Low Volume Manufacturing Service
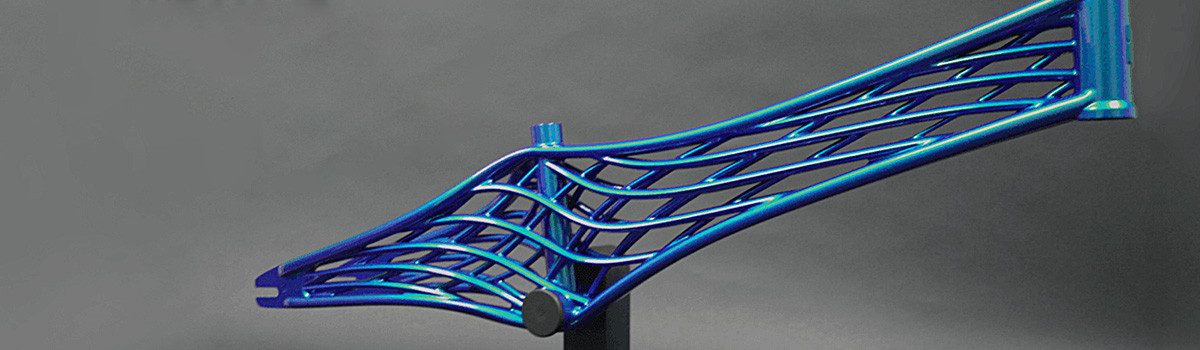
Small businesses often need help finding affordable manufacturing solutions that can produce low volumes of products without incurring high costs. Small businesses with limited resources often need to overcome a significant barrier due to the cost-effectiveness requirement of creating large quantities in traditional manufacturing methods. However, with the emergence of low volume manufacturing services, small businesses can now produce small products at a fraction of the cost of conventional manufacturing methods. This article will explore the benefits of low volume manufacturing services and how they can help small businesses stay competitive.
What is Low Volume Manufacturing?
Low volume manufacturing refers to producing a small number of products, typically ranging from a few units to a few hundred, using manufacturing processes and techniques. Manufacturers design low volume manufacturing to meet the specific needs of small businesses or startups, in contrast to mass production, which focuses on producing large quantities. This approach allows companies to avoid the high upfront costs and risks of producing large volumes. Low volume manufacturing services utilize injection molding, CNC machining, 3D printing, and sheet metal fabrication to efficiently produce small batches of products, making it an ideal solution for businesses looking for cost-effective production options.
The Benefits of Low Volume Manufacturing for Small Businesses
Low volume manufacturing offers small businesses several advantages, offering cost-effective production options tailored to their specific requirements. Here are the key benefits of low volume manufacturing:
- Cost Savings:Small businesses can avoid the high upfront costs associated with traditional mass production by opting for low volume manufacturing. It enables them to produce smaller quantities without excessive setup expenses or the need for significant inventory investments.
- Fast Turnaround Times:Low volume manufacturing services prioritize quick turnaround times, allowing small businesses to swiftly bring their products to market. This agility enables them to respond promptly to market demands and capitalize on emerging opportunities.
- Flexibility in Manufacturing Processes:With low volume manufacturing, businesses can choose from various manufacturing processes based on their product specifications, allowing them to tailor the production approach to their specific needs. Multiple techniques, including injection molding, CNC machining, 3D printing, and sheet metal fabrication, provide the flexibility needed to meet particular needs.
- High-Quality End Products:Low-volume manufacturing maintains stringent quality standards despite producing smaller quantities. Manufacturers employ advanced equipment and expertise to ensure that each product meets the required specifications, resulting in high-quality end products.
- Design for Manufacturing (DFM):Low volume manufacturing services often support design optimization. Manufacturers collaborate with businesses during the design phase, offering valuable insights to enhance product manufacturability, resulting in efficient and cost-effective production.
- Prototyping Services:Many low volume manufacturing services offer prototyping capabilities, enabling small businesses to iterate on their product designs before full-scale production. Prototyping helps identify and address design flaws, assess functionality, and gather valuable feedback for further refinement.
- Material and Process Options:Low volume manufacturing services offer a wide range of materials and manufacturing processes to suit diverse product requirements. Businesses can select suitable options based on strength, durability, aesthetics, and cost.
- Scalability:Low volume manufacturing provides scalability options for small businesses. As demand grows, companies can efficiently adjust production volumes without significant investments or retooling, ensuring a smooth transition to meet market needs.
- Reduced Inventory Risks: Low volume manufacturing minimizes inventory risks for small businesses. They can produce products on demand or maintain lean inventories, reducing the costs and risks associated with excess inventory and potential obsolescence.
Cost Savings with Low Volume Manufacturing
Low volume manufacturing offers several cost-saving advantages for businesses, particularly for small-scale production runs. Here are some key benefits of cost savings with low volume manufacturing:
- Reduced Setup Costs:Traditional manufacturing processes typically involve high setup costs, particularly for small production runs. Businesses can avoid these upfront expenses by optimizing the manufacturing process for small quantities by utilizing low volume manufacturing.
No Minimum Order Quantities: Unlike traditional mass production, low volume manufacturing services typically do not require minimum order quantities. Businesses can save money on excess inventory and waste by only producing what is necessary.
- Lower Tooling Costs:Low volume manufacturing services use tools and equipment optimized for small quantities, reducing the cost of tooling and minimizing the risk of obsolescence.
- Lower Material Costs: Traditional manufacturing often requires bulk purchases of materials, which can lead to excess inventory and waste. With low volume manufacturing, businesses can order smaller quantities, reducing waste and minimizing material costs.
- Reduced Labor Costs: Low volume manufacturing typically requires less labor than traditional mass production, resulting in lower business labor costs.
- Agile Manufacturing:Low volume manufacturing offers agile manufacturing processes, enabling businesses to quickly pivot output based on market demand, reducing the risk of producing excess inventory and waste.
Fast Turnaround Times
Low volume manufacturing refers to producing a relatively small number of products, typically less than 10,000 units. This type of manufacturing is often required when developing new products, testing the market demand for a particular item, or producing articles with specialized features that are in low order.
Fast turnaround times for low-volume manufacturing are crucial to meet market demand, reduce lead times, and accelerate the time-to-market of new products. Here are some strategies to achieve fast turnaround times for low-volume manufacturing:
- Optimize the manufacturing process: The process should minimize production times and maximize efficiency. This includes identifying bottlenecks, simplifying production steps, and ensuring the manufacturing process is lean and agile.
- Use digital manufacturing technologies: Digital manufacturing technologies, such as 3D printing, CNC machining, and injection molding, can significantly reduce production times and costs. These technologies allow for producing parts and components with high precision and accuracy, enabling faster turnaround times.
- Work with an experienced manufacturer: A professional manufacturer will deeply understand the manufacturing process and can offer insights and recommendations for reducing production times. They will also have the necessary expertise and equipment to produce high-quality products quickly and efficiently.
- Utilize just-in-time (JIT) manufacturing: JIT manufacturing is a production strategy that only produces items when needed. This strategy helps to minimize inventory levels, reduce lead times, and improve production efficiency.
- Implement agile manufacturing practices: Agile manufacturing practices use flexible processes and technologies to quickly adapt to changing market demands. This approach allows manufacturers to respond rapidly to new product development and market opportunities.
- Embrace automation: Automation technologies, such as robotics and artificial intelligence, can help to streamline production processes and improve efficiency. These technologies can perform repetitive tasks faster and more accurately than humans, enabling faster turnaround times.
- Use reliable suppliers: Reliable suppliers can provide high-quality materials and components on time, reducing delays in the manufacturing process. It is essential to establish solid relationships with suppliers and ensure they have the necessary capacity to meet production demands.
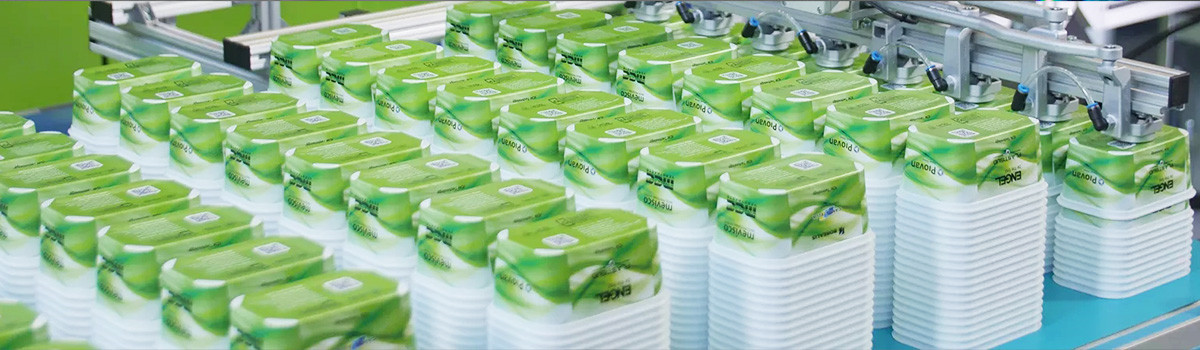
Flexible Manufacturing Processes
Our commitment to quality and customer satisfaction ensures that every product meets or exceeds your expectations.
- Our company is committed to providing flexible manufacturing processes that can adapt to the changing needs of our clients. We understand that every project is unique and may require different approaches, and we design our manufacturing processes to be versatile and adaptable.
- Our experienced engineers and technicians can tailor our manufacturing processes to suit your requirements, whether low or high volume production, rapid prototyping, or custom fabrication. We can produce many products, from small intricate components to large assemblies.
- We utilize the latest technology and equipment to ensure maximum flexibility and efficiency in our manufacturing processes. Our equipment has advanced software and automation capabilities, enabling us to switch between different product specifications and production volumes quickly.
- We offer a variety of manufacturing processes, including CNC machining, injection molding, 3D printing, laser cutting, and more. Our team can work with you to determine the most suitable method for your project needs based on material properties, design complexity, and production volume.
- We also design our manufacturing processes to be scalable, enabling us to ramp up production quickly as demand increases. Depending on your specific requirements, we can efficiently produce small batches or large quantities of products.
- We understand that time-to-market is critical for many of our clients, and our flexible manufacturing processes enable us to provide rapid prototyping and product development services. With our advanced technology and expertise, we can produce high-quality prototypes quickly and efficiently, allowing you to test and refine your designs before moving to mass production.
- We prioritize quality control throughout our manufacturing processes and employ rigorous testing and inspection procedures to ensure that every product meets or exceeds our client’s expectations. Our team monitors each process step, from material selection to final inspection and validation.
- Our commitment to flexibility extends beyond our manufacturing processes. We value open communication and collaboration with our clients, allowing us to understand their needs and provide tailored solutions. Our responsive customer support team is always available to promptly address any concerns or queries.
High-Quality End Products
Our company is committed to delivering high-quality end products that meet or exceed our client’s expectations.
- At our company, we prioritize delivering high-quality end products to meet the exacting standards of our clients. We understand that quality is paramount and strive to exceed expectations by providing top-notch products built to last.
- We employ stringent quality control measures throughout production to ensure that every step meets the highest standards. From material selection to manufacturing and assembly, our experienced team monitors each phase to guarantee the quality and integrity of the end products.
- We work with a network of trusted suppliers who provide us with premium materials that meet rigorous quality specifications. Whether it’s metals, plastics, composites, or other specialized materials, we only source from reputable vendors to ensure the highest quality in our products.
- We execute our manufacturing processes with precision and attention to detail. We utilize advanced technologies and equipment to ensure accuracy, consistency, and repeatability in every product we produce. Our skilled technicians and engineers closely monitor production to identify and address potential issues or deviations from the desired quality.
- We understand that customer satisfaction relies on not only the quality of the end product but also its functionality and performance. We conduct comprehensive testing and validation procedures to verify that our products meet or exceed all necessary specifications and performance requirements.
- Continuous improvement is a core principle of our company. We actively seek feedback from our clients and strive to incorporate their insights into our manufacturing processes. By embracing a continuous learning and enhancement culture, we consistently elevate the quality of our end products.
- Our commitment to delivering high-quality end products extends to various industries and sectors. Whether it’s consumer goods, automotive components, electronic devices, or industrial equipment, we have the expertise and resources to meet the specific quality standards of each industry.
- We understand the importance of timely delivery without compromising quality. Our streamlined production processes and efficient workflows enable us to meet project deadlines while maintaining the highest level of quality control.
- Our dedication to high-quality end products has earned us a strong reputation and a loyal customer base. We take pride in the satisfaction of our clients, and our commitment to quality ensures that every product leaving our facility is of the utmost quality and craftsmanship.
Design for Manufacturing (DFM)
Design for Manufacturing (DFM) is an integrated approach that focuses on optimizing the design of a product to enhance its manufacturability. DFM aims to minimize production costs, reduce assembly time, and ensure high-quality end products by considering manufacturing processes early in the design phase. Here are some key bullet points outlining the significance and principles of DFM:
- Simplified designs:DFM emphasizes simplifying product designs to eliminate unnecessary complexity, reducing the number of components, and streamlining assembly processes. This approach helps lower production costs by minimizing material waste, assembly errors, and production time.
- Material selection: Proper selection is essential in DFM to ensure compatibility with manufacturing processes. Designers must consider factors such as material availability, cost, strength, and ease of fabrication. Choosing materials that align with manufacturing capabilities can significantly improve overall production efficiency.
- Design for assembly (DFA):DFA is a crucial aspect of DFM that focuses on designing products for easy and efficient groups. It involves considering factors such as part orientation, standardization of components, and modular designs. DFA reduces labor costs, improves product quality, and shortens production lead times by optimizing assembly processes.
- Tolerance and fit considerations: In DFM, designers carefully consider tolerances and fits between components to ensure proper assembly and functionality. By defining appropriate tolerances, designers can reduce the likelihood of assembly issues, improve part interchangeability, and minimize the need for rework or adjustments during manufacturing.
Manufacturing process compatibility: DFM considers the capabilities and limitations of the chosen manufacturing processes. To ensure efficient production, designers must understand the constraints of various manufacturing techniques, such as injection molding, machining, or casting, and design products that manufacturing processes can produce quickly.
- Design for testability (DFT):DFT is an essential aspect of DFM that focuses on designing products with built-in features for effective testing and quality control. By incorporating features like test points, access for probes, or self-diagnostic capabilities, DFT enables efficient testing during manufacturing, reducing the likelihood of faulty products reaching the market.
Prototyping Services
Prototyping services offer a valuable solution for companies and individuals looking to bring their ideas to life and validate their designs before mass production. These services encompass a range of capabilities, allowing for the creation of functional prototypes that closely resemble the final product. Here are some key bullet points highlighting the importance and benefits of prototyping services:
- Iterative design process:Prototyping services enable an iterative design approach, allowing designers to refine and improve their concepts through multiple iterations. By quickly creating and testing prototypes, designers can identify design flaws, make necessary adjustments, and optimize the final product’s functionality and aesthetics.
- Proof of concept: Prototypes are tangible evidence of a concept’s feasibility and potential success. By creating a functional prototype, inventors and entrepreneurs can demonstrate the viability of their ideas to investors, stakeholders, or potential customers. This proof of concept can significantly increase the chances of securing funding or gaining support for further development.
- Design validation and testing:Prototyping services provide an opportunity to test and validate product designs before full-scale production thoroughly. Functional prototypes allow for real-world testing, user feedback, and performance evaluation. By identifying and addressing design flaws early on, prototyping services help minimize risks, reduce costs, and improve the overall quality of the final product.
- Customization and personalization:Prototyping services offer the flexibility to create custom-designed prototypes tailored to specific requirements. Whether it’s a unique shape, size, or functionality, these services allow designers to explore various possibilities and develop prototypes that accurately represent their vision. This customization aspect facilitates innovation and promotes the development of highly personalized products.
- Time and cost savings:Utilizing prototyping services can result in significant time and cost savings during product development. Prototypes help prevent costly rework and revisions during mass production by identifying design issues early on. Additionally, rapid prototyping techniques, such as 3D printing, enable faster turnaround times, reducing the time-to-market and allowing for quicker iterations.
- Collaboration and communication:Prototypes are practical communication tools between designers, engineers, and stakeholders. They provide a tangible representation of the product, allowing for more transparent communication and better collaboration. Prototypes facilitate constructive feedback, align expectations, and ensure everyone involved has a shared understanding of the final product’s appearance and functionality.
Materials and Processes Available for Low Volume Manufacturing
Our company offers a comprehensive range of materials and processes for low volume manufacturing.
- Our company offers a wide range of materials and processes specifically tailored for low volume manufacturing. Whether you require small batch production or prototyping, we can meet your unique needs while maintaining high-quality standards.
- Our materials selection includes diverse options suitable for low volume manufacturing. From traditional metals like aluminum and steel to advanced composites and plastics, we can accommodate a variety of product specifications and performance requirements.
- In addition to metals and plastics, we specialize in materials such as ceramics, elastomers, and textiles, allowing us to cater to various industries and applications. Our materials experts can guide you in selecting the most suitable materials for your project needs.
- We design our low volume manufacturing processes to be flexible and efficient, enabling cost-effective production without compromising quality. We employ advanced techniques such as CNC machining, 3D printing, injection molding, and vacuum casting to achieve accurate and repeatable results.
- CNC machining is particularly well-suited for low volume manufacturing as it offers high precision and versatility. With our state-of-the-art equipment and skilled machinists, we can efficiently produce complex parts with tight tolerances.
- 3D printing, or additive manufacturing, is another popular choice for low volume production. It allows rapid prototyping and iterative design changes, reducing lead times and costs. We utilize various 3D printing technologies, including selective laser sintering (SLS) and fused deposition modeling (FDM), to cater to different material and dimensional requirements.
- Injection molding is an excellent option for low volume manufacturing of plastic components. By leveraging our mold design and tooling expertise, we can produce high-quality parts with consistent dimensions and surface finishes.
- Vacuum casting is a cost-effective solution for making small batches of high-quality prototypes or end-use parts. This process allows using various materials and can accurately replicate intricate details and textures.
- We prioritize quality control and rigorous testing throughout the low volume manufacturing process to ensure that every product meets or exceeds your expectations. Our experienced team monitors each step, from material selection and process optimization to final inspection and validation.
- We understand the unique challenges and requirements of low volume manufacturing, and our dedicated team is committed to delivering exceptional results on time and within budget. Whether you need a few prototypes or a limited production run, we design our materials and processes to meet your specific needs and provide the highest level of customer satisfaction.
Injection Molding
Injection molding is a widely used manufacturing process that involves creating plastic parts by injecting molten material into a mold. It offers several advantages, making it a popular choice for mass production. Here are some key bullet points highlighting the significance and benefits of injection molding:
- Versatility:Injection molding provides exceptional versatility regarding part design and complexity. It can produce intricate and detailed parts with varying shapes, sizes, and features, including thin walls, undercuts, and complex geometries. This versatility allows for the creation of customized products to meet specific requirements.
- Cost-effective production:Injection molding is highly efficient for large-scale production runs. Once we create the initial mold, production becomes faster and more cost-effective. The high production speed and the ability to produce multiple parts simultaneously significantly reduce the per-unit cost, making it an economical choice for high-volume manufacturing.
- Material variety:Injection molding supports a wide range of thermoplastic and thermosetting materials, allowing designers to choose the most suitable material for their applications. Materials with varying properties, such as flexibility, rigidity, transparency, or resistance to heat and chemicals, can produce parts with diverse functionalities.
- Consistency and quality:Injection molding ensures excellent part consistency and dimensional accuracy. The automated nature of the process minimizes human error, resulting in consistent and repeatable production. Additionally, the closed mold system provides precise control over the molding conditions, allowing for the production of high-quality parts with tight tolerances and minimal defects.
- High production efficiency:Injection molding offers fast production cycles, enabling a high output of components in a relatively short period. By combining quick cycle times with the ability to automate the process, businesses can achieve increased productivity and improved overall production efficiency. This efficiency makes injection molding an ideal choice for meeting demanding production timelines.
- Design for manufacturing (DFM) compatibility:Injection molding is well-aligned with Design for Manufacturing (DFM) principles. An excellent choice for DFM practices, its capabilities include creating complex shapes, optimizing material usage, and incorporating features like snap fits or living hinges. Designers can leverage these capabilities to enhance manufacturability, reduce costs, and improve production efficiency.
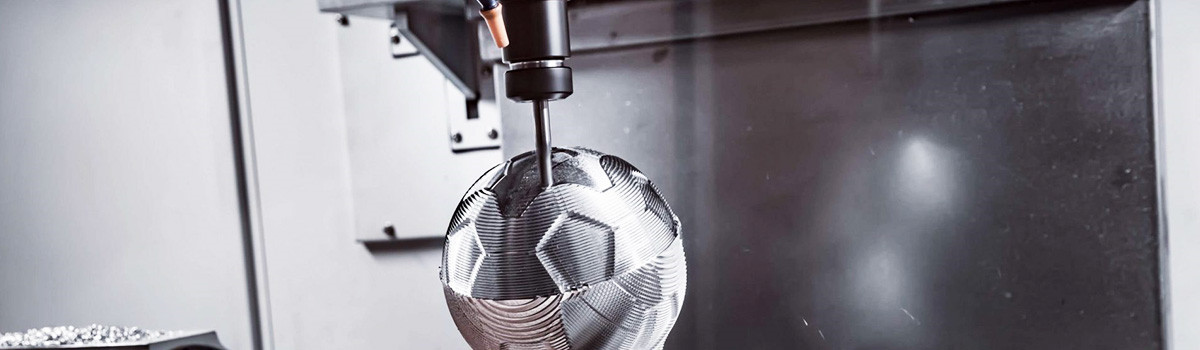
CNC Machining
CNC machining, or computer numerical control machining, is a process used to create precise and complex parts from raw materials such as metal, plastic, or wood. This manufacturing process involves using computer-aided design (CAD) software to design a 3D model of the part, which is then converted into machine code and used to control a CNC machine. CNC machining has many applications, from the aerospace and automotive industries to consumer products and medical devices.
The process of CNC machining involves several steps, including:
- Design: The first step in CNC machining is to create a 3D model of the part using CAD software. We then convert this model into machine code, which we use to control the CNC machine.
- Material selection: The raw material is selected based on the desired properties of the final part, such as strength, durability, and heat resistance.
- Machine setup: We program the CNC machine with the machine code and secure the raw material in the machine.
- Machining: The CNC machine uses various tools, such as drills, lathes, and mills, to remove material from the raw material according to the machine code. This process is exact and can create complex shapes and features.
- Post-processing: Once the machining is complete, the part may require post-processing, such as sanding or polishing, to achieve the desired finish and texture.
The advantages of CNC machining are numerous, including:
- Precision: CNC machining is exact and can create parts with tolerances as low as 0.001 inches.
- Efficiency: CNC machining is a highly efficient manufacturing process that can produce parts quickly and accurately.
- Customization:CNC machining can produce highly customized parts tailored to specific needs and preferences.
- Complexity:CNC machining can create highly complex shapes and designs that would be difficult or impossible to produce using traditional manufacturing methods.
- Consistency: CNC machining produces parts with a high level of consistency, ensuring that each piece meets the exact specifications.
CNC machining has a wide range of applications across various industries, including:
- Aerospace:We use CNC machining to produce aircraft engines, wings, and landing gear parts.
- Automotive: We use CNC machining to make parts for engines, transmissions, and chassis.
- Medical: CNC machining makes surgical instruments, implants, and prosthetics.
- Consumer products:We use CNC machining to produce everything from smartphone cases to kitchen appliances.
- Architecture: We use CNC machining to produce building components and decorative features.
3D Printing
3D printing, also known as additive manufacturing, is a revolutionary technology that has recently transformed the manufacturing industry. This process involves layering material, typically plastic or metal, on top of itself until it forms the desired shape, creating a physical object. 3D printing has a wide range of applications, from prototyping and product development to the production of medical implants and customized consumer products.
The process of 3D printing involves several steps, including:
- Design: The first step in 3D printing is to create a digital model of the desired object using computer-aided design (CAD) software. Then, we upload this model to the 3D printer.
- Printing: The 3D printer begins the printing process by creating a thin layer of material, usually plastic or metal, and fusing it with the previous layer using heat or adhesive. We repeat this process layer by layer until we form the entire object.
- Post-processing: Once the printing is complete, the object may require post-processing, such as sanding or polishing, to achieve the desired finish and texture.
The advantages of 3D printing are numerous, including:
- Customization:3D printing enables us to create highly customized products tailored to specific needs and preferences.
- Speed:3D printing is a rapid prototyping process that can quickly produce a physical object from a digital model.
- Cost-effective:3D printing can be a cost-effective manufacturing process, particularly for small production runs or customized products.
- Complexity: 3D printing can create highly complex shapes and designs that would be difficult or impossible to produce using traditional manufacturing methods.
- Waste reduction: 3D printing minimizes waste using only the necessary material to create the object.
3D printing has a wide range of applications across various industries, including:
- Manufacturing: We can use 3D printing for prototyping, product development, and small production runs.
- Medical: 3D printing can produce customized prosthetics, implants, and surgical models for planning and training purposes.
- Architecture: We can use 3D printing to create scale models and building components.
- Fashion: 3D printing can create unique, customized clothing and accessories.
- Education: 3D printing can be used in schools to teach design and engineering concepts.
Sheet Metal Fabrication
Sheet metal fabrication is a manufacturing process that involves shaping metal sheets into different structures and products. This process combines cutting, bending, punching, and welding techniques to transform flat sheets of metal into various shapes, sizes, and designs. Multiple industries, from construction to automotive, utilize sheet metal fabrication, and it is critical to producing many everyday items, including household appliances and electronic devices.
The process of sheet metal fabrication involves several steps, including:
- Design:The first step in sheet metal fabrication is to create a plan for the desired product. Businesses can utilize computer-aided technique (CAD) software to achieve accurate measurements and specifications.
- Cutting:After finalizing the design, manufacturers cut the metal sheet into the required size and shape using various techniques, such as laser or water jet.
- Bending: The next step is to turn the metal sheet into the desired shape. Manufacturers use specialized tools such as press brakes to create accurate angles and curves in metal.
- Punching:Punching techniques are employed to create holes or other shapes in the metal. These can include stamping or drilling, depending on the complexity of the design.
Welding: Finally, manufacturers weld the various pieces of metal together to create the final product. By subjecting the metal to high heat, we melt and fuse it, creating a solid and long-lasting bond.
Sheet metal fabrication has several advantages over other manufacturing processes. These include:
- Flexibility: Sheet metal can be shaped into virtually any shape or size, making it versatile for a wide range of products.
- Strength:Sheet metal is strong and durable, making it ideal for products that require high durability and reliability.
- Cost-effective: Sheet metal is relatively inexpensive, making it an affordable option for the mass production of products.
- Precision:Sheet metal fabrication enables us to achieve precise measurements and specifications, ensuring we make each product to exacting standards.
A variety of industries utilize sheet metal fabrication, including:
- Construction: Companies use sheet metal to create HVAC ducts, roofing materials, and other structural components in buildings.
- Automotive:Automotive manufacturers use sheet metal to produce car bodies, engine components, and other parts.
- Electronics: Manufacturers use sheet metal to create computer cases, cell phone shells, and other components.
- Aerospace:Aircraft manufacturers use sheet metal to produce aircraft parts and components.
Casting
Casting is an essential process in the entertainment industry. It involves selecting actors and other performers for roles in film, television, theater, and other forms of media. A good casting director can make or break a production, as the right cast can bring a script to life and create a memorable viewing experience for audiences. In this blog post, we will explore the importance of casting and the critical factors in making successful casting decisions.
First and foremost, the role of a casting director is to find the best actors for the job. The process of casting an actor involves assessing not only their abilities but also their schedule, level of professionalism, and suitability for the part. A good casting director will work closely with the director and producers to understand the creative vision for the project and then seek out actors who can bring that vision to life.
Some of the key factors that casting directors consider when evaluating actors include:
- Acting abilityis the most crucial factor, as an excellent performance can make or break a project. Casting directors will look for actors to deliver a convincing and emotionally resonant performance.
- Physical appearance: An actor’s appearance is sometimes crucial to the role. For example, if a character is tall and blonde, the casting director will prioritize actors who match that description.
- Availability:Filming schedules can be demanding, so casting directors must consider an actor’s availability before deciding. If an actor has already committed to another project, they may need help to take on a new role.
- Professionalism:Acting is a job, and casting directors will look for professional and reliable actors. Individuals should arrive on time, be adequately prepared, and treat the project with care to demonstrate respect for the project.
Ultimately, a successful casting decision requires a combination of these factors. An actor may have incredible talent, but if they are not available or do not fit the physical requirements of the role, they may not be the best choice.
In addition to selecting actors for specific roles, casting directors also play an essential role in shaping the overall cast of a production. When making a decision, it is vital to take into account various factors, including:
- Chemistry: In some cases, character relationships are as meaningful as individual performances. Casting directors will look for actors who have a natural chemistry on screen.
- Diversity:Representation is increasingly vital in the entertainment industry, and casting directors often strive to create a diverse cast that reflects the real world.
- Brand recognition: In some cases, casting a well-known actor can generate buzz for a project. For independent films or smaller productions, attracting attention can be crucial. That’s where our help comes in handy.
Extrusion
Extrusion is a manufacturing process that involves shaping a material by pushing it through a die to create a specific shape or profile. Manufacturers commonly use this process to make plastic and metal products such as pipes, tubes, and sheeting. Here, we will discuss extrusion, how it works, and its applications.
How Does Extrusion Work?
Extrusion works by pushing material through a die using an extruder. The extruder consists of a hopper, a screw, and a heating element. The operator feeds the raw material into the hopper, then transports it to the screw. The screw rotates, pushing the material through the heating element, where it is melted and mixed. The machine makes the molten material through the die, where it takes on the desired shape or profile. The extruded material is then cooled and cut to the desired length.
Applications of Extrusion
Extrusion has many applications in various industries, including:
- Construction: Extrusion is used in the construction industry to create plastic and metal pipes, tubes, and sheeting.
- Packaging:Extrusion is used in the packaging industry to create plastic film and sheeting for wrapping products.
- Automotive:Extrusion is used in the automotive industry to create plastic and metal components for cars, such as trim and weatherstripping.
- Food and Beverage: Extrusion is used in the food and beverage industry to create plastic and metal containers for storing and transporting food and beverages.
Advantages of Extrusion
Extrusion offers many advantages over other manufacturing processes, including:
- Cost-effective: Extrusion is a cost-effective manufacturing method, allowing for high-volume production with minimal waste.
- Versatile:Manufacturers can use extrusion to create a wide range of shapes and profiles, making it a universal manufacturing process.
- Consistency: Extrusion produces consistent results, ensuring that each product is identical.
- Speed: Extrusion is a fast process, allowing for high-volume production in a short amount of time.
- Quality: Extrusion produces high-quality products with a smooth surface finish.
Laser Cutting
Laser cutting is a popular manufacturing process that uses a laser beam to cut materials into various shapes and sizes. It offers many advantages over traditional cutting methods, such as precision, speed, and versatility. This blog post will discuss laser cutting, how it works, and some of its applications.
What is Laser Cutting?
Laser cutting is a manufacturing process that uses a laser beam to cut materials into various shapes and sizes. It’s a popular method for cutting different materials, including metal, wood, plastic, and fabric. Operators can control the laser beam to cut precise shapes and patterns with minimal waste.
How Does Laser Cutting Work?
Laser cutting works by directing a high-powered laser beam onto the cut material. A laser resonator generates the laser beam, then focuses on the material through mirrors and lenses. The focused laser beam melts, burns, or vaporizes the fabric, creating a clean and precise cut.
Applications of Laser Cutting
Laser cutting has many applications in various industries, including:
- Manufacturing:The manufacturing industry extensively utilizes laser cutting to cut and shape different materials. Consider writing the active voice. It’s beneficial for creating intricate shapes and patterns that would be difficult or impossible to achieve using traditional cutting methods.
- Architecture: Laser cutting is used in the architecture industry to create decorative panels, screens, and other design elements.
- Jewelry:Laser cutting is used in the jewelry industry to create intricate designs on precious metals.
- Automotive: The automotive industry utilizes laser cutting for cutting and shaping metal components.
- Electronics:The electronics industry employs laser cutting for cutting and shaping circuit boards and other features.
Advantages of Laser Cutting
Laser cutting offers many advantages over traditional cutting methods, including:
- Precision:Laser cutting produces precise cuts with minimal waste, allowing for more efficient use of materials.
- Speed: Laser cutting is faster than traditional cutting methods, allowing for shorter production times.
- Versatility:Laser cutting can cut a wide range of materials, including metal, wood, plastic, and fabric.
- Consistency: Laser cutting produces consistent results, ensuring that each cut is identical.
- Automation: Laser cutting can be automated, allowing for high-volume production with minimal human intervention.
Choosing the Right Low Volume Manufacturing Service Provider
Low volume manufacturing is an essential part of bringing your product to market. It allows you to produce small quantities of your product to test the market and make necessary changes before moving on to large-scale production. Choosing the right low volume manufacturing service provider is crucial to the success of your product. In this blog post, we will discuss the importance of selecting the right low volume manufacturing service provider and some tips for making the right choice.
Why is Choosing the Right Low Volume Manufacturing Service Provider Important?
Choosing the right low volume manufacturing service provider is essential for several reasons:
- Quality control: The right service provider will ensure your product meets your standards.
- Timely delivery: Choosing a reliable service provider can help ensure your product is convenient.
- Cost management: A reputable service provider can help you manage costs by identifying ways to reduce expenses.
- Innovation:Choosing a service provider with experience in your industry can help you identify new opportunities for innovation and product development.
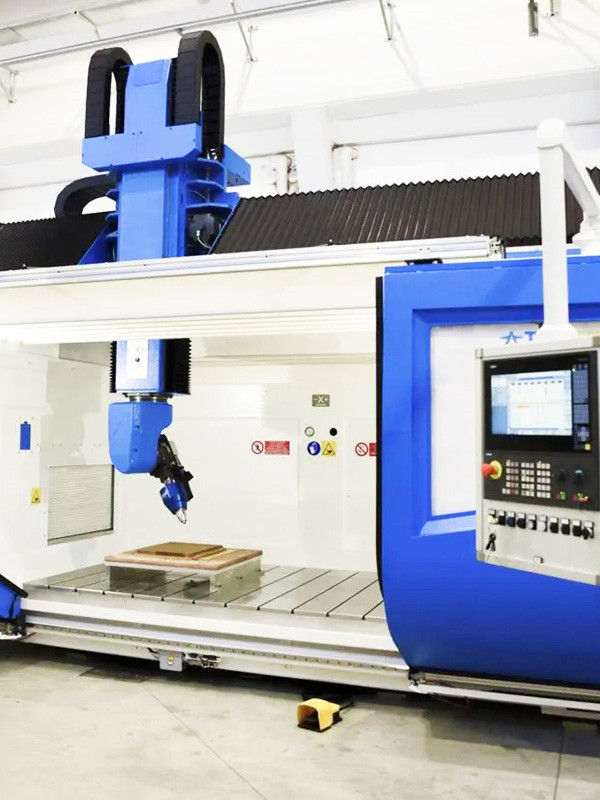
Tips for Choosing the Right Low Volume Manufacturing Service Provider
- Determine your needs: Before choosing a low volume manufacturing service provider, it’s essential to determine your needs. To ensure a successful product launch, it’s important to clearly define your product’s specifications, target market, and delivery timeline.
- Research potential service providersonline and check their reviews and ratings. You can also reach out to other businesses in your industry for recommendations.
- Evaluate experience and expertise:Choose a service provider with experience in your industry and expertise in the product you manufacture. It’s essential to communicate your needs clearly so that the product you receive meets your expectations.
- Consider the location:Choosing a service provider close to your business can help reduce shipping costs and ensure timely delivery.
- Evaluate cost:While cost should not be the only factor in your decision, evaluating the cost of working with different service providers is essential. Compare quotes and choose a competitive pricing provider while still meeting your quality requirements.
- Please request a sample: Before choosing a service provider, request a sample of their work. Assessing the quality of their work can assist you in determining if they are a suitable candidate for your project.
- Communicate your needs:Communication is critical to successfully partnering with your service provider. Be clear about your expectations and communicate any changes or issues throughout the manufacturing process.
Communication and Collaboration with the Manufacturer
Communication and collaboration with the manufacturer are crucial aspects of successfully bringing your product to market. Establishing an open and productive relationship with your manufacturer is essential to ensure that your product meets your expectations and is delivered on time and within budget. This blog post will discuss the importance of communication and collaboration with the manufacturer and some tips for establishing a successful partnership.
Why is Communication and Collaboration with the Manufacturer Important?
Communication and collaboration with the manufacturer are essential for several reasons:
- Quality control:Effective communication and collaboration with the manufacturer can help ensure that the quality of your product meets your expectations.
- Timely delivery:Establishing clear lines of communication can help you ensure the timely delivery of your product.
- Cost management:Collaboration with the manufacturer can help you manage costs by identifying ways to reduce expenses.
- Innovation:Collaboration with the manufacturer can help you identify new innovation and product development opportunities.
Tips for Establishing a Successful Partnership with the Manufacturer
- Establish clear expectations:It’s essential to establish clear expectations for your product from the beginning. Identifying your product’s specifications, target market, and delivery timeline is necessary to ensure successful product delivery.
- Maintain open lines of communication:Regular communication with the manufacturer can help prevent misunderstandings and ensure that the project is progressing as planned. Scheduling frequent check-ins and sharing updates on progress is essential to keep everyone on the same page.
- Foster a collaborative environment: Collaboration with the manufacturer is crucial to developing a successful partnership. We should be receptive to fresh concepts and resolutions and collaborate to find methods to enhance the product.
- Manage expectations: It’s essential to manage expectations throughout the manufacturing process. We are committed to being open and honest about any possible setbacks or problems that may arise and will work to find solutions to mitigate their effects.
- Conduct quality control checks:Regular quality control checks throughout the manufacturing process can help identify any issues early on and prevent them from becoming more significant problems down the line.
Intellectual Property Protection
Intellectual property (IP) refers to the creations of the mind, such as inventions, designs, and artistic works, protected by law. IP protection is essential for businesses and individuals to safeguard their ideas and prevent others from using them without permission. This blog post will discuss the importance of intellectual property protection and some ways to protect your IP.
Why is Intellectual Property Protection Important?
IP protection is crucial for several reasons:
- It protects your business’s competitive advantage: Intellectual property gives companies a competitive edge in the marketplace. For example, if you have a patent for a new product, you can prevent others from making or selling that product, giving your business a competitive advantage.
- It helps you generate revenue:IP protection allows you to license your intellectual property to others and generate revenue through royalties.
- It promotes innovation: Intellectual property protection encourages innovation by incentivizing inventors and creators to develop new ideas and products.
Ways to Protect Your Intellectual Property
- Conduct a comprehensive search:Before filing for any form of IP protection, it’s essential to conduct a thorough search to ensure that your idea is unique and does not infringe on the rights of others. To ensure originality, searching for any previous patents, trademarks, or copyrights that may already exist is necessary.
- File for patents, trademarks, and copyrights: Depending on your invention or creative work, you may need to file for patents, trademarks, or copyrights. A patent protects a design, a trademark protects a brand, and a copyright protects creative works. Filing for these forms of protection can help prevent others from using or copying your ideas.
- Use non-disclosure agreements (NDAs):An NDA is a legal agreement that can help protect your IP when sharing it with others. It establishes a confidential relationship between parties and prevents the recipient from disclosing your idea to others without your permission.
- Monitor for infringement: Monitoring for infringement involves monitoring the market for unauthorized use of your intellectual property. It’s essential to conduct regular online searches to protect your intellectual property. One way to protect your inventions or creative works is by searching for unauthorized copies and monitoring trade shows for any products infringing on your intellectual property.
- Enforce your rights:If you discover that someone is using your intellectual property without your permission, it’s essential to take action. One may consider taking legal action or sending a cease-and-desist letter to prevent infringement.
Finalizing the Manufacturing Process and Receiving Your Products
When bringing a product to market, finalizing the manufacturing process and receiving the finished product is an exciting and crucial step. Now is the time to see the results of your hard work and meticulous planning. However, there are some important considerations to remember to ensure everything goes smoothly and your product arrives as expected.
Here are some tips for finalizing the manufacturing process and receiving your products:
- Double-check everything before finalizing the production:It’s essential to ensure everything is in order before giving the green light for mass production. It’s necessary to thoroughly review the design, materials, and manufacturing process to ensure accuracy and reliability. Any issues found during the show can be expensive to fix, so addressing any potential problems beforehand is essential.
- Stay in close communication with your manufacturer: Maintaining open contact with your manufacturer is crucial to ensure everything runs smoothly. I am committed to keeping you informed by providing frequent updates, answering your inquiries, and promptly addressing any concerns you may have. Good communication can help ensure the production process is smooth.
- Be flexible with timelines: Production timelines can sometimes shift, so it’s essential to be flexible with deadlines. It’s better to receive a quality product a few days later than expected than to receive a defective product on time. Make sure you have contingency plans in place for any unexpected delays.
- Arrange for product testing:Before shipping your products, it’s a good idea to arrange for product testing. One of the areas we cover is testing for quality control, performance, and safety. Testing can help ensure that your product meets all required standards and regulations.
- Choose a reliable shipping method:When shipping your products, choosing a reliable and trustworthy shipping method is essential. Selecting a dependable carrier, using appropriate packaging, and securing sufficient insurance is crucial to ensure a smooth shipping process.
Conclusion
Low volume manufacturing services offer small businesses a cost-effective solution to producing small quantities of products without incurring high costs. These services provide fast turnaround times, flexible manufacturing processes, high-quality end products, and various materials and techniques. By selecting the right low volume manufacturing service provider and communicating effectively with them, small businesses can successfully bring their products to market while staying competitive in their industry.