Different types of injection molding technology for plastic parts manufacturing companies
Different types of injection molding technology for plastic parts manufacturing companies
The manufacturing industry relies on the versatility of plastic to make a wide array of products. Plastic-based products are made industrially through a process called injection molding. This is a suitable form of manufacturing plastic products due to its ability to be melted and harnessed in its molten state. Due to this essential benefit of plastics, injection molding technology has been enhanced and evolved into several types. This post focuses on the types of injection molding technology used in the plastic manufacturing industry.
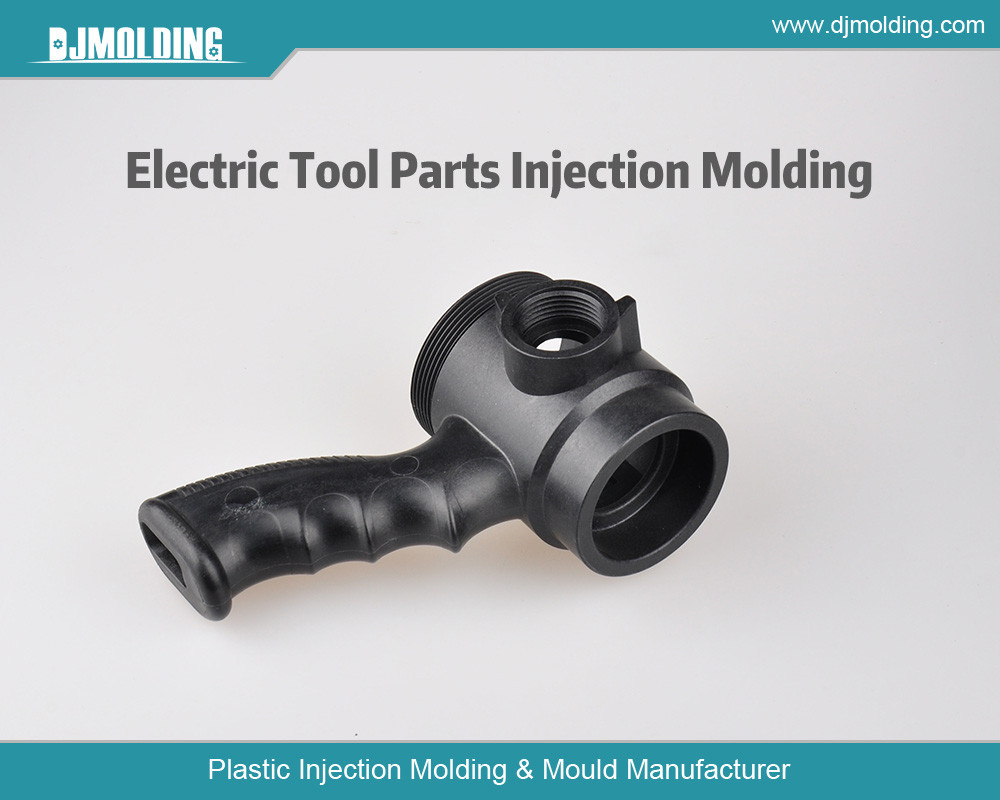
An overview of plastic injection molding
The plastic injection molding process relies on the use of a machine which is used to inject the molten plastic material into a suitable mold. The mold is usually shaped in the form of the final product to be made. When it is in its dry state, the final product is taken out of the mold for further processing and assembly. There are different applications of the injection molding technology. This has evolved into the different types of injection molding technology that we see today.
What are the types of injection molding technology?
When it comes to injection molding technology, we have five different types. Each type of injection molding technology has its unique properties and attributes. These include:
1. Gas-assisted injection molding
In this type of injection molding technology, an inert gas subjected to pressure is forced into the mold. The gas is usually introduced into the mold after inserting the molten form of plastic. This gas is used to force the materials right onto the walls of the mold. This is used to create a cavity. This molding technology can be used to reduce the number of materials used. It is also known to substantially reduce the amount of time it takes it to cool off. This technology works with a wide range of plastic materials.
2. Thin-wall molding
In this type of molding technology, the molten plastic is placed in a thin-walled mold. This helps to save costs and materials during the production process. This helps to reduce the total product cycle time while working to increase the needed pressure of the injection. Thin-walled molding technology has the highest precision when it comes to different technologies.
3. Liquid-silicone injection molding
This is a unique molding technology that helps in the mass production of products made from silicone rubber. Since this technology uses silicone rubber (thermoset rubber), it will need to undergo the process of vulcanization. The silicone rubber in its cold state is injected into the heated cavity of the mold. It is then vulcanized. With this mold injection technology, you will need special machines like metering units, mixers, and molds with perfect seals. This injection molding technology is automated to prevent errors from operators. Another benefit of this molding technology is that you do not need to melt the material and it can be used readily in its liquid form.
4. Structural foam molding
This injection molding technology can be used to make very big industrial parts in large volumes. This material is stored in its liquid form separately before it is then introduced inside the mold where it is mixed. The mixing process involves the introduction of gas inside the mold. This triggers a chemical reaction that leads to the formation of a foam. This foam has a highly porous interior but an exterior with a high density, which forms a protective skin. This molding technology is known for making cost-effective, lightweight, and strong parts.
5. Metal injection molding
This is the newest type of injection molding technology with the most unique properties. It is used to produce metal products through the process of injection molding. The process involves the mixture and granulation of metal powder and a binder. The resulting feed-stock is then forced to go through the injection unit. The raw product is then molded carefully. Then, it is cleaned and purified to produce a complete metallic product. This product undergoes further processing to make it suitable for use in different industries. This type of molding technology helps manufacturers produce complex metal parts that are not possible with traditional methods. It also supports the production of large volumes of metallic products while minimizing the waste of metal parts.
Application of the injection molding technology
The different molding technologies can be applied in various industries that cater to the global consumer market. It has an endless number of applications as this is a very popular way of producing industrial goods. The following are good examples of where the molding technologies can be applied:
- Components for the automotive and aviation industries
- Used in packaging foods and beverages
- Used for making furniture components
- It is used in the fabrication of a wide range of mechanical parts like valves, linkages, gears, pumps, and so on.
- Used in the production of all types of medical devices and parts.
- Used for making all types of consumer plastics and their components.
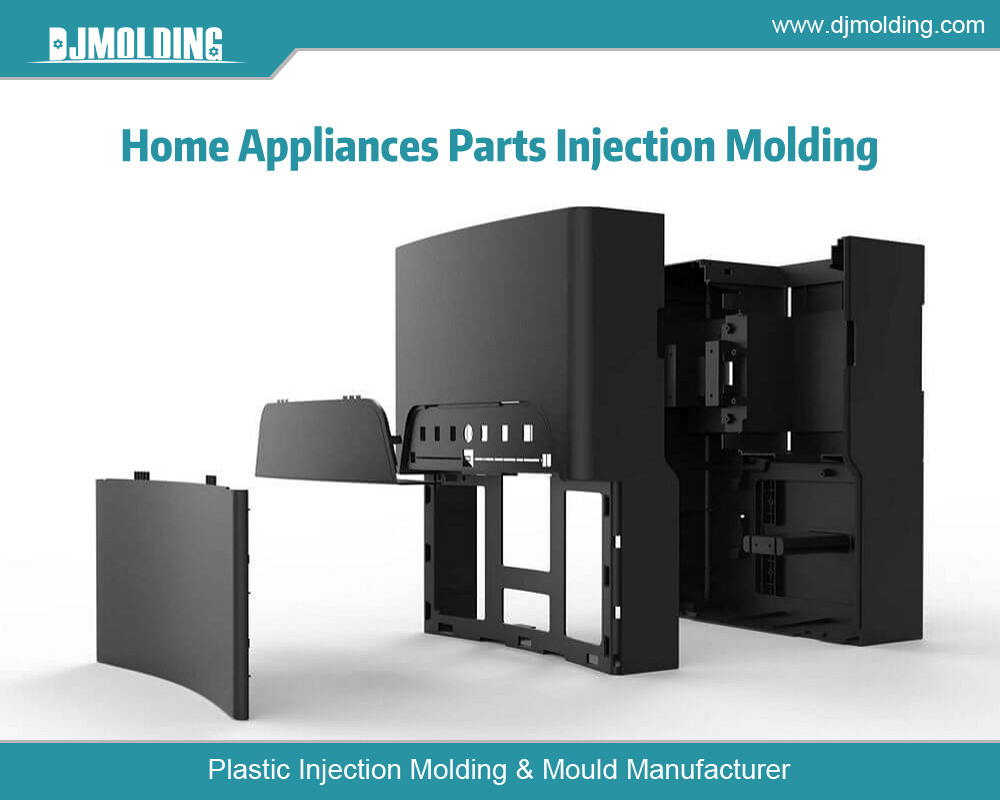
Benefits of injection molding technologies
The different types of injection molding technology are available for industrial use because of their usefulness and benefits. When it comes to this technology, manufacturers tend to enjoy a wide range of advantages. These include:
- This technology is highly cost-effective in the production of large batches of consumer goods.
- The technology specializes in the use of a wide range of materials that can be used to create both general and special products.
- With injection moulding, product designers can create any design and develop it into an actual product.
- The parts used in injection moulding can be modified into any shape to allow for easy application. They can be as small as rice grains or as big as the dashboard of a vehicle. The size of the moulding material depends on the product that is being produced.
- With the help of injection moulding, companies can easily produce parts that have a high degree of complexity. This is not the case with traditional manufacturing because it will require a lot of effort and time – which can be channelled into other parts of the business.
- This manufacturing technology is a production method that ensures little or no waste. In addition, you can recycle the waste to create new materials for production.
For more info about the different types of injection molding technology for plastic parts manufacturing companies,you can pay a visit to djmolding at https://www.djmolding.com/technology-application/ for more info.