A Comprehensive Guide To Liquid Silicone Rubber (LSR) Injection Molding Techniques
A Comprehensive Guide To Liquid Silicone Rubber (LSR) Injection Molding Techniques
When it comes to injection molding, one material that is gaining popularity is liquid silicone rubber (LSR). LSR is a versatile material that can be used in various industries, from medical to automotive. In this comprehensive guide, we will explore the benefits of using LSR in injection molding, including its durability, flexibility, and resistance to extreme temperatures.
We’ll also cover the different LSR injection molding techniques, including compression molding, transfer molding, and injection molding. If you’re looking for a material that can withstand the toughest conditions and produce high-quality products, LSR is definitely worth considering. Let’s dive in and explore the world of liquid silicone rubber injection molding techniques.
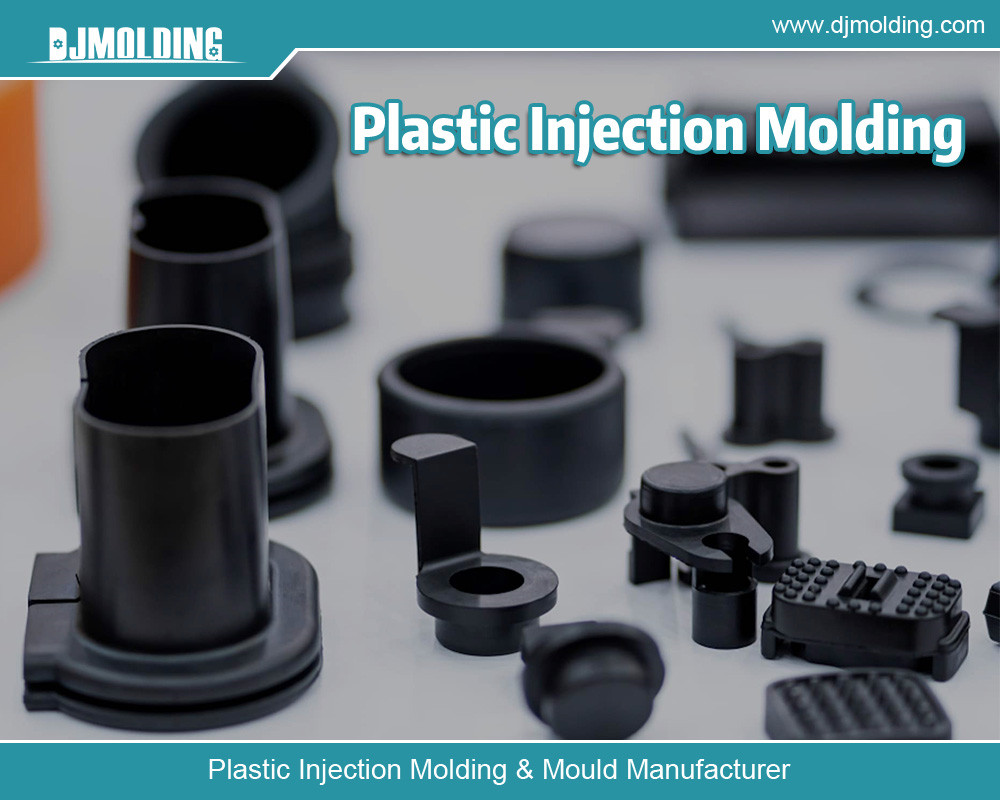
Advantages of LSR Injection Molding Techniques
LSR Injection Molding offers several advantages over traditional injection molding techniques. Firstly, it provides high precision and accuracy, which is essential in industries such as medical and healthcare, where even the slightest deviation can have serious consequences. Secondly, LSR Injection Molding produces low waste, as the liquid silicone rubber is injected directly into the mold cavity, eliminating the need for excess material.
Thirdly, it offers high production efficiency, as the process is automated and can produce large quantities of products in a short amount of time. Fourthly, LSR Injection Molding offers a wide range of material properties, allowing manufacturers to create products with varying levels of hardness, elasticity, and durability. Lastly, LSR materials are biocompatible and chemically resistant, making them suitable for use in medical and healthcare applications.
Understanding the LSR Injection Molding Process
The LSR Injection Molding process involves several steps, including material preparation, injection, curing, and demolding. Firstly, the liquid silicone rubber is prepared by mixing two or more components in a specific ratio. Secondly, the material is injected into the mold cavity using a specialized injection molding machine. Thirdly, the material is cured by heating it to a specific temperature and holding it for a specific time. Lastly, the product is demolded and inspected for quality.
Temperature control and curing time are critical factors in the LSR Injection Molding process, as they can affect the final product’s properties and quality. Compared to traditional injection molding techniques, LSR Injection Molding offers greater precision and accuracy, as well as faster cycle times.
LSR Injection Molding Equipment and Machinery
LSR Injection Molding machines come in various types, including horizontal, vertical, and multi-component machines. The components of an LSR Injection Molding machine include the injection unit, mold, clamping unit, and control system. Proper maintenance and calibration of LSR Injection Molding equipment are essential to ensure optimal performance and product quality. Regular cleaning, lubrication, and inspection of the machine’s components can prevent breakdowns and prolong its lifespan.
Designing LSR Injection Molds for Optimal Results
Mold design is a critical factor in LSR Injection Molding, as it can affect the product’s quality, cycle time, and cost. Factors to consider in mold design include part geometry, gate location, venting, and cooling. Common mold design mistakes to avoid include inadequate venting, improper gate location, and insufficient cooling. Proper mold design can improve product quality, reduce cycle time, and minimize waste.
Material Selection for LSR Injection Molding
LSR materials come in various types, including high consistency rubber (HCR) and liquid silicone rubber (LSR). HCR materials are typically used for compression molding, while LSR materials are used for injection molding. LSR materials offer several properties and characteristics, including high tear strength, low compression set, and biocompatibility. Factors to consider in material selection include the product’s intended use, performance requirements, and regulatory compliance.
LSR Injection Molding Troubleshooting and Maintenance
Common issues in LSR Injection Molding include flash, short shots, and air entrapment. These issues can be resolved by adjusting the injection speed, pressure, and temperature, as well as improving mold design and venting. Regular maintenance and troubleshooting of LSR Injection Molding equipment can prevent breakdowns and ensure optimal performance.
Quality Control and Inspection in LSR Injection Molding
Quality control is essential in LSR Injection Molding to ensure that the products meet the required specifications and standards. Inspection methods include visual inspection, dimensional measurement, and material testing. Quality control standards and regulations vary by industry and application, and compliance is necessary to ensure product safety and reliability.
Applications of LSR Injection Molding in Various Industries
LSR Injection Molding is widely used in various industries, including medical and healthcare, automotive, consumer goods, electronics, and aerospace. In the medical and healthcare industry, LSR Injection Molding is used to produce medical devices, implants, and surgical instruments. In the automotive industry, LSR Injection Molding is used to produce seals, gaskets, and vibration dampeners.
In the consumer goods industry, LSR Injection Molding is used to produce toys, kitchenware, and personal care products. In the electronics industry, LSR Injection Molding is used to produce keypads, connectors, and seals. In the aerospace industry, LSR Injection Molding is used to produce seals, gaskets, and insulation.
Future Trends and Developments in LSR Injection Molding Techniques
LSR Injection Molding has come a long way since its inception, and the future seems bright with the continuous advancements in LSR materials and technology. One of the emerging applications of LSR Injection Molding is 3D printing, which allows for the creation of complex geometries and intricate designs that were previously impossible to achieve. Another emerging application is micro molding, which involves the production of small and precise parts that are used in various industries such as medical devices and electronics. Overmolding is another area where LSR Injection Molding is gaining popularity. Overmolding involves the injection of LSR over a substrate material such as plastic or metal to create a composite part with enhanced properties. This technique is widely used in the automotive industry for creating soft-touch surfaces and improved grip on steering wheels and gear knobs.
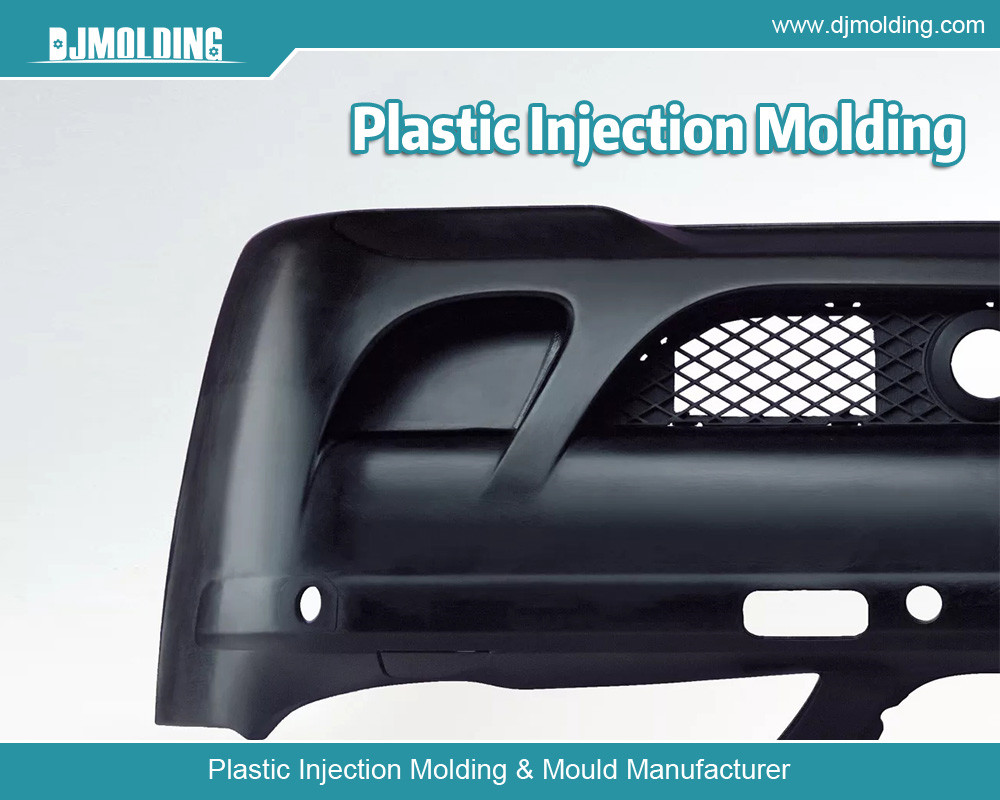
Conclusion
In conclusion, LSR Injection Molding is a versatile and efficient manufacturing process that offers numerous advantages over traditional injection molding techniques. LSR Injection Molding provides high precision and accuracy, low waste production, high production efficiency, a wide range of material properties, biocompatibility, and chemical resistance. Proper understanding of the LSR Injection Molding process, equipment, design, material selection, troubleshooting, and quality control is essential to ensure optimal performance and product quality. The future of LSR Injection Molding is promising, with advancements in LSR materials and technology, and the expansion of LSR Injection Molding into new industries and applications.
For more about a comprehensive guide to liquid silicone rubber (lsr) injection molding techniques,you can pay a visit to Djmolding at https://www.djmolding.com/liquid-silicone-rubberlsr-injection-molding/ for more info.