What Is Rapid Tooling Injection Molding For Plastic Parts Manufacturing?
What Is Rapid Tooling Injection Molding For Plastic Parts Manufacturing?
The plastic parts industry is booming due to the practical manufacturing process known as rapid tooling. This ingenious method of production streamlines your costs with a wide range of tactics available, such as 3D printing, CNC machining, and injection molding – letting you construct your prototypes in almost no time!
You have complete flexibility when designing, but some factors must be considered before opting for this technique. In this post, we’ll dive deep into what rapid tooling entails, its pros and cons, cost comparison vs. traditional manufacturing techniques, and even consider what the future may bring when bringing products from the blueprint to reality conveniently yet cost-effectively.
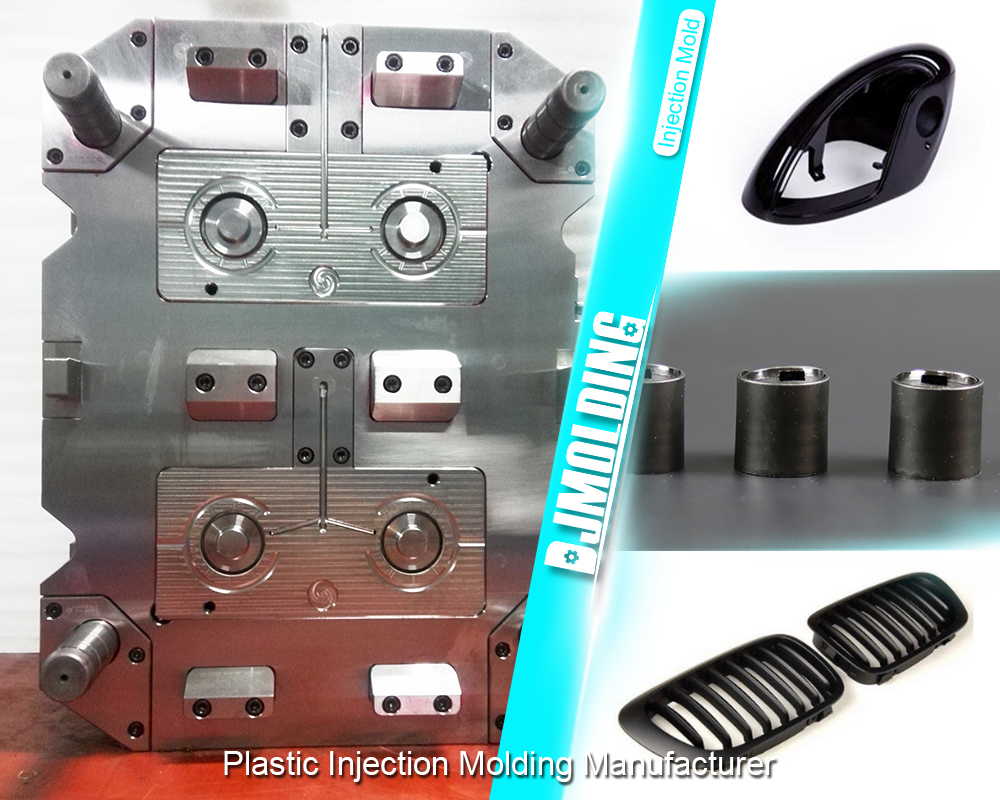
The Need for Rapid Tooling in Plastic Parts Manufacturing
Amidst these trying times in the manufacturing industry, it’s essential to be quick. Long-established methods for plastic parts production involve complex processes, such as fabricating molds and dies, which can drag on for weeks or months. Not to mention, design modifications require additional new molds, thus further insinuating delays.
But with revolutionary rapid tooling techniques being incorporated lately, there’s finally some hope! Utilizing avant-garde technologies like 3D printing and CNC machining enables manufacturers to use efficiency when producing their products.
This boosts speed within market cycles while cutting down costs — a win-win situation! Nowadays, companies needn’t worry about missing deadlines; they can confidently compete in this rat race knowing they can access these remarkable solutions.
Types of Rapid Tooling Techniques for Plastic Parts Manufacturing
With all the quick-turnaround tooling solutions for plastic parts out there, 3D printing’s got to be one of the most popular. Layer by layer, it takes a digital model and turns it into an object—that complex, right? Ideally suited for prototypes made in an instant but not so dependable when you’re cranking out high volumes day after day.
CNC machining is another way to use computer-controlled machines to carve your part from solid plastic blockage. You get tight tolerances and can work through both prototyping and production. It could be more wallet-friendly if you have big batches rolling off the assembly line repeatedly.
Why don’t we look at time-honored injection molding? Molten plastic is thoughtfully injected into molds until the shape you were hoping for arrives! Sure, traditional long lead times remain a bummer when dealing with old-school methods, yet rapid tooling using 3D-printed molds lets you tweak velocity while offsetting expenses.
Advantages of Rapid Tooling for Plastic Parts Manufacturing
Rapid tooling offers numerous advantages to manufacturing plastic parts that can’t be ignored.
It is super-fast
The biggest draw is its intense speed–traditional tooling requires weeks or months to craft a single mold or die, but with rapid tools, you can produce what you need in a matter of days or sometimes hours! This allows businesses to stay one step ahead of ever-changing market demands and get their products onto shelves faster than they’ve ever dreamed possible.
It can reduce cost
Cost savings are an even bigger bonus – traditional methods require substantial investments for costly molds and dies. Still, spending stays low regarding rapid tooling like 3D printing and CNC machining since you don’t need expensive tooling. Plus, there’s less waste, so materials are used more efficiently, keeping your stash nice and trim.
High level of flexibility
Design flexibility increases either way, though – no matter how you look at it because once updated products only require quick edits with the fast techniques that come along with Rapid Tooling instead of starting from scratch with new molds every single time (which isn’t cheap!). With Rapid tools, anybody can try different ideas before committing to complete production on any scale!
improved quality
Beyond everything discussed already, we must mention product quality improvement too. Precision parts achieved by 3D printing or other formatting machines ensure parts fit well together, significantly reducing the requirement for post-production fix-ups so your finished goods always look as good as originally intended.
Limitations of Rapid Tooling for Plastic Parts Manufacturing
Rapid tooling has definite perks, but there’s a flip side. Mainly, the materials you can use and their properties may be lower-grade than traditional methods, less robust in terms of durability, plus restricted on the range you’ve got to choose from.
And if production is your goal? No contest: traditional techniques like injection molding leave rapid tooling in the dust for mass production because of its faster cycle time and cost-per-unit ratio.
Lastly, rigidity comes into play as 3D printed molds usually lack compared to steel molds used for traditional methods – causing more frequent replacement costs over time.
Factors to Consider When Choosing a Rapid Tooling Technique for Plastic Parts Manufacturing
Time’s ticking when it comes to plastic parts production – you have to pick the right rapid tooling technique.
Remember that different techniques have limitations, so bear those materials and performance requirements in mind. If you need to produce a sizable batch of goodies, moving to traditional tools like injection molding is best.
However, if time is money and you need a few with fiddly details, 3D printing or CNC machining might be your stick-out picks. Design complexity is also crucial here: rapid tooling makes life easy if those creations are tricky to craft otherwise.
It’s undeniable – the budget is critical. Rapid tooling techniques have cost-cutting perks, but it’s essential to compare those initial costs against long-term advantages and potential drawbacks before deciding. Ultimately, deciding which technique works best requires careful consideration of these elements.
Lastly, when quick turnarounds trump all else, consider speedy shortcuts, as they may work wonders on that timeline conundrum!
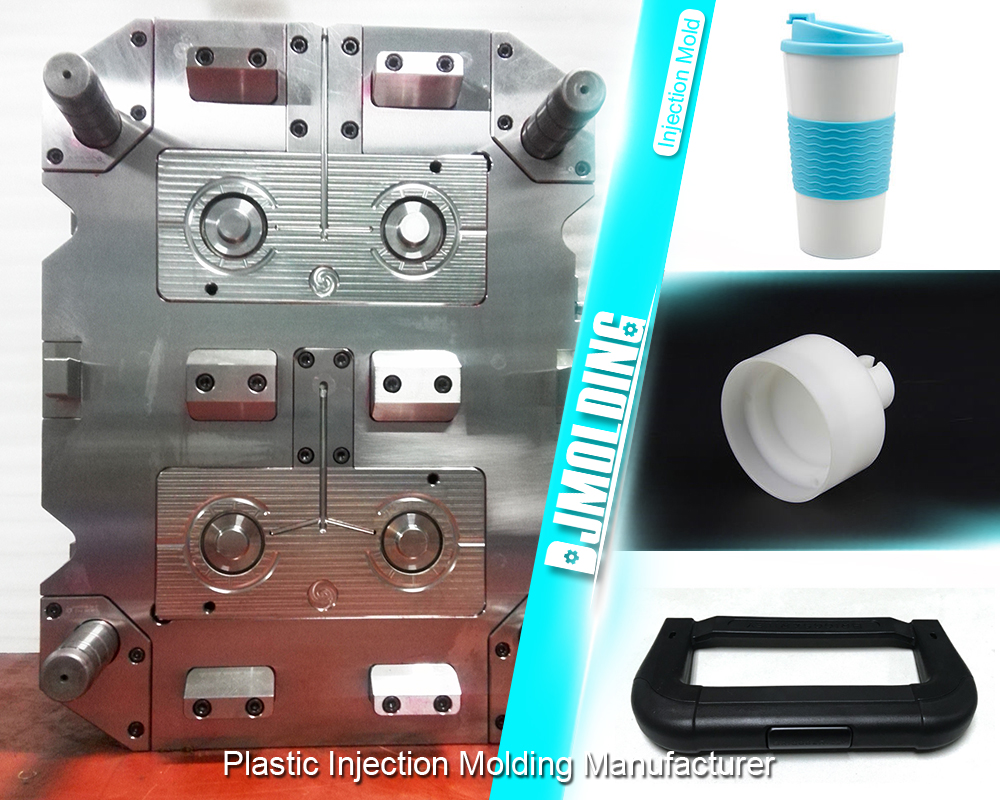
Final Thoughts
Well, there are certainly pros and cons when it comes to rapid tooling for plastic parts manufacturing. On the one hand, we have faster turnaround times, more design flexibility, and improved product quality. Still, on the other hand, there’s lower durability than traditional tooling, fewer material options, and less production volume.
If you’re weighing up your options here, it pays to look at factors like your budgetary restraints and projected batch size, not forgetting time constraints or design complexity. What does all this boil down to? In the end, you need cast-iron assurance that whatever decision you make has been thoroughly thought through!
For more about what is rapid tooling injection molding for plastic parts manufacturing,you can pay a visit to Djmolding at https://www.djmolding.com/best-top-10-rapid-prototyping-services-manufacturers-and-rapid-tooling-services-companies-in-canada/ for more info.