Maximizing Efficiency And Cost Savings With A Trusted Plastic Injection Molding Manufacturer And Supplier Near Me
Maximizing Efficiency And Cost Savings With A Trusted Plastic Injection Molding Manufacturer And Supplier Near Me
There is no doubting the fact that plastic injection molding remains a popular manufacturing process that entails injection of molten plastic into a mold for creation of a specific shape or part. This process is used in a variety of industries, including automotive, medical, and consumer goods. The benefits include high production rates, consistent quality, and the ability to create complex shapes and designs.
However, choosing the right manufacturer is crucial for achieving maximum efficiency and cost savings. A trusted manufacturer can help streamline the design process, select the right materials, implement lean manufacturing techniques, ensure quality control, and collaborate with customers to identify opportunities for cost savings.
This article will reveal how you can maximize efficiency and cost while working with the best plastic injection molding manufacturer.
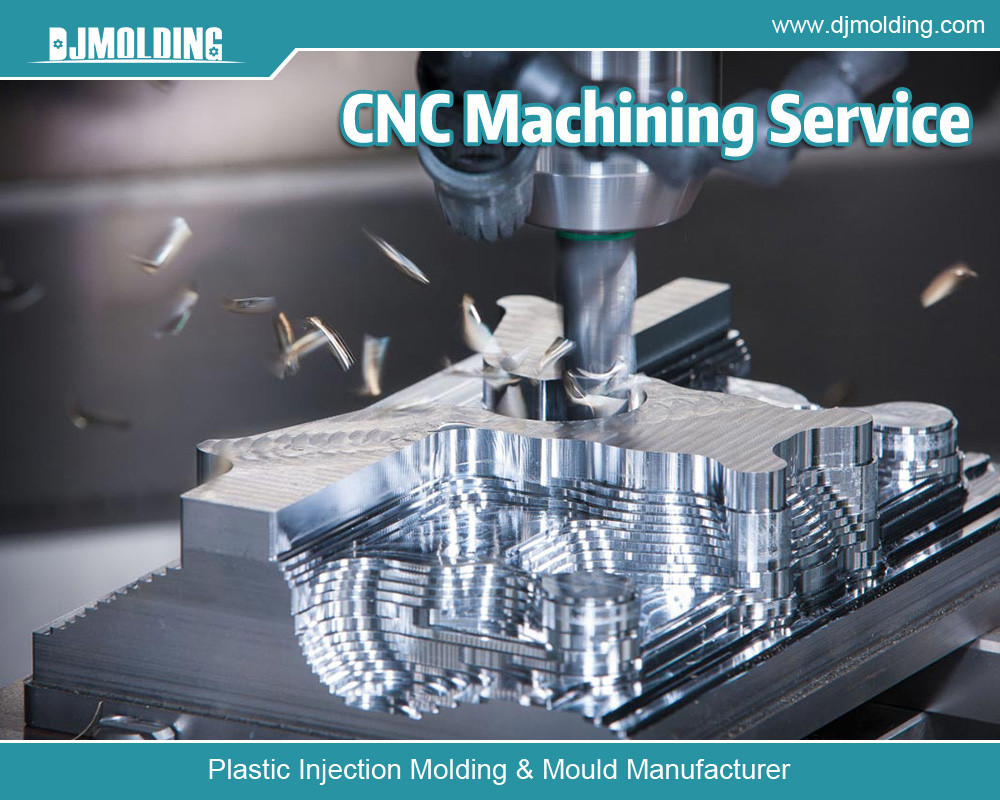
Streamlining the Design Process for Maximum Efficiency
Early collaboration between designers and manufacturers is essential for streamlining the design process and reducing time-to-market. By involving the manufacturer early on in the design process, designers can take advantage of design for manufacturability (DFM) principles to optimize their designs for efficient production.
DFM principles involve designing parts that are easy to manufacture and assemble, reducing the number of parts required, and minimizing the need for secondary operations such as drilling or machining. By designing parts with these principles in mind, designers can reduce design iterations and ensure that their parts are manufactured efficiently.
This is very crucial if you are really serious about achieving the goals of your projects while working with any plastic injection molding manufacturer.
Material Selection: Finding the Right Balance Between Cost and Quality
Choosing the right material for such process is crucial to achieve cost savings in the long run. Although high-quality materials may seem expensive initially, they can help reduce defects and improve part performance, leading to significant cost savings over time. However, it’s important to strike a balance between material cost and quality and performance requirements.
A reliable manufacturer can help identify cost-effective alternatives that meet the necessary performance requirements while reducing material costs. They can also provide valuable insights into the latest materials and technologies available in the market, helping businesses stay ahead of the competition. Ultimately, selecting the right material requires careful consideration of various factors, including durability, strength, flexibility, and environmental impact.
By working with an experienced manufacturer, businesses can make informed decisions that optimize their production processes and improve their bottom line.
Lean Manufacturing Techniques: Reducing Waste and Improving Efficiency
Lean manufacturing techniques have become increasingly popular in the plastic injection molding industry due to their ability to streamline production processes and improve overall efficiency. These techniques involve a systematic approach to identifying and eliminating non-value-added activities, such as excess inventory, overproduction, and unnecessary transportation.
By optimizing production flow, manufacturers can decrease lead times and also improve delivery times, resulting in increased customer satisfaction. In addition to reducing waste and improving efficiency, lean manufacturing techniques also focus on continuous improvement processes. This entails constantly reviewing as well as analyzing of production processes to identify areas which require improvement. It can also help in the implementation of changes to increase efficiency and reduce waste.
By continuously improving processes, manufacturers can stay ahead of the competition and meet the changing needs of their customers. Overall, the implementation of lean manufacturing techniques in molding plastic injection can result in significant cost savings while improving product quality and consistency. By eliminating waste and optimizing production flow, manufacturers can increase their profitability while providing high-quality products to their customers.
Quality Control: Ensuring Consistency and Reliability in Production
Molding plastic injection is a complicated manufacturing process that involves the use of high temperatures and pressures to mold plastic materials into various shapes and sizes. The process can be challenging, and even minor variations in temperature, pressure, or material composition can result in defects or poor part performance. Therefore, quality control is critical to ensure that the final product meets the required specifications and performs as expected.
Quality control processes in molding plastic injection typically involve several steps, including inspection of incoming raw materials, monitoring of the injection molding process, and testing of finished parts. During the inspection of raw materials, manufacturers check for any defects or inconsistencies that could affect the quality of the final product. They also ensure that the materials meet the required specifications in terms of composition, color, and other properties.
During the injection molding process, manufacturers monitor various parameters such as temperature, pressure, and cycle time to ensure that they are within the specified range. They also conduct regular checks on the molds to ensure that they are functioning correctly and producing parts that meet the required standards. Finally, manufacturers test finished parts to ensure that they meet performance requirements such as strength, durability, and dimensional accuracy.
They may use various testing methods such as visual inspection, mechanical testing, and chemical analysis to identify any defects or issues that could affect part performance. By implementing robust quality control processes in plastic injection molding, manufacturers can reduce defects, improve part performance, and ensure customer satisfaction. They can also minimize waste and rework, which can result in significant cost savings over time.
Collaborating with Your Manufacturer: Maximizing Cost Savings Through Partnership
Collaboration between manufacturers and customers is essential for identifying opportunities for cost savings and maximizing efficiency. By working together, manufacturers can help customers optimize their designs for efficient production, select the right materials, implement lean manufacturing techniques, and ensure quality control.
Long-term partnerships with trusted manufacturers can lead to significant cost savings over time by reducing design iterations, improving part performance, and streamlining production processes.
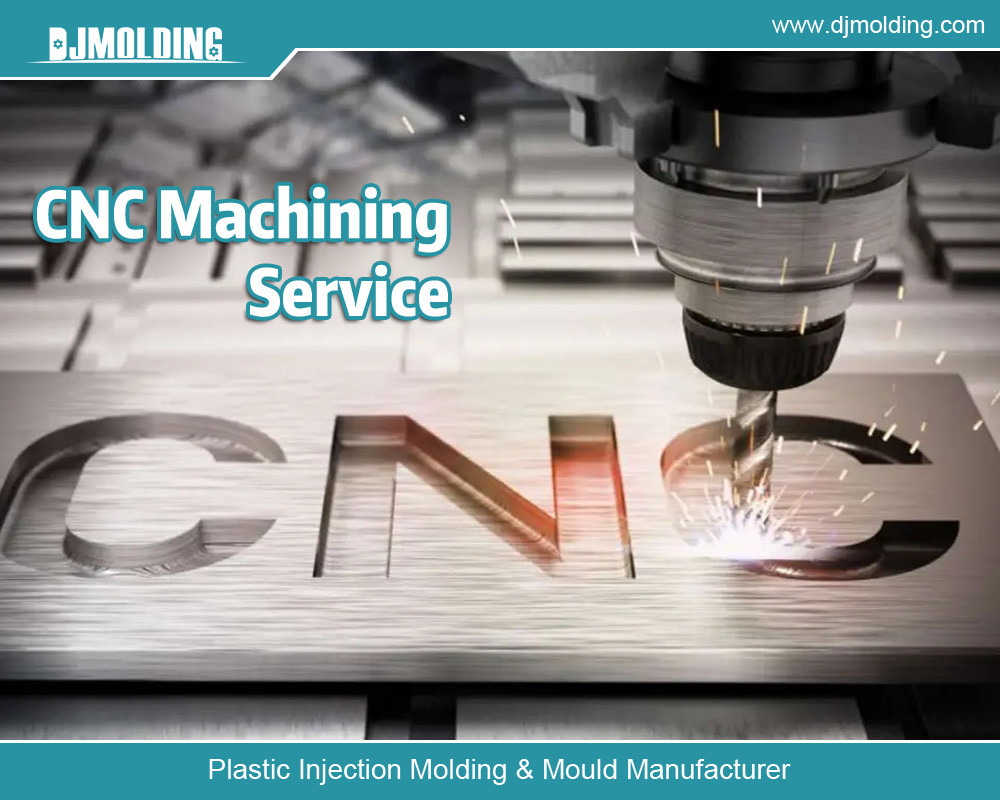
Conclusion
Choosing a trusted plastic injection molding manufacturer is crucial for achieving maximum efficiency and cost savings. By streamlining the design process, selecting the right materials, implementing lean manufacturing techniques, ensuring quality control, and collaborating with customers, manufacturers can help customers achieve long-term success.
Long-term partnerships with trusted manufacturers can lead to significant cost savings over time by reducing design iterations, improving part performance, and streamlining production processes. By working together, manufacturers and customers can achieve mutual success in the competitive world of plastic injection molding.
For more about maximizing efficiency and cost savings with a trusted plastic injection molding manufacturer and supplier near me,you can pay a visit to Djmolding at https://www.djmolding.com/ for more info.