Mastering Low-Volume Silicone Molding Techniques For Liquid Silicone Rubber Injection Molding Manufacturing
Mastering Low-Volume Silicone Molding Techniques For Liquid Silicone Rubber Injection Molding Manufacturing
Learning the Technique of Silicone Molding: Creating Excellent Custom Molded Rubber
Using a heated mold, silicone rubber casting is a process for manufacturing, sculpting, and molding silicone rubber goods and parts. Silicone rubber is compressed or injected into a mold to take on the form and dimensions of the cavity inside the mold. Injection, contraction, and transfer molding are the methods utilized to create silicone rubber-molded parts; each method depends on a steel or cast-iron mold. Are you prepared to explore the intriguing field of silicone molding with liquids? You’re going to enjoy this if you enjoy originality and ingenuity! The fascinating and adaptable method of liquid silicone molding has transformed a variety of industries, including the automotive and healthcare sectors.
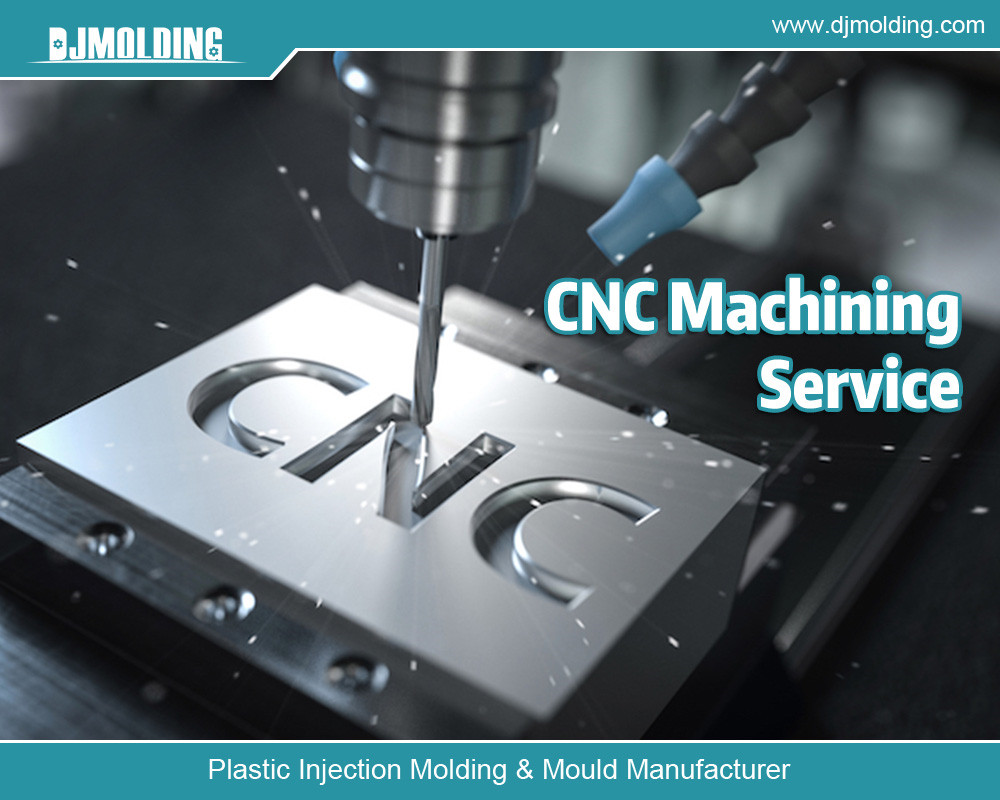
The Enchantment of Silicone Molding at Low Volume
In order to make complex and accurate parts, liquid silicone molding, also known as LSR molding, is a state-of-the-art manufacturing technique that includes pouring liquid silicone rubber onto a casting and allowing it to cure. The extraordinary advantages of this technique cost-effectiveness, speed of production, and minimal post-processing required to achieve complex geometries have led to its tremendous appeal.
LSR molding enables producers to reach extremely high precision levels, much like silicone sculpting. Liquid silicone casting cures at temperatures that are lower than standard rubber molding techniques, which makes it perfect for applications that are sensitive to heat. The outcome is excellent, immaculate, long-lasting, and precisely designed goods.
Making Personalized Molded Rubber Wonders
Revealing the Artistry of Rubber Custom Molding
The ability to use silicone molding to produce bespoke molded rubber products is one of its most alluring features. LSR molding opens up a world of options for engineers and designers who want to create rubber parts that precisely match specifications, spanning seals to closures and beyond.
The Foundation of Liquid Silicone Molding: Pipe Seals
One of the best examples of the way silicon casting has changed industries is pipe seals. These crucial elements guarantee leak-free pipeline connections, averting expensive and damaging environmental leaks. Pipe gaskets are produced with unmatched accuracy utilizing LSR molding, which makes them an essential component of plumbing, infrastructure, and several industrial applications.
Liquid silicone rubber’s elasticity makes pipe seals adaptable to a variety of curved and sized surfaces, guaranteeing a tight fit that will last. Furthermore, because silicone rubber is so resilient, these seals can withstand high temperatures and corrosive environments while still offering dependable, long-lasting performance.
Utilizing Liquid Silicone Molding for Brilliant Applications
Automotive Innovations
The automotive industry has warmly welcomed the liquid silicone molding process. LSR molding is essential for anything from creating ergonomic interiors to sealing important engine components. Silicone rubber components improve driver and passenger comfort and safety, while custom-molded silicone gaskets and seals guarantee that your car’s engine stays in top condition.
Innovations in Healthcare
Aqueous silicone molding has completely changed the medical device manufacturing process. Seals and gaskets made of custom rubber are essential for preserving the quality of medical devices and guaranteeing patient safety. Because silicone rubber is biocompatible, it is the perfect material for uses inside the human body, like prostheses and implanted devices.
The Evolution of Electronics
The accuracy and robustness of liquid silicone molding are advantageous to the electronics sector. Specially molded rubber parts are essential for shielding delicate electronics from outside elements, including vibration, dust, and moisture. LSR molding makes sure that your gadgets function perfectly, whether it’s sealing electrical connections or making seals for cellphones.
Cooking equipment
Since silicone rubber is suitable for food and non-toxic, it is employed in the creation of cookware and food. It may be produced in visually appealing hues and meets FDA criteria for use as a cooking material. Silicone rubber finds extensive application in bakeware due to its ability to retain and preserve the flavor and aroma of the food being baked.
Silicone rubber utensils don’t adhere to surfaces and are simple to clean. They use less oil when preparing meals, which results in a better and more nutritious meal. Silicone bakeware and mixing bowls come in a variety of designs and can be hand- or dishwasher-cleaned without cracking or scratching.
Molds for Silicone Rubber
The creation of silicone castings for the purpose of creating molds using a variety of materials, such as wax, gypsum, resins, and other materials, is one particular application for silicone rubber. With silicone molds, you can easily manufacture personalized goods and designs that are incredibly sturdy, long-lasting, and repeatable. Because silicone rubber is inorganic, it can withstand temperature fluctuations, chemical exposure, and exposure to natural pollutants like fungi and bacteria.
Silicone molding is frequently used to create prototypes for product design analysis. Silicone molds offer a more affordable option than metal molds, which are labor-intensive, time-consuming, and expensive to create. In addition to being used in prototyping, they help create beta units for customer feedback and market testing. While rapid one-off sample creation is best achieved with 3D printing, silicone molds can produce small quantities for testing purposes.
Using Liquid Silicone Molding
After learning more about the diverse field of LSR molding, let’s examine the procedure in detail:
1.Material Preparation: To ensure that it satisfies the project’s unique needs, low-volume silicone rubber gets carefully blended to acquire the appropriate qualities.
2.Injection molding: A precisely engineered mold cavity is filled with liquid silicone rubber. This stage makes it possible to create complicated and detailed shapes.
3.Curing: The liquid silicone hardens to its final rubber shape during the curing process, which is started by heating the mold. To obtain the appropriate hardness and flexibility, the curing temperature and duration are carefully regulated.
4.Demolding: The molded object is carefully taken out of the mold when the cure process is finished. To prevent breaking the fragile silicone product, this step needs to be done carefully and precisely.
5.Quality Control: To guarantee that every custom-molded rubber component satisfies the highest requirements for precision, performance, and longevity, it goes through extensive quality control inspections.
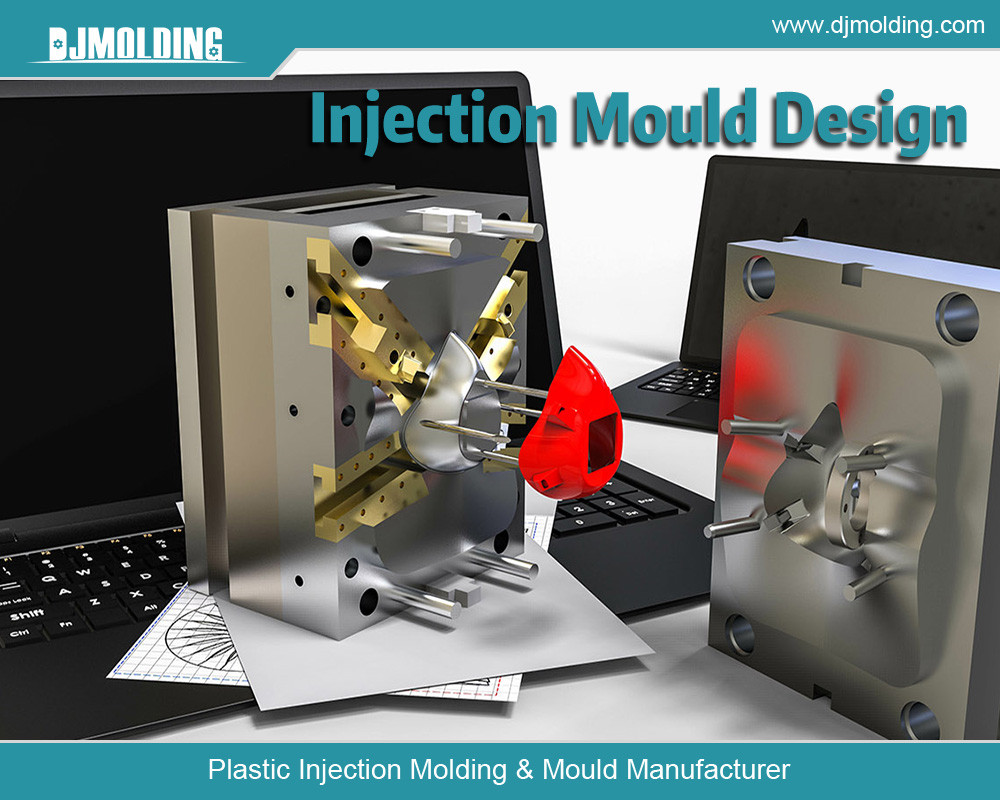
To sum up, low-volume silicone casting is an intriguing and adaptable technique that has revolutionized the production of custom-molded rubber goods, including vital parts like pipe seals. It has revolutionized a variety of industries, including electronics, healthcare, and automotive, thanks to its accuracy, robustness, and broad range of applications. Liquid silicone molding is an establishment that is dedicated to innovation and has limitless potential for shaping the production landscape.
For more about mastering low-volume silicone molding techniques for liquid silicone rubber injection molding manufacturing,you can pay a visit to Djmolding at https://www.djmolding.com/the-advantages-of-low-volume-injection-molding-for-small-scale-plastic-parts-manufacturing/ for more info.