The advantages and disadvantages of plastic injection molding
The advantages and disadvantages of plastic injection molding
One of the most used plastics processing techniques is injection molding, being one of the most common processes for obtaining plastic products. Today every house, every vehicle, every office, every factory, etc. It contains a large number of different items that have been manufactured by injection molding. Among them we can mention: telephones, vessels, etc. and very complex forms a telephone connection plug.
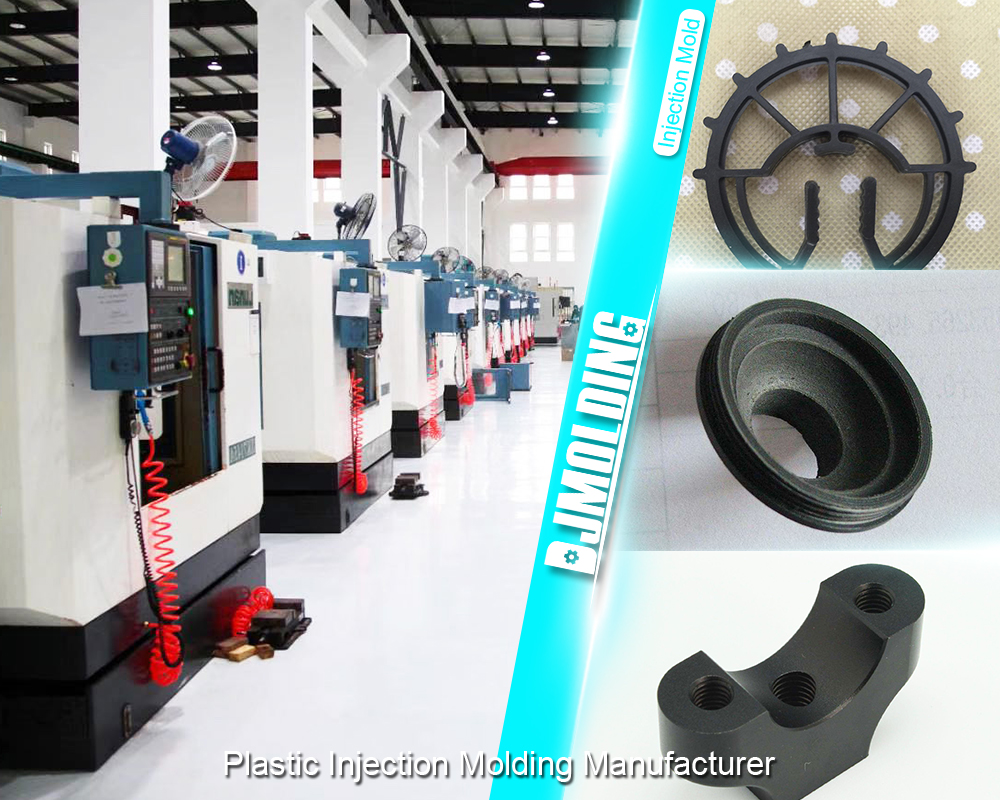
Functioning
Injection molding consists of feeding the pellets or grains to a heated barrel where it melts, then being molten it is forced to pass through a chamber with a die or bipartite die, by means of a hydraulic piston or with the rotary screw of an extruder. As the pressure at the mold inlet increases, the rotary screw begins to move backward, under pressure, up to a predetermined distance; This movement controls the volume of the material to be injected. The screw then stops rotating and is hydraulically pushed forward, forcing the molten plastic into the mold cavity. Injection molding pressures are typically 70 to 200 MPa (10,000 to 30,000 psi).
Once the piece is cold (thermoplastic) or cured (thermofixes), the molds are opened and the piece is ejected. The molds are then closed and the process is repeated automatically. Also, elastomers are injection molded by these processes.
Plastic injection molding requires higher temperatures and pressures than any other transformation technique, but it provides parts and objects with enough precision (as long as the resin used does not have excessive shrinkage), with clean and smooth surfaces, in addition to providing a magnificent use of the material, with a high production rate. However, sometimes parts must be refined or finished later to remove burrs.
Advantages and disadvantages
Injection molding has a number of advantages and disadvantages that make it ideal over other molding processes for specific applications. Some of the advantages and disadvantages could be:
- High levels of production and low costs
- Molding of parts with very complicated geometries.
- High or low automation, this depends on the value of the part.
- The pieces once finished require little finishing, they are finished with the desired roughness, color and transparency.
- Material handling is reduced because the press hopper will usually contain enough material to mold parts for an extended period.
- Longer and smaller diameter core dowels can be used because they can be held at both ends.
- After the mold has been closed before injecting any material into it, parts that contain metal inserts can be molded without having burrs of material in the inserts.
- Relatively tighter tolerances across parting lines are possible.
- The burr on the parting line can be kept to a minimum thickness if the mold is properly designed and well maintained.
- Injection molding of thermoset materials is suitable to automate the process which can result in low prices per part.
- Deformation can be a problem in injection molding because injection materials have smoother flows and more shrinkage. Forcing the material through the trough, channel and inlet, can orient the material producing non-uniform shrinkage.
- Filling parts through one of the two inlets produces parts that have dotted lines. These dotted lines are the weakest areas on the part.
- The total amount of scrap metal produced during injection molding will usually be greater than that of compression molding because of the additional scrap metal created by the trough and trough. In the past, thermoset scrap had to be dumped in a garbage dump. However, some thermoset materials are now being successfully recycled.
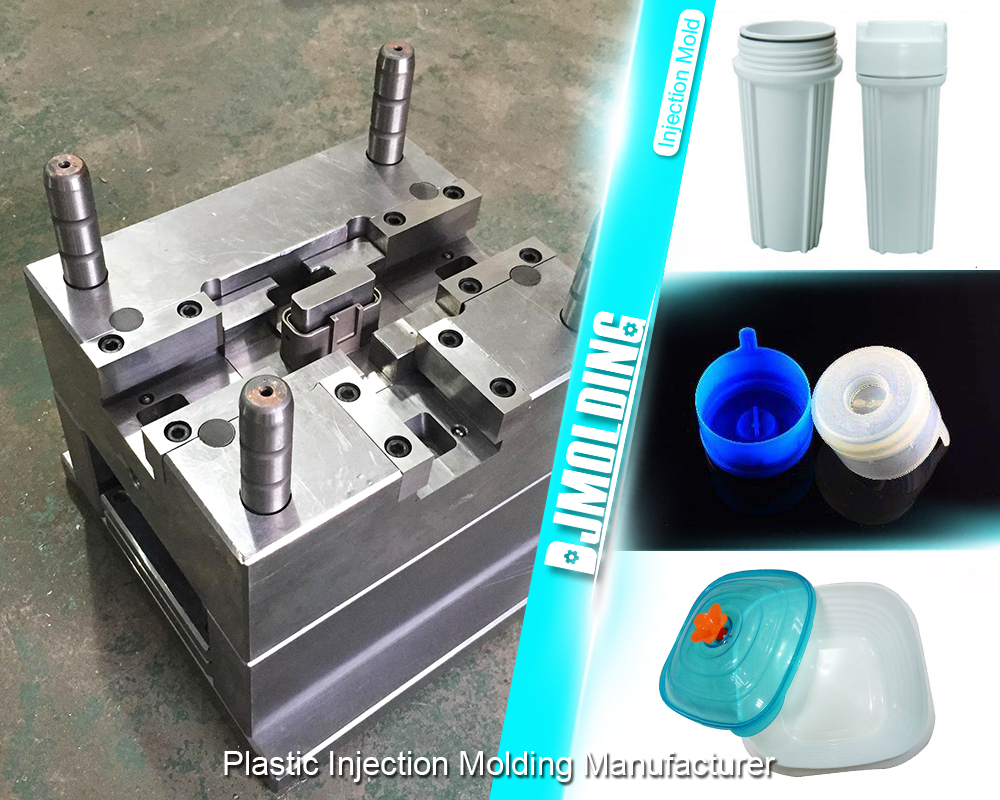
For more about the advantages and disadvantages of plastic injection molding,you can pay a visit to Djmolding at https://www.djmolding.com/ for more info.