Aluminum Injection Molding In Plastic Product Manufacturing
Aluminum Injection Molding In Plastic Product Manufacturing
Aluminum injection molding in plastic product manufacturing has helped so many product producers realize maximum production benefits. So many manufacturing industries rely on this mold material because it helps produce highly accurate and consistent results. In addition, you can easily machine all plastic products that have been produced from this molding system. This is why it can be used to produce highly complex products.
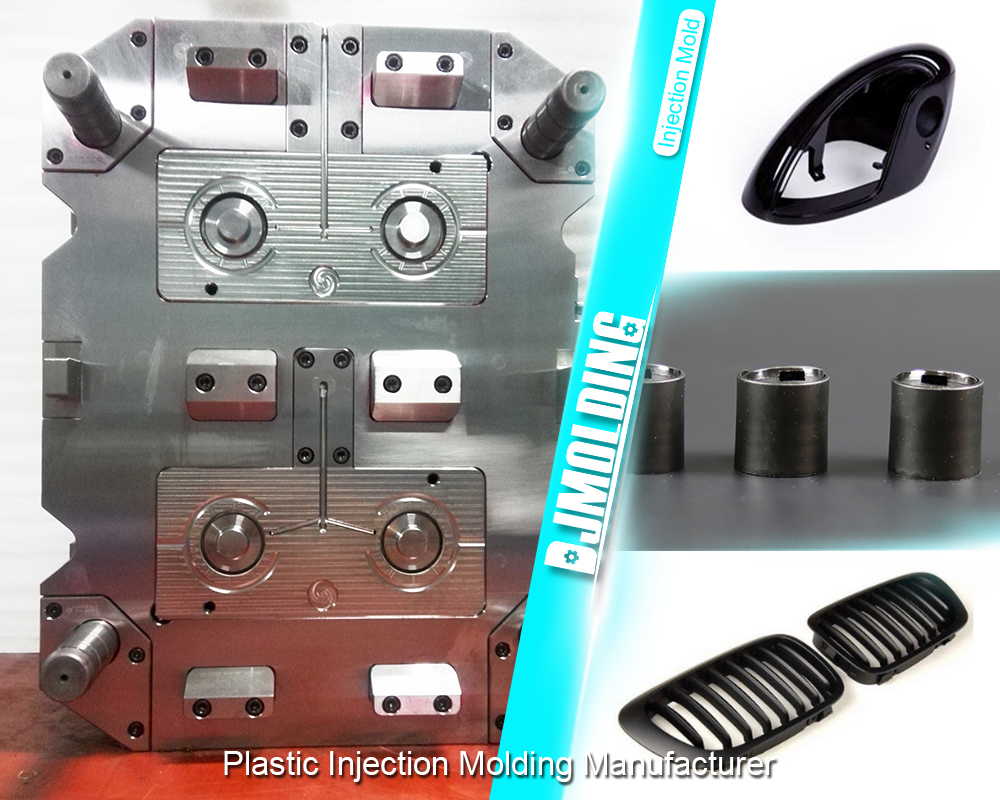
The injection mold production process
The aluminum injection molding is a regular manufacturing technology which is widely used in industrial environments. It is a production model that can be used for prototyping as well as final production runs. This production technology allows for the production of complex product designs due to its flexibility and material efficiency. Manufacturers rely on the technology where a large volume of products with high quality is needed. The process of using injection molding technology is usually based on the product design and the materials being used in enhancing the production process. This is why plastic manufacturers generally rely on aluminum injection molds because they reduce production costs without compromising the quality.
An overview of the aluminum injection molding process
The plastic product manufacturing industry depends heavily on the injection molding process for making quality and robust products. This process is involves forcefully injecting molten plastic into a mold made from aluminum. This mold comes fully pre-fabricated with a cavity that possesses the shape of the product to be made. Aluminum is one of the best materials used for making molds in the plastic manufacturing industry. It is a cost-effective option when compared to steel, which is another common mold material.
Why use aluminum injection molding for the plastic product manufacturing
The plastic product manufacturing industry relies on the use of aluminum molds to manufacture products. This mold material is highly fancied by manufacturers because it can easily emit heat at a very fast rate. Manufacturers prefer a suitable mold material that helps to quickly transfer heat from the molten plastic to the external environment. Since the aluminum mold does this effectively, it means that it helps in quick production processes. Moreover, the aluminum injection molding has a wide spectrum of benefits and this is why it is used in the plastic product manufacturing.
The benefits of using aluminum injection molding in the plastic product manufacturing industry
The aluminum injection molding is a useful equipment in the plastic product manufacturing industry because of several benefits. These include:
It is a cheaper option: Aluminum and steel molds are two most used molds in the plastic product manufacturing industry. However, manufacturers prefer using aluminum because it is quite a cheaper option than the steel molds. If a high-grade aluminum injection molding equipment is used, this helps manufacturers save about 30% of the total cost. This is why product manufacturers tend to maximize the use of the aluminum injection molds.
Decreases production lead times: Design departments in manufacturing companies will tell you that aluminum injection molds help reduce production lead times. Aluminum injection molds are used in the plastic manufacturing industry because it takes a shorter time to design. Compared to steel molds, aluminum molds are usually preferred. Steel molds take several weeks to design. However, you need a maximum of 7 days to design aluminum molds. This means that you can shorten the lead time when making product prototypes and final designs to present to clients.
Good for a faster heat transfer: The aluminum injection molds are fancied in the plastic manufacturing industry because they have quick transfer heat properties. This means that they tend to cool a lot faster and transmit heat out of the mold and then outside. This makes the production process a lot faster than when other mold materials are used. This is why parts manufacturers prefer using the aluminum injection molds for quick and low-volume manufacturing projects.
Create final products without flaws or marks: The injection molding process for making plastics depends on an efficient heat dissipation process to ensure flawless products. Since aluminum injection molds perform well in this area, they generally lead to the production of products without defects. Excellent heat dissipation properties mean that the product will be devoid of usual defects like burn scars, voids, sink marks, and so on. Unlike aluminum injection molds, other mold materials usually have an unequal heat dissipation property which can lead to defective products.
Can be modified and repaired easily: The aluminum injection molds are usually made from aluminum – which is a very soft substance. This is why you can easily repair the mold and also modify it as needed. Since it can be easily repaired, it reduces the total cost needed to maintain the mold.
Good for low-volume production: You can choose the aluminum injection molding for low-volume plastic parts production. This is because they generally have lower initial costs and support in the production of thousands of high-precision product parts at a time.
Some of the problems with aluminum injection molding
There are so many benefits of using aluminum injection molds. But this production technology comes with its own set of drawbacks. Some of the problems that come with this molding technology include:
Poor durability in comparison to steel molds: Aluminum injection molding used for plastic production is not as durable as steel molds. This is why they are more beneficial when used for smaller production runs. In comparison, steel injection molds have more durability with superior thermal stability, wear resistance, and corrosion resistance.
Limits product surface finish options: With aluminum injection molds, manufacturers do not have enough options for surface finishes. This is because of its low density. Steel molds have a higher density which makes it possible for products to be made with a wide range of custom finishes and textures.
Production of products with surface defects: Aluminum injection molds are susceptible to worn-out cavities which appear after several production cycles. These aluminum molds will usually cause flashing during the production of a product. After using this mold for several thousand production cycles, the mold can produce flashing during production. In addition, this type of mold is prone to warpping, shrinkage, and porosity.
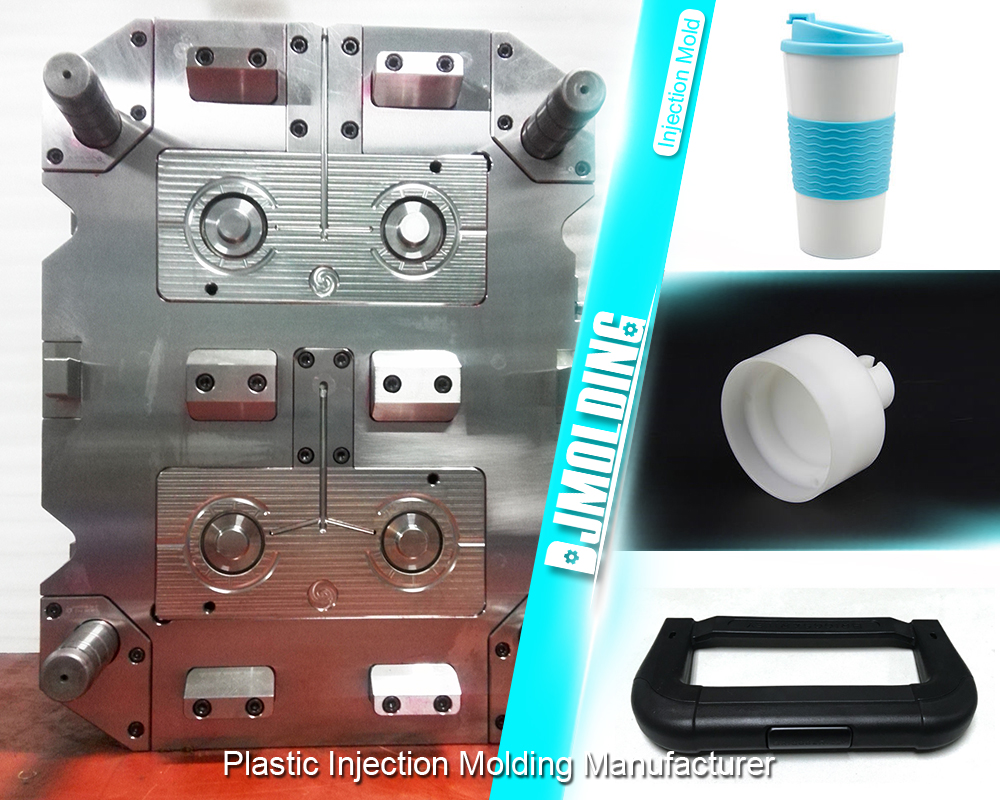
For more about the aluminum injection molding in plastic product manufacturing,you can pay a visit to Djmolding at https://www.djmolding.com/what-is-aluminum-rapid-tooling-for-plastic-injection-molding/ for more info.