The Advantages of LSR Liquid Silicone Rubber Injection Molding For Medical Devices
The Advantages of LSR Liquid Silicone Rubber Injection Molding For Medical Devices
The medical industry requires high-quality products that meet strict standards and regulations. This is where LSR or Liquid Silicone Rubber injection molding shines. It is a cost-effective and efficient manufacturing process that offers a wide range of benefits compared to traditional molding techniques. In this post, we’ll explore the benefits of LSR molding for medical devices and why it’s a valuable solution for the healthcare industry. So buckle up, because we’re about to dive into a world of cutting-edge technology that’s revolutionizing medical device manufacturing!
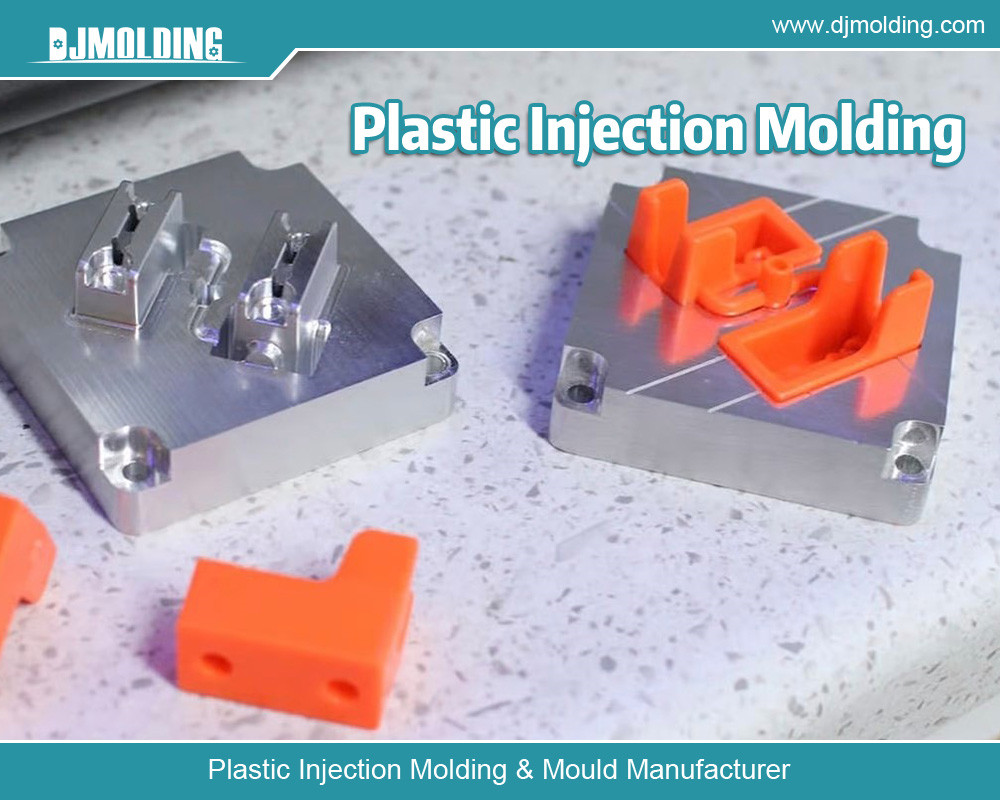
What is LSR Molding?
Before delving into the main details of this post, it is crucial to explain what LSR injection molding implies. It is a process of injecting LSR into a mold to produce a finished product. The process involves heating the LSR material to a liquid state and injecting it into a mold cavity. The mold is then cooled, and the finished product is removed. LSR injection molding offers several advantages over other molding methods, including high precision, consistency, and design flexibility.
Benefits of LSR Molding for Medical Devices
LSR molding offers several benefits for the production of medical devices. These benefits include improved product quality, enhanced design flexibility, and cost-effectiveness. Let’s explore each of these benefits in more detail.
Improved Product Quality with LSR Injection Molding
LSR molding is a highly effective manufacturing process that is widely used in the production of medical devices. One of the key benefits of this process is that it provides a high level of consistency and precision, which is essential for ensuring that each product meets the required specifications.
The LSR material used in this process is highly stable and has a low viscosity, which allows for precise control over the molding process. This means that the finished product will be consistent in size, shape, and quality, which is important for ensuring that it functions correctly and meets the needs of patients.
In addition to providing consistency and precision, LSR injection molding also helps to reduce defects in the finished product. Defects such as flash, sink marks, and warpage can compromise the safety and effectiveness of medical devices, so it is important to minimize them as much as possible.
Enhanced Design Flexibility with LSR Injection Molding
LSR molding enhances design flexibility by allowing for complex geometries, overmolding, and customization. The LSR material can be molded into intricate shapes and designs, which is particularly useful for medical devices that require complex geometries. Overmolding is also possible with LSR injection molding, which allows for the integration of multiple materials into a single part. This is useful for medical devices that require different materials for different functions. Finally, LSR injection molding allows for customization of medical devices, which can improve patient outcomes and satisfaction.
Cost-Effective Manufacturing with LSR Injection Molding
LSR molding is a popular manufacturing process that involves injection of Liquid Silicone Rubber in a mold to create a wide range of products. This process is highly cost-effective due to several factors. Firstly, the LSR material is highly stable and requires minimal processing, which reduces labor costs. This means that fewer workers are needed to handle the material, resulting in lower labor costs for manufacturers.
Secondly, LSR molding has a short cycle time, which allows for faster production times. This means that manufacturers can produce more products in a shorter amount of time, resulting in increased efficiency and productivity. This is especially important for companies that need to produce large quantities of products quickly.
High Precision and Consistency with LSR Injection Molding
LSR molding achieves high precision and consistency by providing precise control over the molding process. The LSR material is highly stable and has a low viscosity, which allows for precise control over the molding process. This results in a finished product that is consistent in size, shape, and quality. Additionally, LSR imolding reduces variability, which improves product performance and reduces the risk of failure.
Biocompatibility and Sterilization of LSR Medical Devices
LSR is biocompatible and easily sterilized, which is essential for medical devices. LSR is a non-toxic material that does not contain any harmful chemicals or additives. Additionally, LSR is resistant to bacteria and can be easily sterilized using standard methods such as autoclaving or gamma radiation. This ensures the safety and effectiveness of medical devices and ensures compliance with regulatory requirements.
Durability and Longevity of LSR Medical Devices
LSR medical devices are durable and long-lasting, which reduces replacement costs and improves patient outcomes. LSR is a highly durable material that can withstand harsh environments and repeated use. Additionally, LSR is resistant to aging and degradation, which ensures the longevity of medical devices. This reduces the need for frequent replacements and improves patient outcomes.
Environmental Sustainability of LSR Injection Molding
LSR molding is environmentally sustainable due to reduced waste, energy efficiency, and recyclability. LSR injection molding produces minimal waste, which reduces material costs and environmental impact. Additionally, LSR injection molding is energy-efficient, which reduces energy consumption and greenhouse gas emissions. Finally, LSR is recyclable, which reduces the need for virgin materials and reduces environmental impact.
Future Trends and Innovations in LSR Injection Molding for Medical Devices
The future of LSR injection molding for medical devices is bright, with several trends and innovations on the horizon. These include the use of advanced materials with conductive properties, and the integration of sensors and electronics into medical devices. Additionally, the use of 3D printing for LSR injection molding is becoming more prevalent, which allows for faster prototyping and customization.
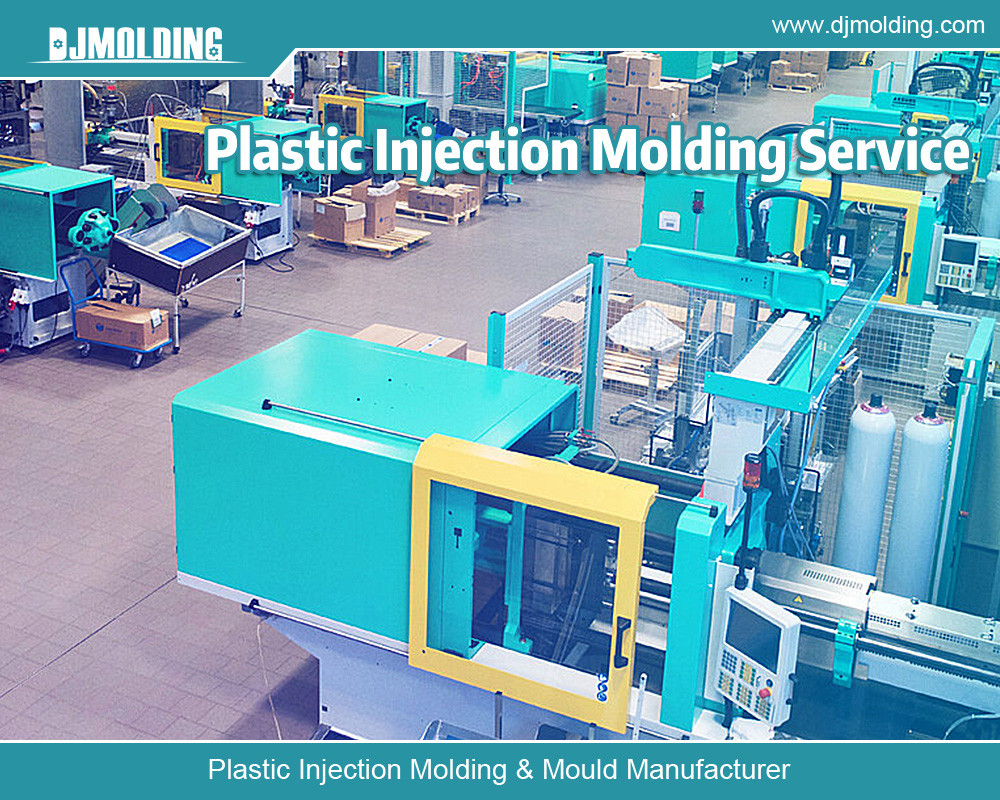
Conclusion
LSR molding offers numerous benefits for the production of medical devices, including improved product quality, enhanced design flexibility, and cost-effectiveness. Additionally, LSR medical devices are biocompatible, easily sterilized, durable, and environmentally sustainable. Manufacturers should consider LSR injection molding for their medical device production needs to improve product performance, reduce costs, and ensure regulatory compliance. The future of LSR injection molding for medical devices is bright, with several trends and innovations on the horizon that will continue to improve the safety and effectiveness of medical devices.
For more about the advantages of lsr liquid silicone rubber injection molding for medical devices,you can pay a visit to Djmolding at https://www.djmolding.com/liquid-silicone-rubberlsr-injection-molding/ for more info.