Efficient Metal Pressing Techniques For Low-Volume Production In Automotive Plastic Parts Manufacturing
Efficient Metal Pressing Techniques For Low-Volume Production In Automotive Plastic Parts Manufacturing
The Fundamentals of Pressing Metal
A manufacturing technique called metal stamping is used to shape flat iron sheets into desired shapes. It’s an intricate procedure that may involve several metal-forming methods, such as punching, bending, piercing, and blanking. Thousands of businesses in the US provide metal pressing services to supply parts to the aerospace, automotive, medical, and other industries. Large amounts of complicated parts that can be produced quickly are becoming more and more necessary as global markets change.
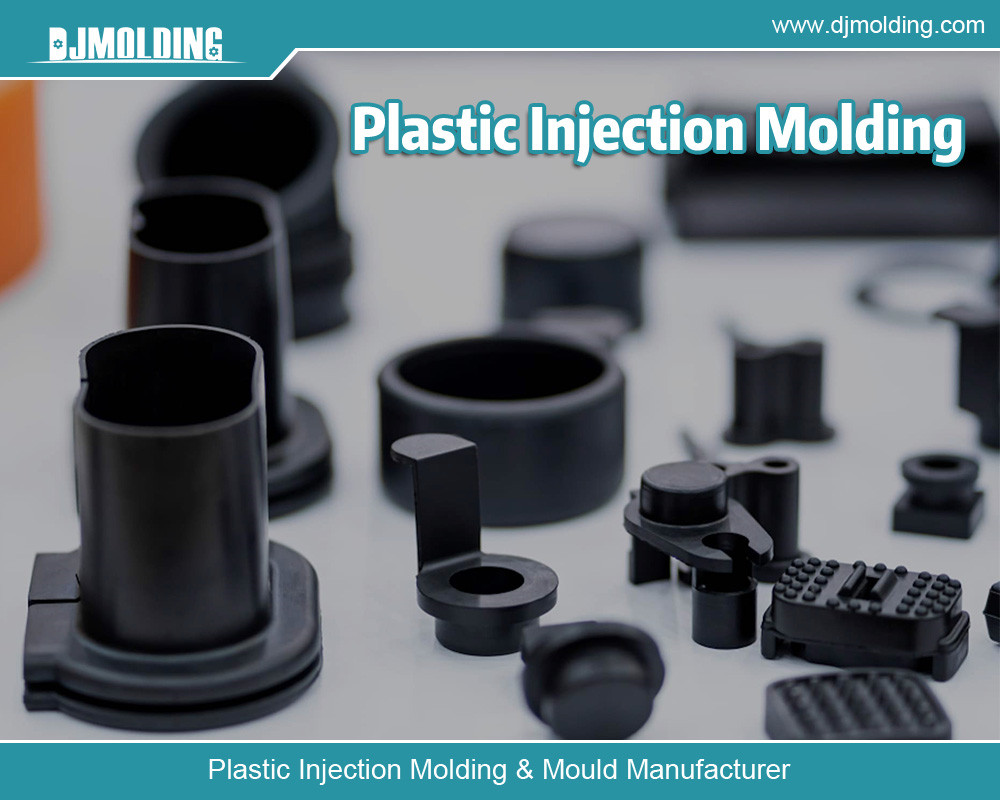
Costs of metal fabrication tooling
To find the optimum choice for a given application, first compare the tooling costs based on different quantities. Roll-forming is one of the processes that can help businesses with high-volume applications since it can make parts that require many procedures in one line. When compared to other processes, roll shaping has the smallest tooling maintenance costs for high-volume runs. However, roll tooling might not be the ideal choice for low-volume runs. Roll lines may get lengthy if an additional metal-forming procedure is necessary, and the cost of fabrication may go up if more tools are needed.
Because press brakes can create parts efficiently and affordably that would otherwise require thousands of dollars’ worth of tooling, they are more frequently employed in low-volume metal fabrication. Press braking, when coupled with a turret, is a less expensive tooling method for producing small numbers of parts than roll forming. The choice between specialized and readily available tooling is another expense factor. Your metal fabricator will be able to cut expenses significantly by not having to create custom tooling if they have a wide range of standard tooling in their catalog.
Recapitulating Metal Forming Costs
The best course of action is to make projections and forecast accurately if your primary objective as a buying manager is to amortize costs over time in order to lessen the initial financial impact. Although it might seem obvious, accurate long-term cost forecasting necessitates a thorough understanding of every stage of the production process. For instance, find out how much manpower will cost you overall. Fabricating and manufacturing individual parts can be quite labor-intensive for businesses that fabricate sheet metal goods. The cost of labor can go up rapidly during every metal fabrication process. Output techniques like roll rolling and stamping are ideal for high volume demands since they should result in lower labor and setup costs per piece as output levels rise.
Product Yield and Raw Material
Selecting the ideal metal manufacturing method for a project involves considering a number of factors. While product volume varies according to customer and requirement, five thousand feet is typically a decent starting point. If you need to create 5,000 feet or more of a product, metal roll forming is a good option. Sometimes the cost of one thousand meters of raw material can reach five thousand feet; in such cases, it is better to buy more material and increase your manufacturing run. Save time while developing your ideas by using the Standard Profile after you have carefully analyzed all of your metal manufacturing alternatives and any potential obstacles.
Pressing Principles
Placing flat sheet metal, either in coil or blank form, into a stamping press is the process of stamping, also known as pressing. The metal is formed into the required shape in the press using an implement and a die surface. To form the metal, stamping handles like striking, stuttering, bending, coining, embossing, or swirling are employed. Stamping experts need to use CAD/CAM engineering technology to develop the tools before the material can be created.
To guarantee that every punch and bend retains appropriate clearance and, consequently, optimal part quality, these designs need to be as exact as possible. Hundreds of parts can be found in just one 3D model, making the design process time-consuming and complex in many cases. A manufacturer can finish the tool’s production by using a range of machining, crushing, wire EDM, and additional manufacturing services after the tool’s design has been created. A quick and affordable fix for this necessity in large-scale manufacturing is metal stamping. When a manufacturer needs metal pieces stamped for a project, they often search for three key characteristics:
Superior quality and robustness
Low Price
Quick Recovery Time
Metal Stamping Types
The progressive, fourslide, and deep draw metal stamping techniques are the three main categories.
Progressive die stamping:
This technique has several stations, each of which serves a distinct purpose. Strip metal is first fed through a stamping press that advances. After the strip steadily unrolls from a coil, it enters a die press, where it is chopped, punched, or bent at each station of the tool. Every station that comes after adds to the labor of the ones that came before it, creating a full section.
A manufacturer may need to use multiple presses, each completing a single step needed for a finished component, or frequently swap out the equipment on a single press. To really finish a product, additional machining services were frequently needed, even with numerous presses. Because of this, progressive die pressing is the best way to meet the following requirements for metal objects with complicated geometry:
quicker response time.
Reduced labor costs
A shorter run duration
Increased reliability
Spiral-bound pressing
Four slides, also called multi-slide, is a process that uses four slides and horizontal alignment. To put it another way, the workpiece is shaped by using four tools at once. Even the most complex elements can be developed with this procedure by making delicate cuts and complex bends. When compared to conventional press stamping, four-slide stamped metal can provide a number of benefits that make it the better option in many situations. Among these benefits are the following:
Flexibility for more intricate components
More adaptability for design modifications
As the name suggests, a four-slide contains four slides, which allows for the simultaneous use of up to four separate tools, one for each slide, to accomplish numerous bends. Each shaft that has a tool attached to it swiftly twists the material as it feeds into a four-slide
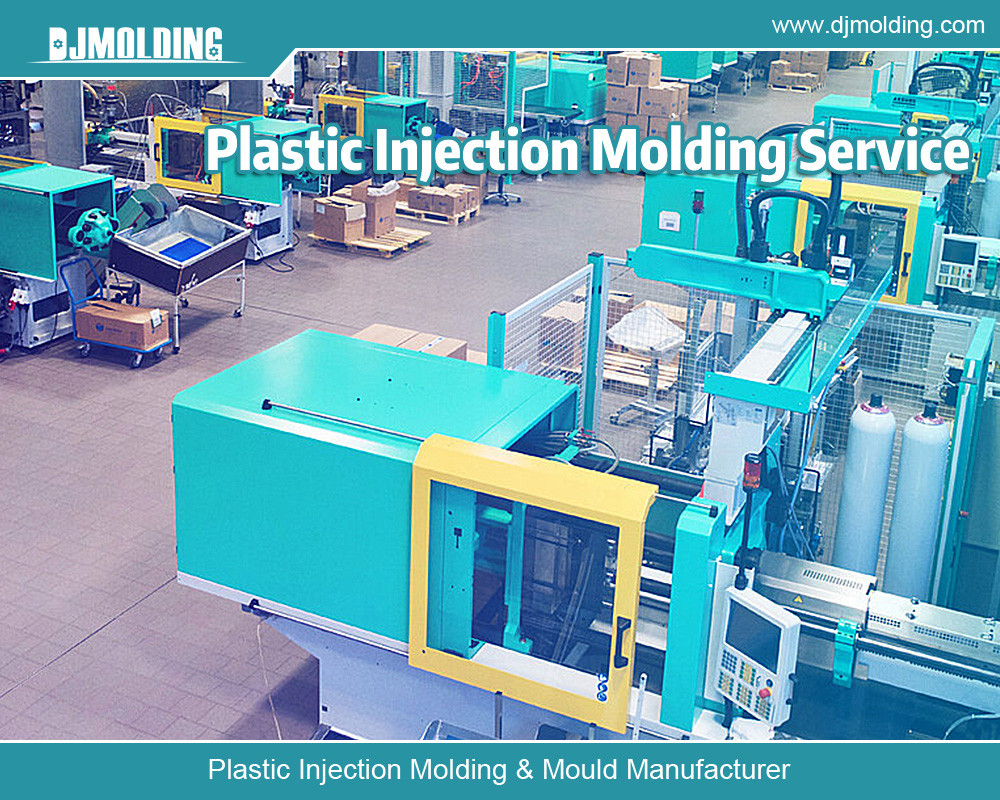
In-Depth Stamping
Deep drawing is the process of shaping a blank piece of metal into a shape by pulling it into the die with a punch. When the drawn part’s depth is greater than its diameter, the technique is known as “deep drawing.” This kind of forming is a more affordable option than turning techniques, which usually call for consuming more raw materials, and is perfect for producing components that require many series of diameters. Typical uses for deep sketching and items created with it include:
automobile parts
Parts of aircraft
Electronic switches
Cutlery and pots and pans
For more about efficient metal pressing techniques for low-volume production in automotive plastic parts manufacturing,you can pay a visit to Djmolding at https://www.djmolding.com/the-ultimate-guide-to-low-volume-production-sheet-metal-everything-you-need-to-know/ for more info.