Improving Your Injection Molding Process: The Key to High-Quality Products
Improving Your Injection Molding Process: The Key to High-Quality Products
The rapid manufacturing sector is undergoing a dramatic shift. It is imperative to get products onto the market as soon as possible in this fast-paced industry. Designers, engineers, and producers must simultaneously make sure that their goods are of high caliber. Injection molding in low volumes is one area of manufacturing that meets customer demands.
Manufacturers are able to produce similar low-volume parts made of plastic with consistent features and attributes thanks to this production process. Modern manufacturers use innovative operating methods to their advantage in changing marketplaces. You will learn all there is to understand regarding low-volume injection molding from this comprehensive handbook.
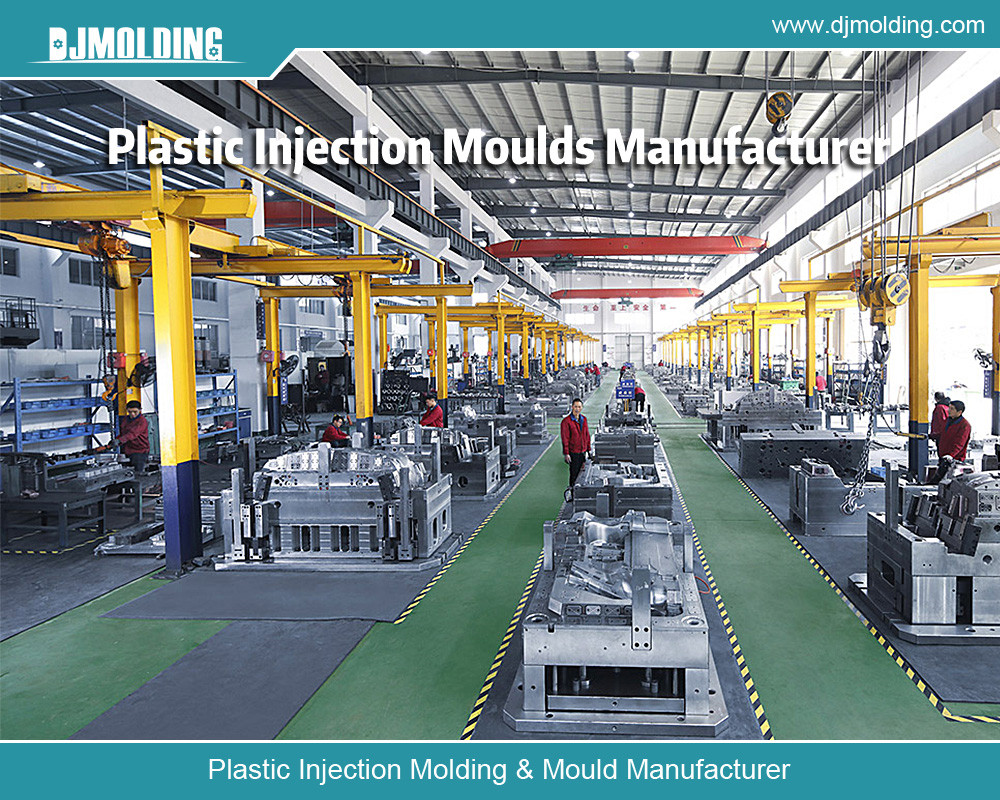
Contingent The Future of Industry: Manufacturing
In the world of manufacturing, at any time, low-volume production is an unusual concept. It significantly alters the way engineers communicate with manufacturers and suppliers in a variety of ways. When it involves customized plastic manufacture, this proves even more true. The manufacturing industry is always changing due to the emergence of new cutting-edge technologies.
By doing this, there is a better chance of removing quotation delays and enhancing prototype production methods. Order visibility throughout the supply channel becomes much easier to understand. Additionally, clients have access to a handy site that allows them to handle their orders from anywhere.
For instance, Djmolding now facilitates Industry 4.0 integration by fusing the newest technology, software, and analytics for big data. In this manner, creative solutions and industry best practices are ensured. It thereby guarantees the cost-effectiveness of producing low-volume plastic parts and leads to smarter production.
Conventional manufacturing entailed producing comparable goods in huge quantities. However, immediate manufacturing makes it possible to produce low-volume, customized items like small-scale plastic injection molding. It makes use of self-service paradigms and cloud-based technology. Customers can now track their orders throughout processing and receive quotes in real-time by utilizing this feature.
Customers may request accurate small-scale injection molding parts through on-demand manufacturing. The order amount will meet the needs for production right away. Numerous issues with time to market, interaction, design for manufacturing capability (DFM), and cost will be resolved by doing this. On-demand manufacturing is spearheading a respectable transformation in business as digital technology becomes more and more integral.
Main Advantages of Injection Molding at Low Volume
In quick production, one of the main procedures is plastic injection molding. This approach is fast-changing, allowing for quicker times to market for production. But the old-fashioned method takes longer than you would want.
In several aspects, the needs of the plastic market run counter to the realities of production. The complexity of the mold design could further extend the time necessary to produce the pieces. Nonetheless, low-volume injection molding contributes to the successful resolution of these issues. These are a few of its benefits.
Softer aluminum tooling is used.
The traditional molding method’s hardened steel mold tooling is not needed for low-volume injection molding. Instead, it makes the molds out of a softer aluminum alloy. Steel is significantly harder than aluminum. Therefore, it is quicker and easier to work with.
Furthermore, since an additional annealing step is not required, heat treatment can be performed more easily with aluminum tooling. Annealing steel tooling is frequently required to eliminate internal tension and achieve the necessary level of metal toughness. Additionally, the majority of surface treatments that are typically applied to steel can be applied to aluminum molds.
High-quality Parts Production
Although low-volume injection molding uses a weaker tooling material, the results are extremely robust and useful. It is a useful manufacturing method that may be used to create a variety of goods. Moreover, aluminum transfers heat more quickly than steel. The location of cooling lines is less important because of the improved conductivity. In this manner, additional mold components can be added. Therefore, low-volume plastic injection closes the gap between high-scale production and prototypes by ensuring higher design freedom.
Cut Costs
The common perception is that purchasing goods frequently results in cost savings. In some instances, this isn’t always the case. While this might hold true for home goods, it might not apply to building supplies. When it comes to manufacturing, the materials utilized in the process have a significant impact on the cost per unit. High-volume injection molding manufacturers can have minimum order requirements. They take this action to defray expenses and balance substantial manufacturing investments.
Conversely, low-volume injection molding frequently has substantially reduced overhead. Manufacturers are able to produce goods in this situation without requiring minimum orders. Thus, this might be really beneficial if you’re trying to start small-batch plastic manufacturing. Additionally, you won’t purchase anything from an out-of-date inventory. These all add up to significant expense savings.
Reduced lead time
In addition to being reasonably priced, the manufacturing process increases the production efficiency of plastic parts. It operates on a mechanism that facilitates quicker order quotations. In order to guarantee precise and prompt production, the software carefully examines the part design.
Furthermore, aluminum’s softness makes mold creation much simpler and faster. Furthermore, hardening is not required to improve durability. Consequently, production can begin in earnest as soon as the mold arrives at the manufacturing facility. This often results in a significant reduction in time to market, which is advantageous both for big and small product teams.
Modalities in Design
Short-run, smaller-quantity production is the focus of small-scale injection molding. Therefore, if a corporation chooses to change the design, it won’t have a significant effect. In this manner, the goods can be flawless before they are delivered to the customer.
A high-quality plastic injection molding technique provides immediate feedback, which improves manufacturability. It makes it possible to test innovative ideas across a range of sectors prior to mass-producing components.
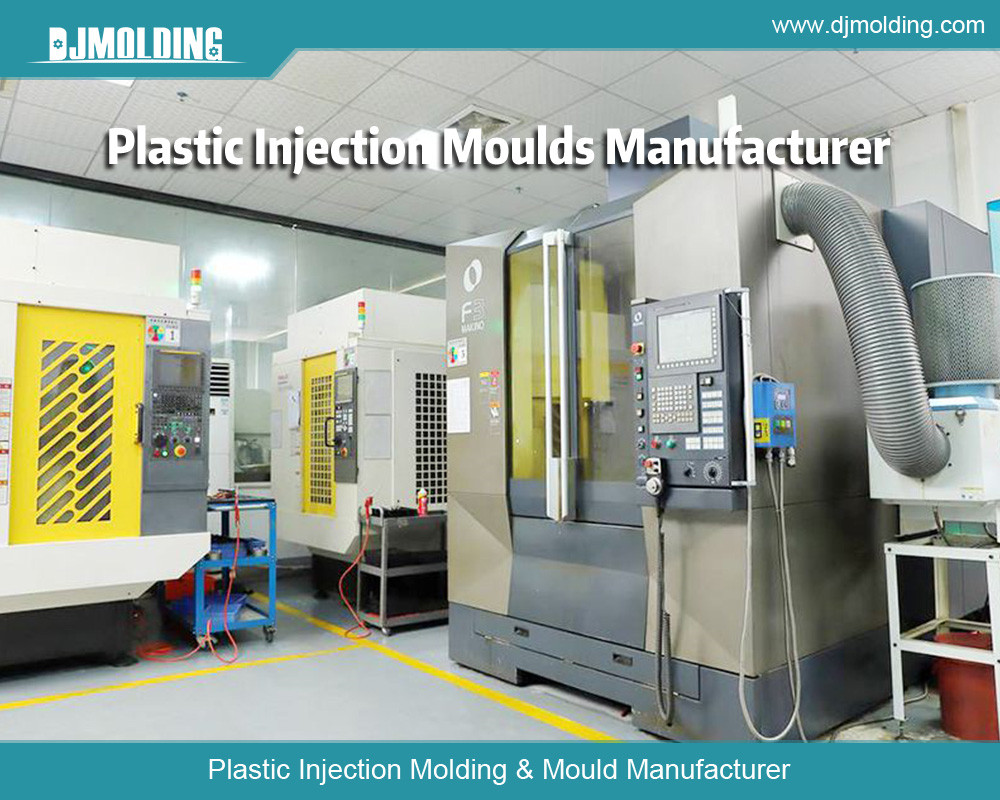
Overpass for Scale
The best place for a business to start if it wants to make plastic products on a large scale is with small-scale manufacturing. It facilitates the transition from prototyping to production. This approach doesn’t require a lot of commitment and produces a workable prototype. It also aids in process and product optimization.
For more about improving your injection molding process: the key to high-quality products,you can pay a visit to Djmolding at https://www.djmolding.com/molding-service/ for more info.