High Volume Injection Molding: The Key to Efficient and Cost-Effective Manufacturing
High Volume Injection Molding: The Key to Efficient and Cost-Effective Manufacturing
Injection molding is a widely used manufacturing process that involves injecting molten material, typically plastic, into a mold cavity to create a desired shape. This process has revolutionized the production of plastic parts due to its efficiency, versatility, and cost-effectiveness. In particular, high volume injection molding enables manufacturers to produce large quantities of plastic parts with remarkable speed and precision. This blog post will delve into high volume injection molding, discussing its benefits, challenges, key considerations, applications, and future trends.
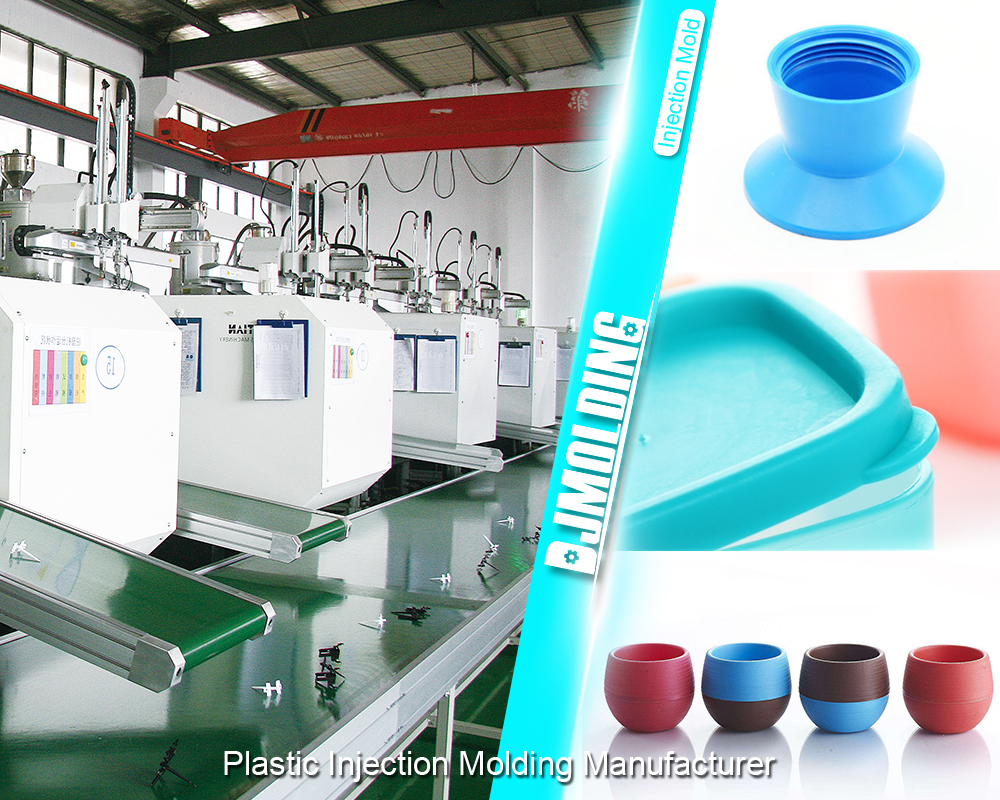
What is High Volume Injection Molding?
High volume injection molding refers to producing plastic parts in large quantities using the injection molding process. It involves using specialized machinery and equipment capable of handling high production volumes. Manufacturers can achieve rapid and efficient production cycles by optimizing mold design, production parameters, and material selection. Compared to low volume injection molding, high volume injection molding offers significant advantages in economies of scale and cost reduction. Numerous consumer products, such as plastic containers, automotive components, and electronic enclosures, are manufactured through high volume injection molding.
Benefits of High Volume Injection Molding
The affordability
High volume production allows for the amortization of tooling costs over many parts, resulting in lower per-unit costs. The economies of scale achieved in high volume injection molding make it an attractive option for cost-sensitive industries.
Efficiency and speed
High volume injection molding enables manufacturers to produce large parts within short timeframes. The production output significantly increases with fast cycle times, automated processes, and efficient machinery.
Continuity and accuracy
Advanced molds, precise control systems, and automated processes ensure consistent part quality and dimensional accuracy. High volume injection molding offers tight tolerances and repeatability, making it ideal for industries that demand precision.
Wide range of materials and designs
High volume injection molding supports a variety of plastic materials, including thermoplastics and thermosetting polymers. It allows for producing intricate and complex designs, giving designers and engineers immense flexibility.
versatility
High volume injection molding offers scalability, allowing manufacturers to ramp up production as demand increases. The process can easily accommodate higher volumes without sacrificing quality or efficiency.
Challenges and Considerations of High Volume Injection Molding
Initial setup and tooling costs
High volume injection molding requires a significant initial investment in molds and tooling. One should carefully evaluate the costs associated with mold design, fabrication, and maintenance.
Material selection and availability
Selecting a suitable material is crucial for achieving desired part properties. When choosing the resin, one must consider material availability, cost, and compatibility with the injection molding process.
Design limitations
Complex designs with thin walls, intricate features, or undercuts may pose challenges in high volume injection molding. Taking into account design for manufacturability helps optimize production efficiency.
Quality control and testing
With large production volumes, maintaining consistent part quality becomes paramount. Rigorous quality control measures, including in-process inspections and post-production testing, are necessary to ensure compliance with specifications.
Environmental Impact and Sustainability
The high volume production of plastic parts raises concerns about sustainability and environmental impact. Manufacturers should explore sustainable materials, recycling options, and energy-efficient processes to minimize the carbon footprint.
Key Factors for Successful High Volume Injection Molding
Proper design and engineering
Effective collaboration between designers and engineers is essential to optimize the high volume injection molding design. Design considerations like wall thickness, draft angles, and gate placement can significantly impact production efficiency and part quality.
Selection of the suitable materials and equipment
Choosing the appropriate resin with the desired mechanical, thermal, and chemical properties is critical. Additionally, selecting the proper injection molding machine, auxiliary equipment, and mold materials ensures smooth production operations.
Rigorous testing and quality control
Implementing a comprehensive quality control system is crucial to identify and rectify potential defects or inconsistencies during production. Conducting thorough testing, such as dimensional inspections, mechanical property evaluations, and functional tests, helps maintain high-quality standards.
Continuous improvement and optimization
High volume injection molding presents opportunities for process optimization and continuous improvement. Analyzing production data, identifying areas of improvement, and implementing corrective measures can lead to enhanced productivity, cost savings, and product quality.
Compliance with regulatory and environmental standards
Manufacturers must adhere to regulatory requirements and industry standards to ensure the safety and compliance of the produced parts. Additionally, adopting environmentally friendly practices, such as waste reduction, recycling, and energy efficiency, contributes to sustainable manufacturing.
Applications and Industries for High Volume Injection Molding
High volume injection molding finds application in various industries, including:
Automotive
Production of interior and exterior components, such as bumpers, dashboards, and door panels, to meet the high-volume demands of the automotive industry.
Consumer goods
They manufacture plastic products like household appliances, packaging containers, toys, and electronics enclosures.
Medical and healthcare
Manufacturers produce medical devices, disposable syringes, laboratory equipment, and surgical instruments with high precision and quality standards.
Electronics and appliances
We manufacture large quantities of electronic device components, connectors, housings, and consumer electronics to meet demand.
Packaging and logistics
Injection molded packaging solutions, crates, pallets, and containers for efficient storage, transportation, and product protection.
Aerospace and defense
We specialize in creating lightweight, durable, high-performance components for aerospace, defense, and aviation applications.
Future Trends and Innovations in High Volume Injection Molding
Automation and robotics
By integrating automation and robotics, we can improve productivity and efficiency and reduce costs in high volume injection molding processes.
Additive manufacturing and 3D printing
They combine the benefits of injection molding and additive manufacturing techniques to enable rapid prototyping, design iterations, and customization.
Advanced materials and composites
They utilize advanced materials, including reinforced polymers and composites, to achieve improved mechanical properties and reduce weight.
Digitalization and Industry 4.0
Leveraging digital technologies, data analytics, and connectivity to optimize production processes, monitor real-time performance, and enable predictive maintenance.
Sustainable and circular economy
They are embracing sustainable practices such as biodegradable materials, recycling initiatives, and closed-loop systems to minimize waste and environmental impact.
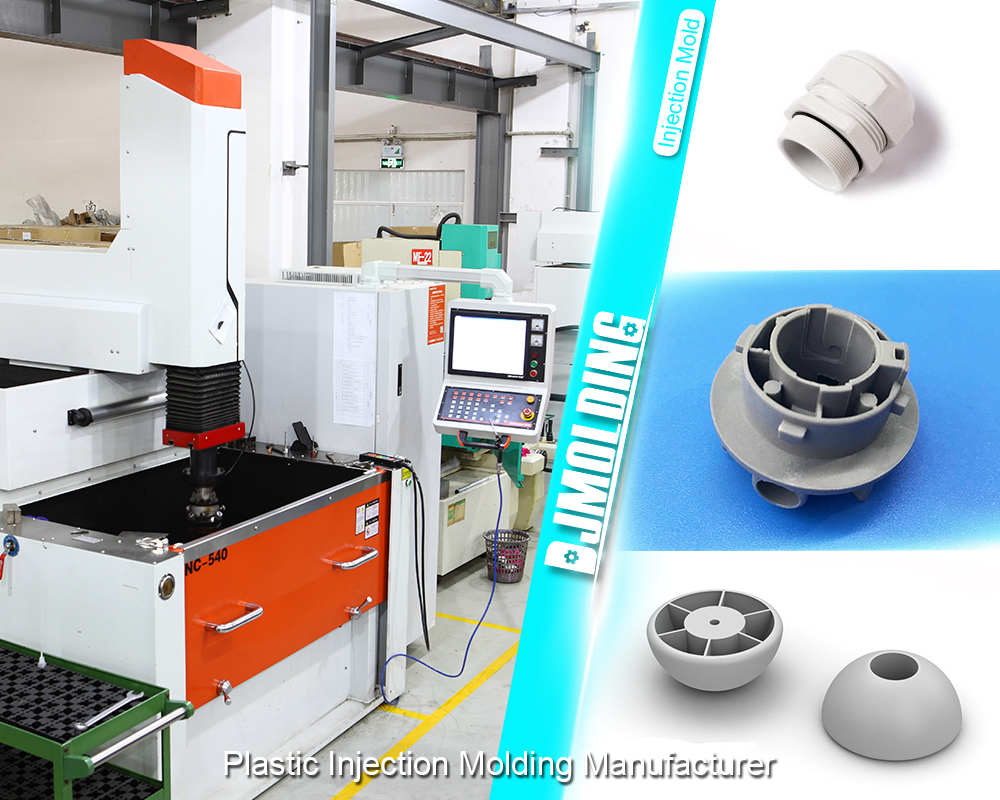
CONCLUSION
High volume injection molding is pivotal in modern manufacturing, enabling the efficient and cost-effective production of plastic parts in large quantities. The benefits of high volume injection molding, including cost-effectiveness, speed, precision, material versatility, and scalability, make it an attractive option for various industries. However, businesses must carefully address challenges such as initial setup costs, material selection, design limitations, and quality control. By considering key factors for successful high volume injection molding and embracing future trends and innovations, manufacturers can harness the full potential of this process. Companies and professionals must explore and leverage the benefits of high volume injection molding, adopting best practices, optimizing production processes, and embracing sustainability to drive success in the rapidly evolving manufacturing landscape. With its ability to meet high-volume demands while maintaining quality and cost-efficiency, high volume injection molding will continue to be a crucial technology in various industries.
For more about high volume injection molding: the key to efficient and cost-effective manufacturing,you can pay a visit to Djmolding at https://www.djmolding.com/high-volume-injection-molding/ for more info.