Injection Mould Manufacturing
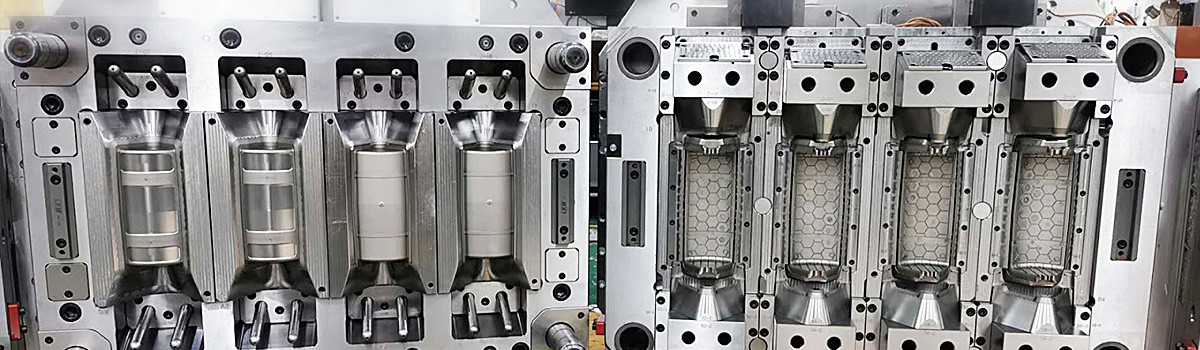
Plastics are a material commonly used for products across a variety of industries. Toys, automotive components, medical devices, tools, and more are all made from plastic. Many of the plastic items or we encounter in our every-day-lives are produced by manipulating melted resin into a specified design with manufacturing process called plastic injection molding. This highly efficient process can make parts in many sizes and shapes and can replicate the same part multiple times using the same mold. At the heart of this process is the mold, also known as tooling. A high-quality mold manufacturing process is essential to producing quality parts while maintaining a cost effective performance. Part quality will go up and overall project costs will go down when investing in high quality mold manufacturing.
Injection Molding Process Steps
Injection molding is one of the most common manufacturing processes used to produce plastic goods. It is a high-demand process that can reproduce the same part thousands of times. The process starts with a Computer Aided Design (CAD) file that contains a digital copy of the part. The CAD file is then used as a set of instructions to aid in the mold manufacturing process. The mold, or tool, is typically made from two pieces of metal. A cavity in the shape of the part is cut into each side of the mold. This mold is usually made from aluminum, steel, or an alloy.
After mold production, the next step is to select the proper plastic material. Material selection will depend on the how the final part will be used. Plastic materials have a variety of characteristics to consider. This includes over all appearance and feel, as well as resistance to chemicals, heat, and abrasion. Speak with the experts at DJmolding to learn more about available plastic materials for injection molding.
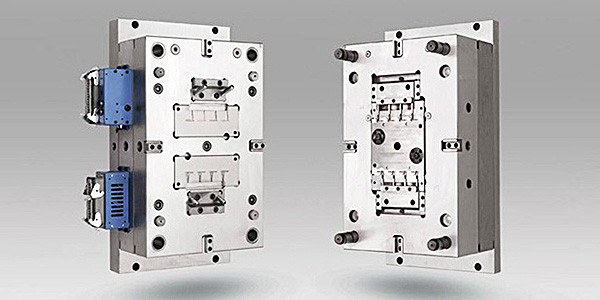
The selected material begins as a plastic pellet that is fed into a hopper on the injection-molding machine. The pellets make their way through a heated chamber where they are melted, compressed, and then injected into the mold cavity. Once the part cools, the two halves of the mold open to eject the part. The machine then resets to begin the process again.
What Material is used for Making Molds?
Mold production is done with steel, aluminum, or an alloy. DJmolding uses high-quality steel for mold manufacturing. Steel mold production is slightly more expensive than using aluminum or an alloy. The higher cost is typically offset by a much longer life span for steel molds. Aluminum molds, while cheaper to produce, do not last as long as steel and must be replaced frequently. Steel molds will typically last well over one hundred thousand cycles. Aluminum molds will need replacement much more frequently. Steel mold production can yield highly complex designs not achievable with aluminum. Steel molds can also be repaired or modified with welding. Aluminum molds will need to be machined from scratch if the mold is damaged or to accommodate changes. High-quality steel molds can be used thousands, hundreds of thousands, and sometimes up to a million cycles.
Injection Mold Components
Most injection molds are made up of two parts – an A side and a B side, or the cavity and the core. The cavity side is typically the best side while the other half, the core, will have some visual imperfections from the ejector pins that push the finished part out of the mold. An injection mold will also include support plates, ejector box, ejector bar, ejector pins, ejector plates, sprue bushing, and a locating ring.
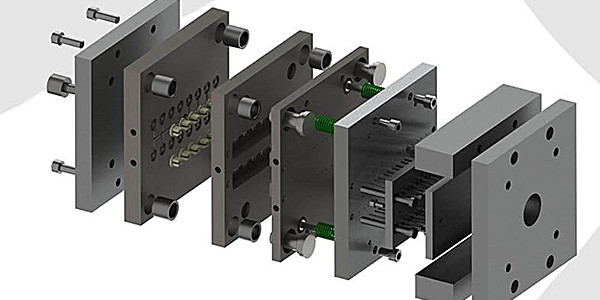
Injection molding is a manufacturing process with a lot of moving pieces. Below are a list of terms that describe many of the pieces necessary for mold production and injection molding. The tooling consists of several steel plates within a frame. The mold frame is placed into the injection-molding machine and held in place with clamps. A cut away of an injection mold viewed from the side would resemble a sandwich with many different layer. Check out our Injection Molding Glossary for a full list of terms.
Mold Frame or Mold Base: A series of steel plates that holds the mold components together, including cavities, cores, runner system, cooling system, and ejection system.
A Plate: One half of the metal mold. This plate does not contain moving parts. Can contain either cavity or core.
B Plate: The other half of the metal mold. The plate contains moving parts or space to allow moving parts to interact with the finished part – typically the ejector pins.
Support Plates: Steel plates within the mold frame that provides stability during the molding process.
Ejector Box: Contains the ejector system used to push the finished part out of the mold.
Ejector Plates: A steel plate that contains the ejector bar. The ejector plate moves to eject the finished product after molding.
Ejector Bar: Part of the ejector plate. The ejector pins are connected to the ejector bar.
Ejector Pins: Steel pins that contact the finished part and push it out of the mold. Ejector pin marks are visible on some injection-molded items, typically a round imprint found on the back of the part.
Sprue Bushing: The connecting piece between the mold and the injection-molding machine where the molten resin will enter the cavity.
Sprue: The spot on the mold frame where molten resin enters the mold cavity.
Locator Ring: Metal ring that ensures the nozzle of the injection-molding machine interfaces properly with the sprue bushing.
Cavity or Die Cavity: Concave impression in mold, usually forming the outer surface of the molded part. Molds are designated as single cavity or multi-cavity depending on the number of such depressions.
Core: Convex impression in the mold, usually forming the inner surface of the molded part. This is a raised portion of the mold. It is the inverse of the cavity. Molten resin is always pushed into the cavity, filling the space. The molten resin will form around the raised core.
Runner or Runner System: Channels within the metal mold that allow molten resin to flow from sprue-to-cavity or cavity-to-cavity.
Gate: The end of a runner where the melted resin enters the mold cavity. There are different gate designs for different application. Commonly used gate types include pin, spoke, fan, edge, disk, fan, tunnel, banana or cashew, and chisel. Gate design and placement are important considerations before starting the mold manufacturing process.
Cooling System: A series of channels in the outer shell of the mold. These channels circulate a fluid to aid the cooling process. Improperly cooled parts may display a variety of surface or structural defects. The cooling process typically makes up the majority of the injection molding cycle. Reducing cooling times can significantly improve mold efficiency and lower cost. Fathom offers Conformal Cooling for many injection-molding applications that will increase mold efficiency up to 60%
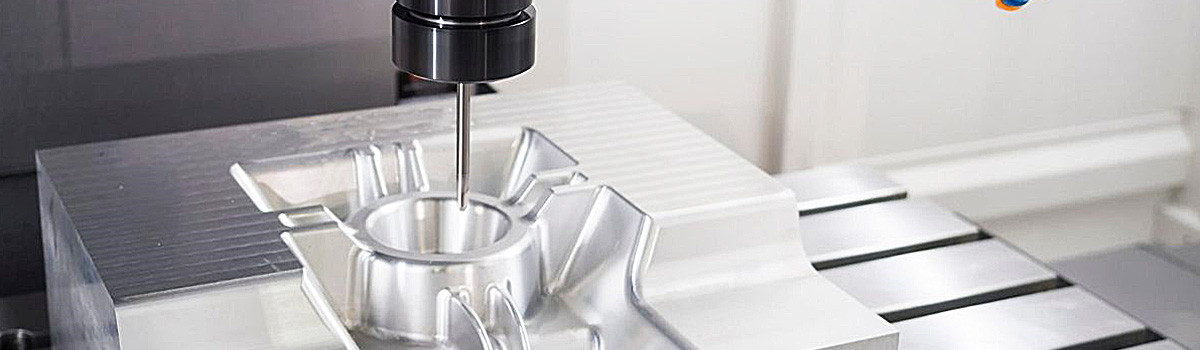
DJmolding mould Manufacturing for Different Molding Processes
The plastic injection molding process can be adjusted to accommodate different and complex needs. While it is ideal for manufacturing large volumes of simple plastic parts, it can also be used to create incredibly intricate parts with complex geometries or assemblies.
Multi-Cavity or Family Mold – This mold has multiple cavities in a single mold frame that produce several of the same or related parts with each injection cycle. This is an ideal way to increase run volumes and lower the per-piece-price.
Overmolding – This injection molding method is used to create parts made with two different types of plastic. A good example of this would be a portable drill body or game controller with a hard outer shell with soft, rubberized grips. A previously molded part is re-inserted into a specially made mold. The mold is closed and a second layer of different plastic is added over the original part. This is an ideal process when two different textures are desired.
Insert Molding – An injection molding process that allows for the incorporation of metal, ceramic, or plastic pieces into the final part. The metal or ceramic parts are placed in the mold and then melted plastic is injected into the mold to create a seamless piece made of two different materials. Insert molding is ideal for automotive applications as it is an innovative way to reduce weight and reduce costly material like metal. Instead of making the entire piece out of metal, only the connecting pieces need to be metal while the rest of the item will be made out of plastic.
Co-Injection Molding – Two different polymers are sequentially or concurrently injected into a cavity. This process can be used to create parts with a skin of one kind of plastic with the core of another.
Thin-Wall Molding – A form of injection molding that focuses on shorter cycle times and higher productivity to produce thin, light, and cheap plastic parts.
Rubber Injection – Rubber is injected into a mold using a process similar to plastic injection molding. Rubber parts require more pressure for successful injection molding.
Ceramic Injection – Injection molding process utilizing ceramic material. Ceramic is a naturally hard, chemically inert material that is used in a variety of industries. Ceramic injection requires several extra steps; including sintering or curing the newly molded parts to ensure the characteristic durability.
Low-Pressure Plastic Injection Molding – Plastic parts that are produced at lower pressures. This is particularly useful for jobs that require an encapsulation of delicate parts, such as electronics.
Contact DJmolding for more information on plastic injection molding. Our team of experts can assist you with your plastic injection molded project.