Family Injection Molds

Family injection molds are a popular manufacturing process for producing various plastic products. They enable the simultaneous creation of multiple parts, resulting in cost savings and increased efficiency. However, it is crucial to understand how family injection molds work, the types of products they are best suited for, and their advantages and disadvantages before deciding whether this manufacturing process suits your project.
What is Family Injection Molds?
Family injection molds are molds used in the injection molding process to produce multiple parts or components simultaneously. Designers create them to accommodate various cavities or impressions within a single mold, enabling the production of different factors in a single molding cycle. Manufacturers often use family molds when there is a need to produce a set of related parts that are used together or have similar characteristics. This approach offers efficiency and cost savings by reducing tooling and setup time, maximizing productivity, and ensuring consistent quality across all parts produced.
How do Family Injection Molds Work?
Family injection molds are complex tools that operate through a well-defined process to produce multiple parts simultaneously. Here are some key points to understand how family injection molds work:
- Mold design: Designers carefully design family molds to accommodate multiple cavities or impressions within a single tool. Designers plan the mold layout to optimize the cavities’ arrangement and spacing, ensuring efficient production and consistent part quality.
- Material selection: We choose the appropriate thermoplastic material based on the desired properties and requirements for producing the parts. Factors such as strength, flexibility, heat resistance, and appearance are crucial in material selection.
- The injection molding process begins by heating the chosen thermoplastic material to its melting point, forming a molten resin. We inject the molten material into the mold cavity through a system of runners and gates, distributing the material to each hole.
- Cooling and solidification:Once the molten material fills the cavities, it cools and solidifies. Cooling channels within the mold help regulate the temperature and facilitate solidification. Proper cooling is critical to ensure consistent part dimensions, minimize warping, and promote efficient cycle times.
- Ejection of parts:After the material solidifies, we open the mold and eject the features from the mold cavities. We can accomplish ejection through various methods, including mechanical ejection systems, air blasts, or hydraulic ejector pins. We must prevent damage to the parts during the ejection process.
- Quality control: Throughout the production cycle, we implement measures to ensure that the parts meet the specified requirements. We closely monitor essential factors like temperature, pressure, and cycle times. We also perform visual inspections and dimensional checks.
- Maintenance and troubleshooting:Regular maintenance is necessary for the optimal performance of family molds. This maintenance includes cleaning, lubrication, and periodic checks for wear or damage. If issues arise during production, we may employ troubleshooting techniques to identify and address mold-related problems.
Advantages of Family Injection Molds
Family injection molds offer several advantages, making them a preferred choice in manufacturing. Here are some key points highlighting the benefits of using family injection molds:
- Increased productivity: Family molds enable the simultaneous production of multiple parts, reducing cycle times and increasing overall productivity. With each molding cycle producing multiple components, manufacturers can achieve higher output rates and meet large volume demands efficiently.
- Cost savings: By producing multiple parts in one cycle, family injection molds help reduce manufacturing costs. Eliminating the need for separate molds for each component results in tooling costs, maintenance, and storage savings. Additionally, optimized production efficiency and reduced material waste contribute to cost savings.
- Time efficiency:Manufacturers can significantly reduce production lead times with family molds. The ability to produce multiple parts in a single cycle eliminates the need for sequential tooling or mold changes, saving valuable time. This accelerated production process enables faster time-to-market and quicker response to customer demands.
- Consistency and quality:Family injection molds ensure consistent part quality across all cavities. Simultaneously producing components within the same mold ensures uniformity in dimensions, appearance, and material properties. This manufacturing process minimizes variations and ensures all parts meet the required specifications.
- Design flexibility: Family molds offer design flexibility, allowing for the production of multiple components with different shapes, sizes, or features within a single tool. This versatility makes them suitable for manufacturing products with complex geometries, customized parts, or variations in design.
- Reduced material waste: With family molds, material waste is minimized compared to using separate molds for each part. The optimization of mold layout, gating systems, and runner designs helps reduce material scrap and improves material utilization, contributing to a more sustainable and cost-effective manufacturing process.
- Streamlined assembly:Family injection molds facilitate streamlined assembly processes. As we produce the parts simultaneously, assembly operations become more efficient, reducing labor costs and assembly time. Additionally, pieces produced by family molds often feature compatible mating surfaces and precise dimensions, making assembly easier and ensuring proper fitment.
The advantages of family injection molds, including increased productivity, cost savings, time efficiency, consistent quality, design flexibility, reduced material waste, and streamlined assembly processes, make them a valuable tool for high-volume manufacturing, offering improved profitability and competitive advantages in the market.
Disadvantages of Family Injection Molds
While family injection molds offer numerous benefits, there are also some potential disadvantages. Here are some key points highlighting the drawbacks of using family injection molds:
- Initial cost:Family molds typically require a higher initial investment than single-cavity molds. The design complexity and the need for precise cavity arrangements increase tooling costs, making it a significant upfront expense for manufacturers. This initial cost may challenge businesses with limited budgets or low production volumes.
- Design limitations:Designing a family mold requires careful consideration of the part geometry, size, and compatibility within the mold. Specific complex or large parts may not be suitable for family molding due to limitations in cavity spacing, cooling requirements, or ejection mechanisms. Regulations in design may require the use of customized molds for specific parts.
- Tooling and maintenance complexity:Family molds can be more intricate than single-cavity molds. The presence of multiple cavities, runners, and gating systems requires meticulous maintenance and occasional repairs. Maintenance tasks can be time-consuming and may require skilled technicians. Any issues or repairs within the mold can simultaneously affect the production of multiple parts.
- Limited flexibility:While family molds offer design flexibility within the mold, changes or modifications to individual components can be challenging. Altering the design or specifications of one part within the family mold may require adjustments to the entire mold, affecting the production of all parts. This lack of flexibility can be a limitation for manufacturers that require frequent design changes or customization.
- Risk of production disruption:In the event of a molding failure or damage, the production of multiple parts can be interrupted. Detecting a defect in one cavity may affect the entire batch of parts produced within the family mold. This risk of production disruption can significantly impact overall manufacturing timelines and delivery schedules.
- Volume requirements:Volume requirements play a crucial role in determining the suitability of family molds for production. Due to their cost-effectiveness and efficiency, family molds are the best option for producing high volumes of products, making them an excellent choice. However, family molds may not be economically viable for low-volume production or prototyping. Opting for single-cavity molds or alternative manufacturing methods may be more practical.
Understanding the potential disadvantages of family injection molds is crucial in making informed decisions regarding their implementation. While these drawbacks exist, proper planning, maintenance, and consideration of specific production requirements can mitigate them.
Types of Family Injection Molds
Family injection molds come in various types, each designed to accommodate different production needs and requirements. Here are some key types of family injection molds:
- Side-by-side family mold:This type of mold consists of multiple cavities arranged side-by-side, with each hole producing a different component. The mold design ensures that each niche is isolated, allowing for individual injection control and minimal part-to-part interference.
- Tandem family mold:Tandem family molds have multiple cavities arranged in a linear sequence, each producing a different component. The mold design enables the production of more extended parts or those with various features in a linear configuration.
- Stack family mold: Stack family molds have multiple sets of cavities stacked on each other. Each group produces a different component, allowing for the production of several different parts in one cycle. The stack design also enables the production of tall or vertical parts with minimal tooling.
- Rotary family mold: This mold has multiple cavities arranged on a rotary table. The injection molding machine rotates the mold to each cavity position during production, enabling the production of various parts with a single device. The rotary design allows the production of symmetrical components, such as gears or wheels.
- Hot runner family mold:Hot runner family molds utilize a hot runner system to distribute the plastic melt to each cavity. This design eliminates the need for runners or gates, allowing for cleaner part production and reduced material waste. Hot runner family molds are suitable for high-volume production.
Each type of family injection mold has unique advantages and limitations, and selecting the most appropriate style depends on the production requirements, part geometry, and material properties. Choosing the right type of family mold can significantly enhance manufacturing efficiency and profitability.
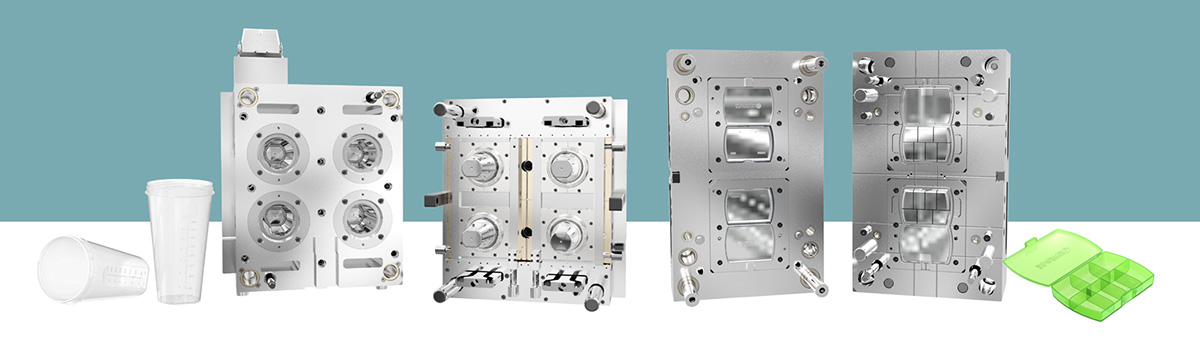
Single Cavity vs. Multi-Cavity Molds
Regarding injection molding, manufacturers can choose between single and multi-cavity molds, offering distinct advantages and considerations. Here are some key points comparing single-cavity molds and multi-cavity molds:
Single Cavity Molds:
- Simplicity: Single cavity molds consist of one cavity, producing a single part in each molding cycle. They are relatively straightforward in design and construction, making them less complex and easier to manufacture.
- Flexibility:Single cavity molds offer greater flexibility regarding design changes or modifications. If a specific part requires a design change, only the mold for that part must be modified, minimizing the impact on the production process.
- Prototyping and low-volume production:Single cavity molds are well-suited for prototyping or low-volume show runs. They allow for efficient testing of new designs or producing small quantities of parts without high initial investments.
- Higher per-part cost:Single cavity molds are less cost-effective for high-volume production as they make fewer parts per molding cycle. The price per part is generally higher than multi-cavity molds due to higher tooling costs and longer cycle times.
Multi-Cavity Molds:
- Increased productivity:Multi-cavity molds have multiple cavities, producing various parts in each molding cycle. This method can significantly increase productivity and production output while reducing manufacturing costs and cycle times.
- Cost efficiency:Multi-cavity molds offer cost advantages for high-volume production. They require lower tooling costs per part produced, making them more cost-effective in large-scale manufacturing operations.
- Consistency and uniformity:Multi-cavity molds ensure consistent part quality across all cavities, as they are produced simultaneously under the same process conditions. This results in all parts’ consistent dimensions, appearance, and material properties.
- Space and equipment requirements:Multi-cavity molds require larger injection molding machines with sufficient clamping force to accommodate the larger tool size. They also need adequate space for multiple cavities, runners, and cooling channels.
- Design considerations:Designing multi-cavity molds requires careful consideration of cavity spacing, gating systems, and cooling requirements. Complex geometries or large parts may pose limitations or require additional design considerations.
Hot Runner vs. Cold Runner Molds
Hot and cold runner molds are two distinct types of injection molds, each with advantages and considerations. Here are some key points comparing hot runner molds and cold runner molds:
Hot Runner Molds:
- Efficient material usage: Hot runner molds utilize a system of heated channels and nozzles to deliver molten plastic directly to the mold cavities. Eliminating the need for runners and gates reduces material waste and optimizes material usage.
- Reduced cycle times:Eliminating runners in hot runner molds leads to shorter cycle times than in cold runner molds. This increased efficiency translates to higher production output and improved overall productivity.
- Consistent part quality: Hot runner molds provide more consistent part quality, as the molten plastic remains at a constant temperature throughout the process—this results in uniform fill and reduced part dimensions, appearance, and material properties variations.
- Flexibility and design options:Hot runner systems offer greater design flexibility, allowing for more complex geometries and producing parts with multiple gates. This versatility can benefit features requiring balanced filling or specific gating requirements.
Cold Runner Molds:
- Lower initial cost:Cold runner molds are generally less expensive to manufacture and set up than hot runner molds. They do not require the additional components and heating elements associated with hot runner systems, resulting in lower tooling costs.
- Material compatibility:Cold runner molds are suitable for a wide range of materials, including those that are heat-sensitive or prone to degradation when exposed to prolonged heating. This versatility makes cold runner molds preferred for specific materials and applications.
- Simplified maintenance:Cold runner molds are often easier to maintain and troubleshoot than hot runner molds. The absence of complex heating systems and components simplifies maintenance tasks, reducing downtime and production interruptions.
Reduced equipment complexity: Standard injection molding machines can use cold runner molds without requiring specialized hot runner controllers. Manufacturers with existing equipment or who prefer a more straightforward setup can benefit.
The choice between hot and cold runner molds depends on production volume, material requirements, part complexity, and budget considerations. Manufacturers should carefully evaluate their needs and consult with mold experts to determine the most suitable option for their injection molding processes.
Two-Plate vs. Three-Plate Molds
Two-plate and three-plate molds are two common types of injection molds used in the manufacturing industry. Here are some key points comparing two-plate molds and three-plate molds:
Two-Plate Molds:
- Simplicity: Two-plate molds consist of two main plates that separate to eject the molded part. The simplicity of the design makes them easier to manufacture, set up, and maintain compared to three-plate molds.
- Cost efficiency:Two-plate molds are generally more cost-effective, requiring fewer components and less complex tooling. The reduced number of plates and more straightforward construction contribute to lower tooling costs.
- Limited gating options:Two-plate molds typically have restricted gating options, with runners and gates positioned on one side of the mold. This limitation can affect the design and gating flexibility, particularly for more complex or significant parts.
Three-Plate Molds:
- Part ejection flexibility: Three-plate molds provide more flexibility in part ejection. The additional plate, the stripper plate, allows for the separate ejection of the runners and the molded part. This method enables the production of complexly designed parts, materials requiring multiple entry points, and hard-to-reach areas during manufacturing.
- Enhanced part quality:Three-plate molds offer improved part quality by effectively separating the runners and gates from the molded part. This separation reduces the chances of gate marks or cosmetic defects on the final product, resulting in a higher-quality finished part.
- Increased design complexity:Three-plate molds allow for more complex part designs and the inclusion of features such as side actions, lifters, or slides. This design versatility can be advantageous when producing parts with intricate geometries or requiring additional features beyond a simple core and cavity.
- Longer cycle times: Three-plate molds typically have longer cycles than two-plate molds. The additional plate and complexity in mold movement contribute to increased cycle times, affecting overall production efficiency.
Choosing between two-plate and three-plate molds depends on factors such as part complexity, gating requirements, desired part quality, and cost considerations. Manufacturers should evaluate their specific needs and consult with mold experts to determine the most suitable option for their injection molding processes.
Material Selection for Family Injection Molds
Material selection for family injection molds is a critical factor that can significantly impact the manufacturing process and the final parts’ quality. Here are some key points to consider when selecting materials for family injection molds:
- Mold base material:The mold base material should have excellent mechanical properties, dimensional stability, and thermal conductivity. Common choices include steel alloys, such as P20 or H13, which provide good hardness, wear resistance, and durability for extended mold life.
- Cavities and cores:The material for cavities and cores should have high hardness, wear resistance, and heat resistance to withstand molding and repeated use. Common materials for cavities and cores include hardened tool steels like S136 or 420 stainless steel or high-speed steels like M2.
- Runner system:Materials with good thermal conductivity and wear resistance are preferred for the runner system to ensure efficient melt flow and minimize material degradation. Due to their excellent thermal properties, manufacturers commonly use copper alloys or beryllium copper for runner inserts.
- Hot runner components:When utilizing hot runner systems, materials with high heat resistance, excellent thermal stability, and good flow properties are necessary. Common choices for hot runner components include stainless steels like 420 or 17-4 PH or specialty alloys like Inconel or Hastelloy for demanding applications.
- Cooling channels:Manufacturers commonly use copper alloys or beryllium copper for cooling channels due to their high thermal conductivity. These materials help in efficient heat dissipation and maintaining consistent mold temperatures.
- Ejector pins and slides:Ejector pins and slides require materials with good wear resistance, high hardness, and sufficient toughness. Common choices include H13 tool steel, D2 tool steel, or stainless steel grades like 420 or 440C.
When selecting materials for family injection molds, it is essential to consider material properties, mold complexity, production volume, and cost. Collaborating with material suppliers, mold designers, and experts can help determine the most suitable materials that meet the specific requirements and optimize the performance and longevity of the mold.
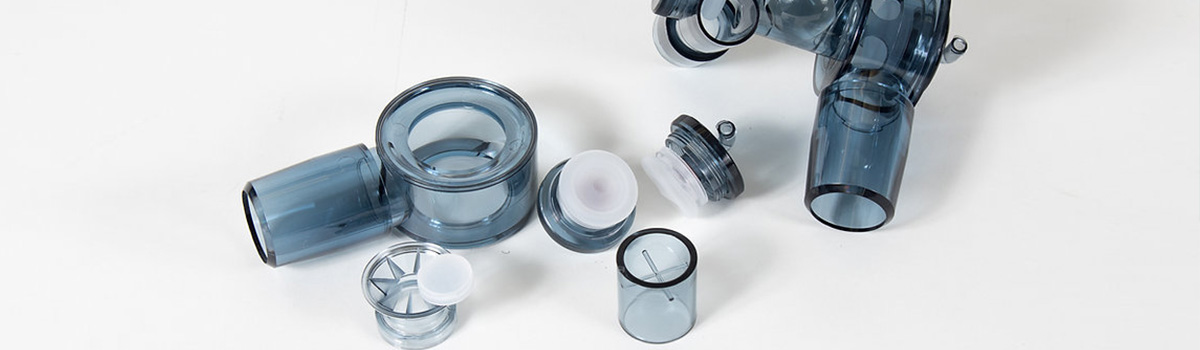
Design Considerations for Family Injection Molds
Designing family injection molds requires careful consideration for optimal functionality, efficiency, and part quality. Here are some key design considerations for family injection molds:
- Part compatibility: Analyze the compatibility of different parts within the family mold, considering size, geometry, and material properties. Ensure the production process efficiently produces the pieces together without interference or quality issues.
- Cavity arrangement: Determine the best performance of cavities within the mold to optimize space utilization and part production efficiency. Consider factors like part orientation, gating locations, and cooling requirements to achieve balanced filling and consistent part quality.
- Runner and gating system: Design an effective runner and gating system that allows for efficient material flow to each cavity while minimizing waste and pressure drop. Consider the type of gating (e.g., edge gates, sub gates, or hot runners) and the placement of gates to achieve optimal filling and avoid part defects.
- Cooling system:Implement an appropriate cooling system to ensure consistent cooling and efficient heat dissipation. Optimize cooling channel design, positioning, and diameter to achieve uniform temperature distribution and minimize cycle times.
- Ejection mechanism: Develop a robust ejection mechanism to facilitate the removal of parts from the mold. Consider the type of ejection (e.g., ejector pins, slides, or lifters) and their positioning to ensure proper part release without causing damage or deformation.
- Venting:Proper venting is crucial to prevent air traps and achieve complete filling of the mold. Ensure adequate vents are incorporated to allow air to escape during the injection process, reducing the risk of defects like short shots or gas porosity.
- Mold maintenance and accessibility:Design the mold for easy maintenance, repair, and cleaning. Consider accessibility to critical components like slides, cores, and ejector pins to facilitate maintenance tasks and reduce downtime.
- Mold strength and rigidity:Ensure the mold design is structurally sound and capable of withstanding the forces and pressures exerted during the injection molding process. Consider factors like mold material selection, ribbing, and support structures to maintain mold integrity.
By carefully addressing these design considerations, manufacturers can optimize family injection molds’ performance, efficiency, and longevity, resulting in high-quality parts and streamlined production processes. Collaborating with experienced mold designers and engineers can provide valuable insights and expertise to achieve an optimal design.
Applications of Family Injection Molds
Family injection molds offer several applications across various industries, providing cost-effective solutions for producing multiple components in a single molding cycle. Here are some critical applications of family injection molds:
- Consumer products:Manufacturers widely use family molds to produce consumer products such as electronics, appliances, and household items. They enable the simultaneous production of different parts or components, reducing manufacturing time and costs.
- Automotive industry:Family injection molds find extensive use in the automotive sector for manufacturing various components like interior trim, dashboard parts, door panels, and engine components. Producing multiple parts in a single cycle enhances productivity and cost efficiency in automotive manufacturing.
- Medical devices: Family molds are crucial in producing medical devices and equipment, including syringe components, drug delivery systems, surgical instruments, and diagnostic devices. The efficient production of multiple parts ensures faster turnaround times and cost savings in the medical industry.
- Packaging:The packaging industry employs family injection molds to produce components such as caps, closures, containers, and packaging inserts. By manufacturing multiple parts simultaneously, family molds enhance production efficiency and enable quicker response to market demands.
- Electrical and electronic components:Manufacturers extensively use family molds to produce electrical and electronic components, such as connectors, switches, housing parts, and circuit board components. They enable the efficient production of multiple elements with consistent quality and reduced cycle times.
- Aerospace industry:Family molds find applications in the aerospace sector for manufacturing components like interior cabin parts, seating components, and air ducts. Producing multiple parts in a single cycle enhances production efficiency and cost-effectiveness.
- Industrial equipment:Manufacturers utilize family molds to produce industrial equipment and machinery components, including gears, bearings, valves, and connectors. By streamlining the manufacturing process and reducing production time, family molds contribute to improved productivity and cost savings.
Family injection molds offer significant advantages in efficiency, cost savings, and streamlined production for various industries. Their versatility and ability to produce multiple parts in a single cycle make them a valuable tool for manufacturers seeking optimized injection molding processes.
Consumer Goods Industry
The consumer goods industry encompasses a wide range of products purchased and used by individuals for personal or household purposes. It is a diverse industry with various sectors and markets. Here are some key points about the consumer goods industry:
- Product variety:The consumer goods industry offers many products, including food and beverages, personal care items, household goods, electronics, clothing, and more. This industry caters to consumers’ everyday needs and preferences, providing various choices.
- Market demand:Consumer demand and preferences drive the production of consumer goods. As consumer tastes and preferences evolve, the industry must adapt and innovate to meet changing needs. Consumer trends, such as sustainability, convenience, and personalized products, heavily influence the industry’s direction.
- Global market:The consumer goods industry operates globally, with products being manufactured, distributed, and sold internationally. Globalization has expanded market opportunities, allowing companies to reach a broader customer base and engage in cross-border trade.
- Branding and marketing: Effective branding and marketing strategies are crucial in the consumer goods industry to differentiate products, build brand loyalty, and influence consumer purchasing decisions. Companies invest heavily in advertising, promotions, packaging design, and brand-building activities to create strong connections with consumers.
- Supply chain and distribution:The consumer goods industry depends on efficient supply chain management to ensure manufacturers produce, distribute, and deliver products to consumers promptly. It involves coordinating various stages, including sourcing raw materials, production, logistics, warehousing, and retailing.
- Consumer trends and innovation:To remain competitive, consumer goods companies must stay attuned to changing consumer trends and preferences. Innovation plays a vital role in developing new products, improving existing ones, and addressing emerging consumer needs and desires.
- Competition and market dynamics:The consumer goods industry is highly competitive, with numerous companies vying for market share. Market dynamics, such as pricing, quality, branding, and customer experience, heavily influence consumer choices and brand loyalty.
The consumer goods industry is dynamic and fast-paced, constantly adapting to meet evolving consumer demands. It plays a significant role in the global economy, driving employment, innovation, and economic growth.
Automotive Industry
The automotive industry is a vast sector encompassing the design, development, production, and sale of automobiles and related components. Here are some key points about the automotive industry:
- Vehicle manufacturing: The automotive industry is primarily engaged in the manufacturing of automobiles, including cars, trucks, SUVs, motorcycles, and commercial vehicles. It involves various stages: design, engineering, prototyping, production, assembly, and quality control.
- Supply chain: The automotive industry relies on a complex global supply chain, with numerous suppliers providing components, systems, and raw materials. Supply chain management is crucial in ensuring the timely delivery of parts to support vehicle production.
- Technological advancements: The automotive industry is at the forefront of technological advances, including electric and autonomous vehicles, connectivity features, advanced safety systems, and alternative fuel technologies. Innovations in vehicle electrification, autonomous driving, and connectivity are transforming the industry.
- Market competition:The automotive industry is highly competitive, with numerous automakers vying for market share as price, quality, performance, safety features, and brand reputation drive competition. Automakers continuously strive to differentiate their offerings and meet customer demands.
- Global market: The automotive industry operates globally, with production facilities, sales networks, and supply chains spanning different countries. Regional regulations, market preferences, economic conditions, and trade policies influence it.
- Environmental considerations:The automotive industry faces increasing pressure to address environmental concerns, including reducing carbon emissions, improving fuel efficiency, and promoting sustainable manufacturing practices. Automakers invest in developing electric and hybrid vehicles, lightweight materials, and eco-friendly manufacturing processes.
- Aftermarket services:The automotive industry includes a significant aftermarket segment, which distributes replacement parts, accessories, maintenance, repair services, and vehicle customization. Aftermarket activities contribute to the industry’s overall revenue and provide ongoing support to vehicle owners.
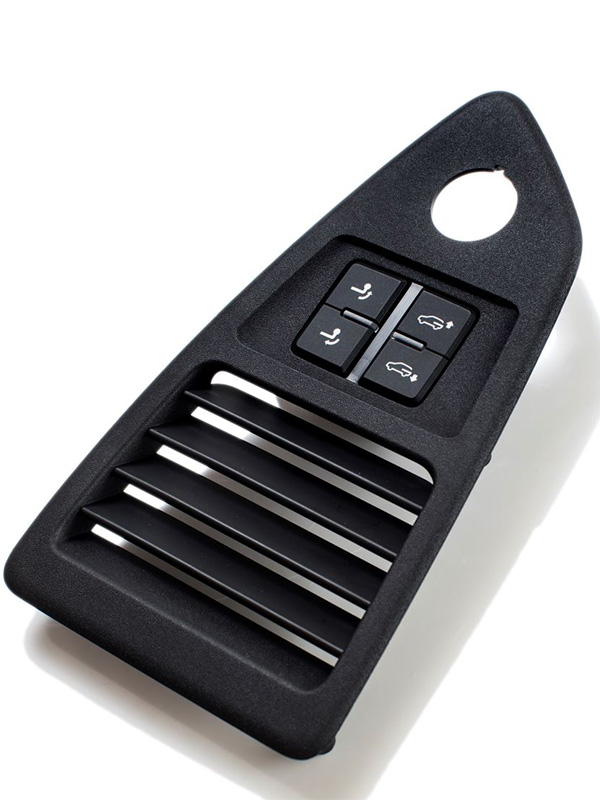
Medical Industry
The medical industry encompasses various sectors in developing, manufacturing, distributing, and delivering medical devices, equipment, pharmaceuticals, and healthcare services. Here are some key points about the medical industry:
- Medical devices:The medical industry is heavily involved in producing various medical devices, including diagnostic equipment, surgical instruments, implants, prosthetics, imaging systems, and monitoring devices. These devices are critical in patient diagnosis, treatment, and care.
- Pharmaceutical products:The medical industry encompasses pharmaceutical companies involved in the research, development, and manufacturing drugs and medications. Pharmaceuticals range from over-the-counter medications to prescription drugs for disease treatment, prevention, and management.
- Healthcare services:The medical industry includes healthcare providers, such as hospitals, clinics, nursing homes, and outpatient facilities. These entities offer patients medical care, diagnostics, treatment, rehabilitation, and other healthcare services.
- Research and development:The medical industry invests heavily in research and development (R&D) to advance medical knowledge, develop new treatments, improve existing therapies, and enhance patient outcomes. R&D efforts focus on drug discovery, clinical trials, medical technology innovation, and healthcare delivery systems.
- Regulatory compliance:The medical industry is subject to stringent regulatory frameworks to ensure patient safety, product efficacy, and ethical practices. Regulatory bodies, such as the Food and Drug Administration (FDA) in the United States, enforce standards and guidelines for medical devices, pharmaceuticals, clinical trials, and healthcare practices.
- Technological advancements: The medical industry continually embraces technological advances to enhance patient care, improve diagnostic accuracy, and facilitate medical procedures. Innovations such as telemedicine, electronic health records (EHR), robotics, AI-driven diagnostics, and precision medicine are transforming the industry.
- Global healthcare challenges:The medical industry addresses global healthcare challenges, including infectious diseases, chronic conditions, aging populations, access to healthcare in underserved areas, and rising healthcare costs. Industry stakeholders work towards developing solutions and improving healthcare delivery worldwide.
The medical industry plays a critical role in preserving and enhancing human health. It combines scientific research, technological innovation, manufacturing expertise, and healthcare services to improve patient outcomes, develop life-saving treatments, and advance the overall well-being of individuals worldwide.
Packaging Industry
The packaging industry plays a vital role in producing, designing, and distributing packaging materials and solutions for various products. Here are some key points about the packaging industry:
- Product protection: The primary function of packaging is to protect products during storage, transportation, and handling. Packaging materials provide physical protection against impacts, moisture, temperature variations, and other external factors that could damage the product.
- Branding and marketing:Packaging is a powerful tool for branding and marketing. Creating a distinctive brand identity, attracting consumer attention, and conveying product information are crucial. Packaging design elements like colors, logos, graphics, and labels help differentiate products and influence consumer purchasing decisions.
- Sustainability and eco-friendliness: The packaging industry increasingly focuses on sustainable practices and eco-friendly materials. Using recyclable, biodegradable, and renewable packaging materials helps reduce environmental impact and supports circular economy initiatives.
- Supply chain efficiency:Efficient packaging solutions contribute to streamlined supply chain operations. Well-designed packaging facilitates efficient handling, storage, and transportation of products, optimizing logistics processes and minimizing costs.
- Customization and innovation:The packaging industry embraces customization and innovative solutions to meet diverse customer needs and market demands. Customized packaging designs, sizes, and materials allow unique and tailored packaging solutions that align with specific product requirements.
- Industry sectors: The packaging industry caters to various sectors, including food and beverages, pharmaceuticals, personal care, household products, electronics, and industrial goods. Each industry has specific packaging requirements, such as barrier properties, tamper-evident features, or product-specific labeling regulations.
- Technological advancements:The packaging industry integrates technological advances to enhance packaging processes and capabilities. Automation, robotics, digital printing, innovative packaging, and track-and-trace systems are revolutionizing the packaging industry, improving efficiency, and enabling innovative functionalities.
The packaging industry is a dynamic sector that continuously adapts to changing consumer preferences, sustainability goals, and technological advancements. It is a crucial link between products and consumers, ensuring product integrity, brand recognition, and an enhanced customer experience.
Aerospace Industry
The aerospace industry is a technologically advanced sector focused on designing, manufacturing, and operating aircraft, spacecraft, satellites, and related components. Here are some key points about the aerospace industry:
- Commercial aviation:The aerospace industry encompasses commercial aviation, including commercial aircraft production, such as airplanes and helicopters. Major manufacturers, like Boeing and Airbus, lead the market in designing and manufacturing commercial aircraft for passenger and cargo transportation.
- Defense and military applications:The aerospace industry closely links to defense and military applications. It involves the production of military aircraft, uncrewed aerial vehicles (UAVs), and defense systems. These technologies are vital for national security, surveillance, reconnaissance, and combat operations.
- Space exploration and satellites: The aerospace industry plays a significant role in space exploration and satellite development. It involves designing, manufacturing, and launching spacecraft, satellites, and space probes for scientific research, communication, weather monitoring, and navigation systems.
- Technological advancements: The aerospace industry is at the forefront of technological advances, driving innovations in aerodynamics, materials, propulsion systems, avionics, and satellite technologies. Promotions include composite materials, fuel-efficient engines, advanced navigation systems, and satellite imaging technologies.
- Global collaboration:The aerospace industry often requires international cooperation due to the complex nature of projects and global demand. Collaboration between governments, aerospace companies, research institutions, and suppliers is common to pool resources, expertise, and funding for large-scale aerospace projects.
- Safety and regulations:Safety is paramount in the aerospace industry. Strict rules and certification processes ensure that aircraft and spacecraft meet rigorous safety standards. Regulatory bodies, such as the Federal Aviation Administration (FAA) and the European Aviation Safety Agency (EASA), enforce safety regulations and oversee airworthiness certifications.
- Supply chain management: The aerospace industry relies on a complex global supply chain that includes suppliers of materials, components, subsystems, and specialized equipment. Effective supply chain management ensures timely delivery, quality control, and compliance with industry standards.
The aerospace industry is a technologically advanced and highly regulated sector contributing to scientific progress, national defense, and global connectivity. It requires extensive collaboration, innovation, and precision engineering to meet the demanding requirements of aircraft and spacecraft operations.
Electronics Industry
The electronics industry is a dynamic sector that involves designing, manufacturing, and distributing electronic components, devices, and systems. Here are some key points about the electronics industry:
- Consumer electronics:The electronics industry produces various electronics, including smartphones, televisions, laptops, tablets, cameras, and home appliances. These products are designed for personal and recreational use and often incorporate advanced technologies and features.
- Semiconductor industry:Electronics heavily relies on semiconductors to produce integrated circuits (ICs), microchips, and electronic components. Semiconductors are fundamental building blocks in electronic devices, enabling computing, memory storage, communication, and control functions.
- Research and development:Research and development (R&D) is a crucial aspect of the electronics industry. Companies invest in R&D to innovate and develop new technologies, improve existing products, and meet emerging consumer needs. R&D efforts focus on miniaturization, energy efficiency, connectivity, and artificial intelligence (AI).
- Global supply chain:The electronics industry operates globally, with a complex supply chain involving suppliers of raw materials, electronic components, manufacturing equipment, and distribution networks. Global collaboration is essential to source materials, produce parts, and assemble electronic devices.
- Manufacturing processes: Electronics manufacturing involves various methods, including printed circuit board (PCB) assembly, surface mount technology (SMT), chip packaging, and final product assembly. These processes require precision engineering, quality control, and adherence to industry standards.
- Market competition: The electronics industry is highly competitive, with numerous companies vying for market share. Companies differentiate themselves through product features, design aesthetics, pricing, brand reputation, and customer service. The industry experiences rapid product obsolescence and requires continuous innovation to stay competitive.
- Emerging technologies:The electronics industry drives the development and adoption of emerging technologies, including advancements in AI, the Internet of Things (IoT), virtual reality (VR), augmented reality (AR), wearable devices, and innovative home technologies. These technologies are shaping various sectors, including healthcare, automotive, and entertainment.
The electronics industry is a vital sector influencing various aspects of modern life. It continuously evolves to meet the demands of consumers and businesses, enabling connectivity, productivity, and technological advancements. The industry’s ability to innovate, manufacture high-quality products, and meet market demands contribute to its significance in the global economy.
Sports Equipment Industry
The sports equipment industry is a diverse sector encompassing the design, manufacturing, and distribution of equipment and gear used in various sports and recreational activities. Here are some key points about the sports equipment industry:
- Sporting goods:The sports equipment industry produces a wide range of sporting goods, including equipment for team sports (such as soccer, basketball, and hockey), individual sports (such as tennis, golf, and running), water sports (such as swimming and surfing), outdoor activities (such as camping and hiking), and fitness (such as gym equipment and accessories).
- Performance and safety: Sports equipment manufacturers prioritize performance and safety in their designs. Engineers design equipment to enhance athletes’ performance, optimize their skills, and protect them from injuries. We use advanced materials, ergonomic methods, and strict adherence to safety standards to ensure safety.
- Innovation and technology:The sports equipment industry constantly embraces innovation and technology to improve product performance and user experience. Innovations include lightweight materials, aerodynamic designs, advanced cushioning systems, intelligent sensors, and wearable technology. These advancements improve performance, injury prevention, and athlete data tracking.
- Customization and personalization: The sports equipment industry recognizes the importance of customization and personalization. Many manufacturers offer customization options, such as selecting colors, adding logos, or tailoring equipment to fit individual athletes’ specifications. Providing a personalized experience can boost athletes’ sense of identity.
- Sponsorships and endorsements:The sports equipment industry relies on support and acceptance from professional athletes and sports teams to build brand recognition and credibility. Collaborations between equipment manufacturers and athletes often involve product development, testing, and marketing partnerships.
- Sustainability:The sports equipment industry increasingly focuses on sustainability and environmental responsibility. Manufacturers employ eco-friendly materials, reduce waste in production processes, and promote recycling programs. Sustainable practices aim to minimize the industry’s environmental impact and support long-term sustainability.
- Global market:The sports equipment industry operates globally, with products manufactured and distributed worldwide. The enterprise caters to diverse markets and cultural preferences, adapting products to meet different regions’ and sports’ specific needs and preferences.
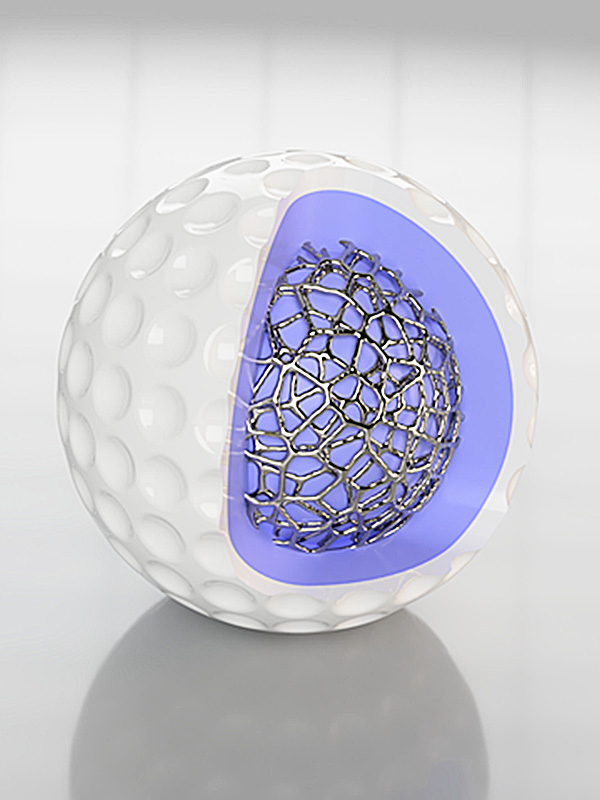
The sports equipment industry supports athletes, promotes physical activity, and enhances sports performance. Continuous innovation, adherence to safety standards, and customization options contribute to the industry’s growth and ability to meet the evolving demands of athletes and sports enthusiasts.
Toys and Games Industry
The toys and games industry is a vast sector that includes designing, manufacturing, and distributing toys and games for children and adults. Here are some key points about the toys and games industry:
- Types of toys and games: The toys and games industry produces a wide range of products, including traditional toys such as dolls, action figures, and puzzles, as well as electronic toys, board games, card games, and video games. The industry caters to diverse interests, ages, and skill levels.
- Innovation and technology:The toys and games industry continuously evolves, with manufacturers employing innovative technology to create new products and enhance user experience. To create engaging and immersive experiences, we can incorporate virtual, augmented reality, and interactive elements.
- Safety and quality: Safety and quality are essential considerations for the toys and games industry. Manufacturers must comply with safety regulations and standards to ensure their products do not harm consumers. To ensure the quality of our products, we conduct thorough testing, implement strict quality control measures, and continuously monitor them.
- Licensing and branding: Many toys and games are based on popular characters, movies, and TV shows, leading to licensing and branding collaborations between manufacturers and entertainment companies. Licensed products are often popular among consumers, as they provide a sense of familiarity and attachment to beloved characters.
- Global market:the toys and games industry operates globally, with manufacturers and distributors producing and distributing products worldwide. The enterprise caters to diverse markets and cultural preferences, adapting products to meet the specific needs and preferences of different regions and demographics.
- Impact on development:Toys and games have a significant effect on child development, fostering creativity, imagination, social skills, and cognitive abilities. Many toys and game designers create products to promote learning and development, often collaborating with child development experts to ensure they meet these goals.
The toys and games industry is crucial in providing entertainment and promoting development among children and adults. Continuous innovation, adherence to safety standards, and licensing and branding collaborations contribute to the industry’s growth and its ability to meet the evolving demands of consumers.
Choosing the Right Manufacturer for Family Injection Molds
Choosing the proper manufacturer for family injection molds is a crucial step in ensuring the success of your project. Here are some key points to consider when selecting a manufacturer:
- Expertise and experience:Look for a manufacturer with extensive knowledge and experience in family injection molding. Consider their track record, years in operation, and understanding of your target industries or products.
- Technical capabilities:Assess the manufacturer’s technical capabilities, including equipment, machinery, and manufacturing processes. Ensure they have the necessary tools and resources to handle the complexity and specifications of family injection molds.
- Quality control:Quality control is vital in injection molding to maintain consistency and precision in the production of molds. Check if the manufacturer has established quality control measures and certifications, such as ISO 9001, to ensure they adhere to industry standards and consistently deliver high-quality molds.
- Customization and flexibility:Family injection molds often require customization to accommodate multiple parts and designs. Choose a manufacturer who can accommodate your specific requirements and has the flexibility to adapt to changes or revisions during the manufacturing process.
- Communication and collaboration:Effective communication and collaboration are essential for a successful partnership. Evaluate the manufacturer’s responsiveness, willingness to communicate, and ability to understand your needs. A manufacturer who can provide clear and open lines of communication throughout the project will help ensure a smooth manufacturing process.
- Cost and timeline: Consider the manufacturer’s pricing structure and lead times. While cost is a factor, be cautious of meager prices that may compromise quality. Find a balance between competitive pricing and reasonable lead times to meet your project deadlines.
- References and testimonials:Request references or testimonials from other clients who have worked with the manufacturer. You can gain valuable insights by analyzing their reputation, customer satisfaction, and ability to follow through on commitments.
By carefully evaluating these factors and conducting thorough research, you can make an informed decision when choosing the proper manufacturer for your family injection molds. A reliable and competent manufacturer will contribute to the success of your project and ensure the production of high-quality molds that meet your specifications.
Conclusion
Family injection molds offer many benefits to manufacturers looking to produce plastic products efficiently and cost-effectively. Understanding the various types of molds, their advantages and disadvantages, and design considerations are critical to making the most of this manufacturing process. With the proper manufacturer and design, family injection molds can be a reliable and effective solution for various industries and applications.