Effective Low-Volume Manufacturing Strategies For Business Growth
Effective Low-Volume Manufacturing Strategies For Business Growth
Low-volume Production
Prototyping and manufacturing now use digital technology like robotics, automation, and 3D printing. The secret is to handle complexity and speed with comfort. In the end, quick gratification is the norm in our world, and customers are demanding more variety and customization than ever before, in addition to getting what they want when they want it.
This kind of setting creates endless opportunities but also presents countless obstacles when progressing swiftly. Reaching the prototype stage of design is one thing, but really starting “manufacturing” is another. With product life cycles being shorter and launch cycles getting shorter, it’s imperative that your strategy prioritize quick innovation and time-to-market.
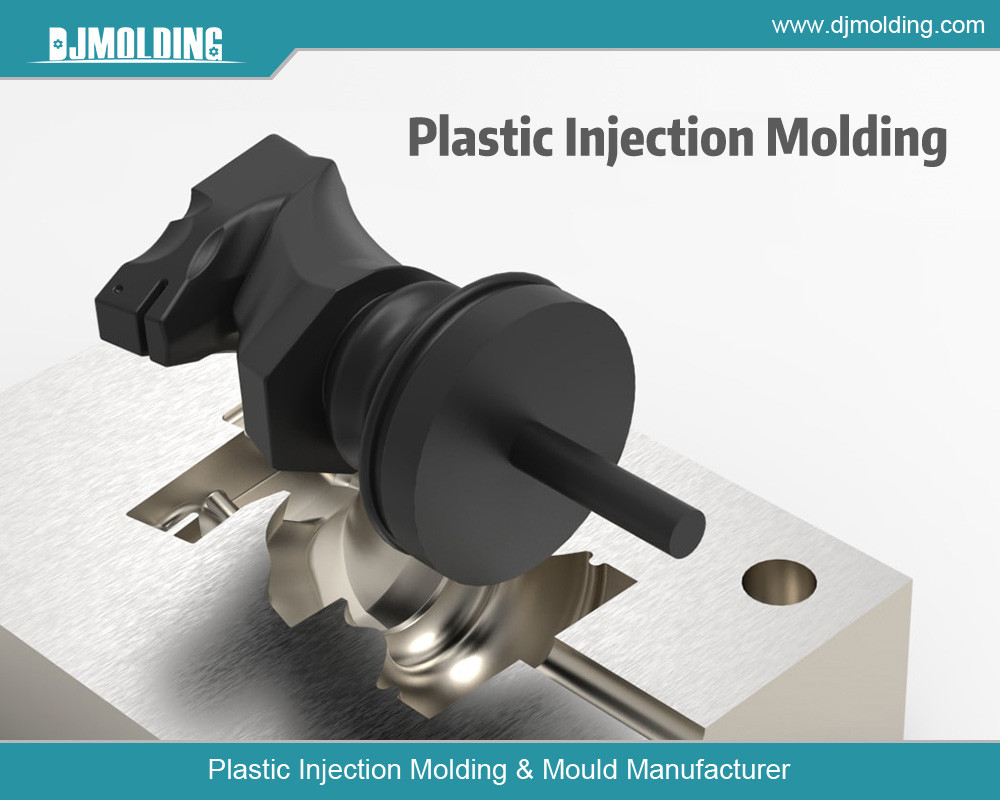
What lies in the middle, ambiguously, between mass production and prototype?
Effective low-volume production is one of the industrial industry’s most underappreciated sectors. Firms are seeking low-volume providers of solutions to help prevent and fix ramp difficulties ahead of high-volume production because of the numerous risks and expenses associated with expanding quickly enough to “mass commercialization.”
Sadly, businesses are usually compelled to use tier 1 manufacturing capabilities, which are very expensive, or tier 2 or 3 services, which are not very suitable for low-volume manufacturing. On the contrary, because of their low-scale production needs, startups are unable to even obtain the necessary resources and experience.
Nevertheless, we think that following these five stages will enable successful low-volume production for business growth:
Establishing a Digital Thread
Getting every phase of the product life cycle right is crucial, from research to realization. However, without the smooth flow of data, none of this would be feasible. This is precisely what the digital thread accomplishes, linking data from the supply chain to manufacturing to design. Agility, a crucial component of developing products that change people’s lives, may be enabled by providing all stakeholders in the item’s lifecycle with the appropriate data.
Finishing up the concurrent design
Although it is easy to view the method of getting a product to the marketplace as a series of steps from conception to completion, this perspective can actually slow down the entire process. I cannot stress enough how important speed is. Anticipating the needs of eager customers will help you deliver ideas faster and beat the competition. All of the parallel disciplines are integrated into a good product development process since they are interdependent. For instance, in order to guarantee that certain parts can be acquired consistently, at the appropriate cost, and on schedule, design stakeholders must communicate with those in the supply chain.
Bringing Diverse Teams Together with Domain Knowledge
As crucial as it is to connect data and processes, connecting people is what truly creates magic. Bringing disparate teams together can result in the introduction of fresh ideas, problems, and solutions. Utilizing individuals with domain expertise allows you to make use of the newest tools and methods.
Employing state-of-the-art technology
We now have access to new technologies thanks to the digital revolution, like digital twins, augmented reality, and additive manufacturing. Where it is economically feasible, using these technologies as electronic building blocks for the duration of the product lifecycle and throughout the design phase can result in a significant impact. To guarantee that emerging technologies function during the design, prototype, small-scale build manufacturing, and mass production stages, true engineering rigor is required. Recent developments have made it possible to transfer additive manufacturing work into high-volume manufacturing.
Orchestration of the Supply Chain
All of the hard work that goes into designing, developing, or prototyping is worth nothing if the supply chain collapses! No matter how brilliant your concept or design is, the end result will fail if you can’t make it. This is true for both mass manufacturing and low-volume builds. Components with lengthy lead times, parts that are only available from one supplier, or risks in the supply chain can all harm a product’s ability to reach consumers and turn a profit.
Early on in the product life cycle, supply chain orchestration is implemented. When it comes to managing a fast product launch, absorbing volume changes, and reducing risk, you need to be adaptable and agile. Having the proper tools and experience are crucial in this situation. Something truly unique can be made and supplied at the proper time, in the right amount, at the right quality, and at the right price if the foundations are laid correctly and the appropriate digital building blocks are connected. All of the aforementioned components are necessary.
Three Strategies for Low-Volume Manufacturing to Take into Account
Manufacturing using a High Mix and Low Volume (HMLV)
Significant Mix, Lower Volume Manufacturing can seem like a chaotic operation because tiny batches of several items are usually produced simultaneously. This plan calls for a wide range of supplies and equipment, as well as numerous process modifications. Because it necessitates innovation and flexibility, it is therefore not a choice that is appropriate for an assembly line setting.
Lean, low-volume, adaptive manufacturing
Although at first glance, lean concepts don’t seem to be intended for low-volume production, there are certain helpful features that are appropriate. Reducing waste is one such component. Developing a method that enables the construction of one item in the fewest steps is a smart idea, even for low-volume production. Creators can more effectively scale their operations and lower the cost of the production stage by always looking to enhance their procedures.
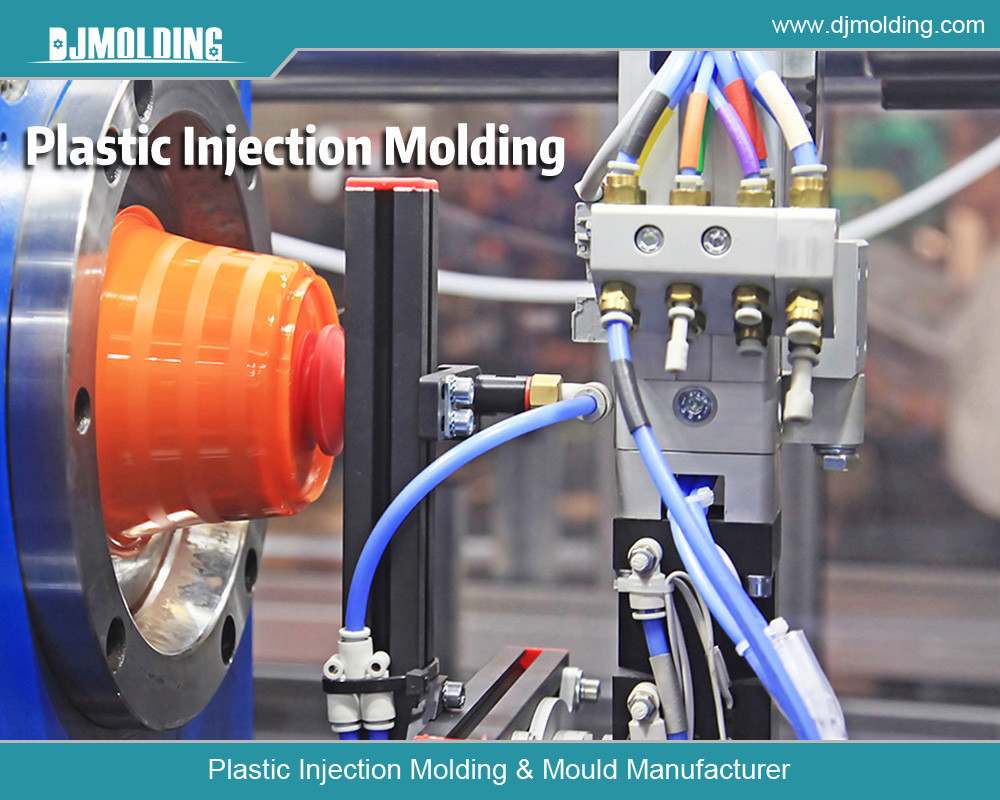
Just-in-Time (JIT) Production
Both high- and low-volume settings can benefit from JIT. Really, everything comes down to meeting demand. The manufacturing process happens after the order, as opposed to producing goods in advance of sales. Manufacturers can control costs and maintain low inventory levels by choosing this option, which also saves storage space.
JIT works best in industries where producing goods requires a lot of money or time. It is particularly helpful when resources to create new items are expensive or limited. Its popularity in the automobile sector can be attributed to this. It’s a production technique that works well for creating customized products as well.
For more about effective low-volume manufacturing strategies for business growth,you can pay a visit to Djmolding at https://www.djmolding.com/low-volume-manufacturing-service/ for more info.