Exploring The Benefits Of Low-Volume Production Silicone Molds
Exploring The Benefits Of Low-Volume Production Silicone Molds
Manufacturers can produce similar, low-volume silicone components with consistent features and attributes by using this production method. Modern manufacturing techniques are being used by manufacturers to get the upper hand in ever-evolving marketplaces.
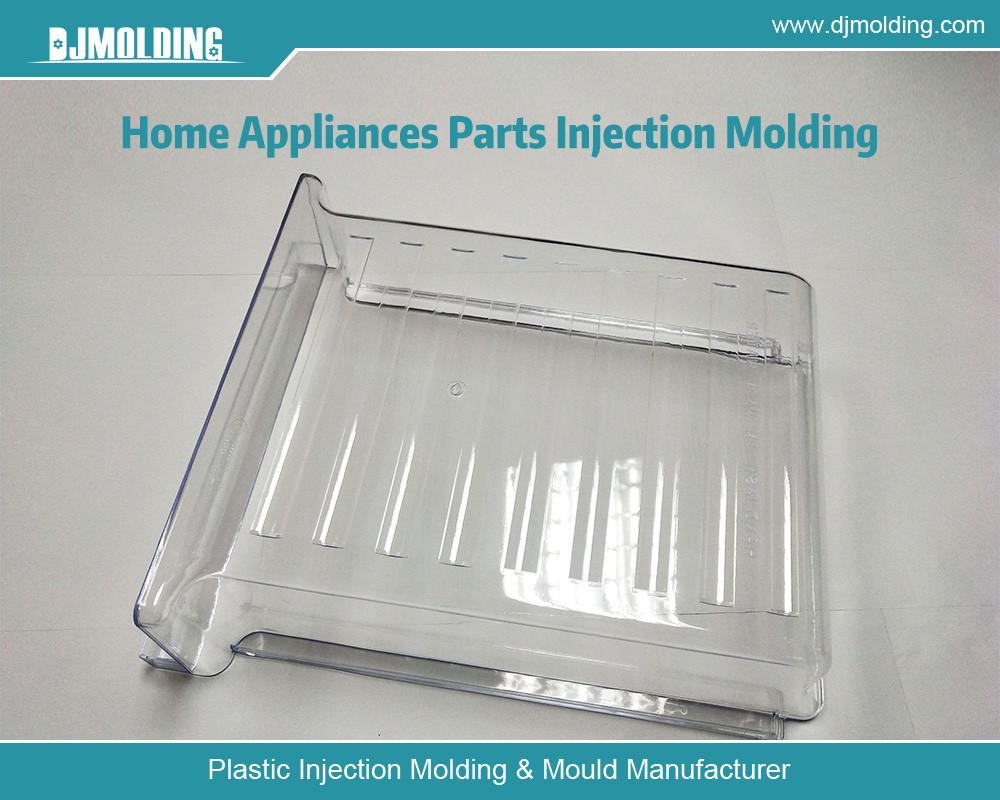
Low-Volume Silicone Molding: What Is It?
The best manufacturing method for making a component in smaller quantities than 1 lac is low-capacity molding. It is used for mass-manufacturing similar components prior to subscribing for long lasting molding setup; nevertheless, some low-volume plastic products could never require larger-scale manufacturing, so it is used beforehand. One of the more common methods used to create plastics nowadays is molding.
The optimum applications for MPM equipment are modestly produced plastic-molded items. They can employ cheap instruments with a single cavity, are affordable, and need little space. Among other applications, low-volume silicone molding machines are perfect for producing prototypes, bridges, and ASTM specimens. Additionally, these devices may fulfill orders for smaller amounts.
Comparing Low Volume vs. Traditional Silicone Casting
The basic key differences in low-capacity silicone casting and conventional injection casting is the production pace. Compared with the low-capacity injection casting, common molding takes a lot longer. Moreover, conventional injection molding requires more intricate mold shapes, that could lengthen the time span required to produce the components. This is why there are numerous benefits to using small scale silicone molding instead of more conventional techniques.
Benefits of Injection Molding at Low Volume
Low-Volume silicone Molding by injection is a vital process in the field of quick production. The ongoing development of the model might shorten lead times for transportation and production. Regretfully, the conventional method does not yield the desired outcomes as rapidly.
Nonetheless, the features of the production process conflict with the demands of the plastics market in a number of ways. If the mold’s design is complex, the manufacturing time for the parts could increase significantly. On the other hand, low-volume casting is a useful technique for quickly addressing these issues. Just a handful of its many benefits are as follows:
Employs more comfortable aluminum tooling
Unlike the conventional molding process, low-volume silicone molding eliminates the need for hard steel casting tools. Instead, it uses aluminum, which is easier to mold into the desired shape. The hardness of aluminum is significantly less than that of steel. It significantly reduces complexity and facilitates speedy, simple use.
When aluminum is utilized for tooling, the annealing step of the heat treatment procedure might be omitted to expedite it. In order to adequately harden the metal and release internal tensions, steel tools frequently require annealing. Apart from this, aluminum castings can benefit from the majority of surface methods which are applied to steel molds.
Superior Components Production
Low-volume molding creates longer-lasting and more functional products, even though the tooling material is softer. Numerous things can be assembled using this production approach. Moreover, aluminum conducts heat transfer to steel much more quickly unlike steel. Exact placement of the cooling pipes is rendered unnecessary by the increased conductivity. It might add more mold pieces in this way. Thus, low-capacity molding offers greater design flexibility, bridging the distance between mass production and prototype.
Cheap Injection Molding for Large Volumes
A common misconception is that people may save money just by purchasing goods. Even though this is frequently the situation, there are instances in which it isn’t. Although this might be true for residential items, it is less definite for those used in the workplace. The cost of each finished product is largely determined by the components used in production. Injection molding operations with high volumes may occasionally need to fulfill very less order needs. They would have to take this action to offset their expenses or to make payments for the significant production-related charges.
However, compared to high-scale silicone molding, low-volume silicone molding frequently has significantly lower overhead. In this scenario, producers might produce a large quantity of things for sale without requiring minimum orders from customers. If you’re considering injection molding in small quantities for plastic batch manufacturing, that could be beneficial. You also won’t take a chance by purchasing from a supplier who hasn’t updated its inventory in a long time. All such factors could result in significant cost savings.
Reduced lead time
The manufacturing strategy helps increase the output of plastic components while also lowering the cost of production. It makes use of technology that speeds up price quotes for orders placed by customers. To ensure dependable and effective manufacture, the program also examines the component’s design.
Aluminum is such a pliable metal that it takes a lot less time and effort to cast molds from it. It is possible to extend the material’s lifespan without using hardening. Production may now begin in earnest as the mold can be delivered to the facility. This could reduce the time required to bring a product to market, which is beneficial for product departments of all sizes.
Design Flexibility
The goal of low-scale silicone molding is to create fewer pieces in a shorter amount of time. Because of this, a company’s decision to make little alterations or modifications to the design won’t have a big effect. Before the product is delivered to the customer, it can be improved iteratively using this process. Superior injection molding of plastic provides instant feedback, hence enhancing the product’s manufacturability. It makes it possible to test novel concepts across a range of sectors prior to the need for expensive mass manufacturing.
Bridge Regarding Scale
A corporation should begin small-scale silicone production if it intends to eventually make its products in huge quantities. It facilitates the move from prototype to large-scale manufacturing. With this technique, a prototype that can be produced in large quantities can now be created. Beyond that, it enhances the process as well as the final product.
Options for Molding Silicone in Low Volumes
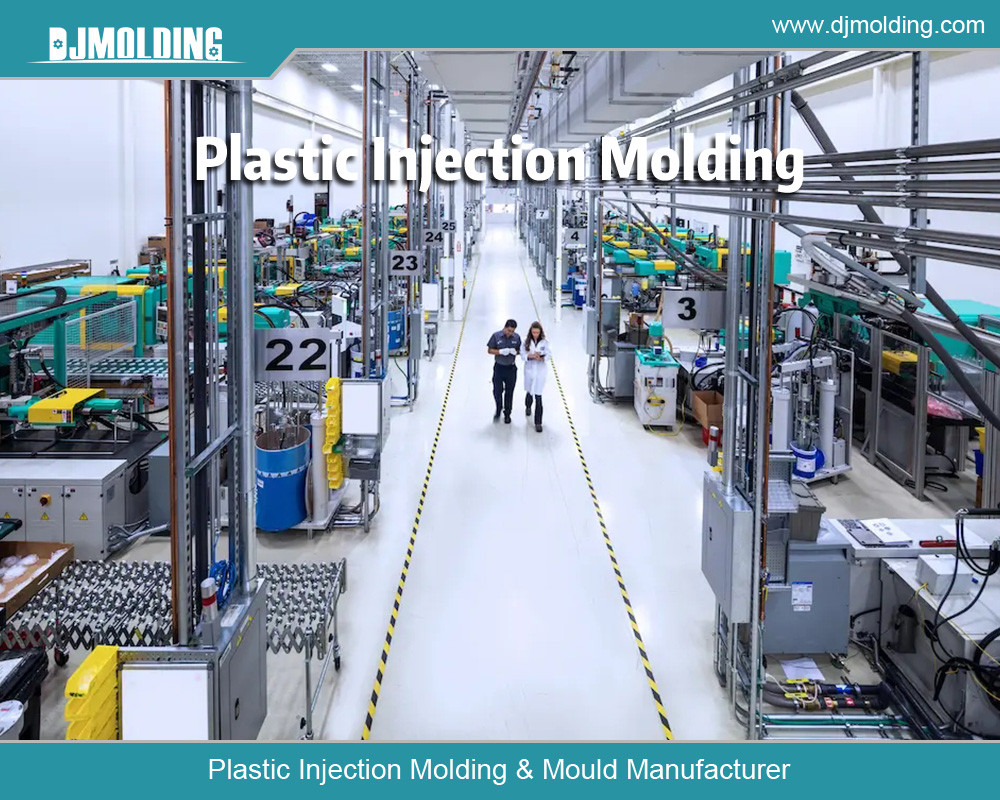
3D Digitizing
This procedure is the most innovative method for creating high-quality products in small quantities. Because it doesn’t require the development of molds at the beginning, three-dimensional printing shortens manufacturing times and lowers costs. Objects that are 3D printed frequently have layered surfaces. To achieve the desired surface quality, the surfaces can be readily painted and sanded.
CNC Workholding
Despite being one of the first manufacturing techniques, CNC machining is still recognized as one of the most dependable methods for producing goods in small to medium quantities. Because of its versatility, you can use it on a variety of materials. Making precise molds, trends, or dies that can be used in a variety of manufacturing processes is a beneficial application of it.
Thermally molding
Making molds to keep a thin sheet of plastic in place when it is heated is another useful method. After the plastic has heated, it can be molded using vacuum pressure, additional mechanical force, or another method. Any excess plastic sheet will be trimmed off after it has molded into the mold. This approach requires temperatures and pressures toward the bottom of this scale. To construct the mold, you’ll need a few low-cost items.
Casting of Urethane
Urethane casting is a great substitute for prototype injection molding. Urethane casting is unique to the alternative process in that there are no upfront expenses. The process requires that a master pattern of the object be created utilizing CNC machining or high-resolution 3D printing.
For more about exploring the benefits of low-volume production silicone molds,you can pay a visit to Djmolding at https://www.djmolding.com/the-advantages-of-low-volume-injection-molding-for-small-scale-plastic-parts-manufacturing/ for more info.