Maximizing Efficiency With Low Volume Injection Molding Techniques
Maximizing Efficiency With Low Volume Injection Molding Techniques
Injection molding is a widely used manufacturing process that enables the production of large quantities of high-quality plastic products at a low cost. However, for businesses with low volume production needs, traditional injection molding techniques may not be the most efficient and cost-effective solution.
Fortunately, low-volume injection molding techniques have emerged as a viable option for those who require smaller quantities of products. Today, we will explore how low-volume injection molding techniques can maximize efficiency and save costs for businesses of all sizes.
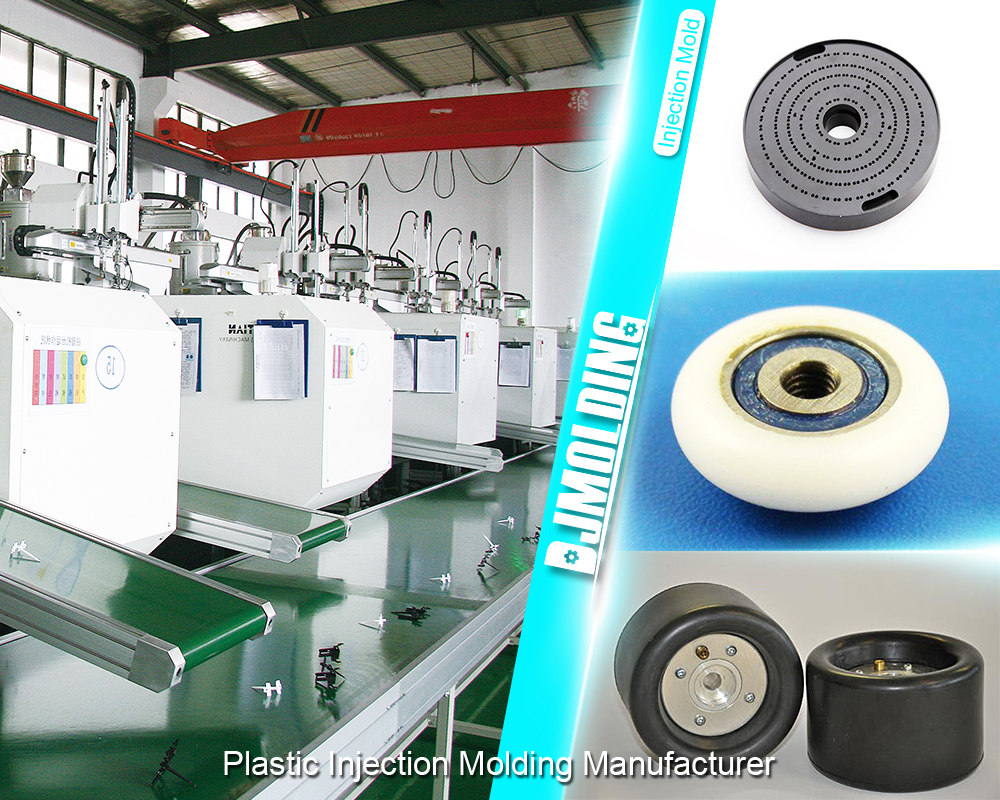
Benefits of Low-Volume Injection Molding Techniques
Reduced costs are one of the most significant benefits of low-volume injection molding techniques. Traditional injection molding requires expensive tooling and equipment, which can be cost-prohibitive for small production runs. Low-volume injection molding techniques, on the other hand, use less expensive tooling and equipment, making it a more cost-effective option for small production runs.
Faster turnaround times are another benefit of low-volume injection molding techniques. Traditional injection molding can take weeks or even months to produce parts, which can be a significant issue for companies that need parts quickly. Low-volume injection molding techniques can produce parts in a matter of days, allowing companies to get their products to market faster.
Increased design flexibility is also a significant benefit of low volume molding techniques. Traditional injection molding requires expensive tooling, which can limit design options. Low volume molding techniques, on the other hand, allow for more design flexibility, as the tooling is less expensive and can be modified more easily.
Lower material waste is another benefit of low volume molding techniques. Traditional injection molding can produce a significant amount of material waste, as the tooling is designed for high-volume production runs. Low-volume injection molding techniques, on the other hand, can produce parts with minimal material waste, making it a more sustainable option for companies.
Factors to Consider When Choosing Low-Volume Injection Molding Techniques
When choosing low-volume injection molding techniques, there are several factors to consider. Production volume is one of the most critical factors to consider, as low-volume injection molding techniques are best suited for small production runs. Material selection is also crucial, as different materials have different properties that can affect the production process.
Part complexity is another factor to consider, as more complex parts may require more advanced tooling and equipment. Tooling requirements are also important to consider, as different tooling options can affect the cost and production time of the parts.
Design Considerations for Low Volume Injection Molding
When designing parts for low-volume injection molding, there are several design considerations to keep in mind. Wall thickness is one of the most critical design considerations, as thicker walls can lead to longer production times and higher costs. Draft angles are also important to consider, as they can affect the ease of part ejection from the mold. Undercuts are another design consideration, as they can be challenging to produce with traditional injection molding techniques. Gate location is also important to consider, as it can affect the quality and consistency of the parts.
Materials Suitable for Low Volume Injection Molding
There are several materials suitable for low volume molding, including thermoplastics, thermosets, elastomers, and composites. Thermoplastics are the most commonly used material for low-volume injection molding, as they are versatile and can be used in a wide range of applications. Thermosets are also suitable for low-volume injection molding, as they can be molded into complex shapes and have excellent heat resistance.
Elastomers are another material suitable for low-volume injection molding, as they have excellent flexibility and can be used in a wide range of applications. Composites are also suitable for low volume molding, as they can be used to produce lightweight and durable parts.
Techniques for Achieving High Precision with Low-Volume Injection Molding
Achieving high precision with low-volume injection molding requires tight tolerances, advanced tooling, and process control. Tight tolerances are essential for producing parts with high precision, as they ensure that the parts are produced to the correct specifications. Advanced tooling is also crucial for achieving high precision, as it allows for more complex parts to be produced with greater accuracy. Process control is also important, as it ensures that the production process is consistent and repeatable.
Cost-Effective Strategies for Low-Volume Injection Molding
There are several cost-effective strategies for low volume molding, including tooling alternatives, material selection, and process optimization. Tooling alternatives, such as 3D printing, can be a cost-effective option for small production runs. Material selection is also important, as different materials have different costs and properties that can affect the production process. Process optimization is also crucial for reducing costs, as it ensures that the production process is as efficient as possible.
Applications of Low-Volume Injection Molding Techniques
Low-volume injection molding techniques can be used in a wide range of applications, including medical devices, aerospace components, consumer products, and automotive parts. Medical devices require high precision and accuracy, making low-volume molding techniques an ideal option. Aerospace components also require high precision and accuracy, as well as lightweight and durable materials.
Consumer products can benefit from low-volume molding techniques, as they allow for more design flexibility and faster production times. Automotive parts can also benefit from low-volume molding techniques, as they require high precision and accuracy, as well as lightweight and durable materials.
Future Trends in Low Volume Injection Molding Techniques
The future of low-volume injection molding techniques is likely to be influenced by additive manufacturing integration, smart manufacturing technologies, and sustainable materials and processes. Additive manufacturing integration can allow for more complex parts to be produced with greater accuracy and precision.
Smart manufacturing technologies can allow for the production process to be monitored and adjusted in real-time, ensuring that the parts are produced consistently. Sustainable materials and processes can also be a significant trend in the future of low volume injection molding techniques, as companies look for more environmentally-friendly options.
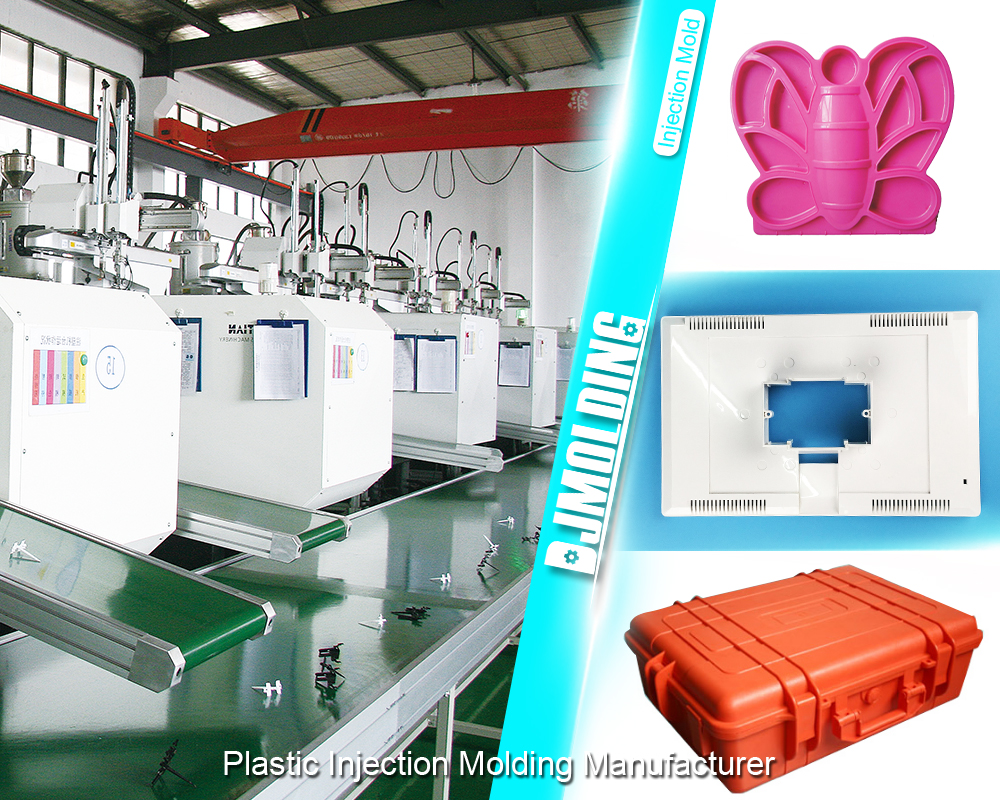
Conclusion
It is clear that low-volume molding techniques are a cost-effective and efficient option for companies that need to produce small quantities of parts quickly and accurately. Maximizing efficiency in manufacturing is crucial for companies to remain competitive in today’s market. By utilizing low volume molding techniques, companies can reduce costs, increase design flexibility, and minimize material waste. It is essential to consider factors such as production volume, material selection, part complexity, and tooling requirements when choosing low-volume injection molding techniques.
For more about maximizing efficiency with low volume injection molding techniques,you can pay a visit to Djmolding at https://www.djmolding.com/low-volume-injection-molding/ for more info.