Plastics injection molding in various ways: Injection over other methods
Plastics molding in various ways: Injection over other methods
In the manufacture of pieces of plastic material, various types of molds are used that delimit the plastic mass, while hardening and keeping the desired shape. These molds are mounted on a press that will open and close the mold, which will apply great pressure if necessary, and which will facilitate loading the mold by external means.
The plastic material is held in the mold under pressure while it hardens sufficiently so that its shape is retained after removal.
Steam, hot water, oil or electricity are used to heat the molds. The type of heating to be used in a given job is determined by the means available and by the nature of the job itself.
In some cases, the molds must be cooled by circulating water or another coolant, to keep the temperature of the molds constant, equipment is available for this purpose.
Plastic compounds differ greatly from one another and lend themselves to a wide variety of molding methods. Each material is better adapted to one of the methods, although many can be manufactured by several of them. The material to be molded is in granular powder form, although for some there is a preliminary preforming operation before use.
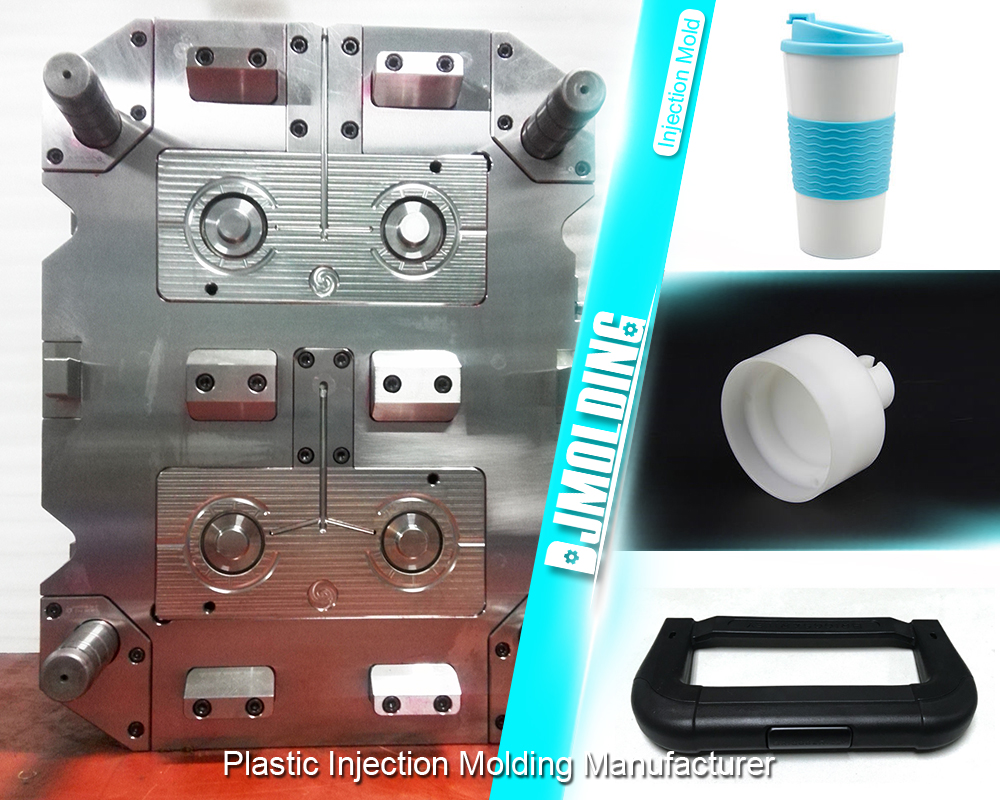
Injection as the best process
Injection molding is the most widely used process for the manufacture of thermoplastic components. In this process, the molten plastic is forced into the cavity of the metal die that has been machined to the desired product shape.
When the plastic has solidified enough, the die is opened and the part is removed. The raw plastic material is placed in the form of pellets in the hopper of the machine. Then it enters the heater where it melts. The molten plastic is then pushed into the die cavity by direct application of hydraulic or mechanical pressure.
Large capacity injection molding machines can exert several hundred tons of pressure and can be used to make large pieces of plastic in one piece. Examples include automotive body components such as assemblies, hoods, fenders, bumpers, and grills.
The injection process can be summarized in five steps:
Step 1: The parts of the mold are closed.
Step 2: The piston moves forward and pushes the material into the heating cylinder, at the same time injecting the plasticized material into the mold.
Step 3: The piston remains in this position for some time maintaining pressure through the nozzle. During this time the material is cooling and solidifying as necessary to maintain the shape of the mold.
Step 4: The piston recoils, but the mold remains closed, a new quantity of material falls from the feeder hopper.
Step 5: The mold opens at the same time that it rejects the molded parts by means of the action of the drills.
The advantages of this process are:
- Saving of material, manufacturing space and production time.
- Accuracy of shape and dimensions of the injected parts.
- Possibility of forming holes and inserting elements from other materials with which production is complete.
- Smooth and clean surface of the injected parts.
- Good resistance properties.
- Quick production of large quantity of parts.
The disadvantages of the process are:
- Not recommended for low production due to high tooling cost.
- Resins can solidify before filling the mold when dealing with very thin sections.
- Complicated parts increase tooling cost.
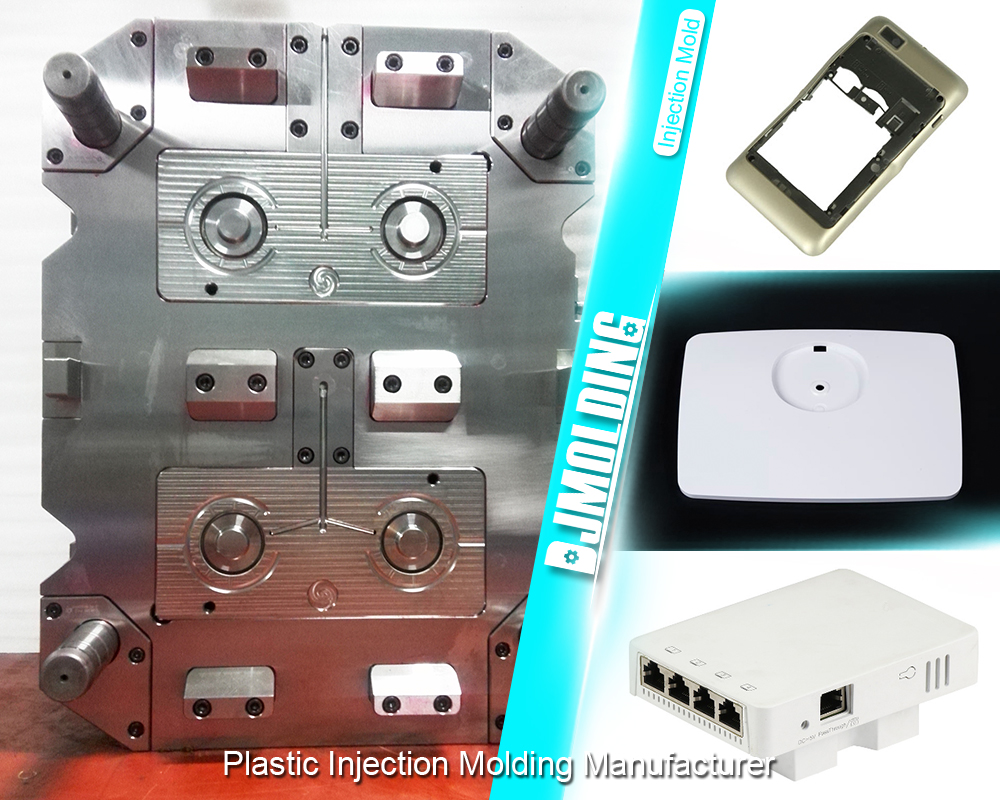
For more about the plastics injection molding in various ways: Injection over other methods,you can pay a visit to Djmolding at https://www.djmolding.com/ for more info.