Understanding PBT Injection Molding: A Comprehensive Guide
Understanding PBT Injection Molding: A Comprehensive Guide
PBT (Polybutylene Terephthalate) injection molding has emerged as a crucial technique in manufacturing, particularly in producing plastic components that require high durability, heat resistance, and excellent dimensional stability. This versatile thermoplastic polymer is favored in various industries, including automotive, electronics, and consumer goods, due to its exceptional mechanical properties and ease of processing. This article provides an in-depth understanding of PBT injection molding, covering its characteristics, advantages, applications, and process, along with relevant subtopics that further illuminate this important manufacturing technique.
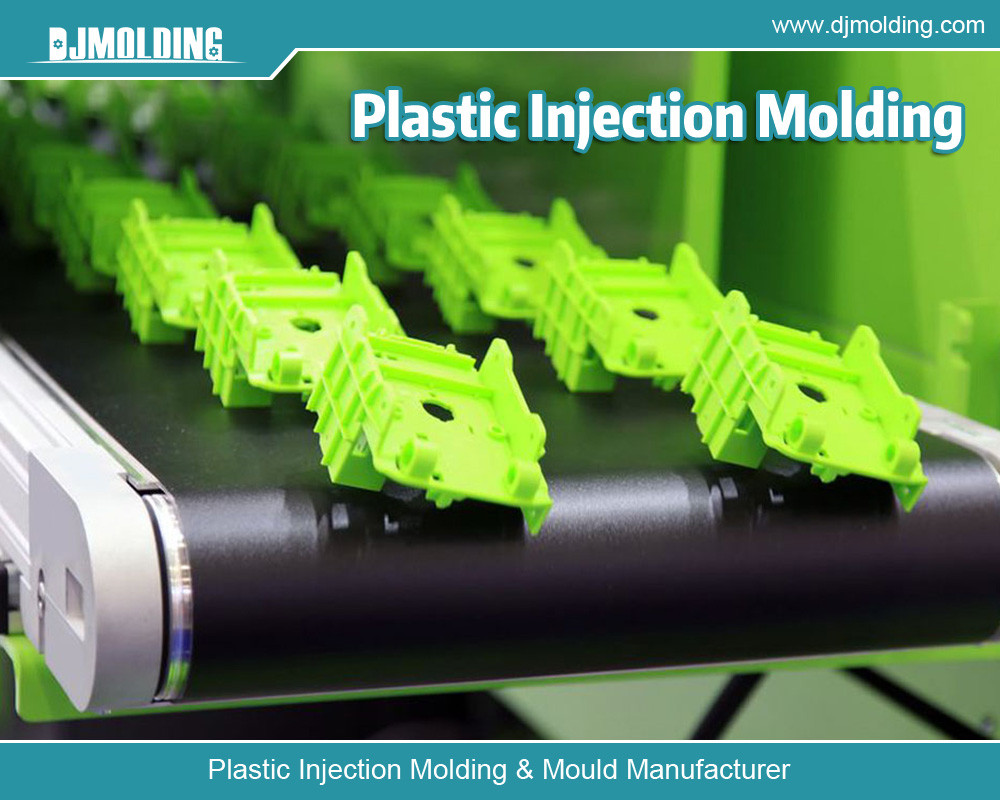
Understanding the Chemistry of PBT
PBT is a thermoplastic polyester produced by polymerizing butanediol and terephthalic acid. The chemical structure of PBT gives it unique properties that are beneficial for injection molding:
- Linear Polymer Structure: This structure allows for better flow characteristics during the melting and molding.
- Hydrophilic Nature: PBT can absorb moisture, which impacts processing and contributes to its mechanical properties.
- Thermal Stability: The chemical bonds within PBT resist degradation under heat, making it suitable for high-temperature applications.
Critical Properties of PBT Relevant to Injection Molding
PBT possesses several vital properties that enhance its suitability for injection molding:
- High Strength and Toughness: PBT can withstand mechanical stress without deformation, making it ideal for structural applications.
- Excellent Surface Finish: The smooth surface of PBT molded parts is aesthetically pleasing and suitable for various surface treatments.
- Low Moisture Absorption: Its low hygroscopicity minimizes swelling and maintains dimensional stability, which is critical in precision applications.
- Chemical Resistance: PBT is resistant to many acids and solvents, vital in applications exposed to various chemicals.
Comparison of PBT with Other Thermoplastics
When selecting materials for injection molding, it is essential to compare PBT with other common thermoplastics:
- PBT vs. PET: While both are polyesters, PBT is more flexible and has a lower melting point than PET, making it easier to process but slightly less heat resistant.
- PBT vs. ABS: PBT has superior chemical resistance and thermal stability compared to ABS (Acrylonitrile Butadiene Styrene), making it preferable for high-performance applications.
- PBT vs. PA (Nylon): Nylon offers better wear resistance, but PBT has a better surface finish and is easier to process for complex shapes.
The Role of Additives in PBT Injection Molding
Additives play a significant role in enhancing the properties of PBT for specific applications:
- Colorants: These are added to achieve desired colors in the final products, enhancing aesthetic appeal.
- Fillers: Incorporating fillers such as glass fibers can improve strength and rigidity but may affect the material’s processing characteristics.
- Stabilizers: UV stabilizers can protect PBT from degradation due to sunlight exposure, making it suitable for outdoor applications.
- Flame Retardants: These additives can enhance the fire resistance of PBT, making it safer for use in electrical and electronic applications.
Environmental Impact and Sustainability of PBT
Sustainability is becoming increasingly important in manufacturing. PBT has several environmental considerations:
- Recyclability: PBT can be recycled, reducing waste and promoting a circular economy in plastics.
- Low Emissions During Processing: The injection molding process for PBT typically produces fewer emissions than other manufacturing techniques.
- Biodegradable Alternatives: While PBT is not biodegradable, ongoing research is being done into blending it with biodegradable materials to enhance sustainability.
Troubleshooting Common Issues in PBT Injection Molding
Despite its advantages, PBT injection molding can encounter several common issues:
- Inadequate Melt Flow: Inadequate Melt Flow can lead to incomplete mold filling; adjusting the temperature and pressure can help.
- Surface Defects: Issues such as sink marks and warping may arise; proper mold design and cooling strategies can mitigate these problems.
- Moisture-Related Defects: Excess moisture can cause bubbles or voids, so it is critical to ensure thorough drying of PBT before processing.
Future Trends in PBT Injection Molding Technology
As the industry evolves, several trends are shaping the future of PBT injection molding:
- Advanced Simulation Techniques: Computer-aided design (CAD) and simulation software can optimize mold designs and predict potential issues before physical production.
- 3D Printing Integration: Combining traditional molding with 3D printing techniques enables rapid prototyping and more complex part designs.
- Smart Manufacturing: Adopting IoT (Internet of Things) in injection molding processes improves efficiency, monitoring, and predictive maintenance.
Best Practices for PBT Injection Molding
To ensure high-quality production and efficiency in PBT injection molding, several best practices should be followed:
- Material Preparation: Always dry PBT pellets properly to minimize moisture content before processing.
- Mold Maintenance: Regular inspection and maintenance of molds can prevent defects and improve part quality.
- Temperature Control: Maintain optimal melting and mold temperatures to ensure consistent flow and cooling rates.
Case Studies: Successful Applications of PBT Injection Molding
Numerous industries have successfully utilized PBT injection molding. Here are a few examples:
- Automotive Industry: PBT is commonly used in manufacturing connectors and housing for vehicle electronic controls, benefiting from its heat resistance and dimensional stability.
- Consumer Electronics: Devices like smartphones and laptops utilize PBT for casings due to its lightweight and durable nature.
- Household Appliances: Kitchen appliances often feature PBT components, providing functionality and aesthetic appeal.
Cost Analysis of PBT Injection Molding versus Other Methods
When considering PBT injection molding, it is essential to analyze the costs involved:
- Material Costs: PBT can be more expensive than some alternatives, but its properties can justify the investment for high-performance applications.
- Production Efficiency: The ability to produce complex geometries with minimal waste can offset higher material costs.
- Long-Term Savings: The durability and reliability of PBT components can lead to lower maintenance and replacement costs over time.
The Importance of Quality Control in PBT Injection Molding
Quality control is crucial in the PBT injection molding process to ensure the production of high-quality components. Effective quality control measures involve:
- Regular Inspection: Routine checks of molded parts help identify defects early, ensuring that any issues can be addressed promptly.
- Material Testing: Analyzing PBT materials before processing verifies their properties and suitability for specific applications.
- Process Monitoring: Monitoring parameters like temperature, pressure, and cycle times can prevent defects caused by variations in the injection molding process.
- Final Product Evaluation: Conducting tests on finished products, such as tensile strength and dimensional accuracy, guarantees that they meet industry standards and customer expectations.
Implementing stringent quality control protocols can enhance reliability, reduce waste, and increase customer satisfaction in PBT injection molding applications.
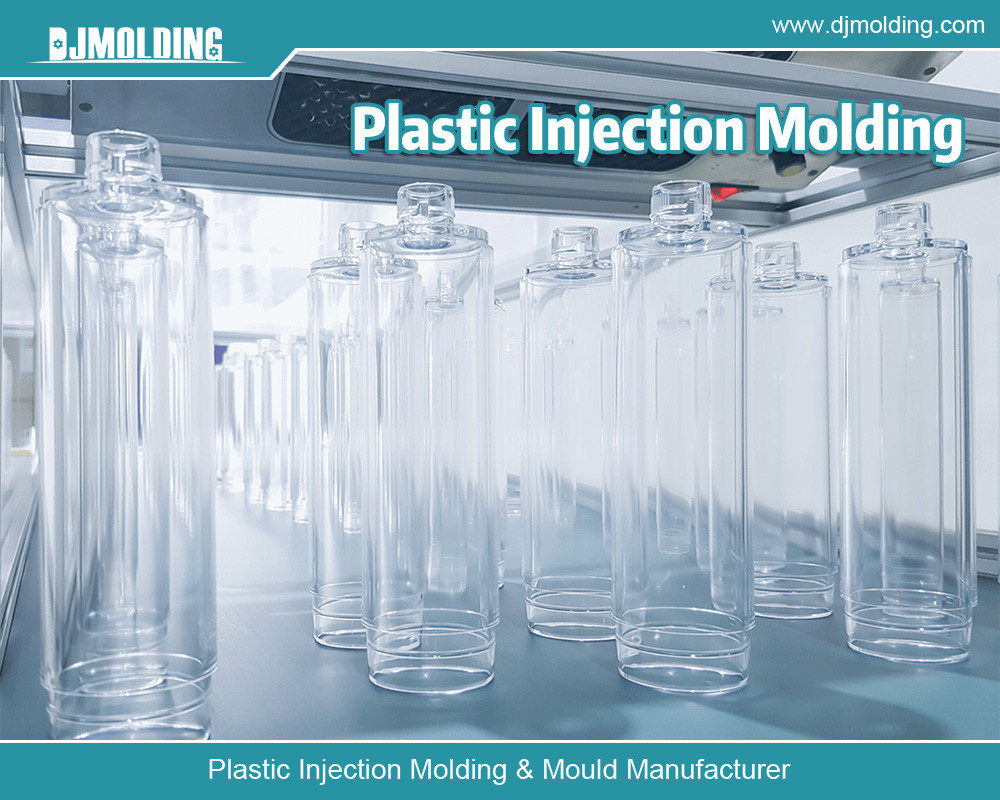
Conclusion
PBT injection molding is a vital manufacturing process that harnesses the unique properties of Polybutylene Terephthalate to produce high-quality components across various industries. Its advantages, including strength, durability, and aesthetic appeal, make it a preferred choice for manufacturers seeking to create reliable and visually appealing products. While challenges exist, ongoing innovations and advancements in the field promise to enhance the efficiency and sustainability of PBT injection molding. As technology progresses, PBT’s potential applications and benefits will continue to expand, solidifying its place as a critical material in modern manufacturing.
For more about pbt injection molding: a comprehensive guide, you can pay a visit to Djmolding at https://www.djmolding.com/ for more info.