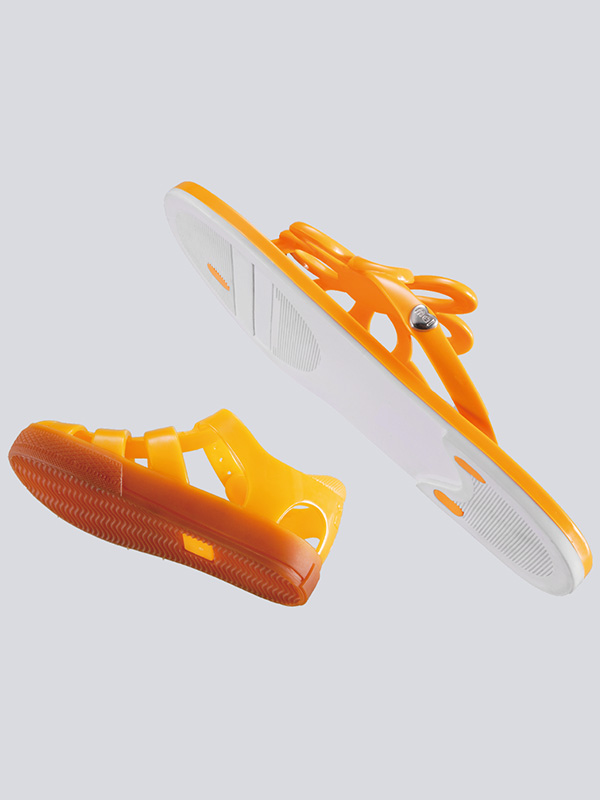
Cost considerations for two-color injection molding
Two-color injection molding is a process that allows for the creation of complex, multi-colored plastic parts in a single operation. This process involves using two different thermoplastic materials injected into a mold, each forming a distinct layer of the final product. While this process can produce impressive results, it has some unique cost considerations. This blog post will explore some of these cost considerations and how they can impact the overall cost of two-color injection molding.
Material Costs
The materials’ cost is one of the most apparent cost considerations for two-color injection molding. The process involves using two materials, and designers must carefully select both to ensure compatibility and quality. It’s essential to choose materials that will work well together and meet the required specifications of the final product. Depending on the materials selected, the cost of the raw materials can be a significant portion of the project’s overall cost.
Tooling Costs
The tooling cost required for two-color injection molding is another primary consideration. Two different materials will require two separate molds, and designers must design these molds to work together in creating the final product. The tooling cost for two-color injection molding is higher than traditional injection molding processes. Additionally, the complexity of the mold design will impact the tooling costs, as more complex molds will require more time and effort to produce.
Labor Costs
The labor costs associated with two-color injection molding can also be higher than traditional injection molding processes. This task requires a higher level of skill and accuracy to perform correctly. Additionally, the process can consume more time as operators must meticulously inject and mold the two materials to create the final product. Higher labor costs for the project may be the outcome.
Quality Control Costs
Quality control is essential to any manufacturing process and is significant for two-color injection molding. Because the process involves two different materials, ensuring the final product meets the required specifications. This essential can require additional testing and inspection, adding to the project’s overall cost.
Two-color injection molding can be a more expensive process than traditional injection molding. However, the benefits of this process – including the ability to create complex, multi-colored parts in a single operation – can make it a worthwhile investment. By carefully considering the cost factors outlined above, manufacturers can decide whether two-color injection molding is the right choice for their project.
Some of the critical cost considerations for two-color injection molding include the following:
- Material costs, as two different materials, will be used and must be carefully selected to meet the required specifications.
- Tooling costs increase because designers must design and produce two molds to create the final product.
- Labor costs, as the process requires more skill and experience on the operator’s part and can be more time-consuming.
- Quality control costs, such as additional testing and inspection, may be required to ensure that the final product meets the required specifications.
By carefully considering these cost factors, manufacturers can decide whether two-color injection molding is the right choice for their project.
Quality control in two-color injection molding
Quality control is essential to any manufacturing process and is significant for two-color injection molding. In this blog post, we will explore some of the key elements of quality control in two-color injection molding.
Material Selection
Material selection is one of the most critical aspects of quality control in two-color injection molding. Designers must carefully choose the materials to ensure compatibility and quality. It’s essential to select materials that will work well together and meet the required specifications of the final product. Designers must also choose the materials with an eye toward minimizing the risk of defects, such as warping or color bleeding.
Mold Design and Construction
The design and construction of the mold used in two-color injection molding are also critical to ensuring high quality. Designers must design and construct the mold precisely to ensure it can produce parts that meet the required specifications and work with the materials used. Designers must also create the mold to minimize the risk of defects, such as parting lines, flashing, or sink marks.
Injection Molding Process
The injection molding process is another crucial aspect of quality control in two-color injection molding. Operators must carefully control the process to inject the two different materials in the correct amounts and at the proper temperatures. The task demands the operator to have both precision and expertise at a high level. Any deviations from the appropriate process parameters can result in defects in the final product.
Inspection and Testing
Finally, inspection and testing are critical aspects of quality control in two-color injection molding. Operators must carefully inspect the final product to ensure that it meets the required specifications regarding its physical dimensions and its cosmetic appearance. This process may require visual inspection, measurement, and testing. Operators must identify and address defects before shipping the product to the customer.
Some of the key aspects of quality control in two-color injection molding include:
- Material selection to ensure compatibility and quality
- Mold design and construction to ensure precision and minimize defects
- Injection molding process control to ensure precise injection of materials
- Inspection and testing to ensure that the final product meets the required specifications.
Troubleshooting common issues in two-color injection molding
Like any manufacturing process, several issues can arise during two-color injection molding. In this blog post, we will discuss some of the most common problems manufacturers face during two-color injection molding and provide some tips for troubleshooting those issues.
Incomplete Fill
One of the most common issues manufacturers encounter during two-color injection molding is incomplete fill. When the substance injected into the mold does not fill it, it produces parts with missing or incomplete features. There are several possible causes of incomplete fill, including:
- Insufficient injection pressure
- Improper gate size or location
- Poor venting
- Inadequate or uneven heating of the mold
Manufacturers should actively adjust the injection pressure to troubleshoot this issue and ensure the mold fills completely. They should also actively check the gate size and location and ensure they adequately vent the mold. Additionally, operators should verify that they are heating the mold evenly and using appropriate materials for the mold and the process.
Warping
Another common issue that manufacturers face during two-color injection molding is warping. The part can become distorted or misshapen during or after the molding process, making it unsuitable for use or unattractive in appearance. There are several possible causes of warping, including:
- Uneven cooling
- Poor mold design
- Improper material selection
- Incorrect processing parameters
To troubleshoot warping, manufacturers should actively ensure they design the mold correctly and use the appropriate materials. They should also adjust the cooling process to ensure the part cools evenly and slowly. Finally, they should verify that the processing parameters are correct, including the temperature, pressure, and cycle time.
Color Bleeding
A third common issue manufacturers encounter during two-color injection molding is color bleeding. When the colors in a product blend together, it can make it look unattractive or even render it useless. There are several possible causes of color bleeding, including:
- Poor material selection
- Improper material mixing
- Incorrect processing parameters
- Poor mold design
To troubleshoot color bleeding, manufacturers should ensure that the materials used are compatible and appropriate. They should also actively verify that they mix the materials and set the processing parameters correctly. Finally, they should ensure that the mold design is suitable for the process and that the materials are injected in the proper order and at the correct times.
Comparison of two-color injection molding with other molding processes
While two-color injection molding has some unique advantages, it is essential to understand how it compares to other molding processes. In this blog post, we will compare two-color injection molding with other molding processes and discuss the benefits and limitations of each.
Two-Color Injection Molding vs. Single-Color Injection Molding
Single-color injection molding is the most common type, where a single material is injected into a mold to create a part. Compared to two-color injection molding, single-color injection molding has some advantages, including:
- Simpler process
- Lower cost
- Faster cycle times
However, single-color injection molding is limited in creating multi-colored or multi-material parts. Two-color injection molding allows for more design flexibility and the creation of more complex parts with multiple colors or materials.
Two-Color Injection Molding vs. Overmolding
Overmolding is a process that involves molding one material onto another to create a part with multiple materials or properties. Compared to two-color injection molding, over-molding has some advantages, including:
- Ability to mold onto existing parts
- Lower cost for small runs
- Simpler tooling
However, over-molding can be limited in producing complex parts with intricate designs and multiple colors. Two-color injection molding allows for more design flexibility and the creation of more complex parts with various colors or materials.
Two-Color Injection Molding vs. Insert Molding
Insert molding is a process that involves molding around an insert or component to create a part with added functionality or properties. Compared to two-color injection molding, insert molding has some advantages, including:
- Ability to incorporate functional components
- Lower cost for small runs
- Simpler tooling
However, insert molding can be limited in producing parts with intricate designs and multiple colors. Two-color injection molding allows for more design flexibility and the creation of more complex parts with various colors or materials.
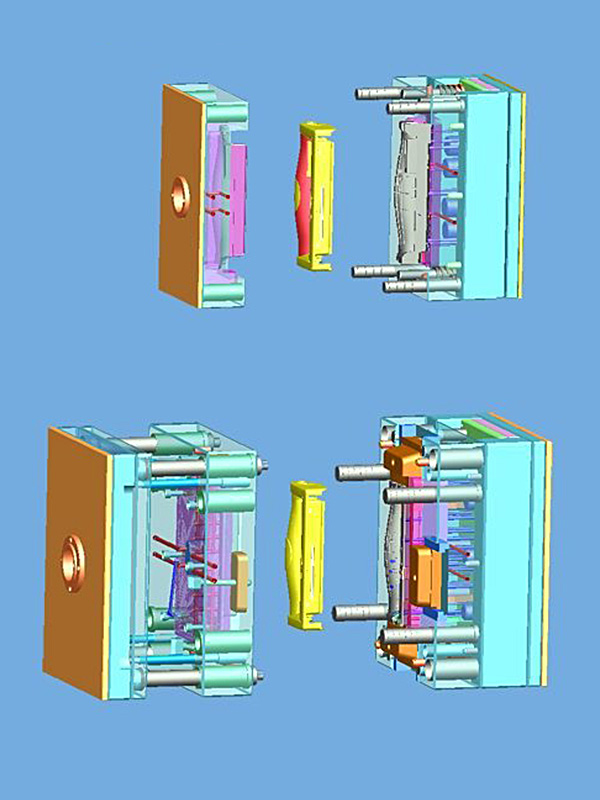
Sustainability and environmental impact of two-color injection molding
As environmental concerns continue to grow, manufacturers need to consider their manufacturing processes’ sustainability and environmental impact. Two-color injection molding is a popular manufacturing process that offers several benefits, but it is also essential to understand its environmental impact and potential for sustainability. This blog post will explore the sustainability and ecological impact of two-color injection molding.
Sustainability in Two-Color Injection Molding
Two-color injection molding has some potential for sustainability due to its ability to create parts with multiple materials and properties. This process can lead to producing components with better durability, less waste, and greater energy efficiency. In addition, two-color injection molding can offer some sustainability benefits:
- They are reducing the need for additional assembly or finishing processes, which can reduce waste and energy use.
- Using recycled materials in the molding process can reduce waste and conserve resources.
- They are reducing the amount of scrap material generated during molding, which can reduce waste and conserve resources.
Environmental Impact of Two-Color Injection Molding
While two-color injection molding has some potential for sustainability, it is also essential to understand its environmental impact. The ecological implications of two-color injection molding can include the following:
- Energy consumption during molding can contribute to greenhouse gas emissions and climate change.
- Waste generated during the molding process, including scrap material and packaging waste.
- The potential use of toxic or hazardous materials in molding can pose a risk to workers and the environment.
To address these environmental concerns, manufacturers can take several steps to minimize the ecological impact of two-color injection molding, including:
- Using energy-efficient equipment and processes to reduce energy consumption during the molding process.
- Implement waste reduction and recycling programs to minimize waste generated during molding.
- Using environmentally friendly materials and avoiding toxic or hazardous materials in molding.
Future trends in two-color injection molding
As technology continues to evolve, several future trends in two-color injection molding are worth exploring. This blog post will discuss some of the emerging trends and advancements in two-color injection molding.
Increased Automation
One of the most significant trends in two-color injection molding is the increased use of automation. Automation can improve efficiency and reduce the risk of human error, which leads to lower costs and improved quality. Some ways that manufacturers are using automation in two-color injection molding include:
- Automated part removal and packaging
- Automatic material handling and mixing
- Automated mold changes
Advanced Materials
Another emerging trend in two-color injection molding is the use of advanced materials. Advanced materials can offer improved performance, durability, and functionality, which can help to differentiate products in the marketplace. Some manufacturers are using advanced materials in two-color injection molding, including:
- High-performance thermoplastics
- Biodegradable and compostable materials
- Liquid silicone rubber (LSR) and thermoplastic elastomers (TPE)
Smart Manufacturing
Smart manufacturing is another trend impacting the future of two-color injection molding. Smart manufacturing involves using advanced technologies and data analytics to optimize manufacturing processes and improve product quality. Manufacturers are using intelligent manufacturing in various ways in two-color injection molding, including:
- Real-time monitoring and analytics of molding parameters
- Predictive maintenance and troubleshooting
- Integration with other smart technologies, such as robotics and automation
Sustainability
Sustainability is a growing trend across all industries; two-color injection molding is no exception. Manufacturers are increasingly focused on reducing waste, conserving resources, and minimizing environmental impact. Manufacturers are actively addressing sustainability in two-color injection molding through various approaches, including:
- Use of recycled materials
- Optimization of molding parameters to reduce waste and energy consumption
- Implementation of closed-loop recycling systems
Case studies of two-color injection molding projects
Two-color injection molding is a popular manufacturing process that offers design flexibility, improved functionality, and unique aesthetic options. In this blog post, we will explore some case studies of two-color injection molding projects to showcase the versatility and effectiveness of this process.
Automotive Industry: Two-Color Steering Wheel
The automotive industry often uses two-color injection molding to create parts with both visual appeal and functionality. One example is a two-color steering wheel that uses a rigid material for the base and a soft fabric for the grip. This design offers both comfort and durability for the driver. The two-color molding process also allows branding or design elements to be incorporated directly into the steering wheel.
Medical Industry: Two-Color Syringe
The medical industry often uses two-color injection molding to create parts with unique functionality and safety features. A two-color syringe design can incorporate a hard outer layer for protection and a soft inner layer for ease of use. Moreover, the two-color molding process allows manufacturers to create a clear window on the syringe, effectively indicating the amount of fluid they dispense.
Consumer Electronics Industry: Two-Color Phone Case
The consumer electronics industry often uses two-color injection molding to create parts with both aesthetic appeal and functionality. A two-color phone case design can incorporate a hard outer layer for protection and a soft inner layer for shock absorption. The two-color molding process also allows branding or design elements to be incorporated directly into the phone case.
Household Goods Industry: Two-Color Toothbrush
The household goods industry often uses two-color injection molding to create parts with unique design features and functionality. A designer can create a two-color toothbrush with a hard outer layer for durability and a soft inner layer for comfort. The two-color molding process also allows for the creation of bristle patterns and colors to match the branding or design of the toothbrush.
Sports Industry: Two-Color Bicycle Helmet
The sports industry often uses two-color injection molding to create parts with functionality and aesthetic appeal. Designers can create a two-color bicycle helmet with a hard outer layer for protection and a soft inner layer for comfort. The two-color molding process also allows for incorporating branding or design elements into the helmet.
Training and certification for two-color injection molding
Training and certification programs have become increasingly popular for individuals who wish to specialize in this field. This blog post will explore the importance of training and certification for two-color injection molding and some available programs.
Why is Training and Certification Important?
Training and certification are crucial for individuals in the two-color injection molding industry. Proper training ensures that individuals have the skills and knowledge to operate machinery safely and effectively and create high-quality products. Certification programs provide a standardized measure of proficiency and demonstrate a commitment to ongoing professional development.
Some of the Benefits of Training and Certification Include:
- Improved Safety:Proper training and certification can help reduce the risk of accidents and injuries by ensuring that individuals know the best machine operation and maintenance practices.
- Increased Productivity:Individuals who have received training and certification are typically more efficient and effective in their roles, leading to improved productivity and output.
- Enhanced Quality:Proper training and certification can help ensure that products meet the necessary quality standards and specifications.
Training and Certification Programs Available
- Manufacturers:Many equipment manufacturers offer training programs for their specific machines. These programs typically cover machine operation, maintenance, troubleshooting, and safety.
- Trade Schools:Some trade schools offer two-color injection molding courses that cover materials, design, and machine operation. These programs may also include hands-on training.
- Certification Organizations: Some organizations offer certification programs for individuals in the two-color injection molding industry. These programs typically include both written and practical exams to demonstrate proficiency.
Two-color injection molding for prototyping
The two-color injection molding process is widely used in manufacturing to create complex parts with multiple colors or materials. However, it can also be an excellent option for prototyping. In this blog post, we will explore the benefits of using two-color injection molding for prototyping.
Benefits of Two-Color Injection Molding for Prototyping
- Cost-Effective: Two-color injection molding can be a cost-effective option for prototyping because it allows for creating parts with multiple colors or materials in a single mold. By reducing the number of molds needed, manufacturers can lower costs.
- High-Quality Parts:Two-color injection molding produces high-quality parts with tight tolerances and excellent surface finishes. A crucial aspect of prototyping is creating components that accurately reflect the final product.
- Faster Turnaround Times:Using two-color injection molding for prototyping can lead to shorter turnaround times because it allows for creating complex parts in a single mold. By eliminating the need to assemble multiple components, manufacturers can reduce the time required for prototyping.
- Design Flexibility:Two-color injection molding provides a high design flexibility, allowing for the creation of parts with complex geometries and intricate features. Making accurate representations of the final product is crucial in prototyping.
- Material Selection:Two-color injection molding allows for different materials in a single part, which is vital in prototyping because it will enable evaluating varying material properties and combinations.
Applications of Two-Color Injection Molding in Prototyping
- Consumer Products:Manufacturers can use two-color injection molding to create prototypes of consumer products such as toys, appliances, and electronics. Producing parts with multiple colors or materials in a single mold is particularly useful in this industry.
- Automotive Industry: Two-color injection molding can create prototypes of automotive components such as interior trim, steering wheels, and gear shift knobs. Producing parts with different textures and finishes is essential in this industry.
- Medical Devices:Two-color injection molding can create prototypes of medical devices such as handles, buttons, and switches. Producing parts with different materials is essential in this industry, where biocompatibility and sterilization properties are critical.
Choosing the right partner for your two-color injection molding project
Choosing the right partner for your two-color injection molding project is critical to the success of your project. It would help if you found a partner who has the expertise, experience, and capabilities to meet your specific needs. This blog post will explore some important factors to consider when choosing the right partner for your two-color injection molding project.
Factors to Consider When Choosing a Partner for Your Two-Color Injection Molding Project:
- Expertise:Choosing a partner with expertise in two-color injection molding is crucial. They should have a deep understanding of the process and be able to provide advice and guidance on the design and production of your parts.
- Experience:Experience is essential when choosing a partner for your two-color injection molding project. Look for a partner with a proven track record of success producing high-quality parts with tight tolerances and excellent surface finishes.
- Capabilities:Consider the powers of the partner you are considering. Do they have the necessary equipment, resources, and personnel to handle your project? Can they handle large volumes and complex parts? Make sure your partner has the capabilities to meet your specific needs.
- Quality Control: Quality control is critical in two-color injection molding. Ensure your partner has a robust quality control system to ensure the parts they produce meet your specifications and standards.
- Communication: Communication is key to any successful project. Make sure your partner is responsive and communicative throughout the entire process. They should keep you informed of any issues or challenges and be proactive in finding solutions.
- Cost: Cost is always a consideration when choosing a partner for your two-color injection molding project. However, it is essential to remember that the lowest price does not always mean the best value. Look for a partner who offers competitive pricing while still providing high-quality parts and excellent service.
- Sustainability:Sustainability is becoming increasingly important in manufacturing. Consider partnering with a company committed to sustainability and reducing their environmental impact.
Conclusion
Two-color injection molding is a versatile and increasingly popular manufacturing process that offers many advantages, such as improved design flexibility, reduced assembly time, and enhanced functionality. While it has its limitations and challenges, it can produce high-quality parts at a competitive cost with the proper design considerations, equipment, and materials. Two-color injection molding has applications in various industries, and as technology advances, we can expect to see more innovations in this field. Working with a reliable and experienced partner who can provide the expertise, equipment, and resources needed is essential for ensuring the success of your two-color injection molding project.