Optimizing Efficiency: The Art of Low-Volume Plastic Parts Production
Optimizing Efficiency: The Art of Low-Volume Plastic Parts Production
Strategies for Increasing Low Volume Molding Parts by Injection Cost for Manufacturers of Little Batch Plastic Parts
Low-volume molding may be the best option if you want to use injection molding to make tiny quantities of items. Low-volume injection molding might, nevertheless, cost more per unit than high-volume molding. Elements influencing low-volume injection molding prices. Low-volume injection molding costs can vary depending on a number of parameters, such as cycle time, material choice, complexity and design of the mold, and finishing. The choice of material has a significant impact on low-volume injection molding costs. Some things are more costly than others, and they all have various qualities and specifications. When choosing materials for its parts, businesses need to take their cost-effectiveness into account.
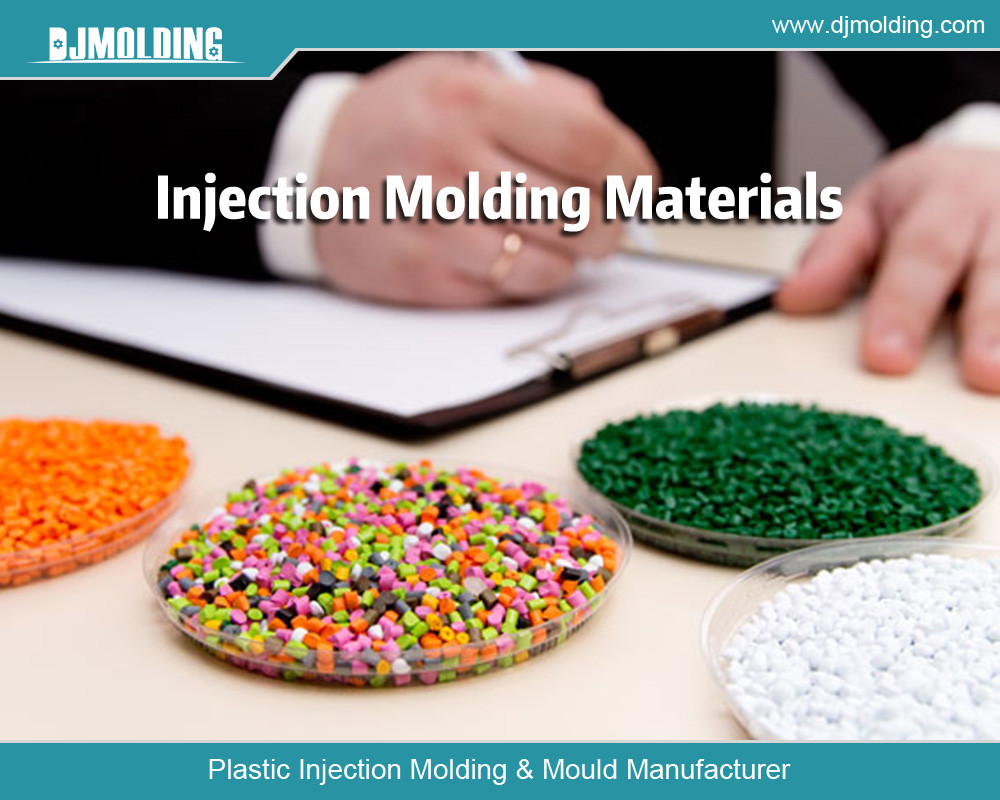
Mold creation
The complexity and design of the mold can also have an impact on low-volume injection molding costs. The time and money needed to create more intricate molds might raise the cost of manufacturing. Furthermore, more cavity molds can yield more parts in a cycle, which lowers the part cost overall.
Time of the cycle
Another important component that affects low-volume injection molding costs is cycle time. Because it takes a greater amount of resources to make each part, longer cycle times might result in higher manufacturing costs. Optimizing injection molding settings is crucial for businesses seeking to decrease cycle time and boost productivity.
Tips for maximizing low-volume injection molding parts by mold design
Another crucial element in low-volume injection molding cost efficiency is mold design optimization. By employing multi-cavity molds, streamlining part design, and lowering mold design complexity, businesses can maximize their mold design. Reducing production costs and mold complexity can be achieved by simplifying part design. Companies can increase the speed and economy of part production by minimizing the features and intricacies of the part design.
A decrease in price
Lowering the complexity of the mold design can also aid in lowering the cost of production. Businesses can cut down on the amount of time and money needed to make each part by streamlining the mold design. Because multi-cavity molds produce more parts every cycle, they can also help lower production costs. Because multi-cavity molds can make numerous parts at once, the cost per part is reduced overall.
Techniques for choosing the ideal material for injection molding in small quantities
Low-volume injection molding success depends on the choice of material. When choosing materials for their parts, businesses need to take into account the characteristics and specifications of the materials, their cost-effectiveness, availability, and lead time. When choosing material for low-volume injection molding, material needs and attributes are crucial factors to take into account. The rigidity, flexibility, and durability of various materials vary, so businesses need to choose materials that match the specifications for their components.
Another important factor to take into account when choosing components for low-volume molding by injection is cost. While choosing materials for its parts, businesses must take cost-effectiveness into account, as certain materials are more costly than others. The materials’ lead time and availability should be taken into account when choosing materials for low-volume molding by injection. Certain materials can be hard to come by or have lengthy lead times, which could throw off budgets and production timelines.
Best Practices for Low-Volume Induction Molded Parts Post-Processing and Finishing
In low-volume injection molding, finishing and finishing are essential processes for creating high-quality products. By employing surface finishing techniques, ensuring correct trimming and deburring, and putting inspection and control procedures in place, businesses may guarantee the quality of their products. Parts can be made to meet standards by ensuring that superfluous material is removed and rough edges are smoothed off by proper trimming and deburring. Surface finishing methods like painting and polishing can also make components look and work better.
Methods for reducing low-volume injection molding cycle times
In low-volume injection molding, cycle time minimization is crucial to cost optimization. By utilizing hot runners and other cutting-edge molding technologies, improving injection molding parameters, and maintaining equipment appropriately, businesses can reduce cycle time.
Reducing cycle time and improving efficiency can be achieved by optimizing injection molding parameters. In order to make parts more rapidly and economically, businesses can adjust parameters like injection speed, pressure, and temperature.
Increasing efficiency and cutting cycle time can also be achieved by utilizing hot spindles and other cutting-edge molding technology. Inject molding systems known as “hot runners” use heated tubes to maintain the plastic material’s molten condition, cutting down on the amount of time needed for heating the substance during each cycle.
Reducing cycle time and improving efficiency also depend on proper equipment maintenance. Equipment downtime may be avoided, and maximum efficiency can be ensured with routine maintenance and cleaning.
How to Use Technology to Cut Costs in Low-Volume Injection Molding
Utilizing technology and automation is another technique to cut expenses in low-volume molding processes. To boost productivity and cut expenses, businesses can employ computer engineering and modeling tools, automation and robotics in the manufacturing process, data analytics, and process monitoring. Automation and robotics can lower labor costs and boost productivity in the manufacturing process. Robots are faster and more accurate than humans at repetitive operations like packaging and part removal.
The amount of time and money needed to make parts can be decreased by utilizing digital engineering and simulation techniques. With the use of these technologies, businesses may virtually develop and test parts, negating the need for tooling modifications and actual prototypes. By combining process monitoring and data analytics, businesses can find opportunities for development and streamline their production procedures. Businesses can find inefficiencies and make changes to boost productivity and cut costs by examining data on production performance.
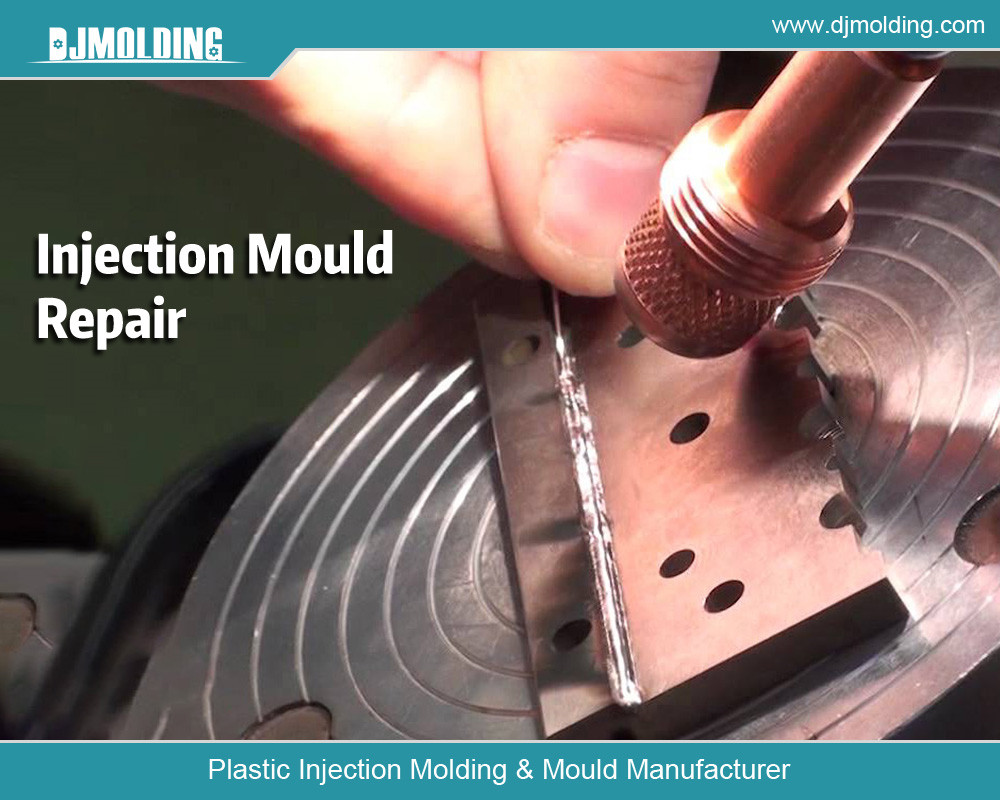
Conclusions Regarding Optimizing Low-Volume Injection Molding Expenses
In summary, low-volume injection molding enables businesses to swiftly and affordably create small numbers of high-quality parts, making it a crucial component of product development. Through process optimization and the use of automation and technology, businesses can save expenses and boost productivity in low-volume plastic injection molding.
For more about optimizing efficiency: the art of low-volume plastic parts production,you can pay a visit to Djmolding at https://www.djmolding.com/the-advantages-of-low-volume-injection-molding-for-small-scale-plastic-parts-manufacturing/ for more info.