Description of the plastic injection molding method and manufacturing process step by step
Description of the plastic injection molding method and manufacturing process step by step
In the last fifty years the plastic materials industry has developed, of gigantic proportion, dominating over basic materials, even surpassing the steel industry. Plastics have entered every home regardless of social status, in all cities including the most remote and in industrialized countries, as in all economies. The development of this industry is fascinating and has changed the way of the world in which we live.
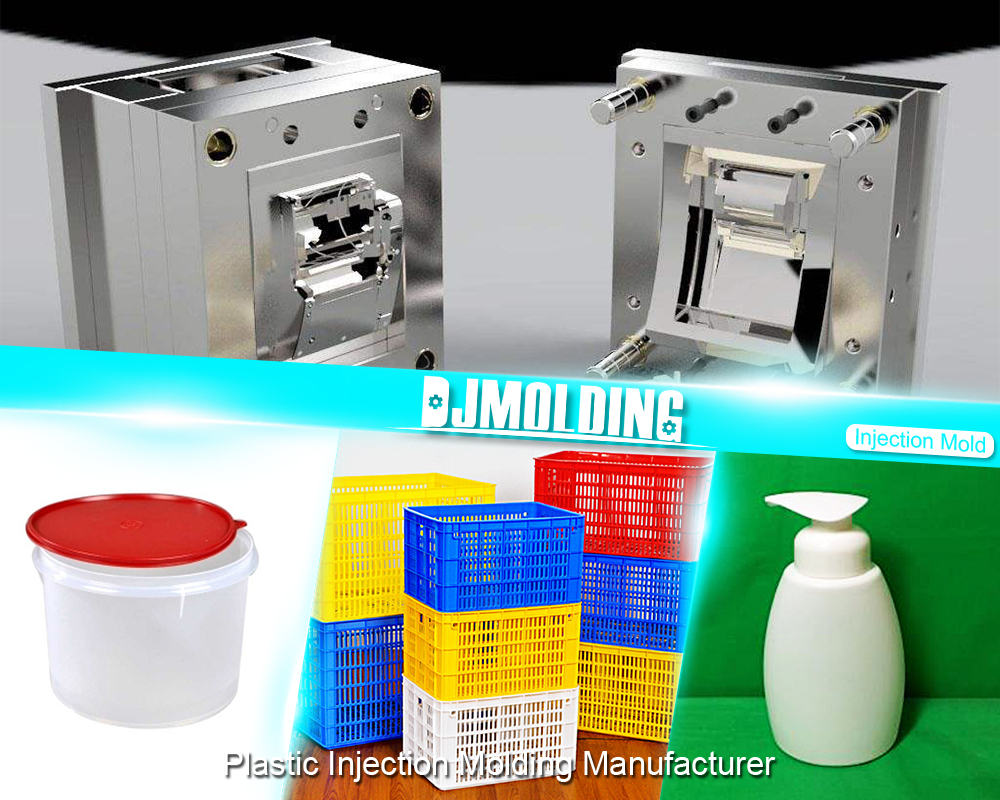
Injection Molding Process
Plastic compounds differ greatly from one another and lend themselves to a variety of processing methods. Each material is better suited to one of the methods, although many can be manufactured by several of them. In most processes, the molding material is in powder or granular form, although for some there is a preliminary preforming operation before use. When heat is applied to a thermoplastic material to melt it, it is said to be plasticized. Already molten or heat laminated material can be made to flow by applying pressure and filling a mold where the material solidifies and takes the shape of the mold. This process is known as injection molding. The basic principle of injection molding comprises the following three basic operations:
- a) Raise the temperature of the plastic to a point where it can flow under the application of pressure. This is normally done by heating and chewing the solid granules of the material to form a melt with a uniform viscosity and temperature. Currently, this is done inside the barrel of the machine by means of a screw, which provides the mechanical work (friction) that together with the heat of the barrel melt (plasticize) the plastic. That is, the screw transports, mixes and plasticizes the plastic material. This is shown in the figure
- b) Allow solidification of the material in the closed mold. At this stage the molten material already laminated in the machine barrel is transferred (injected) through a nozzle, which connects the barrel to the various channels of the mold until it reaches the cavities where it takes the shape of the final product.
- c) Opening of the mold for the extraction of the piece. This is done after keeping the material under pressure inside the mold and once the heat (which was applied to plasticize it) is removed to allow the material to solidify in the desired way.
In the various molding procedures, the variations in melting or plasticizing temperature play a different role depending on whether it is a thermoplastic material or a thermofix.
The fusion of the thermoplastic materials is carried out gradually in the plasticizing cylinder, under controlled conditions. The external heating provided by the plasticizing cylinder adds the heat generated by the friction of the spindle that rotates and mixes the material. The temperature control in the different zones of the plasticizing cylinder is carried out by means of thermocouples inserted at various points along the path of the material, from the hopper to the nozzle. Thermocouples are connected to automatic control instruments, which maintain the temperature of each zone at a preset level. However, the actual temperature of the melt to be injected into the mold may be different from that recorded by thermocouples either on the cylinder or at the nozzle.
For this reason, it is advisable to directly measure the temperature of the material by making a little material come out of the nozzle on an insulating plate and make the measurement right there. Variations in temperature in the mold can produce parts with variable quality and different dimensions, each separation of the operating temperature results in faster or slower cooling of the molten mass injected into the mold cavity. If the mold temperature is lowered, the molded part cools down more quickly and this can create a marked orientation in the structure, high internal stresses, mechanical properties and poor surface appearance.
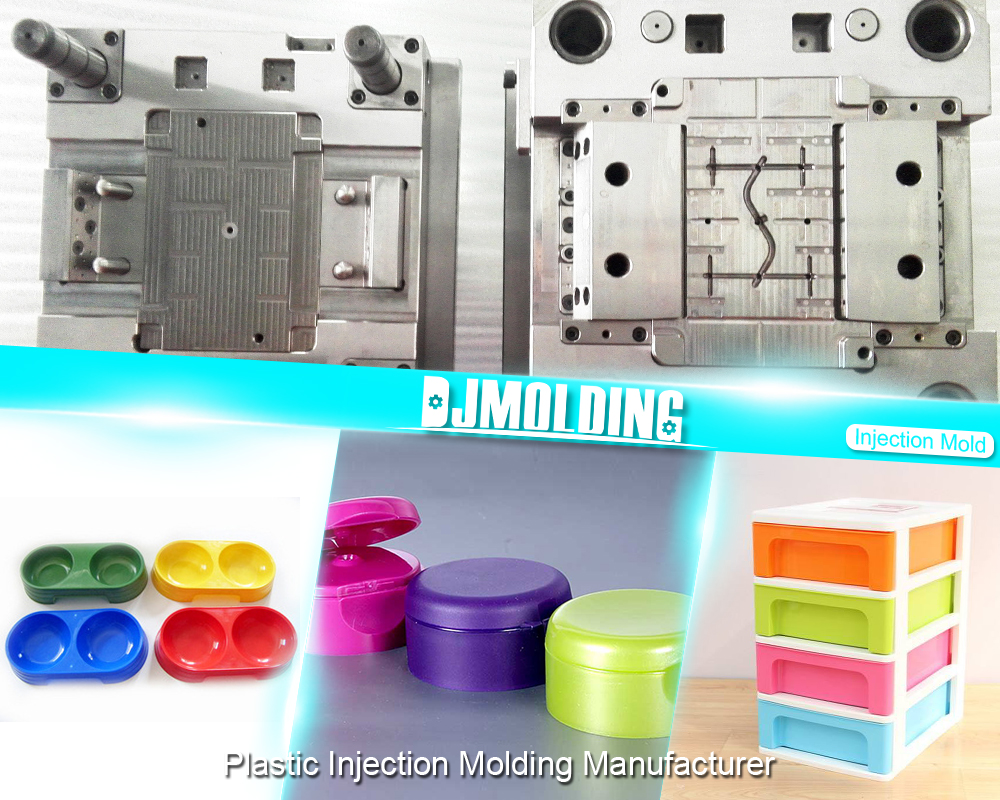
For more about the description of the plastic injection molding method and manufacturing process step by step,you can pay a visit to Djmolding at https://www.djmolding.com/ for more info.