How to troubleshoot plastic injection molded parts
How to troubleshoot plastic injection molded parts
All plastic injection molding experience problems during production at some point. In this “troubleshooting” guide, we present typical problems that arise during the injection process and that affect the quality of molded parts.
While many such guides are available, sometimes these guides explain what to do, but do not explain the phenomenon causing the problem. This article seeks to fill – at least in part – this lack, explaining the phenomena that generate the problems, and thus giving the engineering and operations team better decision-making tools.
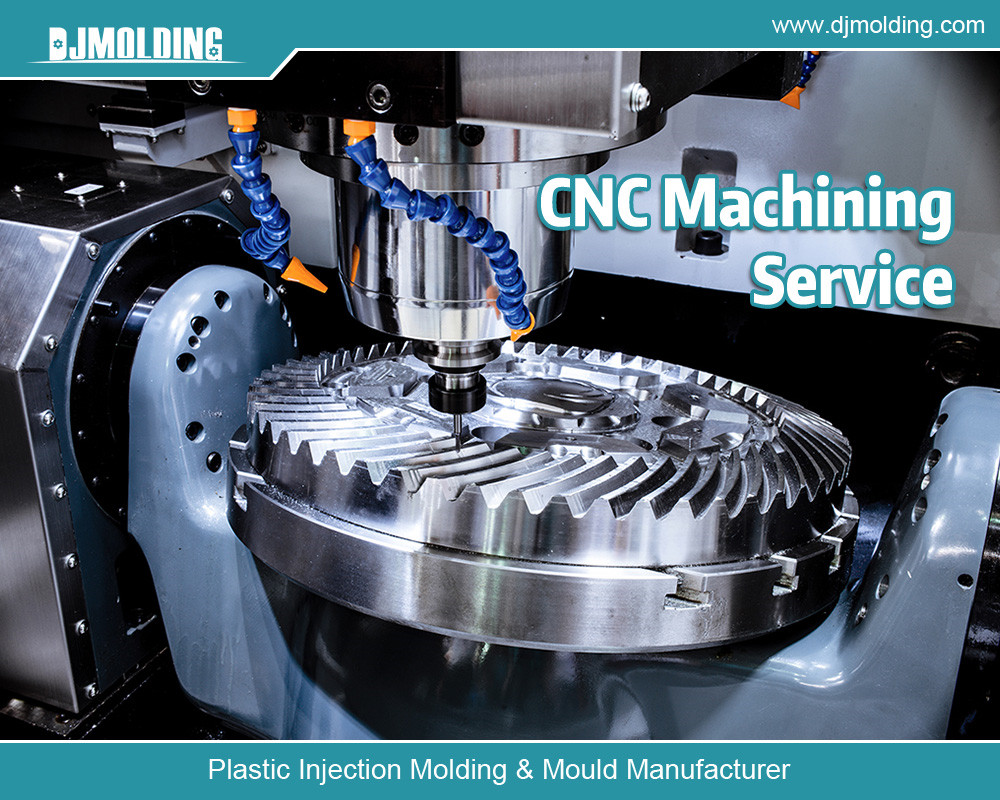
Shrinkage
Almost all materials shrink when solidifying. In the case of polymers, which compared to other materials have great shrink potential, this shrinkage can lead to dimensional problems. The amount of shrinkage is basically determined by the temperature at which the post-pressure is released during injection, and by the level of this post-pressure. This level of shrinkage can be measured on the PvT diagram
One factor that substantially affects shrinkage is crystallization. In semi-crystalline polymers, such as polyethylene or polypropylene, the energy available in the polymer when melting it is translated in order of molecules forming crystalline structures once the material returns to its original solid state. The degree of crystallinity that the material reaches depends on the cooling rate: if there is a sudden cooling, the time available for this ordering of molecules to occur is low, and therefore there is a low degree of crystallization within the mold. On the other hand, if the cooling rate is slow, a higher degree of crystallization is achieved within the mold.
In general, if there is greater crystallization, the shrinkage is greater. To increase crystallization, it is recommended to increase the temperature of the mold. It is also possible to use nucleating agent. It is desirable for the material to achieve a high degree of crystallization inside the mold, since otherwise it can crystallize outside the mold later (depending on how hot it is when ejected and how much energy is available inside it for this effect to occur). post-crystallization). In post-crystallization, the material locally reduces its dimensions, which can generate warpage or dimensional distortion, without the mold dimensions restricting this contraction.
Union lines
Joint lines, or weld lines, occur on any plastic part at the point where two flow fronts meet. For example, if a clamping hole is designed, the flow fronts join around the hole in the part. Because it represents a separation of the material that would otherwise be complete, these bond lines represent a decrease in the mechanical integrity of the material and therefore weaken it. However, its effect can be mitigated by controlling the location of the injection point and the process parameters.
Black spots and dots
Black dots are a sign of material contamination. If recycled material is used, appropriate measures may not be in place during the recovery process to ensure that the recovered parts are not contaminated: for example, there may be contamination on the floor, in the containers where the parts are stored, or where they are ground. It is important to ensure a clean environment in the plant and educate operators on the importance of careful handling of parts to be recycled (for example, not picking up pieces of soil that may have been contaminated). It is also recommended to have a maintenance routine for the machine and its surroundings.
Another factor that negatively affects the purity of the piece is the presence of fine powders, particularly from the mill. Because the ratio of surface area to volume is much higher in these powders than in normal pellets, they melt much faster than pellets and burn. In this case, the solution is to sift the material and filter the fines before processing.
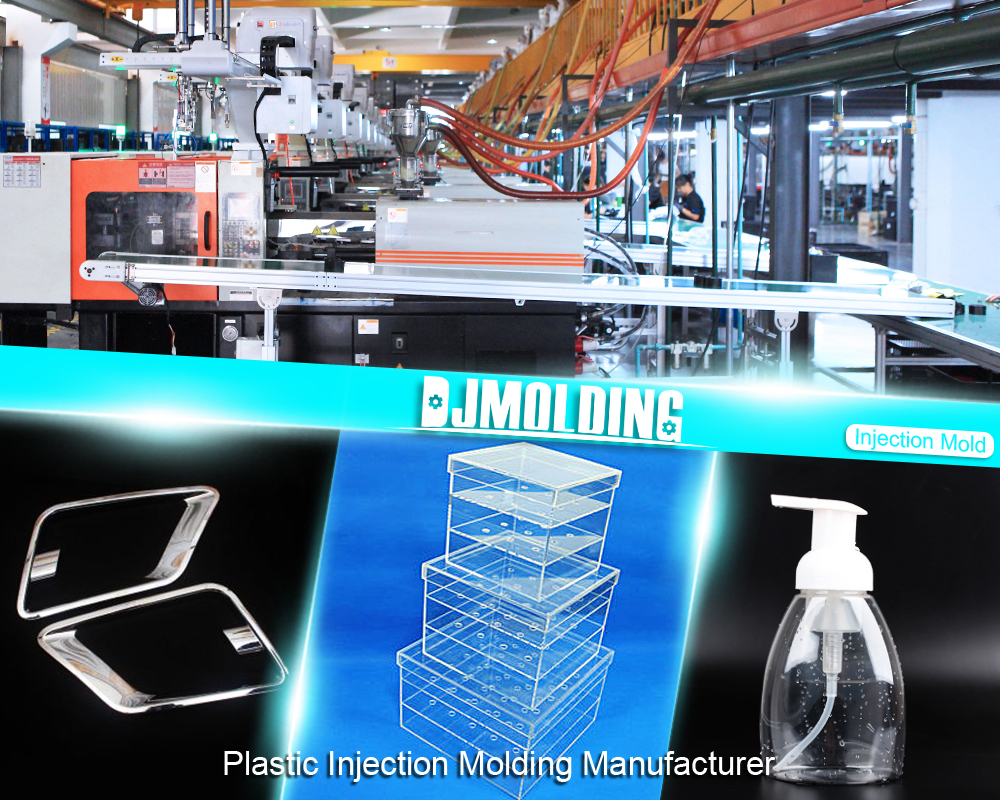
For more about how to troubleshoot plastic injection molded parts,you can pay a visit to Djmolding at https://www.djmolding.com/ for more info.